From the ATLAS SCT endcap module production to
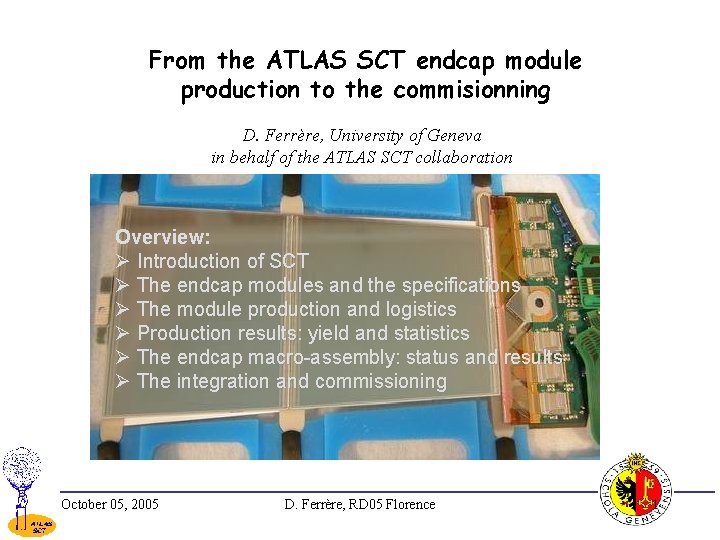
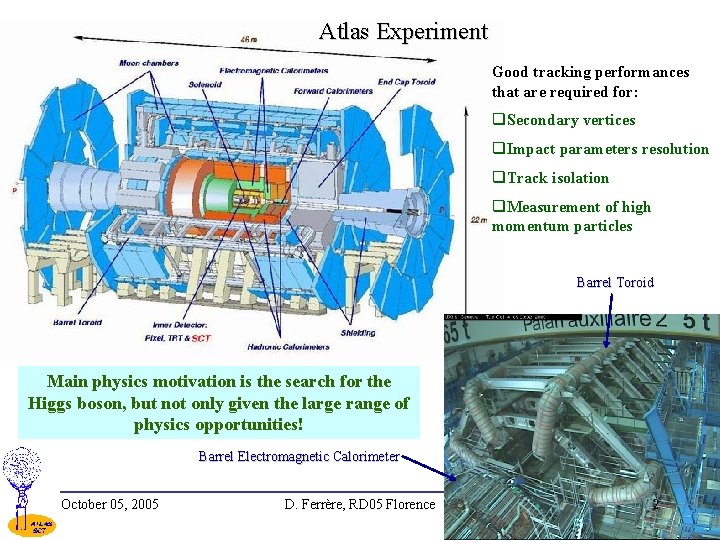
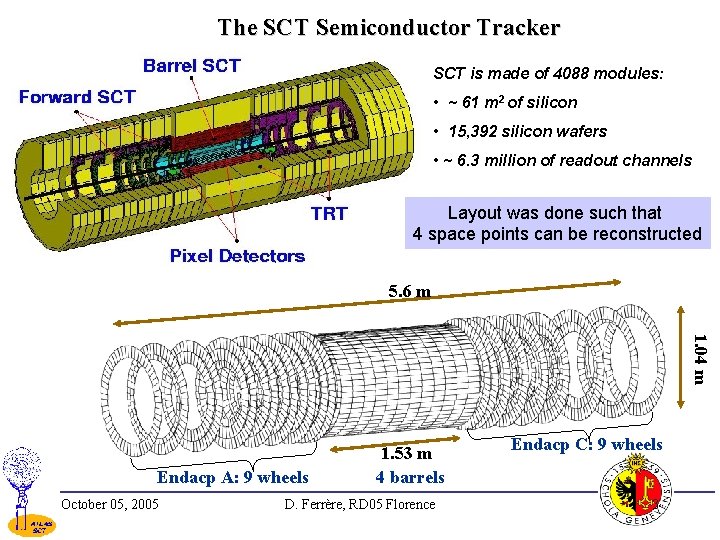
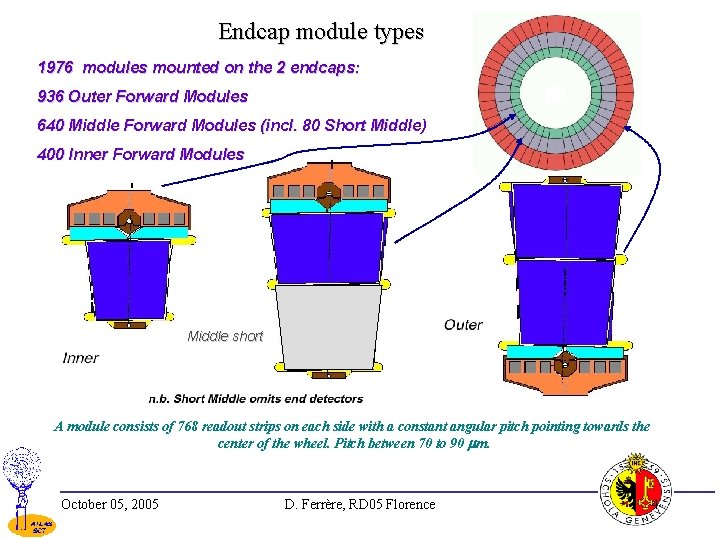
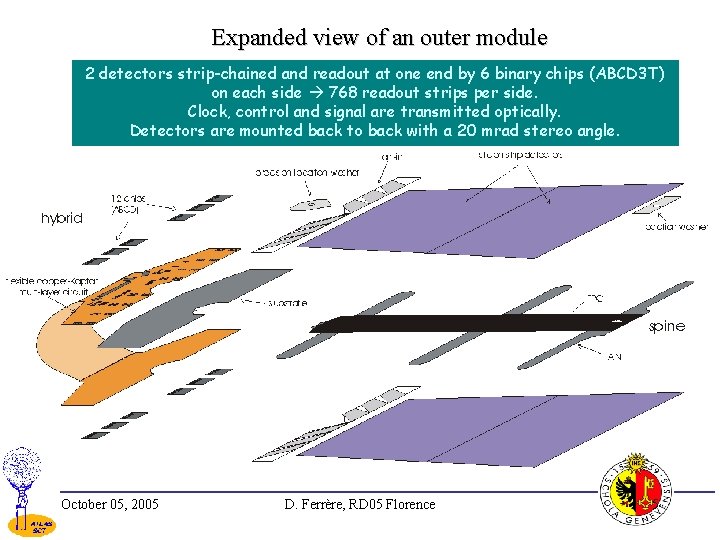
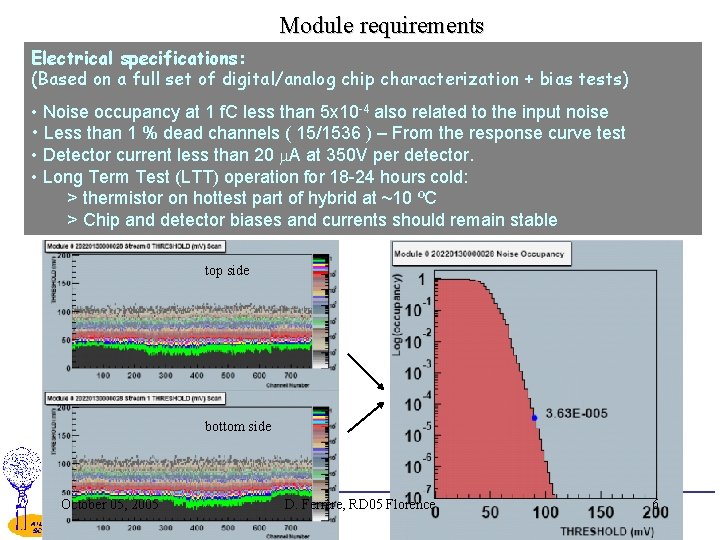
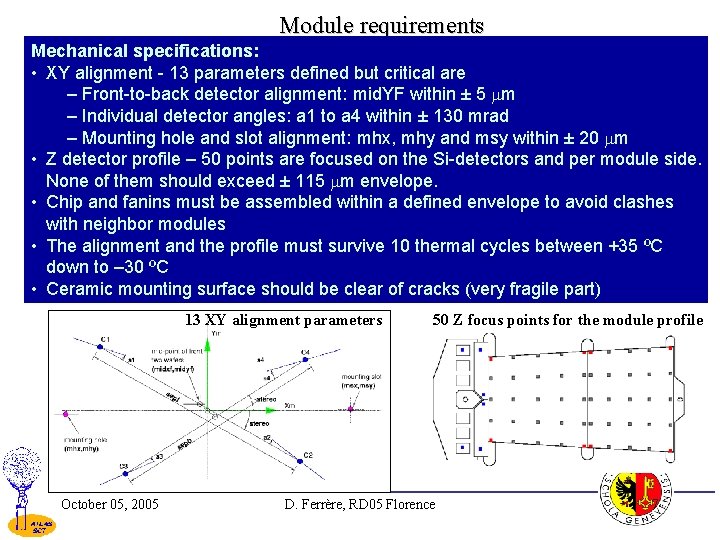
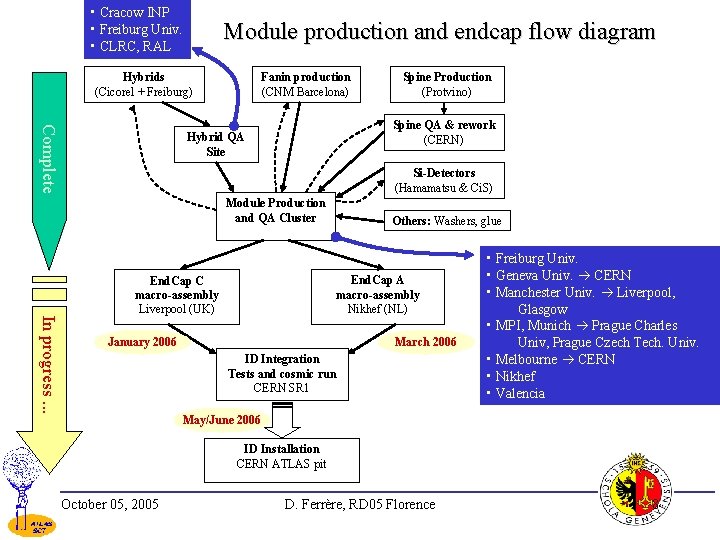
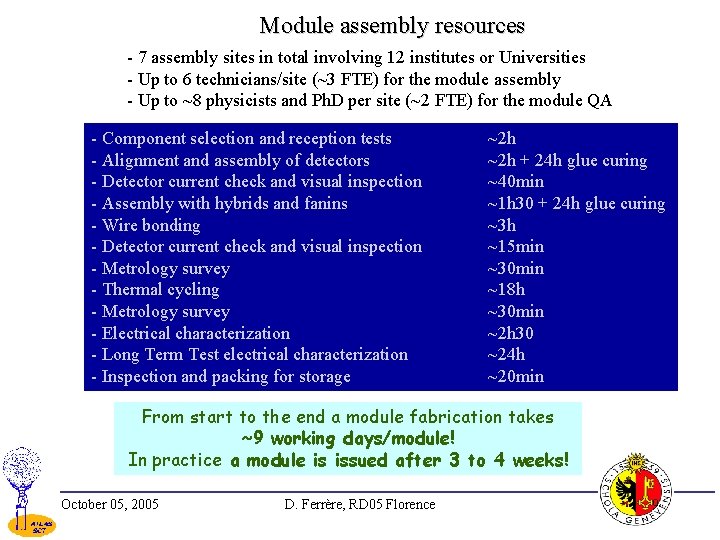
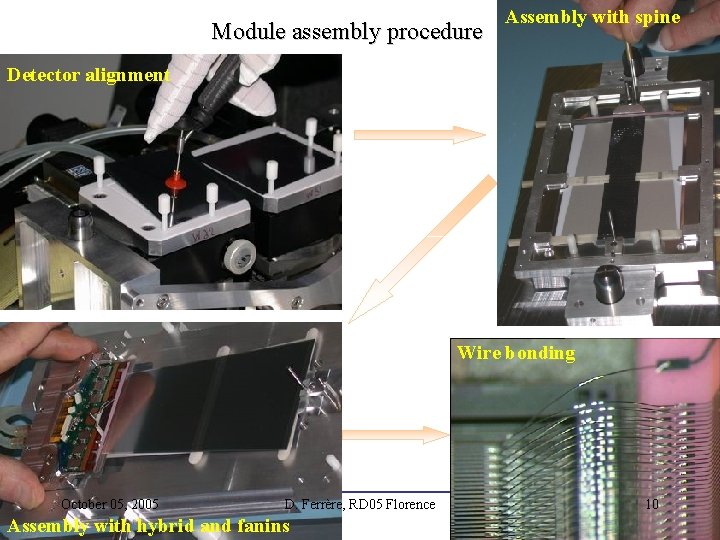
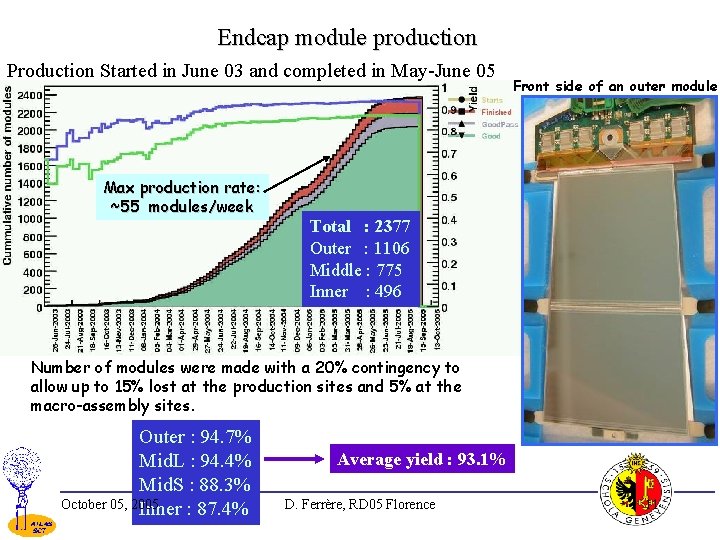
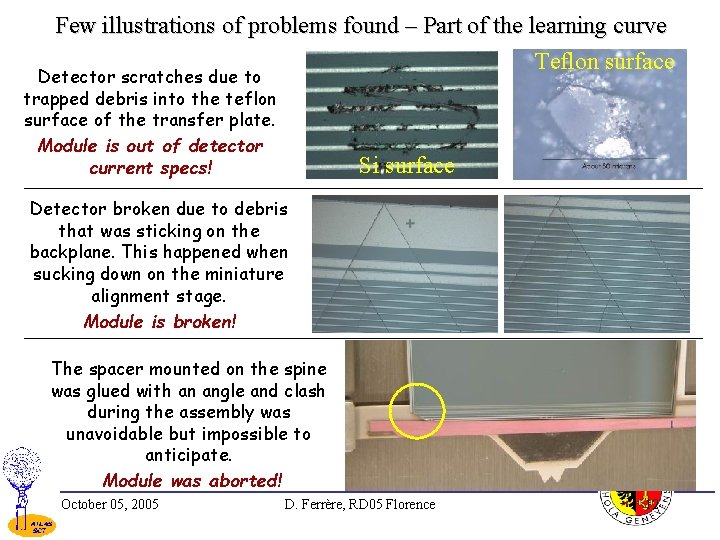
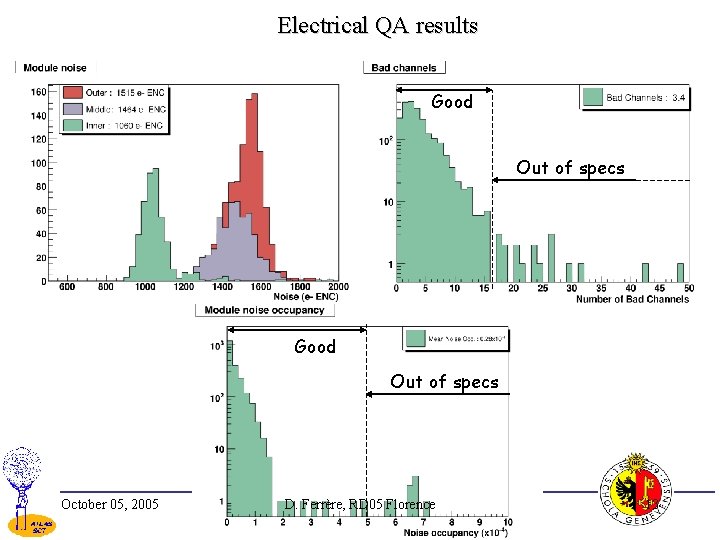
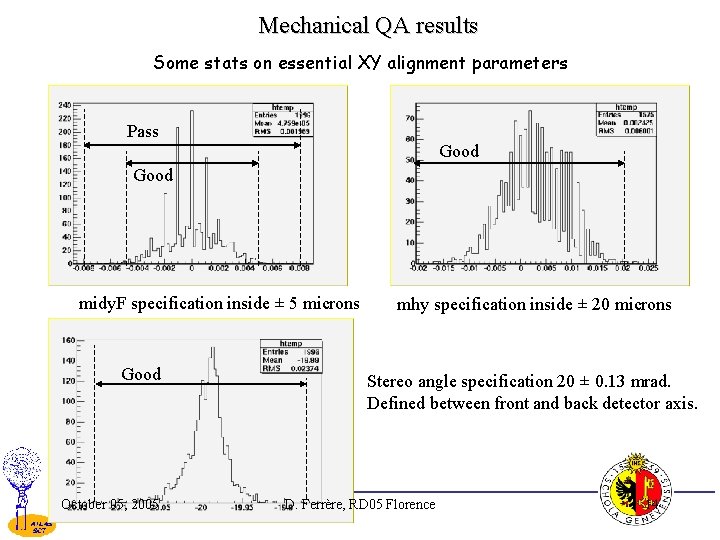
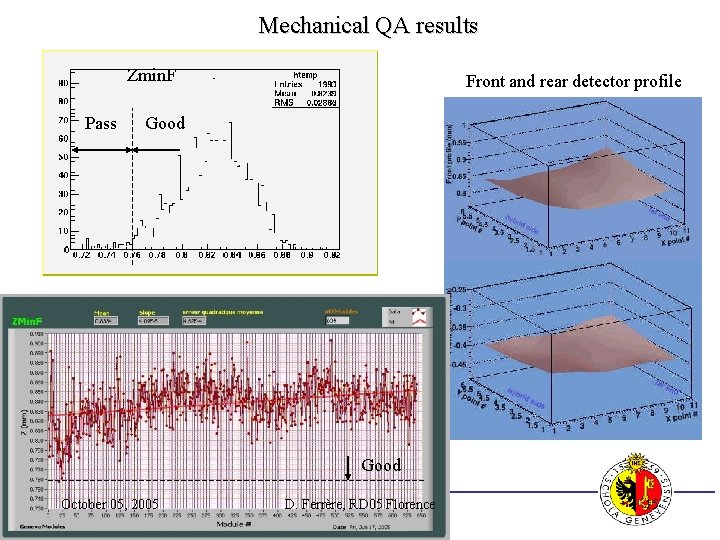
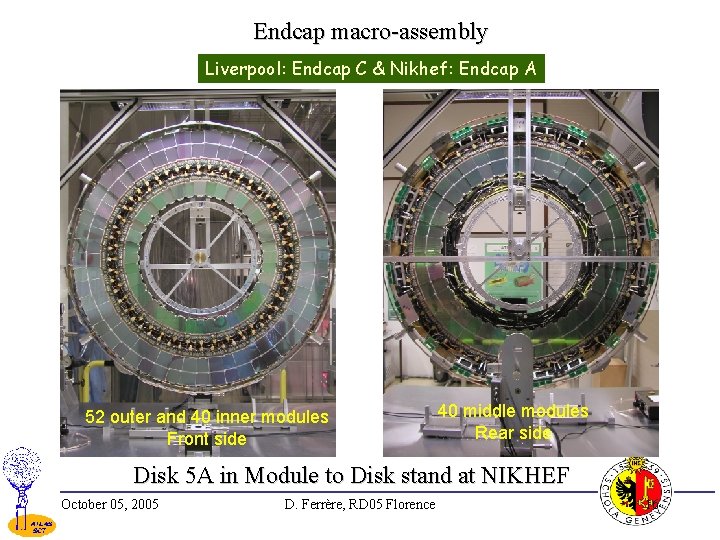
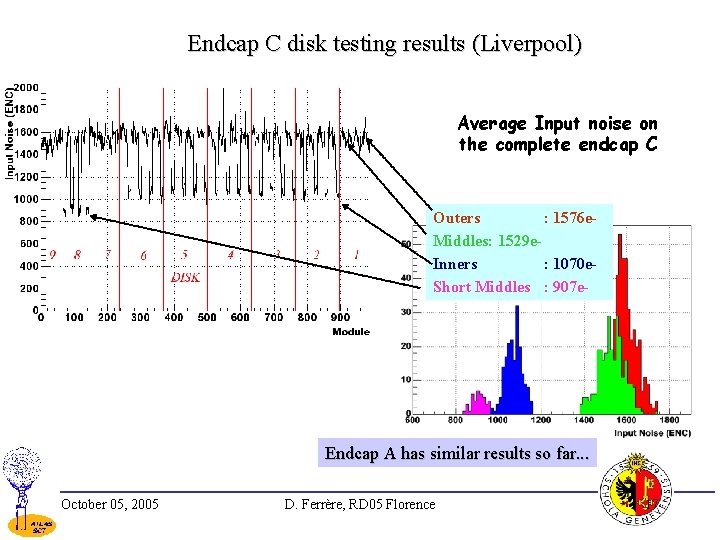
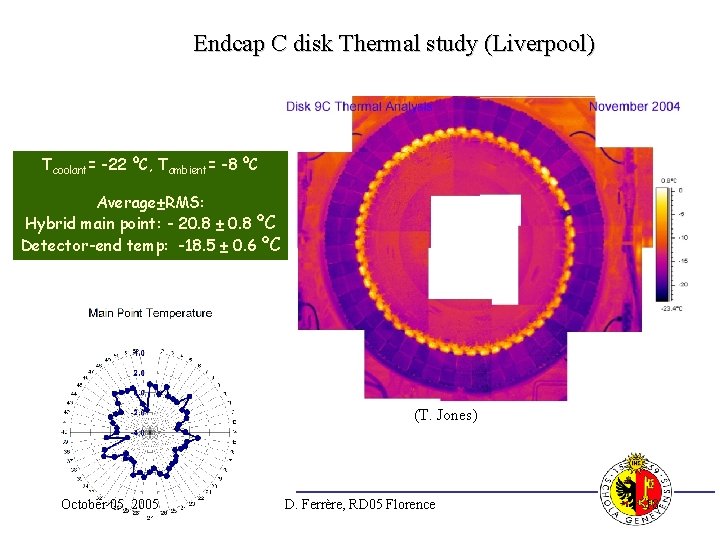
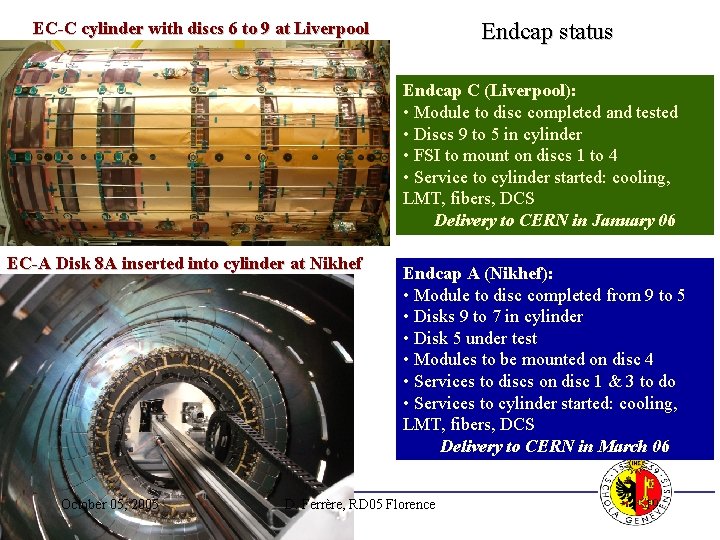
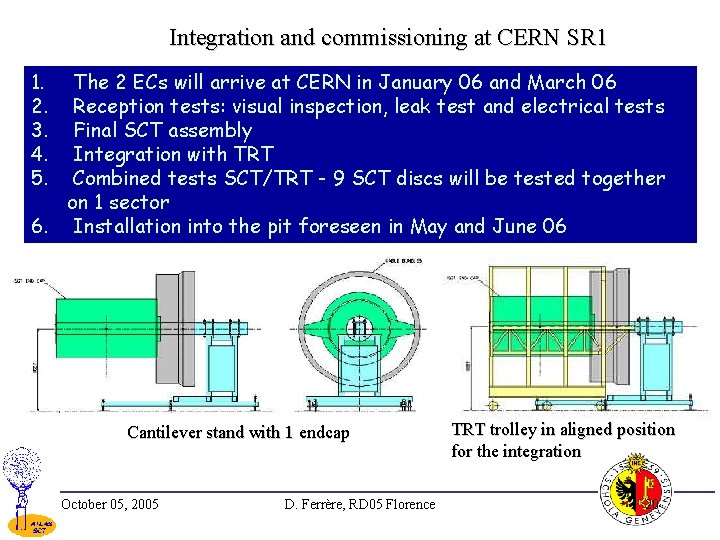
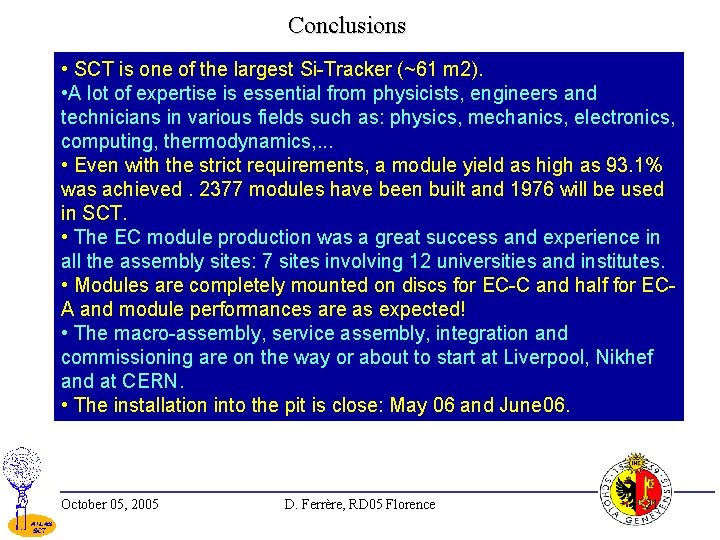
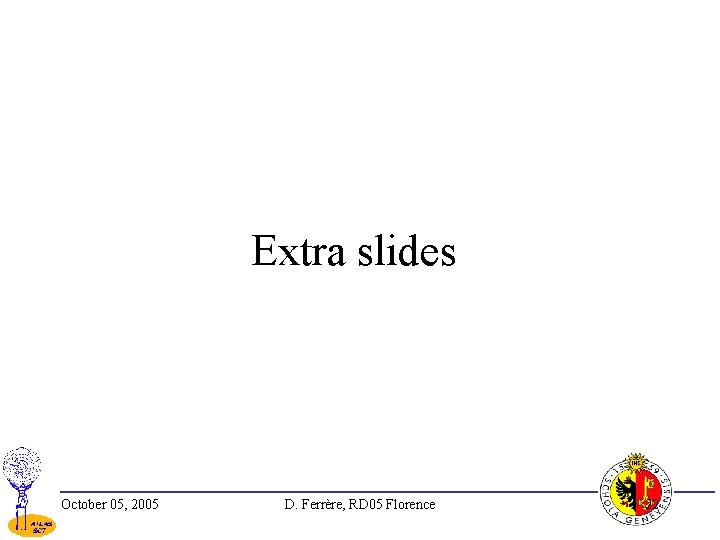
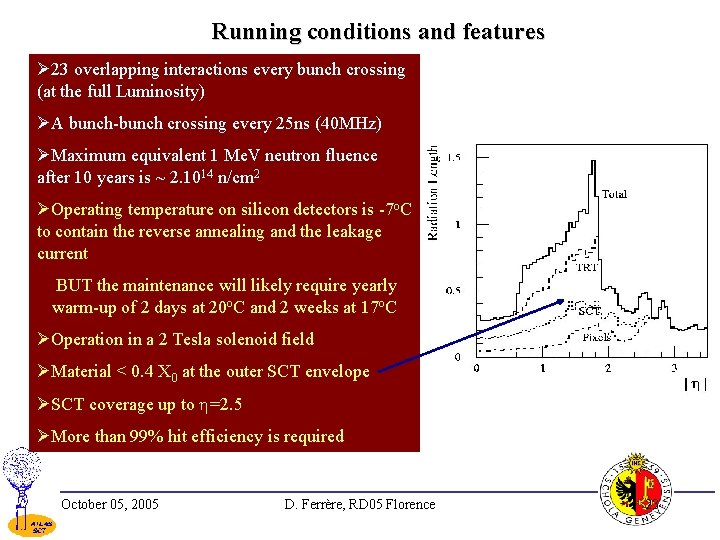
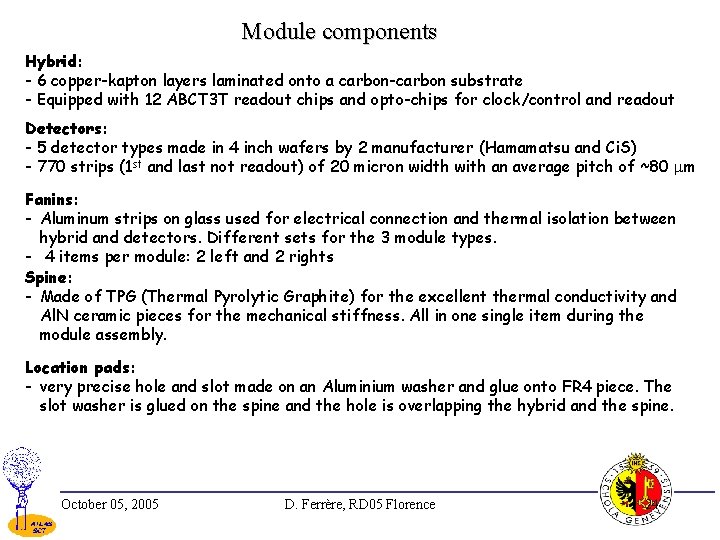
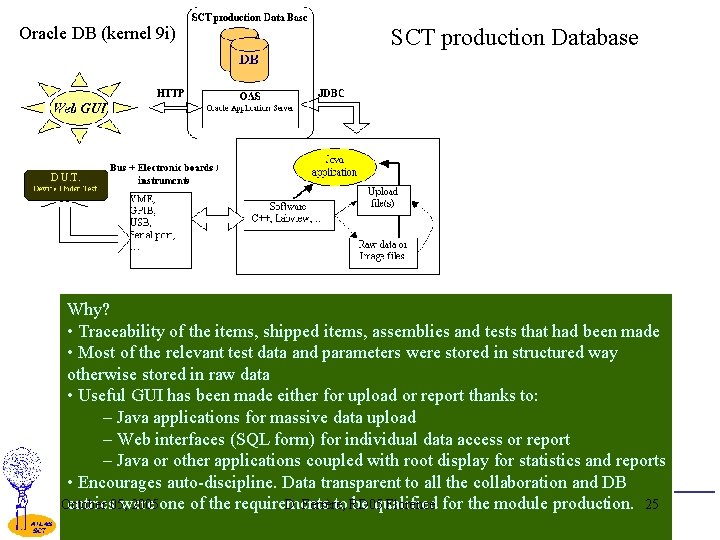
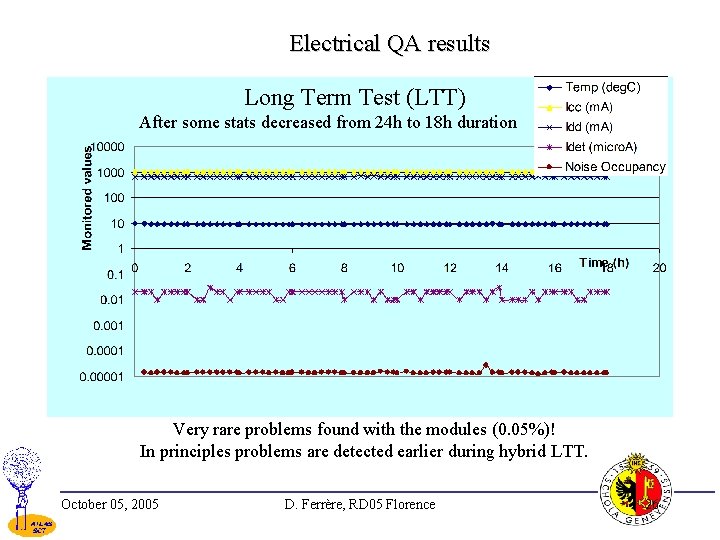
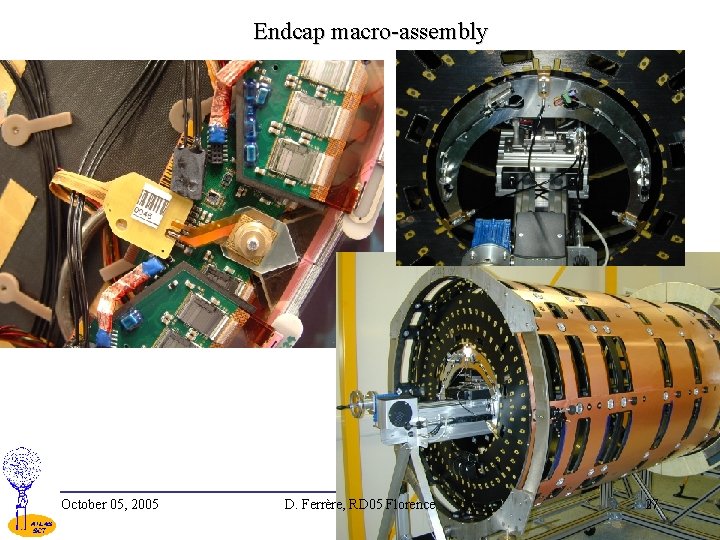
- Slides: 27
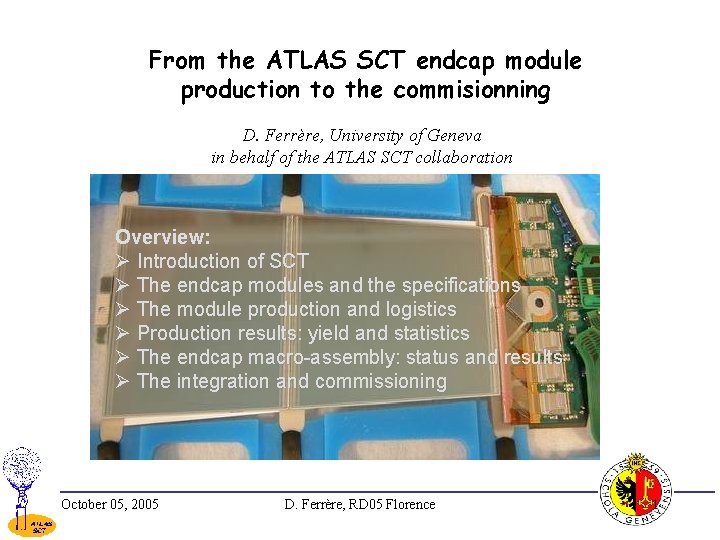
From the ATLAS SCT endcap module production to the commisionning D. Ferrère, University of Geneva in behalf of the ATLAS SCT collaboration Overview: Ø Introduction of SCT Ø The endcap modules and the specifications Ø The module production and logistics Ø Production results: yield and statistics Ø The endcap macro-assembly: status and results Ø The integration and commissioning October 05, 2005 D. Ferrère, RD 05 Florence 1
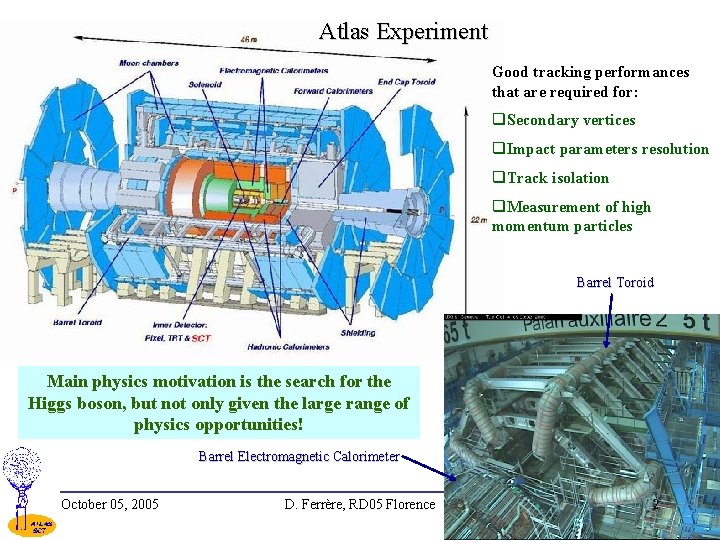
