Guidance on Corrective Action and Root Cause Analysis
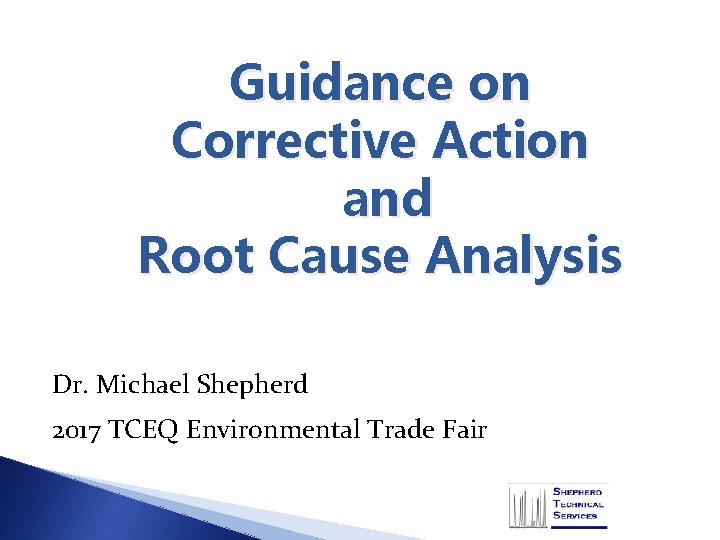
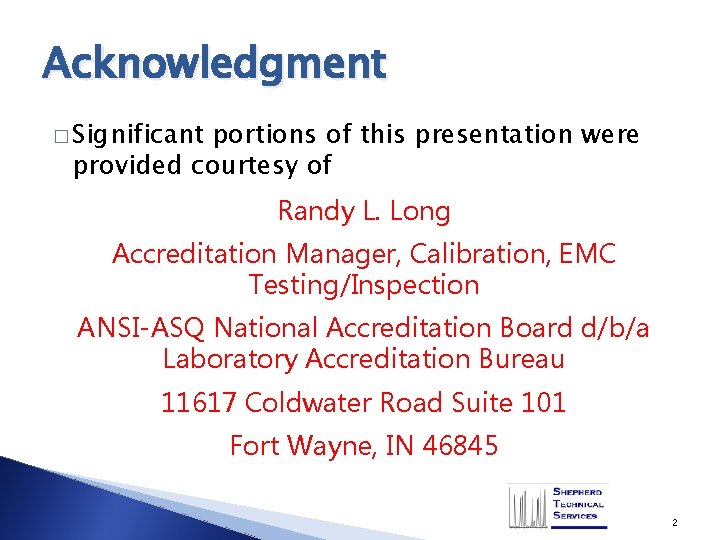
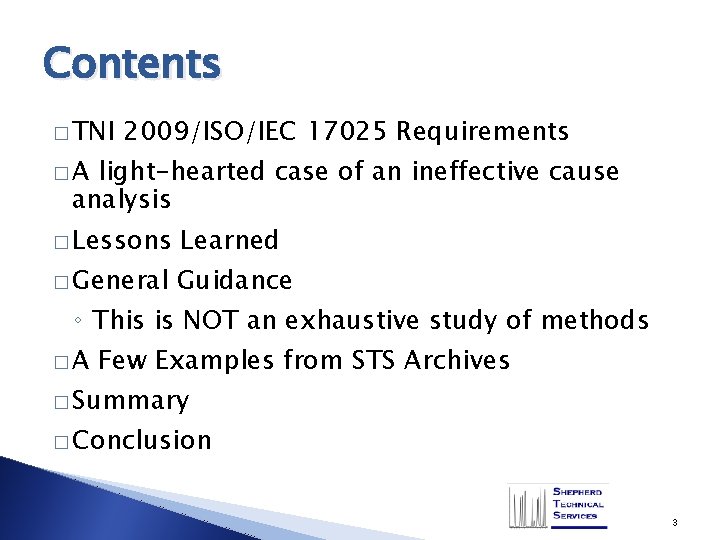
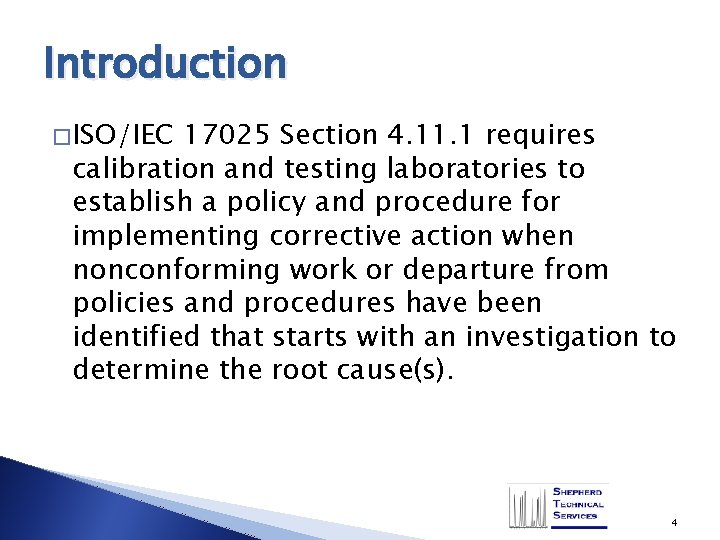
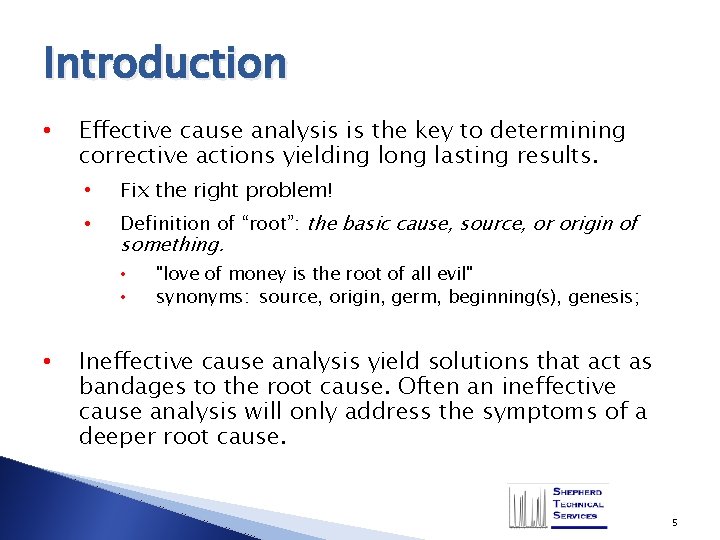
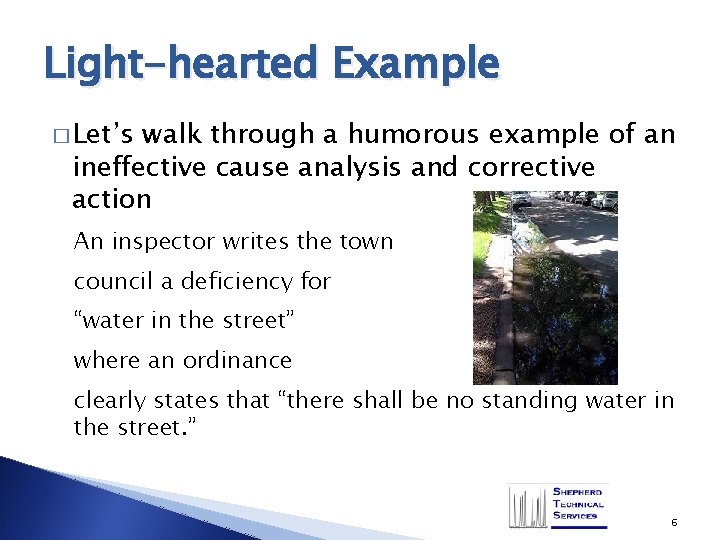
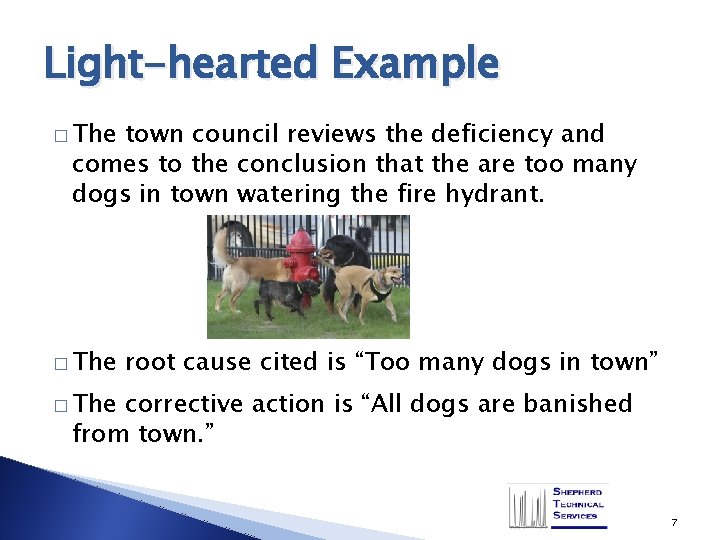
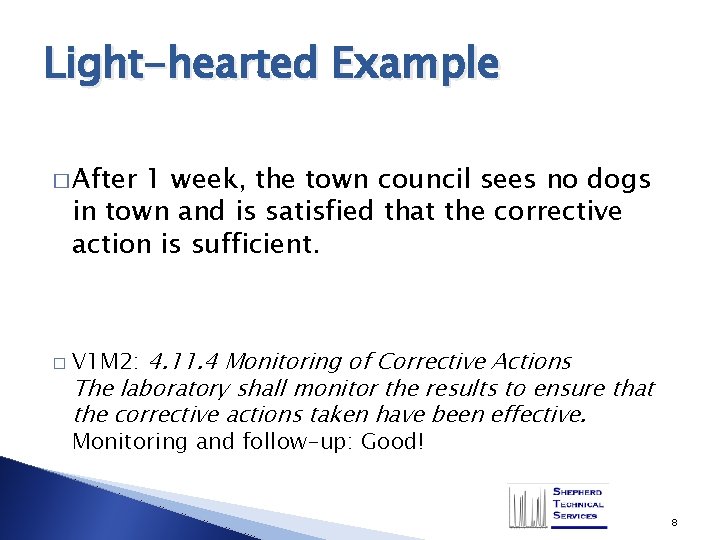
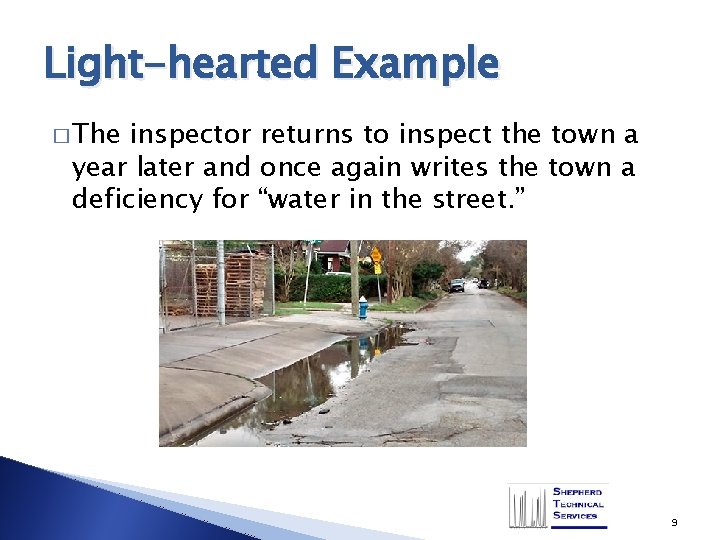
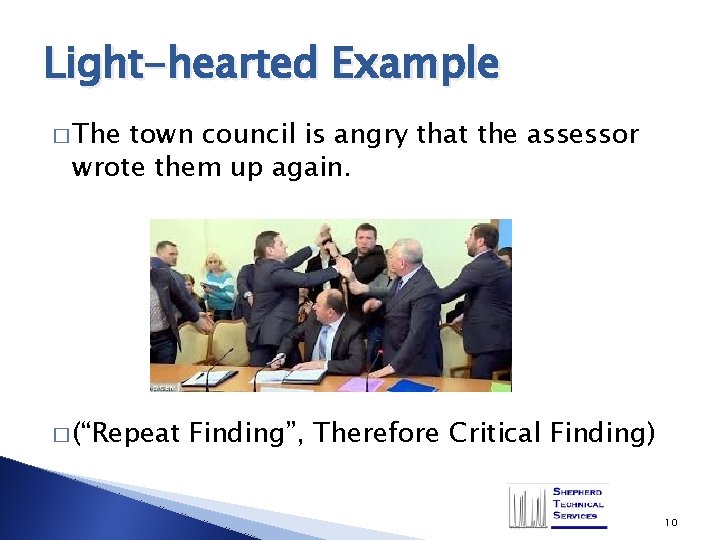
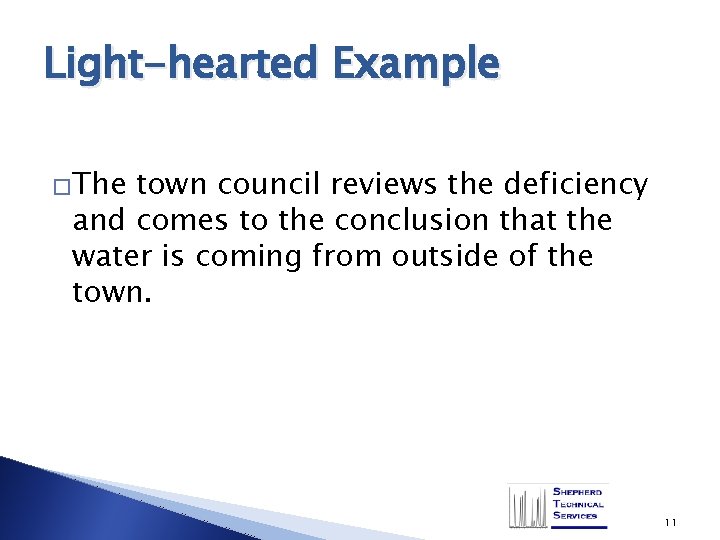
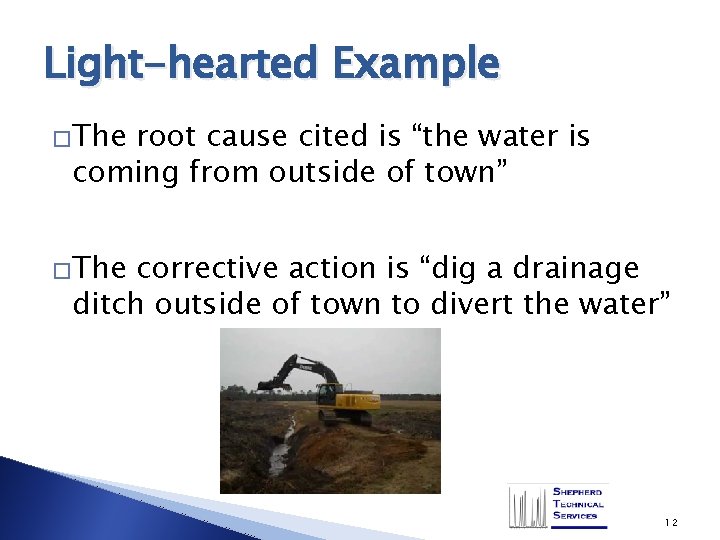
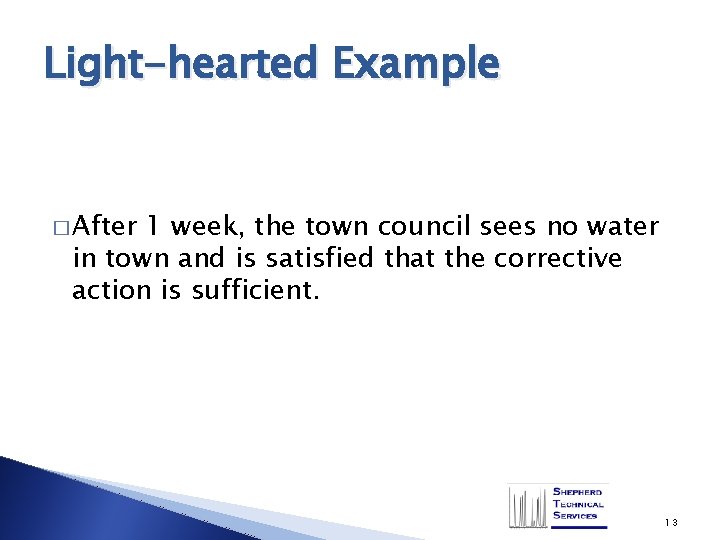
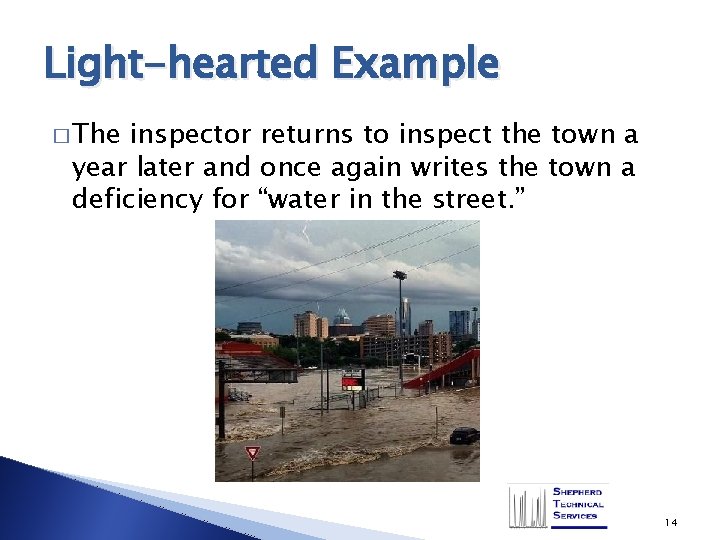
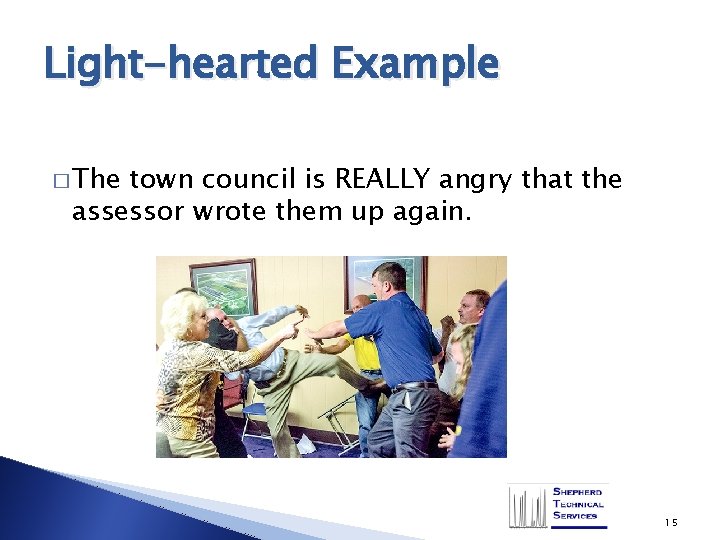
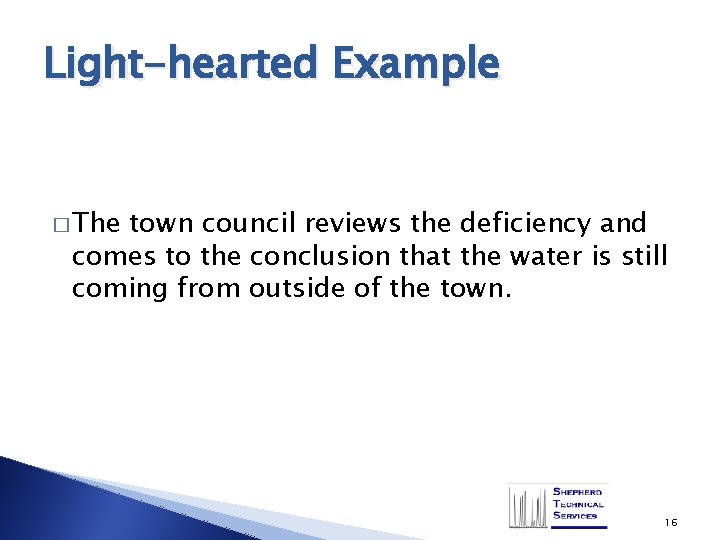
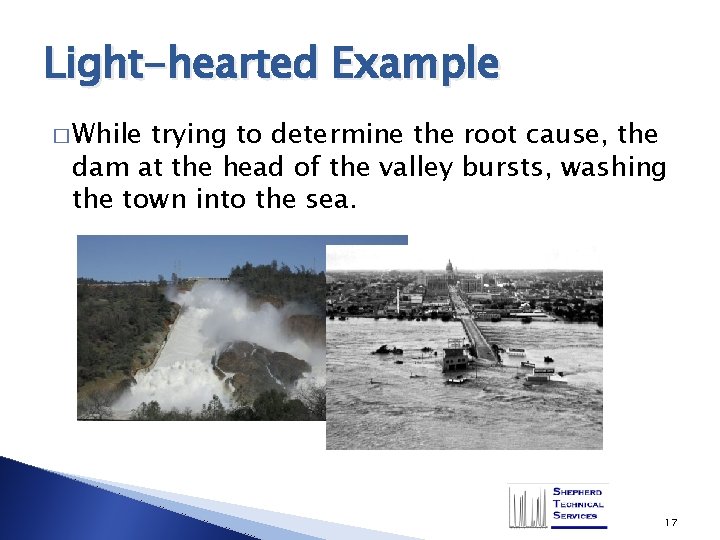
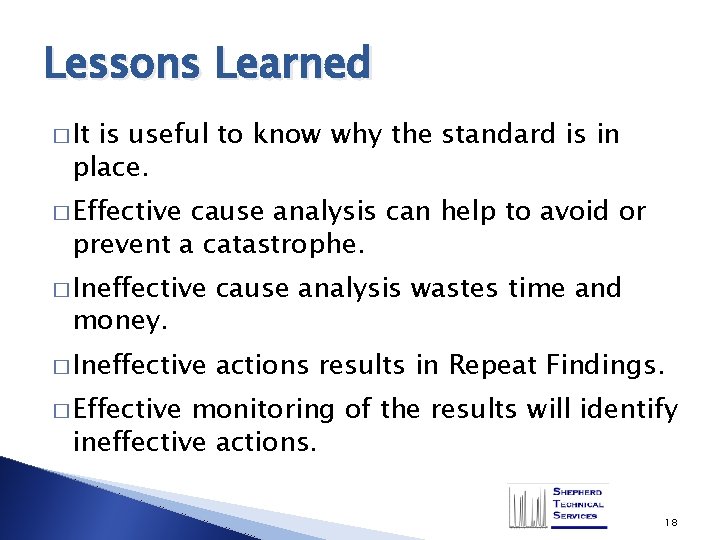
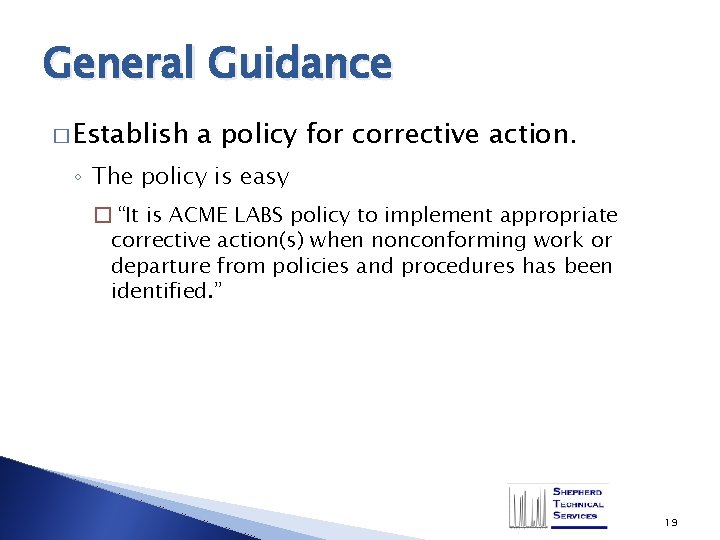
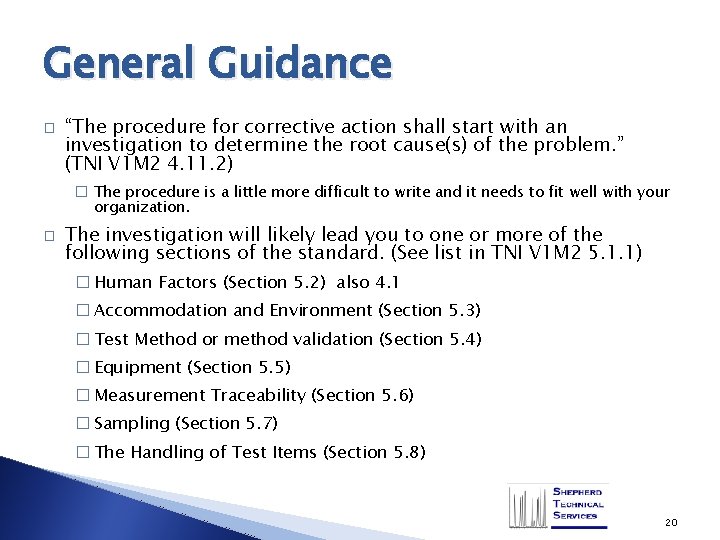
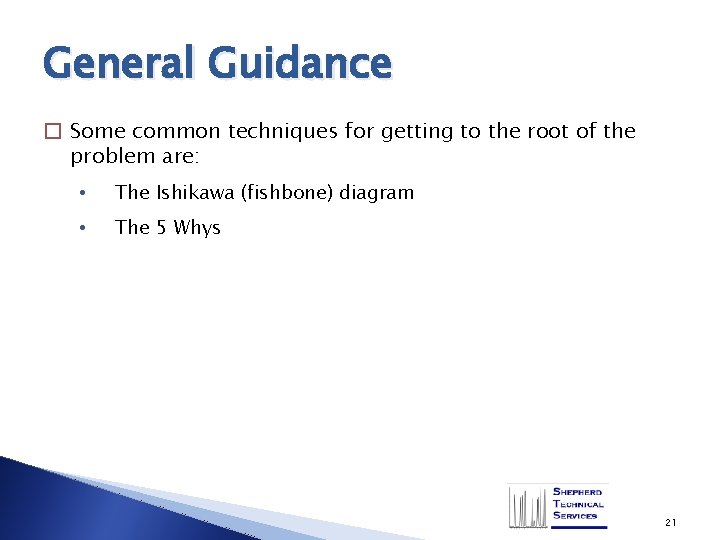
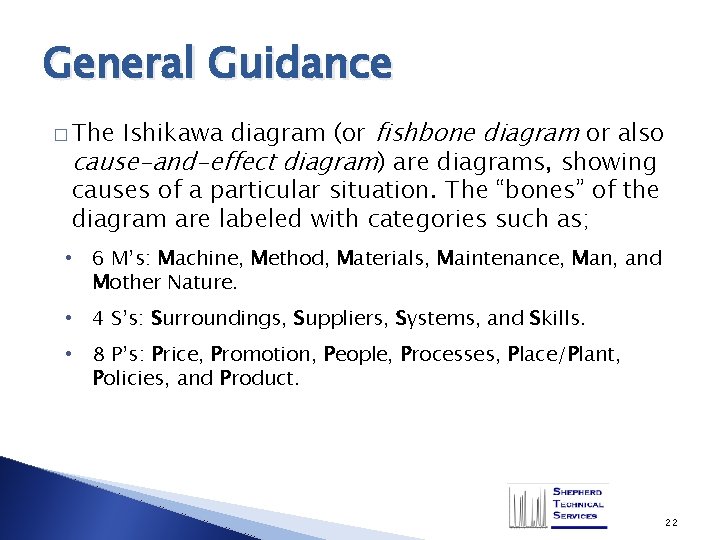
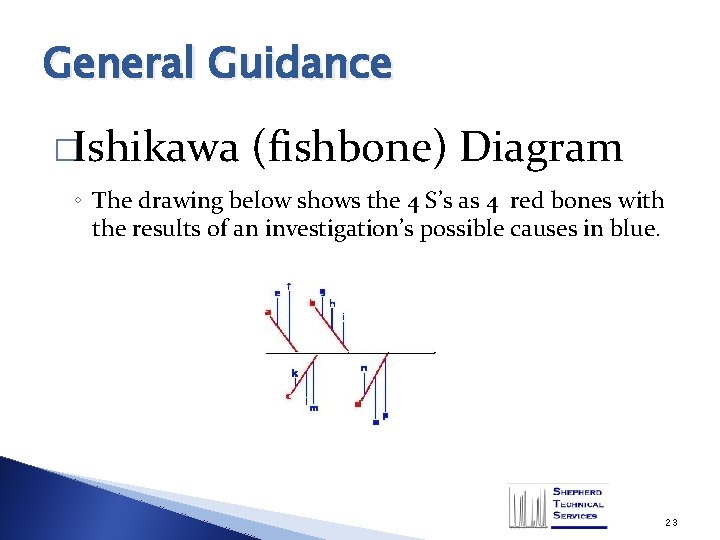
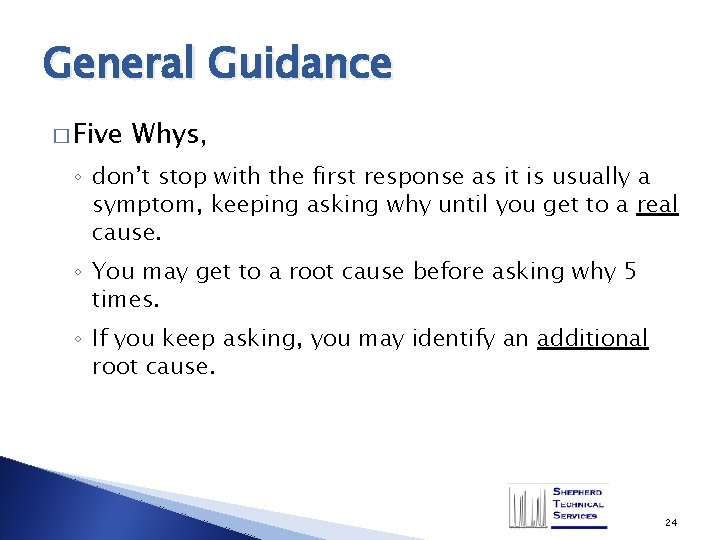
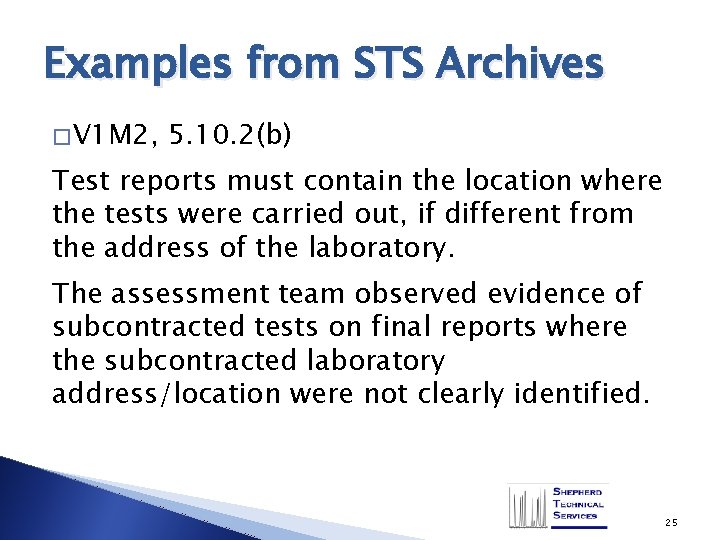
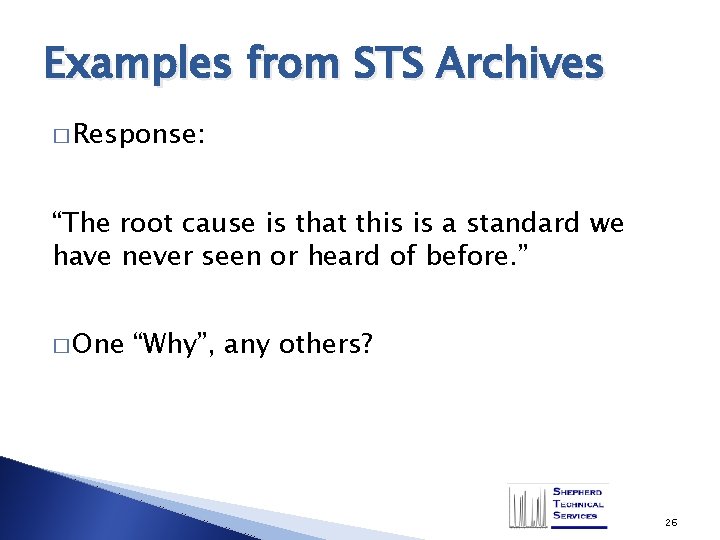
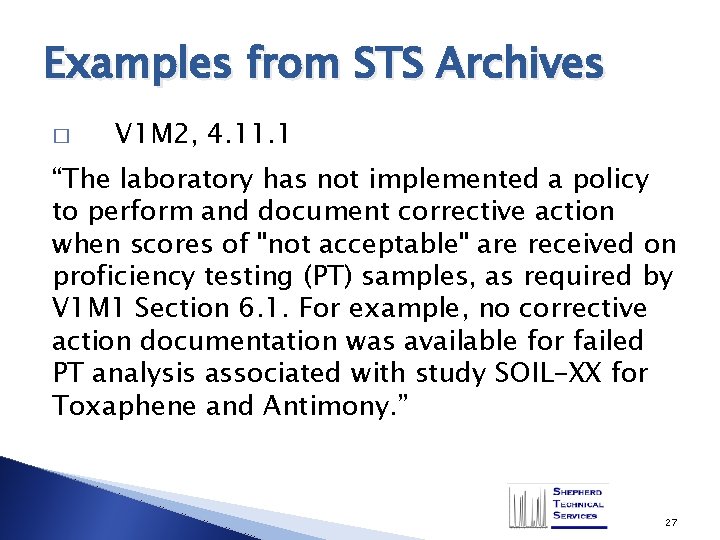
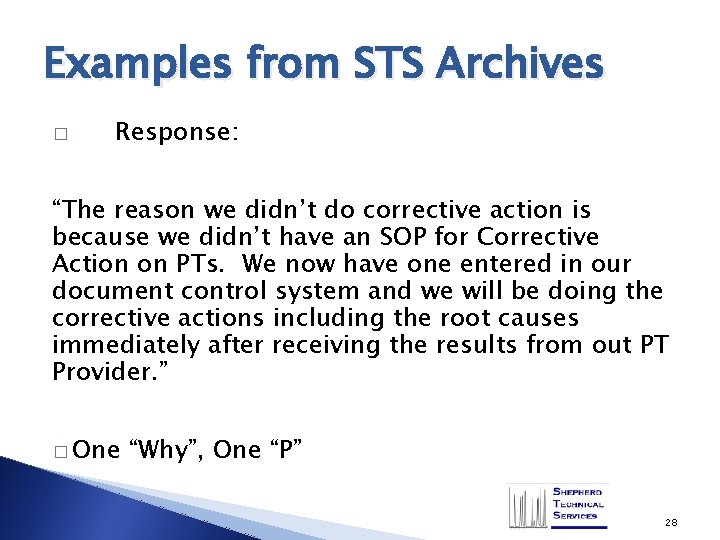
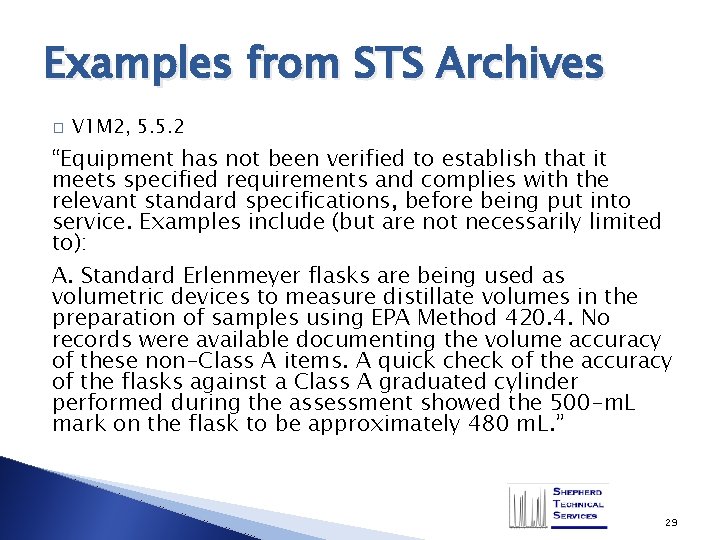
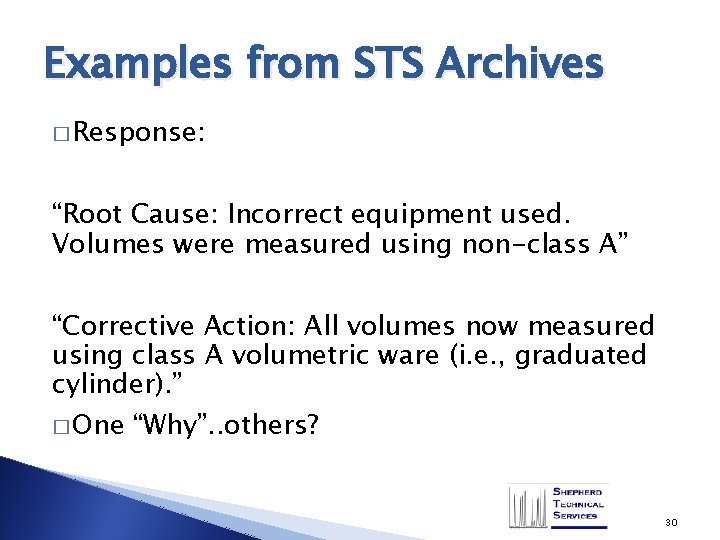
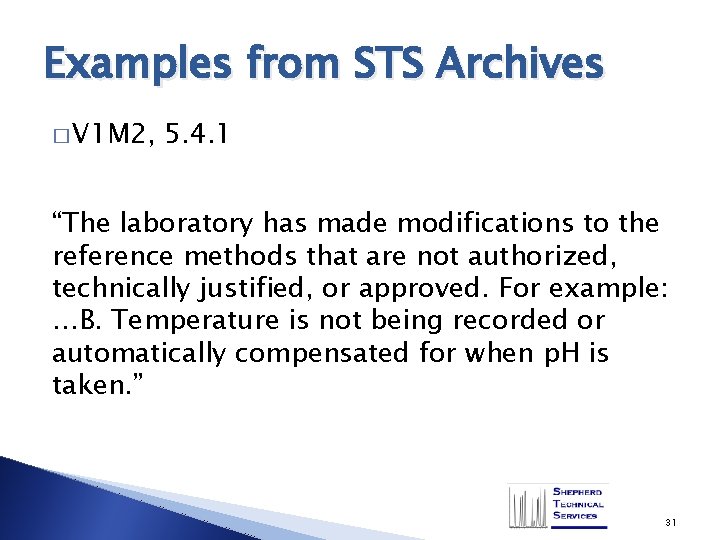
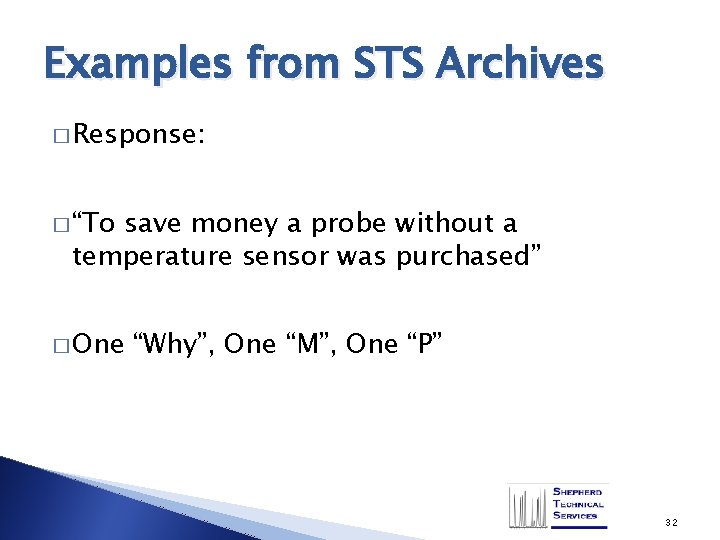
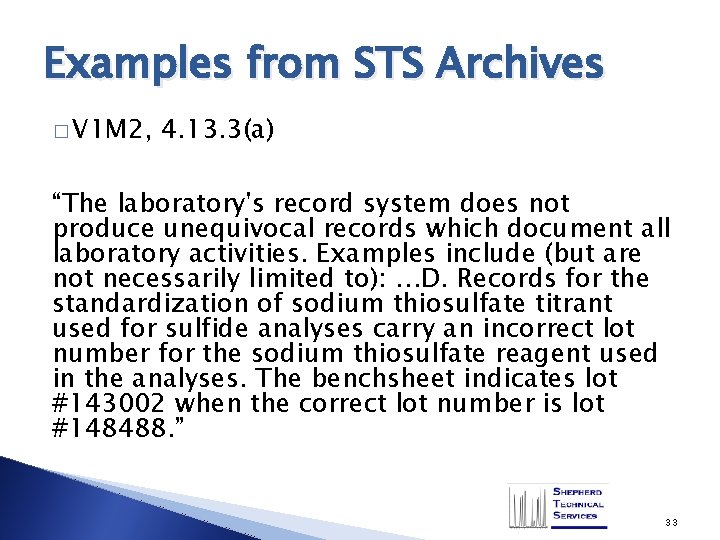
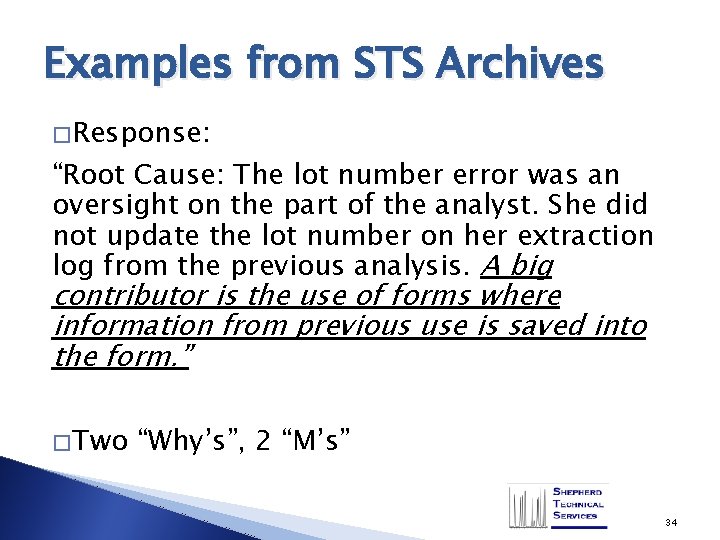
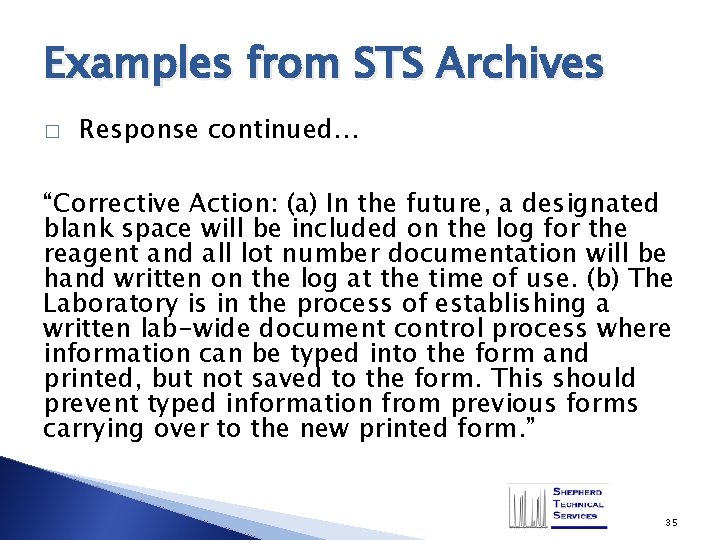
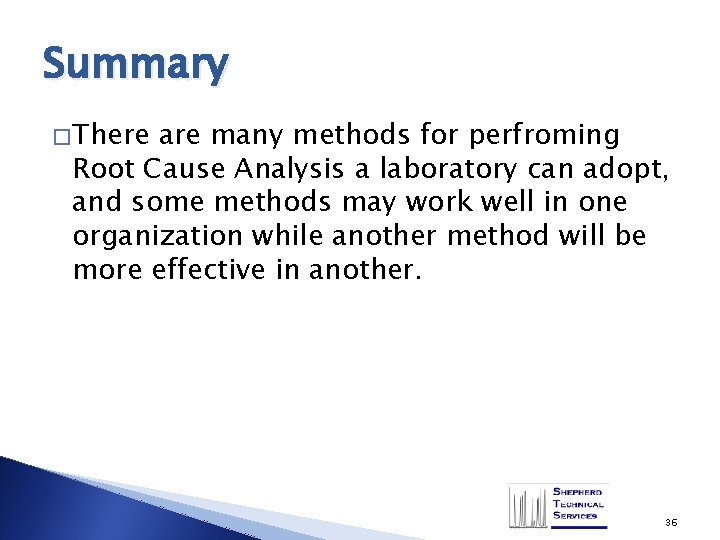
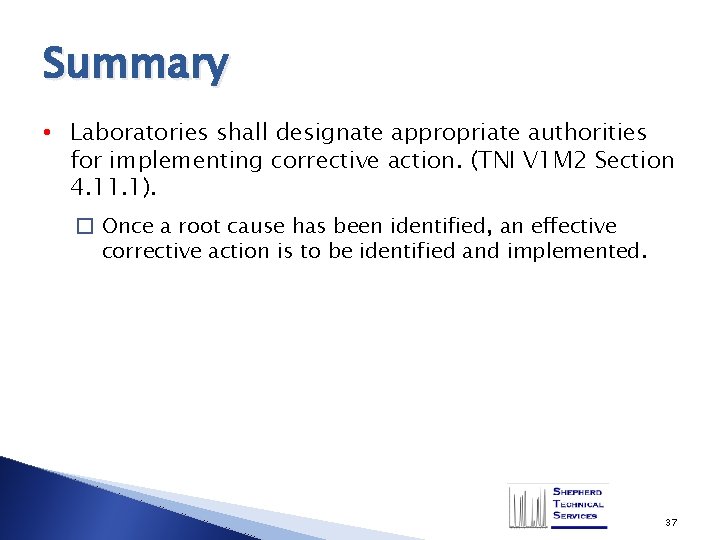
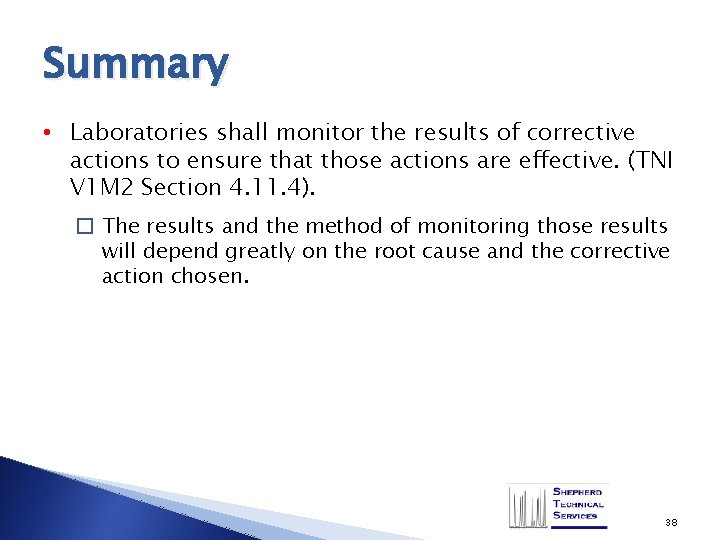
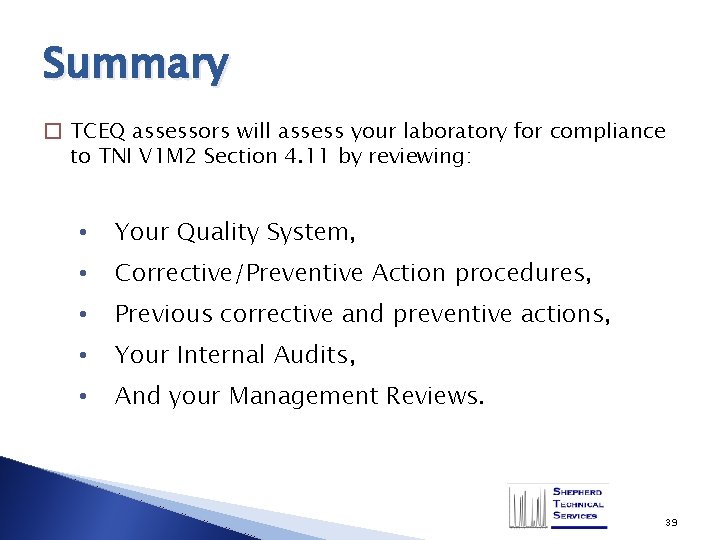
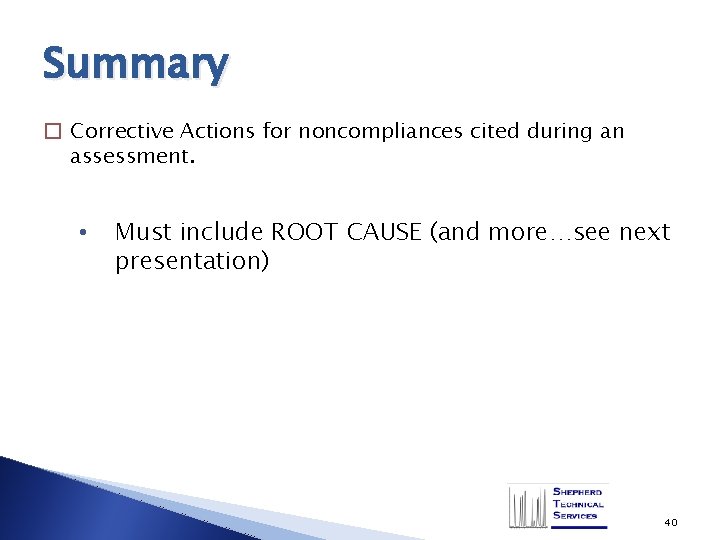

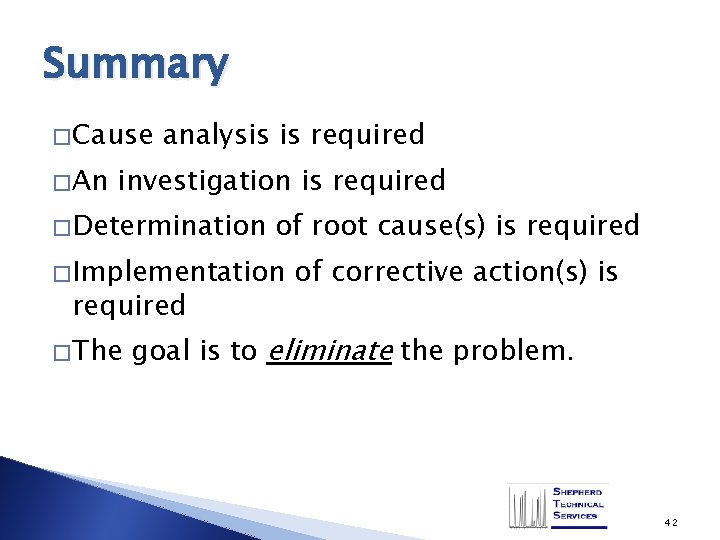
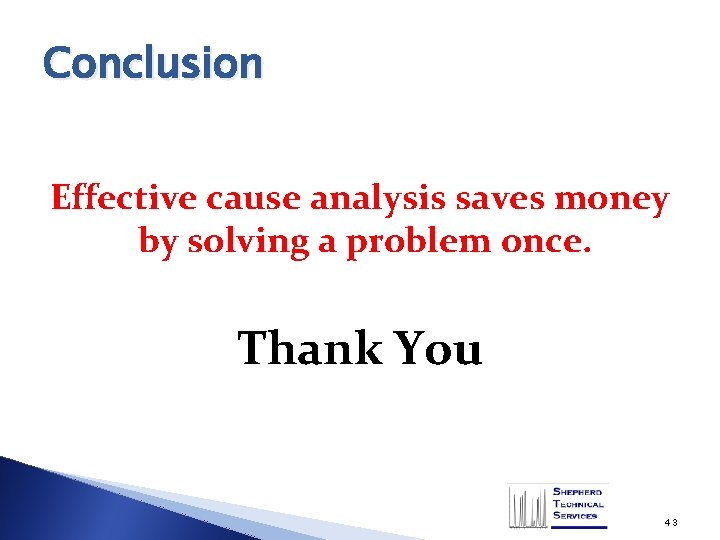
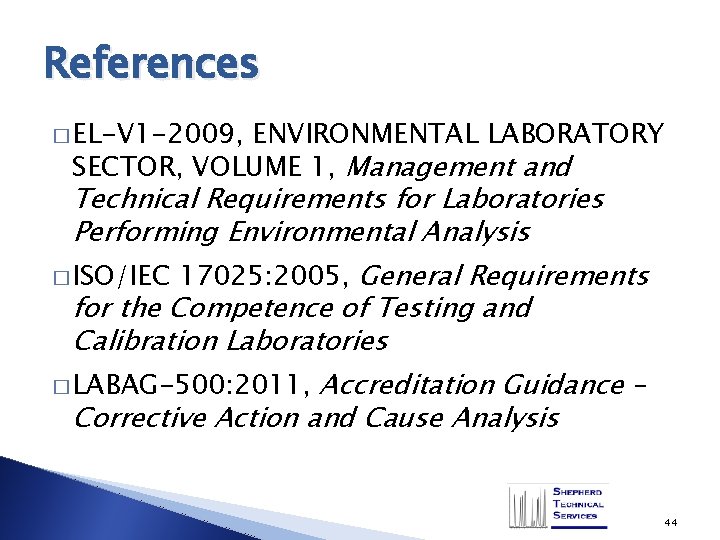
- Slides: 44
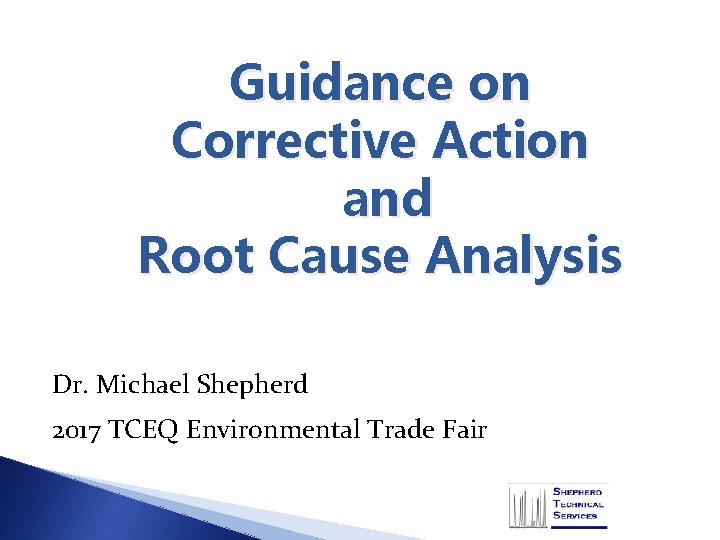
Guidance on Corrective Action and Root Cause Analysis Dr. Michael Shepherd 2017 TCEQ Environmental Trade Fair
