Environmental concerns are driving the development of the
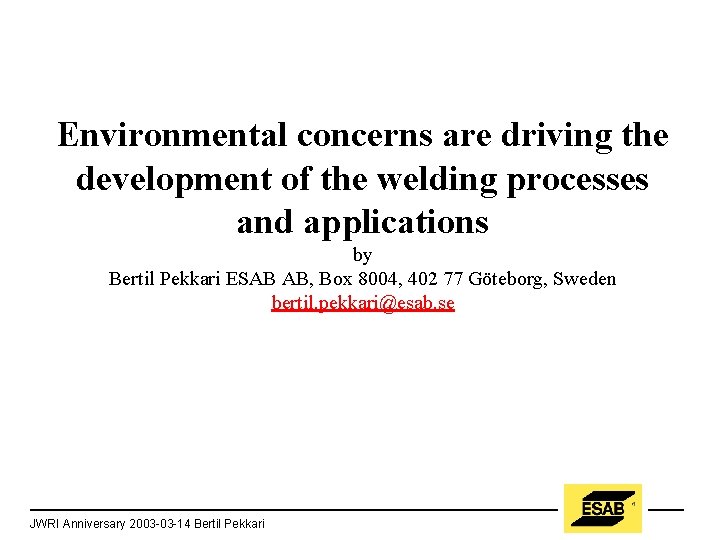
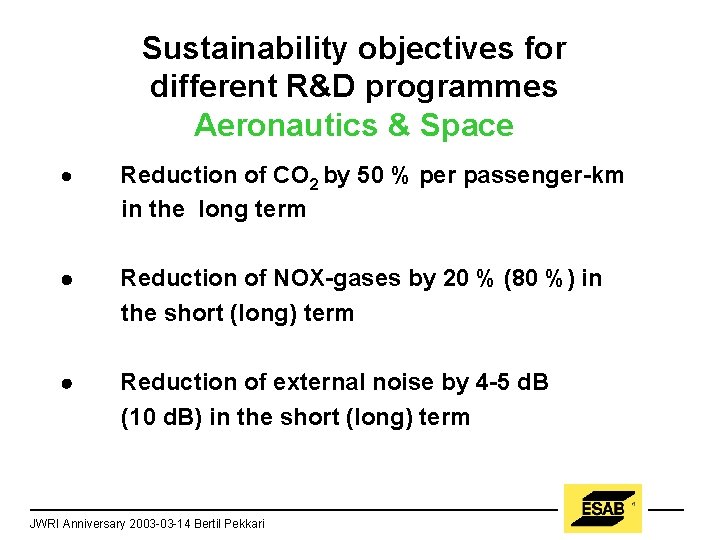
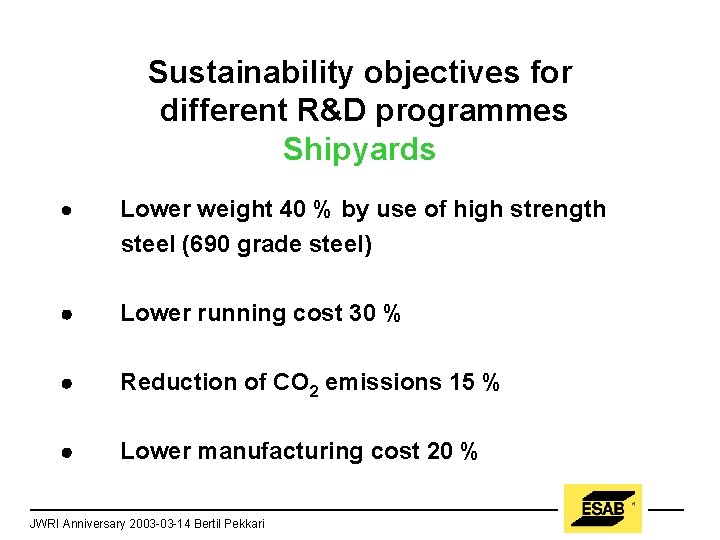
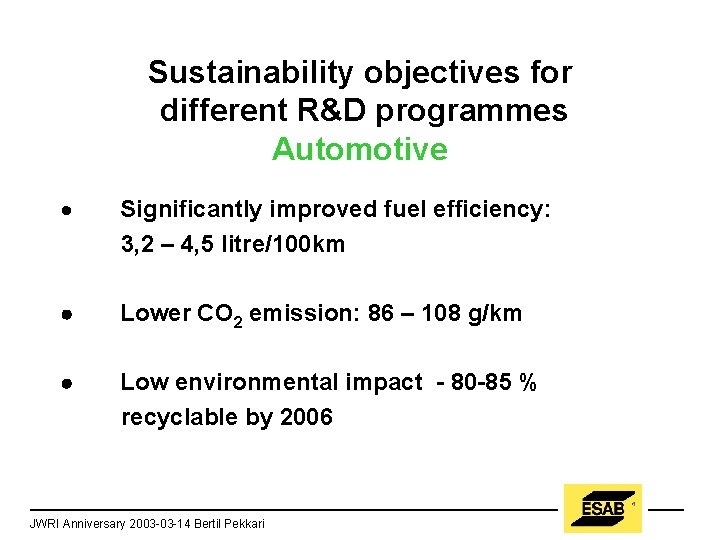
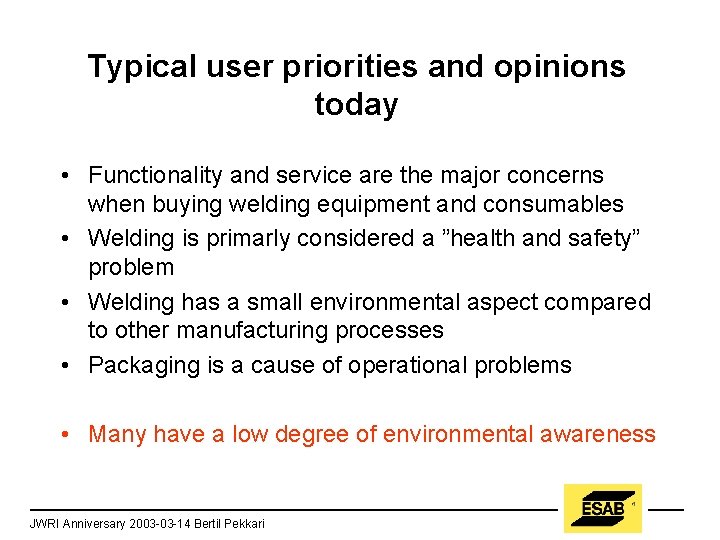

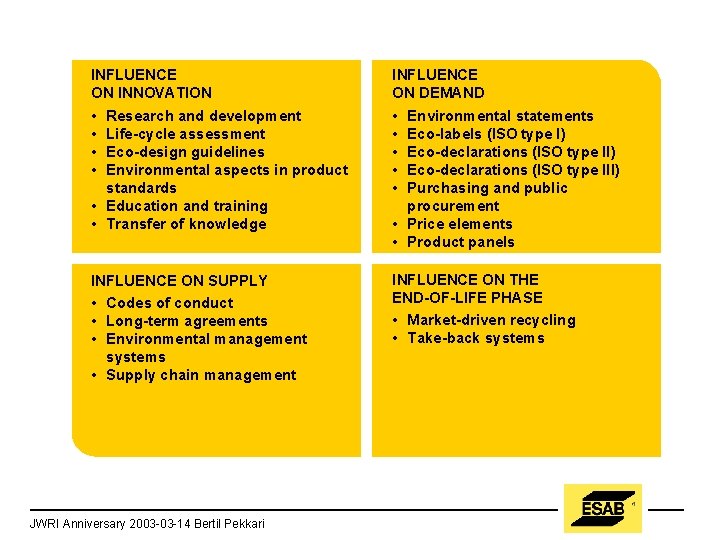
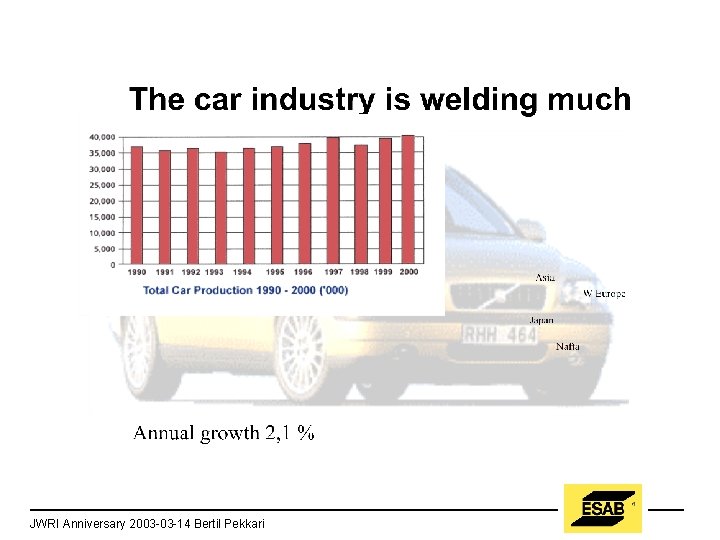
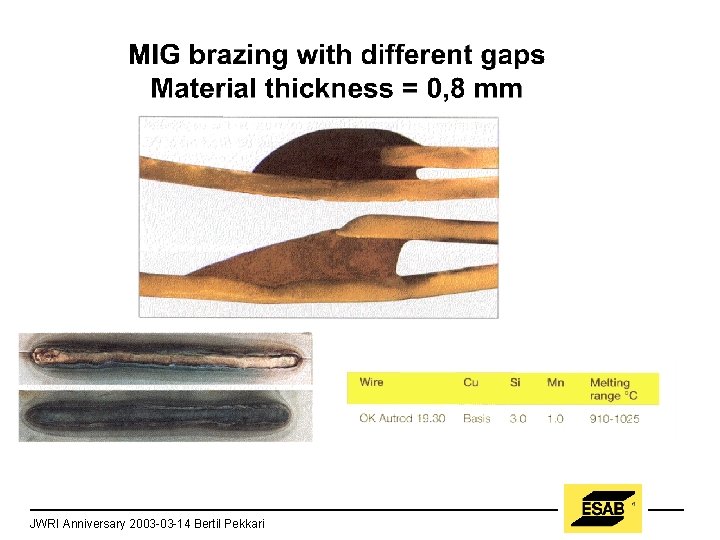
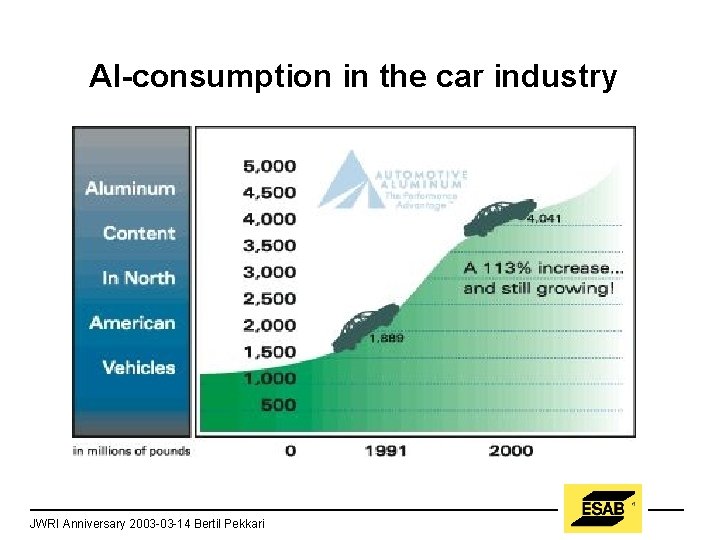
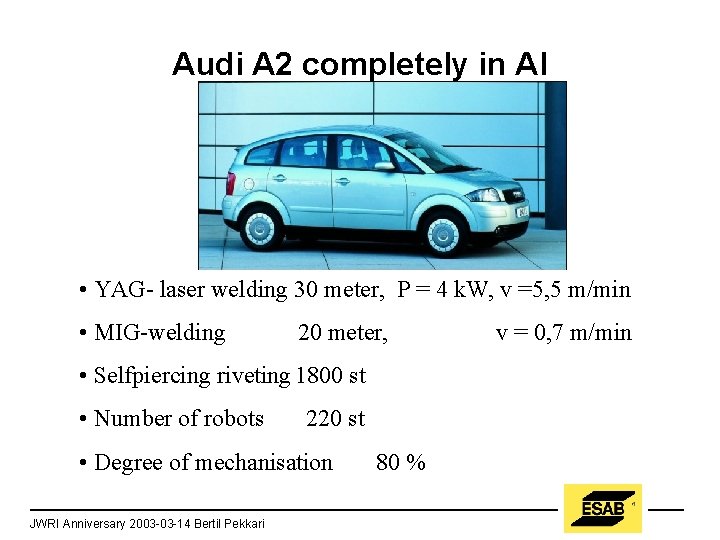
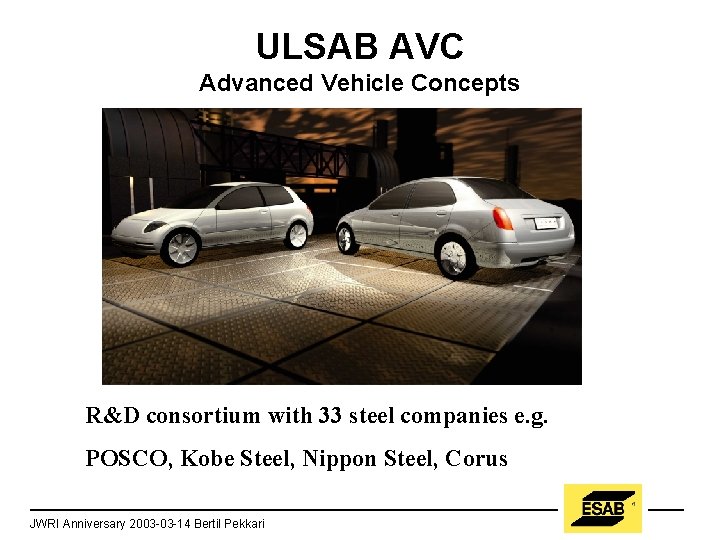
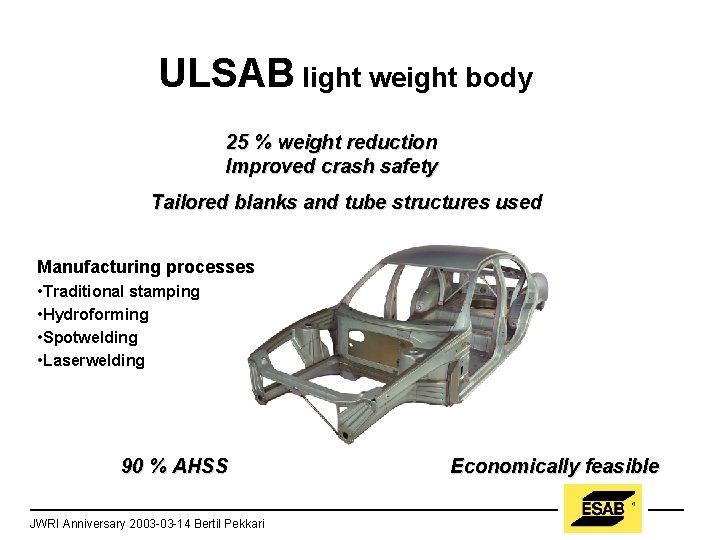
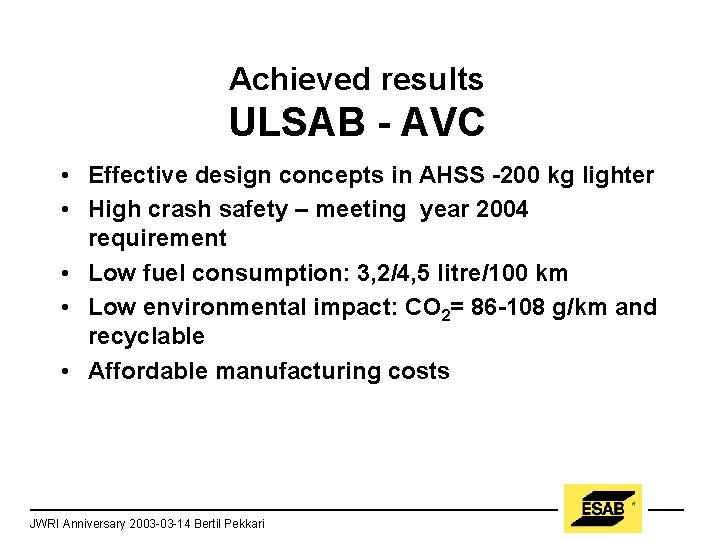
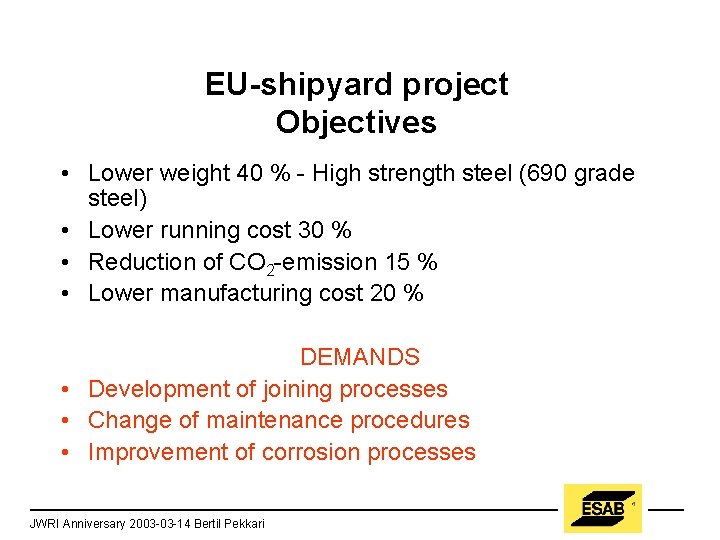
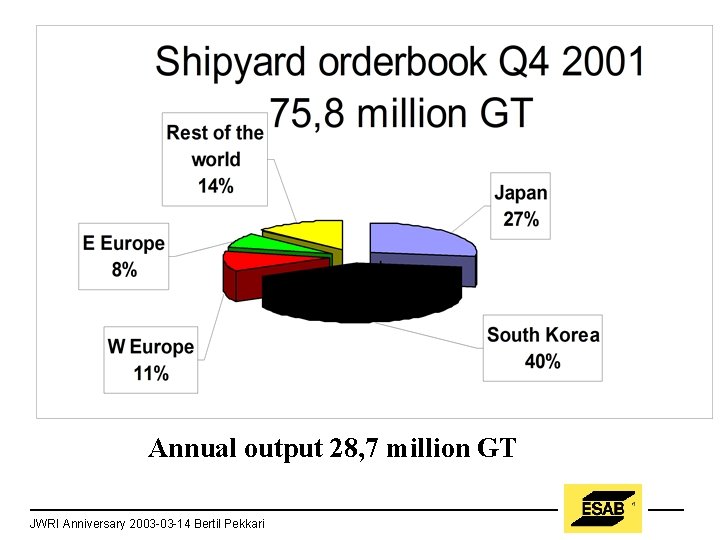
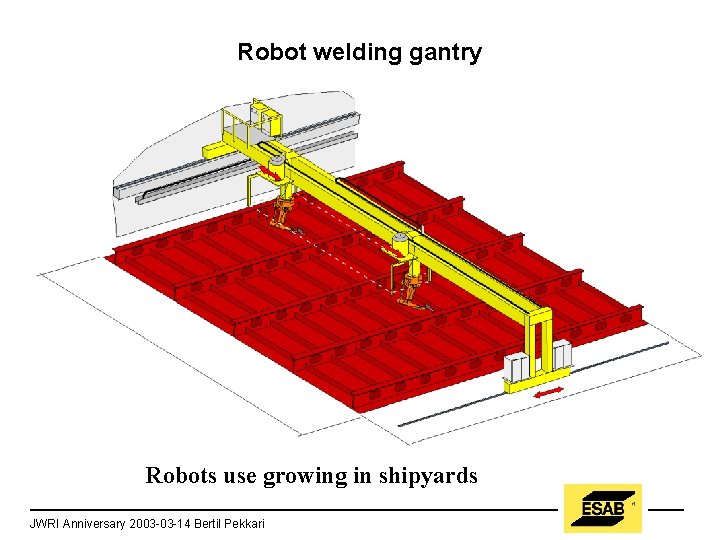
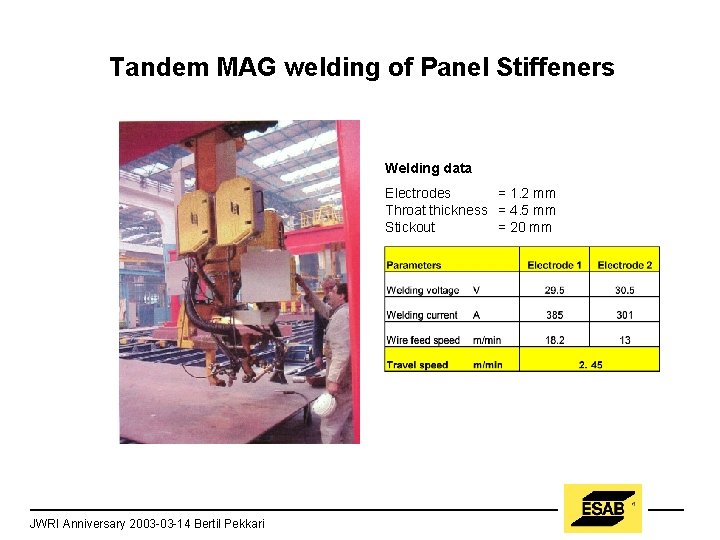
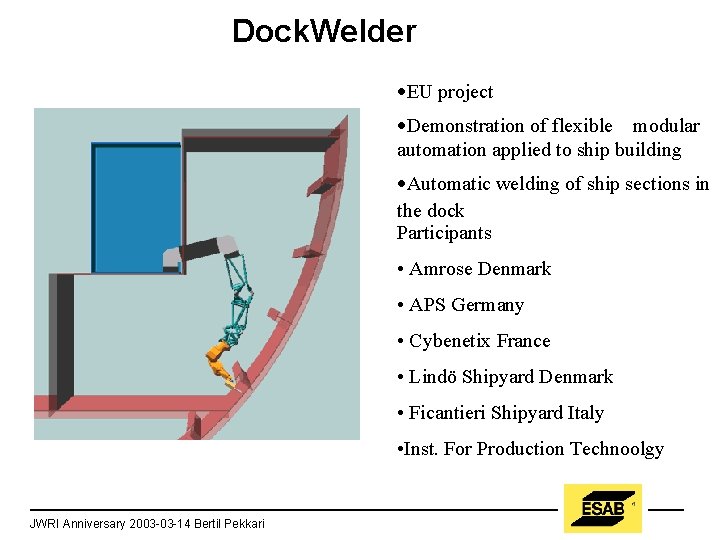
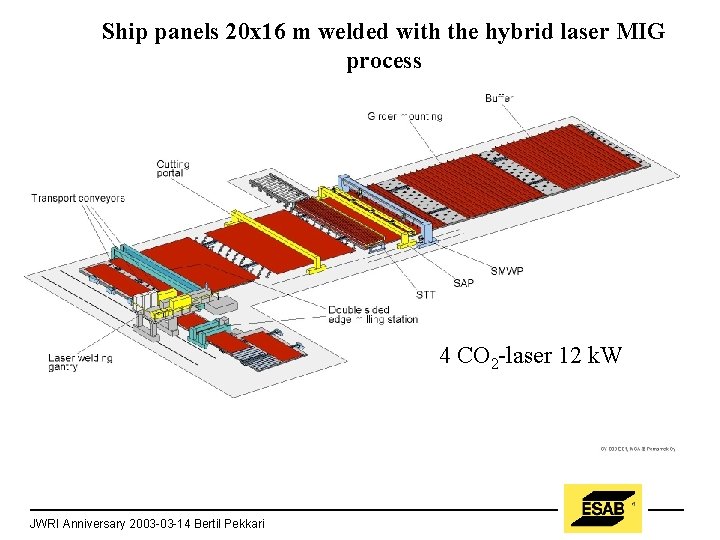
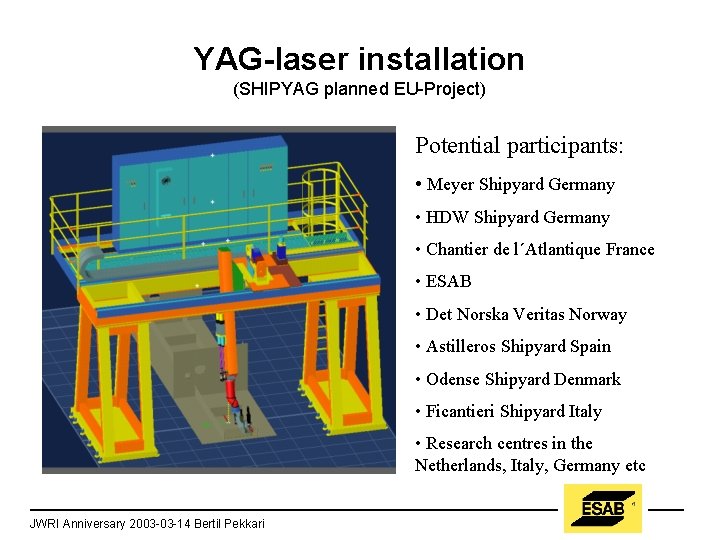
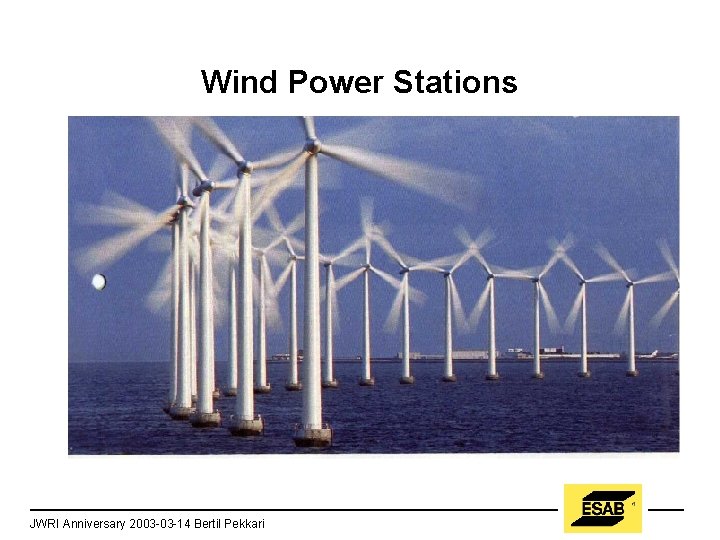
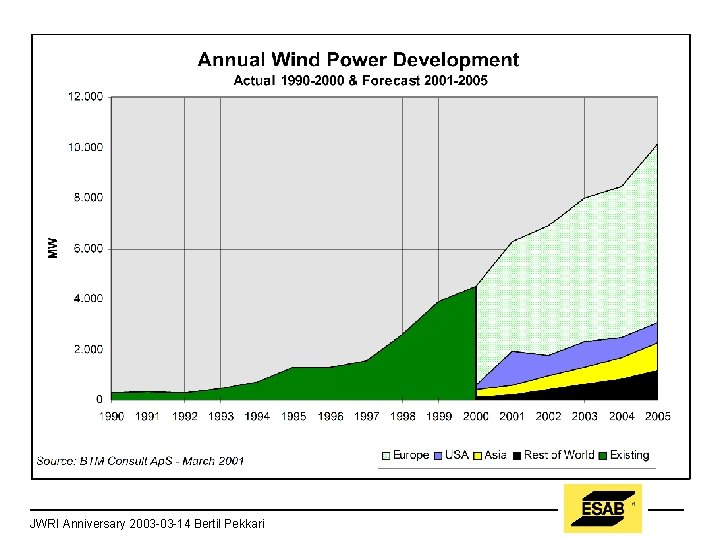
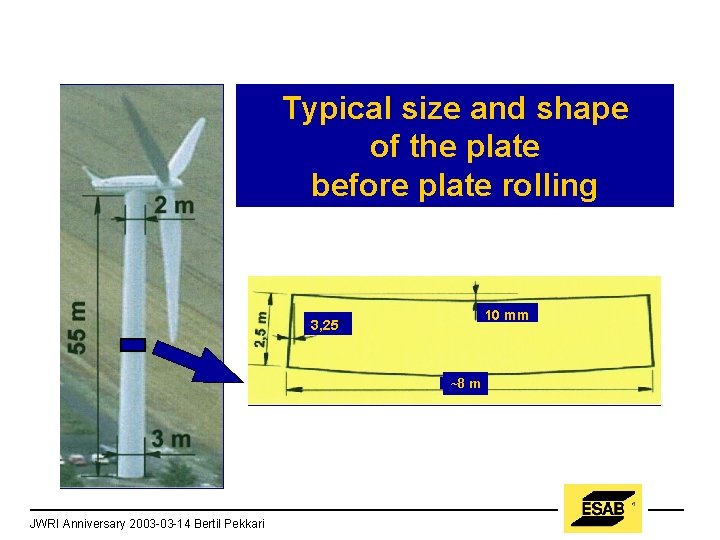
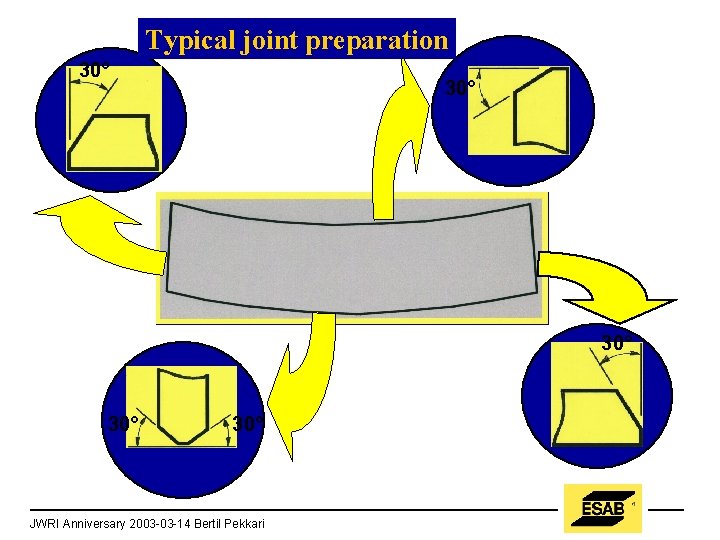
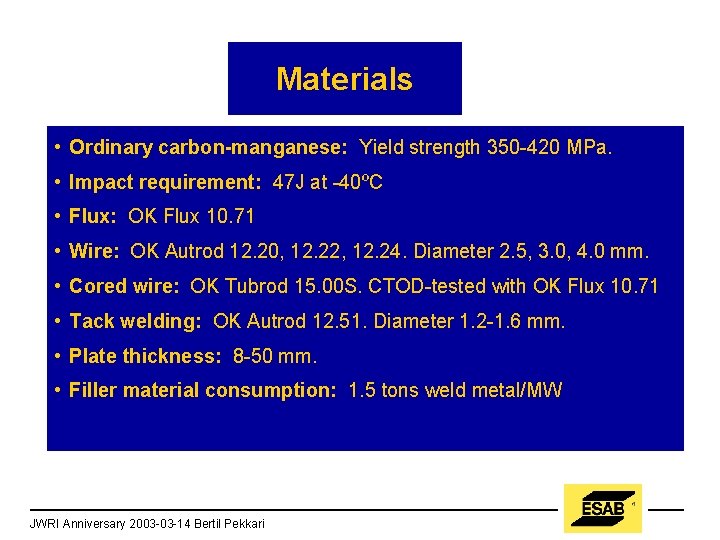
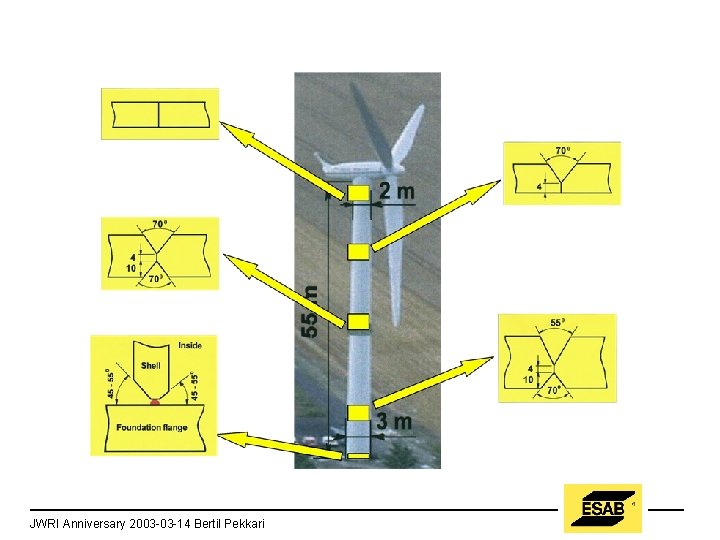
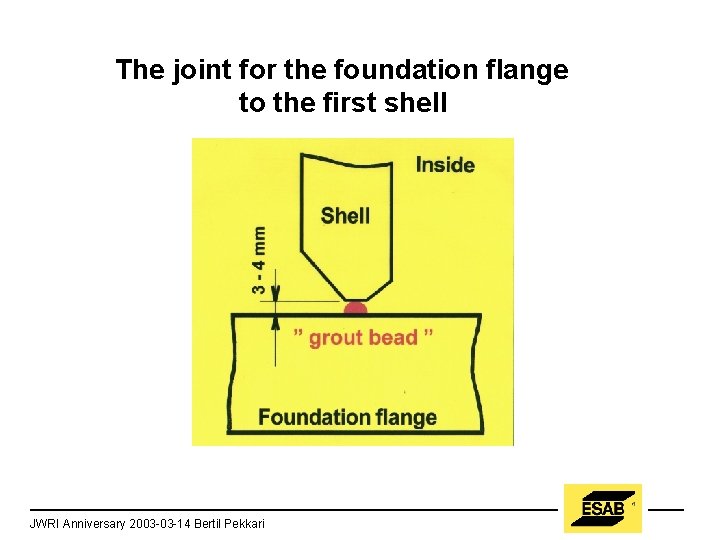
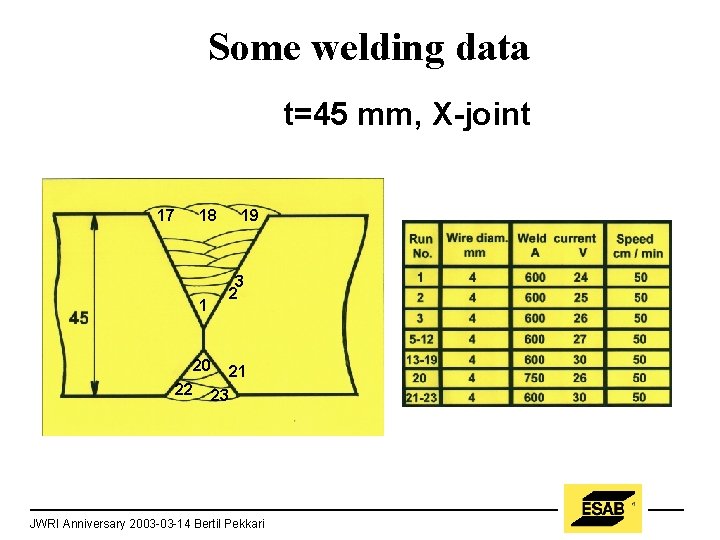
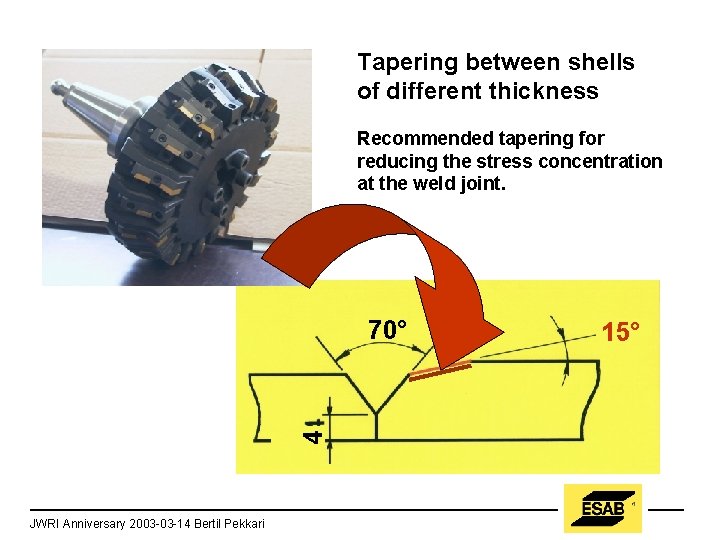
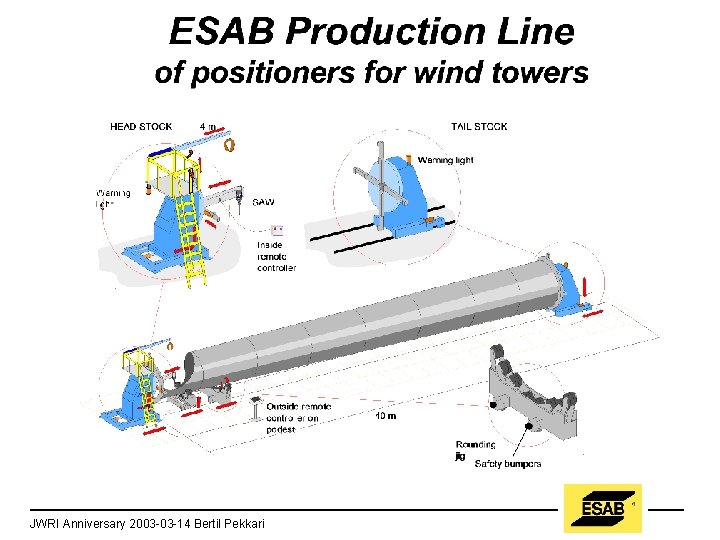
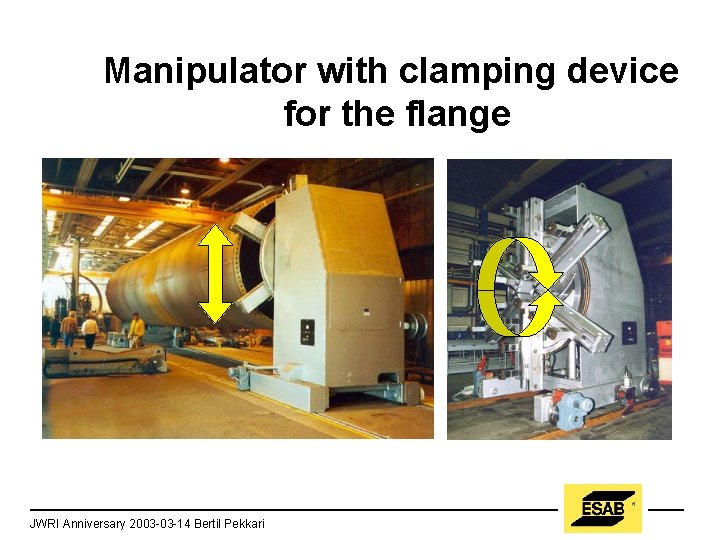
