Design of Heat Exchanger Double Pipe Heat Exchager
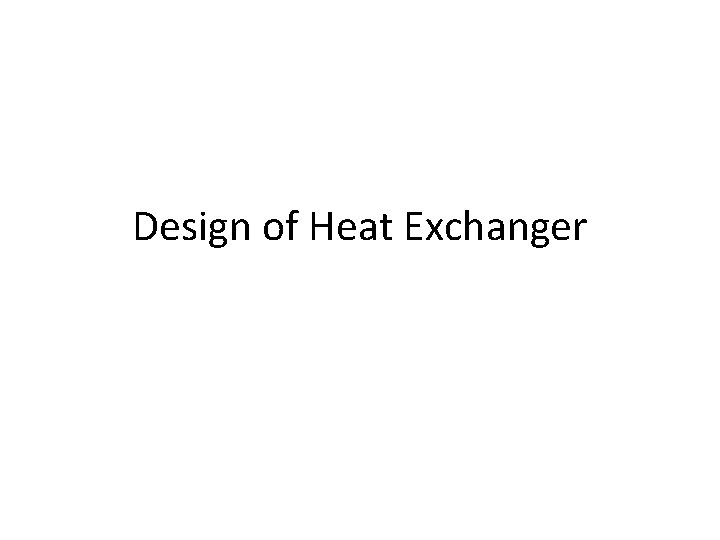
Design of Heat Exchanger
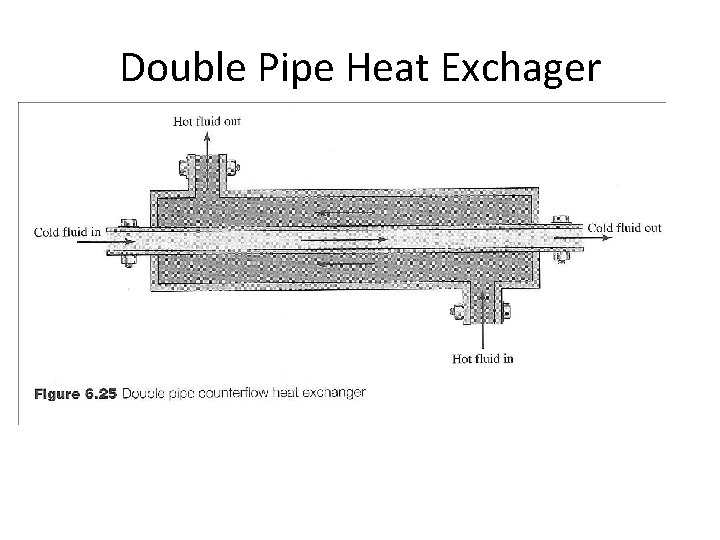
Double Pipe Heat Exchager
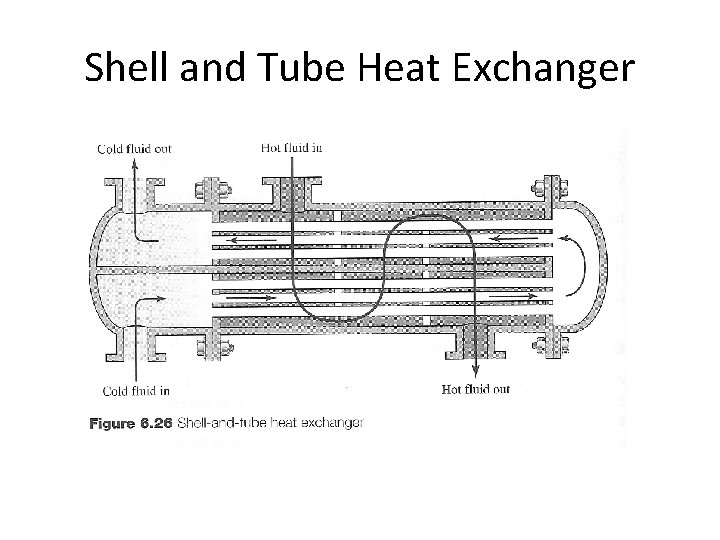
Shell and Tube Heat Exchanger
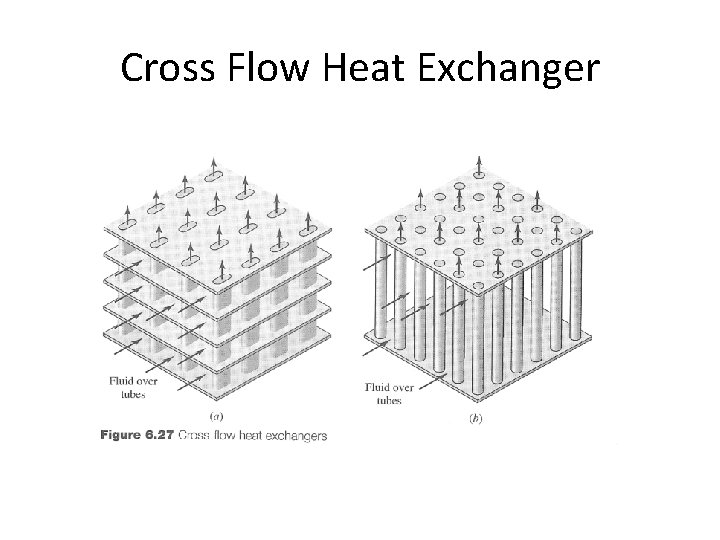
Cross Flow Heat Exchanger
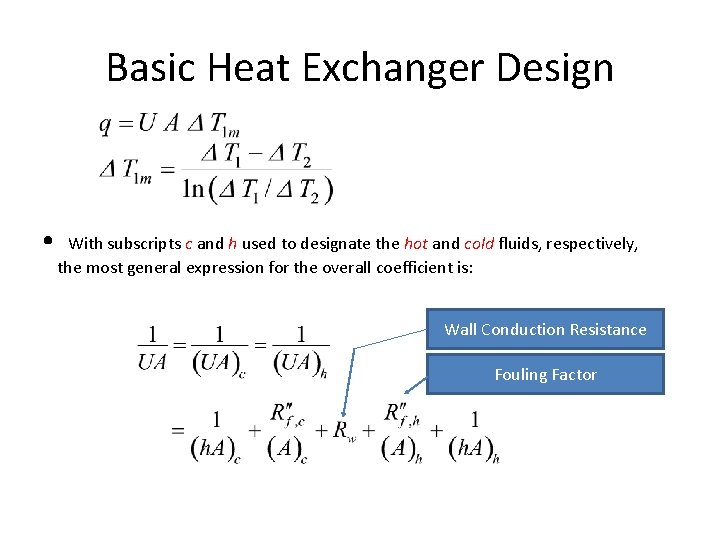
