FORMS OF CORROSION 1 Uniform or general attack
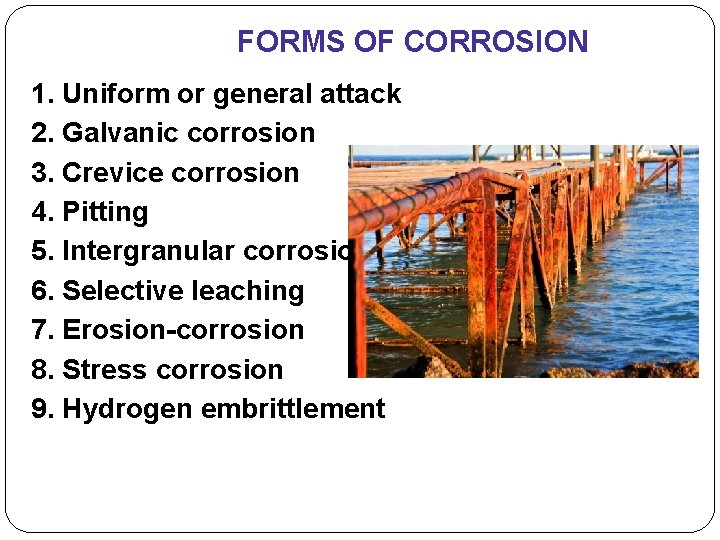
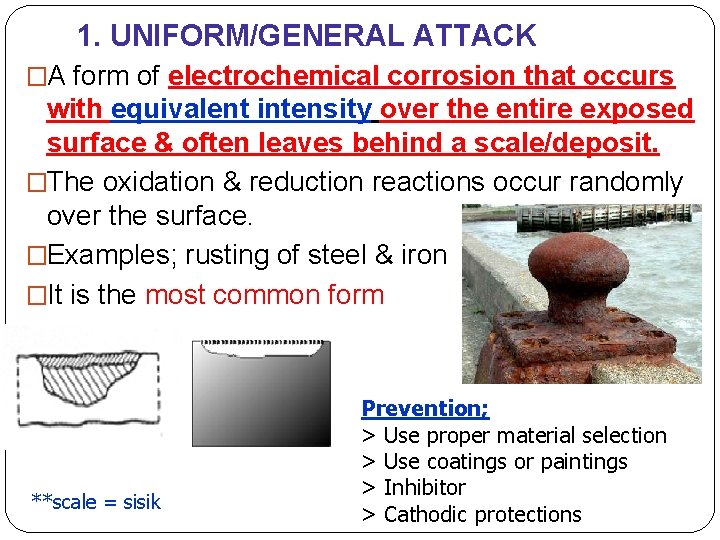
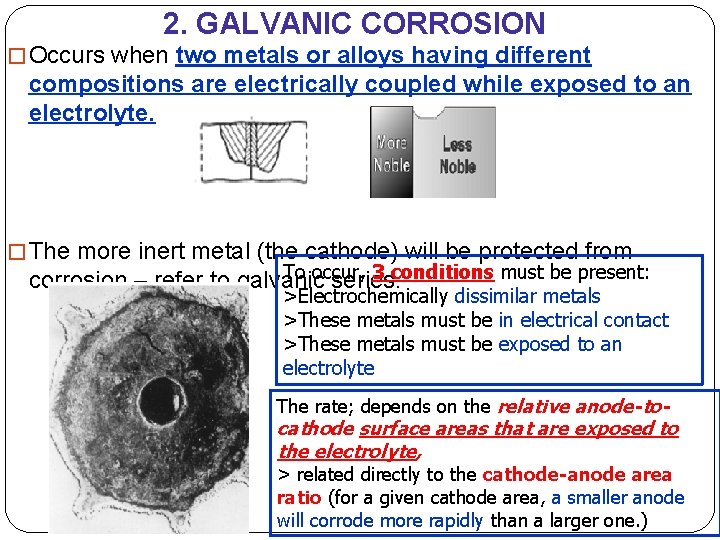
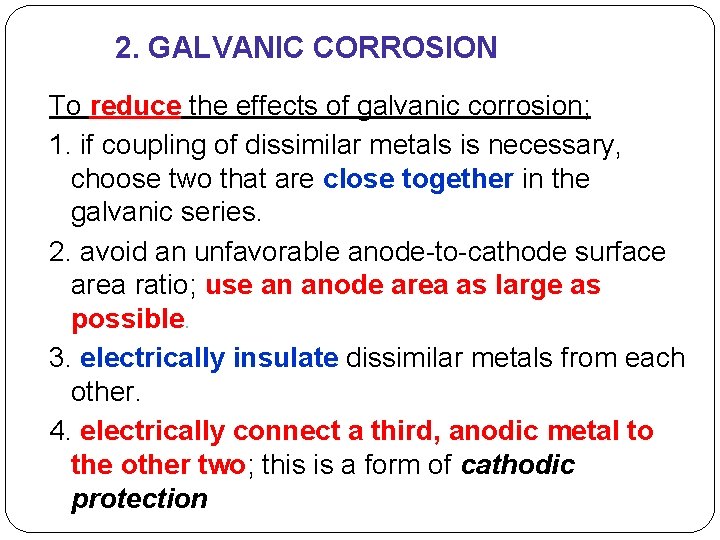

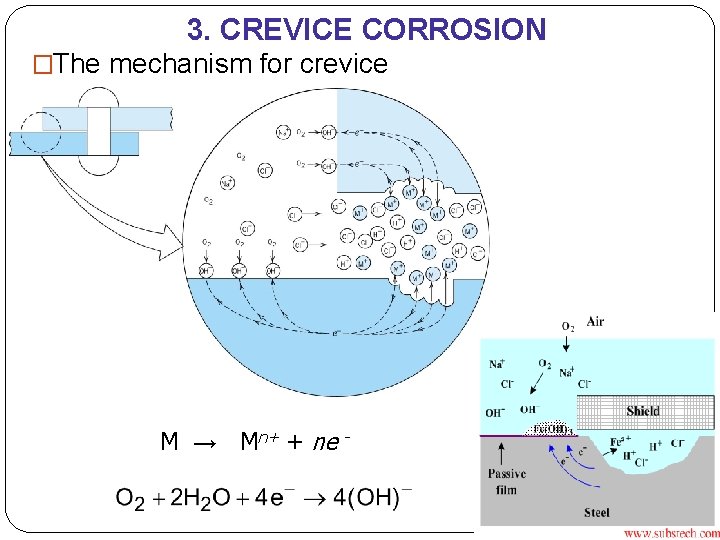
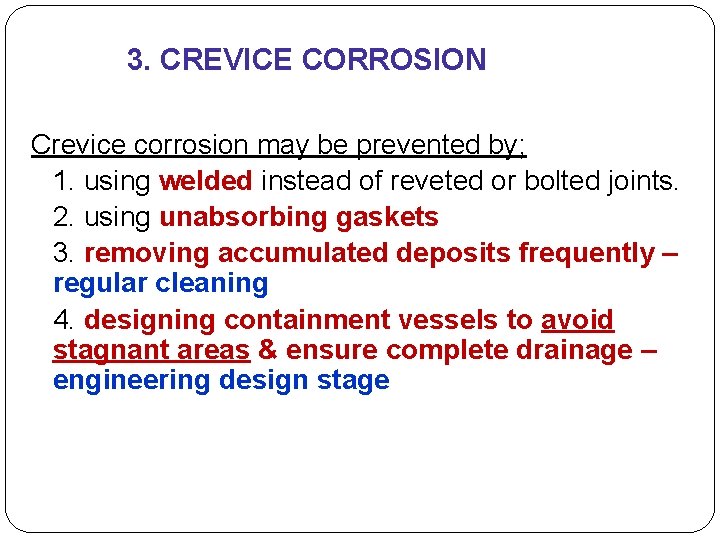
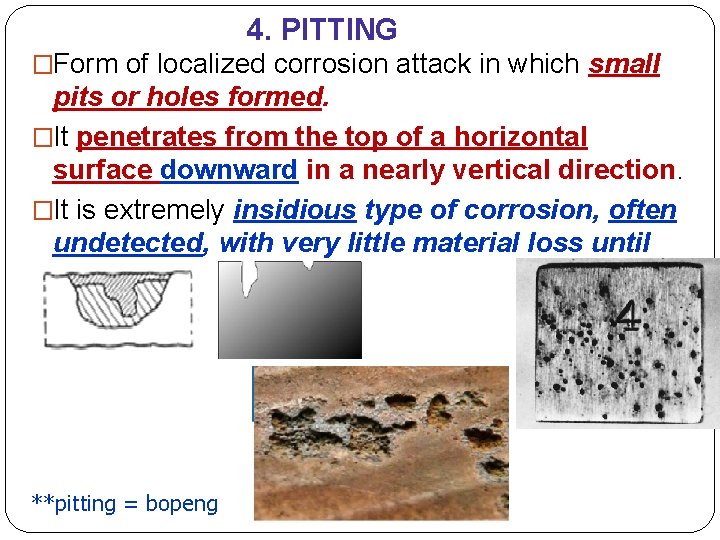
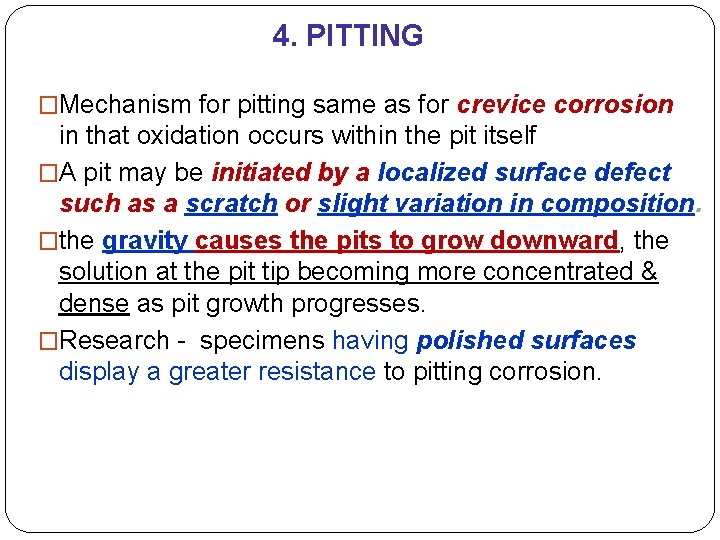
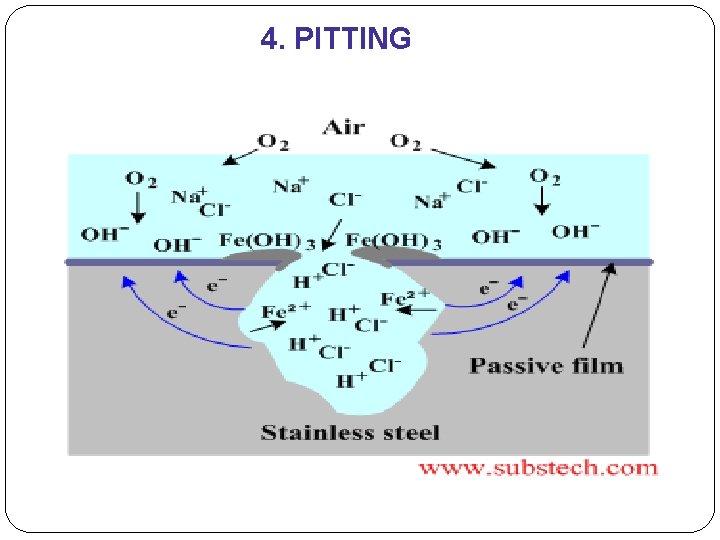
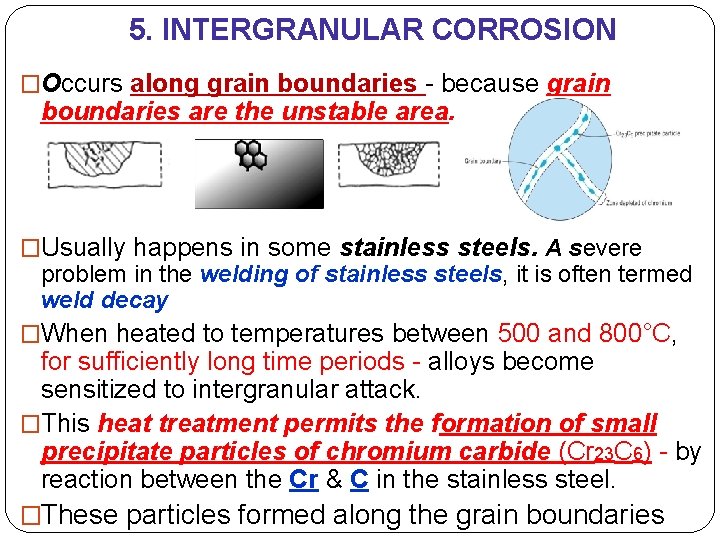
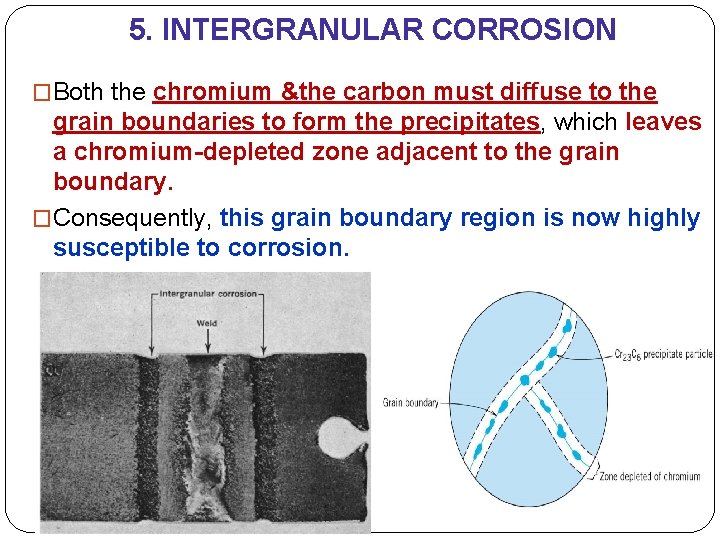
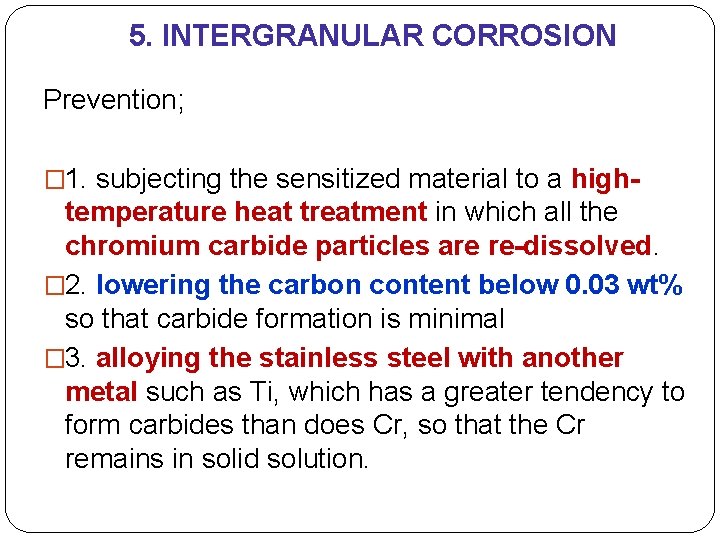
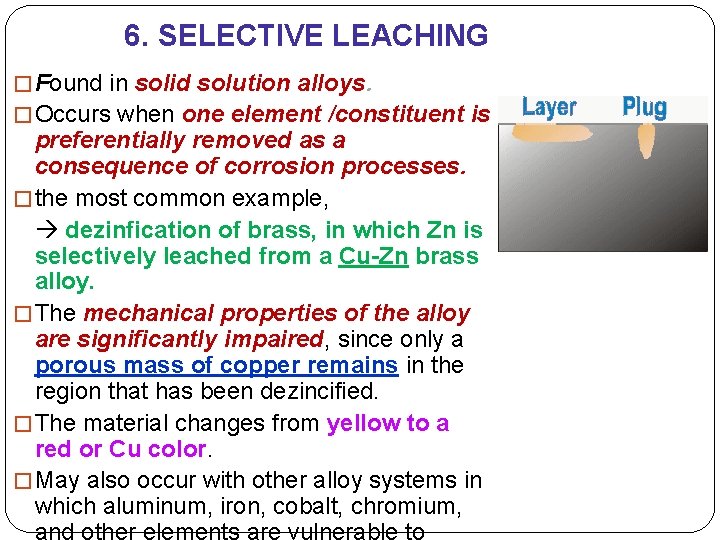
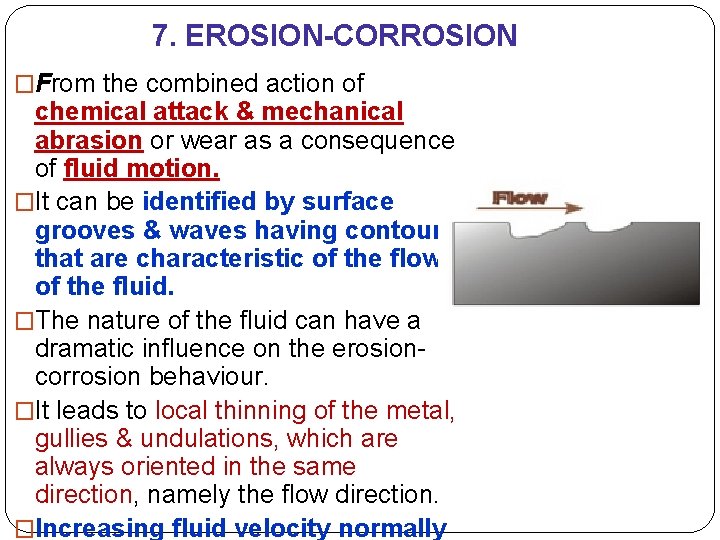
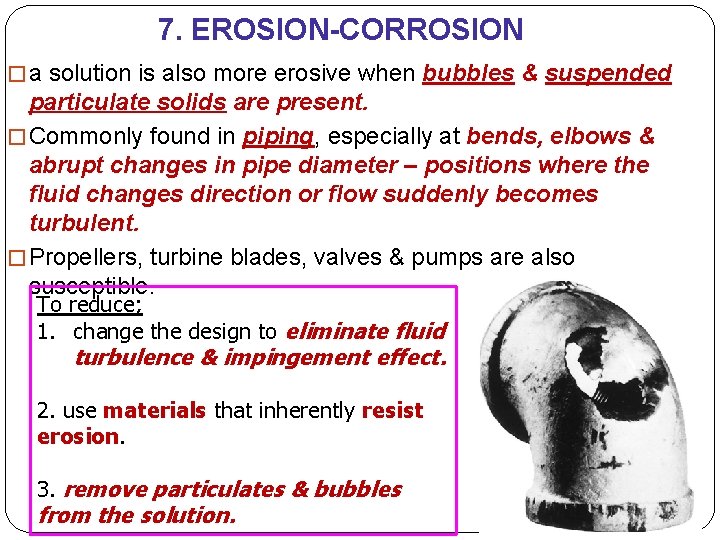
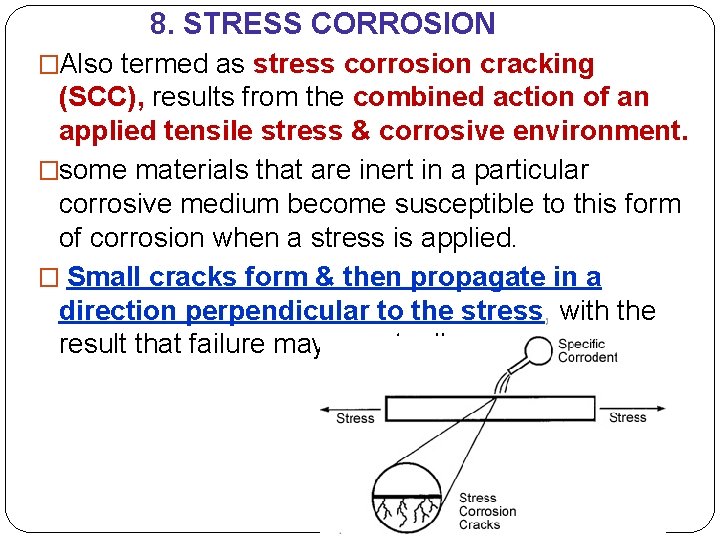
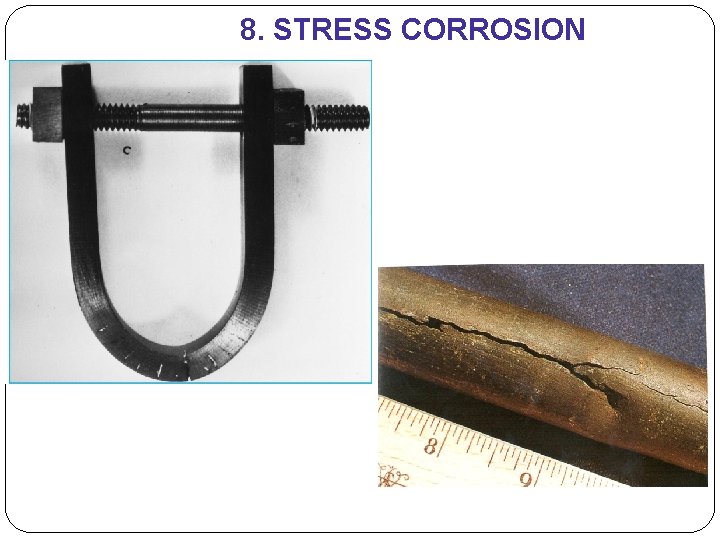
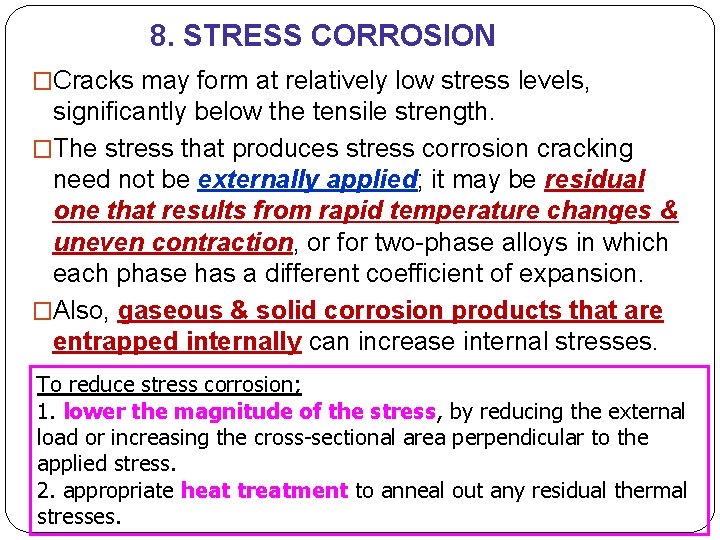
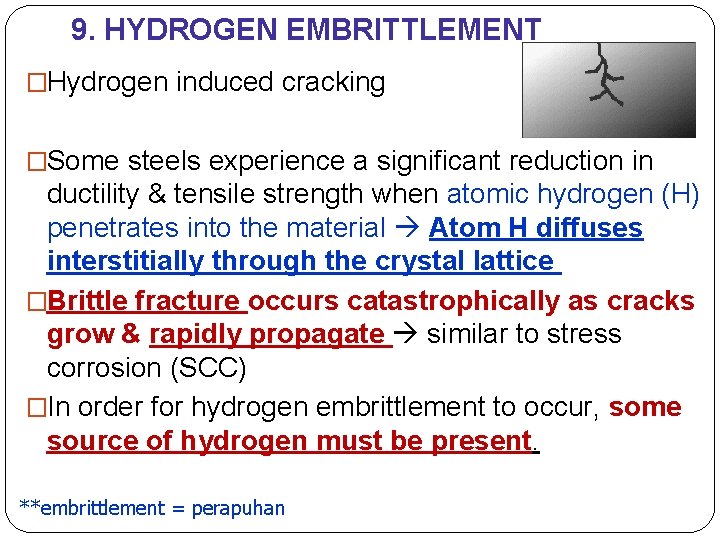
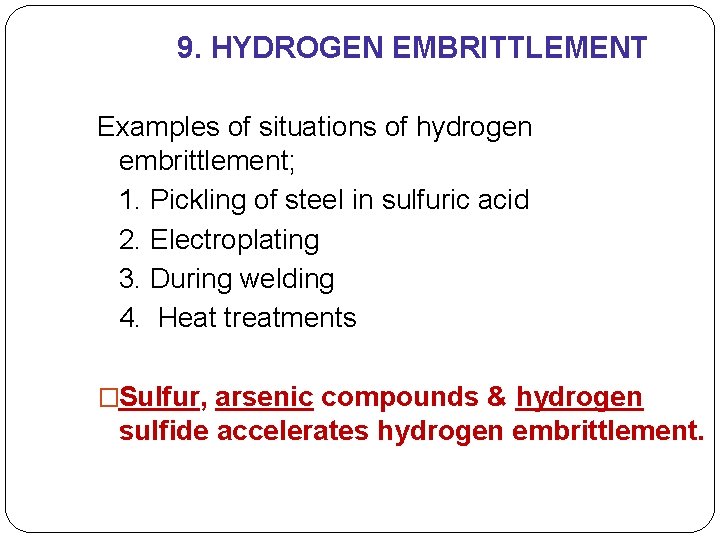
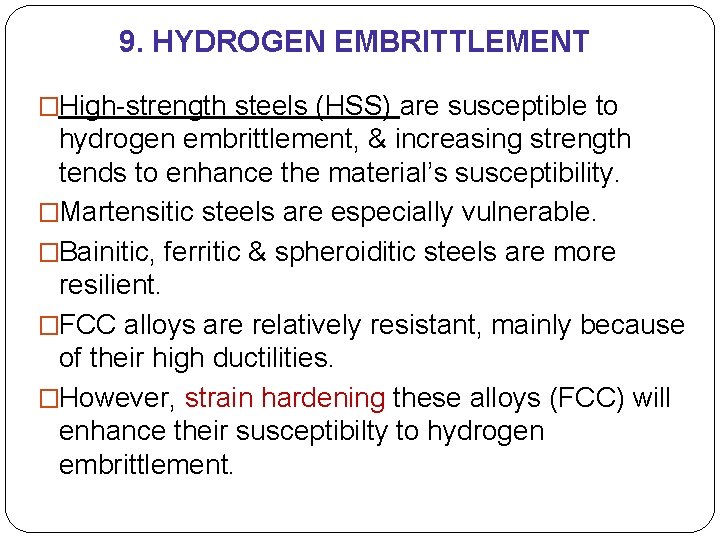
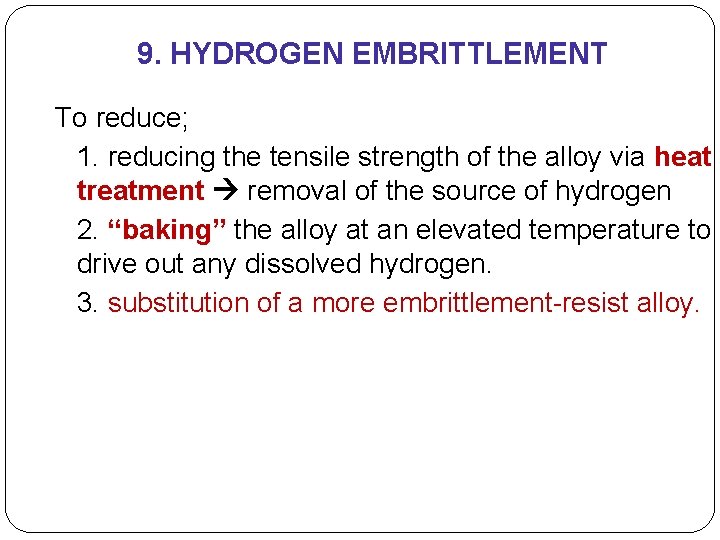
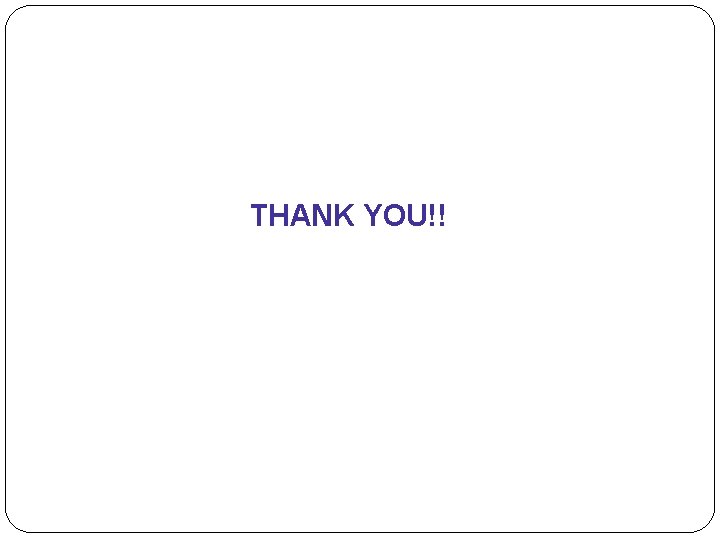