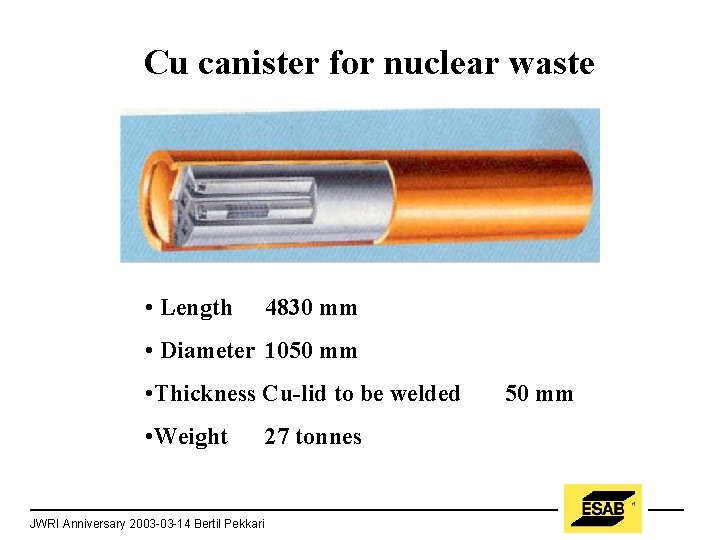
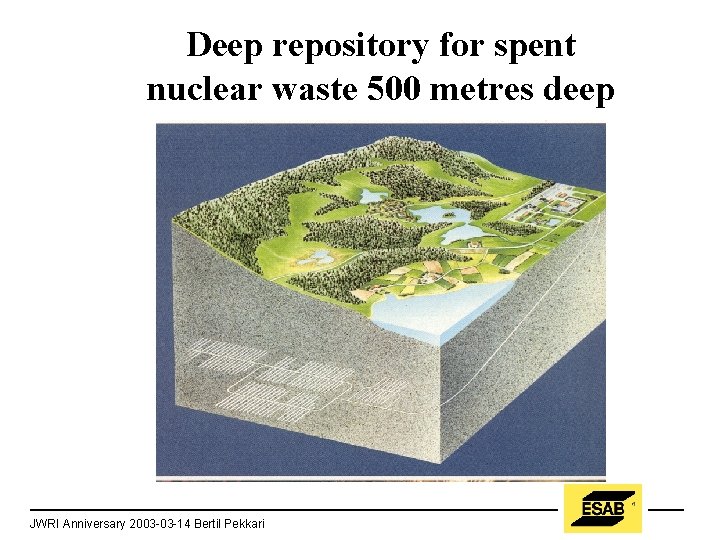
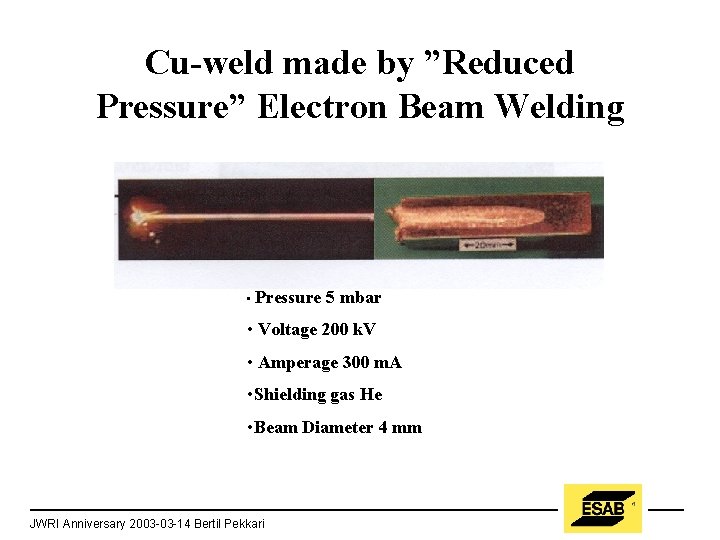
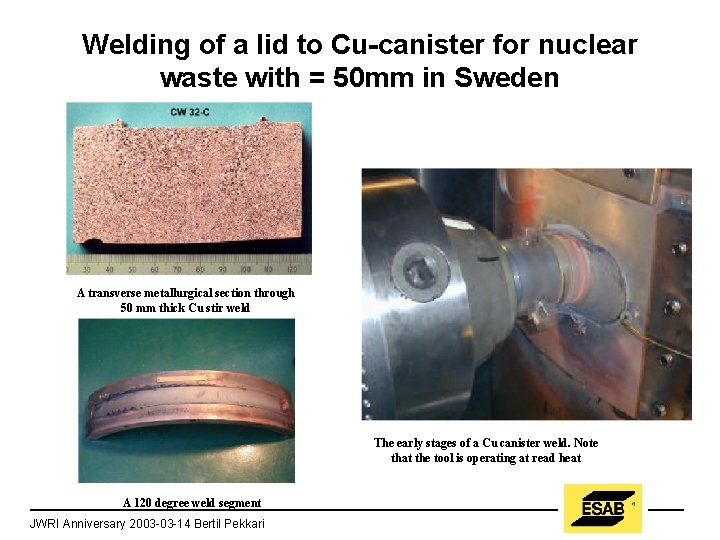

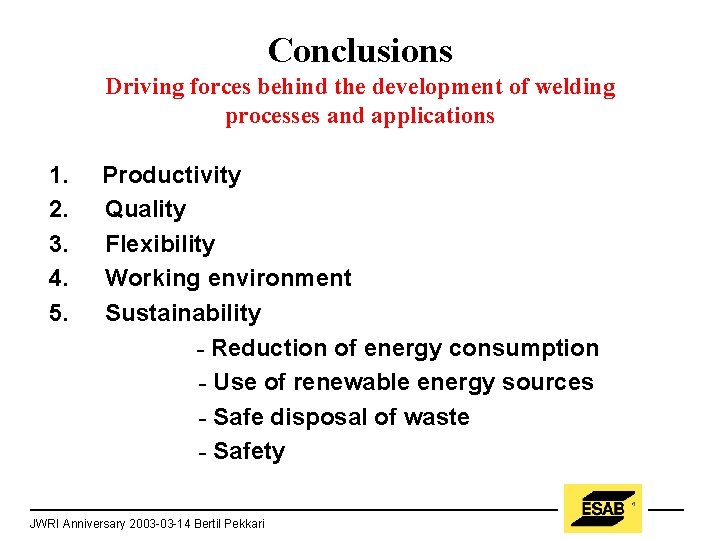
- Slides: 38
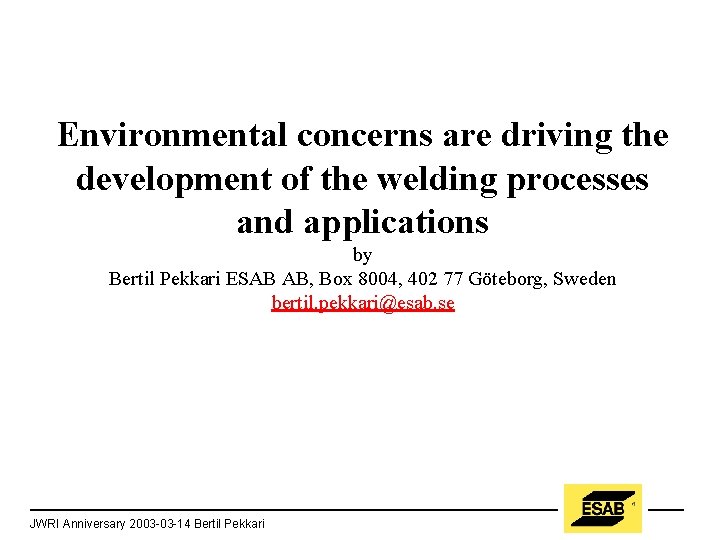
Environmental concerns are driving the development of the welding processes and applications by Bertil Pekkari ESAB AB, Box 8004, 402 77 Göteborg, Sweden bertil. pekkari@esab. se JWRI Anniversary 2003 -03 -14 Bertil Pekkari
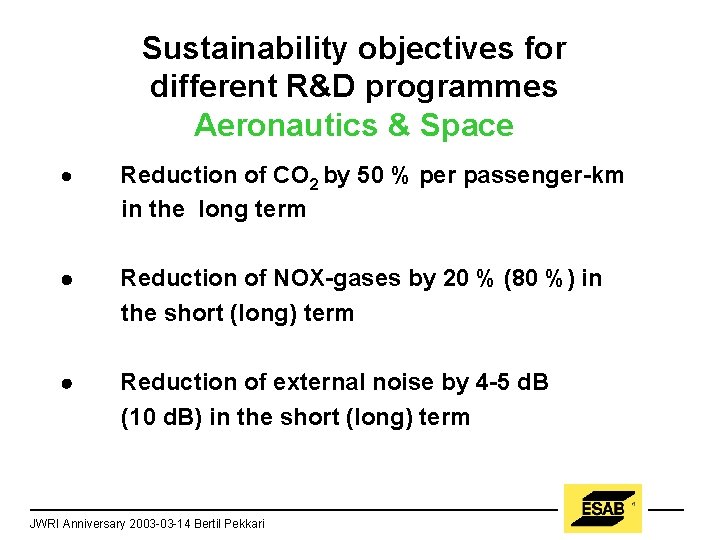
Sustainability objectives for different R&D programmes Aeronautics & Space · Reduction of CO 2 by 50 % per passenger-km in the long term · Reduction of NOX-gases by 20 % (80 %) in the short (long) term · Reduction of external noise by 4 -5 d. B (10 d. B) in the short (long) term JWRI Anniversary 2003 -03 -14 Bertil Pekkari
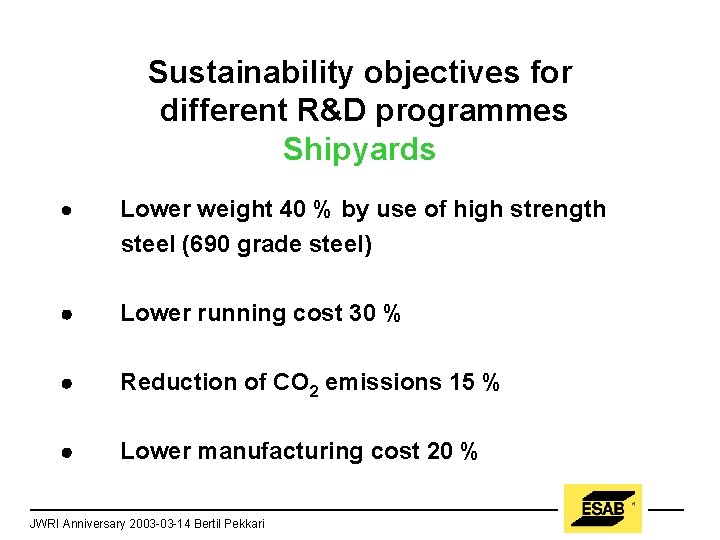
Sustainability objectives for different R&D programmes Shipyards · Lower weight 40 % by use of high strength steel (690 grade steel) · Lower running cost 30 % · Reduction of CO 2 emissions 15 % · Lower manufacturing cost 20 % JWRI Anniversary 2003 -03 -14 Bertil Pekkari
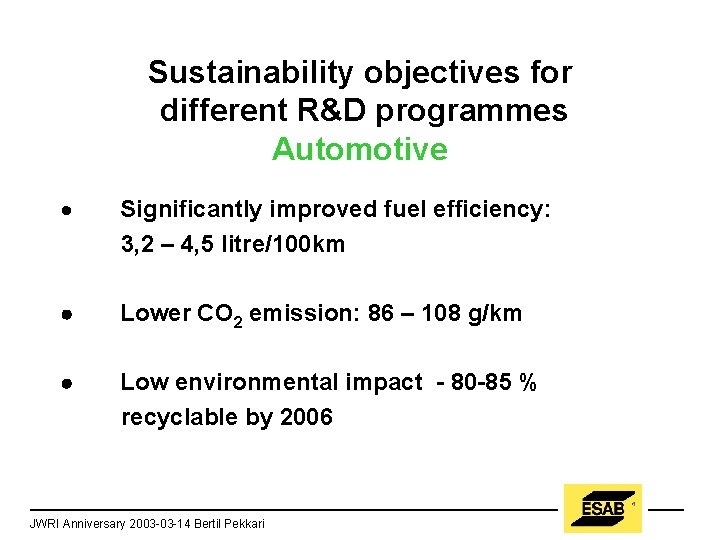
