Full Mission Simulation Report Temple University Fred Avery
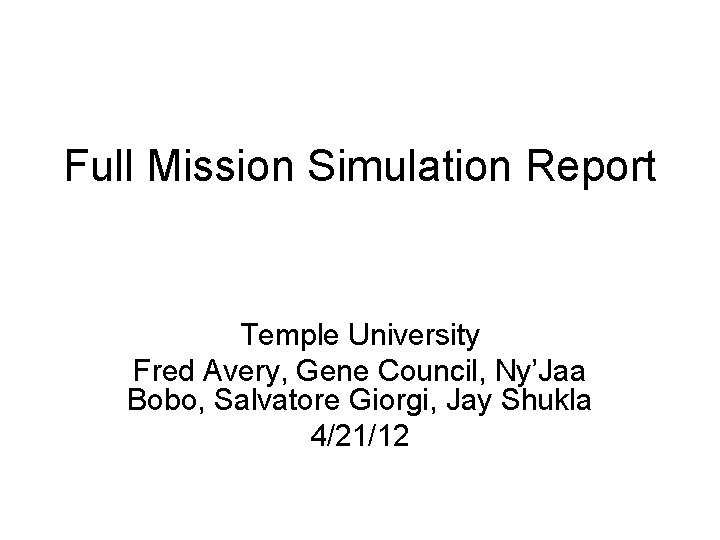
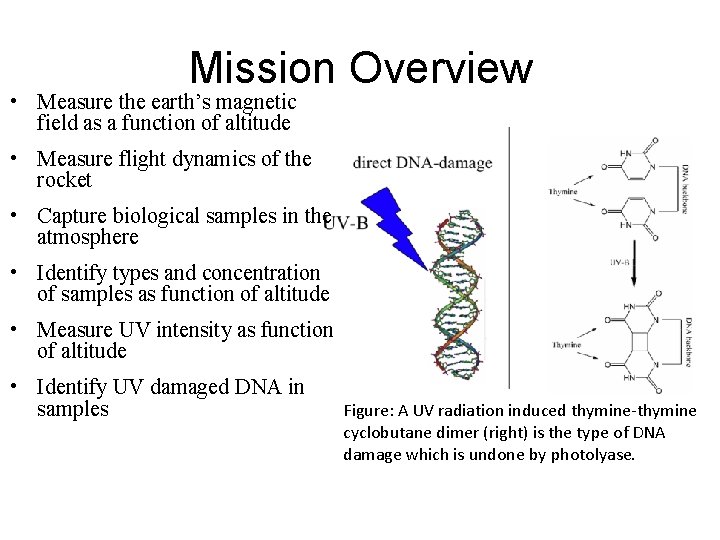
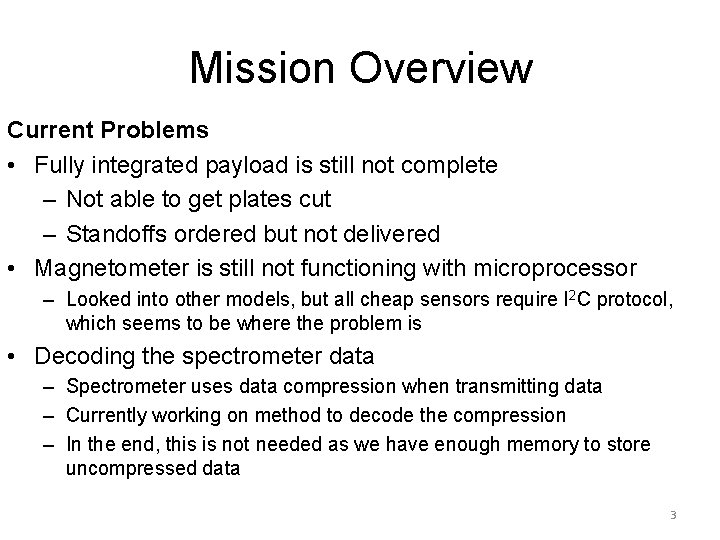

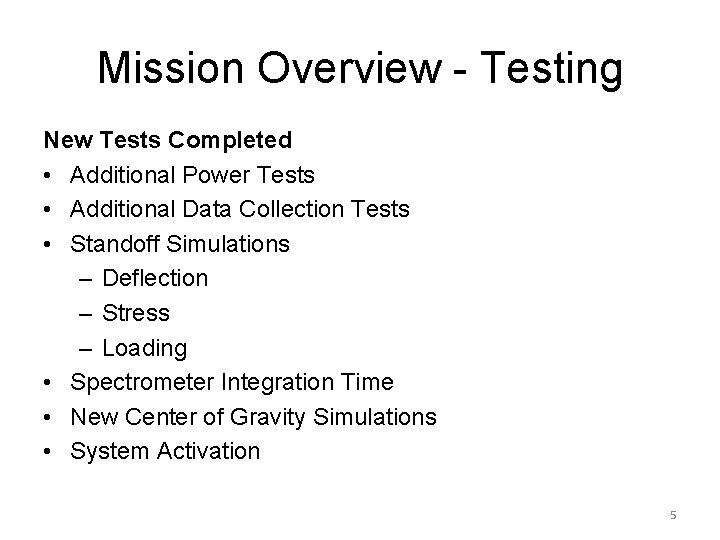
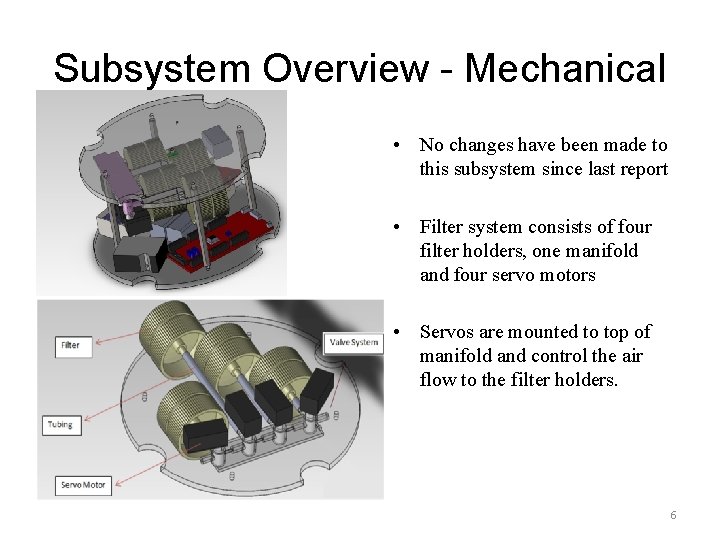
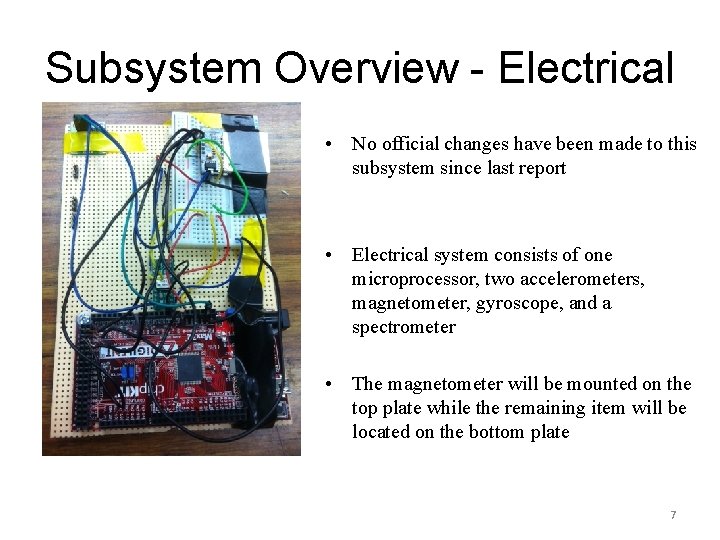
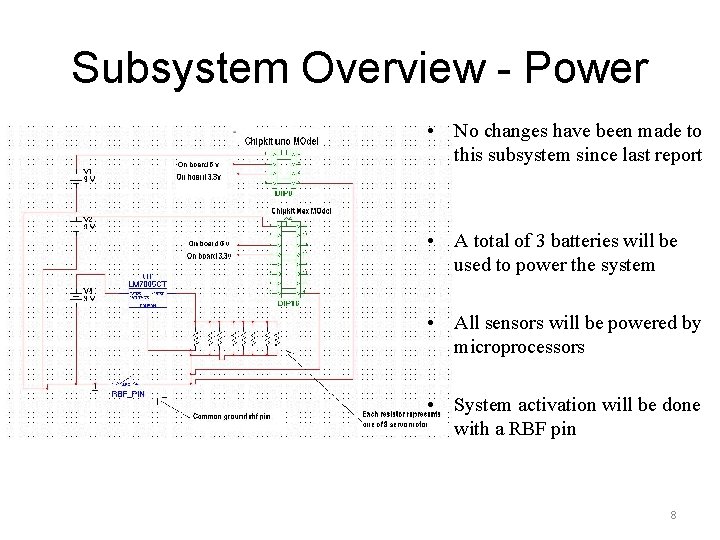
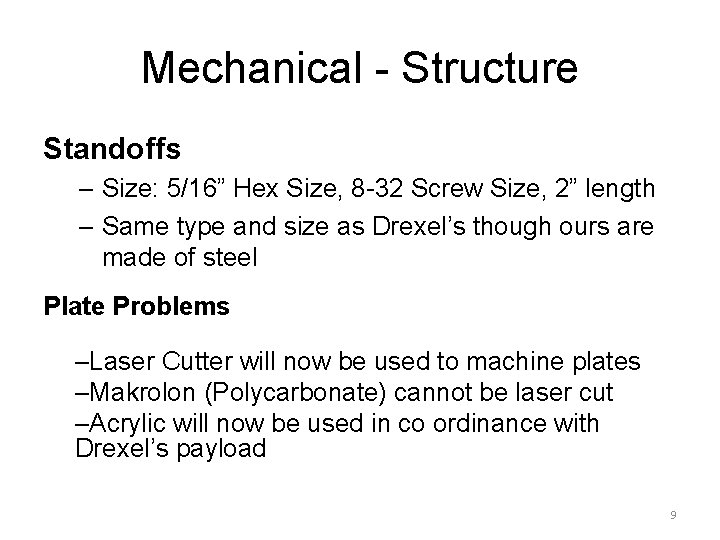