- Slides: 24
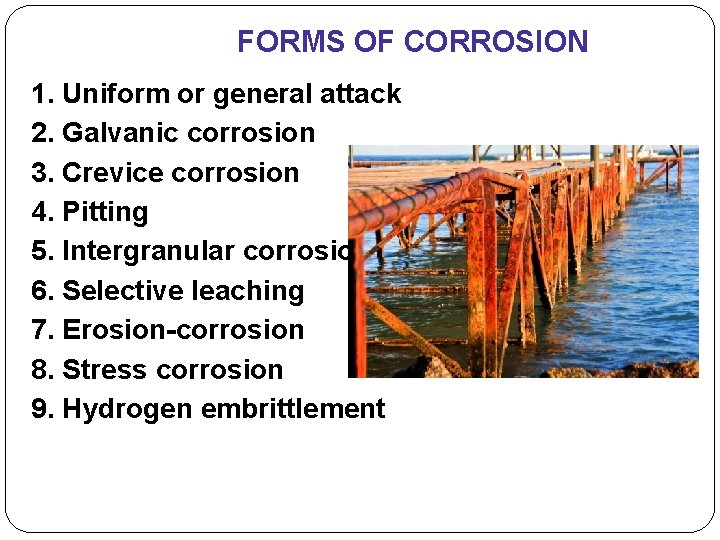
FORMS OF CORROSION 1. Uniform or general attack 2. Galvanic corrosion 3. Crevice corrosion 4. Pitting 5. Intergranular corrosion 6. Selective leaching 7. Erosion-corrosion 8. Stress corrosion 9. Hydrogen embrittlement
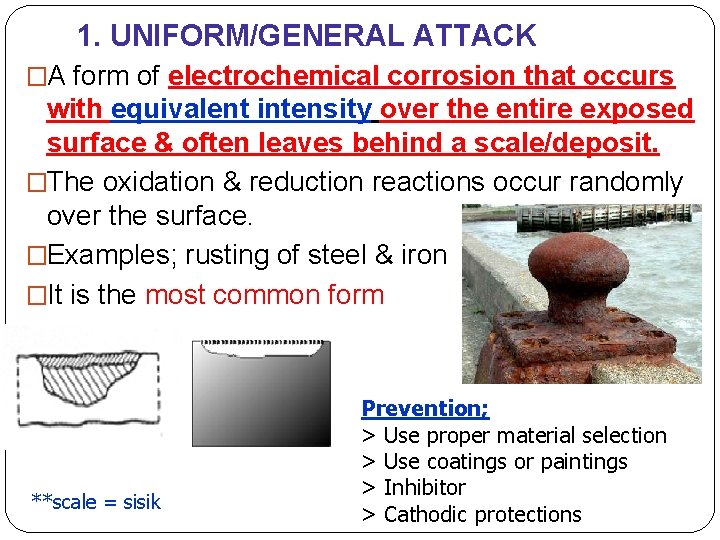
1. UNIFORM/GENERAL ATTACK �A form of electrochemical corrosion that occurs with equivalent intensity over the entire exposed surface & often leaves behind a scale/deposit. �The oxidation & reduction reactions occur randomly over the surface. �Examples; rusting of steel & iron �It is the most common form **scale = sisik Prevention; > Use proper material selection > Use coatings or paintings > Inhibitor > Cathodic protections
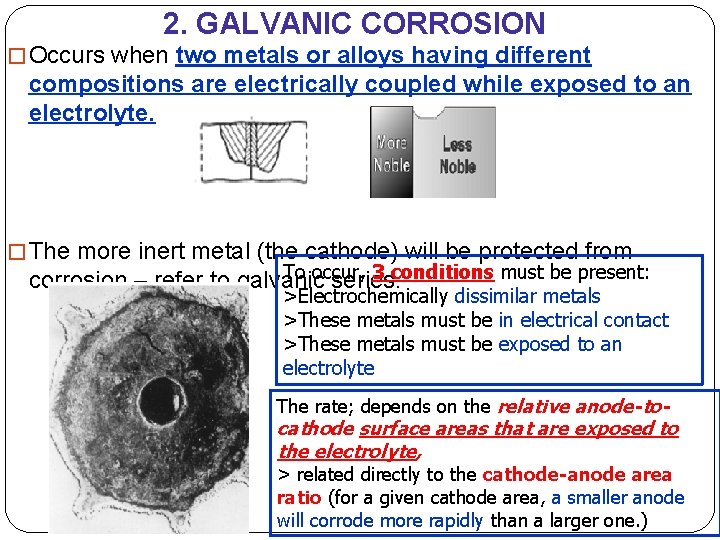
2. GALVANIC CORROSION � Occurs when two metals or alloys having different compositions are electrically coupled while exposed to an electrolyte. � The more inert metal (the cathode) will be protected from To occur, 3 conditions must be present: corrosion – refer to galvanic series. >Electrochemically dissimilar metals >These metals must be in electrical contact >These metals must be exposed to an electrolyte The rate; depends on the relative anode-to- cathode surface areas that are exposed to the electrolyte, > related directly to the cathode-anode area ratio (for a given cathode area, a smaller anode will corrode more rapidly than a larger one. )
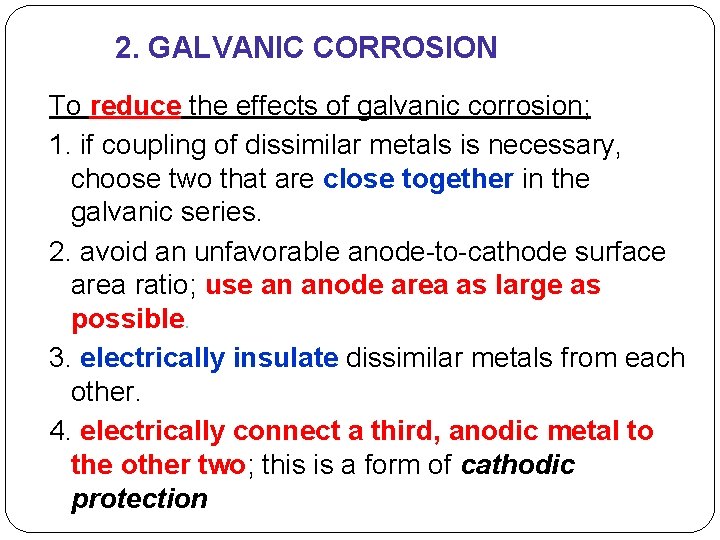
2. GALVANIC CORROSION To reduce the effects of galvanic corrosion; 1. if coupling of dissimilar metals is necessary, choose two that are close together in the galvanic series. 2. avoid an unfavorable anode-to-cathode surface area ratio; use an anode area as large as possible. 3. electrically insulate dissimilar metals from each other. 4. electrically connect a third, anodic metal to the other two; this is a form of cathodic protection