Basic Heat Exchanger Design • With subscripts c and h used to designate the hot and cold fluids, respectively, the most general expression for the overall coefficient is: Wall Conduction Resistance Fouling Factor
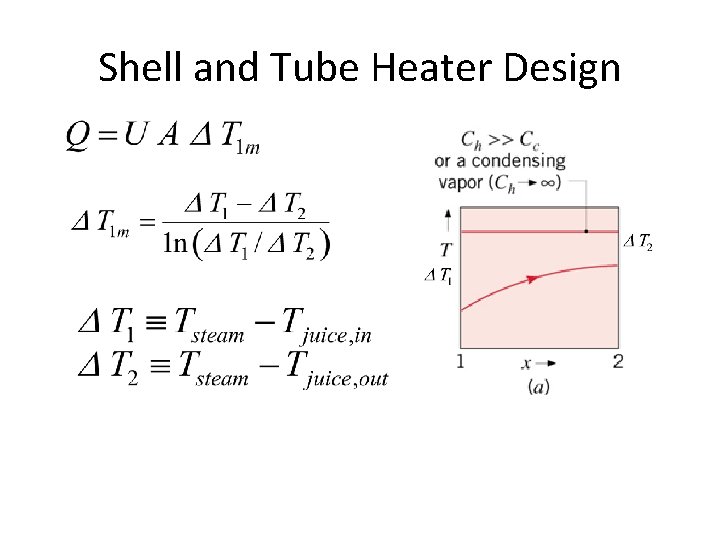
Shell and Tube Heater Design
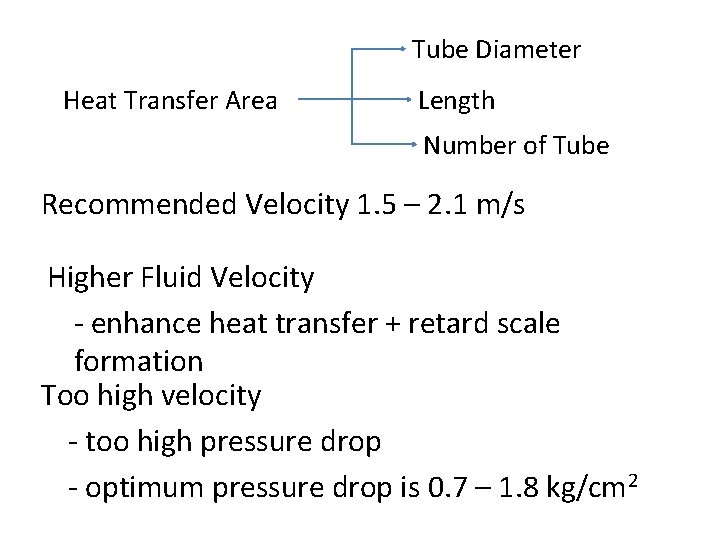