Sustainability objectives for different R&D programmes Automotive · Significantly improved fuel efficiency: 3, 2 – 4, 5 litre/100 km · Lower CO 2 emission: 86 – 108 g/km · Low environmental impact - 80 -85 % recyclable by 2006 JWRI Anniversary 2003 -03 -14 Bertil Pekkari
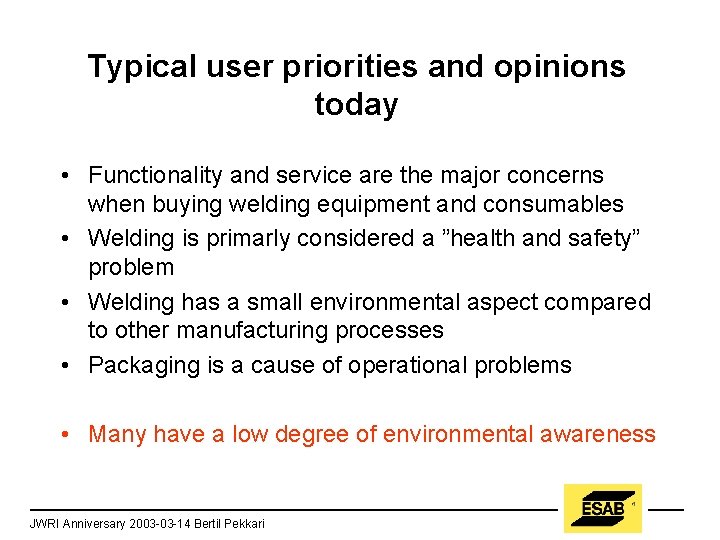
Typical user priorities and opinions today • Functionality and service are the major concerns when buying welding equipment and consumables • Welding is primarly considered a ”health and safety” problem • Welding has a small environmental aspect compared to other manufacturing processes • Packaging is a cause of operational problems • Many have a low degree of environmental awareness JWRI Anniversary 2003 -03 -14 Bertil Pekkari

Companies segregated according to their environmental awareness Passive companies Authority abiding companies Law optimizing companies Environmentally conscious companies Environmentally adapted companies Increased environmental awareness JWRI Anniversary 2003 -03 -14 Bertil Pekkari
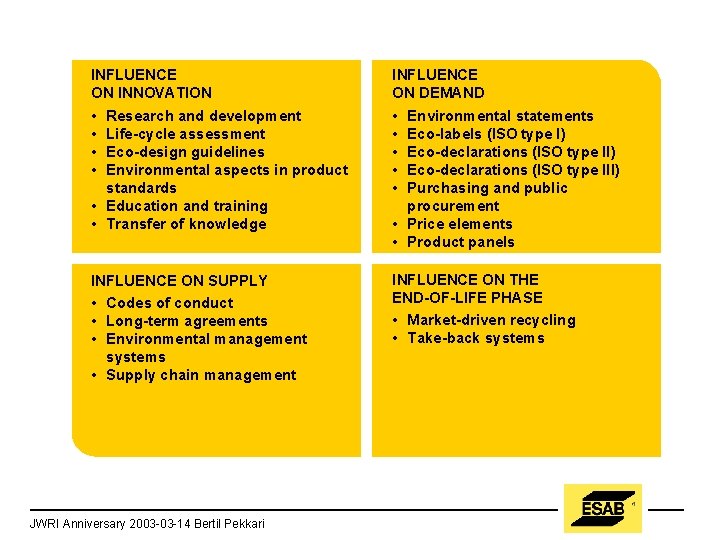
INFLUENCE ON INNOVATION INFLUENCE ON DEMAND • • Research and development Life-cycle assessment Eco-design guidelines Environmental aspects in product standards • Education and training • Transfer of knowledge • • • INFLUENCE ON SUPPLY INFLUENCE ON THE END-OF-LIFE PHASE • Codes of conduct • Long-term agreements • Environmental management systems • Supply chain management JWRI Anniversary 2003 -03 -14 Bertil Pekkari Environmental statements Eco-labels (ISO type I) Eco-declarations (ISO type III) Purchasing and public procurement • Price elements • Product panels • Market-driven recycling • Take-back systems
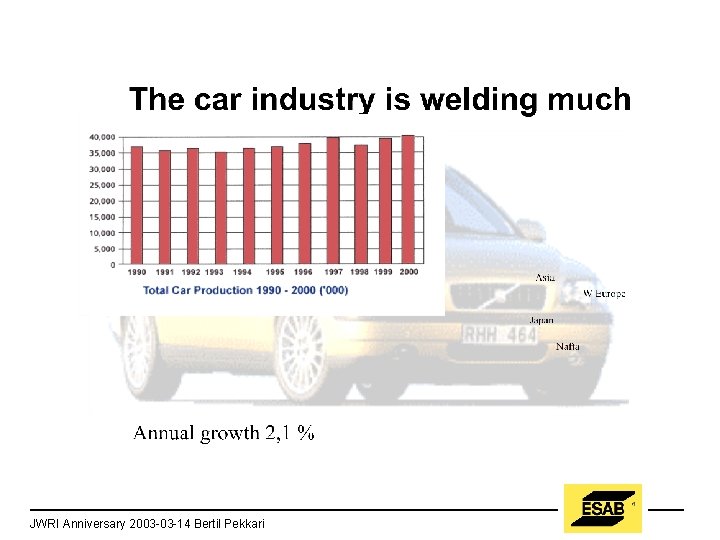
JWRI Anniversary 2003 -03 -14 Bertil Pekkari
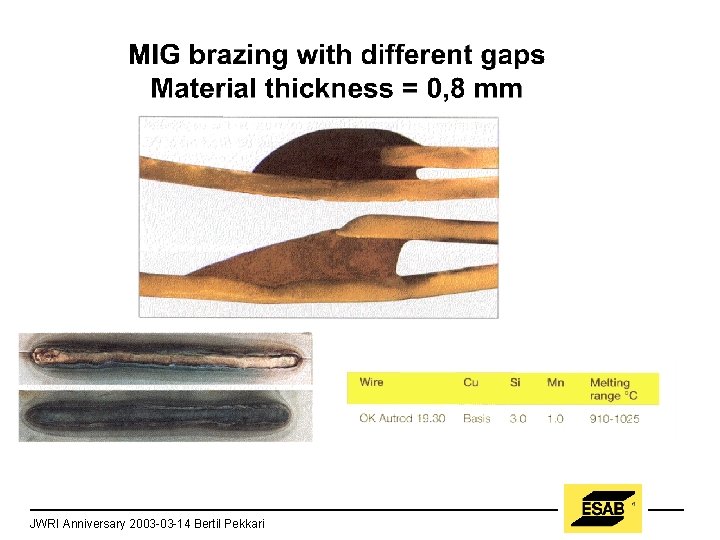
JWRI Anniversary 2003 -03 -14 Bertil Pekkari
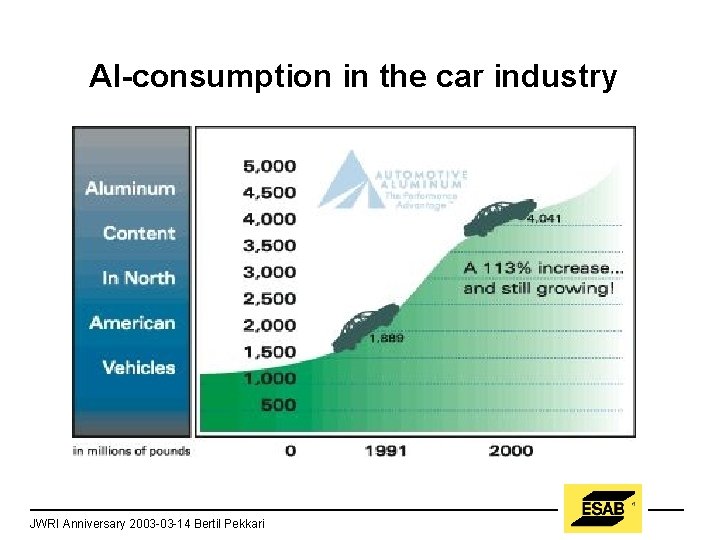
Al-consumption in the car industry JWRI Anniversary 2003 -03 -14 Bertil Pekkari
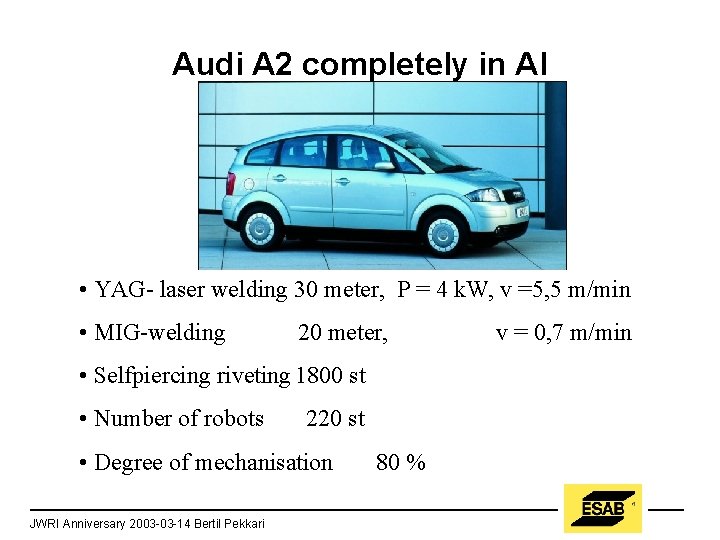
Audi A 2 completely in Al • YAG- laser welding 30 meter, P = 4 k. W, v =5, 5 m/min • MIG-welding 20 meter, v = 0, 7 m/min • Selfpiercing riveting 1800 st • Number of robots 220 st • Degree of mechanisation 80 % JWRI Anniversary 2003 -03 -14 Bertil Pekkari
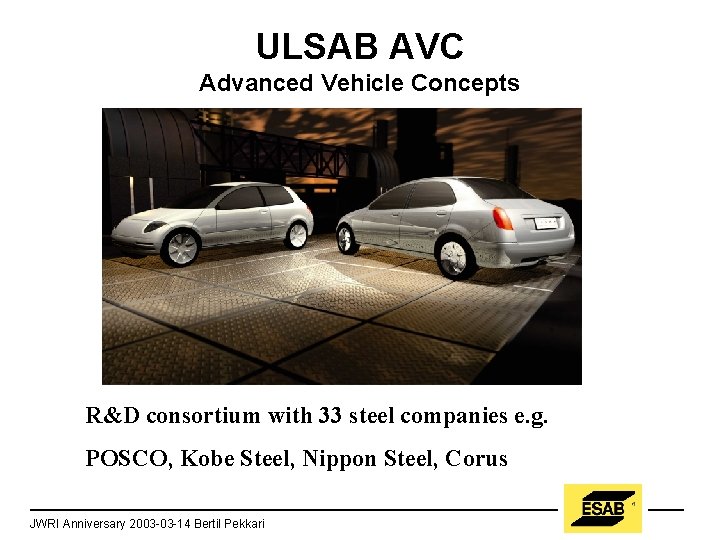
ULSAB AVC Advanced Vehicle Concepts R&D consortium with 33 steel companies e. g. POSCO, Kobe Steel, Nippon Steel, Corus JWRI Anniversary 2003 -03 -14 Bertil Pekkari
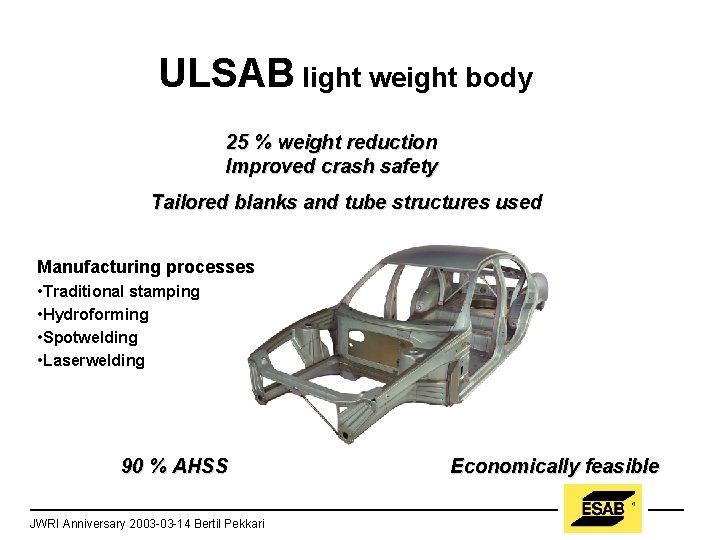
ULSAB light weight body 25 % weight reduction Improved crash safety Tailored blanks and tube structures used Manufacturing processes • Traditional stamping • Hydroforming • Spotwelding • Laserwelding 90 % AHSS JWRI Anniversary 2003 -03 -14 Bertil Pekkari Economically feasible