3. CREVICE CORROSION � Electrochemical corrosion may also occur as a consequence of concentration differences of ions or dissolved gasses in the electrolyte solution, and between two regions of the same metal piece concentration cell � Corrosion occurs in the locale that has the lower concentration. � Occurs in crevices & recesses or under deposits of dirt or corrosion products where the solution becomes stagnant & there is localized depletion of dissolved oxygen. � The crevice must be wide enough for the solution to penetrate, yet narrow enough for stagnancy; usually the width is several thousandth of an inch. **crevice = celahan
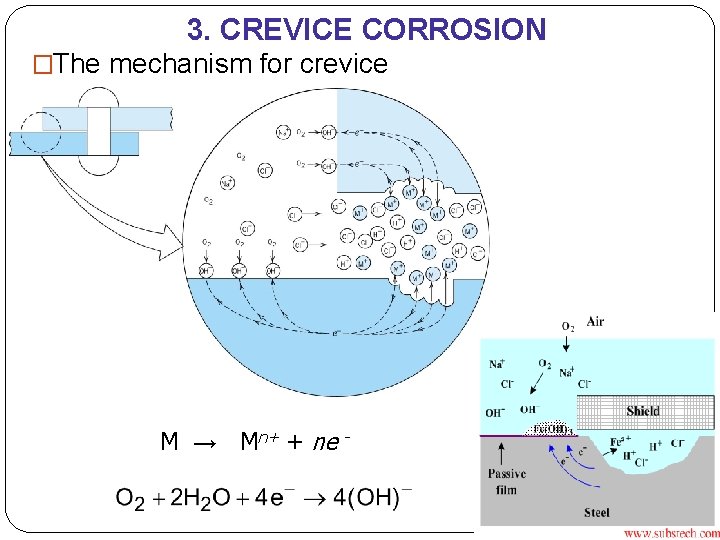
3. CREVICE CORROSION �The mechanism for crevice M → Mn+ + ne -
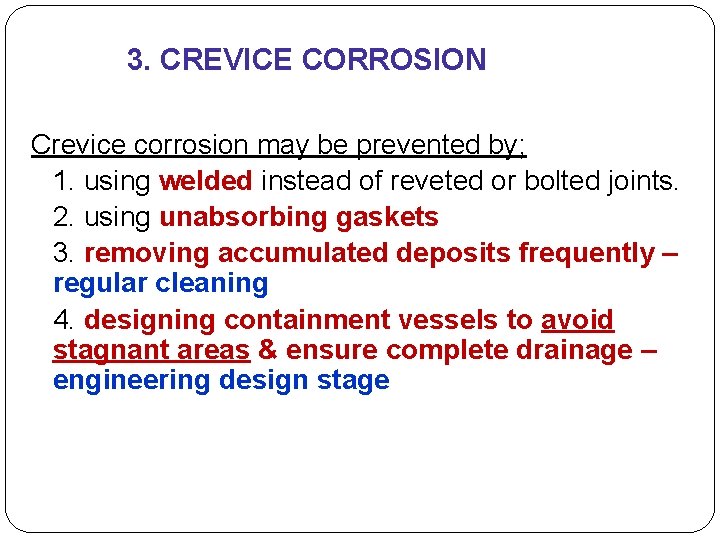
3. CREVICE CORROSION Crevice corrosion may be prevented by; 1. using welded instead of reveted or bolted joints. 2. using unabsorbing gaskets 3. removing accumulated deposits frequently – regular cleaning 4. designing containment vessels to avoid stagnant areas & ensure complete drainage – engineering design stage