Atlas Experiment Good tracking performances that are required for: q. Secondary vertices q. Impact parameters resolution q. Track isolation q. Measurement of high momentum particles Barrel Toroid Main physics motivation is the search for the Higgs boson, but not only given the large range of physics opportunities! Barrel Electromagnetic Calorimeter October 05, 2005 D. Ferrère, RD 05 Florence 2
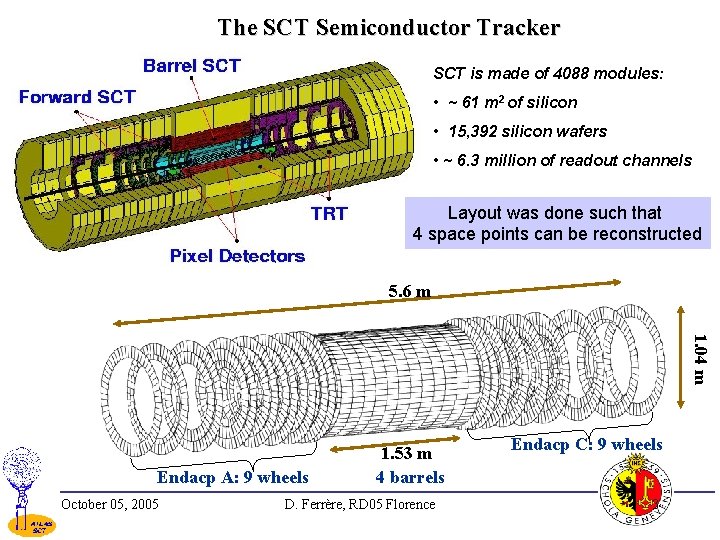
The SCT Semiconductor Tracker SCT is made of 4088 modules: • ~ 61 m 2 of silicon • 15, 392 silicon wafers • ~ 6. 3 million of readout channels Layout was done such that 4 space points can be reconstructed 5. 6 m 1. 04 m Endacp A: 9 wheels October 05, 2005 1. 53 m 4 barrels D. Ferrère, RD 05 Florence Endacp C: 9 wheels 3
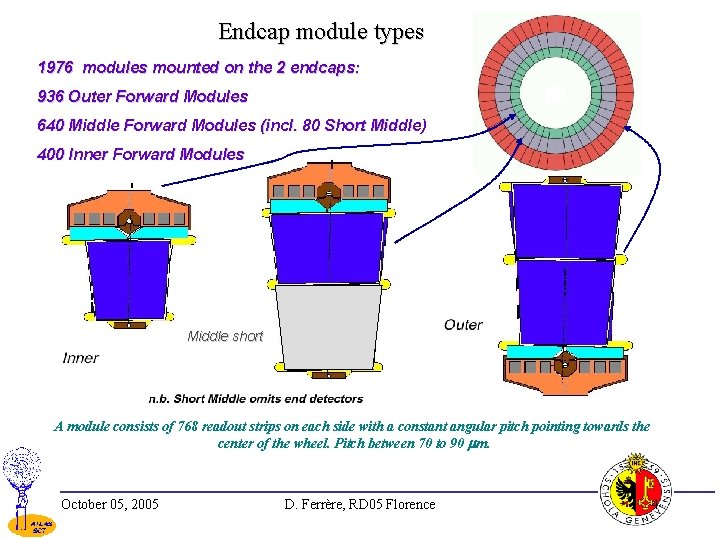
Endcap module types 1976 modules mounted on the 2 endcaps: 936 Outer Forward Modules 640 Middle Forward Modules (incl. 80 Short Middle) 400 Inner Forward Modules Middle short A module consists of 768 readout strips on each side with a constant angular pitch pointing towards the center of the wheel. Pitch between 70 to 90 m. October 05, 2005 D. Ferrère, RD 05 Florence 4
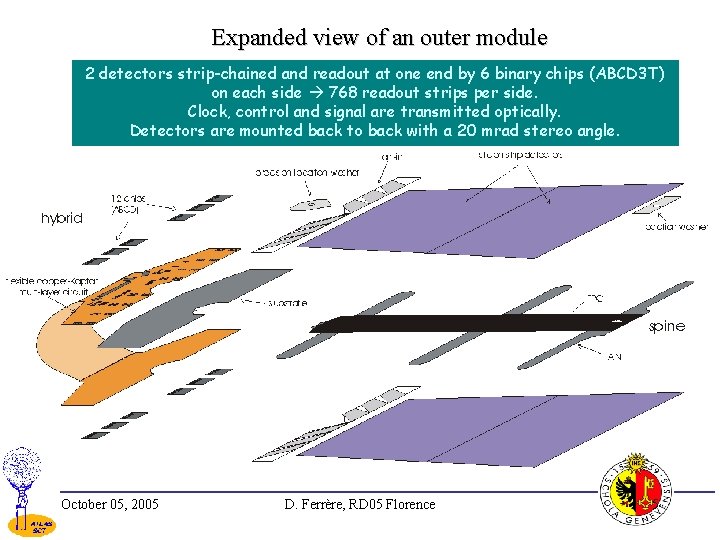
Expanded view of an outer module 2 detectors strip-chained and readout at one end by 6 binary chips (ABCD 3 T) on each side 768 readout strips per side. Clock, control and signal are transmitted optically. Detectors are mounted back to back with a 20 mrad stereo angle. October 05, 2005 D. Ferrère, RD 05 Florence 5
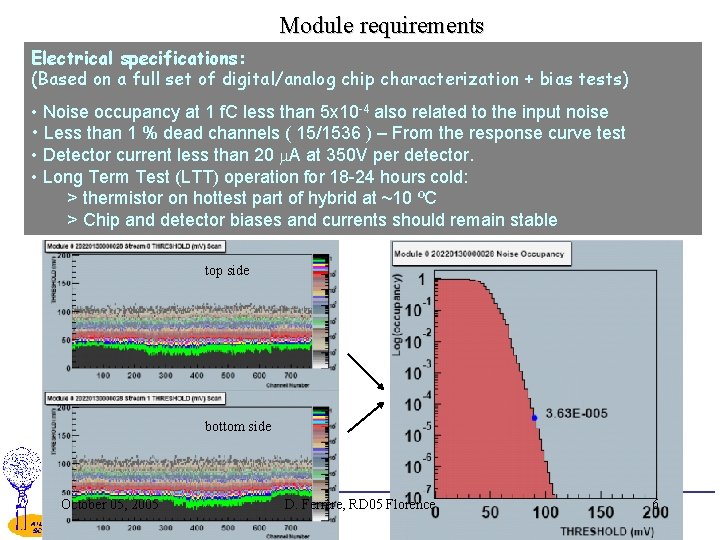
Module requirements Electrical specifications: (Based on a full set of digital/analog chip characterization + bias tests) • Noise occupancy at 1 f. C less than 5 x 10 -4 also related to the input noise • Less than 1 % dead channels ( 15/1536 ) – From the response curve test • Detector current less than 20 A at 350 V per detector. • Long Term Test (LTT) operation for 18 -24 hours cold: > thermistor on hottest part of hybrid at ~10 ºC > Chip and detector biases and currents should remain stable top side bottom side October 05, 2005 D. Ferrère, RD 05 Florence 6