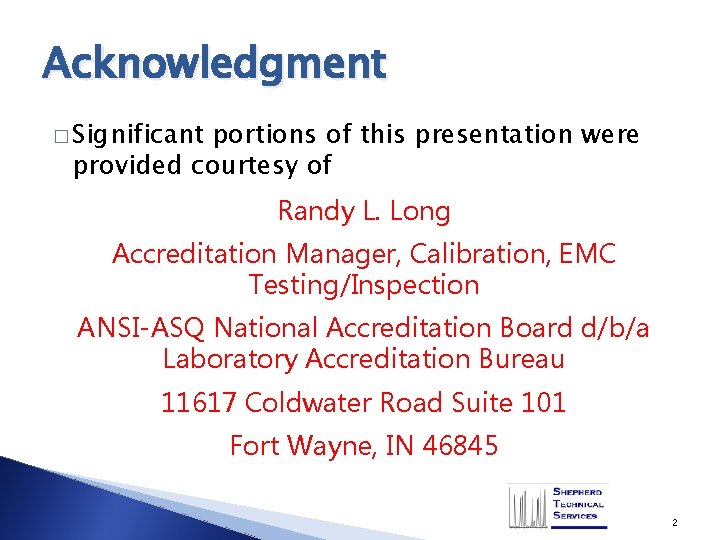
Acknowledgment � Significant portions of this presentation were provided courtesy of Randy L. Long Accreditation Manager, Calibration, EMC Testing/Inspection ANSI-ASQ National Accreditation Board d/b/a Laboratory Accreditation Bureau 11617 Coldwater Road Suite 101 Fort Wayne, IN 46845 2
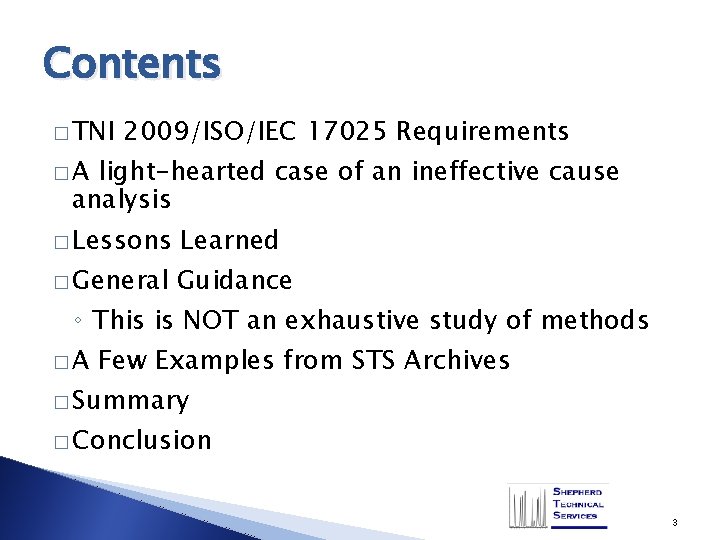
Contents � TNI 2009/ISO/IEC 17025 Requirements �A light-hearted case of an ineffective cause analysis � Lessons Learned � General Guidance ◦ This is NOT an exhaustive study of methods �A Few Examples from STS Archives � Summary � Conclusion 3
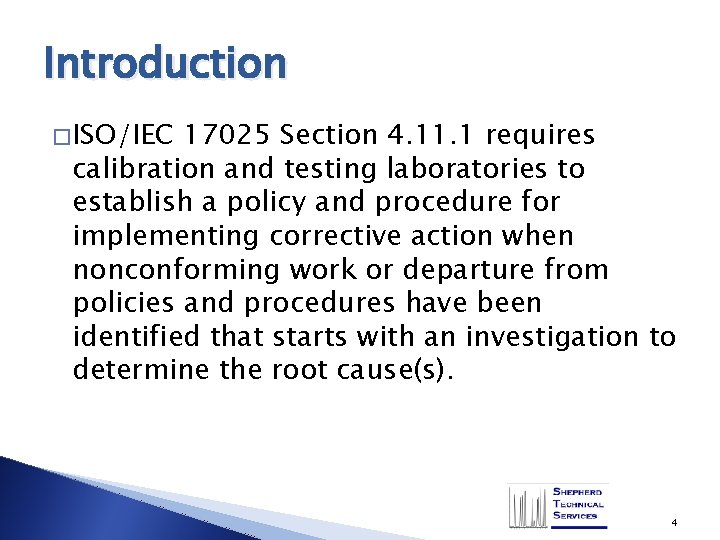
Introduction � ISO/IEC 17025 Section 4. 11. 1 requires calibration and testing laboratories to establish a policy and procedure for implementing corrective action when nonconforming work or departure from policies and procedures have been identified that starts with an investigation to determine the root cause(s). 4
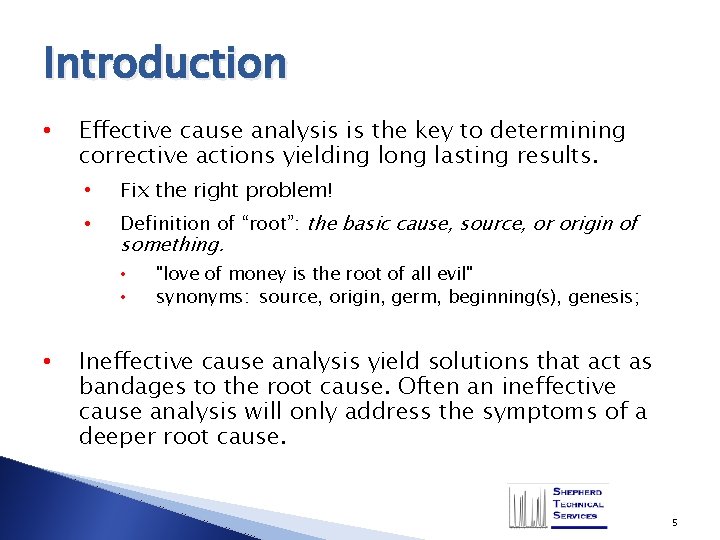
Introduction • Effective cause analysis is the key to determining corrective actions yielding long lasting results. • Fix the right problem! • Definition of “root”: the basic cause, source, or origin of something. • • • "love of money is the root of all evil" synonyms: source, origin, germ, beginning(s), genesis; Ineffective cause analysis yield solutions that act as bandages to the root cause. Often an ineffective cause analysis will only address the symptoms of a deeper root cause. 5
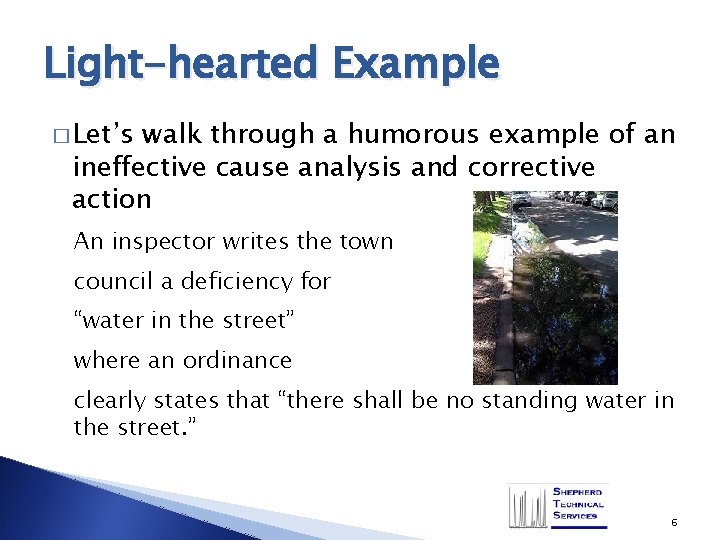
Light-hearted Example � Let’s walk through a humorous example of an ineffective cause analysis and corrective action An inspector writes the town council a deficiency for “water in the street” where an ordinance clearly states that “there shall be no standing water in the street. ” 6
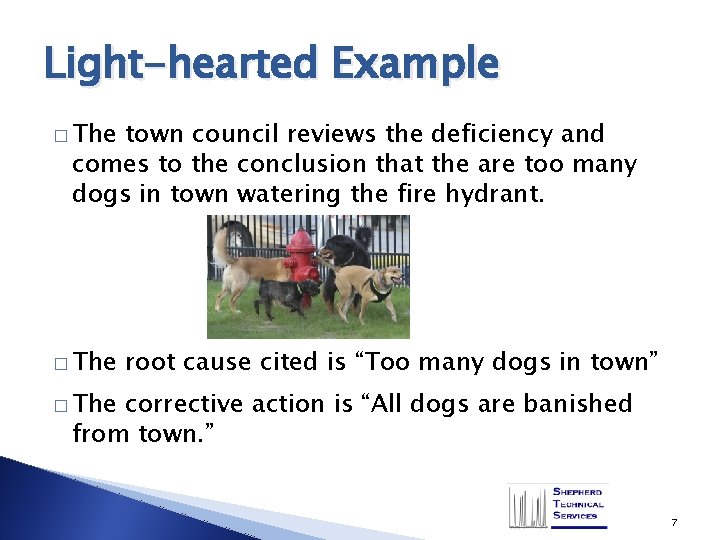