Tube Diameter Heat Transfer Area Length Number of Tube Recommended Velocity 1. 5 – 2. 1 m/s Higher Fluid Velocity - enhance heat transfer + retard scale formation Too high velocity - too high pressure drop - optimum pressure drop is 0. 7 – 1. 8 kg/cm 2
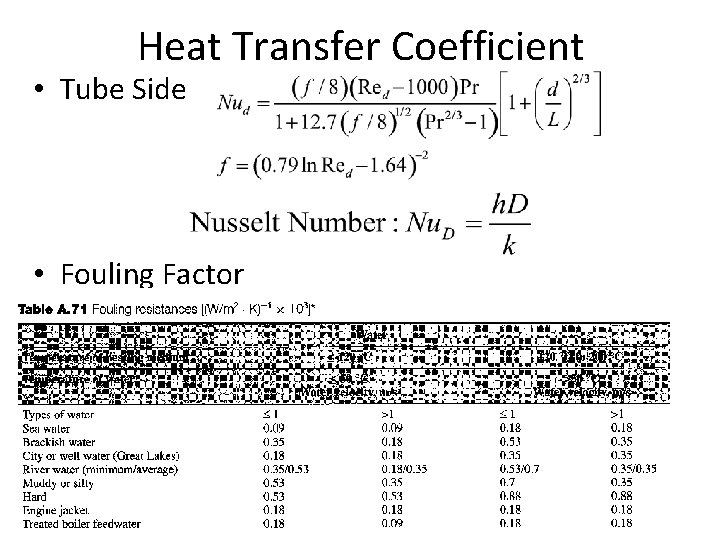
Heat Transfer Coefficient • Tube Side • Fouling Factor
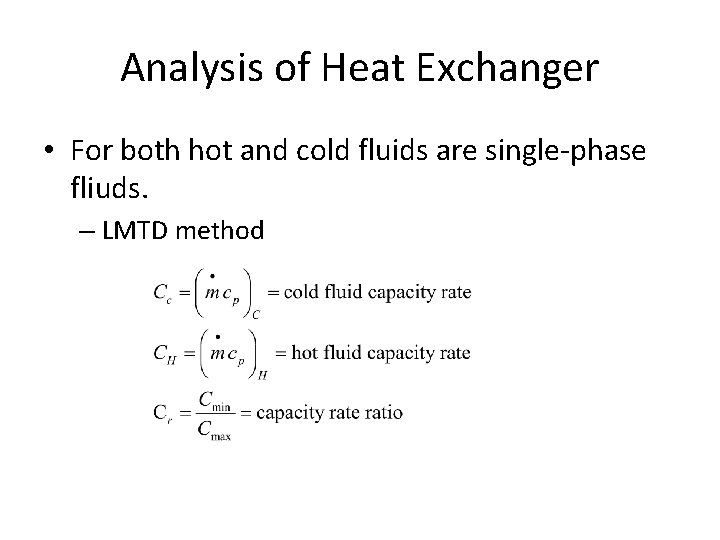
