Design of Experiments a Paradigm Popper Your job
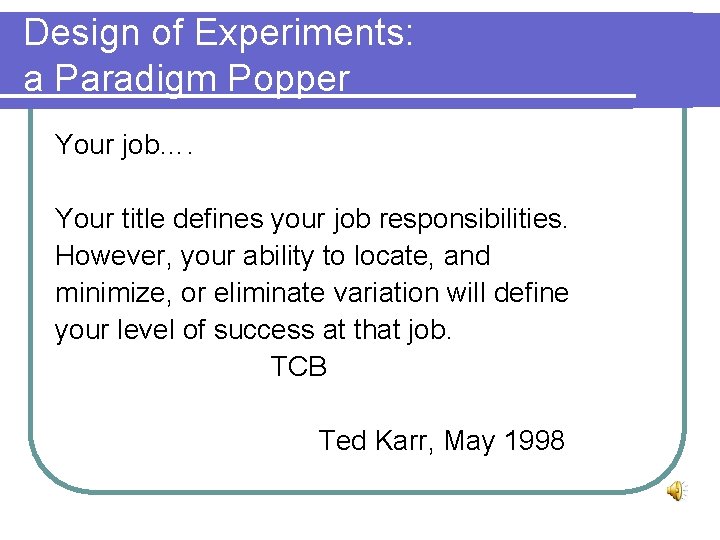
Design of Experiments: a Paradigm Popper Your job…. Your title defines your job responsibilities. However, your ability to locate, and minimize, or eliminate variation will define your level of success at that job. TCB Ted Karr, May 1998
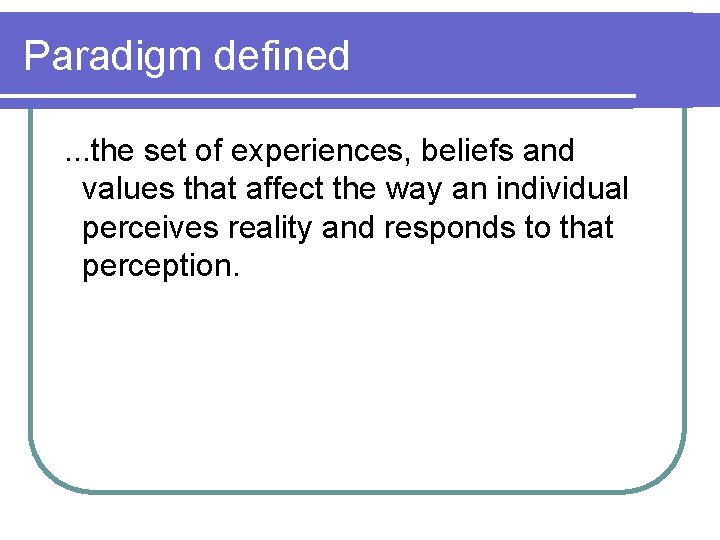
Paradigm defined . . . the set of experiences, beliefs and values that affect the way an individual perceives reality and responds to that perception.
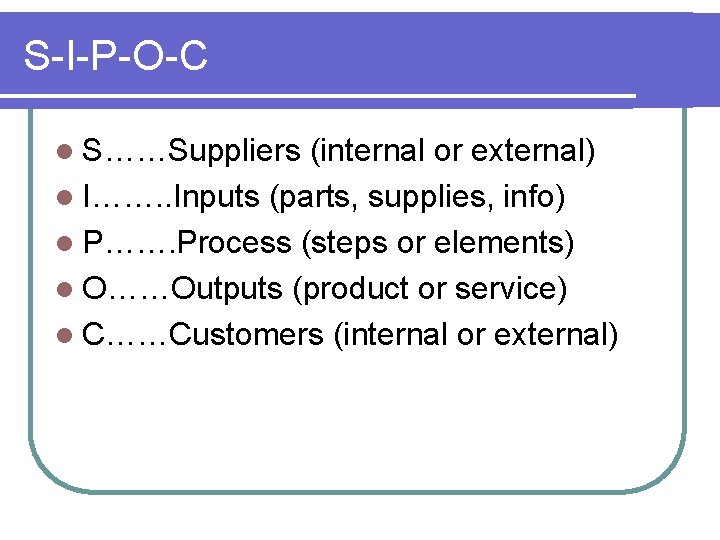
S-I-P-O-C l S……Suppliers (internal or external) l I……. . Inputs (parts, supplies, info) l P……. Process (steps or elements) l O……Outputs (product or service) l C……Customers (internal or external)