Light-hearted Example � The town council reviews the deficiency and comes to the conclusion that the are too many dogs in town watering the fire hydrant. � The root cause cited is “Too many dogs in town” � The corrective action is “All dogs are banished from town. ” 7
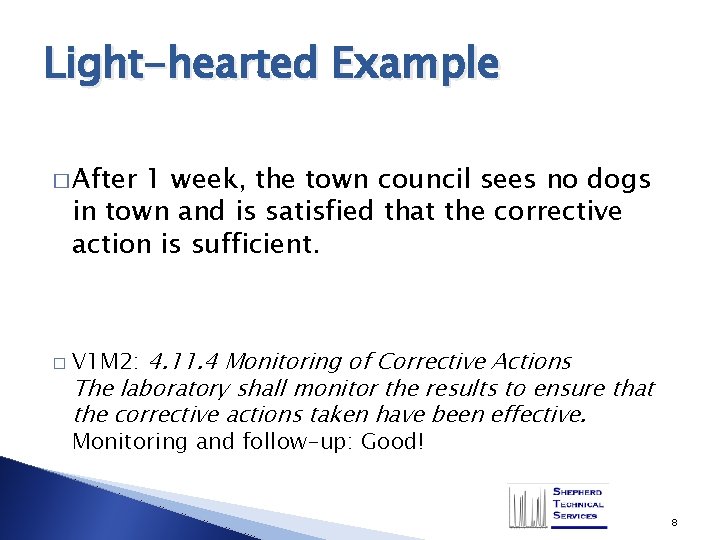
Light-hearted Example � After 1 week, the town council sees no dogs in town and is satisfied that the corrective action is sufficient. � V 1 M 2: 4. 11. 4 Monitoring of Corrective Actions The laboratory shall monitor the results to ensure that the corrective actions taken have been effective. Monitoring and follow-up: Good! 8
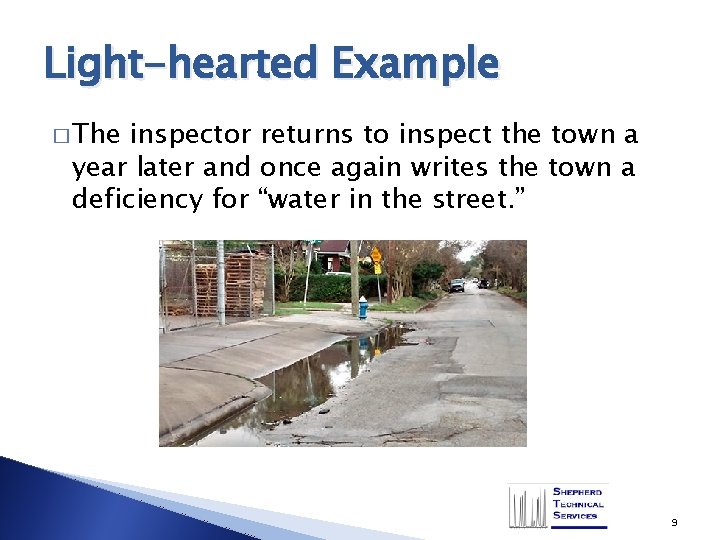
Light-hearted Example � The inspector returns to inspect the town a year later and once again writes the town a deficiency for “water in the street. ” 9
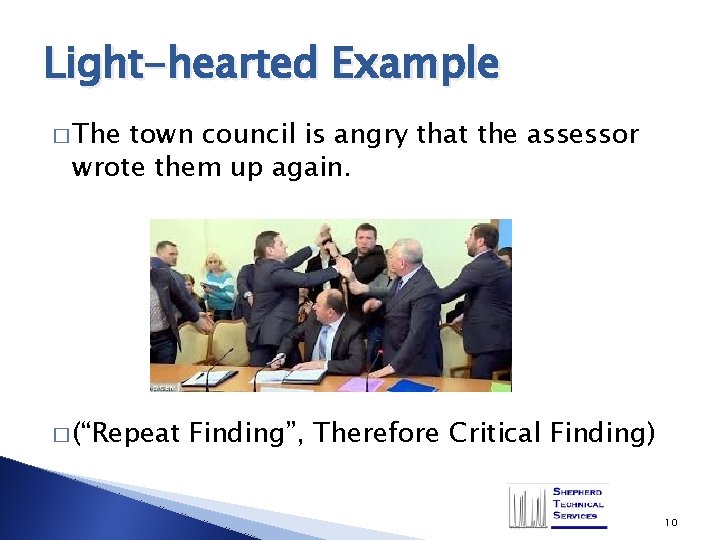
Light-hearted Example � The town council is angry that the assessor wrote them up again. � (“Repeat Finding”, Therefore Critical Finding) 10
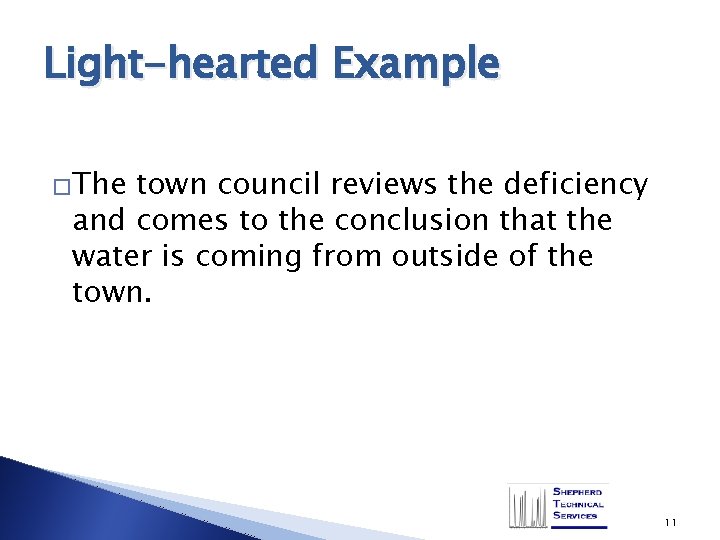
Light-hearted Example �The town council reviews the deficiency and comes to the conclusion that the water is coming from outside of the town. 11
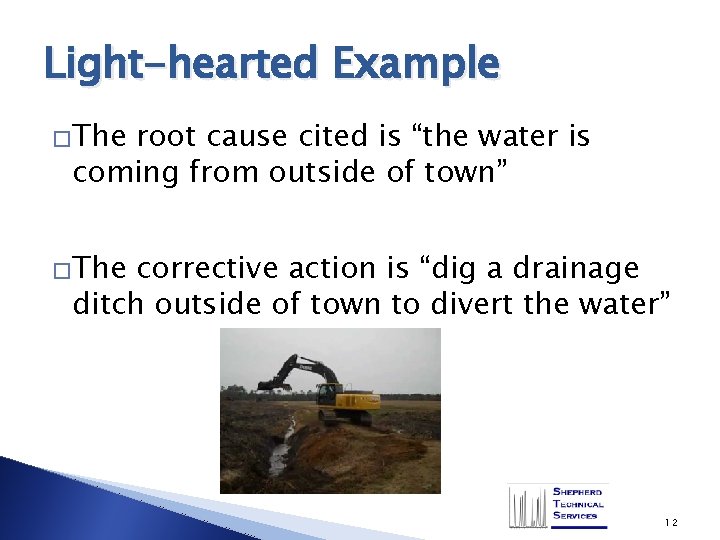
Light-hearted Example �The root cause cited is “the water is coming from outside of town” �The corrective action is “dig a drainage ditch outside of town to divert the water” 12
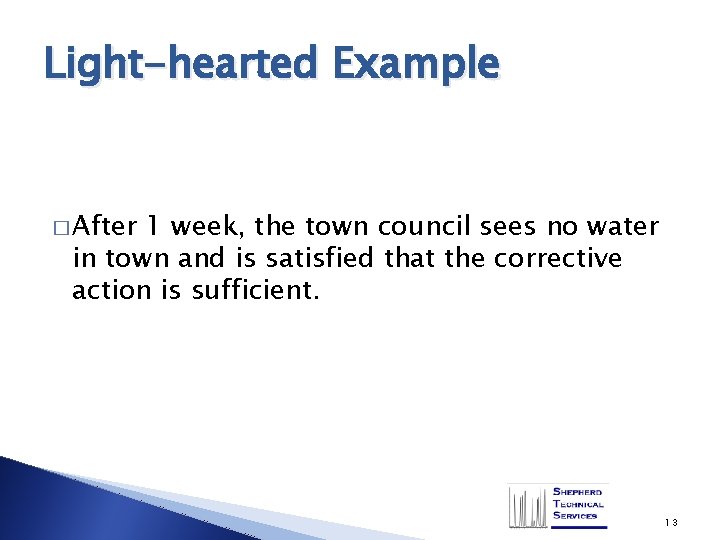
Light-hearted Example � After 1 week, the town council sees no water in town and is satisfied that the corrective action is sufficient. 13
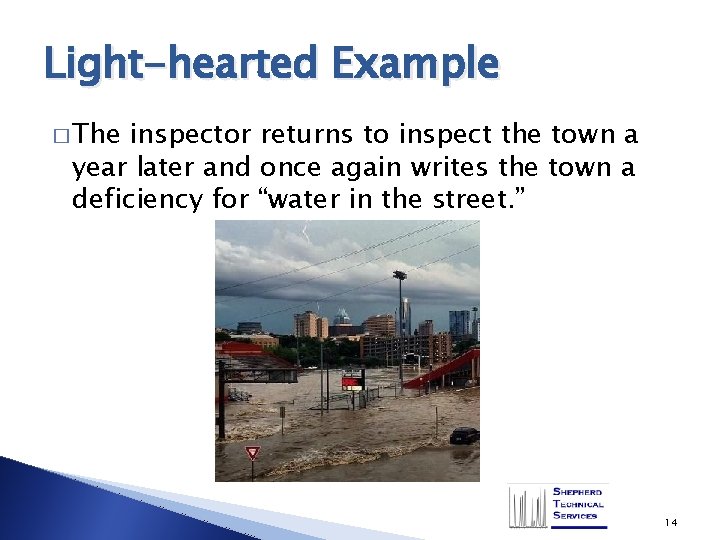
Light-hearted Example � The inspector returns to inspect the town a year later and once again writes the town a deficiency for “water in the street. ” 14
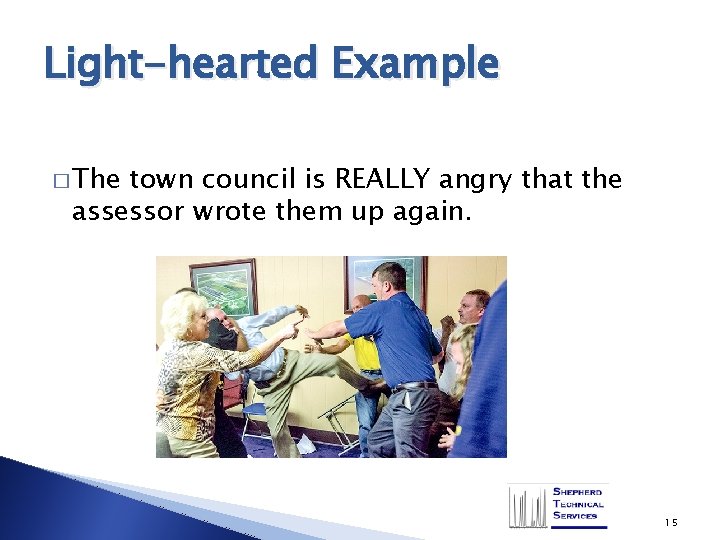
Light-hearted Example � The town council is REALLY angry that the assessor wrote them up again. 15
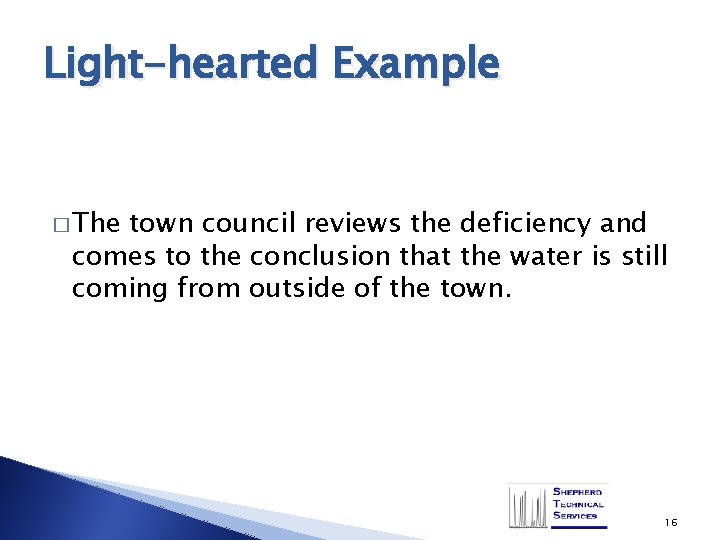