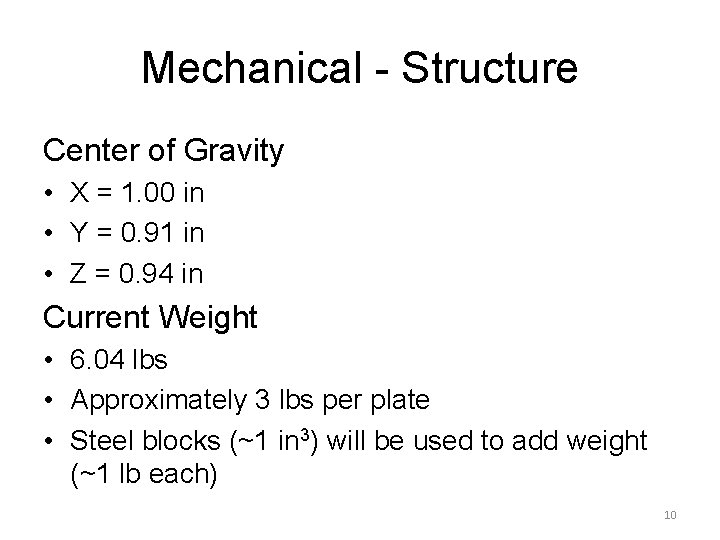
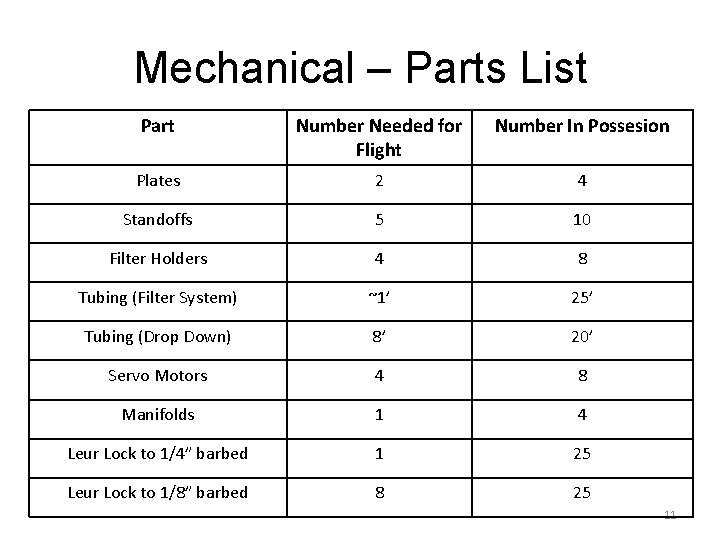
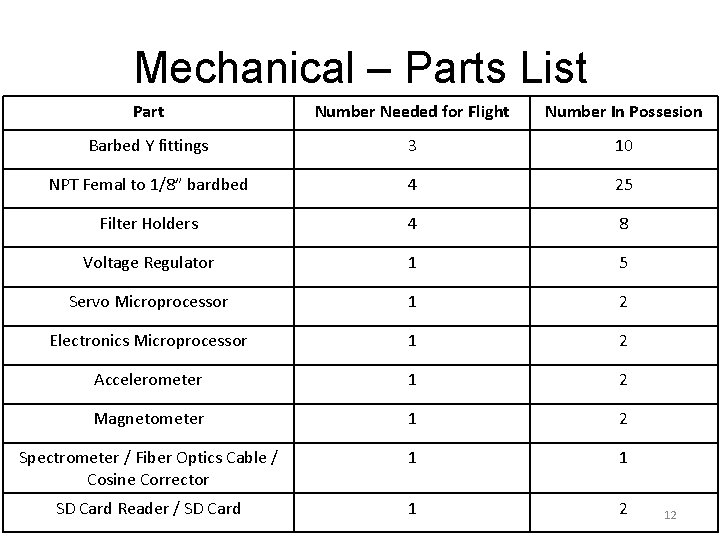
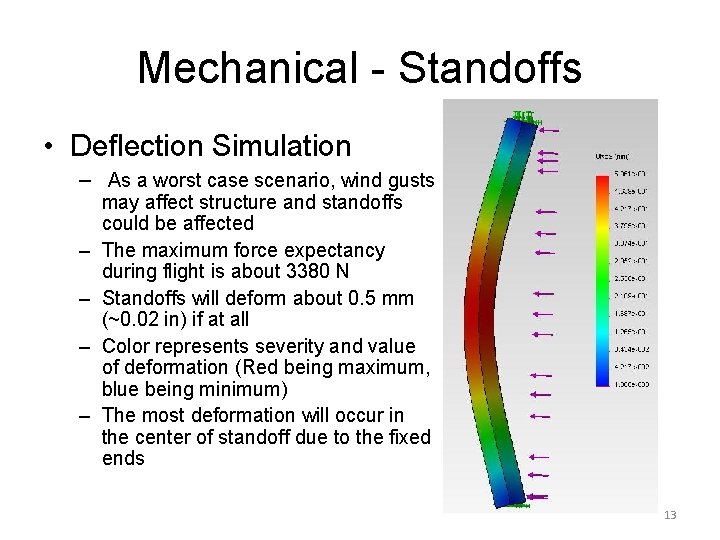
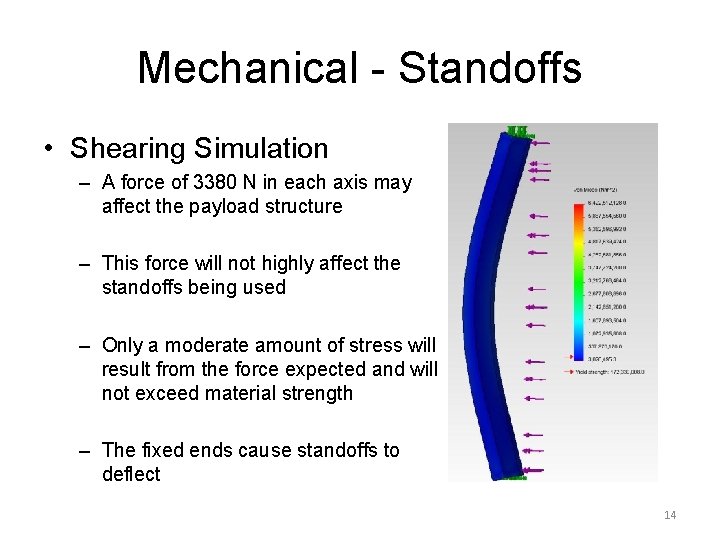
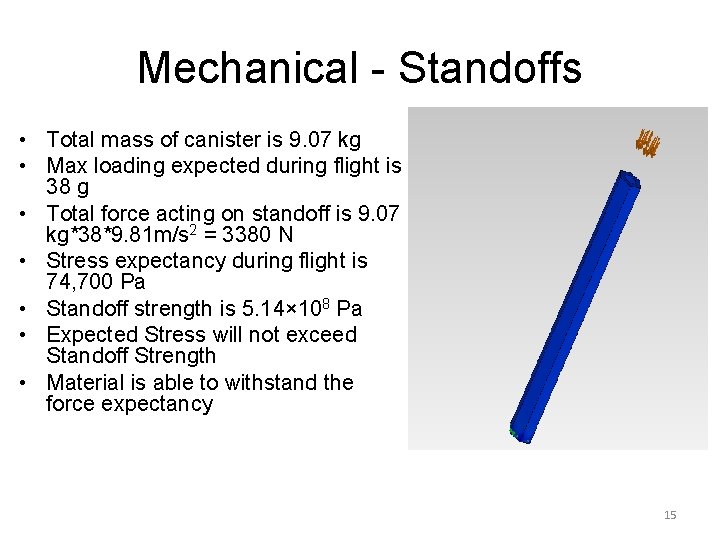
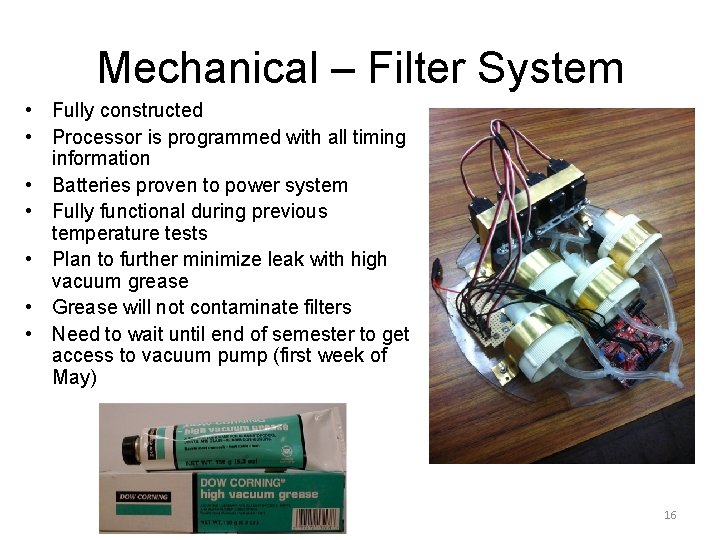
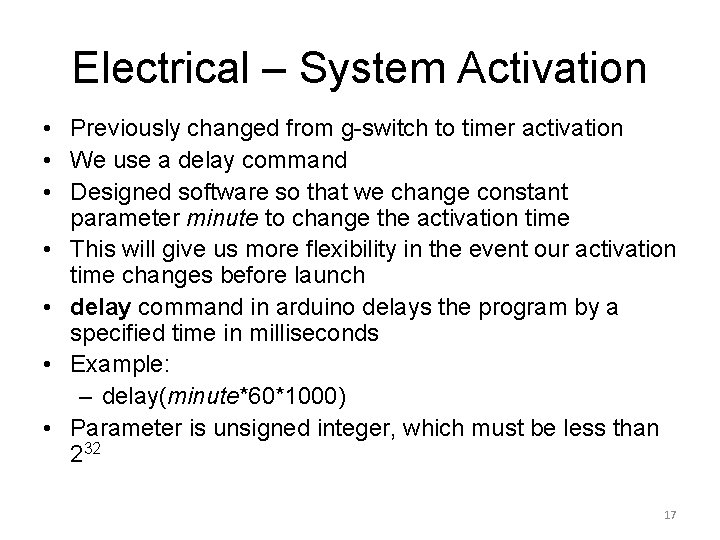
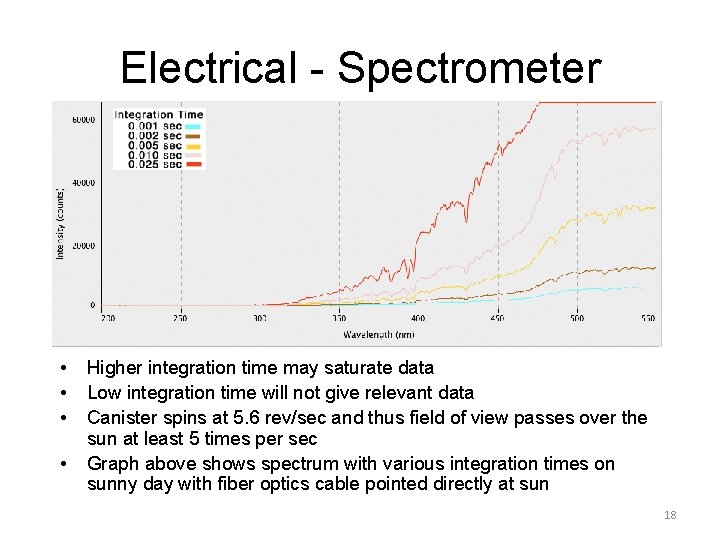
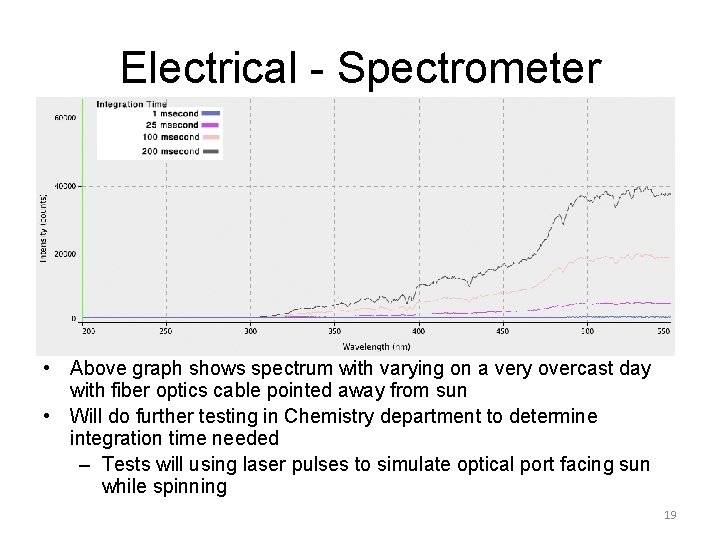