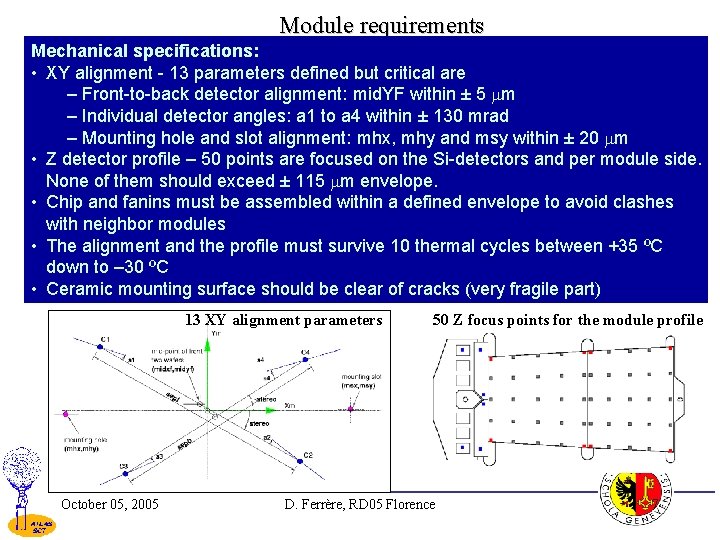
Module requirements Mechanical specifications: • XY alignment - 13 parameters defined but critical are – Front-to-back detector alignment: mid. YF within ± 5 m – Individual detector angles: a 1 to a 4 within ± 130 mrad – Mounting hole and slot alignment: mhx, mhy and msy within ± 20 m • Z detector profile – 50 points are focused on the Si-detectors and per module side. None of them should exceed ± 115 m envelope. • Chip and fanins must be assembled within a defined envelope to avoid clashes with neighbor modules • The alignment and the profile must survive 10 thermal cycles between +35 ºC down to – 30 ºC • Ceramic mounting surface should be clear of cracks (very fragile part) 13 XY alignment parameters October 05, 2005 50 Z focus points for the module profile D. Ferrère, RD 05 Florence 7
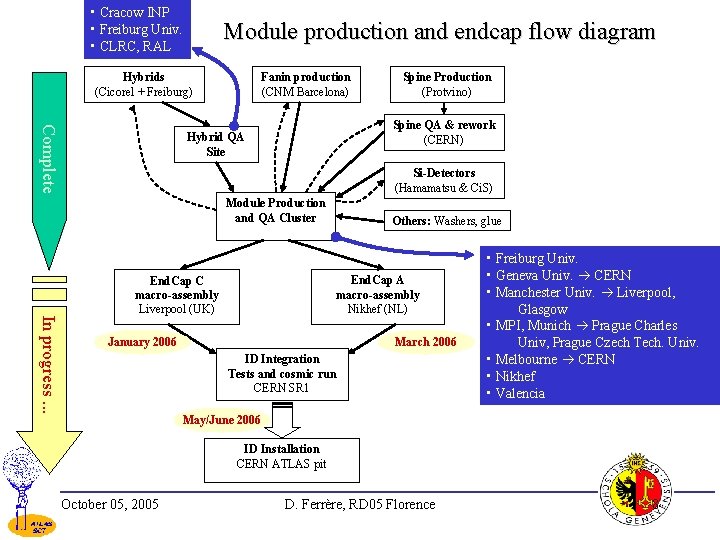
• Cracow INP • Freiburg Univ. • CLRC, RAL Module production and endcap flow diagram Hybrids (Cicorel + Freiburg) Fanin production (CNM Barcelona) Spine Production (Protvino) Complete Spine QA & rework (CERN) Hybrid QA Site Si-Detectors (Hamamatsu & Ci. S) Module Production and QA Cluster Others: Washers, glue End. Cap A macro-assembly Nikhef (NL) End. Cap C macro-assembly Liverpool (UK) In progress. . . January 2006 March 2006 ID Integration Tests and cosmic run CERN SR 1 • Freiburg Univ. • Geneva Univ. CERN • Manchester Univ. Liverpool, Glasgow • MPI, Munich Prague Charles Univ, Prague Czech Tech. Univ. • Melbourne CERN • Nikhef • Valencia May/June 2006 ID Installation CERN ATLAS pit October 05, 2005 D. Ferrère, RD 05 Florence 8