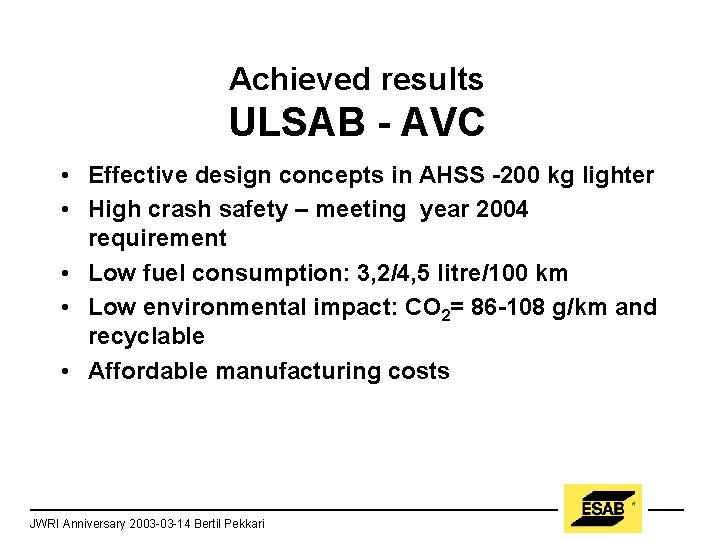
Achieved results ULSAB - AVC • Effective design concepts in AHSS -200 kg lighter • High crash safety – meeting year 2004 requirement • Low fuel consumption: 3, 2/4, 5 litre/100 km • Low environmental impact: CO 2= 86 -108 g/km and recyclable • Affordable manufacturing costs JWRI Anniversary 2003 -03 -14 Bertil Pekkari
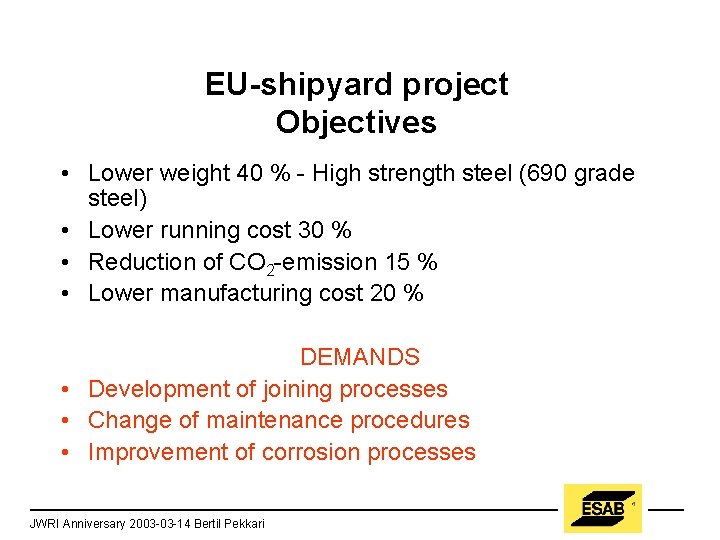
EU-shipyard project Objectives • Lower weight 40 % - High strength steel (690 grade steel) • Lower running cost 30 % • Reduction of CO 2 -emission 15 % • Lower manufacturing cost 20 % DEMANDS • Development of joining processes • Change of maintenance procedures • Improvement of corrosion processes JWRI Anniversary 2003 -03 -14 Bertil Pekkari
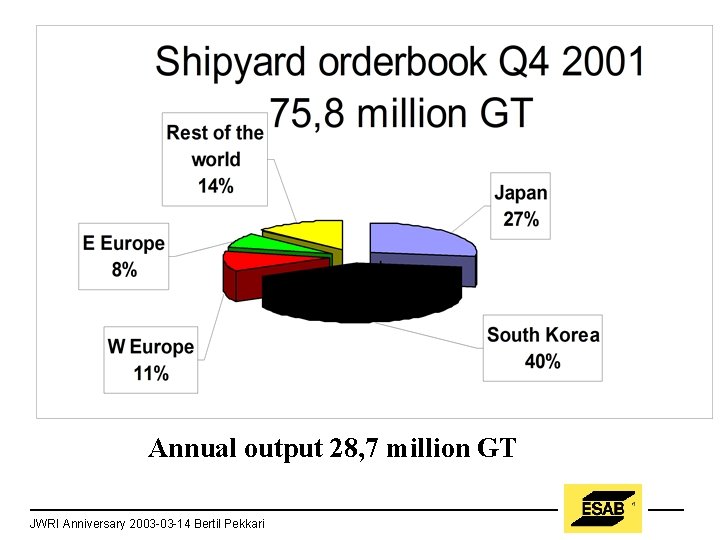
Annual output 28, 7 million GT JWRI Anniversary 2003 -03 -14 Bertil Pekkari
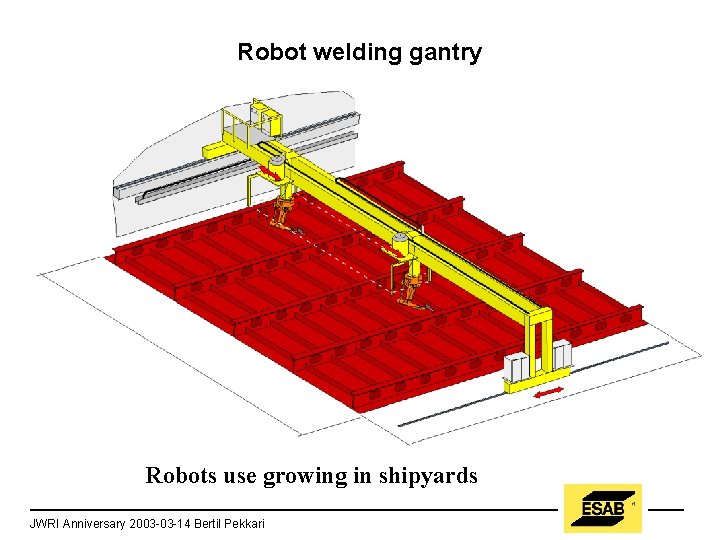
Robot welding gantry Robots use growing in shipyards JWRI Anniversary 2003 -03 -14 Bertil Pekkari
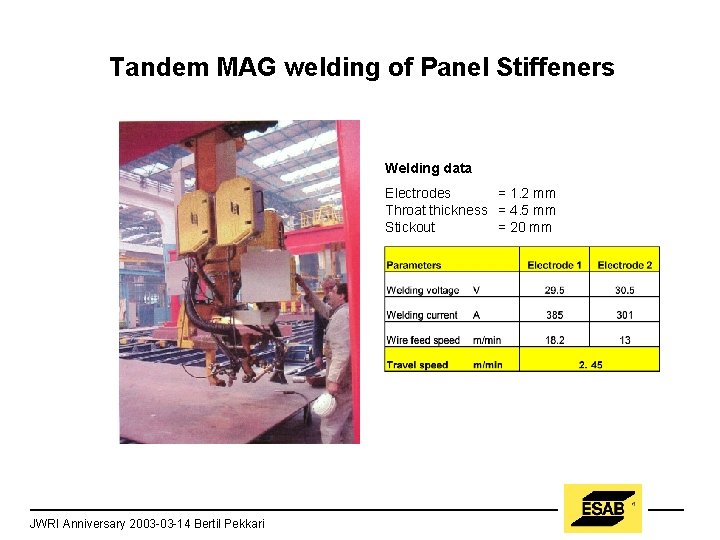
Tandem MAG welding of Panel Stiffeners Welding data Electrodes = 1. 2 mm Throat thickness = 4. 5 mm Stickout = 20 mm JWRI Anniversary 2003 -03 -14 Bertil Pekkari
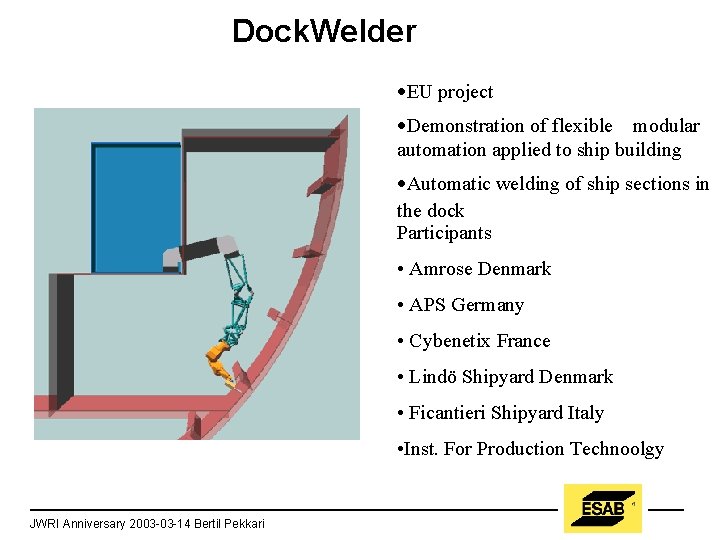
