Dow Chemical ERP Training Importance of Scheduling Hahki
![Dow Chemical ERP Training Importance of Scheduling Hahki [1998]; Schaaf [1999] Dow Chemical ERP Training Importance of Scheduling Hahki [1998]; Schaaf [1999]](https://slidetodoc.com/presentation_image_h/b26bf53c5db0ade719e933095f57c520/image-1.jpg)
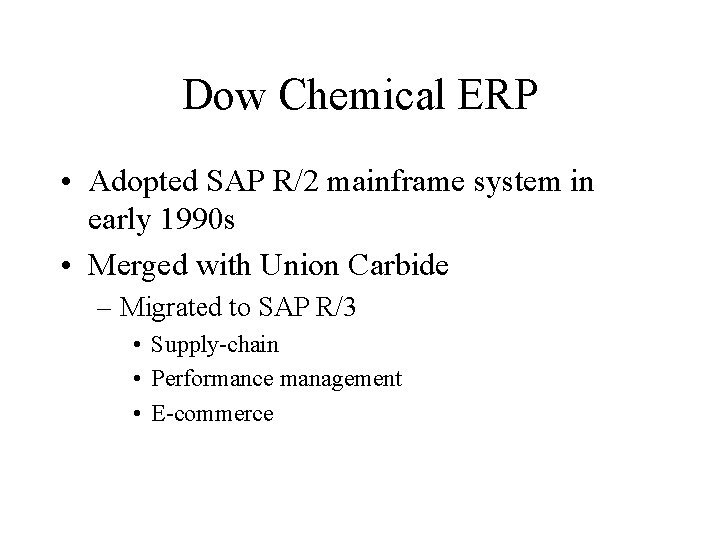
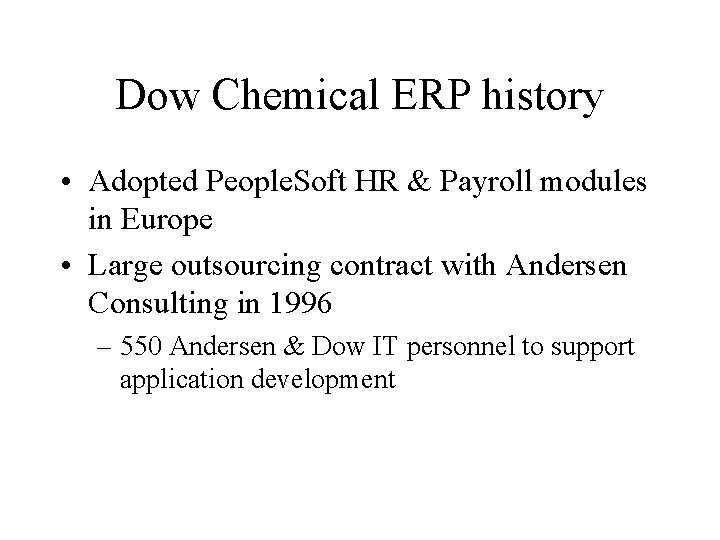
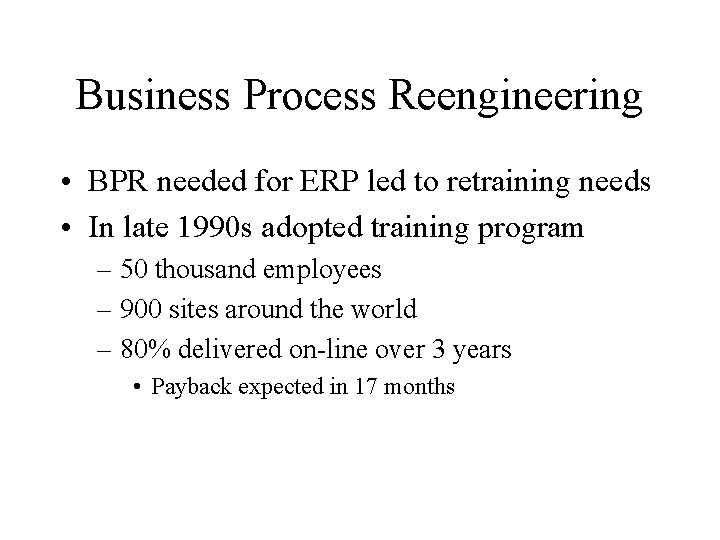
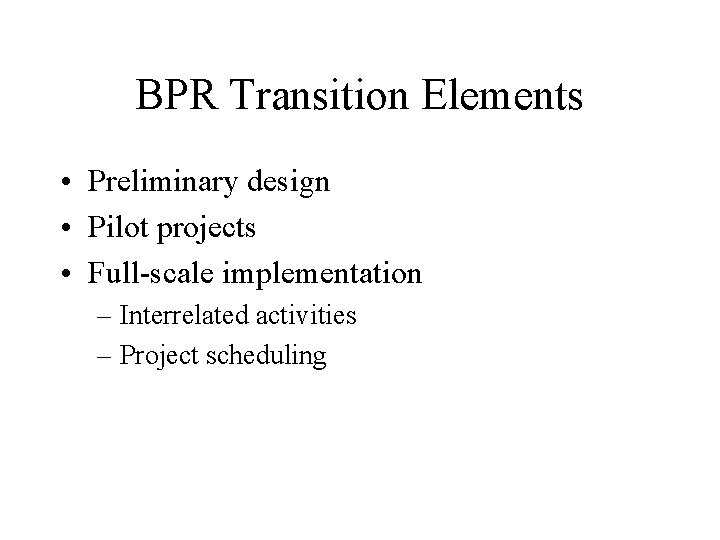
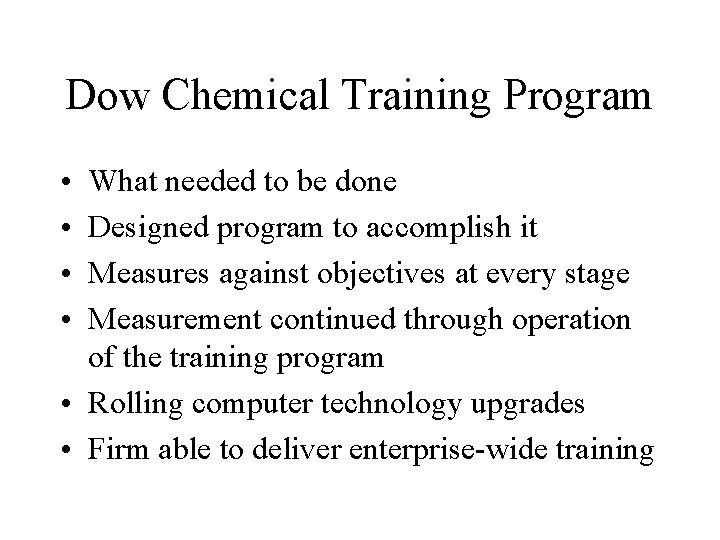
![Owens Corning ERP Implementation Koch [1999] Hammer & Stanton [1999] Owens Corning ERP Implementation Koch [1999] Hammer & Stanton [1999]](https://slidetodoc.com/presentation_image_h/b26bf53c5db0ade719e933095f57c520/image-7.jpg)
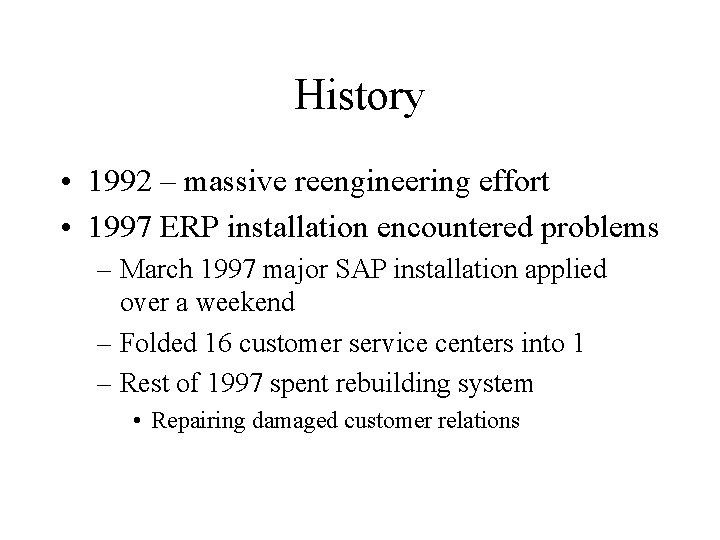
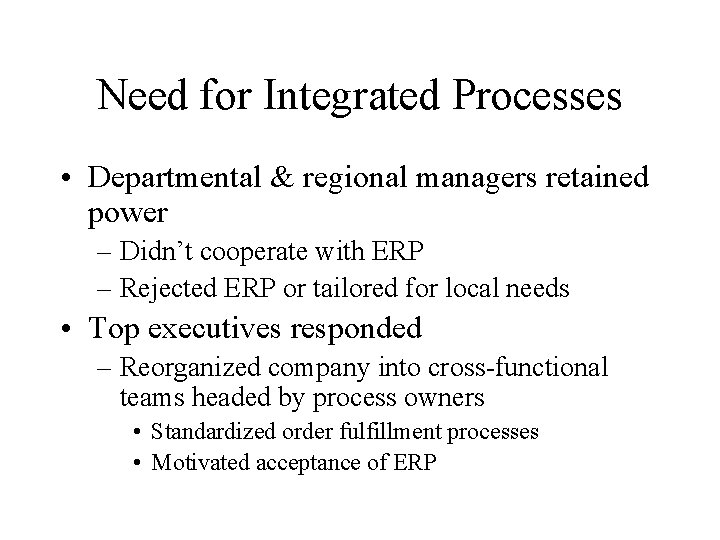
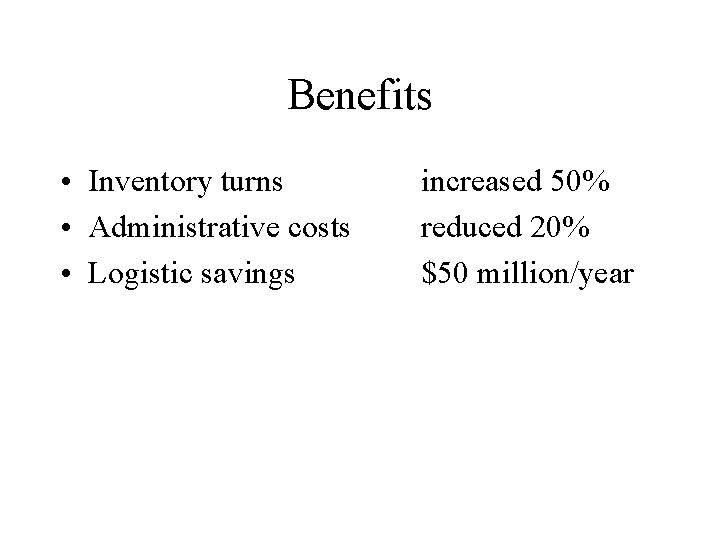
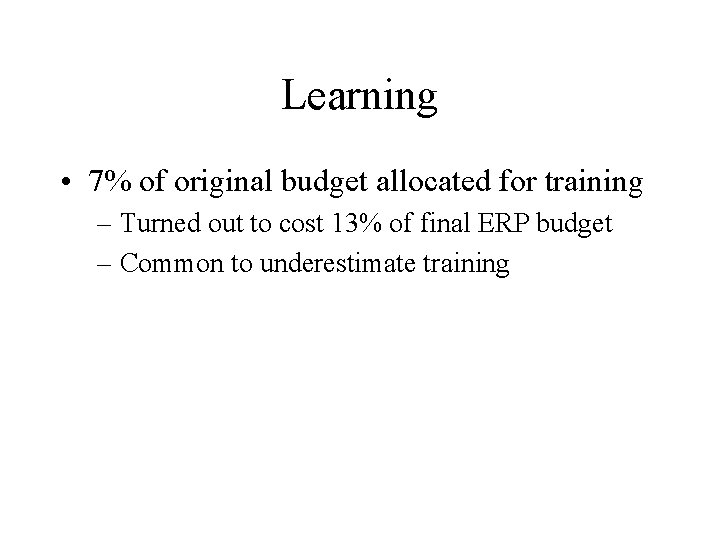
- Slides: 11
![Dow Chemical ERP Training Importance of Scheduling Hahki 1998 Schaaf 1999 Dow Chemical ERP Training Importance of Scheduling Hahki [1998]; Schaaf [1999]](https://slidetodoc.com/presentation_image_h/b26bf53c5db0ade719e933095f57c520/image-1.jpg)
Dow Chemical ERP Training Importance of Scheduling Hahki [1998]; Schaaf [1999]