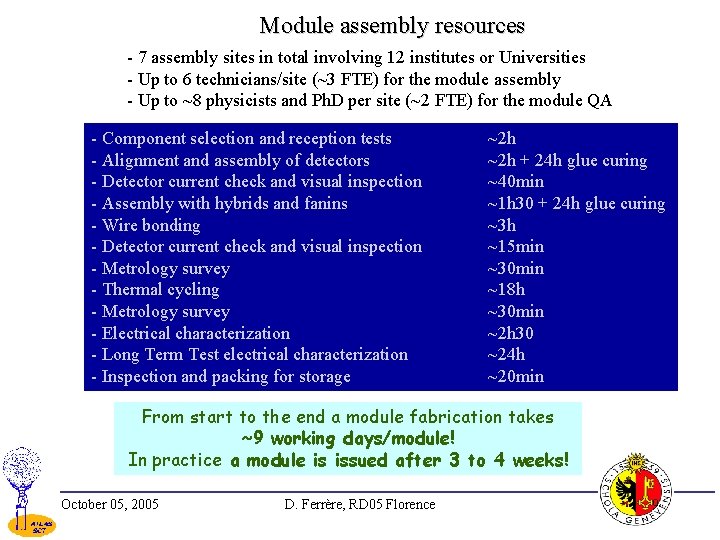
Module assembly resources - 7 assembly sites in total involving 12 institutes or Universities - Up to 6 technicians/site (~3 FTE) for the module assembly - Up to ~8 physicists and Ph. D per site (~2 FTE) for the module QA - Component selection and reception tests - Alignment and assembly of detectors - Detector current check and visual inspection - Assembly with hybrids and fanins - Wire bonding - Detector current check and visual inspection - Metrology survey - Thermal cycling - Metrology survey - Electrical characterization - Long Term Test electrical characterization - Inspection and packing for storage ~2 h + 24 h glue curing ~40 min ~1 h 30 + 24 h glue curing ~3 h ~15 min ~30 min ~18 h ~30 min ~2 h 30 ~24 h ~20 min From start to the end a module fabrication takes ~9 working days/module! In practice a module is issued after 3 to 4 weeks! October 05, 2005 D. Ferrère, RD 05 Florence 9
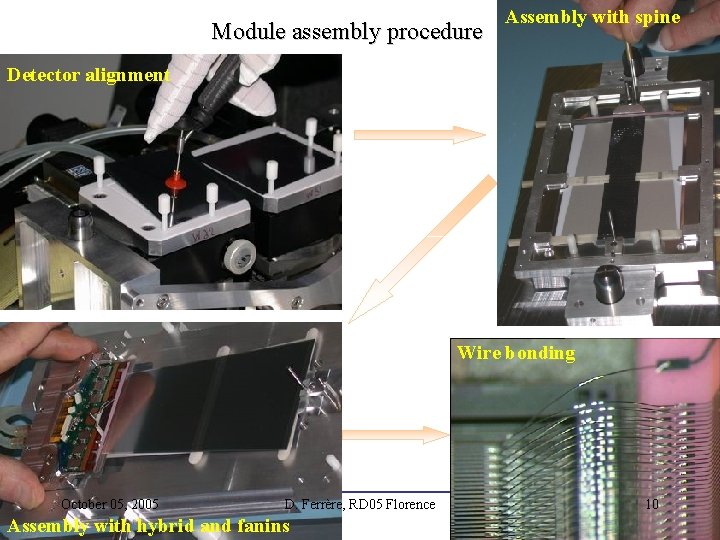
Module assembly procedure Assembly with spine Detector alignment Wire bonding October 05, 2005 D. Ferrère, RD 05 Florence Assembly with hybrid and fanins 10
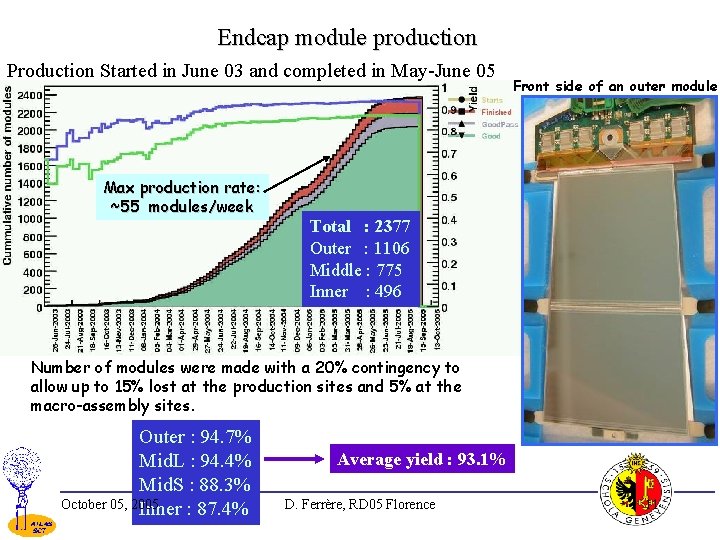
Endcap module production Production Started in June 03 and completed in May-June 05 Max production rate: ~55 modules/week Front side of an outer module Total : 2377 Outer : 1106 Middle : 775 Inner : 496 Number of modules were made with a 20% contingency to allow up to 15% lost at the production sites and 5% at the macro-assembly sites. Outer : 94. 7% Mid. L : 94. 4% Mid. S : 88. 3% October 05, 2005 Inner : 87. 4% Average yield : 93. 1% D. Ferrère, RD 05 Florence 11
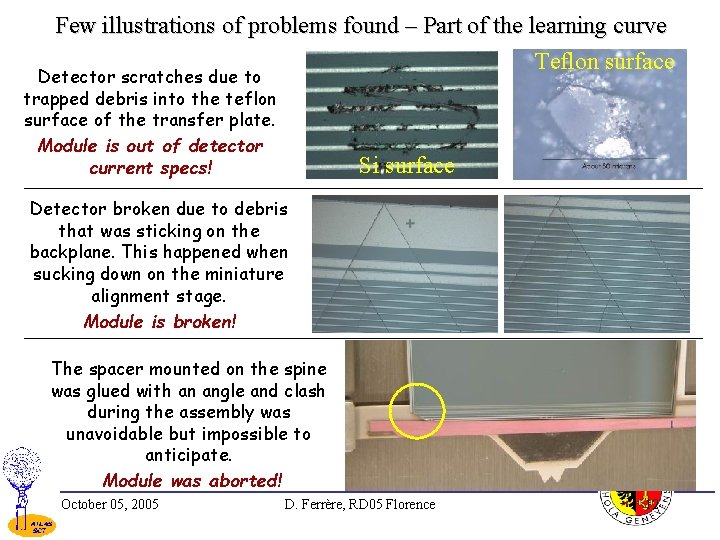