Light-hearted Example � The town council reviews the deficiency and comes to the conclusion that the water is still coming from outside of the town. 16
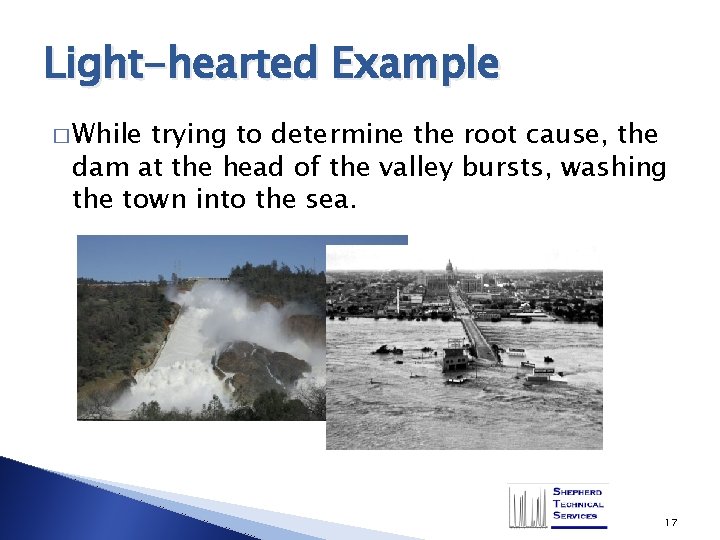
Light-hearted Example � While trying to determine the root cause, the dam at the head of the valley bursts, washing the town into the sea. 17
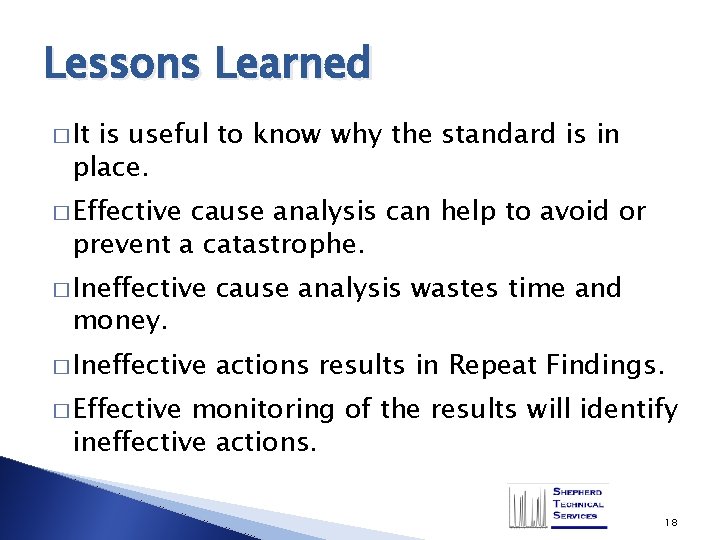
Lessons Learned � It is useful to know why the standard is in place. � Effective cause analysis can help to avoid or prevent a catastrophe. � Ineffective cause analysis wastes time and � Ineffective actions results in Repeat Findings. money. � Effective monitoring of the results will identify ineffective actions. 18
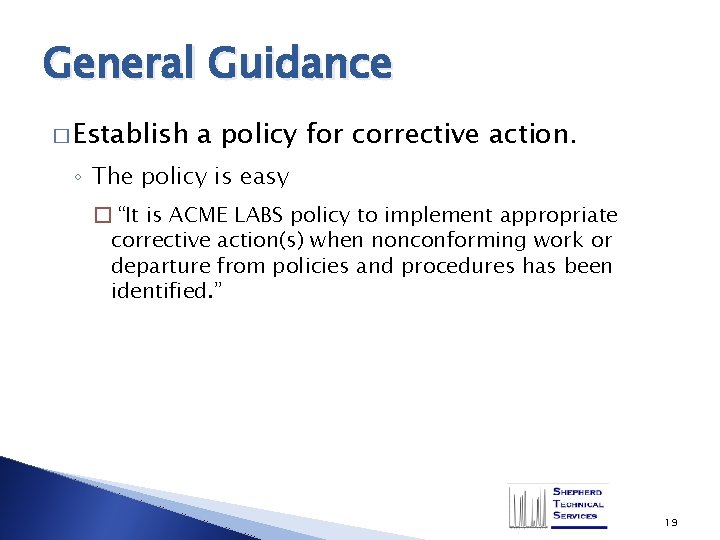
General Guidance � Establish a policy for corrective action. ◦ The policy is easy � “It is ACME LABS policy to implement appropriate corrective action(s) when nonconforming work or departure from policies and procedures has been identified. ” 19
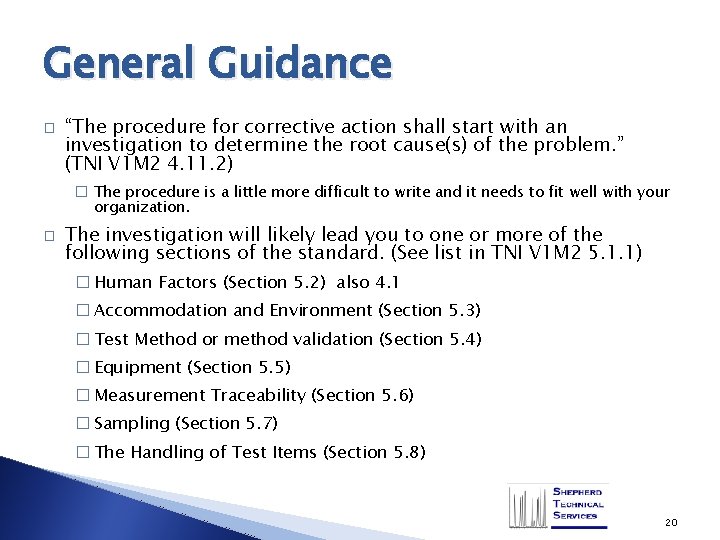
General Guidance � “The procedure for corrective action shall start with an investigation to determine the root cause(s) of the problem. ” (TNI V 1 M 2 4. 11. 2) � The procedure is a little more difficult to write and it needs to fit well with your organization. � The investigation will likely lead you to one or more of the following sections of the standard. (See list in TNI V 1 M 2 5. 1. 1) � Human Factors (Section 5. 2) also 4. 1 � Accommodation and Environment (Section 5. 3) � Test Method or method validation (Section 5. 4) � Equipment (Section 5. 5) � Measurement Traceability (Section 5. 6) � Sampling (Section 5. 7) � The Handling of Test Items (Section 5. 8) 20
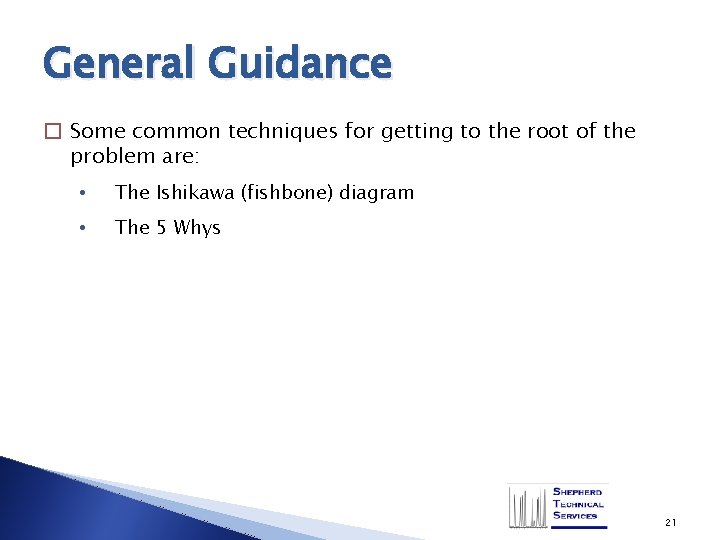
General Guidance � Some common techniques for getting to the root of the problem are: • The Ishikawa (fishbone) diagram • The 5 Whys 21
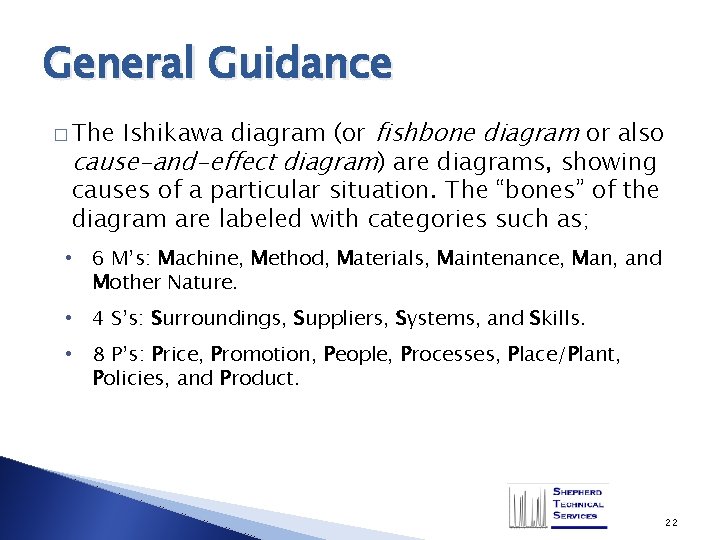