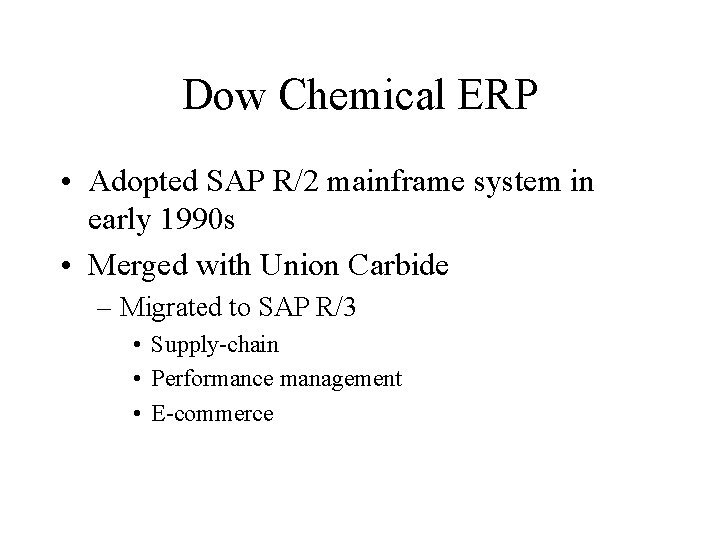
Dow Chemical ERP • Adopted SAP R/2 mainframe system in early 1990 s • Merged with Union Carbide – Migrated to SAP R/3 • Supply-chain • Performance management • E-commerce
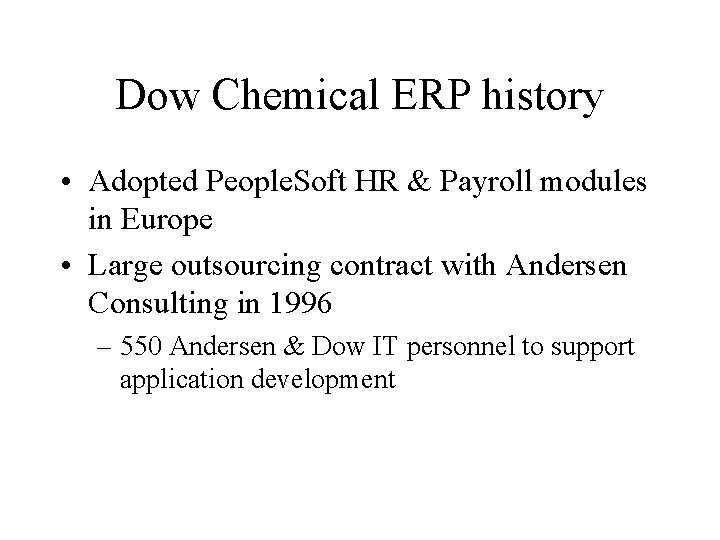
Dow Chemical ERP history • Adopted People. Soft HR & Payroll modules in Europe • Large outsourcing contract with Andersen Consulting in 1996 – 550 Andersen & Dow IT personnel to support application development
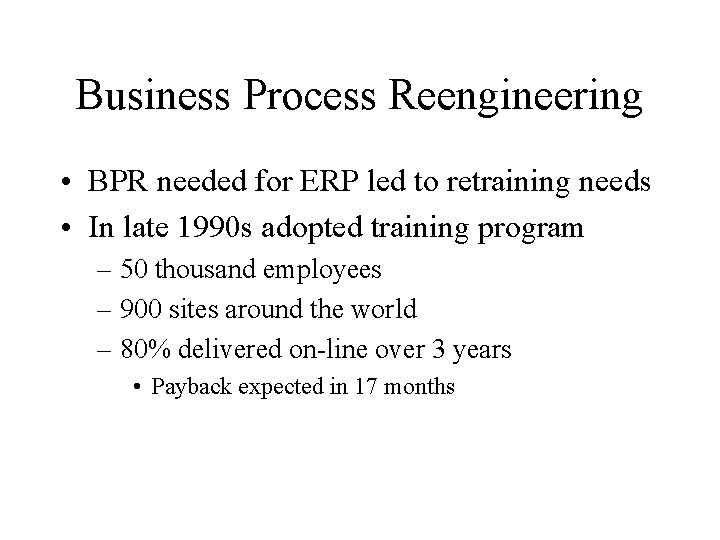
Business Process Reengineering • BPR needed for ERP led to retraining needs • In late 1990 s adopted training program – 50 thousand employees – 900 sites around the world – 80% delivered on-line over 3 years • Payback expected in 17 months