Dock. Welder ·EU project ·Demonstration of flexible modular automation applied to ship building ·Automatic welding of ship sections in the dock Participants • Amrose Denmark • APS Germany • Cybenetix France • Lindö Shipyard Denmark • Ficantieri Shipyard Italy • Inst. For Production Technoolgy JWRI Anniversary 2003 -03 -14 Bertil Pekkari
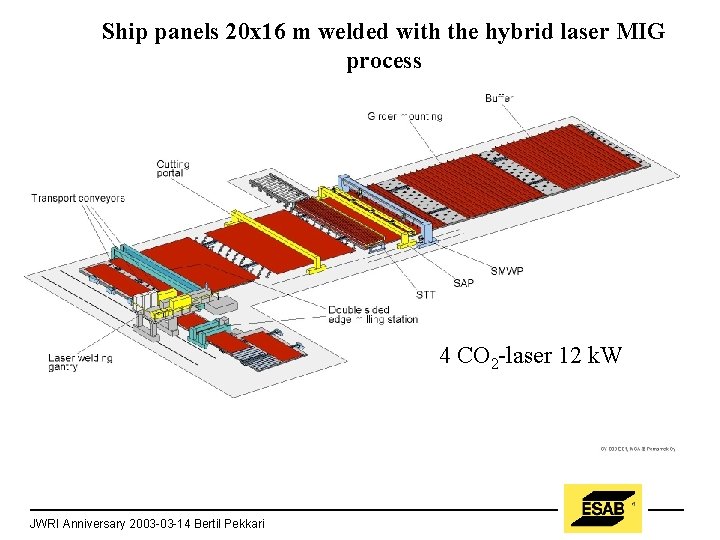
Ship panels 20 x 16 m welded with the hybrid laser MIG process 4 CO 2 -laser 12 k. W JWRI Anniversary 2003 -03 -14 Bertil Pekkari
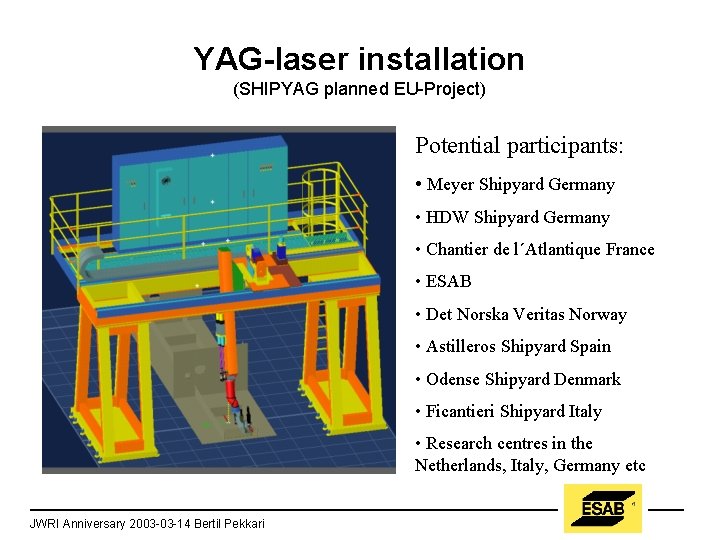
YAG-laser installation (SHIPYAG planned EU-Project) Potential participants: • Meyer Shipyard Germany • HDW Shipyard Germany • Chantier de l´Atlantique France • ESAB • Det Norska Veritas Norway • Astilleros Shipyard Spain • Odense Shipyard Denmark • Ficantieri Shipyard Italy • Research centres in the Netherlands, Italy, Germany etc JWRI Anniversary 2003 -03 -14 Bertil Pekkari
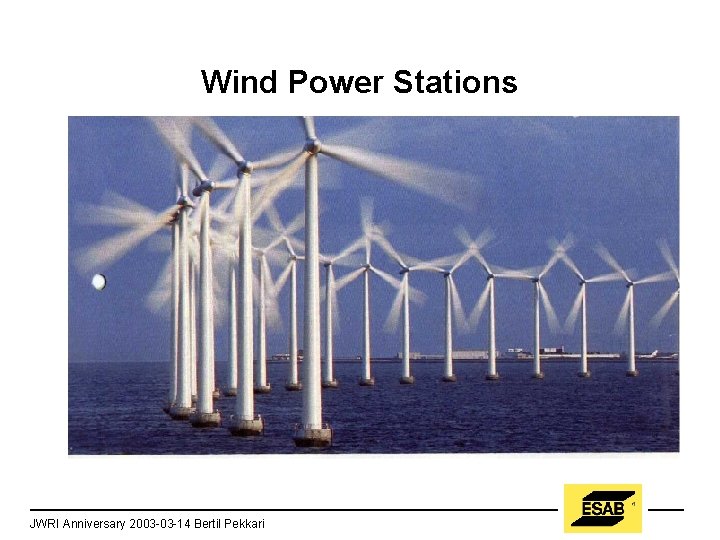
Wind Power Stations JWRI Anniversary 2003 -03 -14 Bertil Pekkari
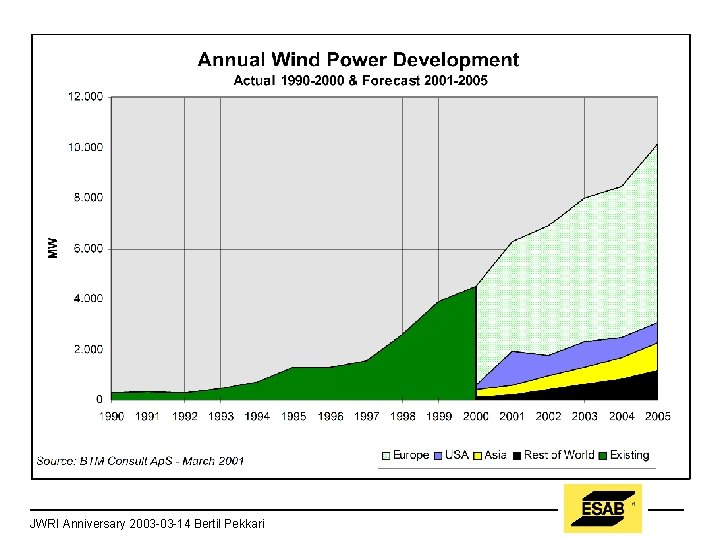
JWRI Anniversary 2003 -03 -14 Bertil Pekkari
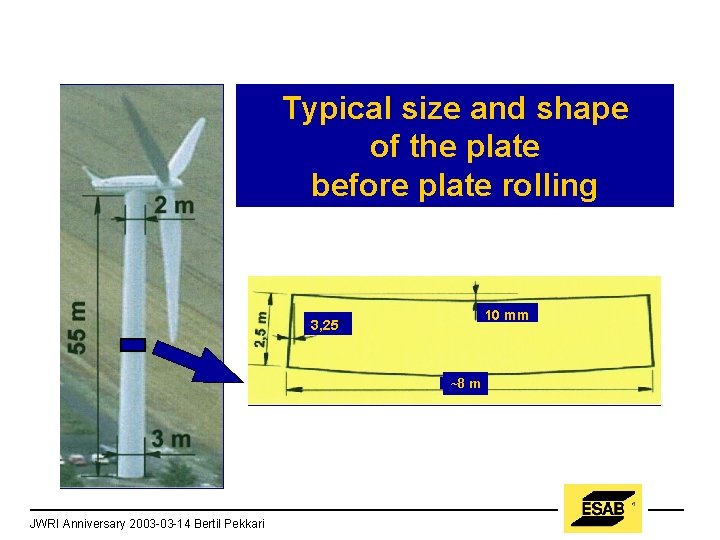
Typical size and shape of the plate before plate rolling 10 mm 3, 25° ~8 m JWRI Anniversary 2003 -03 -14 Bertil Pekkari
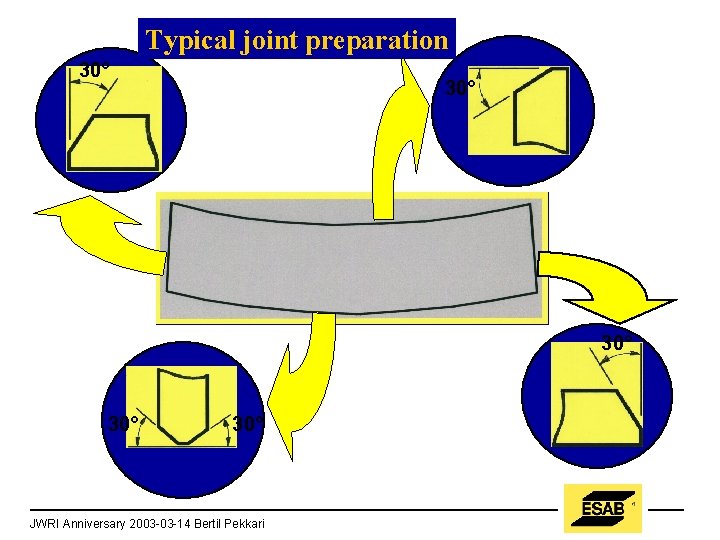
Typical joint preparation 30° 30° 30° JWRI Anniversary 2003 -03 -14 Bertil Pekkari
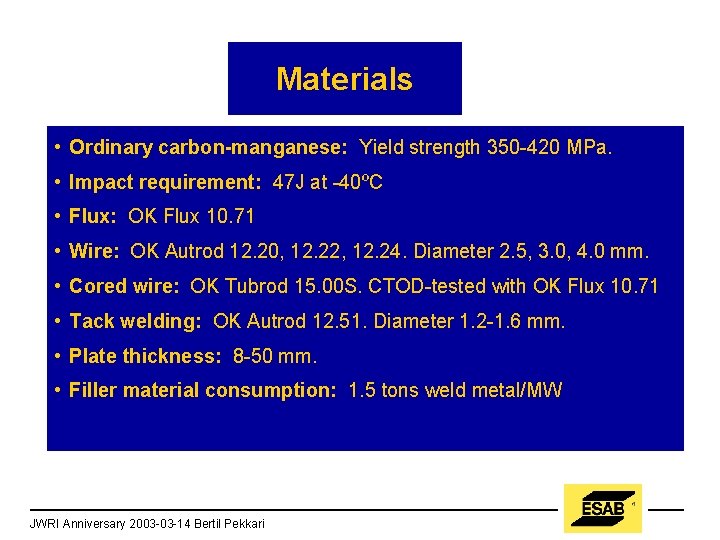
