High Voltage Power Supply for RPC Suvendu Nath
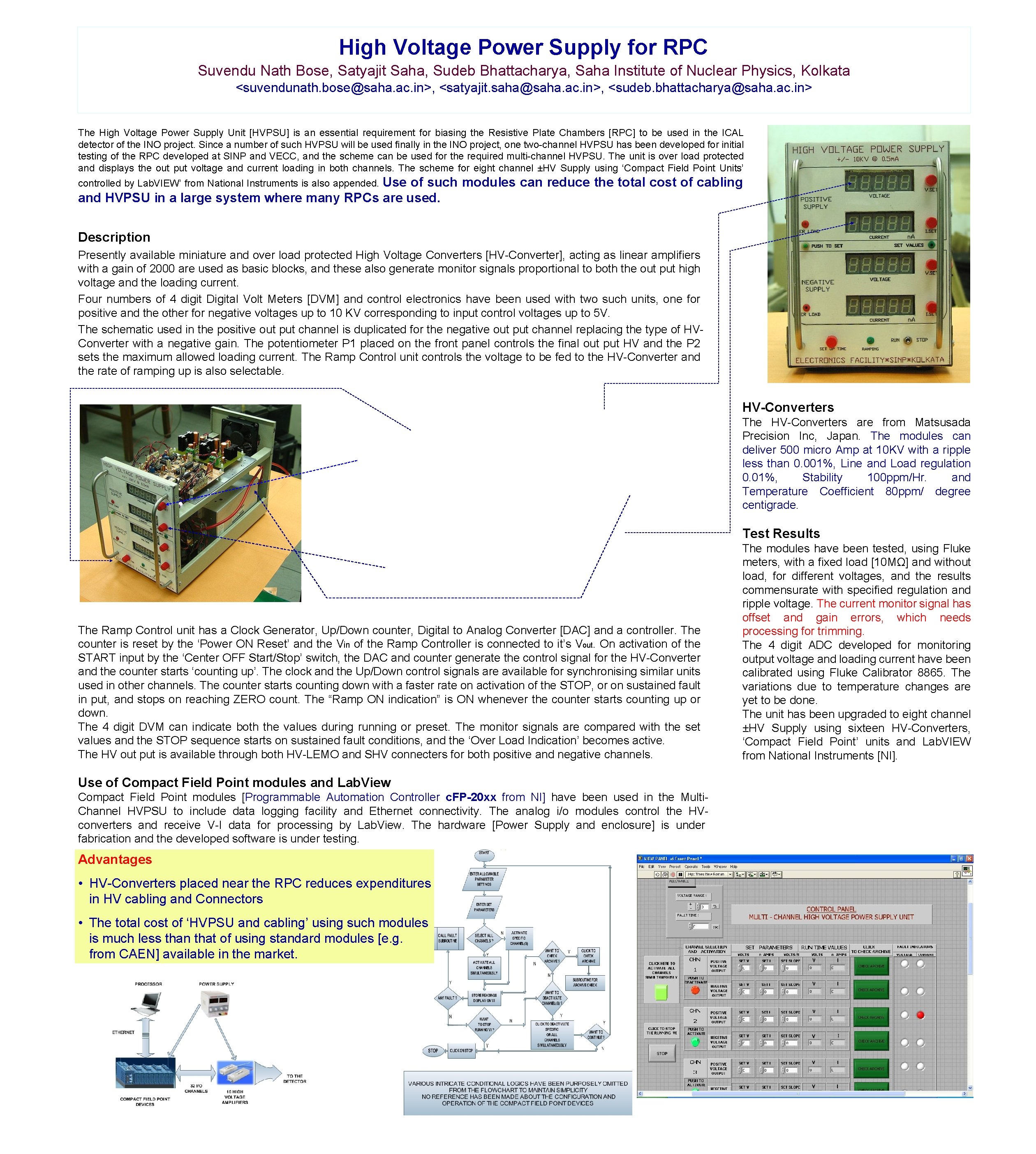
- Slides: 1
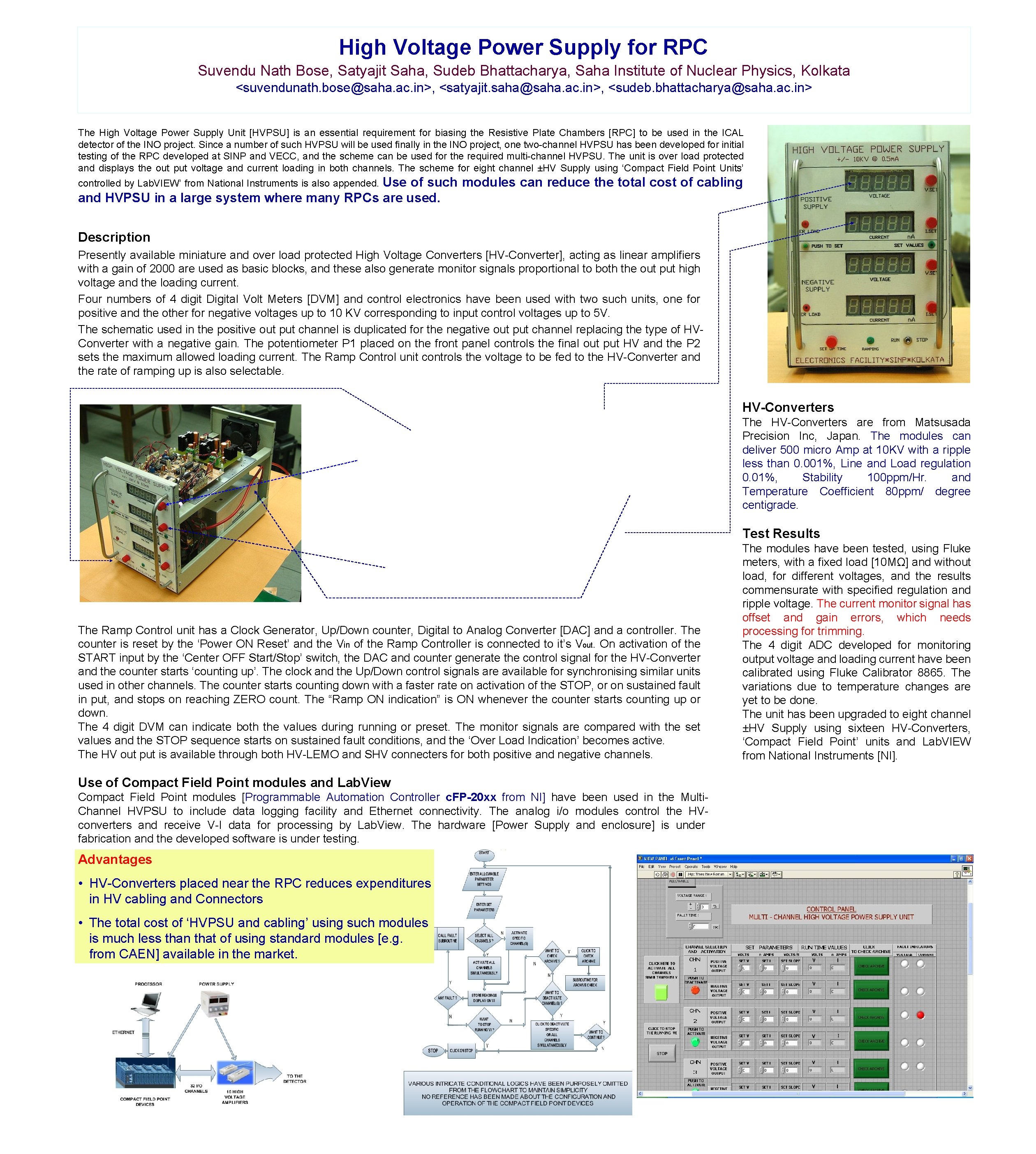
High Voltage Power Supply for RPC Suvendu Nath Bose, Satyajit Saha, Sudeb Bhattacharya, Saha Institute of Nuclear Physics, Kolkata <suvendunath. bose@saha. ac. in>, <satyajit. saha@saha. ac. in>, <sudeb. bhattacharya@saha. ac. in> The High Voltage Power Supply Unit [HVPSU] is an essential requirement for biasing the Resistive Plate Chambers [RPC] to be used in the ICAL detector of the INO project. Since a number of such HVPSU will be used finally in the INO project, one two-channel HVPSU has been developed for initial testing of the RPC developed at SINP and VECC, and the scheme can be used for the required multi-channel HVPSU. The unit is over load protected and displays the out put voltage and current loading in both channels. The scheme for eight channel ±HV Supply using ‘Compact Field Point Units’ Use of such modules can reduce the total cost of cabling and HVPSU in a large system where many RPCs are used. controlled by Lab. VIEW’ from National Instruments is also appended. Description Presently available miniature and over load protected High Voltage Converters [HV-Converter], acting as linear amplifiers with a gain of 2000 are used as basic blocks, and these also generate monitor signals proportional to both the out put high voltage and the loading current. Four numbers of 4 digit Digital Volt Meters [DVM] and control electronics have been used with two such units, one for positive and the other for negative