DirectDrive Rotary Generator Design by Genetic Algorithm for
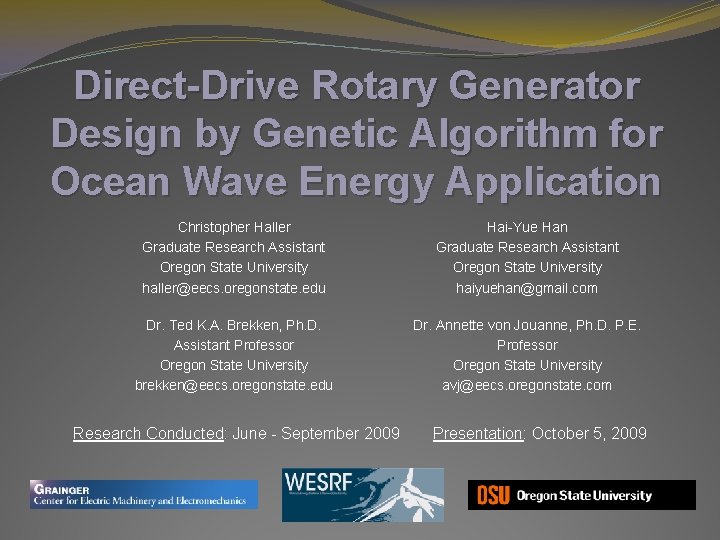
Direct-Drive Rotary Generator Design by Genetic Algorithm for Ocean Wave Energy Application Christopher Haller Graduate Research Assistant Oregon State University haller@eecs. oregonstate. edu Hai-Yue Han Graduate Research Assistant Oregon State University haiyuehan@gmail. com Dr. Ted K. A. Brekken, Ph. D. Assistant Professor Oregon State University brekken@eecs. oregonstate. edu Dr. Annette von Jouanne, Ph. D. P. E. Professor Oregon State University avj@eecs. oregonstate. com Research Conducted: June - September 2009 Presentation: October 5, 2009
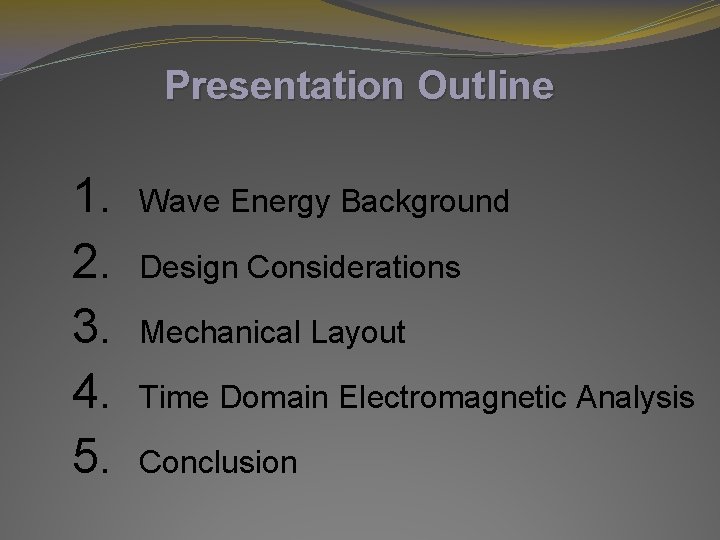
Presentation Outline 1. 2. 3. 4. 5. Wave Energy Background Design Considerations Mechanical Layout Time Domain Electromagnetic Analysis Conclusion
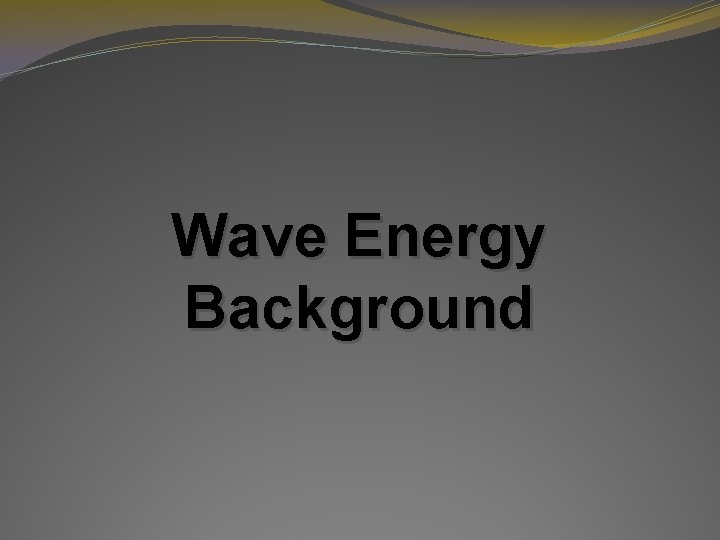
Wave Energy Background
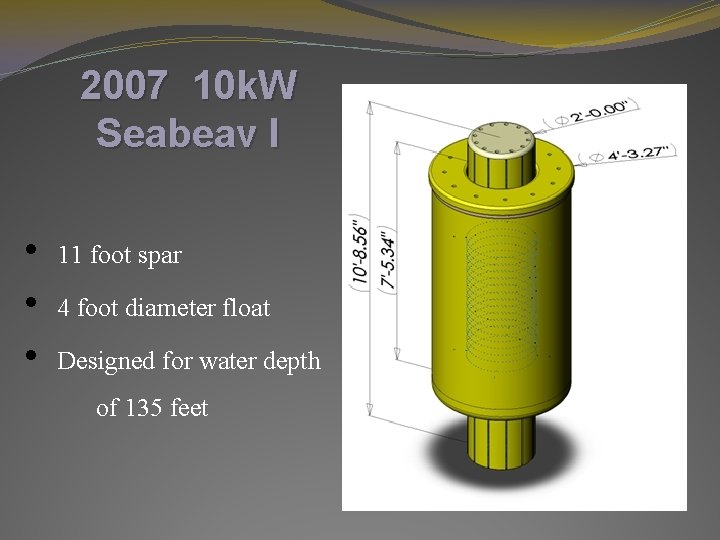