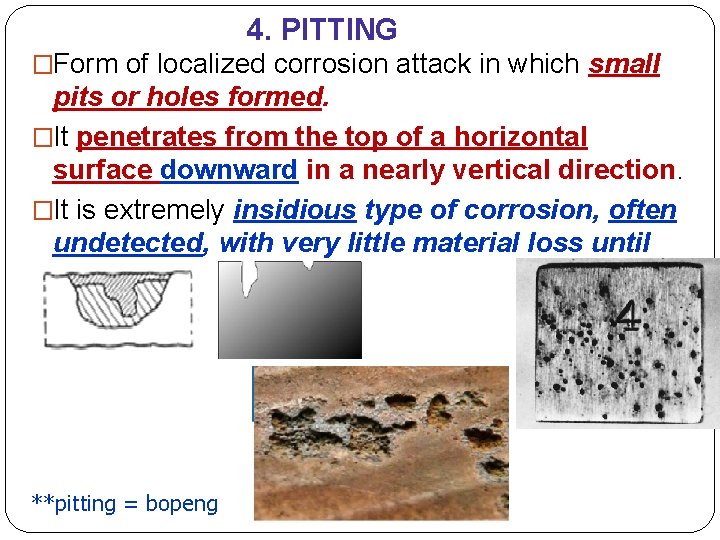
4. PITTING �Form of localized corrosion attack in which small pits or holes formed. �It penetrates from the top of a horizontal surface downward in a nearly vertical direction. �It is extremely insidious type of corrosion, often undetected, with very little material loss until failure occurs. **pitting = bopeng
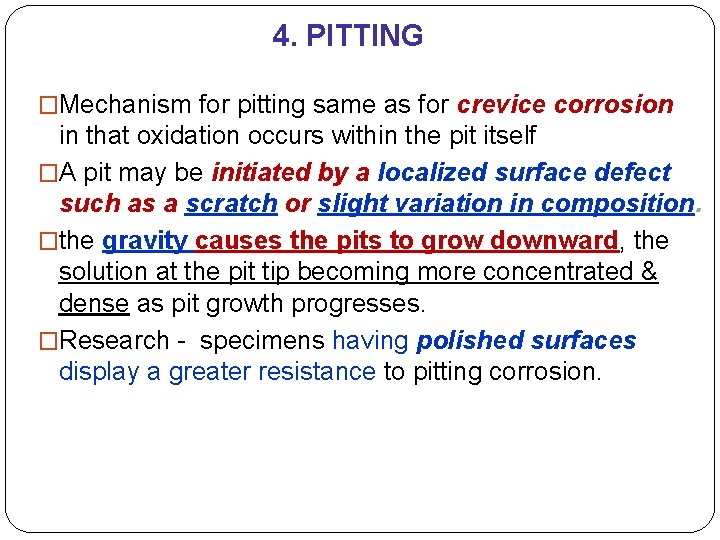
4. PITTING �Mechanism for pitting same as for crevice corrosion in that oxidation occurs within the pit itself �A pit may be initiated by a localized surface defect such as a scratch or slight variation in composition. �the gravity causes the pits to grow downward, the solution at the pit tip becoming more concentrated & dense as pit growth progresses. �Research - specimens having polished surfaces display a greater resistance to pitting corrosion.