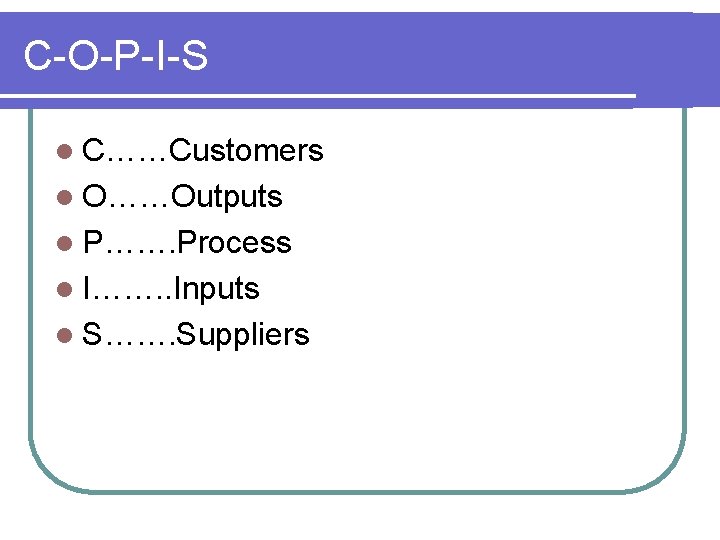
C-O-P-I-S l C……Customers l O……Outputs l P……. Process l I……. . Inputs l S……. Suppliers
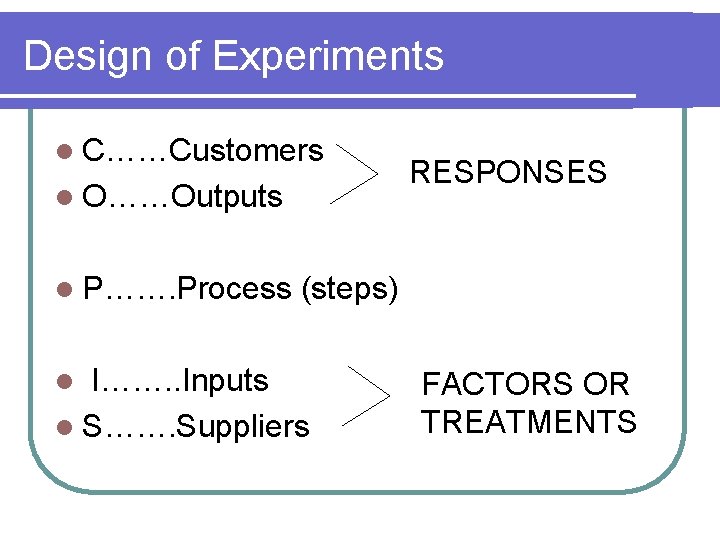
Design of Experiments l C……Customers l O……Outputs RESPONSES l P……. Process (steps) l I……. . Inputs l S……. Suppliers FACTORS OR TREATMENTS
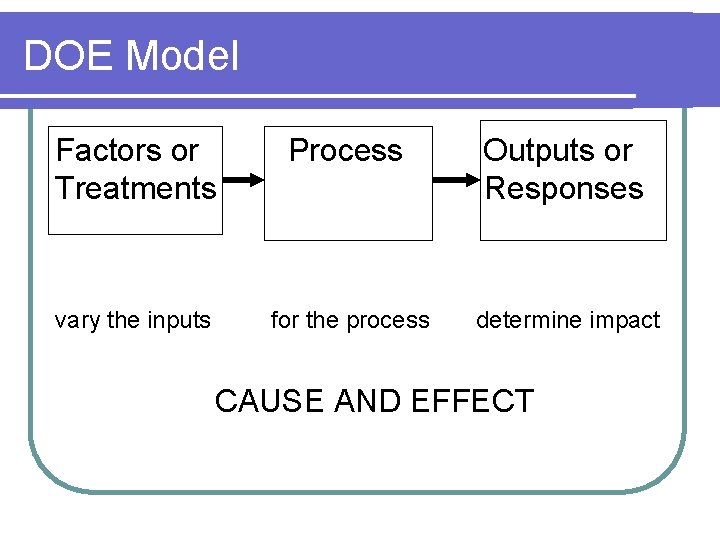
DOE Model Factors or Process Outputs or Treatments Responses vary the inputs for the process determine impact CAUSE AND EFFECT
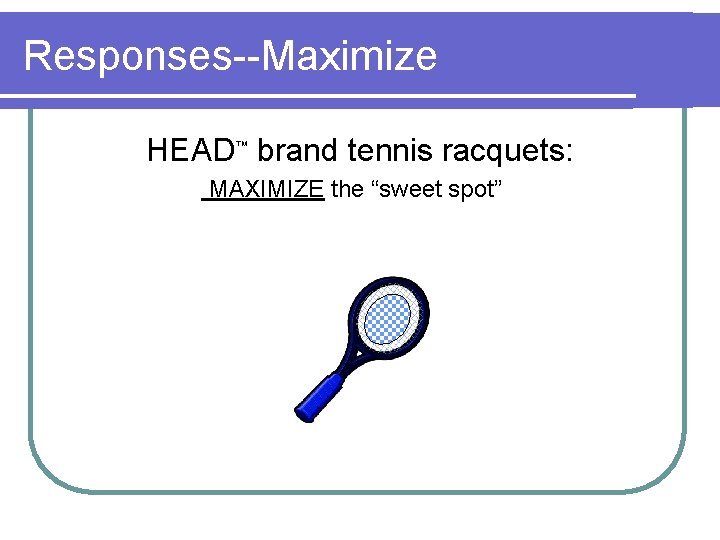
Responses--Maximize HEAD™ brand tennis racquets: MAXIMIZE the “sweet spot”
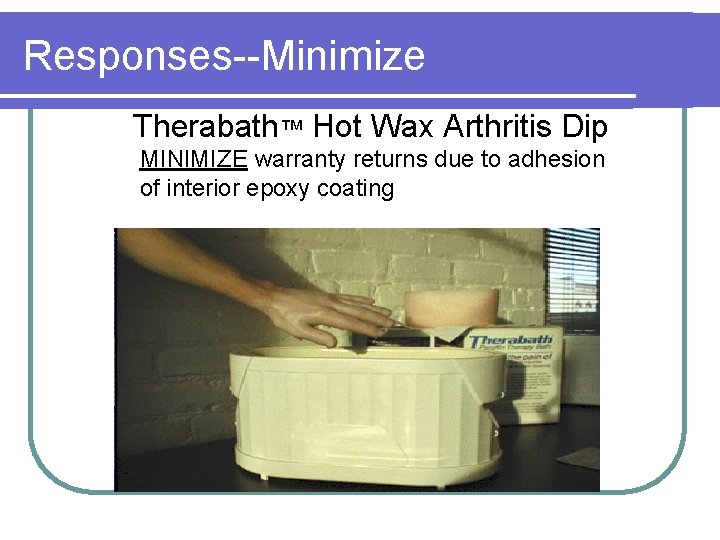