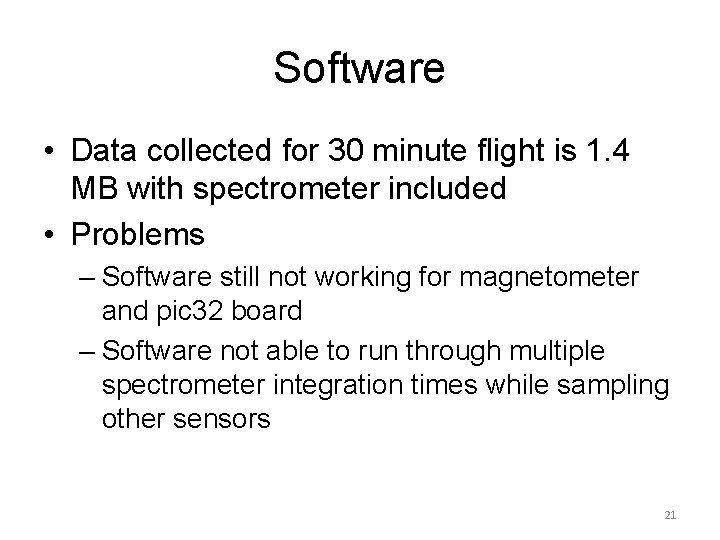
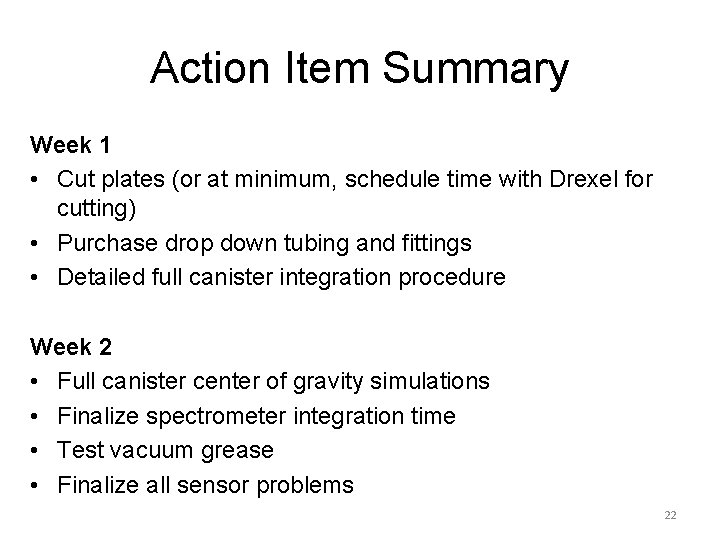
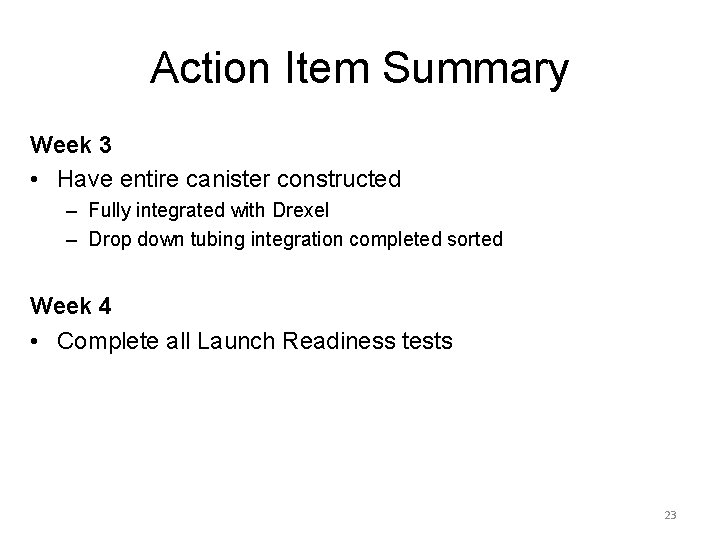
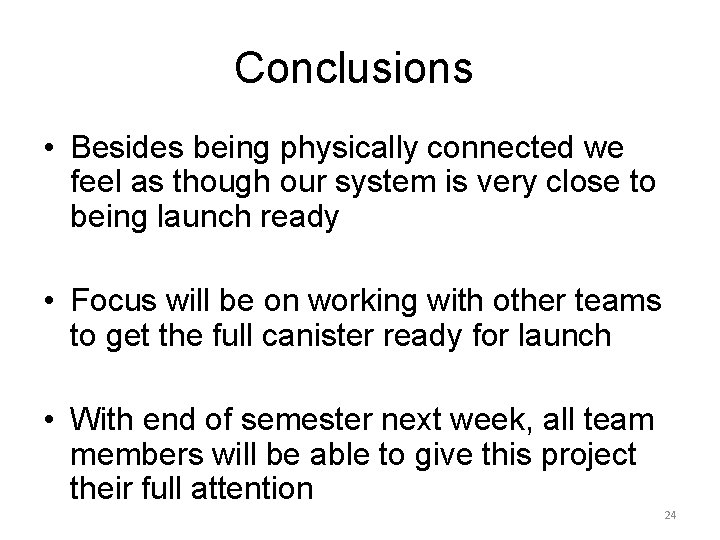
- Slides: 24
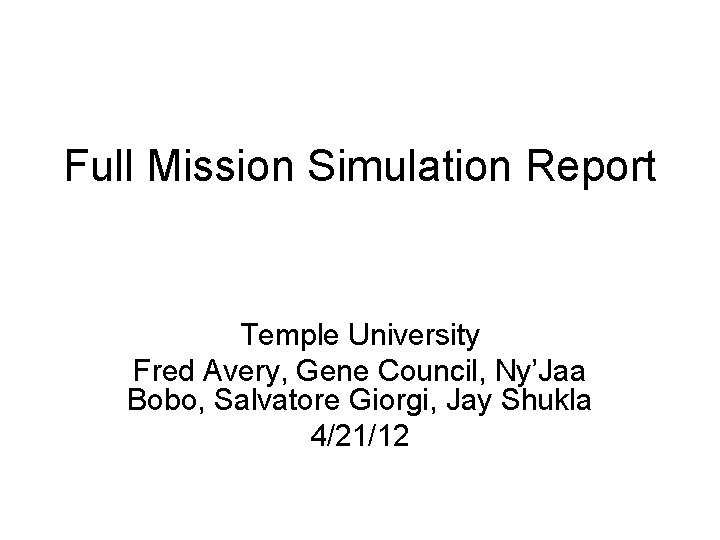
Full Mission Simulation Report Temple University Fred Avery, Gene Council, Ny’Jaa Bobo, Salvatore Giorgi, Jay Shukla 4/21/12
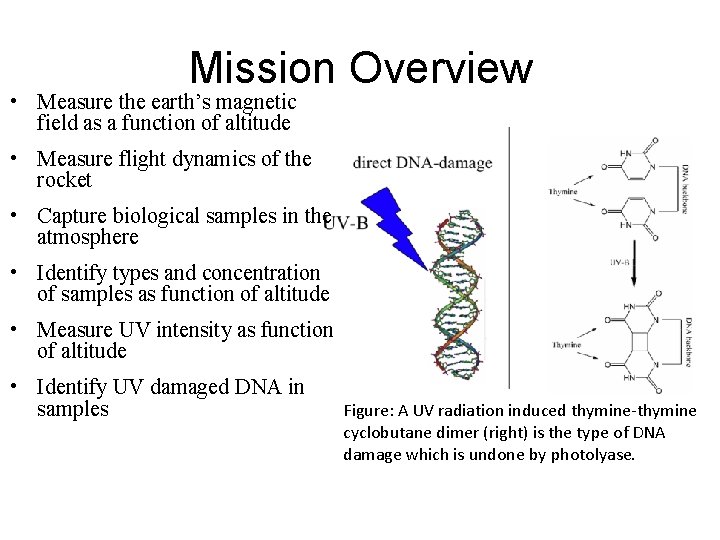
Mission Overview • Measure the earth’s magnetic field as a function of altitude • Measure flight dynamics of the rocket • Capture biological samples in the atmosphere • Identify types and concentration of samples as function of altitude • Measure UV intensity as function of altitude • Identify UV damaged DNA in samples Figure: A UV radiation induced thymine-thymine cyclobutane dimer (right) is the type of DNA damage which is undone by photolyase.
