ENGI 8926 Mechanical Design Project II Downhole Turbine
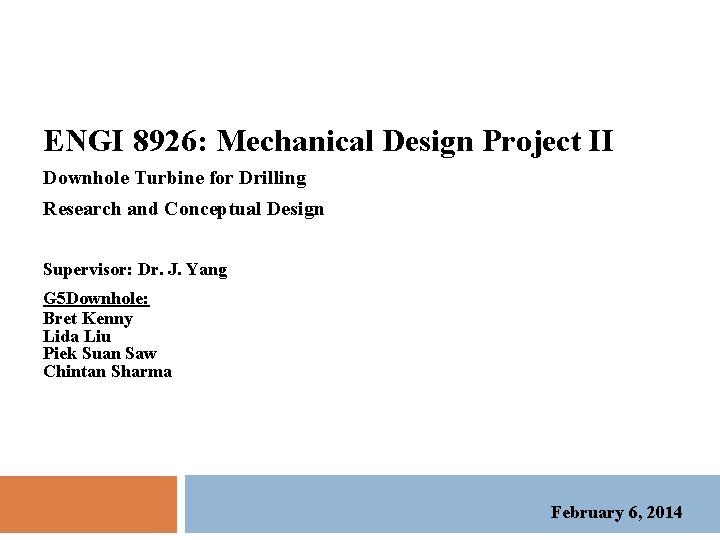
ENGI 8926: Mechanical Design Project II Downhole Turbine for Drilling Research and Conceptual Design Supervisor: Dr. J. Yang G 5 Downhole: Bret Kenny Lida Liu Piek Suan Saw Chintan Sharma February 6, 2014
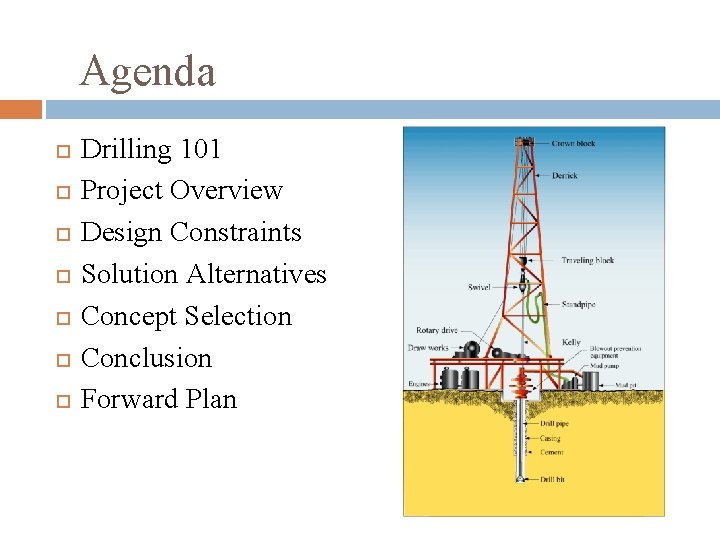
Agenda Drilling 101 Project Overview Design Constraints Solution Alternatives Concept Selection Conclusion Forward Plan
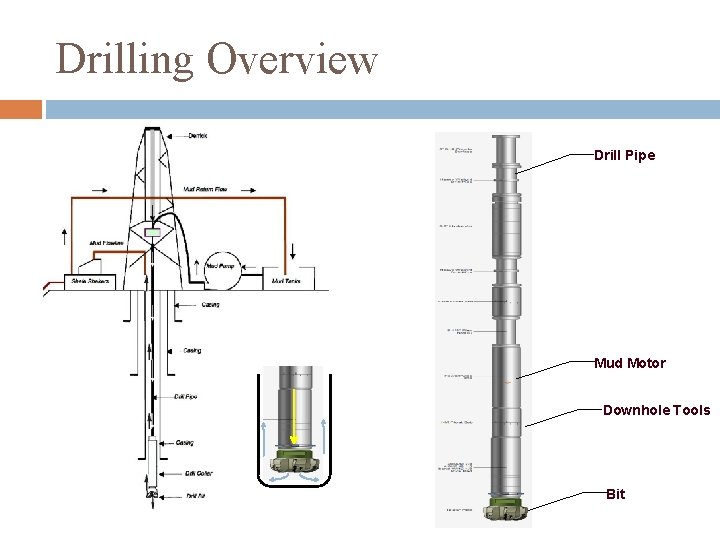
Drilling Overview Drill Pipe Mud Motor Downhole Tools Bit
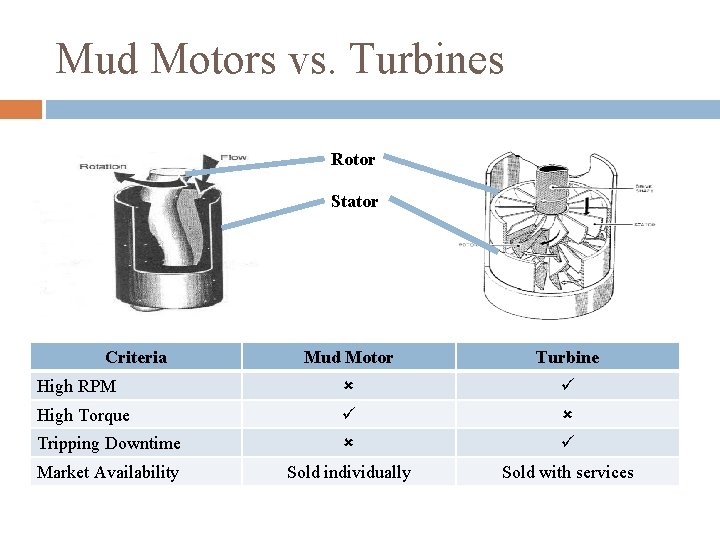