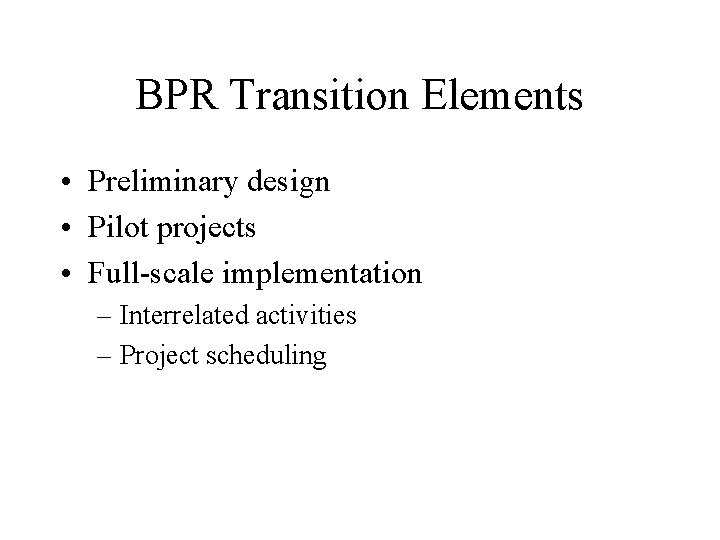
BPR Transition Elements • Preliminary design • Pilot projects • Full-scale implementation – Interrelated activities – Project scheduling
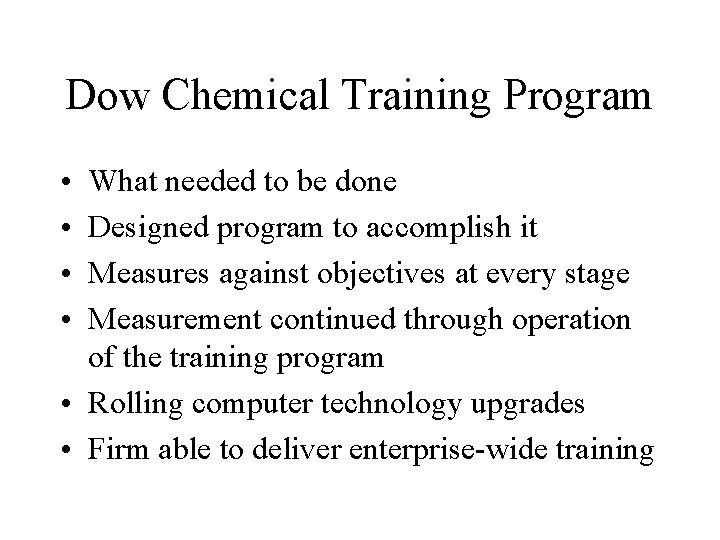
Dow Chemical Training Program • • What needed to be done Designed program to accomplish it Measures against objectives at every stage Measurement continued through operation of the training program • Rolling computer technology upgrades • Firm able to deliver enterprise-wide training