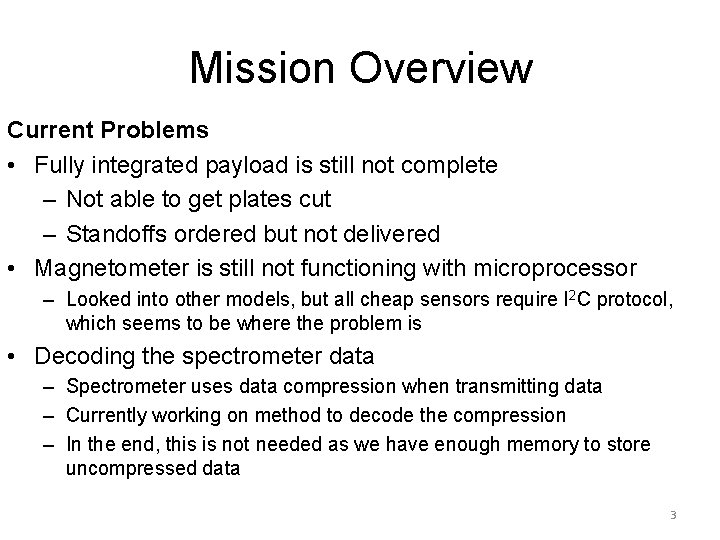
Mission Overview Current Problems • Fully integrated payload is still not complete – Not able to get plates cut – Standoffs ordered but not delivered • Magnetometer is still not functioning with microprocessor – Looked into other models, but all cheap sensors require I 2 C protocol, which seems to be where the problem is • Decoding the spectrometer data – Spectrometer uses data compression when transmitting data – Currently working on method to decode the compression – In the end, this is not needed as we have enough memory to store uncompressed data 3

Mission Overview - Testing Tests Previously Completed • Filtration System Temperature Tests • Filtration System Pressure Tests • Data Collection • Power • Spin • Plate Stress/Strain Simulations 4
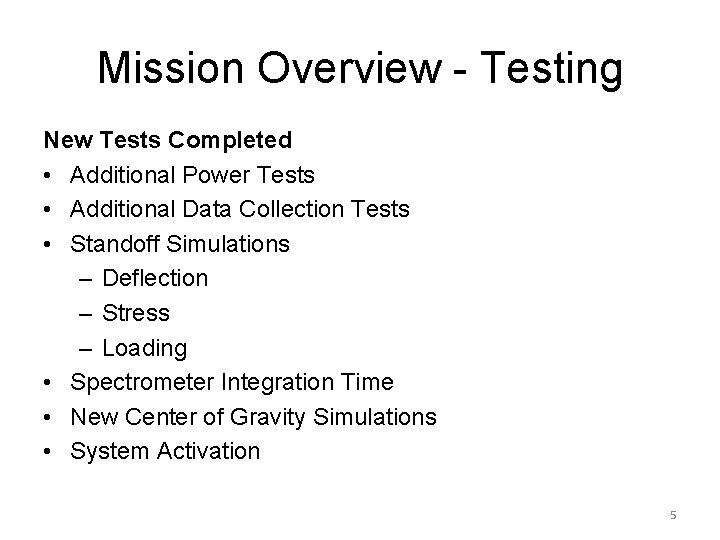
Mission Overview - Testing New Tests Completed • Additional Power Tests • Additional Data Collection Tests • Standoff Simulations – Deflection – Stress – Loading • Spectrometer Integration Time • New Center of Gravity Simulations • System Activation 5
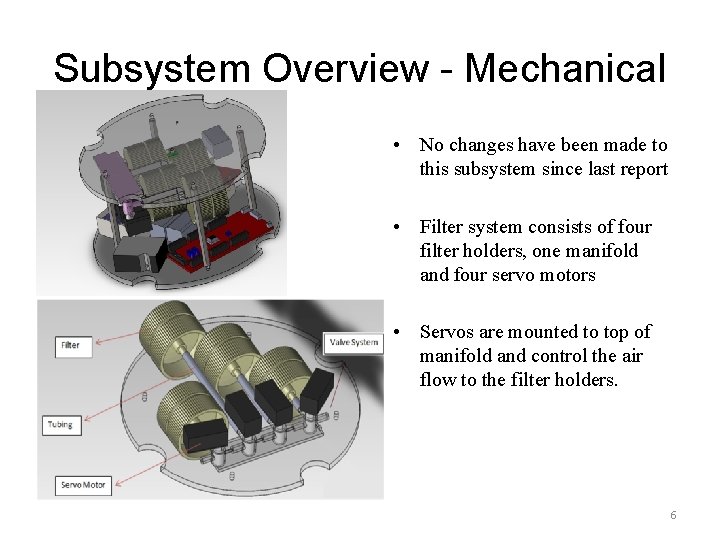
Subsystem Overview - Mechanical • No changes have been made to this subsystem since last report • Filter system consists of four filter holders, one manifold and four servo motors • Servos are mounted to top of manifold and control the air flow to the filter holders. 6
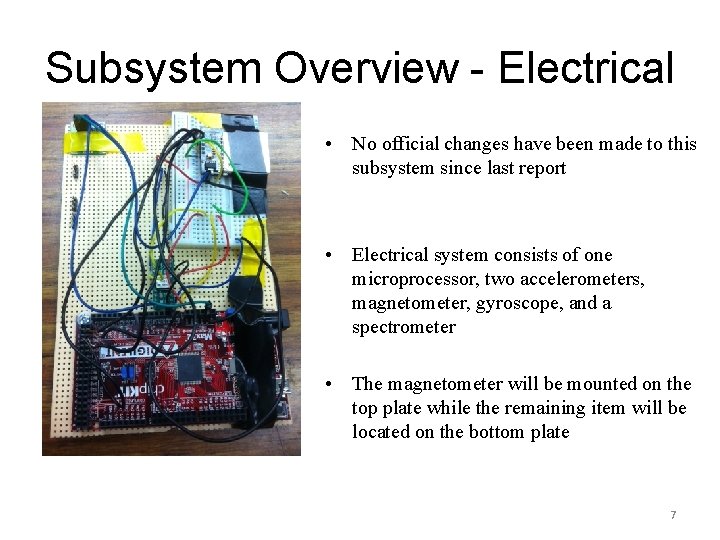
Subsystem Overview - Electrical • No official changes have been made to this subsystem since last report • Electrical system consists of one microprocessor, two accelerometers, magnetometer, gyroscope, and a spectrometer • The magnetometer will be mounted on the top plate while the remaining item will be located on the bottom plate 7
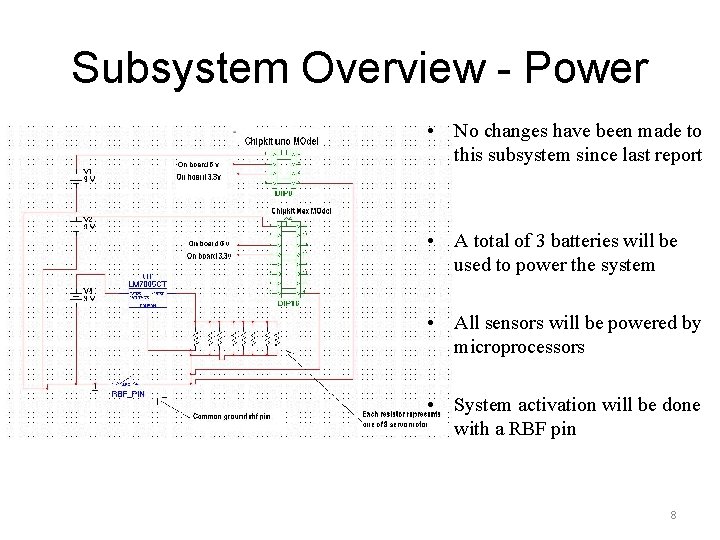
Subsystem Overview - Power • No changes have been made to this subsystem since last report • A total of 3 batteries will be used to power the system • All sensors will be powered by microprocessors • System activation will be done with a RBF pin 8
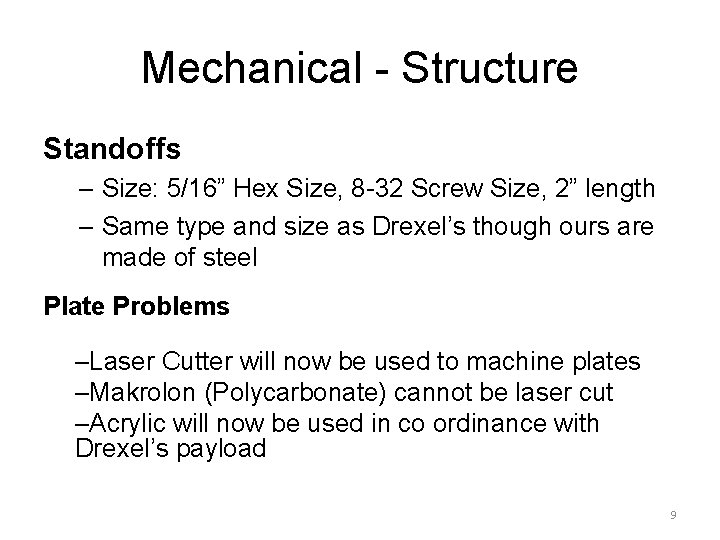