Responses--Minimize Therabath™ Hot Wax Arthritis Dip MINIMIZE warranty returns due to adhesion of interior epoxy coating
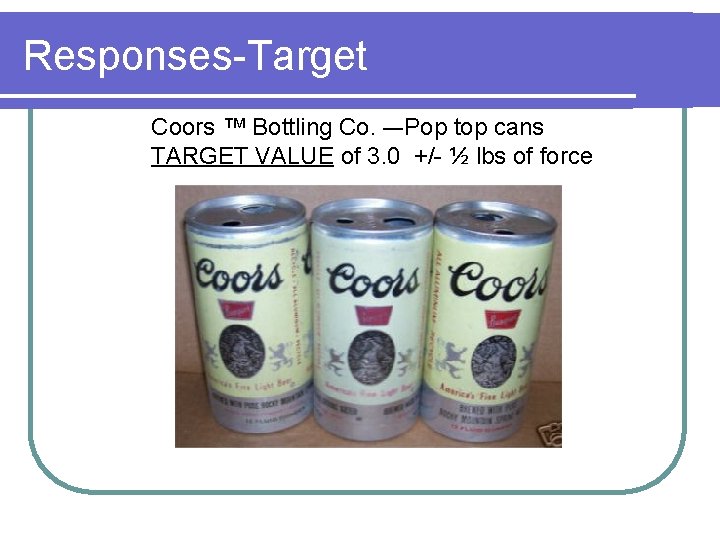
Responses-Target Coors ™ Bottling Co. –-Pop top cans TARGET VALUE of 3. 0 +/- ½ lbs of force
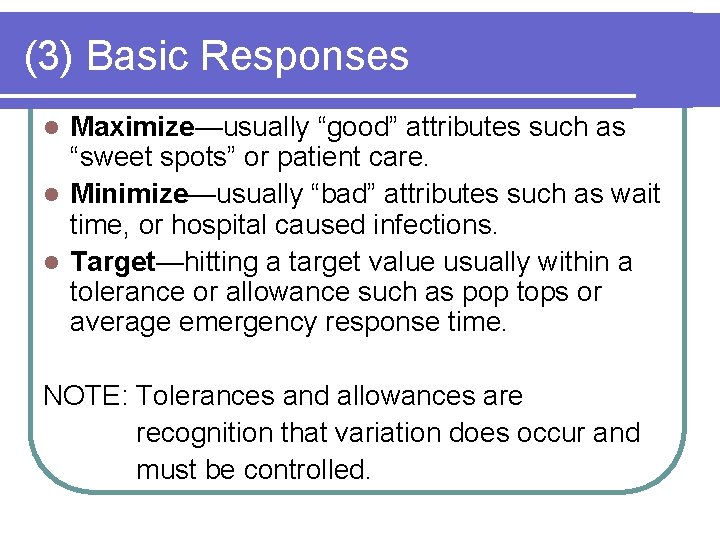
(3) Basic Responses Maximize—usually “good” attributes such as “sweet spots” or patient care. l Minimize—usually “bad” attributes such as wait time, or hospital caused infections. l Target—hitting a target value usually within a tolerance or allowance such as pop tops or average emergency response time. l NOTE: Tolerances and allowances are recognition that variation does occur and must be controlled.