Analysis of Heat Exchanger • For both hot and cold fluids are single-phase fliuds. – LMTD method
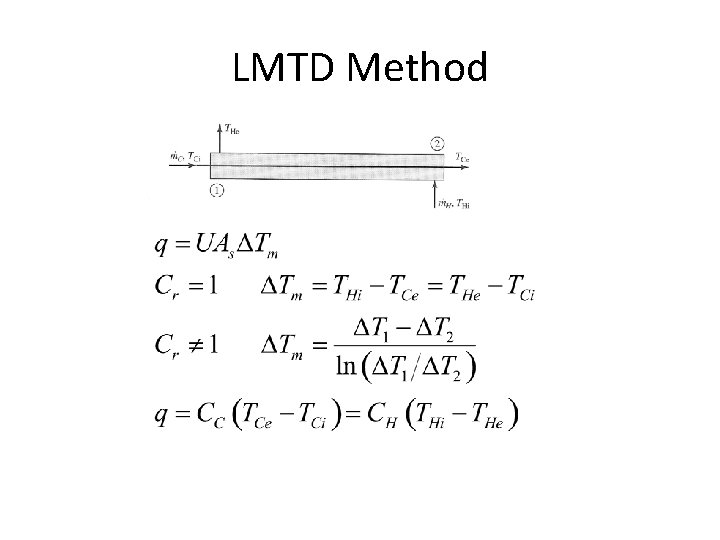
LMTD Method
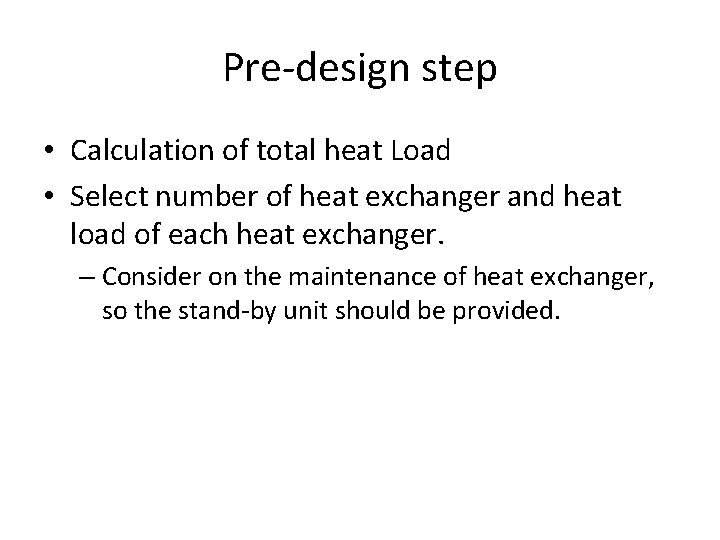
Pre-design step • Calculation of total heat Load • Select number of heat exchanger and heat load of each heat exchanger. – Consider on the maintenance of heat exchanger, so the stand-by unit should be provided.