Mechanical - Structure Standoffs – Size: 5/16” Hex Size, 8 -32 Screw Size, 2” length – Same type and size as Drexel’s though ours are made of steel Plate Problems –Laser Cutter will now be used to machine plates –Makrolon (Polycarbonate) cannot be laser cut –Acrylic will now be used in co ordinance with Drexel’s payload 9
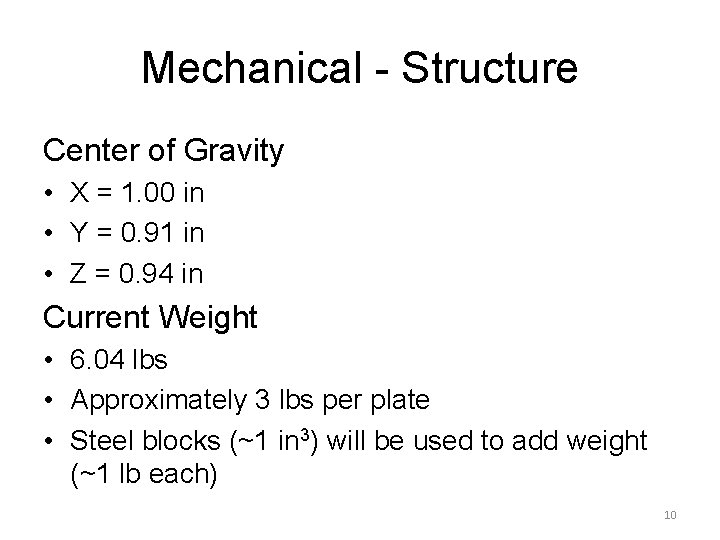
Mechanical - Structure Center of Gravity • X = 1. 00 in • Y = 0. 91 in • Z = 0. 94 in Current Weight • 6. 04 lbs • Approximately 3 lbs per plate • Steel blocks (~1 in 3) will be used to add weight (~1 lb each) 10
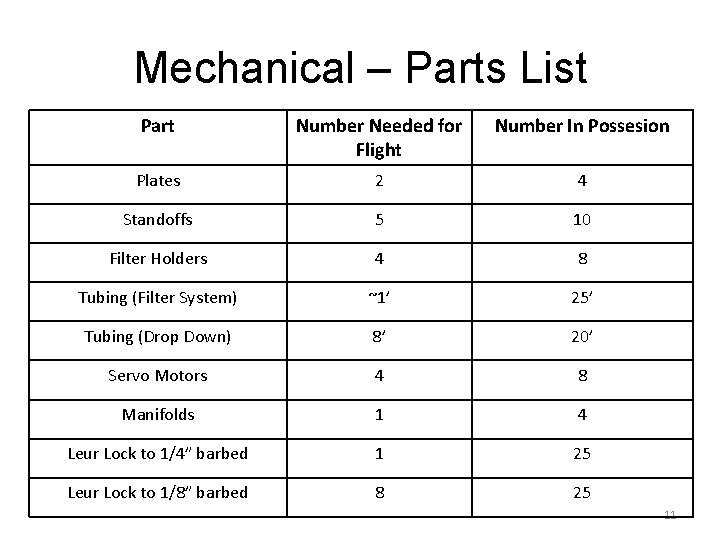
Mechanical – Parts List Part Number Needed for Flight Number In Possesion Plates 2 4 Standoffs 5 10 Filter Holders 4 8 Tubing (Filter System) ~1’ 25’ Tubing (Drop Down) 8’ 20’ Servo Motors 4 8 Manifolds 1 4 Leur Lock to 1/4” barbed 1 25 Leur Lock to 1/8” barbed 8 25 11
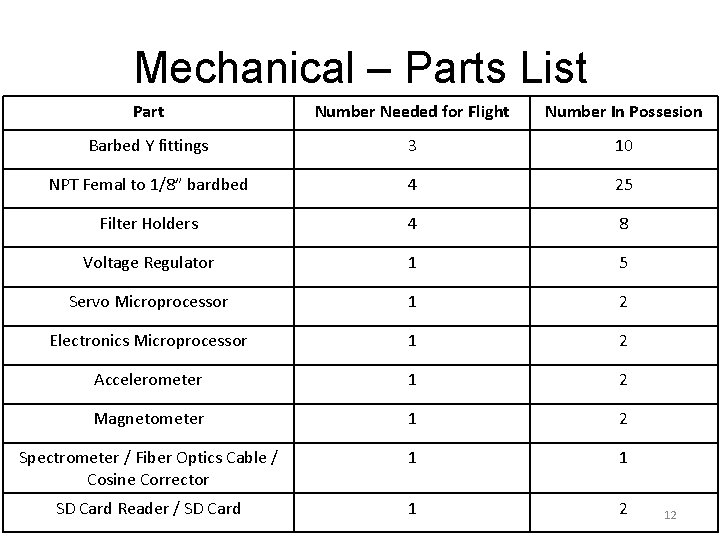
Mechanical – Parts List Part Number Needed for Flight Number In Possesion Barbed Y fittings 3 10 NPT Femal to 1/8” bardbed 4 25 Filter Holders 4 8 Voltage Regulator 1 5 Servo Microprocessor 1 2 Electronics Microprocessor 1 2 Accelerometer 1 2 Magnetometer 1 2 Spectrometer / Fiber Optics Cable / Cosine Corrector 1 1 SD Card Reader / SD Card 1 2 12
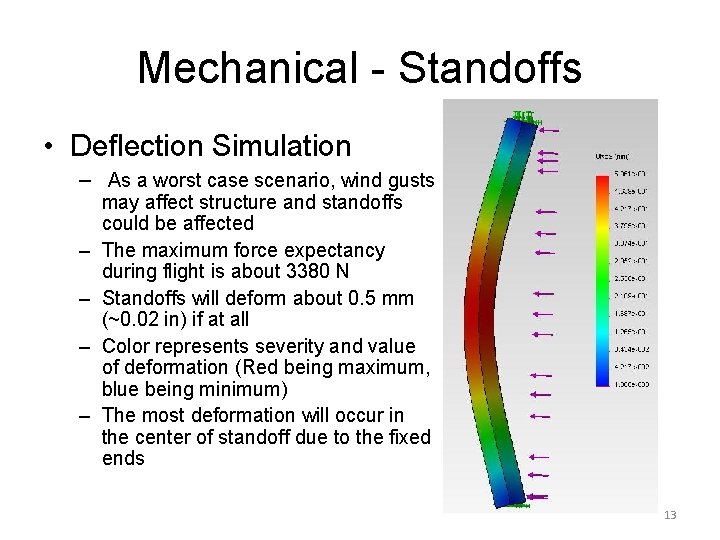
Mechanical - Standoffs • Deflection Simulation – As a worst case scenario, wind gusts – – may affect structure and standoffs could be affected The maximum force expectancy during flight is about 3380 N Standoffs will deform about 0. 5 mm (~0. 02 in) if at all Color represents severity and value of deformation (Red being maximum, blue being minimum) The most deformation will occur in the center of standoff due to the fixed ends 13
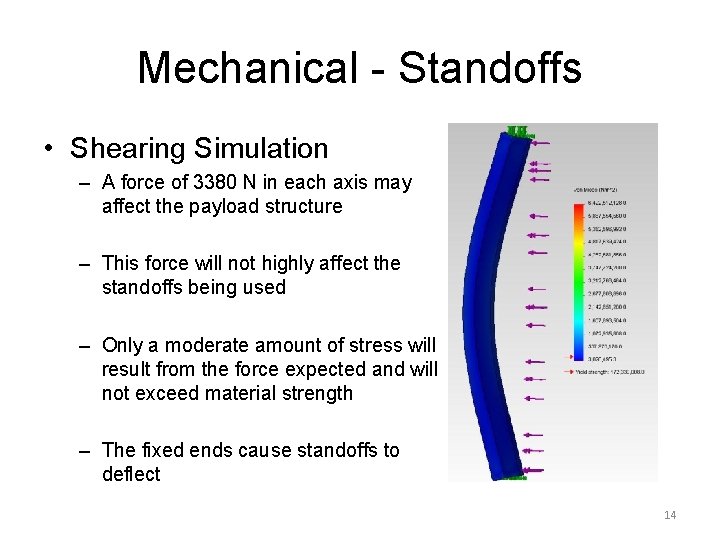
Mechanical - Standoffs • Shearing Simulation – A force of 3380 N in each axis may affect the payload structure – This force will not highly affect the standoffs being used – Only a moderate amount of stress will result from the force expected and will not exceed material strength – The fixed ends cause standoffs to deflect 14
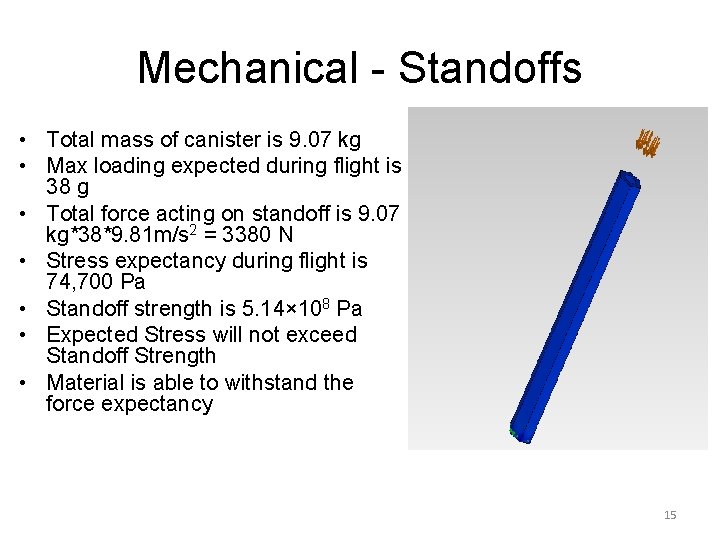