Mud Motors vs. Turbines Rotor Stator Criteria Mud Motor Turbine High RPM High Torque Tripping Downtime Market Availability Sold individually Sold with services
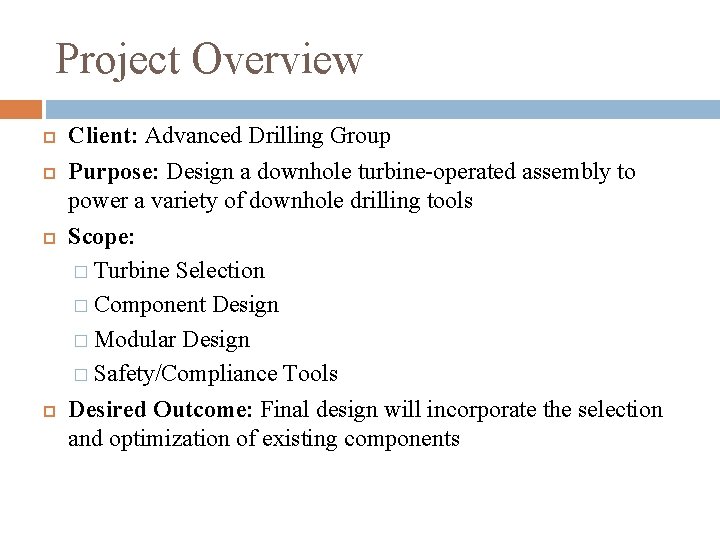
Project Overview Client: Advanced Drilling Group Purpose: Design a downhole turbine-operated assembly to power a variety of downhole drilling tools Scope: � Turbine Selection � Component Design � Modular Design � Safety/Compliance Tools Desired Outcome: Final design will incorporate the selection and optimization of existing components
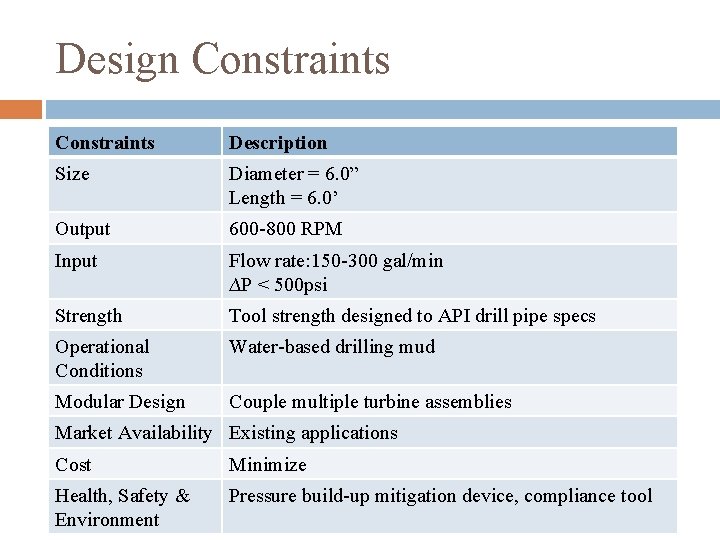
Design Constraints Description Size Diameter = 6. 0” Length = 6. 