2007 10 k. W Seabeav I • 11 foot spar • 4 foot diameter float • Designed for water depth of 135 feet
![2007 10 k. W Seabeav I Preparing for sea trial in Newport [5] 2007 10 k. W Seabeav I Preparing for sea trial in Newport [5]](http://slidetodoc.com/presentation_image_h/16200ac2cea8497b4f407be837694d40/image-5.jpg)
2007 10 k. W Seabeav I Preparing for sea trial in Newport [5]
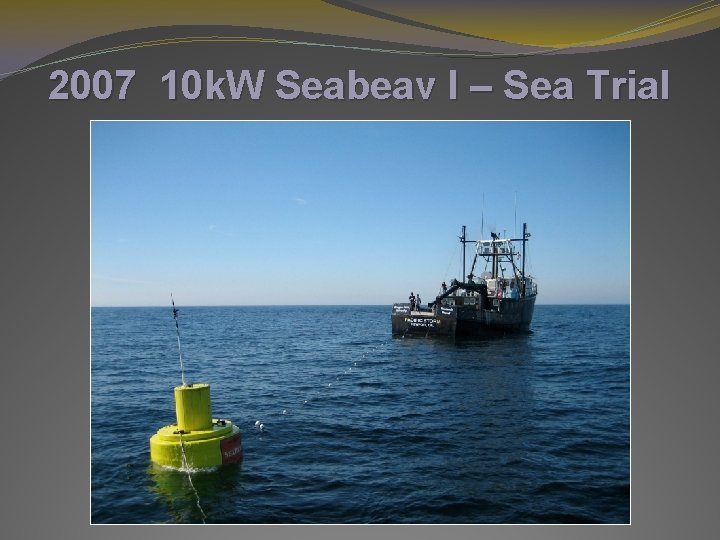
2007 10 k. W Seabeav I – Sea Trial
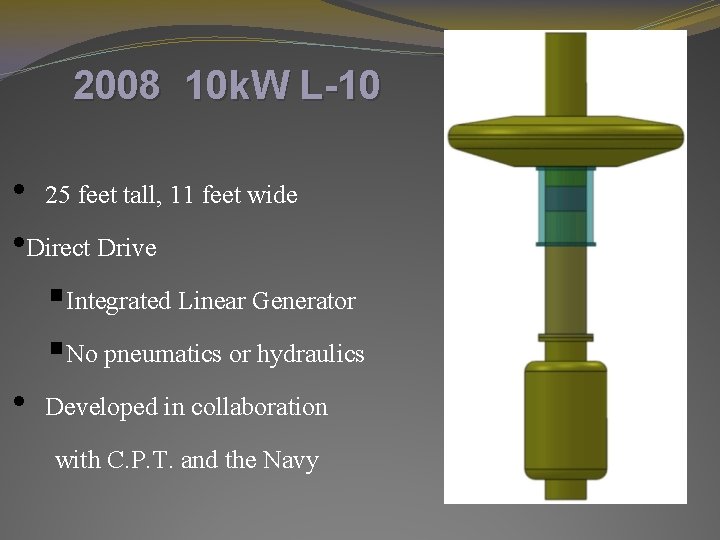
2008 10 k. W L-10 • 25 feet tall, 11 feet wide • Direct Drive §Integrated Linear Generator §No pneumatics or hydraulics • Developed in collaboration with C. P. T. and the Navy
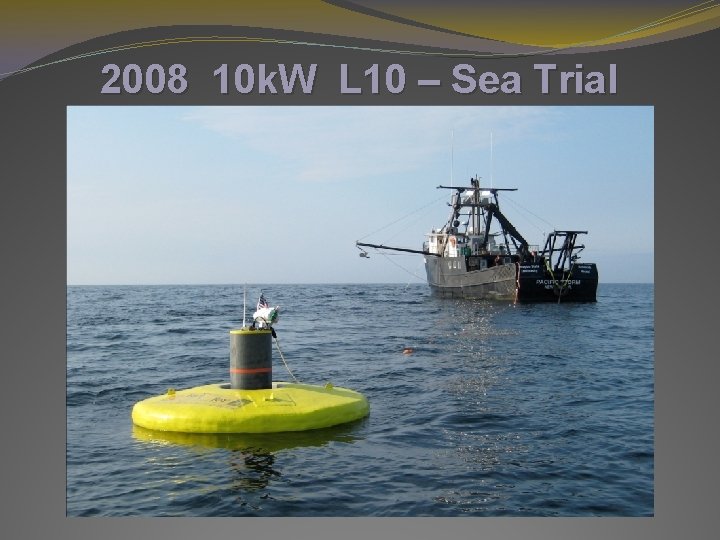
2008 10 k. W L 10 – Sea Trial
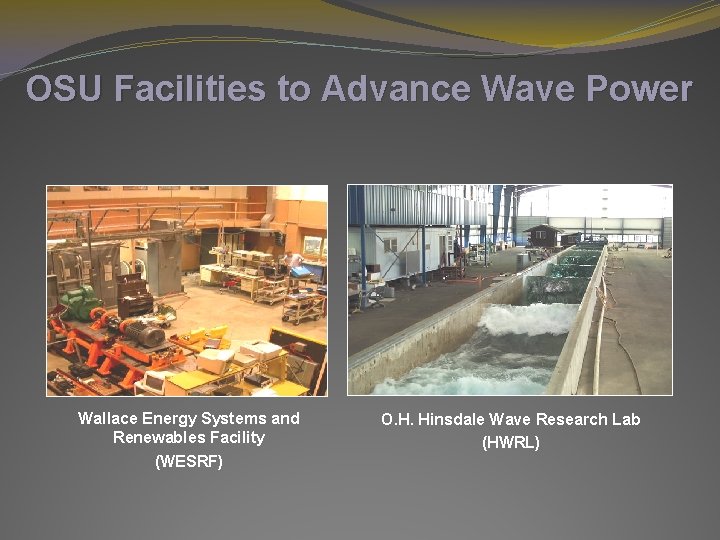
OSU Facilities to Advance Wave Power Wallace Energy Systems and Renewables Facility (WESRF) O. H. Hinsdale Wave Research Lab (HWRL)