![Owens Corning ERP Implementation Koch 1999 Hammer Stanton 1999 Owens Corning ERP Implementation Koch [1999] Hammer & Stanton [1999]](https://slidetodoc.com/presentation_image_h/b26bf53c5db0ade719e933095f57c520/image-7.jpg)
Owens Corning ERP Implementation Koch [1999] Hammer & Stanton [1999]
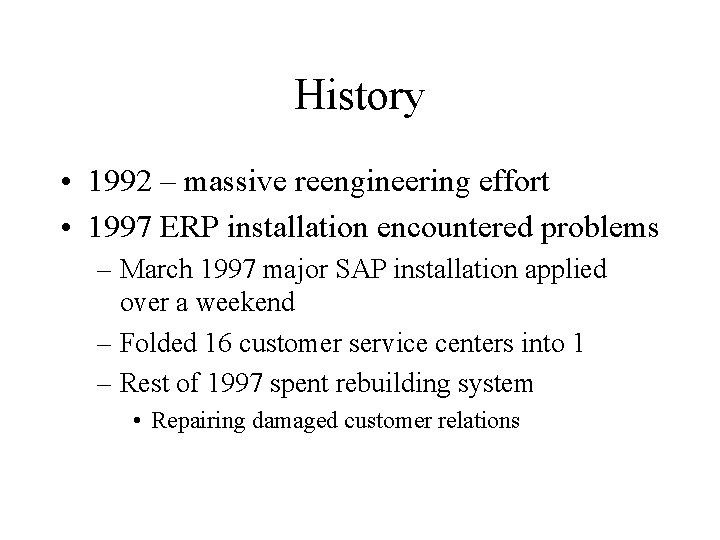
History • 1992 – massive reengineering effort • 1997 ERP installation encountered problems – March 1997 major SAP installation applied over a weekend – Folded 16 customer service centers into 1 – Rest of 1997 spent rebuilding system • Repairing damaged customer relations
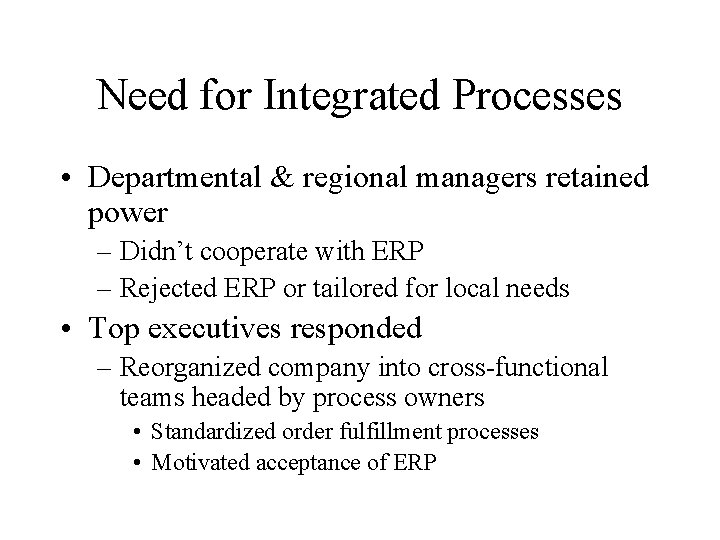