Materials • Ordinary carbon-manganese: Yield strength 350 -420 MPa. • Impact requirement: 47 J at -40ºC • Flux: OK Flux 10. 71 • Wire: OK Autrod 12. 20, 12. 22, 12. 24. Diameter 2. 5, 3. 0, 4. 0 mm. • Cored wire: OK Tubrod 15. 00 S. CTOD-tested with OK Flux 10. 71 • Tack welding: OK Autrod 12. 51. Diameter 1. 2 -1. 6 mm. • Plate thickness: 8 -50 mm. • Filler material consumption: 1. 5 tons weld metal/MW JWRI Anniversary 2003 -03 -14 Bertil Pekkari
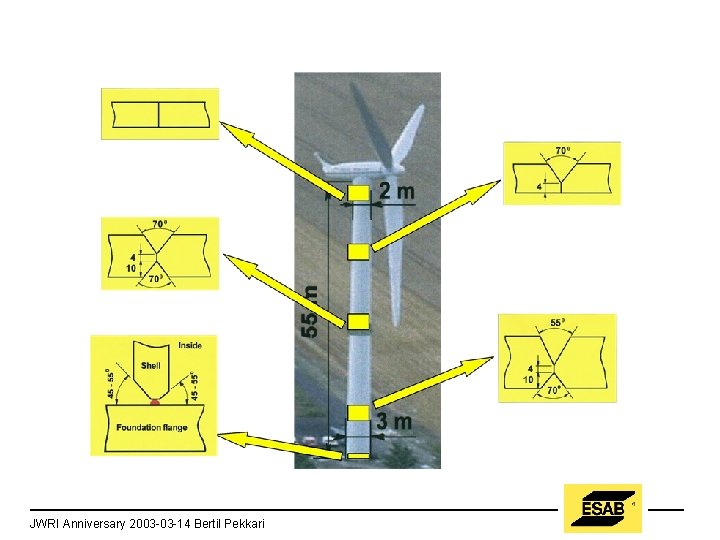
JWRI Anniversary 2003 -03 -14 Bertil Pekkari
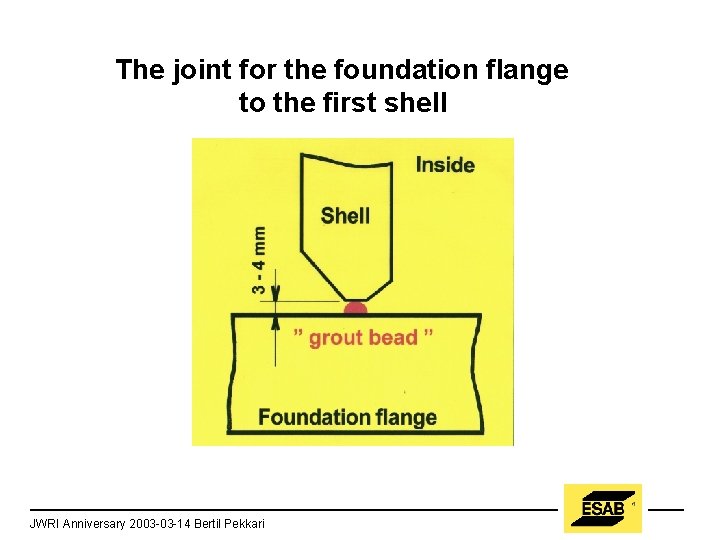
The joint for the foundation flange to the first shell JWRI Anniversary 2003 -03 -14 Bertil Pekkari
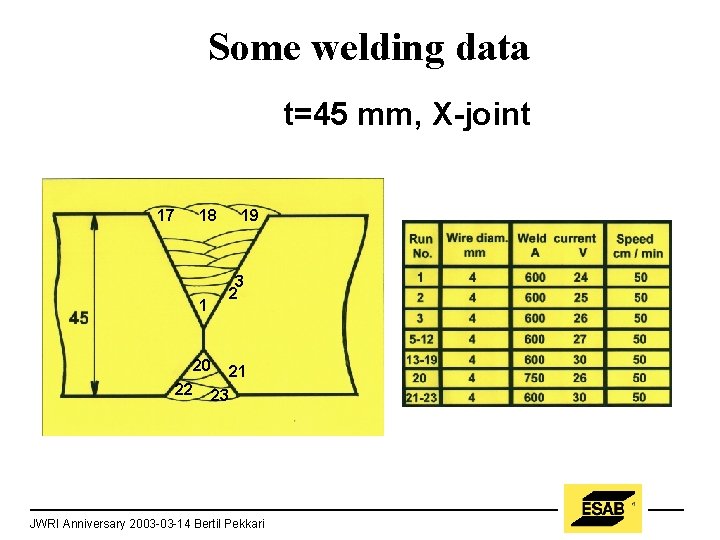
Some welding data t=45 mm, X-joint 17 18 3 2 1 20 22 19 21 23 JWRI Anniversary 2003 -03 -14 Bertil Pekkari
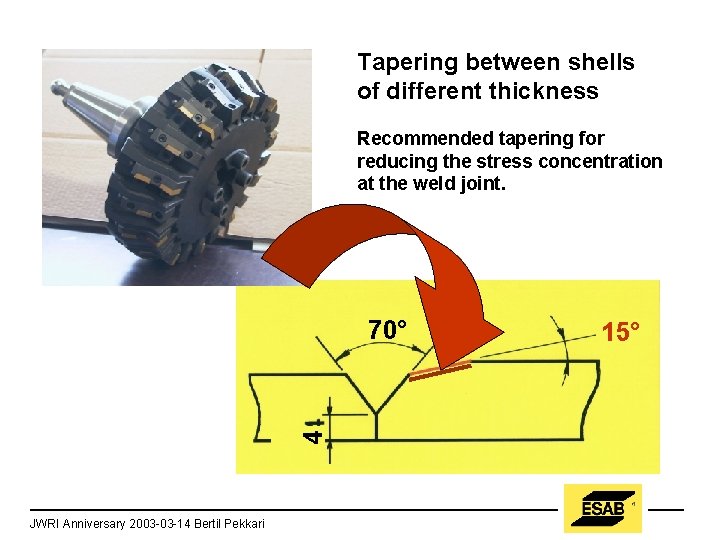
Tapering between shells of different thickness Recommended tapering for reducing the stress concentration at the weld joint. 4 70° JWRI Anniversary 2003 -03 -14 Bertil Pekkari 15°
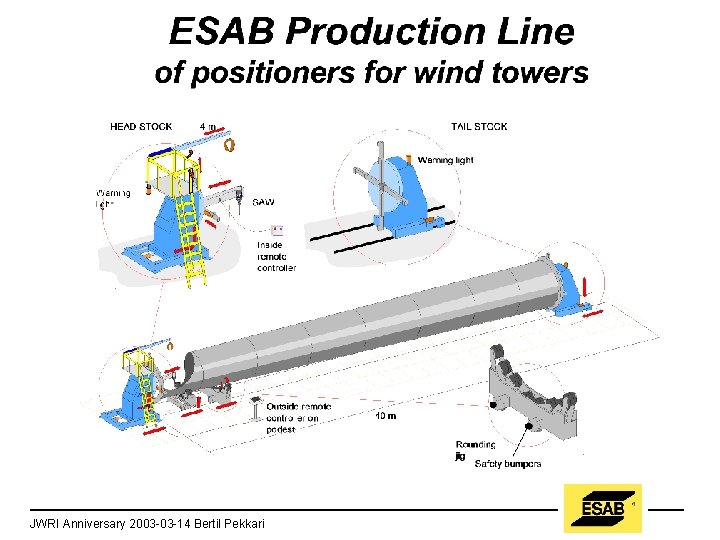
JWRI Anniversary 2003 -03 -14 Bertil Pekkari
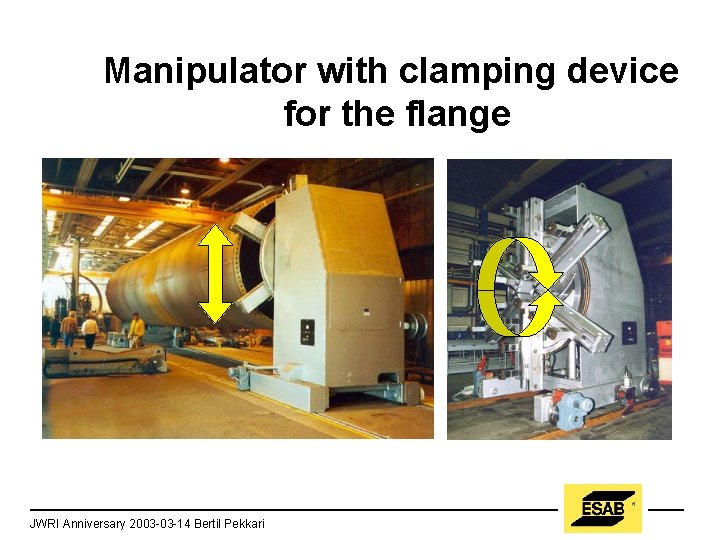
Manipulator with clamping device for the flange JWRI Anniversary 2003 -03 -14 Bertil Pekkari
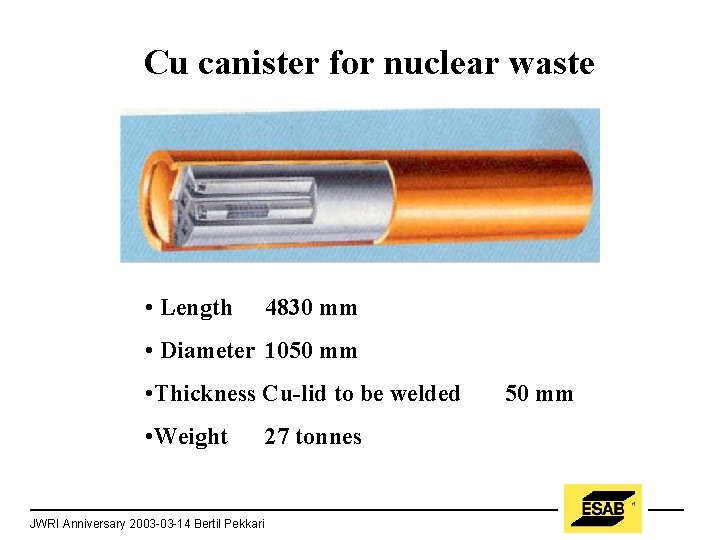