0’ Output 600 -800 RPM Input Flow rate: 150 -300 gal/min ∆P < 500 psi Strength Tool strength designed to API drill pipe specs Operational Conditions Water-based drilling mud Modular Design Couple multiple turbine assemblies Market Availability Existing applications Cost Minimize Health, Safety & Environment Pressure build-up mitigation device, compliance tool
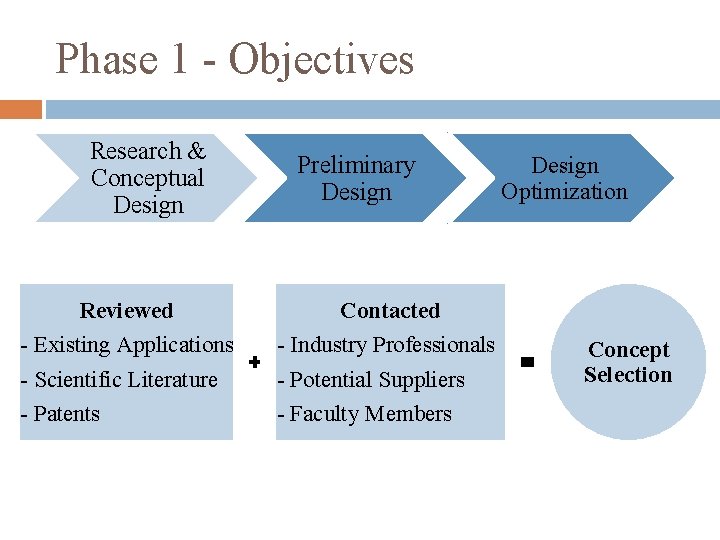
Phase 1 - Objectives Research & Conceptual Design Preliminary Design Reviewed - Existing Applications Contacted - Industry Professionals - Scientific Literature - Potential Suppliers - Patents - Faculty Members Design Optimization Concept Selection
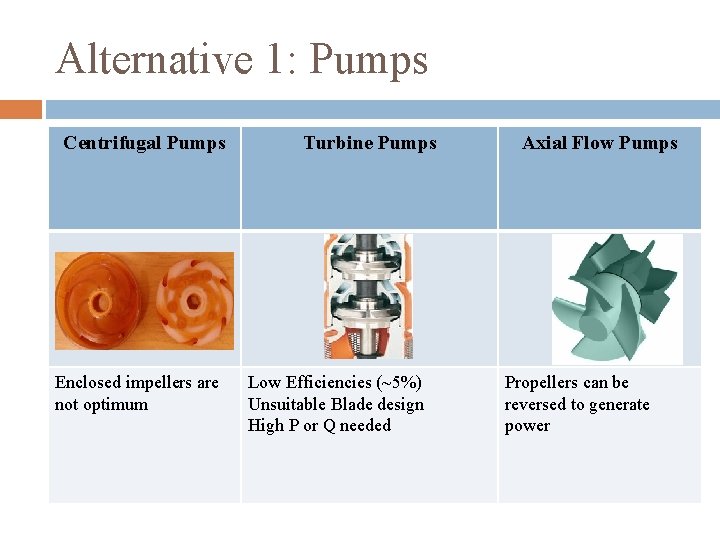