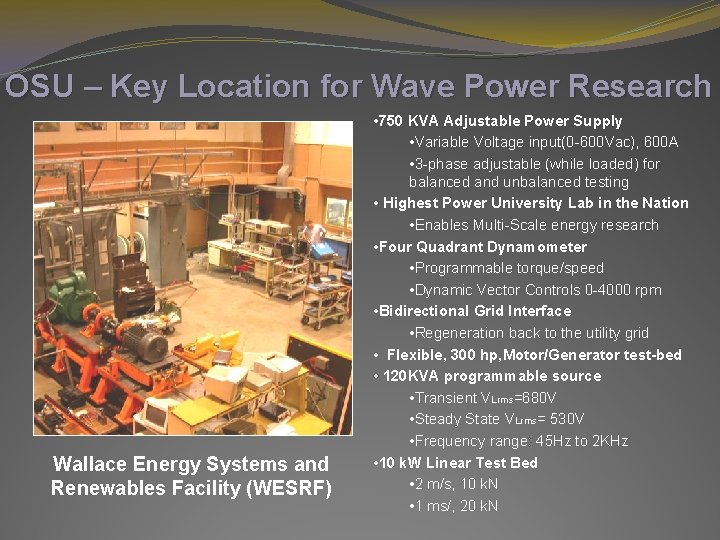
OSU – Key Location for Wave Power Research Wallace Energy Systems and Renewables Facility (WESRF) • 750 KVA Adjustable Power Supply • Variable Voltage input(0 -600 Vac), 600 A • 3 -phase adjustable (while loaded) for balanced and unbalanced testing • Highest Power University Lab in the Nation • Enables Multi-Scale energy research • Four Quadrant Dynamometer • Programmable torque/speed • Dynamic Vector Controls 0 -4000 rpm • Bidirectional Grid Interface • Regeneration back to the utility grid • Flexible, 300 hp, Motor/Generator test-bed • 120 KVA programmable source • Transient VLrms=680 V • Steady State VLrms= 530 V • Frequency range: 45 Hz to 2 KHz • 10 k. W Linear Test Bed • 2 m/s, 10 k. N • 1 ms/, 20 k. N
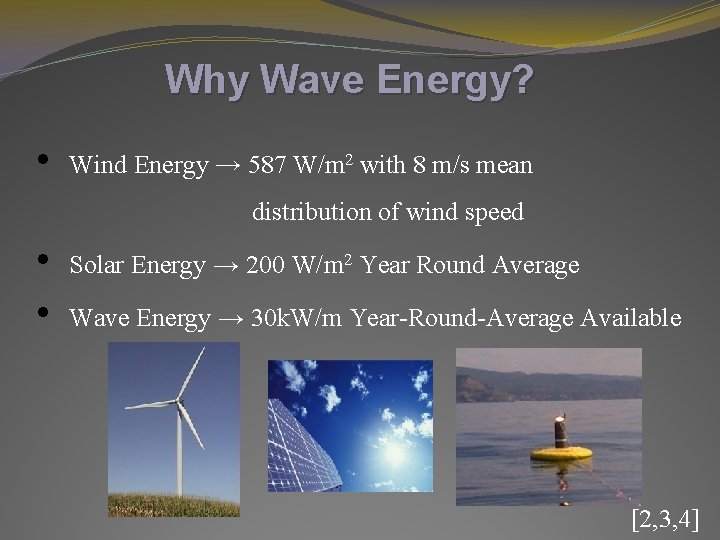
Why Wave Energy? • Wind Energy → 587 W/m 2 with 8 m/s mean distribution of wind speed • Solar Energy → 200 W/m 2 Year Round Average • Wave Energy → 30 k. W/m Year-Round-Average Available [2, 3, 4]