General Guidance Ishikawa diagram (or fishbone diagram or also cause-and-effect diagram) are diagrams, showing causes of a particular situation. The “bones” of the diagram are labeled with categories such as; � The • 6 M’s: Machine, Method, Materials, Maintenance, Man, and Mother Nature. • 4 S’s: Surroundings, Suppliers, Systems, and Skills. • 8 P’s: Price, Promotion, People, Processes, Place/Plant, Policies, and Product. 22
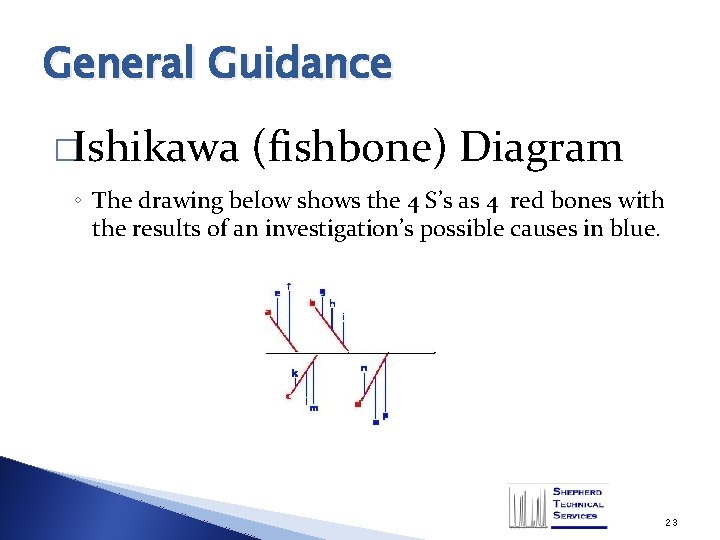
General Guidance �Ishikawa (fishbone) Diagram ◦ The drawing below shows the 4 S’s as 4 red bones with the results of an investigation’s possible causes in blue. 23
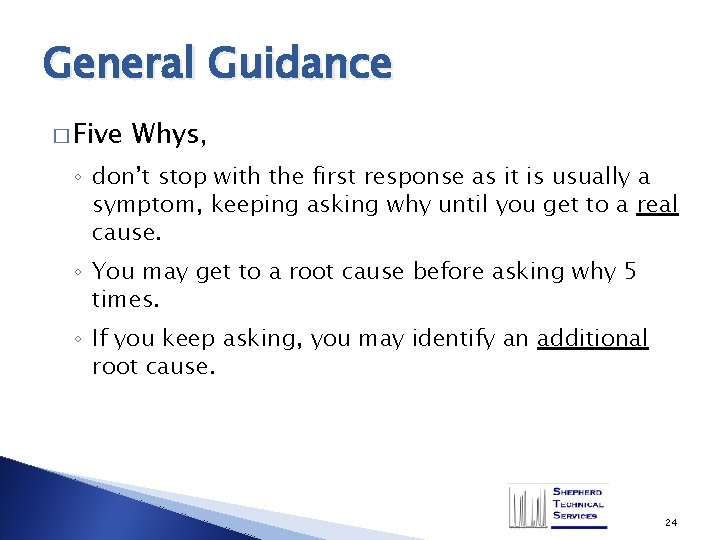
General Guidance � Five Whys, ◦ don’t stop with the first response as it is usually a symptom, keeping asking why until you get to a real cause. ◦ You may get to a root cause before asking why 5 times. ◦ If you keep asking, you may identify an additional root cause. 24
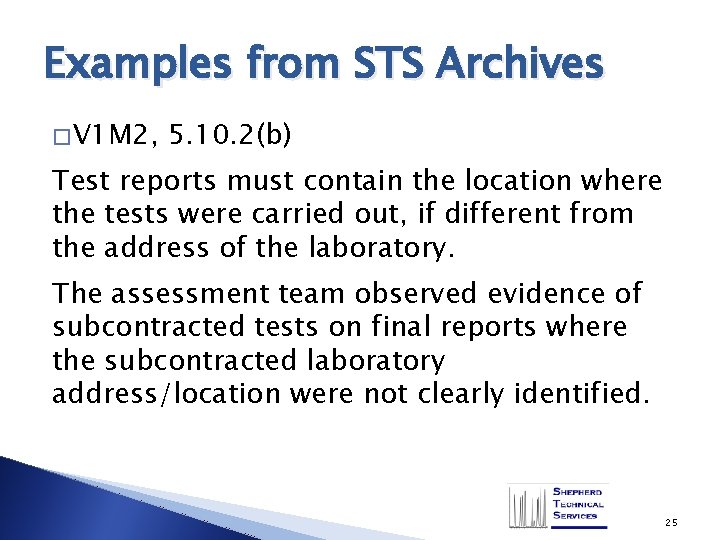
Examples from STS Archives � V 1 M 2, 5. 10. 2(b) Test reports must contain the location where the tests were carried out, if different from the address of the laboratory. The assessment team observed evidence of subcontracted tests on final reports where the subcontracted laboratory address/location were not clearly identified. 25
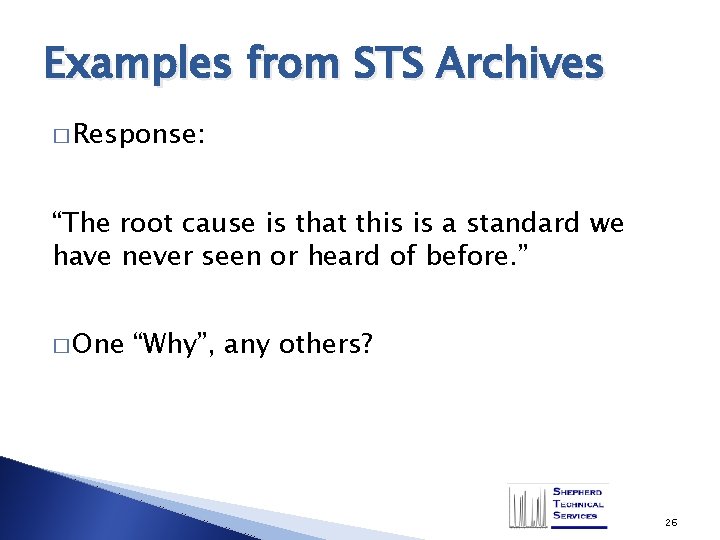
Examples from STS Archives � Response: “The root cause is that this is a standard we have never seen or heard of before. ” � One “Why”, any others? 26
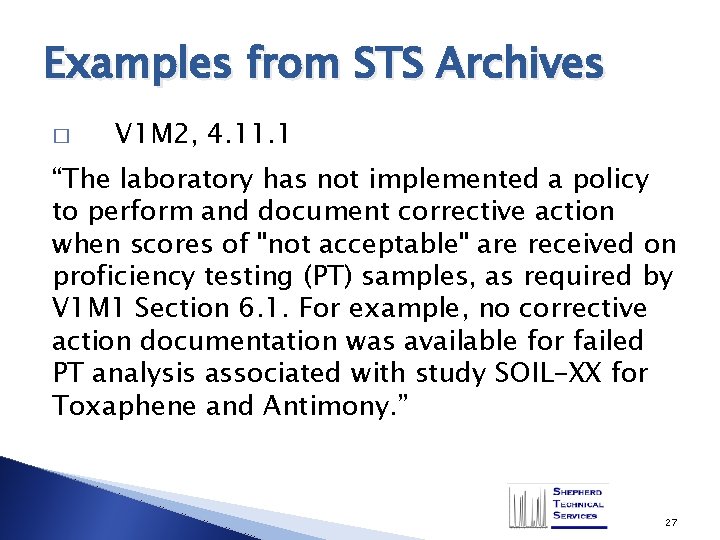
Examples from STS Archives � V 1 M 2, 4. 11. 1 “The laboratory has not implemented a policy to perform and document corrective action when scores of "not acceptable" are received on proficiency testing (PT) samples, as required by V 1 M 1 Section 6. 1. For example, no corrective action documentation was available for failed PT analysis associated with study SOIL-XX for Toxaphene and Antimony. ” 27
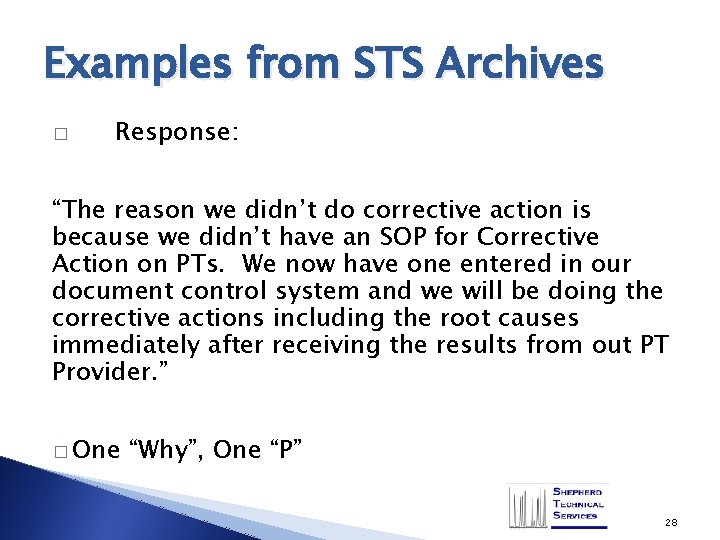