Alternative 1: Pumps Centrifugal Pumps Enclosed impellers are not optimum Turbine Pumps Low Efficiencies (~5%) Unsuitable Blade design High P or Q needed Axial Flow Pumps Propellers can be reversed to generate power
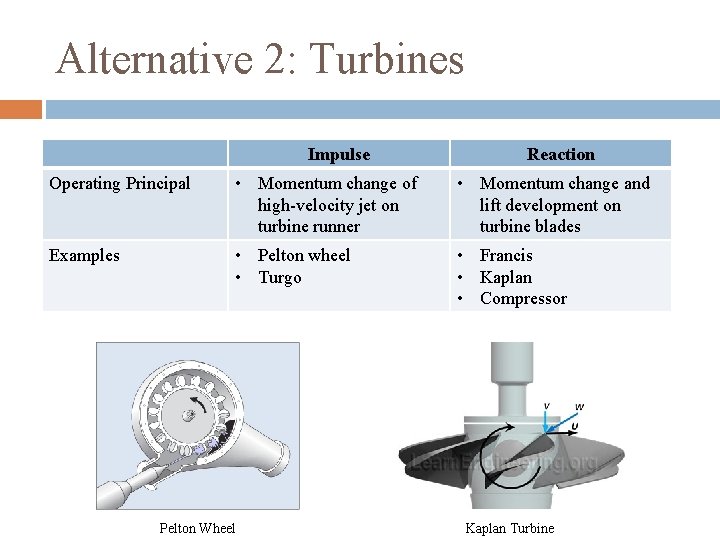
Alternative 2: Turbines Impulse Reaction Operating Principal • Momentum change of high-velocity jet on turbine runner • Momentum change and lift development on turbine blades Examples • Pelton wheel • Turgo • Francis • Kaplan • Compressor Pelton Wheel Kaplan Turbine
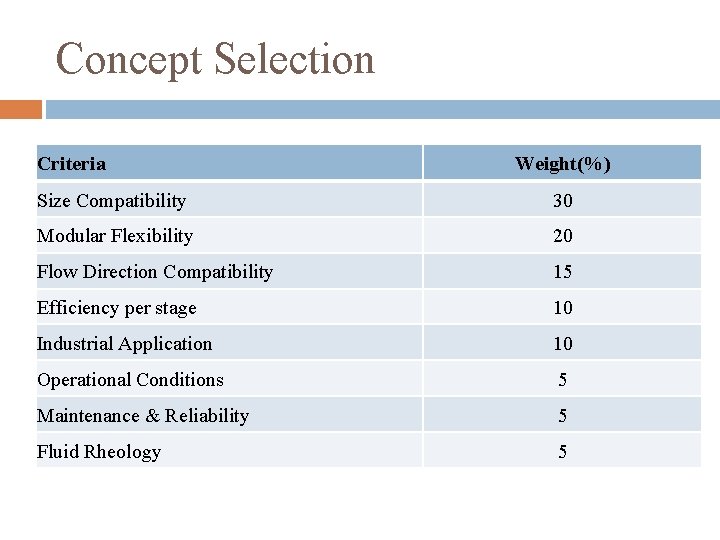
Concept Selection Criteria Weight(%) Size Compatibility 30 Modular Flexibility 20 Flow Direction Compatibility 15 Efficiency per