![Why Wave Energy? Wave Power Density in Kilowatts per Meter [k. W/m] [1] Why Wave Energy? Wave Power Density in Kilowatts per Meter [k. W/m] [1]](http://slidetodoc.com/presentation_image_h/16200ac2cea8497b4f407be837694d40/image-12.jpg)
Why Wave Energy? Wave Power Density in Kilowatts per Meter [k. W/m] [1]
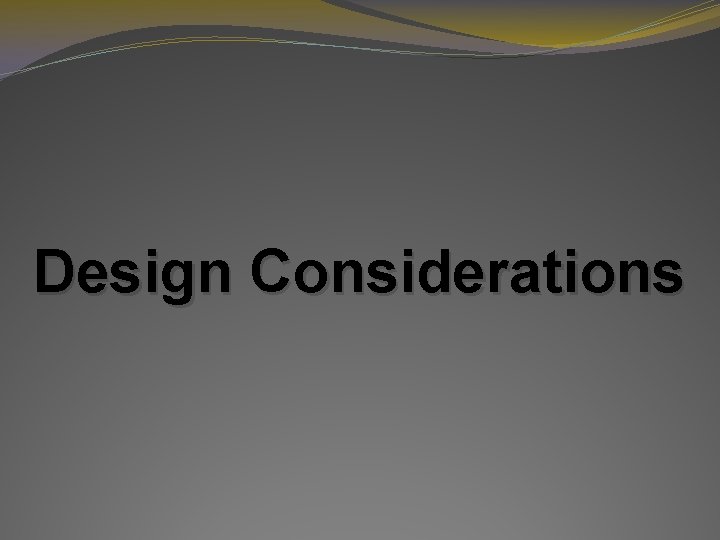
Design Considerations
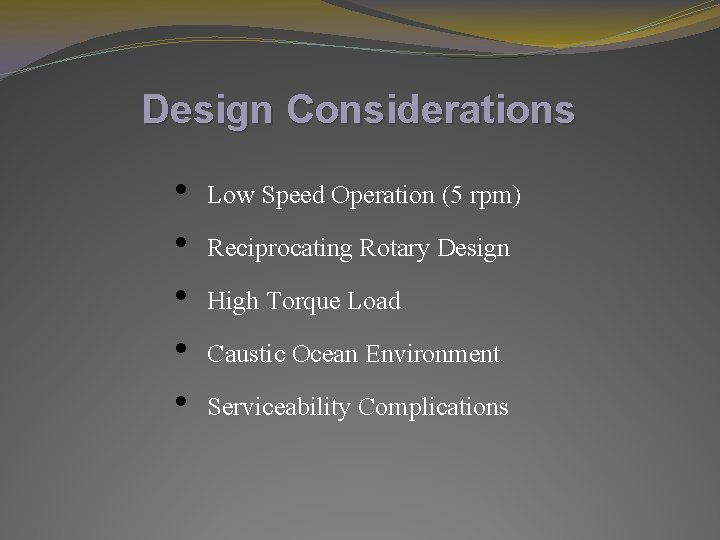
Design Considerations • Low Speed Operation (5 rpm) • Reciprocating Rotary Design • High Torque Load • Caustic Ocean Environment • Serviceability Complications
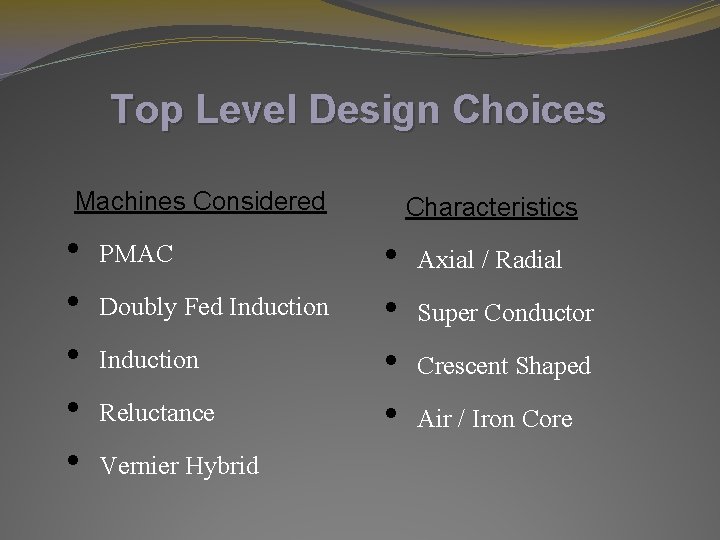
Top Level Design Choices Machines Considered Characteristics • PMAC • Doubly Fed Induction • Reluctance • Vernier Hybrid • Axial / Radial • Super Conductor • Crescent Shaped • Air / Iron Core
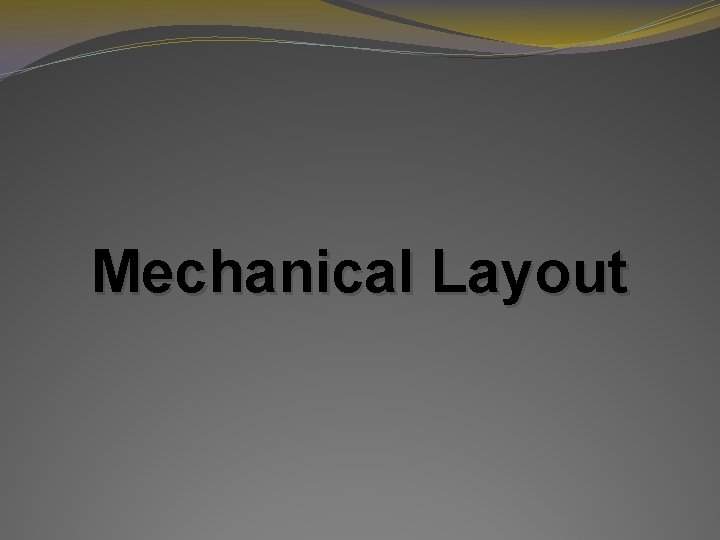
Mechanical Layout
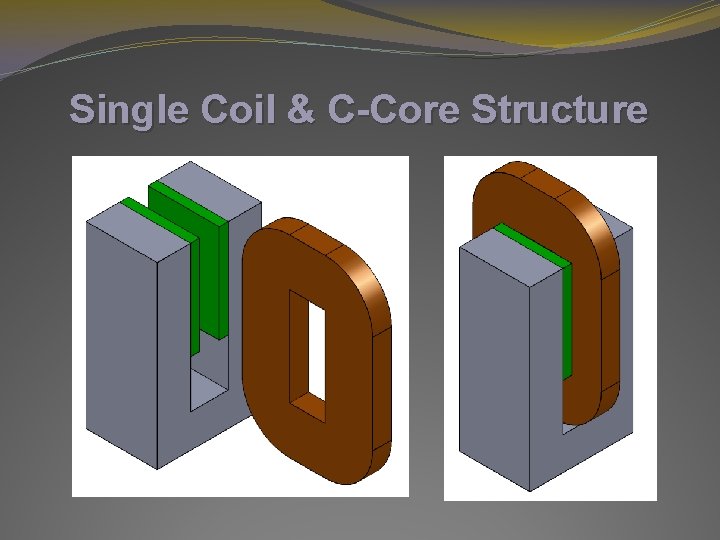