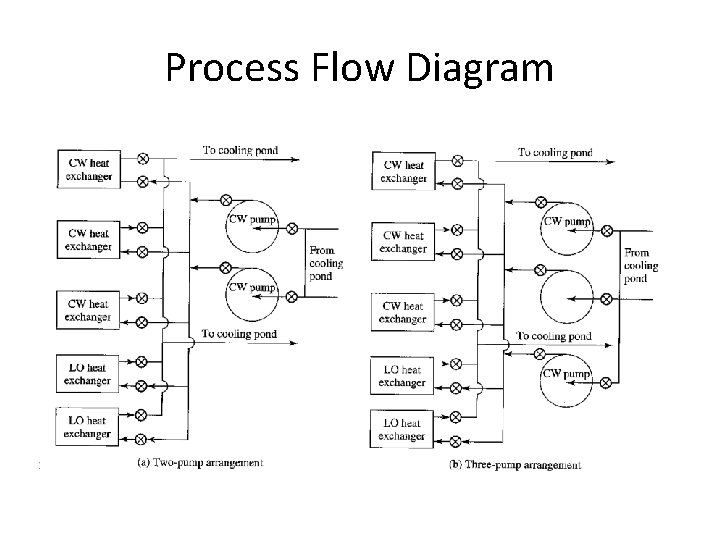
Process Flow Diagram
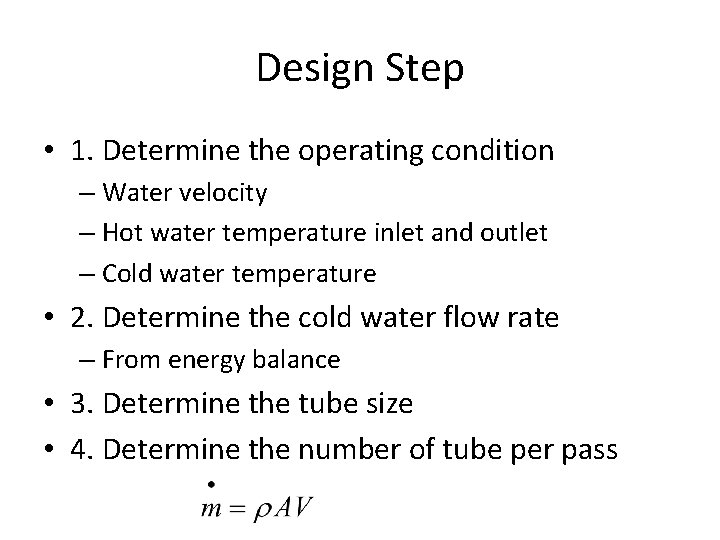
Design Step • 1. Determine the operating condition – Water velocity – Hot water temperature inlet and outlet – Cold water temperature • 2. Determine the cold water flow rate – From energy balance • 3. Determine the tube size • 4. Determine the number of tube per pass
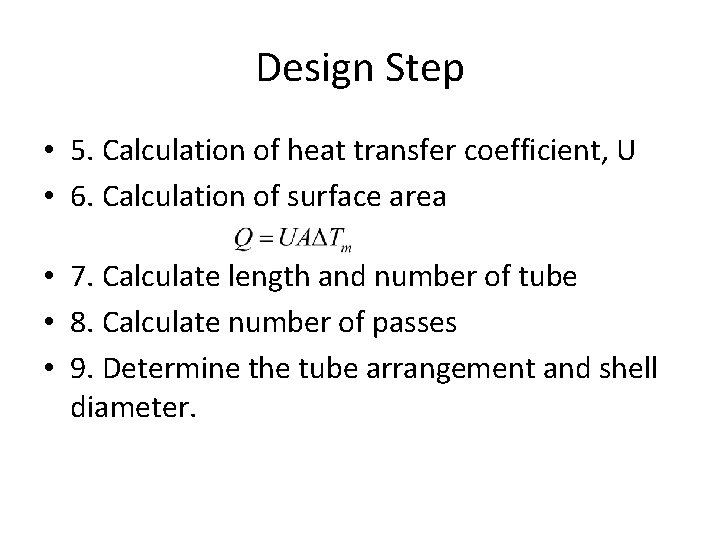
Design Step • 5. Calculation of heat transfer coefficient, U • 6. Calculation of surface area • 7. Calculate length and number of tube • 8. Calculate number of passes • 9. Determine the tube arrangement and shell diameter.