stage 10 Industrial Application 10 Operational Conditions 5 Maintenance & Reliability 5 Fluid Rheology 5
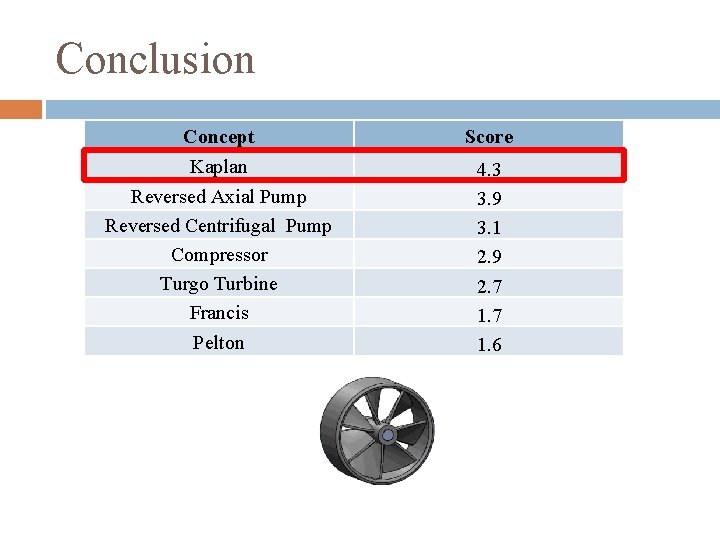
Conclusion Concept Score Kaplan Reversed Axial Pump Reversed Centrifugal Pump Compressor Turgo Turbine Francis Pelton 4. 3 3. 9 3. 1 2. 9 2. 7 1. 6
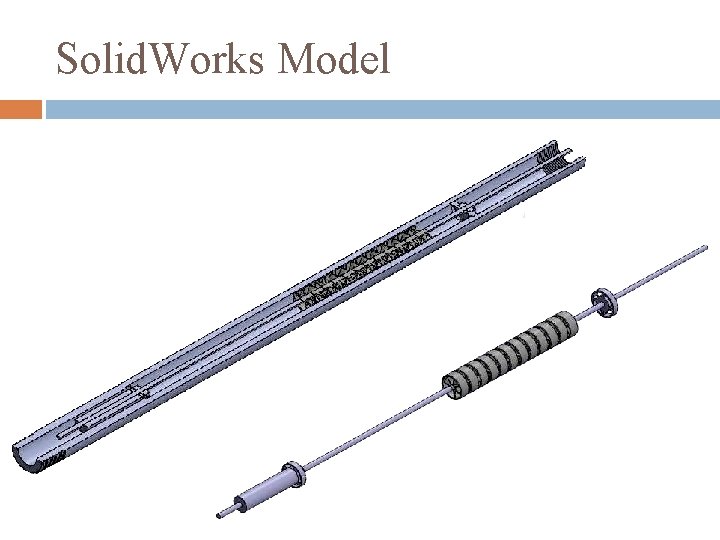
Solid. Works Model
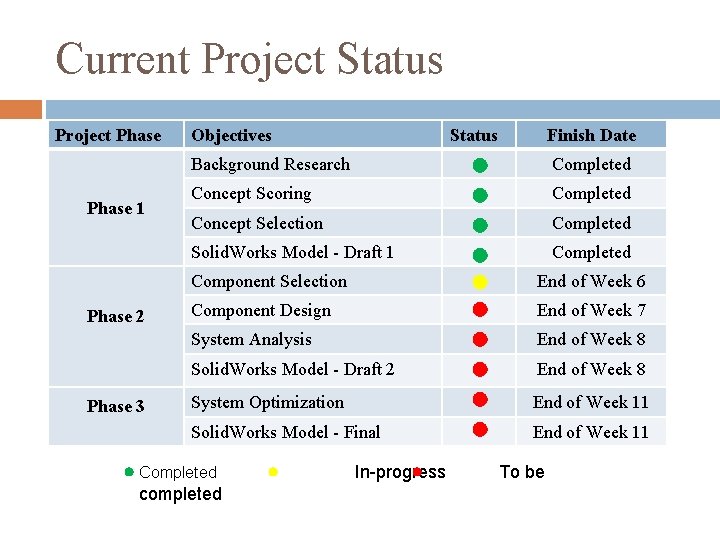
Current Project Status Project Phase 1 Phase 2 Phase 3 Objectives Status Finish Date Background Research Completed Concept Scoring Completed Concept Selection Completed Solid. Works Model - Draft 1 Completed Component Selection End of Week 6 Component Design End