Examples from STS Archives � Response: “The reason we didn’t do corrective action is because we didn’t have an SOP for Corrective Action on PTs. We now have one entered in our document control system and we will be doing the corrective actions including the root causes immediately after receiving the results from out PT Provider. ” � One “Why”, One “P” 28
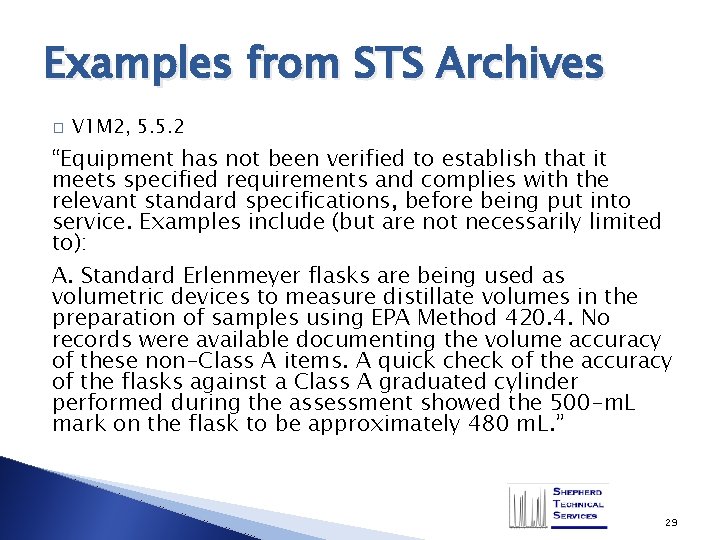
Examples from STS Archives � V 1 M 2, 5. 5. 2 “Equipment has not been verified to establish that it meets specified requirements and complies with the relevant standard specifications, before being put into service. Examples include (but are not necessarily limited to): A. Standard Erlenmeyer flasks are being used as volumetric devices to measure distillate volumes in the preparation of samples using EPA Method 420. 4. No records were available documenting the volume accuracy of these non-Class A items. A quick check of the accuracy of the flasks against a Class A graduated cylinder performed during the assessment showed the 500 -m. L mark on the flask to be approximately 480 m. L. ” 29
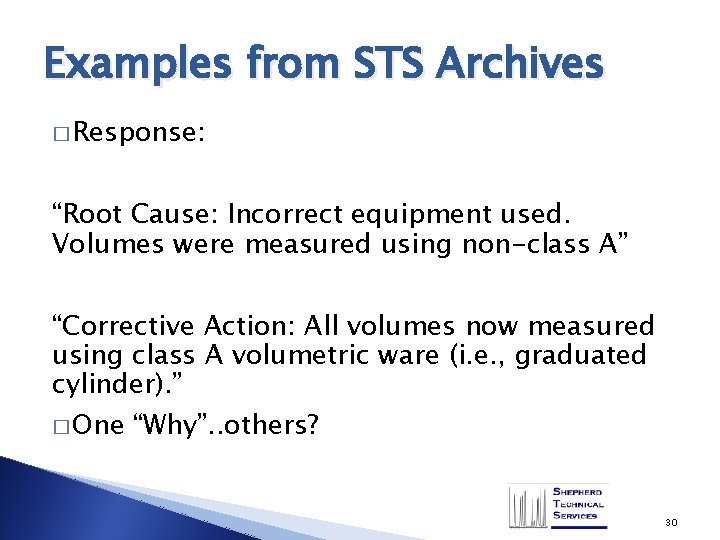
Examples from STS Archives � Response: “Root Cause: Incorrect equipment used. Volumes were measured using non-class A” “Corrective Action: All volumes now measured using class A volumetric ware (i. e. , graduated cylinder). ” � One “Why”. . others? 30
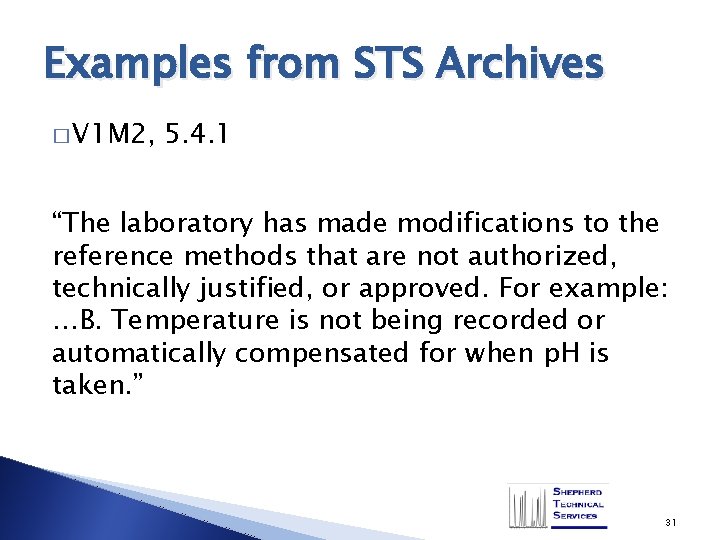
Examples from STS Archives � V 1 M 2, 5. 4. 1 “The laboratory has made modifications to the reference methods that are not authorized, technically justified, or approved. For example: …B. Temperature is not being recorded or automatically compensated for when p. H is taken. ” 31
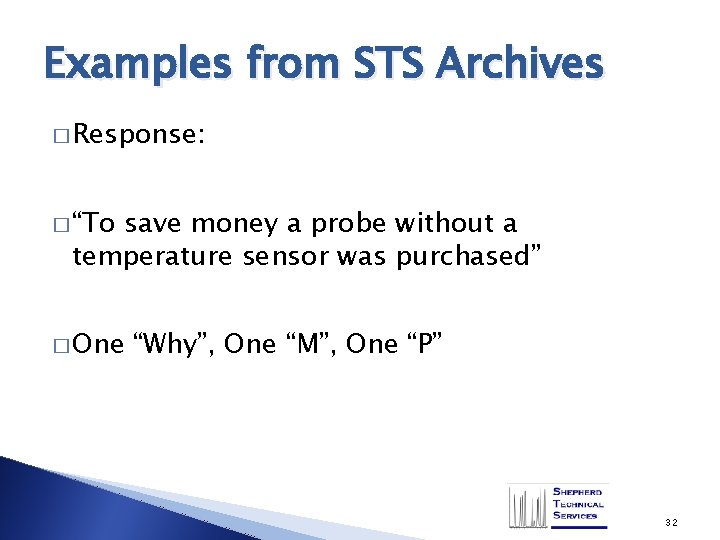
Examples from STS Archives � Response: � “To save money a probe without a temperature sensor was purchased” � One “Why”, One “M”, One “P” 32
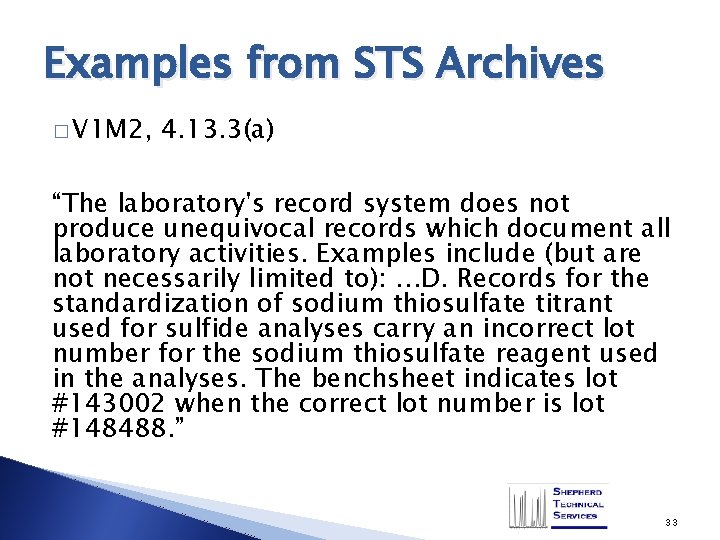