Cu canister for nuclear waste • Length 4830 mm • Diameter 1050 mm • Thickness Cu-lid to be welded • Weight JWRI Anniversary 2003 -03 -14 Bertil Pekkari 27 tonnes 50 mm
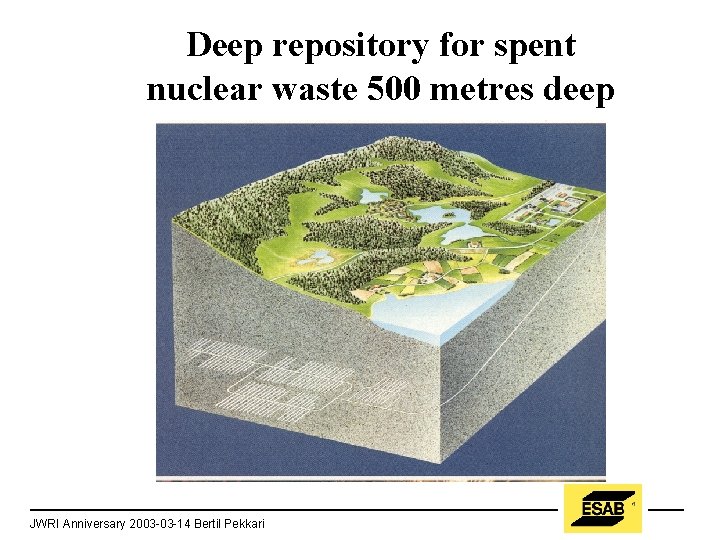
Deep repository for spent nuclear waste 500 metres deep JWRI Anniversary 2003 -03 -14 Bertil Pekkari
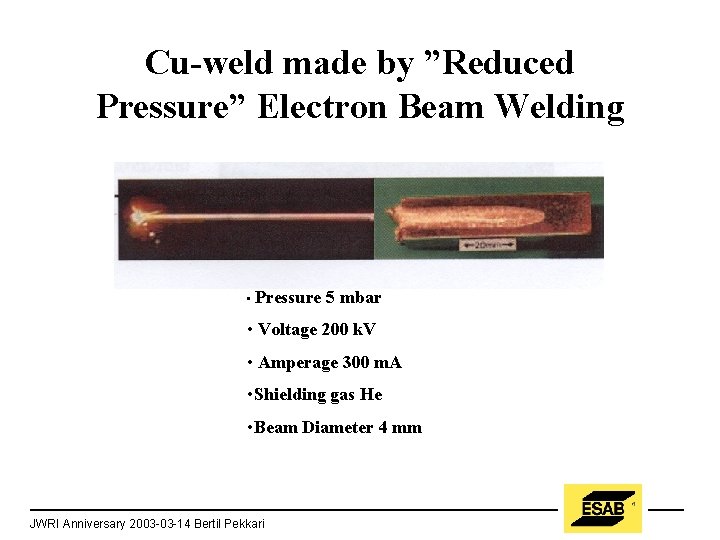
Cu-weld made by ”Reduced Pressure” Electron Beam Welding • Pressure 5 mbar • Voltage 200 k. V • Amperage 300 m. A • Shielding gas He • Beam Diameter 4 mm JWRI Anniversary 2003 -03 -14 Bertil Pekkari
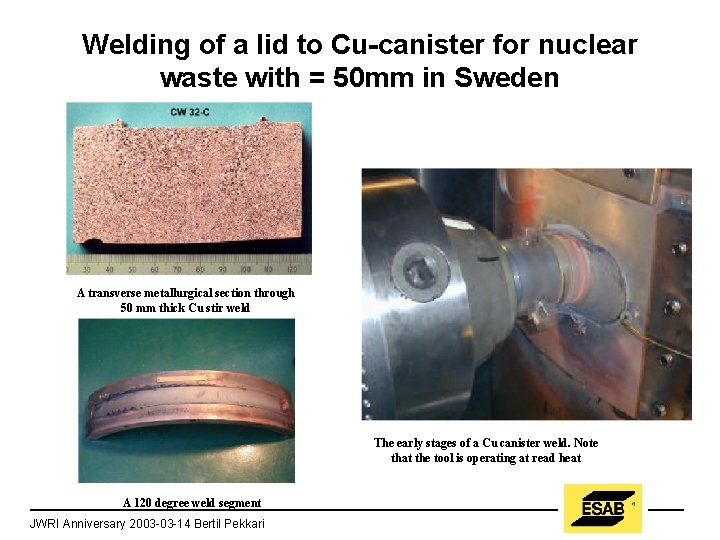
Welding of a lid to Cu-canister for nuclear waste with = 50 mm in Sweden A transverse metallurgical section through 50 mm thick Cu stir weld The early stages of a Cu canister weld. Note that the tool is operating at read heat A 120 degree weld segment JWRI Anniversary 2003 -03 -14 Bertil Pekkari

FSW plant for welding Cucanister for nuclear waste JWRI Anniversary 2003 -03 -14 Bertil Pekkari
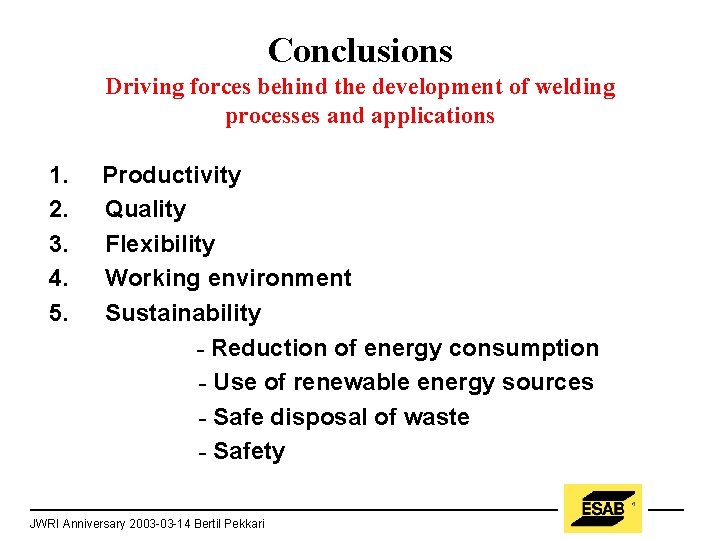
Conclusions Driving forces behind the development of welding processes and applications 1. Productivity 2. Quality 3. Flexibility 4. Working environment 5. Sustainability - Reduction of energy consumption - Use of renewable energy sources - Safe disposal of waste - Safety JWRI Anniversary 2003 -03 -14 Bertil Pekkari