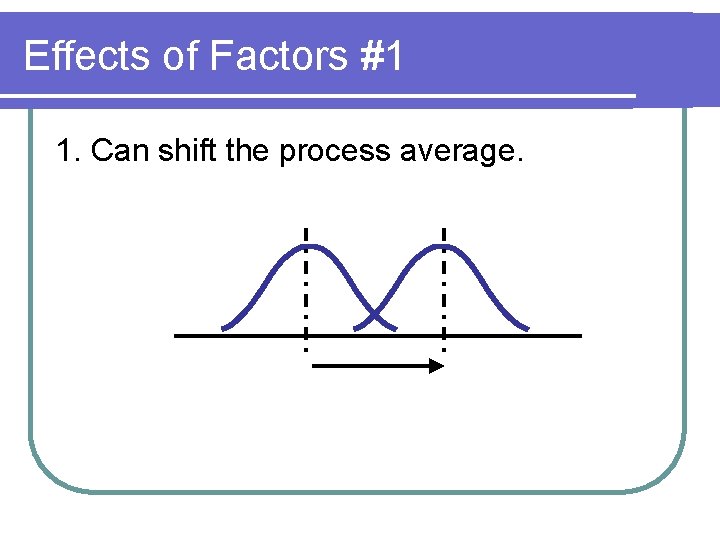
Effects of Factors #1 1. Can shift the process average.
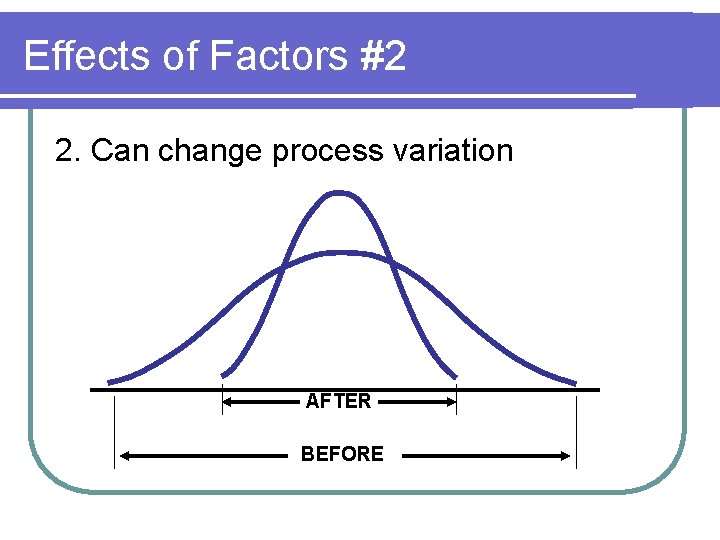
Effects of Factors #2 2. Can change process variation AFTER BEFORE
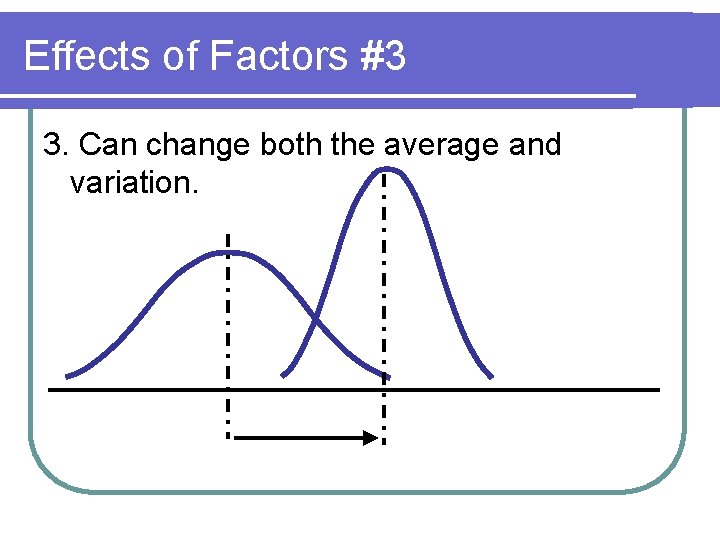
Effects of Factors #3 3. Can change both the average and variation.
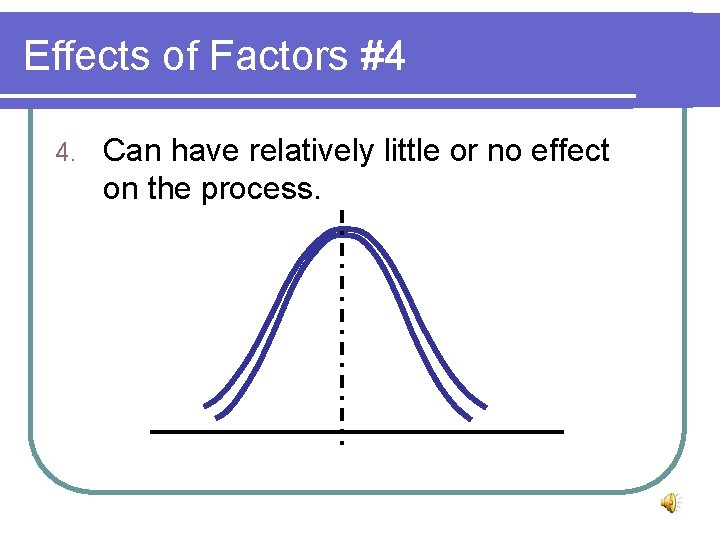
Effects of Factors #4 4. Can have relatively little or no effect on the process.