Single Coil & C-Core Structure
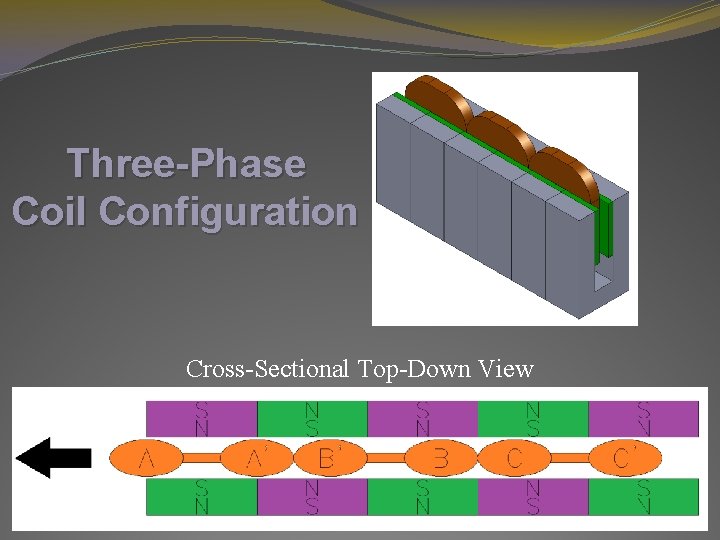
Three-Phase Coil Configuration Cross-Sectional Top-Down View
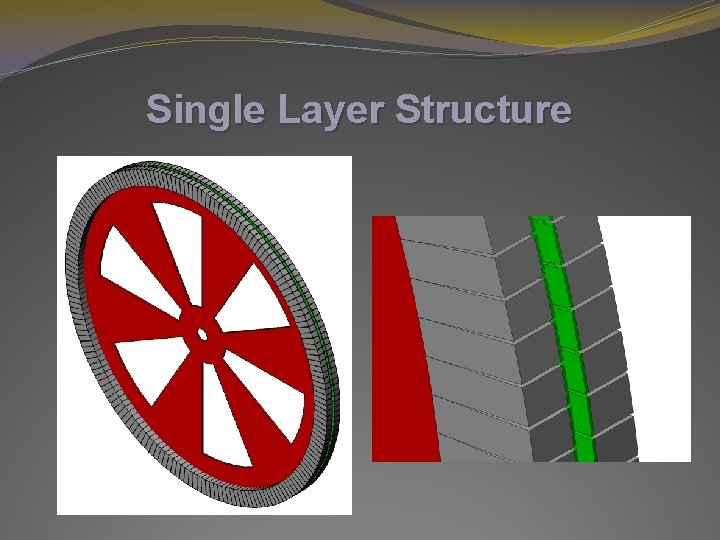
Single Layer Structure
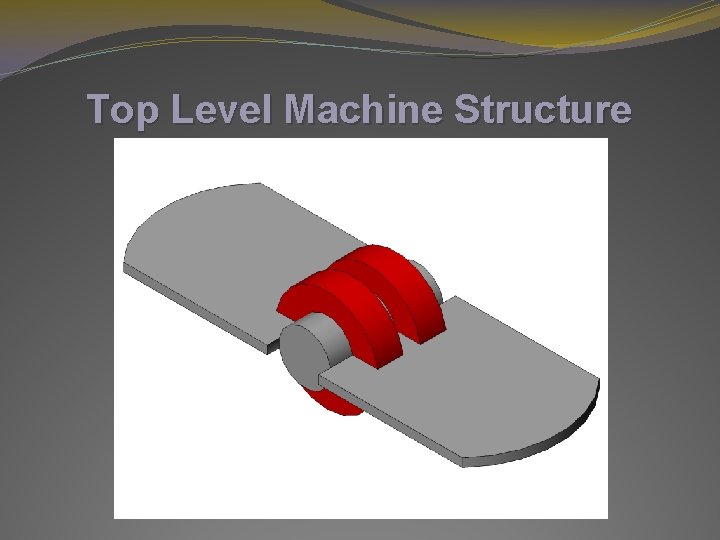
Top Level Machine Structure
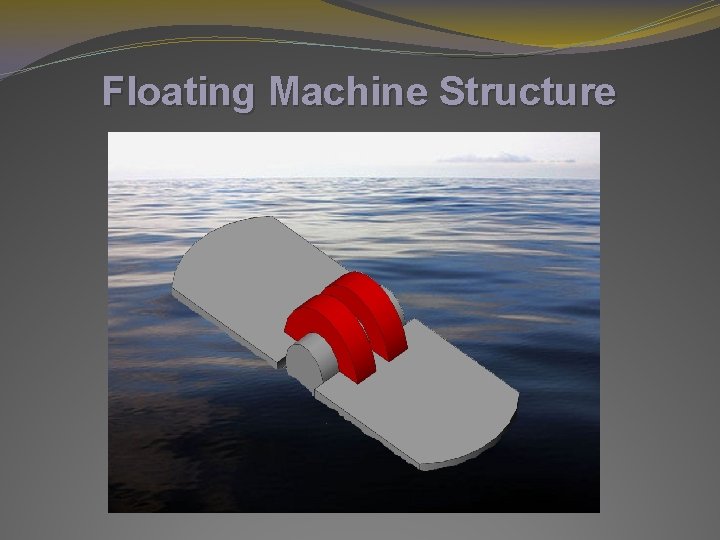
Floating Machine Structure
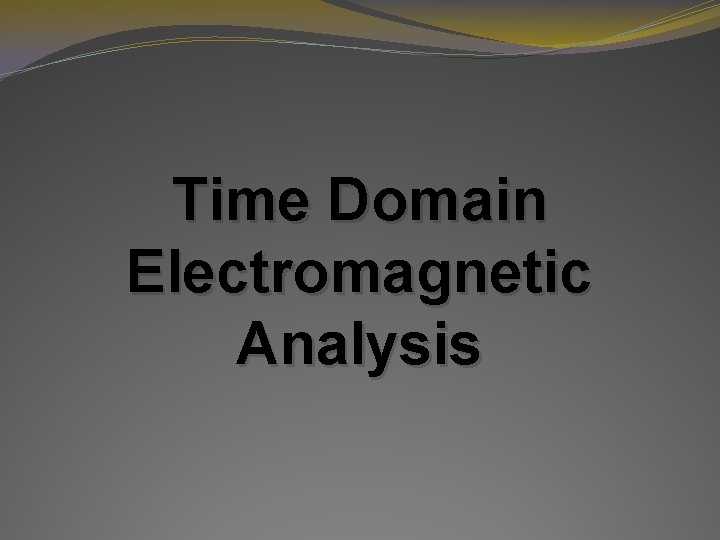
Time Domain Electromagnetic Analysis
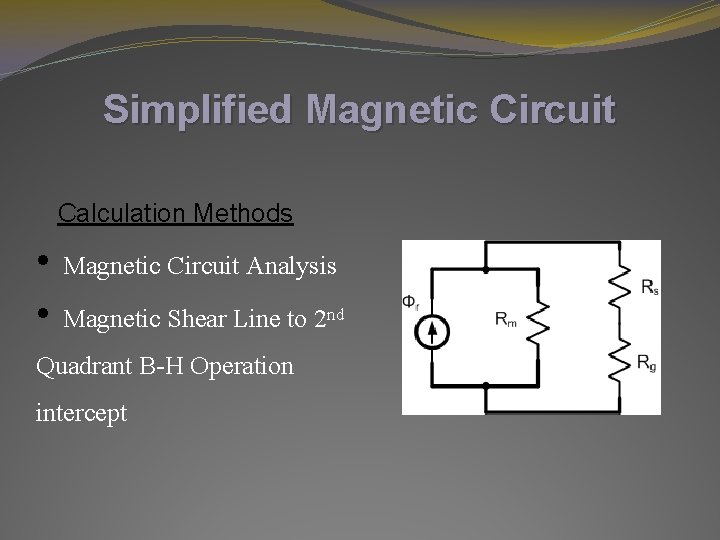
Simplified Magnetic Circuit Calculation Methods • Magnetic Circuit Analysis • Magnetic Shear Line to 2 nd Quadrant B-H Operation intercept
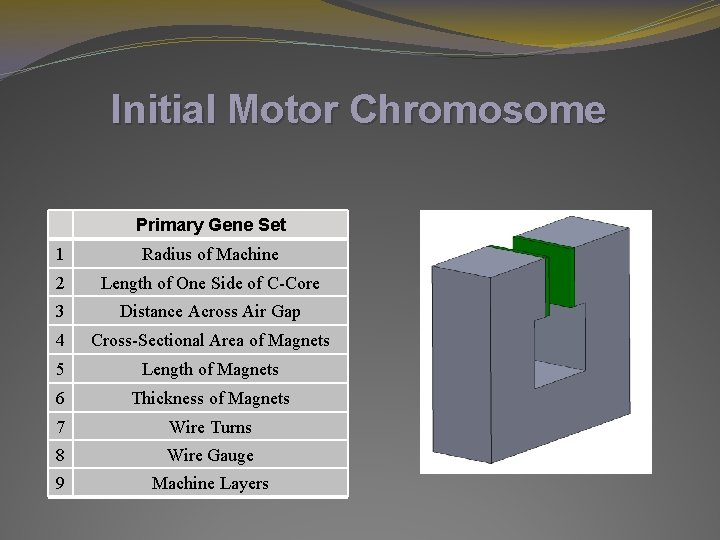
Initial Motor Chromosome Primary Gene Set 1 Radius of Machine 2 Length of One Side of C-Core 3 Distance Across Air Gap 4 Cross-Sectional Area of Magnets 5 Length of Magnets 6 Thickness of Magnets 7 Wire Turns 8 Wire Gauge 9 Machine Layers
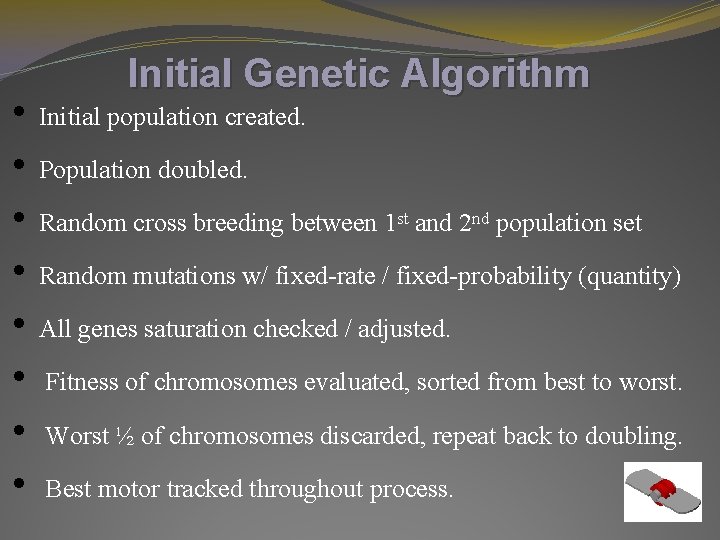