voltages up to 10 KV corresponding to input control voltages up to 5 V. The schematic used in the positive out put channel is duplicated for the negative out put channel replacing the type of HVConverter with a negative gain. The potentiometer P 1 placed on the front panel controls the final out put HV and the P 2 sets the maximum allowed loading current. The Ramp Control unit controls the voltage to be fed to the HV-Converter and the rate of ramping up is also selectable. HV-Converters The HV-Converters are from Matsusada Precision Inc, Japan. The modules can deliver 500 micro Amp at 10 KV with a ripple less than 0. 001%, Line and Load regulation 0. 01%, Stability 100 ppm/Hr. and Temperature Coefficient 80 ppm/ degree centigrade. Test Results The Ramp Control unit has a Clock Generator, Up/Down counter, Digital to Analog Converter [DAC] and a controller. The counter is reset by the ‘Power ON Reset’ and the Vin of the Ramp Controller is connected to it’s Vout. On activation of the START input by the ‘Center OFF Start/Stop’ switch, the DAC and counter generate the control signal for the HV-Converter and the counter starts ‘counting up’. The clock and the Up/Down control signals are available for synchronising similar units used in other channels. The counter starts counting down with a faster rate on activation of the STOP, or on sustained fault in put, and stops on reaching ZERO count. The “Ramp ON indication” is ON whenever the counter starts counting up or down. The 4 digit DVM can indicate both the values during running or preset. The monitor