Need for Integrated Processes • Departmental & regional managers retained power – Didn’t cooperate with ERP – Rejected ERP or tailored for local needs • Top executives responded – Reorganized company into cross-functional teams headed by process owners • Standardized order fulfillment processes • Motivated acceptance of ERP
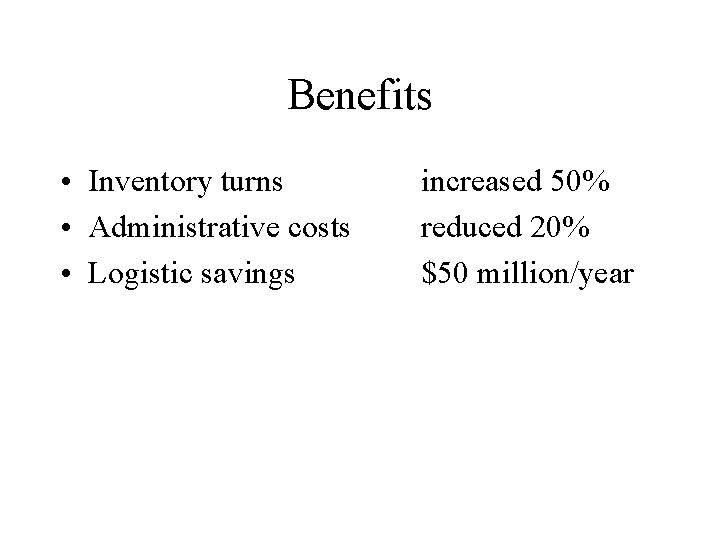
Benefits • Inventory turns • Administrative costs • Logistic savings increased 50% reduced 20% $50 million/year
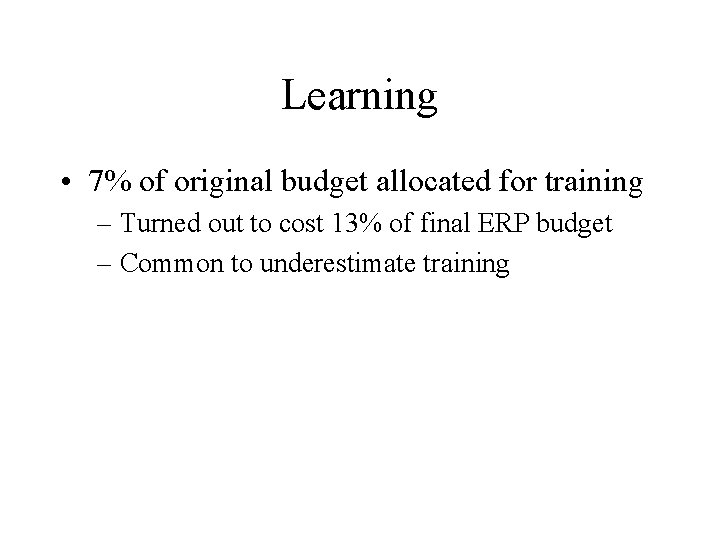
Learning • 7% of original budget allocated for training – Turned out to cost 13% of final ERP budget – Common to underestimate training