Initial Genetic Algorithm • Initial population created. • Population doubled. • Random cross breeding between 1 st and 2 nd population set • Random mutations w/ fixed-rate / fixed-probability (quantity) • All genes saturation checked / adjusted. • Fitness of chromosomes evaluated, sorted from best to worst. • Worst ½ of chromosomes discarded, repeat back to doubling. • Best motor tracked throughout process.
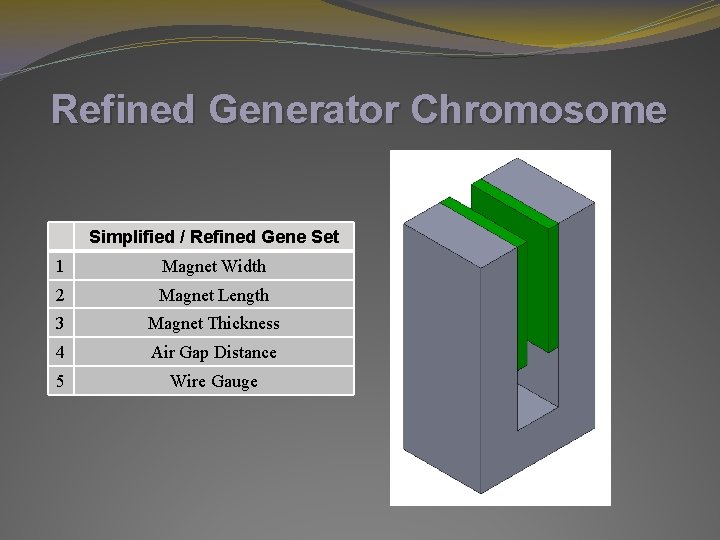
Refined Generator Chromosome Simplified / Refined Gene Set 1 Magnet Width 2 Magnet Length 3 Magnet Thickness 4 Air Gap Distance 5 Wire Gauge
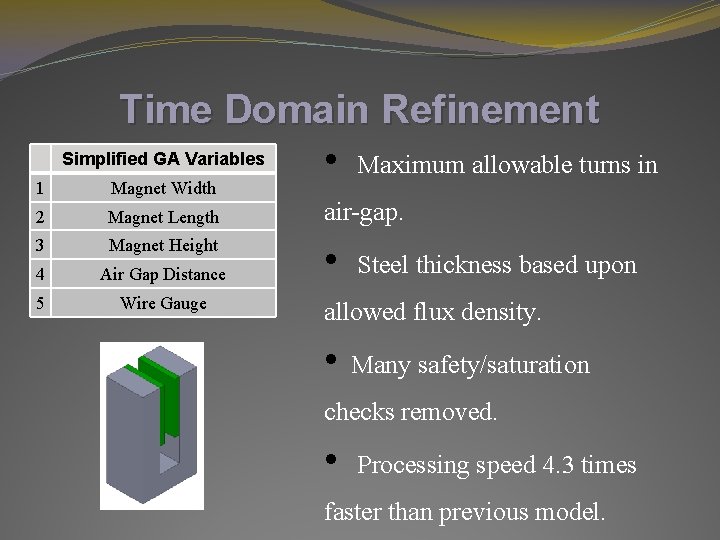
1 Time Domain Refinement Simplified GA Variables • Maximum allowable turns in Magnet Width 2 Magnet Length 3 Magnet Height 4 Air Gap Distance 5 Wire Gauge air-gap. • Steel thickness based upon allowed flux density. • Many safety/saturation checks removed. • Processing speed 4. 3 times faster than previous model.