Few illustrations of problems found – Part of the learning curve Teflon surface Detector scratches due to trapped debris into the teflon surface of the transfer plate. Module is out of detector current specs! Si surface Detector broken due to debris that was sticking on the backplane. This happened when sucking down on the miniature alignment stage. Module is broken! The spacer mounted on the spine was glued with an angle and clash during the assembly was unavoidable but impossible to anticipate. Module was aborted! October 05, 2005 D. Ferrère, RD 05 Florence 12
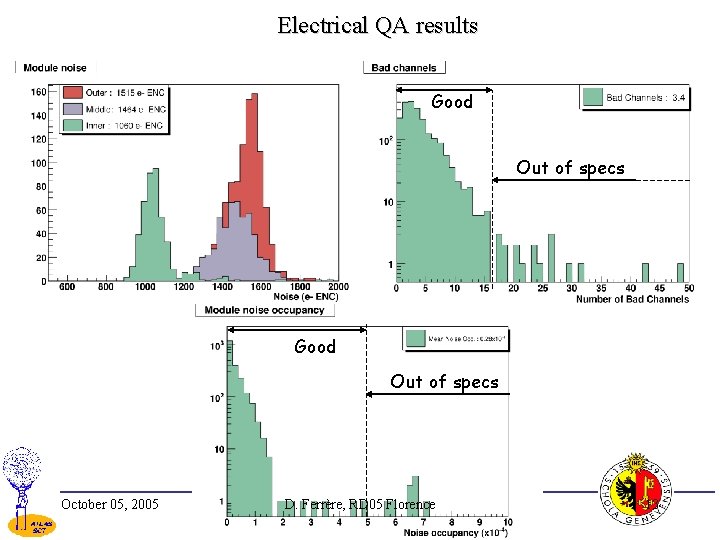
Electrical QA results Good Out of specs October 05, 2005 D. Ferrère, RD 05 Florence 13
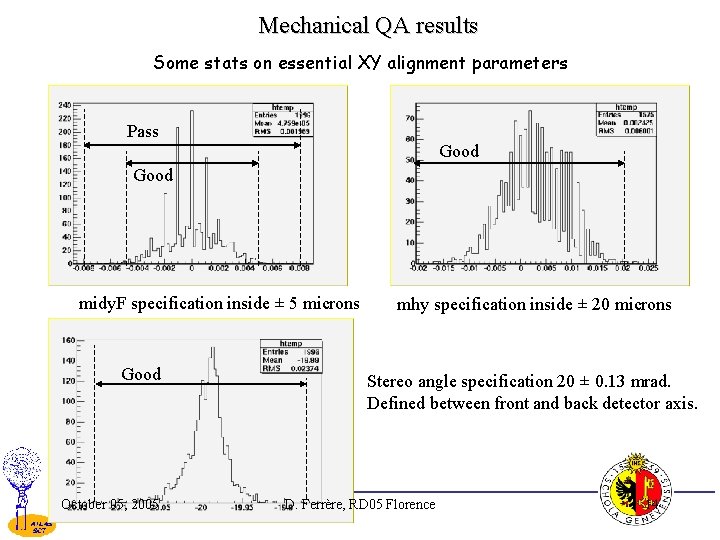
Mechanical QA results Some stats on essential XY alignment parameters Pass Good midy. F specification inside ± 5 microns Good October 05, 2005 mhy specification inside ± 20 microns Stereo angle specification 20 ± 0. 13 mrad. Defined between front and back detector axis. D. Ferrère, RD 05 Florence 14
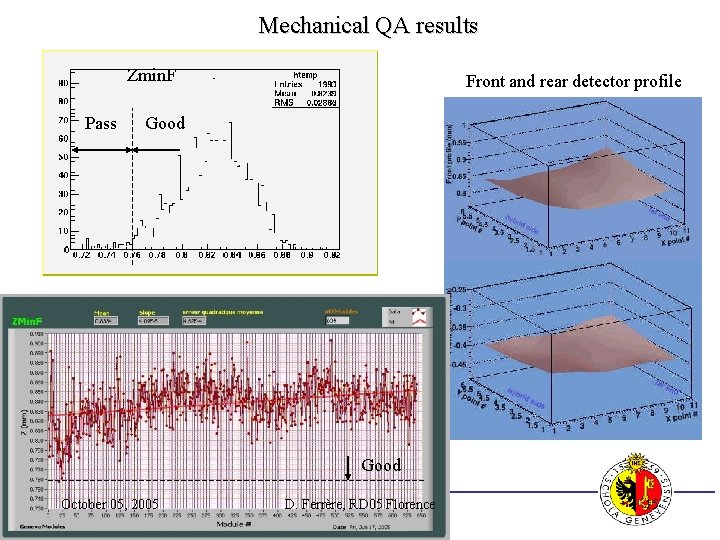
Mechanical QA results Zmin. F Pass Front and rear detector profile Good October 05, 2005 D. Ferrère, RD 05 Florence 15
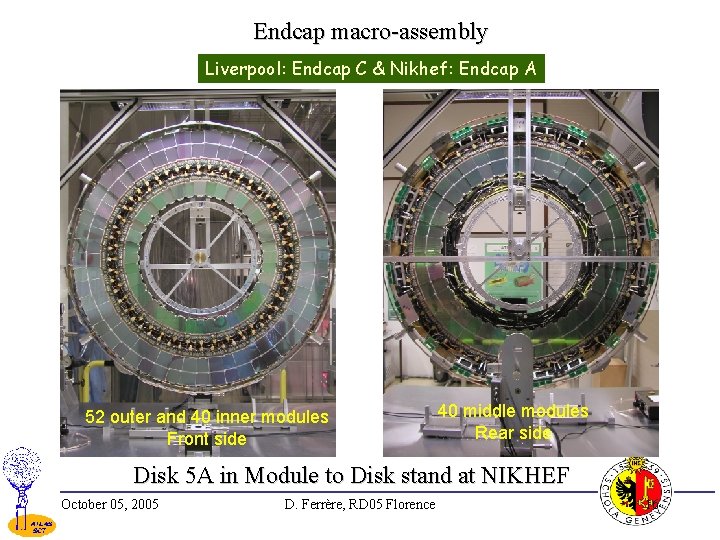
Endcap macro-assembly Liverpool: Endcap C & Nikhef: Endcap A 52 outer and 40 inner modules Front side 40 middle modules Rear side Disk 5 A in Module to Disk stand at NIKHEF October 05, 2005 D. Ferrère, RD 05 Florence 16
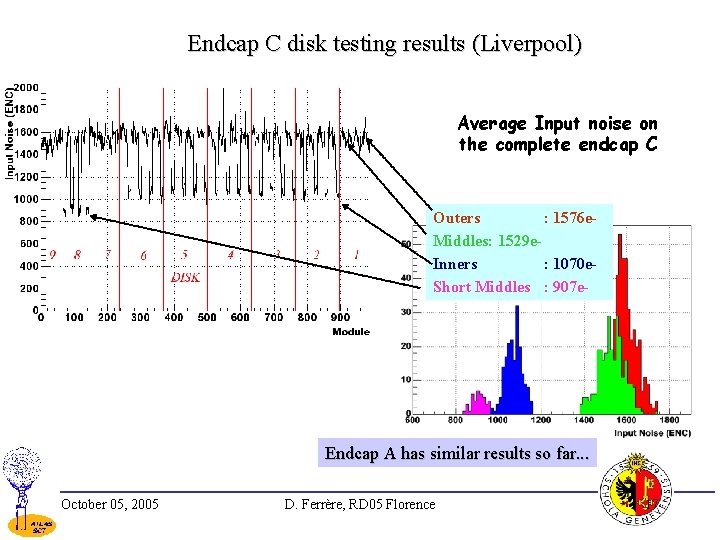
Endcap C disk testing results (Liverpool) Average Input noise on the complete endcap C Outers : 1576 e. Middles: 1529 e. Inners : 1070 e. Short Middles : 907 e- Endcap A has similar results so far. . . October 05, 2005 D. Ferrère, RD 05 Florence 17