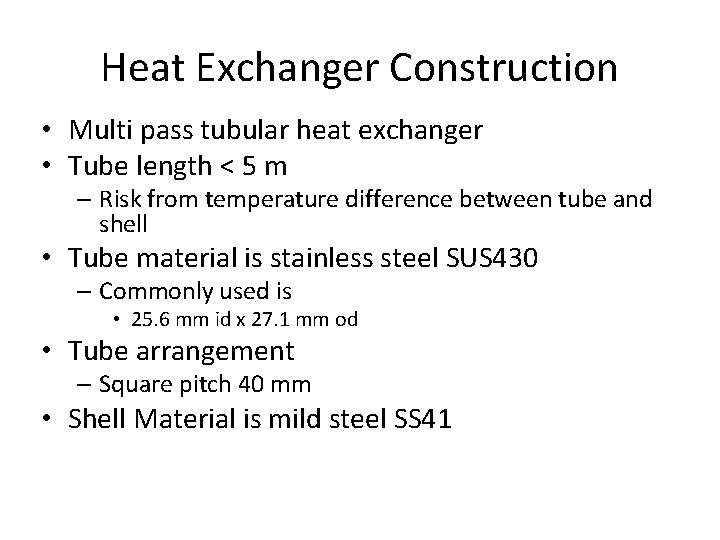
Heat Exchanger Construction • Multi pass tubular heat exchanger • Tube length < 5 m – Risk from temperature difference between tube and shell • Tube material is stainless steel SUS 430 – Commonly used is • 25. 6 mm id x 27. 1 mm od • Tube arrangement – Square pitch 40 mm • Shell Material is mild steel SS 41

Given • • • Fouling Resistance = 1. 5 x 10 -4 m 2 K/W Engine cooling water inlet = 55 o. C Engine cooling water outlet = 70 o. C Cooling water from cooling tower = 35 o. C Cooling water temp diff = 5 o. C Heat transfer coefficient of outside of tube, ho = 700 W/m 2/K
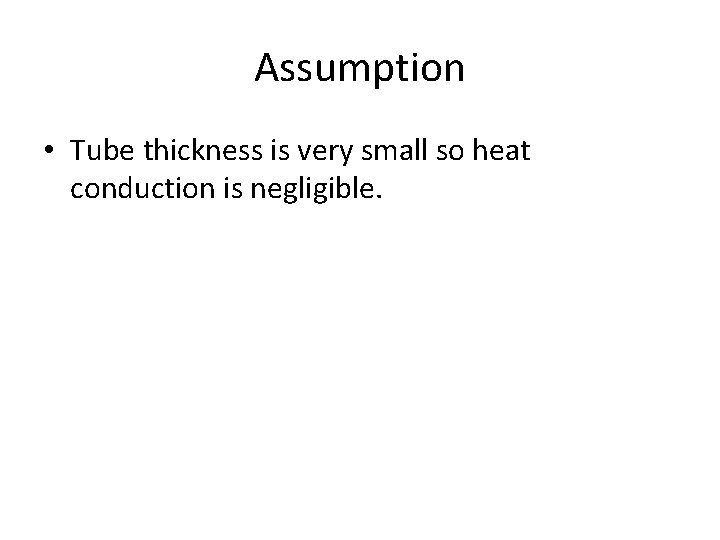
Assumption • Tube thickness is very small so heat conduction is negligible.