signals are compared with the set values and the STOP sequence starts on sustained fault conditions, and the ‘Over Load Indication’ becomes active. The HV out put is available through both HV-LEMO and SHV connecters for both positive and negative channels. Use of Compact Field Point modules and Lab. View Compact Field Point modules [Programmable Automation Controller c. FP-20 xx from NI] have been used in the Multi. Channel HVPSU to include data logging facility and Ethernet connectivity. The analog i/o modules control the HVconverters and receive V-I data for processing by Lab. View. The hardware [Power Supply and enclosure] is under fabrication and the developed software is under testing. Advantages • HV-Converters placed near the RPC reduces expenditures in HV cabling and Connectors • The total cost of ‘HVPSU and cabling’ using such modules is much less than that of using standard modules [e. g. from CAEN] available in the market. The modules have been tested, using Fluke meters, with a fixed load [10 MΩ] and without load, for different voltages, and the results commensurate with specified regulation and ripple voltage. The current monitor signal has offset and gain errors, which needs processing for trimming. The 4 digit ADC developed for monitoring output voltage and loading current have been calibrated using Fluke Calibrator 8865. The variations due to temperature changes are yet to be done. The unit has been upgraded to eight channel ±HV Supply using sixteen HV-Converters, ‘Compact Field Point’ units and Lab. VIEW from National Instruments [NI].