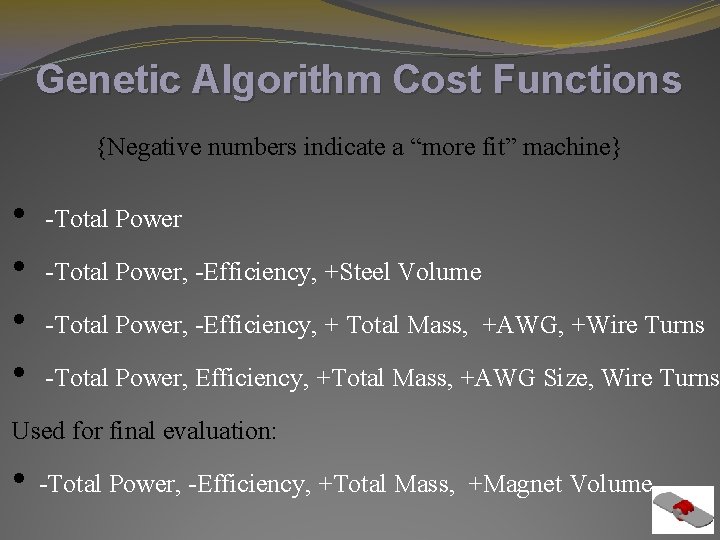
Genetic Algorithm Cost Functions {Negative numbers indicate a “more fit” machine} • -Total Power, -Efficiency, +Steel Volume • -Total Power, -Efficiency, + Total Mass, +AWG, +Wire Turns • -Total Power, Efficiency, +Total Mass, +AWG Size, Wire Turns Used for final evaluation: • -Total Power, -Efficiency, +Total Mass, +Magnet Volume
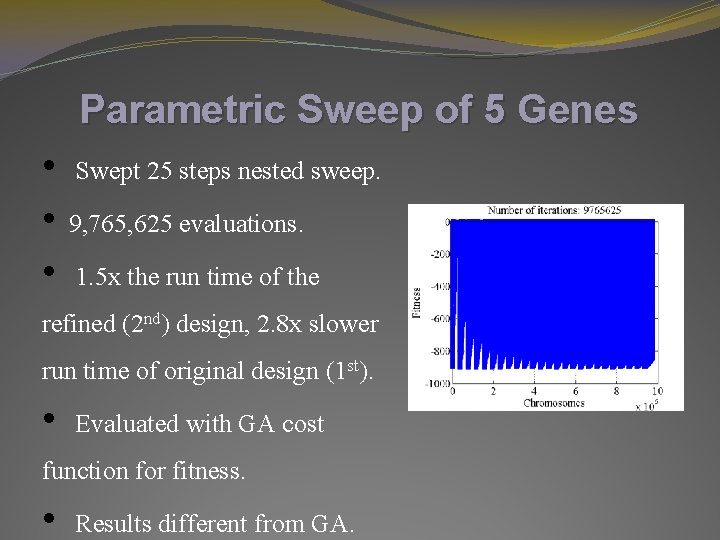
Parametric Sweep of 5 Genes • Swept 25 steps nested sweep. • 9, 765, 625 evaluations. • 1. 5 x the run time of the refined (2 nd) design, 2. 8 x slower run time of original design (1 st). • Evaluated with GA cost function for fitness. • Results different from GA.
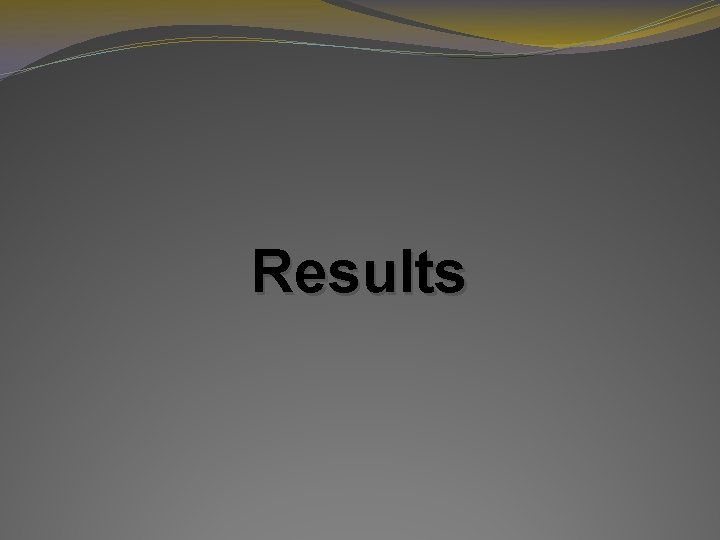
Results
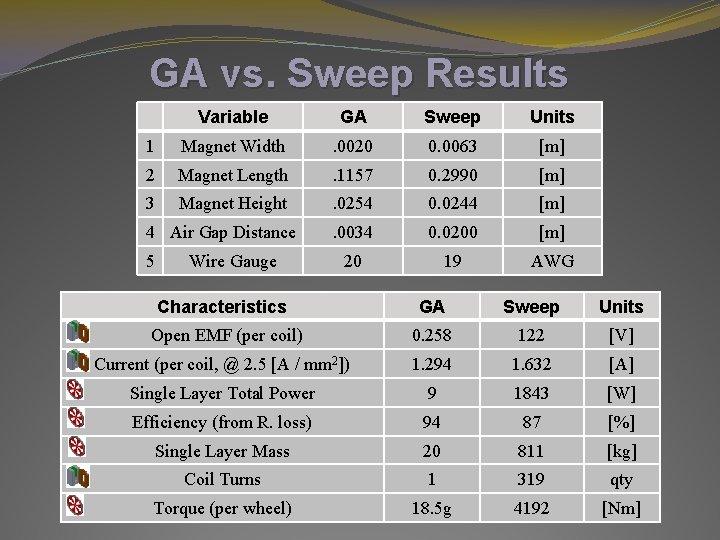
GA vs. Sweep Results Variable GA Sweep Units 1 Magnet Width . 0020 0. 0063 [m] 2 Magnet Length . 1157 0. 2990 [m] 3 Magnet Height . 0254 0. 0244 [m] . 0034 0. 0200 [m] 20 19 AWG 4 Air Gap Distance 5 Wire Gauge Characteristics GA Sweep Units Open EMF (per coil) 0. 258 122 [V] Current (per coil, @ 2. 5 [A / mm 2]) 1. 294 1. 632 [A] Single Layer Total Power 9 1843 [W] Efficiency (from R. loss) 94 87 [%] Single Layer Mass 20 811 [kg] Coil Turns 1 319 qty Torque (per wheel) 18. 5 g 4192 [Nm]
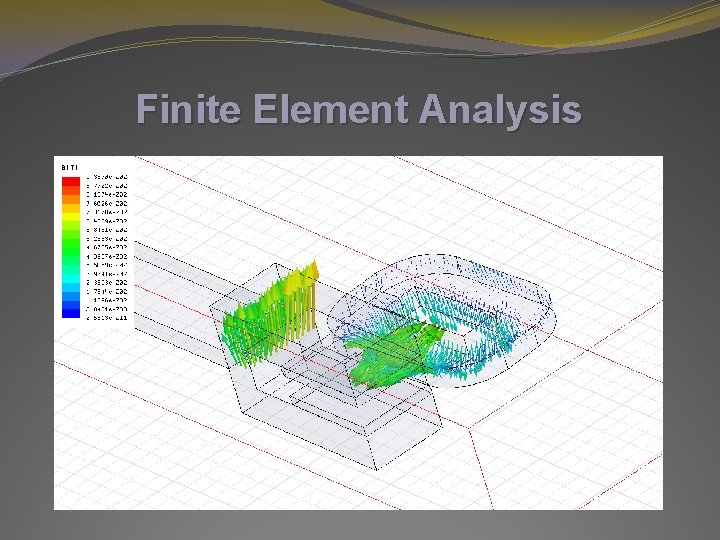
Finite Element Analysis
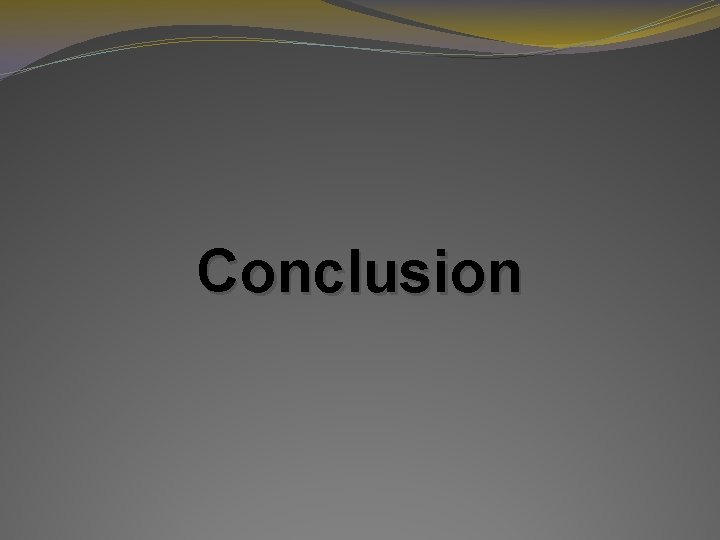
Conclusion
![Conclusions & Future Work Conclusions: • 5 [rpm] generator is feasible. • Generator possible, Conclusions & Future Work Conclusions: • 5 [rpm] generator is feasible. • Generator possible,](http://slidetodoc.com/presentation_image_h/16200ac2cea8497b4f407be837694d40/image-34.jpg)
Conclusions & Future Work Conclusions: • 5 [rpm] generator is feasible. • Generator possible, but heavy. • Weight and slow speed lead to issue of cost. Future Work Direction: • Examine larger variety of motor topologies. • Perform more in-depth cost analysis. • Refinements to manufacturability.