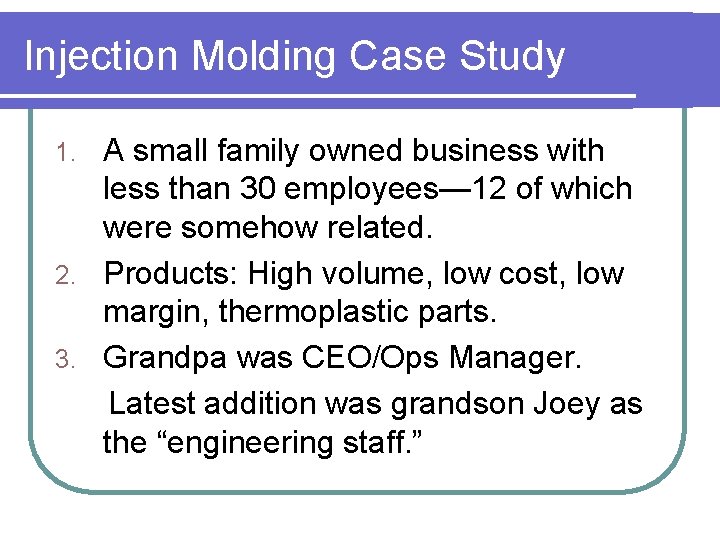
Injection Molding Case Study A small family owned business with less than 30 employees— 12 of which were somehow related. 2. Products: High volume, low cost, low margin, thermoplastic parts. 3. Grandpa was CEO/Ops Manager. Latest addition was grandson Joey as the “engineering staff. ” 1.
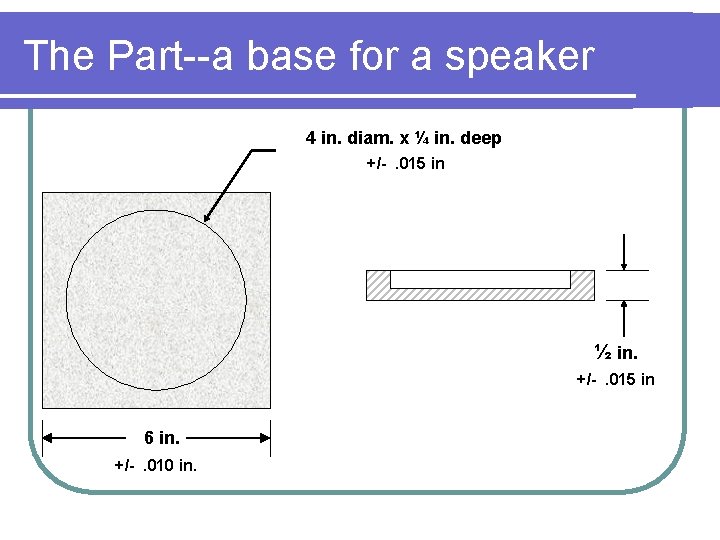
The Part--a base for a speaker 4 in. diam. x ¼ in. deep +/- . 015 in ½ in. +/- . 015 in 6 in. +/- . 010 in.
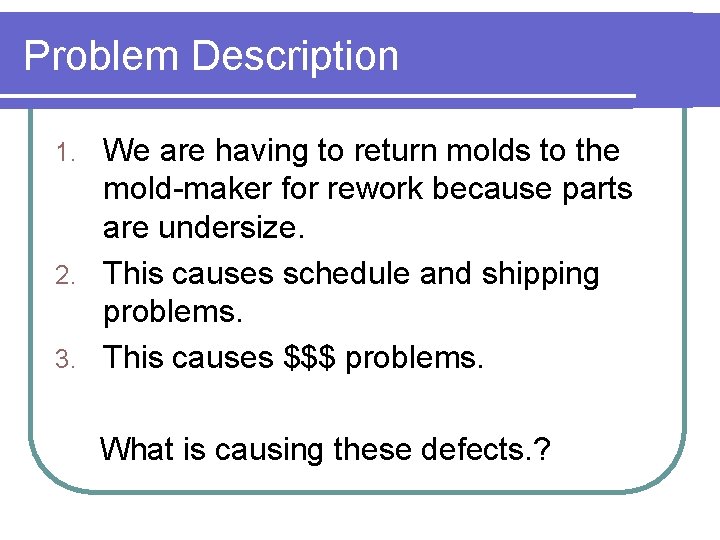
Problem Description We are having to return molds to the mold-maker for rework because parts are undersize. 2. This causes schedule and shipping problems. 3. This causes $$$ problems. What is causing these defects. ? 1.