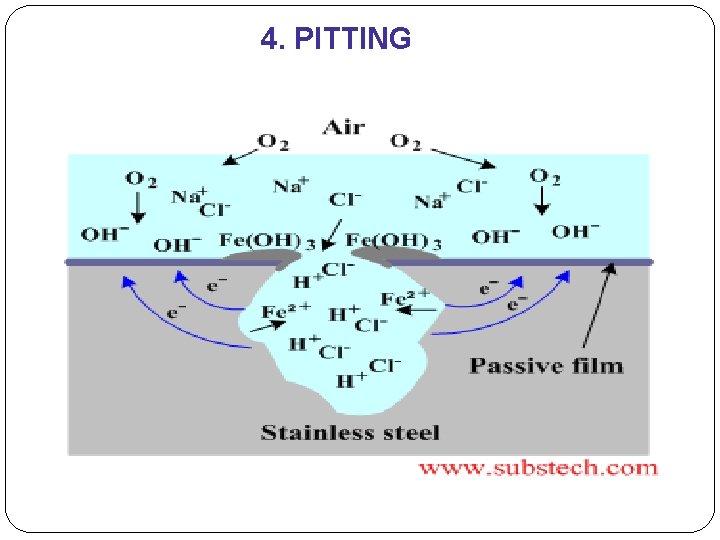
4. PITTING
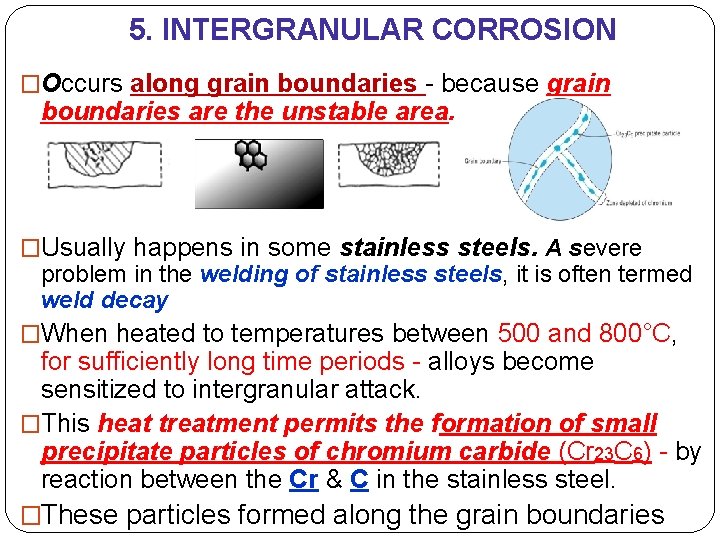
5. INTERGRANULAR CORROSION �Occurs along grain boundaries - because grain boundaries are the unstable area. �Usually happens in some stainless steels. A severe problem in the welding of stainless steels, it is often termed weld decay �When heated to temperatures between 500 and 800°C, for sufficiently long time periods - alloys become sensitized to intergranular attack. �This heat treatment permits the formation of small precipitate particles of chromium carbide (Cr 23 C 6) - by reaction between the Cr & C in the stainless steel. �These particles formed along the grain boundaries
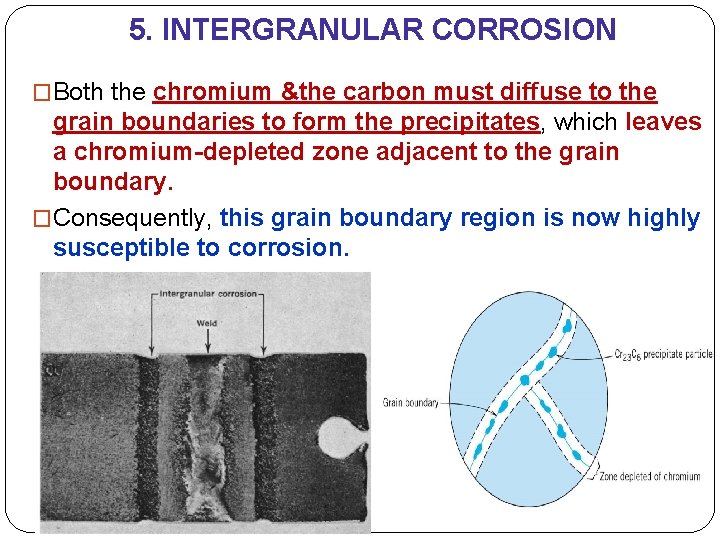
5. INTERGRANULAR CORROSION �Both the chromium &the carbon must diffuse to the grain boundaries to form the precipitates, which leaves a chromium-depleted zone adjacent to the grain boundary. �Consequently, this grain boundary region is now highly susceptible to corrosion.
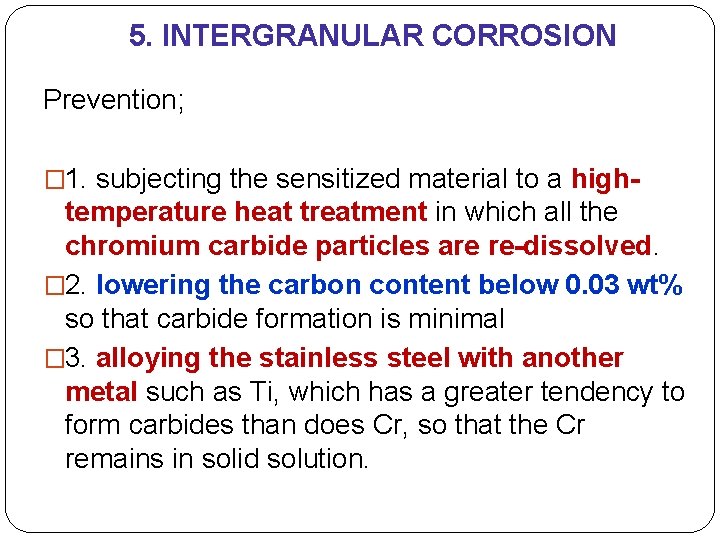
5. INTERGRANULAR CORROSION Prevention; � 1. subjecting the sensitized material to a high- temperature heat treatment in which all the chromium carbide particles are re-dissolved. � 2. lowering the carbon content below 0. 03 wt% so that carbide formation is minimal � 3. alloying the stainless steel with another metal such as Ti, which has a greater tendency to form carbides than does Cr, so that the Cr remains in solid solution.