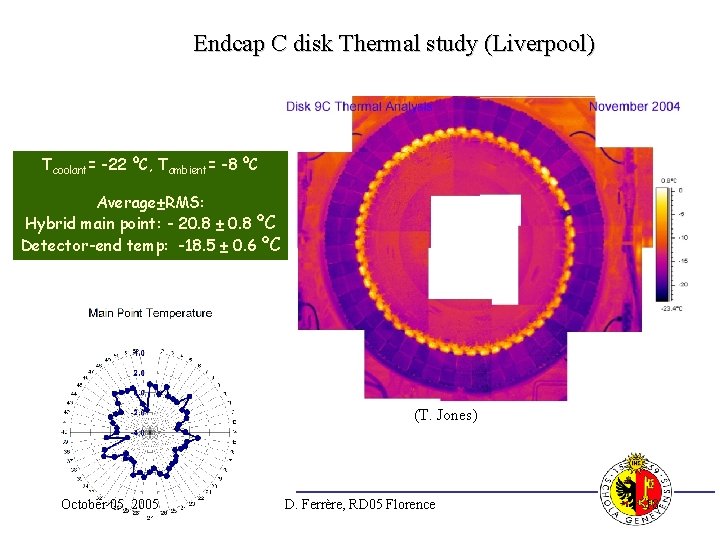
Endcap C disk Thermal study (Liverpool) Tcoolant= -22 ºC, Tambient= -8 ºC Average±RMS: Hybrid main point: - 20. 8 ± 0. 8 ºC Detector-end temp: -18. 5 ± 0. 6 ºC (T. Jones) October 05, 2005 D. Ferrère, RD 05 Florence 18
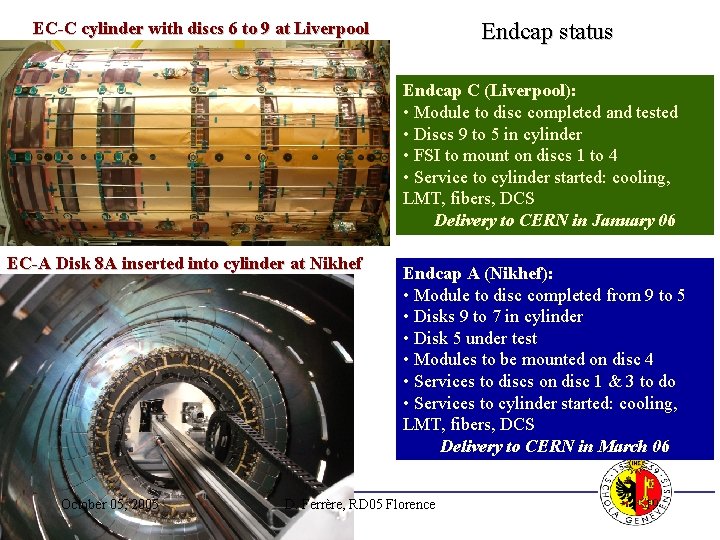
Endcap status EC-C cylinder with discs 6 to 9 at Liverpool Endcap C (Liverpool): • Module to disc completed and tested • Discs 9 to 5 in cylinder • FSI to mount on discs 1 to 4 • Service to cylinder started: cooling, LMT, fibers, DCS Delivery to CERN in January 06 EC-A Disk 8 A inserted into cylinder at Nikhef October 05, 2005 Endcap A (Nikhef): • Module to disc completed from 9 to 5 • Disks 9 to 7 in cylinder • Disk 5 under test • Modules to be mounted on disc 4 • Services to discs on disc 1 & 3 to do • Services to cylinder started: cooling, LMT, fibers, DCS Delivery to CERN in March 06 D. Ferrère, RD 05 Florence 19
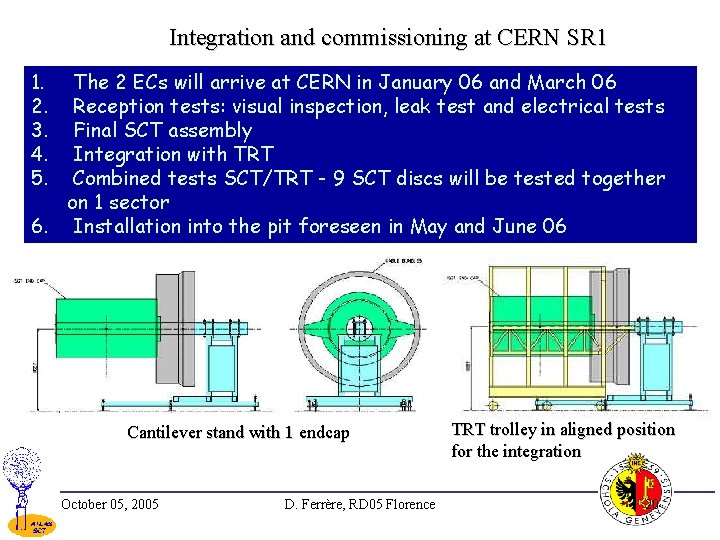
Integration and commissioning at CERN SR 1 1. 2. 3. 4. 5. The 2 ECs will arrive at CERN in January 06 and March 06 Reception tests: visual inspection, leak test and electrical tests Final SCT assembly Integration with TRT Combined tests SCT/TRT - 9 SCT discs will be tested together on 1 sector 6. Installation into the pit foreseen in May and June 06 Cantilever stand with 1 endcap October 05, 2005 D. Ferrère, RD 05 Florence TRT trolley in aligned position for the integration 20
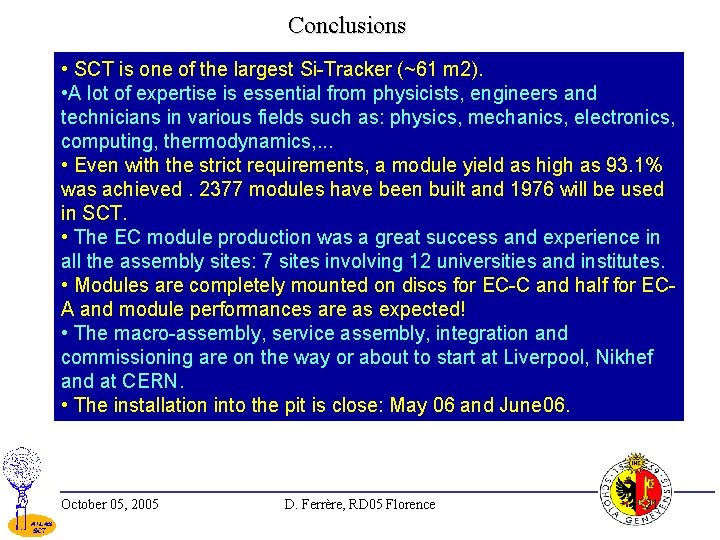
Conclusions • SCT is one of the largest Si-Tracker (~61 m 2). • A lot of expertise is essential from physicists, engineers and technicians in various fields such as: physics, mechanics, electronics, computing, thermodynamics, . . . • Even with the strict requirements, a module yield as high as 93. 