of Week 7 System Analysis End of Week 8 Solid. Works Model - Draft 2 End of Week 8 System Optimization End of Week 11 Solid. Works Model - Final End of Week 11 Completed completed In-progress To be
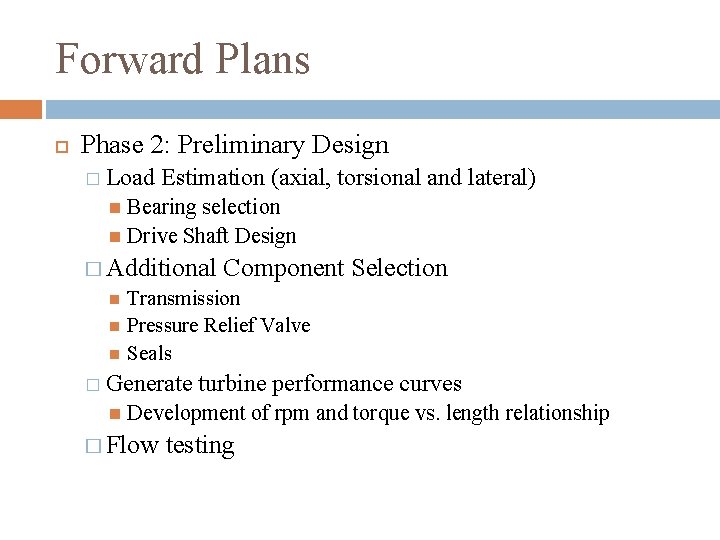
Forward Plans Phase 2: Preliminary Design � Load Estimation (axial, torsional and lateral) Bearing selection Drive Shaft Design � Additional Component Selection Transmission Pressure Relief Valve Seals � Generate turbine performance curves Development of rpm and torque vs. length relationship � Flow testing
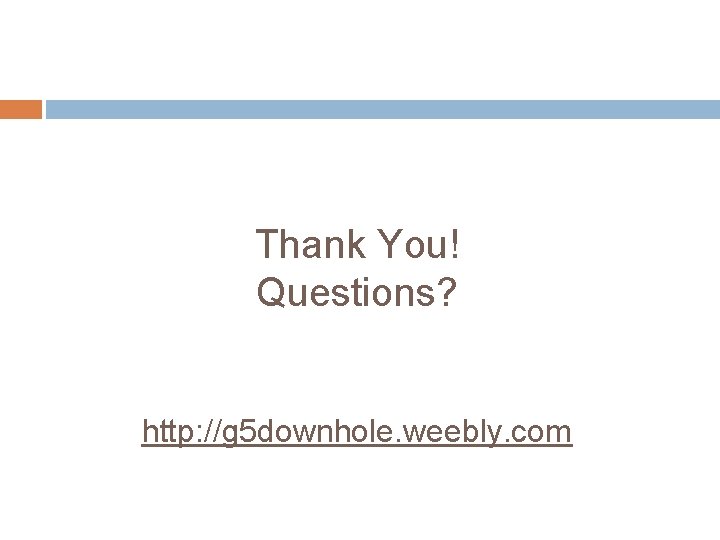
Thank You! Questions? http: //g 5 downhole. weebly. com
- Slides: 15