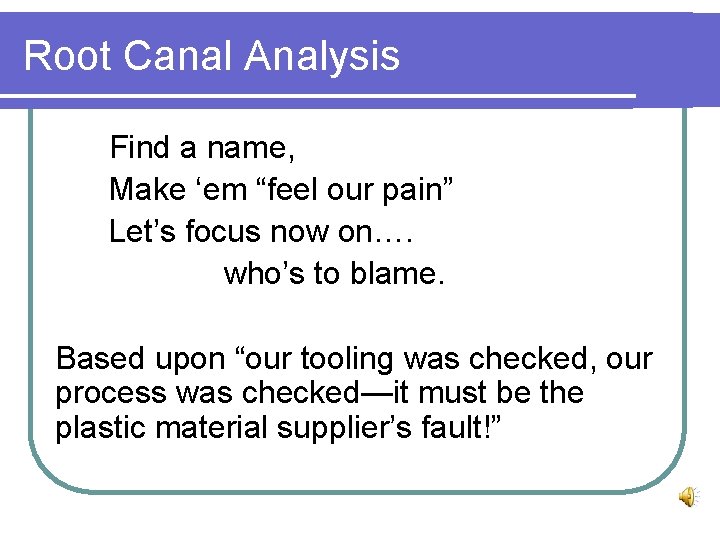
Root Canal Analysis Find a name, Make ‘em “feel our pain” Let’s focus now on…. who’s to blame. Based upon “our tooling was checked, our process was checked—it must be the plastic material supplier’s fault!”
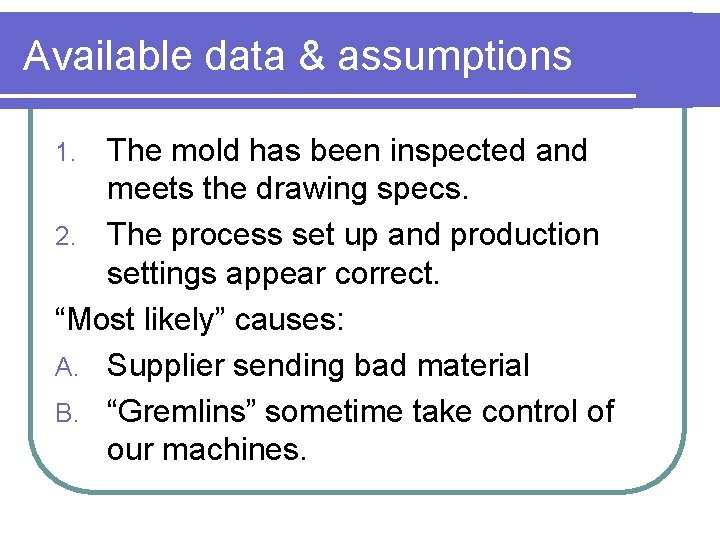
Available data & assumptions The mold has been inspected and meets the drawing specs. 2. The process set up and production settings appear correct. “Most likely” causes: A. Supplier sending bad material B. “Gremlins” sometime take control of our machines. 1.
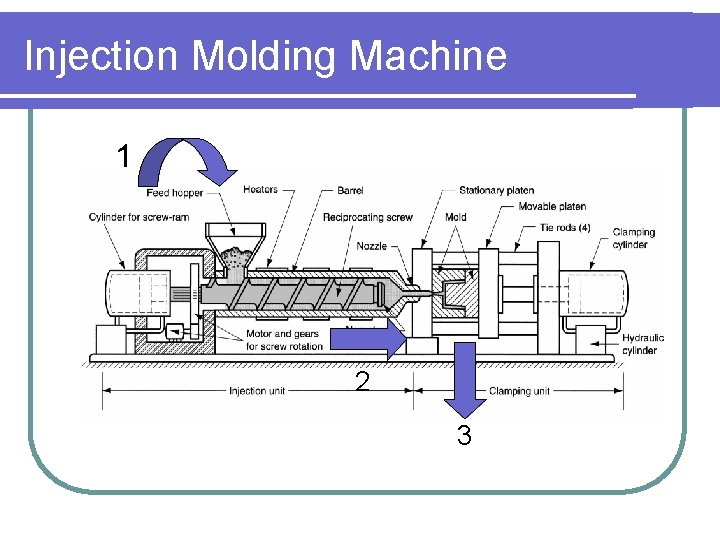
Injection Molding Machine 1 2 3
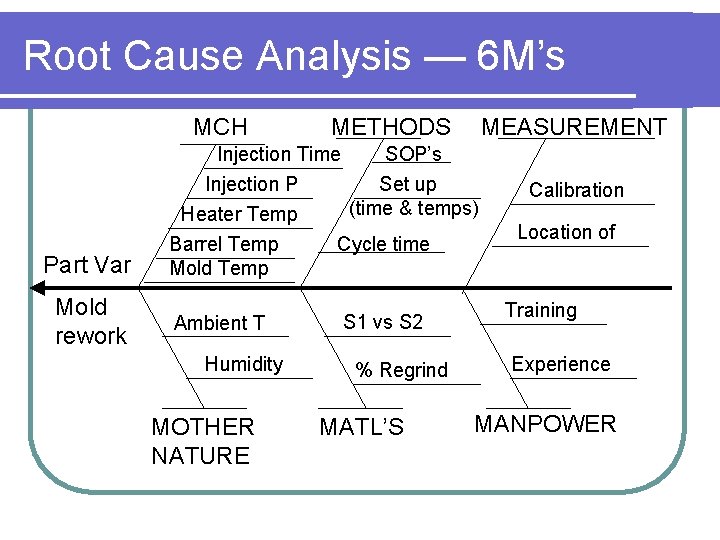