Examples from STS Archives � V 1 M 2, 4. 13. 3(a) “The laboratory's record system does not produce unequivocal records which document all laboratory activities. Examples include (but are not necessarily limited to): …D. Records for the standardization of sodium thiosulfate titrant used for sulfide analyses carry an incorrect lot number for the sodium thiosulfate reagent used in the analyses. The benchsheet indicates lot #143002 when the correct lot number is lot #148488. ” 33
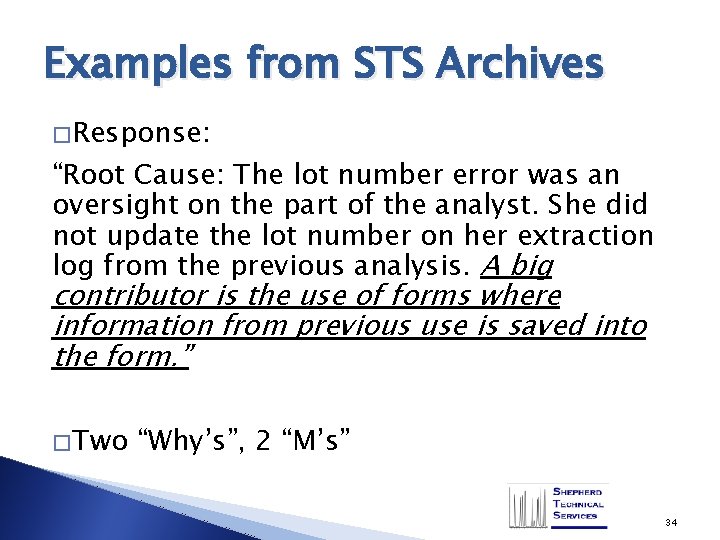
Examples from STS Archives � Response: “Root Cause: The lot number error was an oversight on the part of the analyst. She did not update the lot number on her extraction log from the previous analysis. A big contributor is the use of forms where information from previous use is saved into the form. ” � Two “Why’s”, 2 “M’s” 34
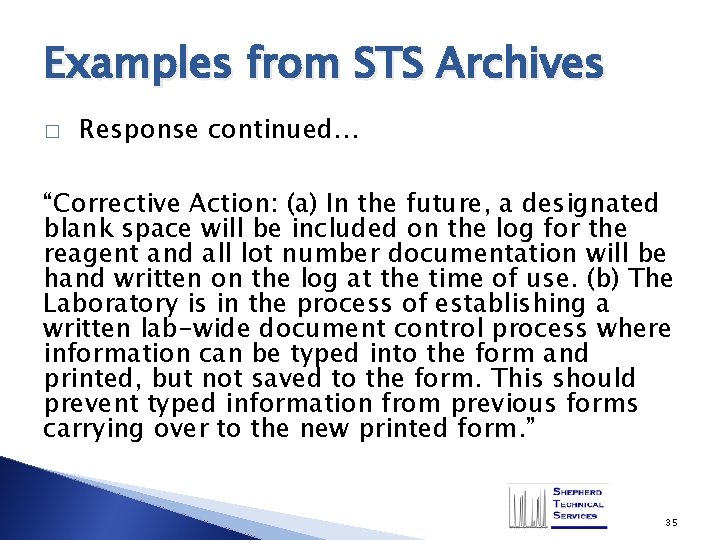
Examples from STS Archives � Response continued… “Corrective Action: (a) In the future, a designated blank space will be included on the log for the reagent and all lot number documentation will be hand written on the log at the time of use. (b) The Laboratory is in the process of establishing a written lab-wide document control process where information can be typed into the form and printed, but not saved to the form. This should prevent typed information from previous forms carrying over to the new printed form. ” 35
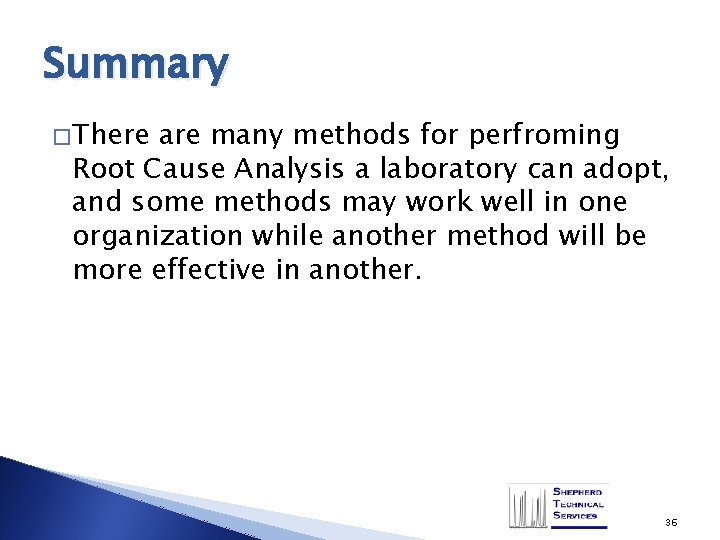
Summary � There are many methods for perfroming Root Cause Analysis a laboratory can adopt, and some methods may work well in one organization while another method will be more effective in another. 36
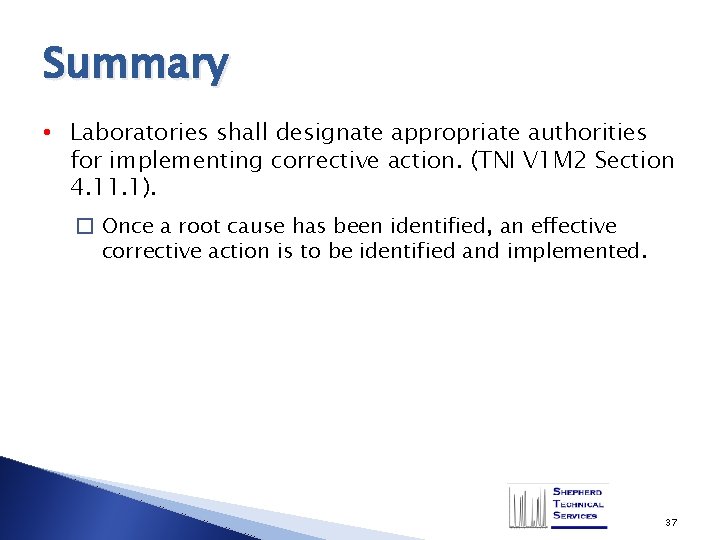
Summary • Laboratories shall designate appropriate authorities for implementing corrective action. (TNI V 1 M 2 Section 4. 11. 1). � Once a root cause has been identified, an effective corrective action is to be identified and implemented. 37
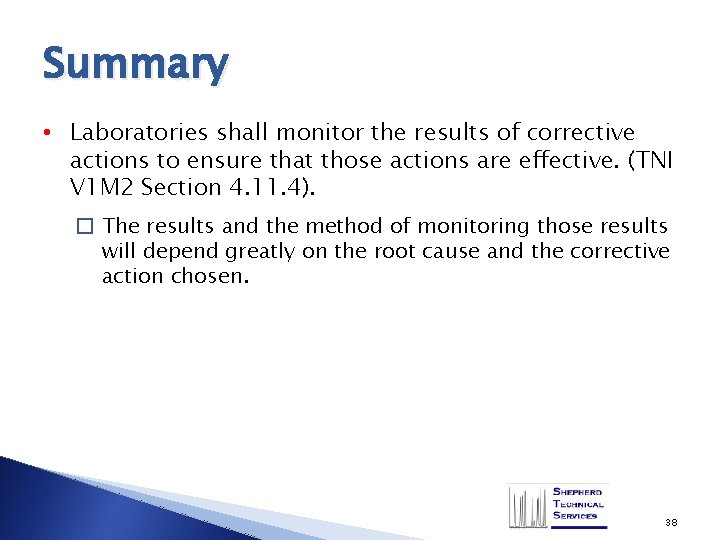