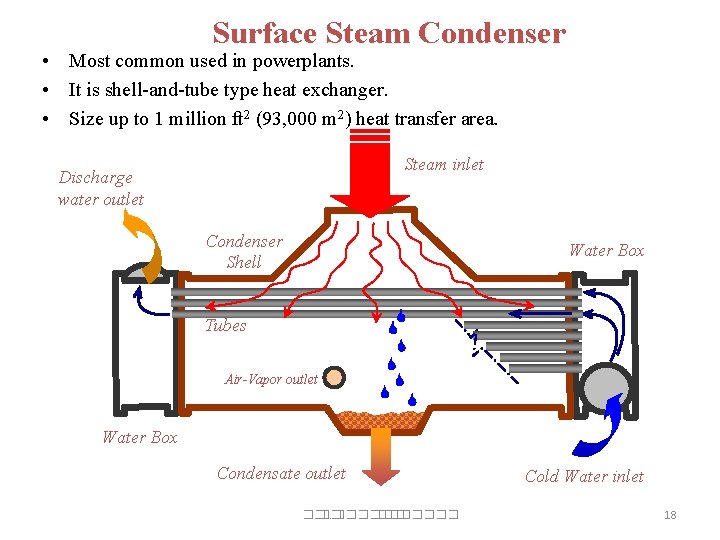
Surface Steam Condenser • Most common used in powerplants. • It is shell-and-tube type heat exchanger. • Size up to 1 million ft 2 (93, 000 m 2) heat transfer area. Steam inlet Discharge water outlet Condenser Shell Water Box Tubes Air-Vapor outlet Water Box Condensate outlet ��. ������� Cold Water inlet 18
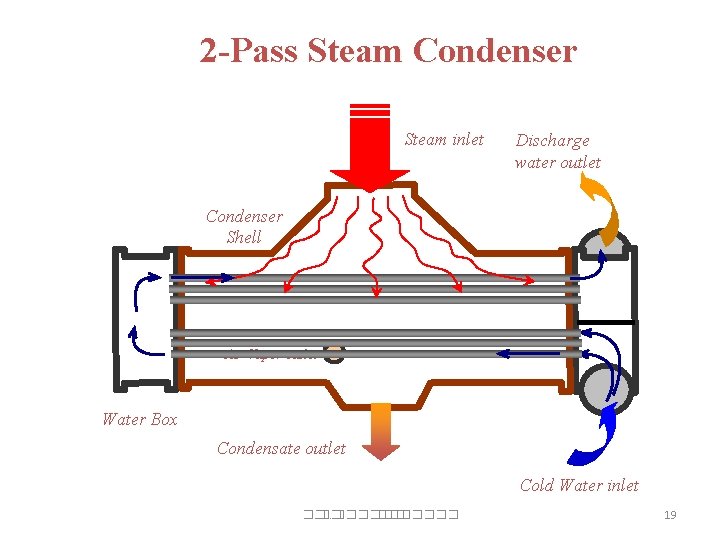
2 -Pass Steam Condenser Steam inlet Discharge water outlet Condenser Shell Air-Vapor outlet Water Box Condensate outlet Cold Water inlet ��. ������� 19
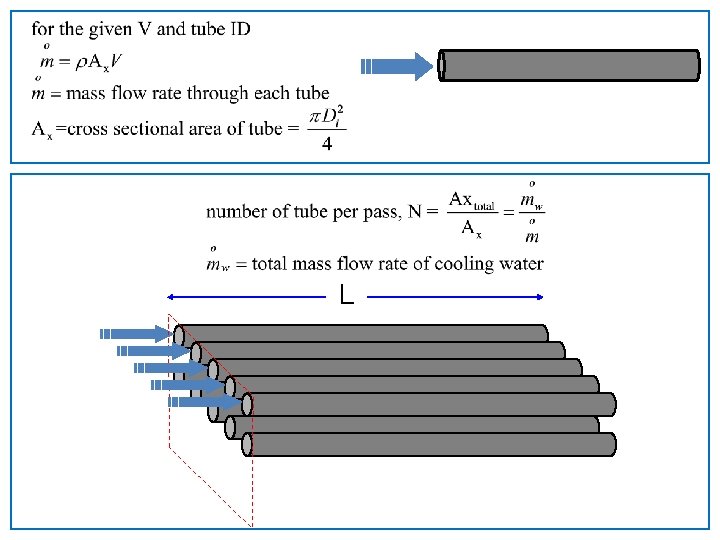
L
- Slides: 20