Root Cause Analysis — 6 M’s MCH Part Var Mold rework METHODS MEASUREMENT Injection Time SOP’s Injection P Set up (time & temps) Heater Temp Barrel Temp Cycle time Mold Temp Ambient T Humidity MOTHER NATURE S 1 vs S 2 % Regrind MATL’S Calibration Location of Training Experience MANPOWER
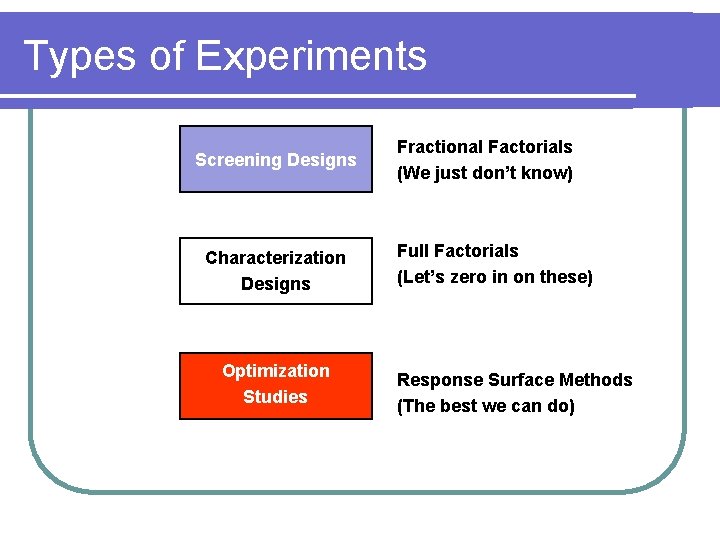
Types of Experiments Screening Designs Characterization Designs Optimization Studies Fractional Factorials (We just don’t know) Full Factorials (Let’s zero in on these) Response Surface Methods (The best we can do)
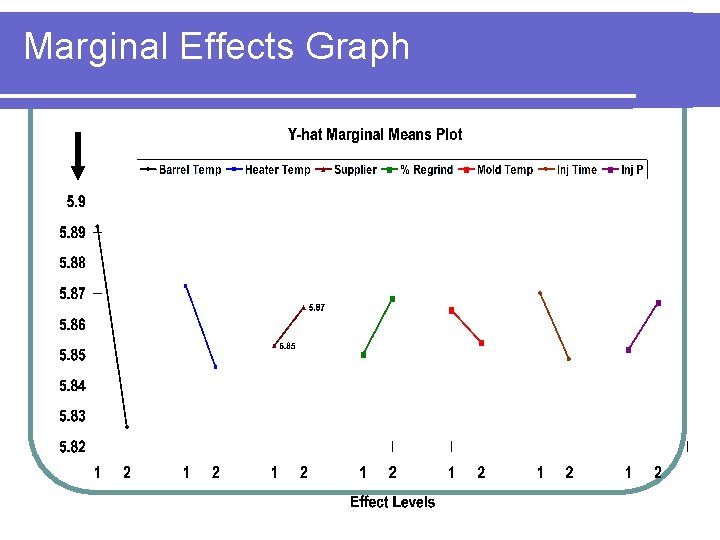
Marginal Effects Graph
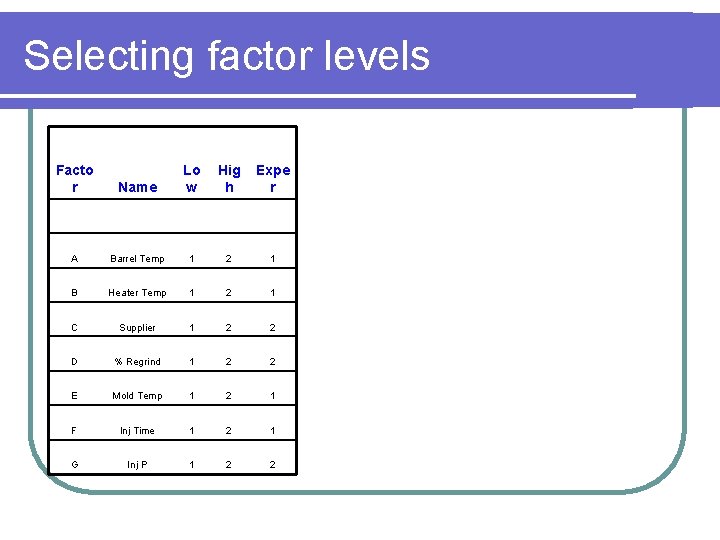