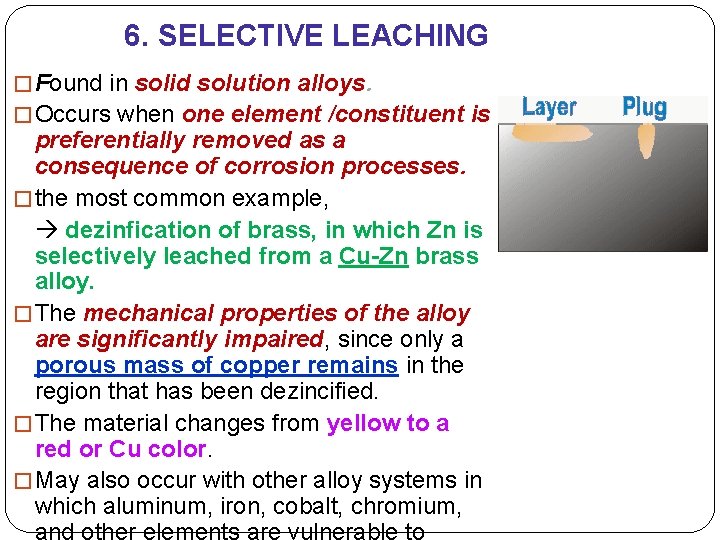
6. SELECTIVE LEACHING � Found in solid solution alloys. � Occurs when one element /constituent is preferentially removed as a consequence of corrosion processes. � the most common example, dezinfication of brass, in which Zn is selectively leached from a Cu-Zn brass alloy. � The mechanical properties of the alloy are significantly impaired, since only a porous mass of copper remains in the region that has been dezincified. � The material changes from yellow to a red or Cu color. � May also occur with other alloy systems in which aluminum, iron, cobalt, chromium,
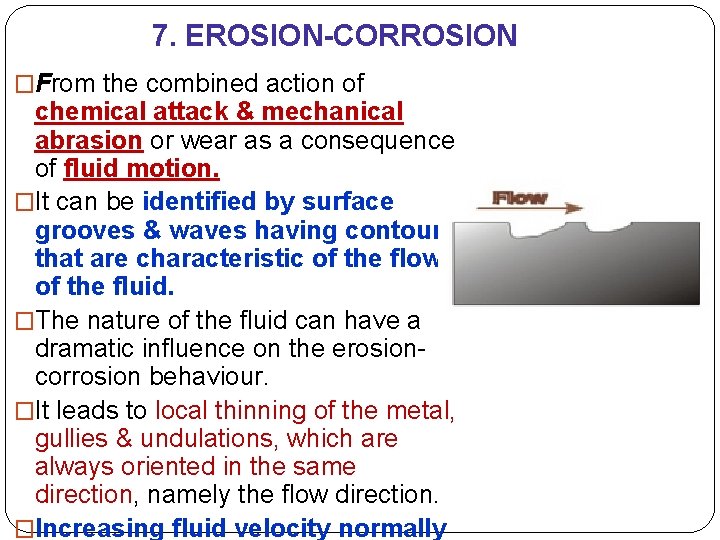
7. EROSION-CORROSION �From the combined action of chemical attack & mechanical abrasion or wear as a consequence of fluid motion. �It can be identified by surface grooves & waves having contours that are characteristic of the flow of the fluid. �The nature of the fluid can have a dramatic influence on the erosioncorrosion behaviour. �It leads to local thinning of the metal, gullies & undulations, which are always oriented in the same direction, namely the flow direction. �Increasing fluid velocity normally
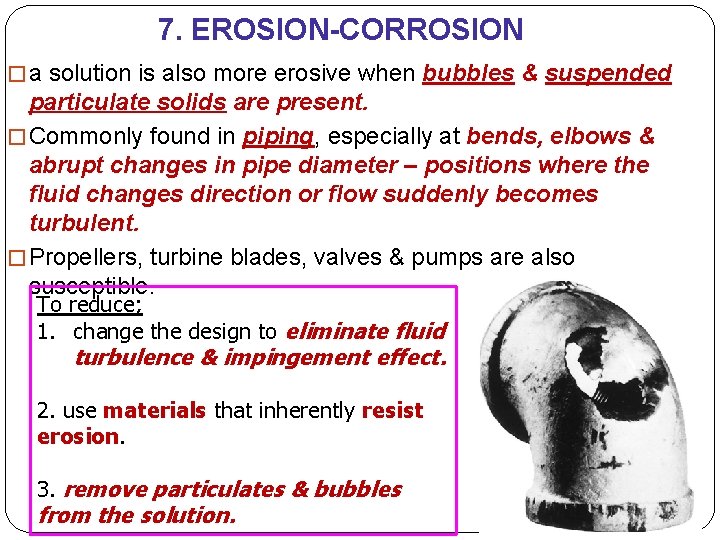
7. EROSION-CORROSION � a solution is also more erosive when bubbles & suspended particulate solids are present. � Commonly found in piping, especially at bends, elbows & abrupt changes in pipe diameter – positions where the fluid changes direction or flow suddenly becomes turbulent. � Propellers, turbine blades, valves & pumps are also susceptible. To reduce; 1. change the design to eliminate fluid turbulence & impingement effect. 2. use materials that inherently resist erosion. 3. remove particulates & bubbles from the solution.
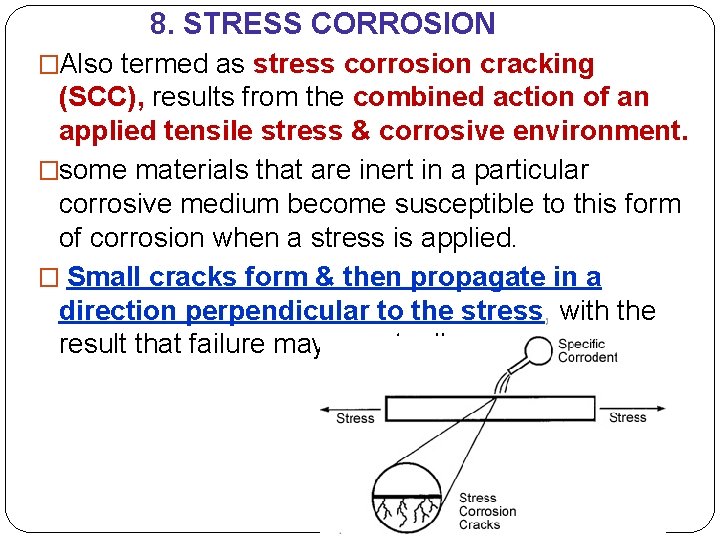
8. STRESS CORROSION �Also termed as stress corrosion cracking (SCC), results from the combined action of an applied tensile stress & corrosive environment. �some materials that are inert in a particular corrosive medium become susceptible to this form of corrosion when a stress is applied. � Small cracks form & then propagate in a direction perpendicular to the stress, with the result that failure may eventually occur.
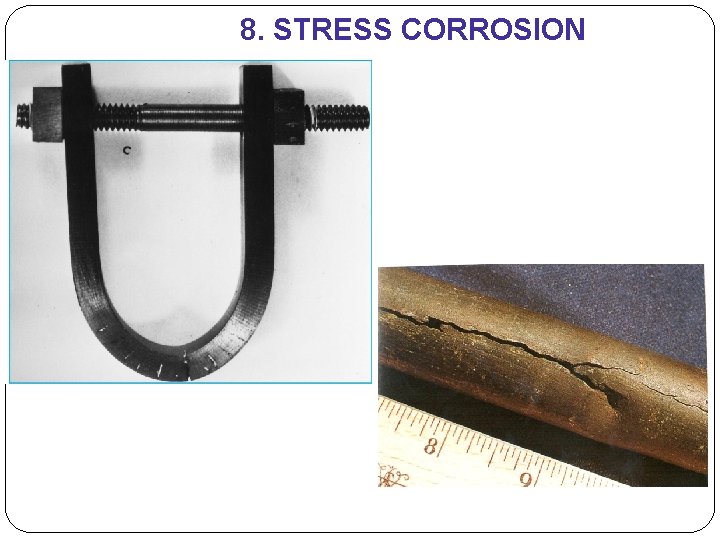
8. STRESS CORROSION
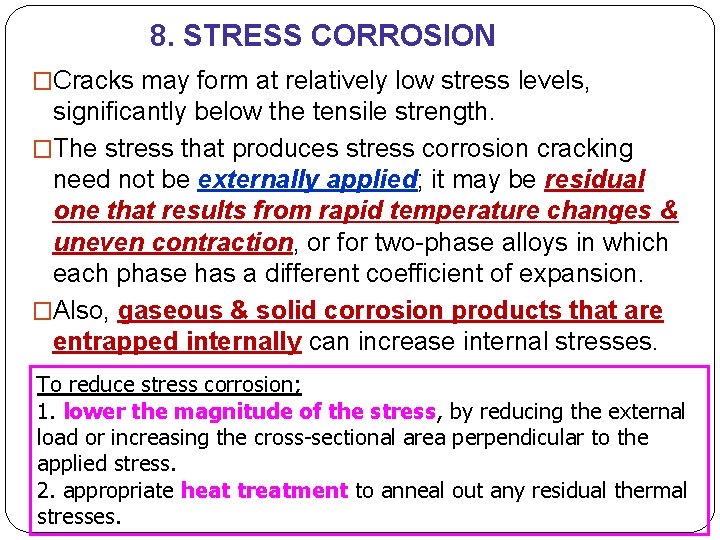
8. STRESS CORROSION �Cracks may form at relatively low stress levels, significantly below the tensile strength. �The stress that produces stress corrosion cracking need not be externally applied; it may be residual one that results from rapid temperature changes & uneven contraction, or for two-phase alloys in which each phase has a different coefficient of expansion. �Also, gaseous & solid corrosion products that are entrapped internally can increase internal stresses. To reduce stress corrosion; 1. lower the magnitude of the stress, by reducing the external load or increasing the cross-sectional area perpendicular to the applied stress. 2. appropriate heat treatment to anneal out any residual thermal stresses.