Mechanical - Standoffs • Total mass of canister is 9. 07 kg • Max loading expected during flight is 38 g • Total force acting on standoff is 9. 07 kg*38*9. 81 m/s 2 = 3380 N • Stress expectancy during flight is 74, 700 Pa • Standoff strength is 5. 14× 108 Pa • Expected Stress will not exceed Standoff Strength • Material is able to withstand the force expectancy 15
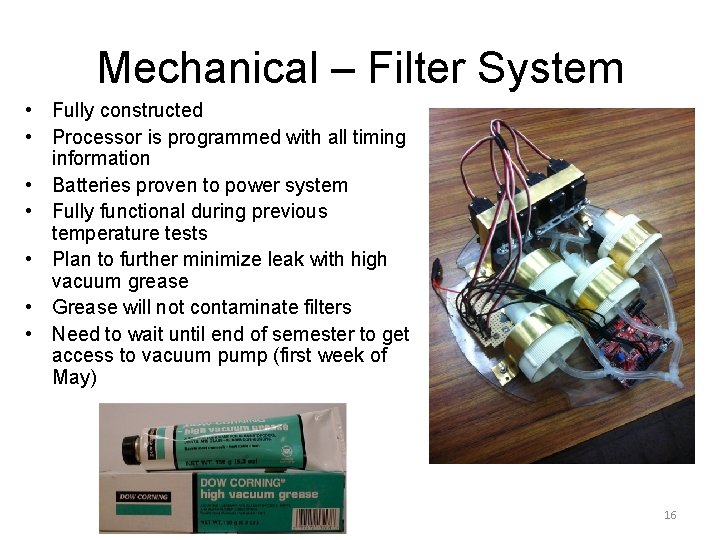
Mechanical – Filter System • Fully constructed • Processor is programmed with all timing information • Batteries proven to power system • Fully functional during previous temperature tests • Plan to further minimize leak with high vacuum grease • Grease will not contaminate filters • Need to wait until end of semester to get access to vacuum pump (first week of May) 16
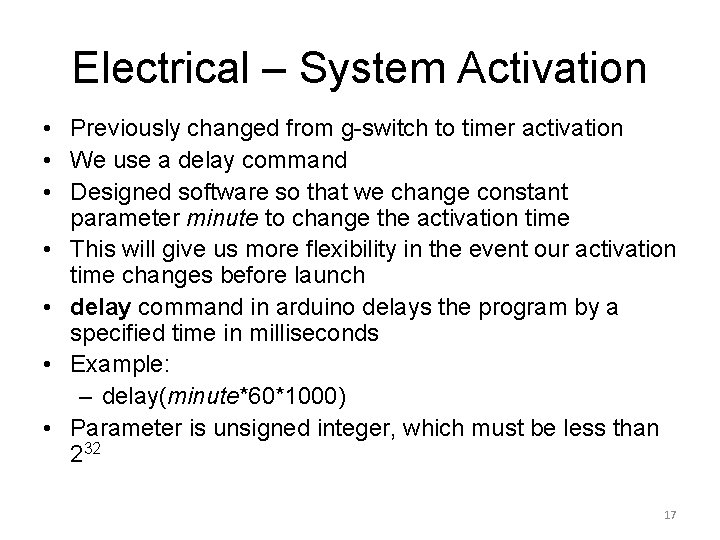
Electrical – System Activation • Previously changed from g-switch to timer activation • We use a delay command • Designed software so that we change constant parameter minute to change the activation time • This will give us more flexibility in the event our activation time changes before launch • delay command in arduino delays the program by a specified time in milliseconds • Example: – delay(minute*60*1000) • Parameter is unsigned integer, which must be less than 232 17
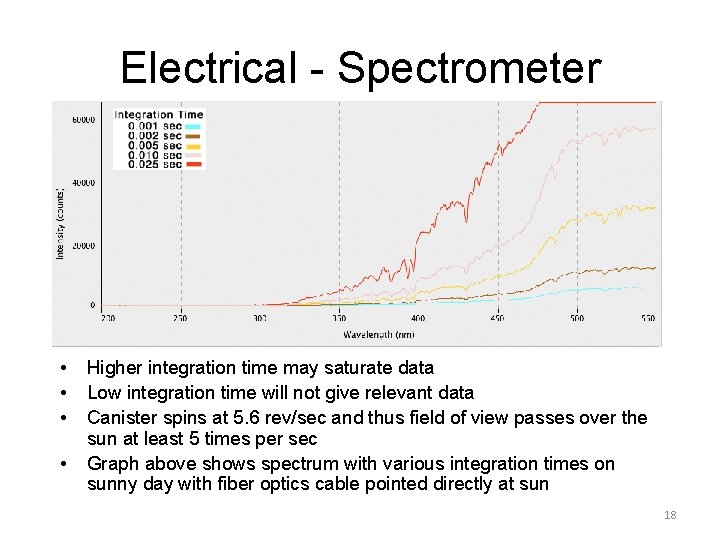
Electrical - Spectrometer • • Higher integration time may saturate data Low integration time will not give relevant data Canister spins at 5. 6 rev/sec and thus field of view passes over the sun at least 5 times per sec Graph above shows spectrum with various integration times on sunny day with fiber optics cable pointed directly at sun 18
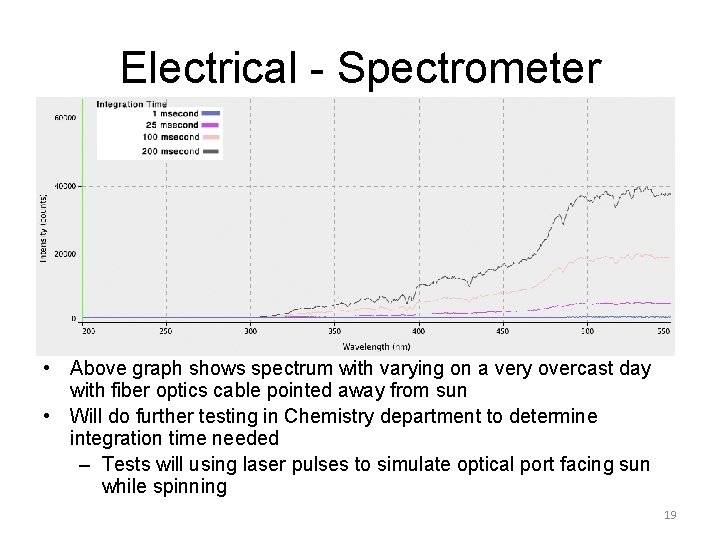
Electrical - Spectrometer • Above graph shows spectrum with varying on a very overcast day with fiber optics cable pointed away from sun • Will do further testing in Chemistry department to determine integration time needed – Tests will using laser pulses to simulate optical port facing sun while spinning 19