![Bibliography [1] http: //www. geni. org/globalenergy/library/renewable-energy-resources/ocean. shtml Global Energy Network Institute [2] http: //blogs. Bibliography [1] http: //www. geni. org/globalenergy/library/renewable-energy-resources/ocean. shtml Global Energy Network Institute [2] http: //blogs.](http://slidetodoc.com/presentation_image_h/16200ac2cea8497b4f407be837694d40/image-35.jpg)
Bibliography [1] http: //www. geni. org/globalenergy/library/renewable-energy-resources/ocean. shtml Global Energy Network Institute [2] http: //blogs. mysanantonio. com/weblogs/clockingin/wind%20 turbine. jpg [3] http: //venturebeat. com/wp-content/uploads/2009/07/solar-panel-1. jpg [4] http: //eecs. oregonstate. edu/wesrf/projects/images/Wave%20 Energy_Final. ppt [5] Steven Ernst. Personal interview, 2009. Oregon State University. [6] Duane C. Hanselman. Brushless Permanent-Magnet Motor Design, 1994. [7] Magcraft. Permanent magnet selection and design handbook. National Imports, April 2007. [8] Ned Mohan. Electric Drives: An Integrative Approach, 2003. [9] Joseph Prudell. Email, 2009. Oregon State University. [10]Joseph Prudell. Novel design and implementation of a permanent magnet linear tubular generator for ocean wave energy conversion, 2007. Thesis for Master of Science. [11] P. C. Sen. Principles of Electric Machines and Power Electronics, 1997. [12] Mueller & Mc. Donald. A Lightweight Low Speed Permanent Magnet Electrical Generator for Direct-Drive Wind Turbines, 2008.
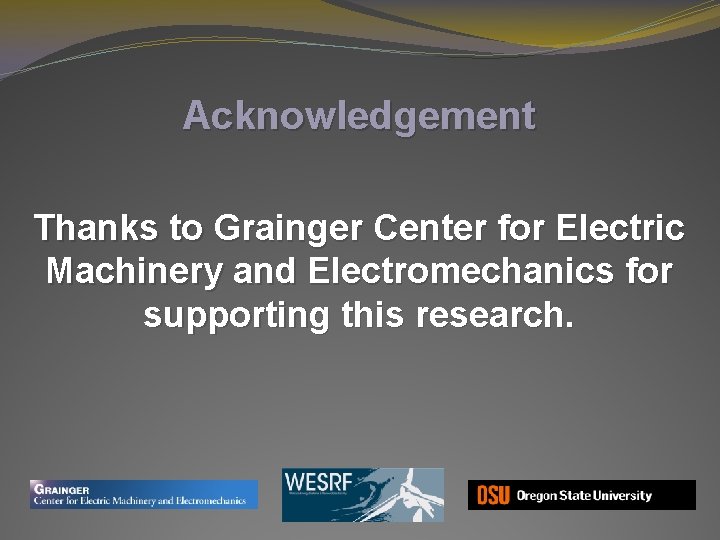
Acknowledgement Thanks to Grainger Center for Electric Machinery and Electromechanics for supporting this research.
- Slides: 36