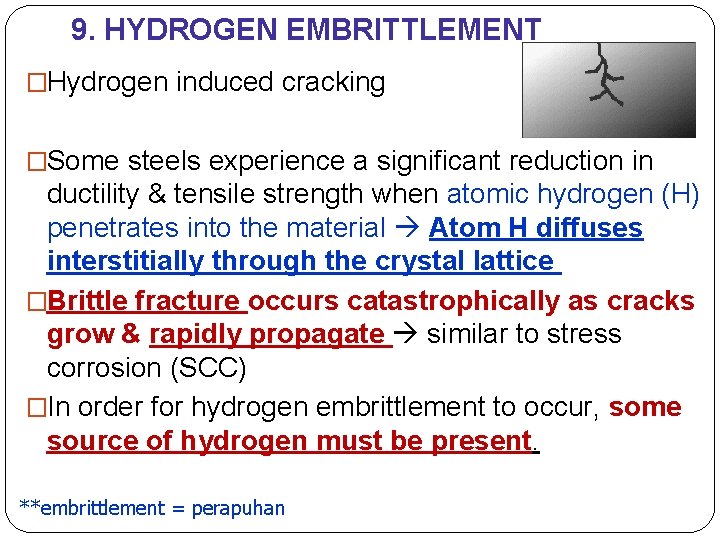
9. HYDROGEN EMBRITTLEMENT �Hydrogen induced cracking �Some steels experience a significant reduction in ductility & tensile strength when atomic hydrogen (H) penetrates into the material Atom H diffuses interstitially through the crystal lattice �Brittle fracture occurs catastrophically as cracks grow & rapidly propagate similar to stress corrosion (SCC) �In order for hydrogen embrittlement to occur, some source of hydrogen must be present. **embrittlement = perapuhan
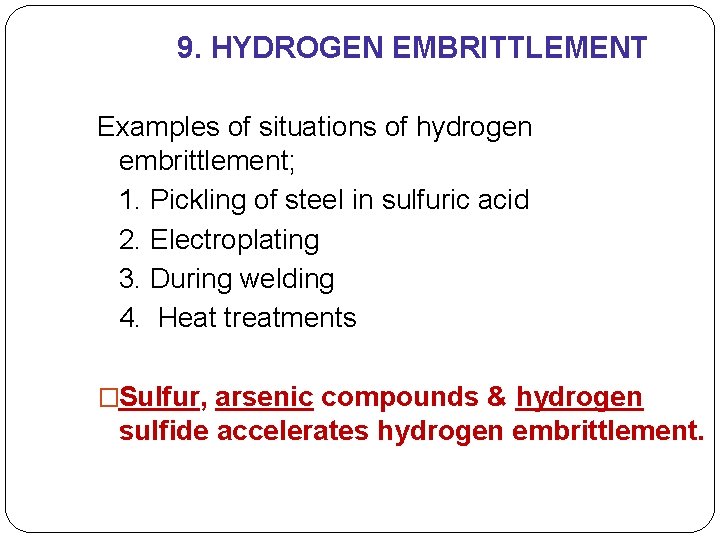
9. HYDROGEN EMBRITTLEMENT Examples of situations of hydrogen embrittlement; 1. Pickling of steel in sulfuric acid 2. Electroplating 3. During welding 4. Heat treatments �Sulfur, arsenic compounds & hydrogen sulfide accelerates hydrogen embrittlement.
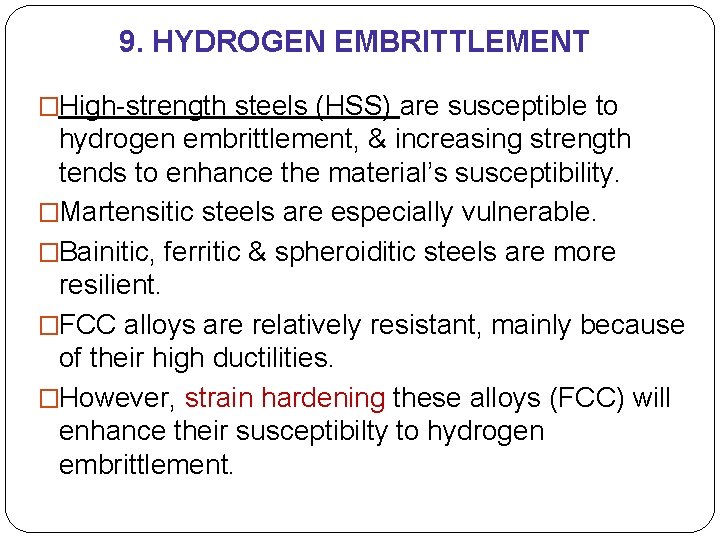
9. HYDROGEN EMBRITTLEMENT �High-strength steels (HSS) are susceptible to hydrogen embrittlement, & increasing strength tends to enhance the material’s susceptibility. �Martensitic steels are especially vulnerable. �Bainitic, ferritic & spheroiditic steels are more resilient. �FCC alloys are relatively resistant, mainly because of their high ductilities. �However, strain hardening these alloys (FCC) will enhance their susceptibilty to hydrogen embrittlement.
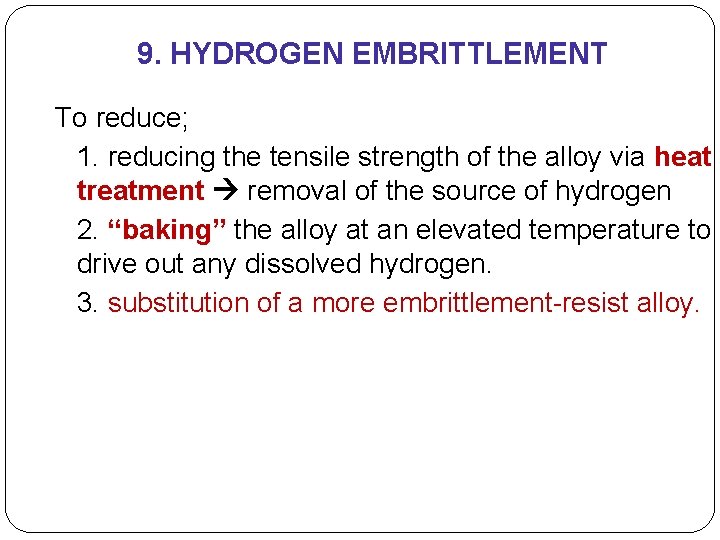
9. HYDROGEN EMBRITTLEMENT To reduce; 1. reducing the tensile strength of the alloy via heat treatment removal of the source of hydrogen 2. “baking” the alloy at an elevated temperature to drive out any dissolved hydrogen. 3. substitution of a more embrittlement-resist alloy.
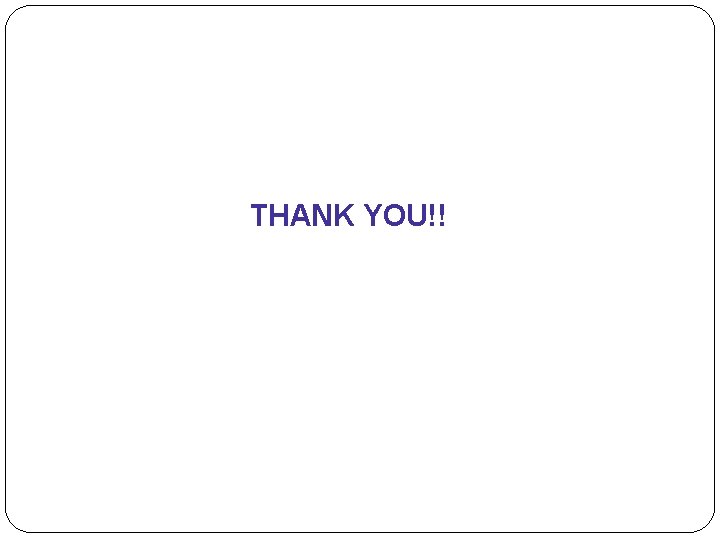
THANK YOU!!