Power (EPS) Battery Initial Voltage (V) Final Voltage (V) Electronics Microprocessor 9. 07 8. 65 Servo Microprocessor 9. 01 8. 90 Servos 9. 02 7. 22 • Above table shows voltage values for 30 minute flight simulation • Batteries were able to power everything, as expected 20
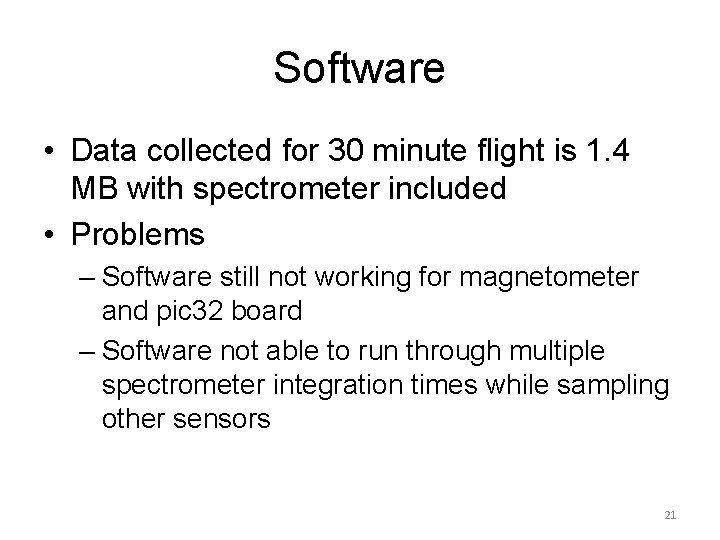
Software • Data collected for 30 minute flight is 1. 4 MB with spectrometer included • Problems – Software still not working for magnetometer and pic 32 board – Software not able to run through multiple spectrometer integration times while sampling other sensors 21
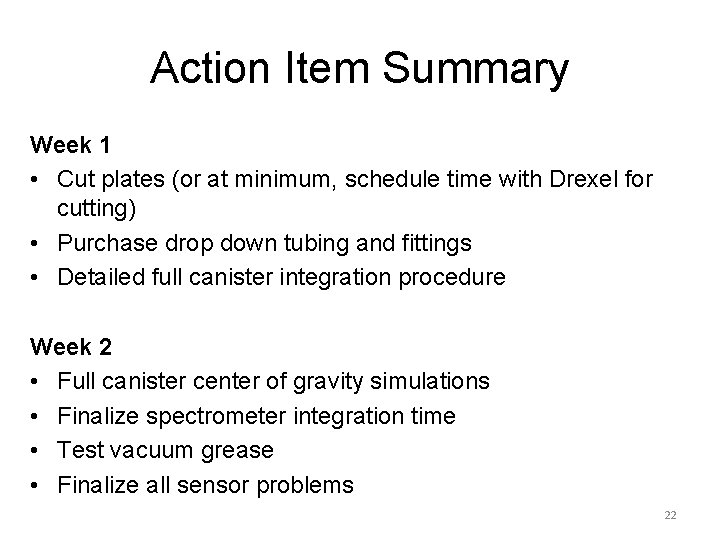
Action Item Summary Week 1 • Cut plates (or at minimum, schedule time with Drexel for cutting) • Purchase drop down tubing and fittings • Detailed full canister integration procedure Week 2 • Full canister center of gravity simulations • Finalize spectrometer integration time • Test vacuum grease • Finalize all sensor problems 22
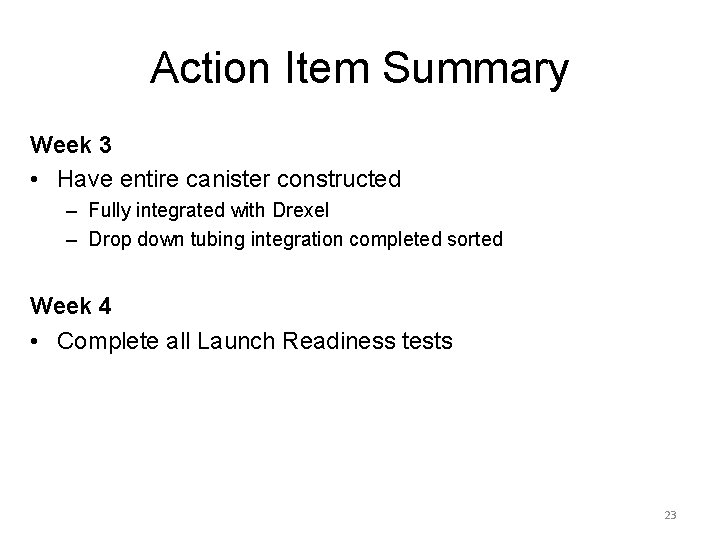
Action Item Summary Week 3 • Have entire canister constructed – Fully integrated with Drexel – Drop down tubing integration completed sorted Week 4 • Complete all Launch Readiness tests 23
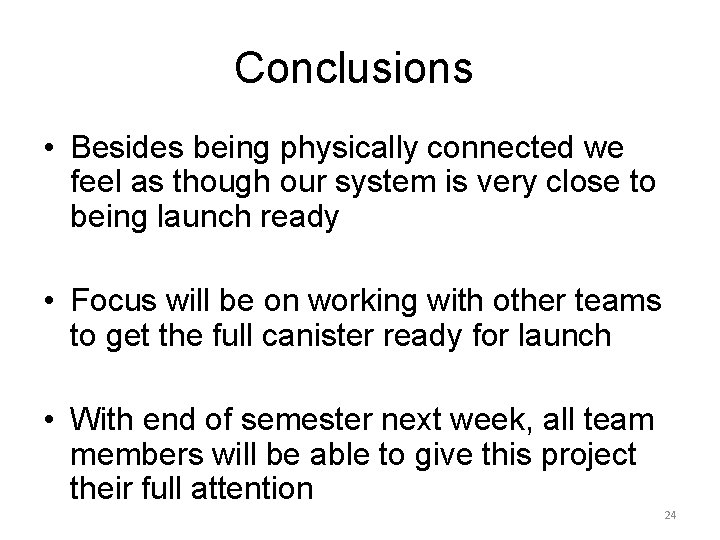
Conclusions • Besides being physically connected we feel as though our system is very close to being launch ready • Focus will be on working with other teams to get the full canister ready for launch • With end of semester next week, all team members will be able to give this project their full attention 24
How does avery’s adoptive mother describe who avery is?
Temple university entrepreneurship
Engineering temple run
Irb temple
Temple disability services
Temple university study abroad
Temple university admission requirements
Temple university writing center
Isss temple university
Vraj temple philadelphia
Tempel body
Aarononpc
Temple university undergraduate bulletin
Temple university cis
Marketing simulation game report
Nyu avery fisher center
Who is mr. avery in to kill a mockingbird
Avery dulles models of the church
Sacrament model of the church
Fish morphology worksheet answers
Avery v bowden
Annabella avery bella thorne
Avery's experiment
Avery cheng
James dewey watson