Summary • Laboratories shall monitor the results of corrective actions to ensure that those actions are effective. (TNI V 1 M 2 Section 4. 11. 4). � The results and the method of monitoring those results will depend greatly on the root cause and the corrective action chosen. 38
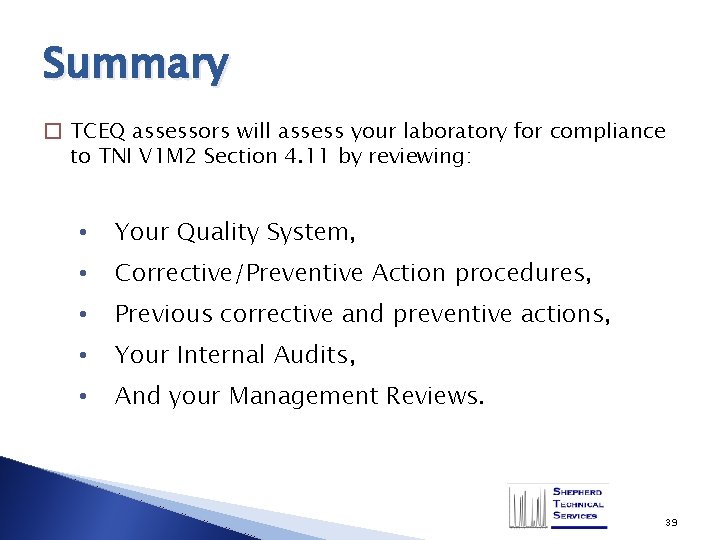
Summary � TCEQ assessors will assess your laboratory for compliance to TNI V 1 M 2 Section 4. 11 by reviewing: • Your Quality System, • Corrective/Preventive Action procedures, • Previous corrective and preventive actions, • Your Internal Audits, • And your Management Reviews. 39
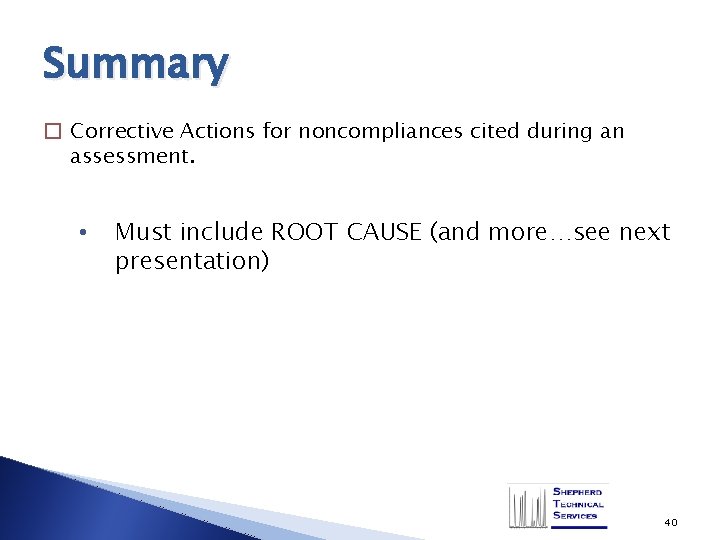
Summary � Corrective Actions for noncompliances cited during an assessment. • Must include ROOT CAUSE (and more…see next presentation) 40

Summary � TCEQ staff, during the technical review(s) of your laboratory’s assessment, assesses compliance by evaluating the evidence submitted in response to non-compliances for: ◦ corrective actions with identified root causes, ◦ effective corrective actions which seek to prevent the cited noncompliance from recurring, � During subsequent assessments, compliance is evaluated by: ◦ evidence of the corrective action, and ◦ verification of the effectiveness of the corrective action. 41
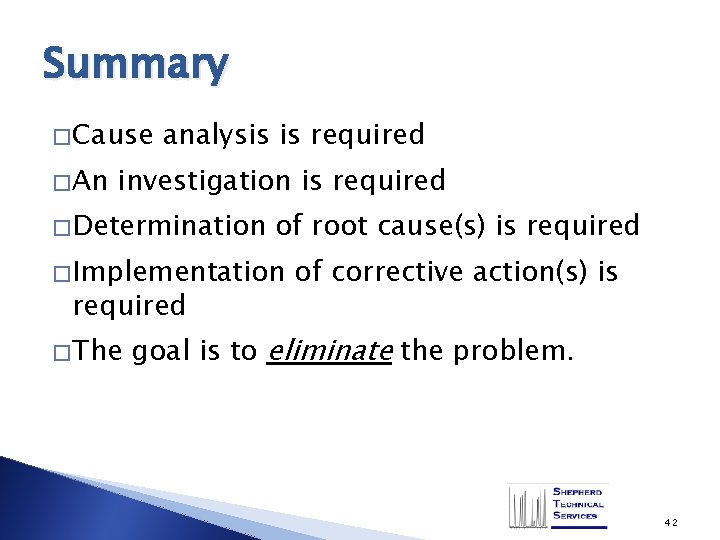
Summary � Cause � An analysis is required investigation is required � Determination of root cause(s) is required � Implementation required � The of corrective action(s) is goal is to eliminate the problem. 42
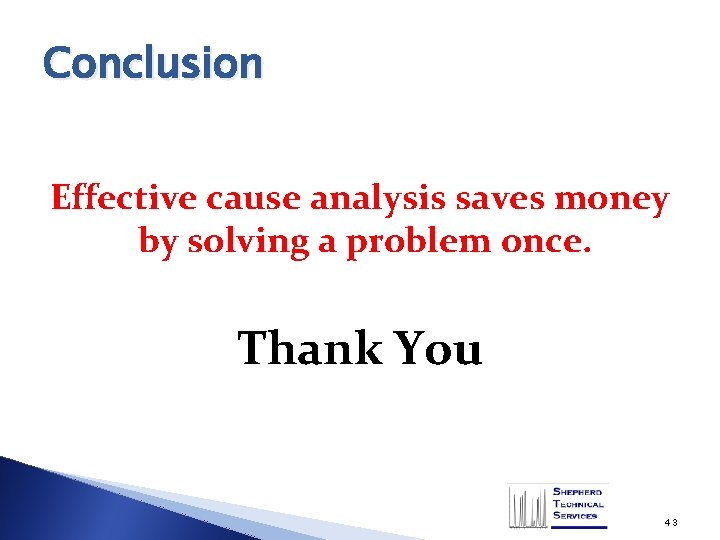
Conclusion Effective cause analysis saves money by solving a problem once. Thank You 43
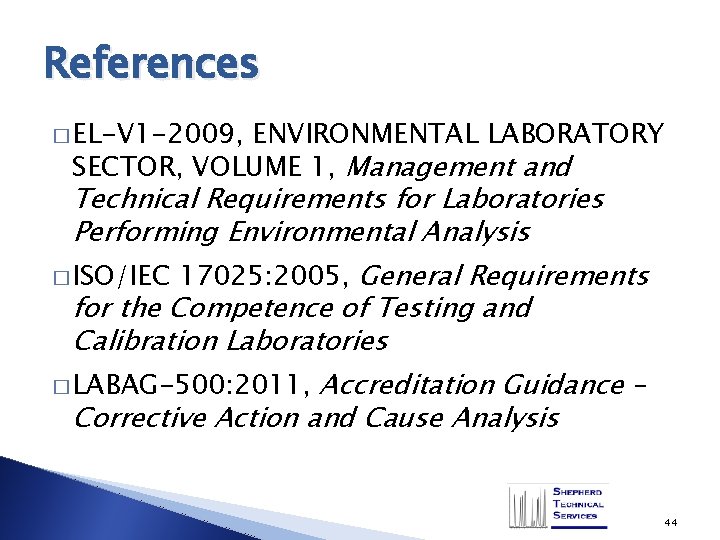
References � EL-V 1 -2009, ENVIRONMENTAL LABORATORY SECTOR, VOLUME 1, Management and Technical Requirements for Laboratories Performing Environmental Analysis � ISO/IEC 17025: 2005, General Requirements for the Competence of Testing and Calibration Laboratories Accreditation Guidance – Corrective Action and Cause Analysis � LABAG-500: 2011, 44