1% was achieved. 2377 modules have been built and 1976 will be used in SCT. • The EC module production was a great success and experience in all the assembly sites: 7 sites involving 12 universities and institutes. • Modules are completely mounted on discs for EC-C and half for ECA and module performances are as expected! • The macro-assembly, service assembly, integration and commissioning are on the way or about to start at Liverpool, Nikhef and at CERN. • The installation into the pit is close: May 06 and June 06. October 05, 2005 D. Ferrère, RD 05 Florence 21
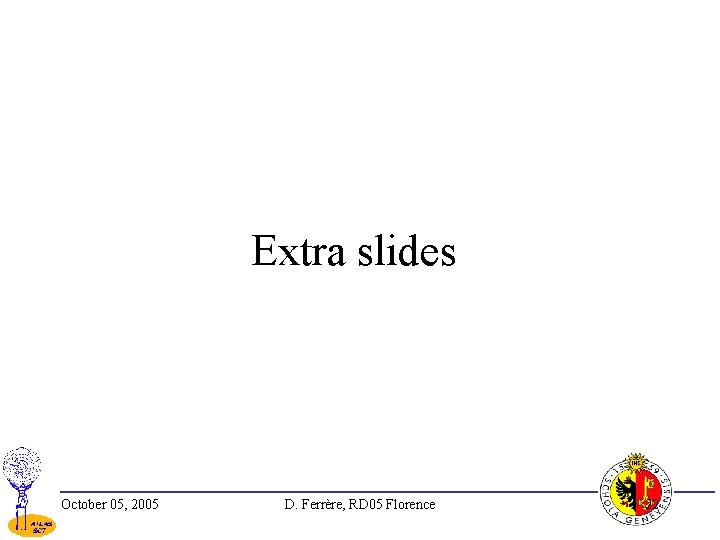
Extra slides October 05, 2005 D. Ferrère, RD 05 Florence 22
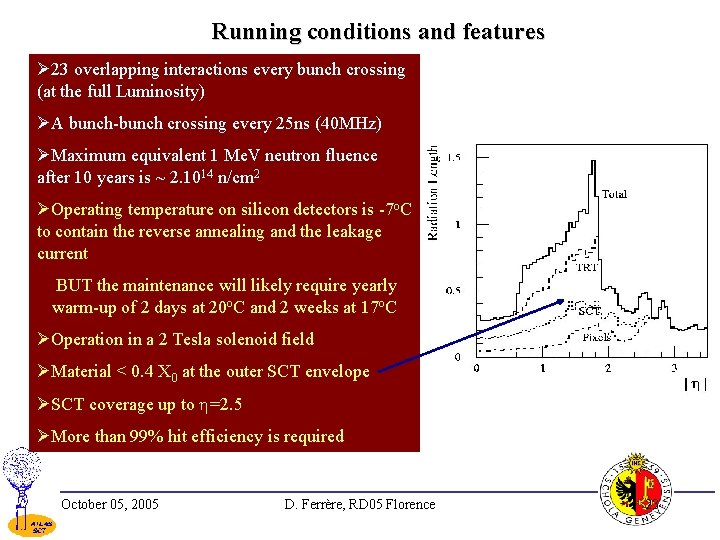
Running conditions and features Ø 23 overlapping interactions every bunch crossing (at the full Luminosity) ØA bunch-bunch crossing every 25 ns (40 MHz) ØMaximum equivalent 1 Me. V neutron fluence after 10 years is ~ 2. 1014 n/cm 2 ØOperating temperature on silicon detectors is -7 o. C to contain the reverse annealing and the leakage current BUT the maintenance will likely require yearly warm-up of 2 days at 20 o. C and 2 weeks at 17 o. C ØOperation in a 2 Tesla solenoid field ØMaterial < 0. 4 X 0 at the outer SCT envelope ØSCT coverage up to =2. 5 ØMore than 99% hit efficiency is required October 05, 2005 D. Ferrère, RD 05 Florence 23
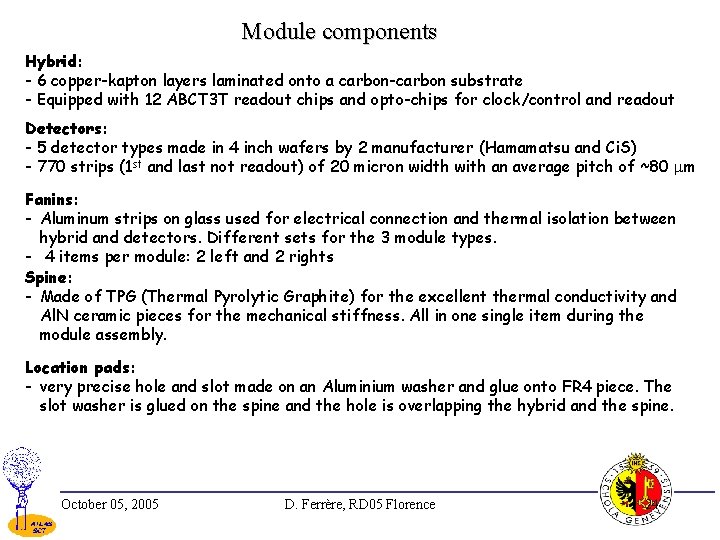
Module components Hybrid: - 6 copper-kapton layers laminated onto a carbon-carbon substrate - Equipped with 12 ABCT 3 T readout chips and opto-chips for clock/control and readout Detectors: - 5 detector types made in 4 inch wafers by 2 manufacturer (Hamamatsu and Ci. S) - 770 strips (1 st and last not readout) of 20 micron width with an average pitch of ~80 m Fanins: - Aluminum strips on glass used for electrical connection and thermal isolation between hybrid and detectors. Different sets for the 3 module types. - 4 items per module: 2 left and 2 rights Spine: - Made of TPG (Thermal Pyrolytic Graphite) for the excellent thermal conductivity and Al. N ceramic pieces for the mechanical stiffness. All in one single item during the module assembly. Location pads: - very precise hole and slot made on an Aluminium washer and glue onto FR 4 piece. The slot washer is glued on the spine and the hole is overlapping the hybrid and the spine. October 05, 2005 D. Ferrère, RD 05 Florence 24
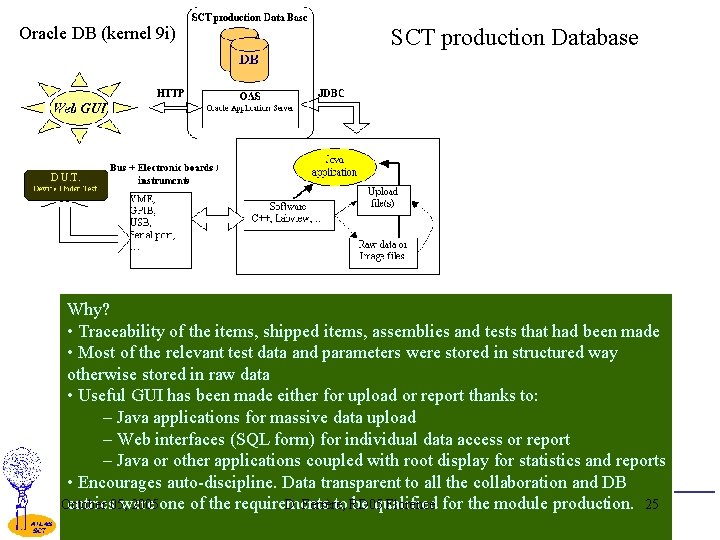
Oracle DB (kernel 9 i) SCT production Database Why? • Traceability of the items, shipped items, assemblies and tests that had been made • Most of the relevant test data and parameters were stored in structured way otherwise stored in raw data • Useful GUI has been made either for upload or report thanks to: – Java applications for massive data upload – Web interfaces (SQL form) for individual data access or report – Java or other applications coupled with root display for statistics and reports • Encourages auto-discipline. Data transparent to all the collaboration and DB October 2005 one of the requirements D. Ferrère, Florence for the module production. 25 entries 05, were to RD 05 be qualified
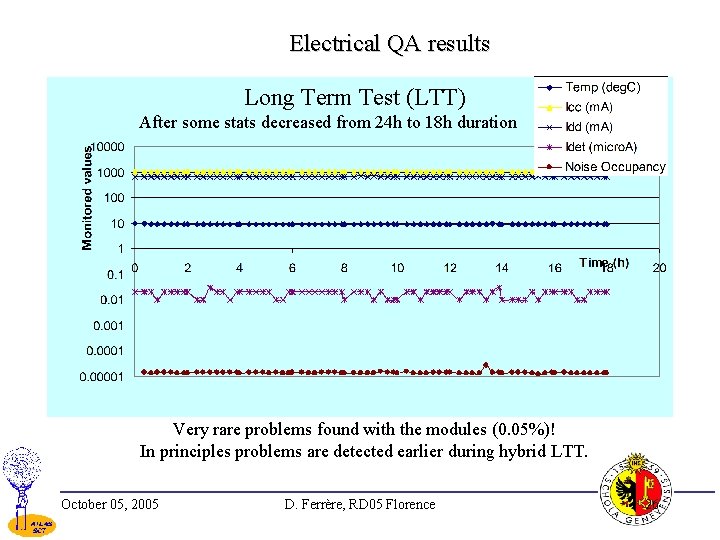
Electrical QA results Long Term Test (LTT) After some stats decreased from 24 h to 18 h duration Very rare problems found with the modules (0. 05%)! In principles problems are detected earlier during hybrid LTT. October 05, 2005 D. Ferrère, RD 05 Florence 26
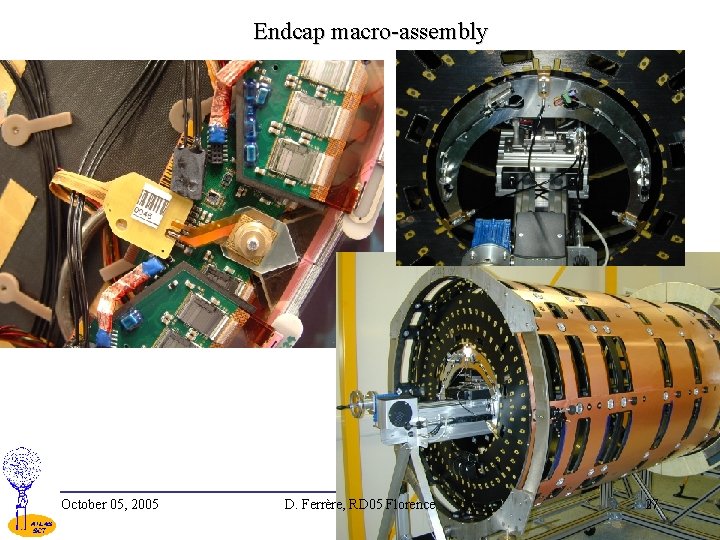
Endcap macro-assembly October 05, 2005 D. Ferrère, RD 05 Florence 27