Selecting factor levels Facto r Name Lo w Hig h Expe r A Barrel Temp 1 2 1 B Heater Temp 1 2 1 C Supplier 1 2 2 D % Regrind 1 2 2 E Mold Temp 1 2 1 F Inj Time 1 2 1 G Inj P 1 2 2
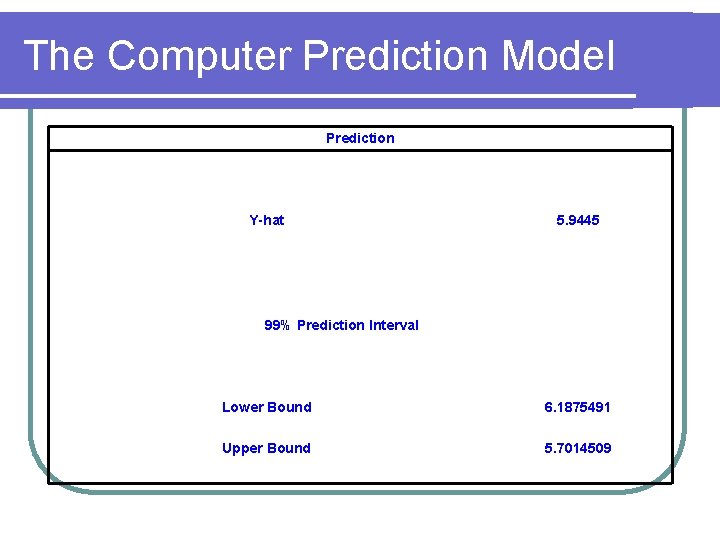
The Computer Prediction Model Prediction Y-hat 5. 9445 99% Prediction Interval Lower Bound 6. 1875491 Upper Bound 5. 7014509
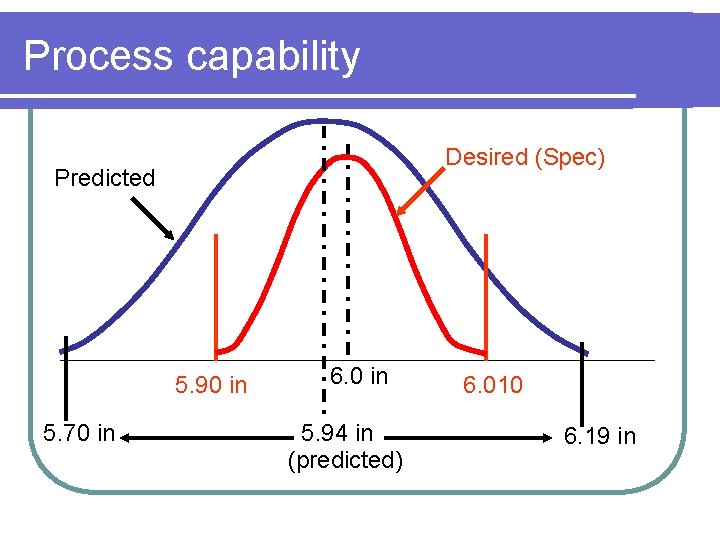
Process capability Desired (Spec) Predicted 5. 90 in 5. 70 in 6. 0 in 5. 94 in (predicted) 6. 010 6. 19 in
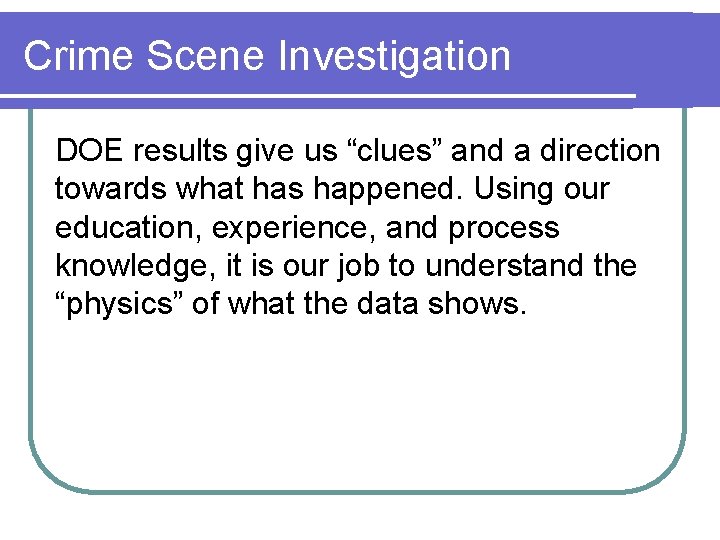
Crime Scene Investigation DOE results give us “clues” and a direction towards what has happened. Using our education, experience, and process knowledge, it is our job to understand the “physics” of what the data shows.
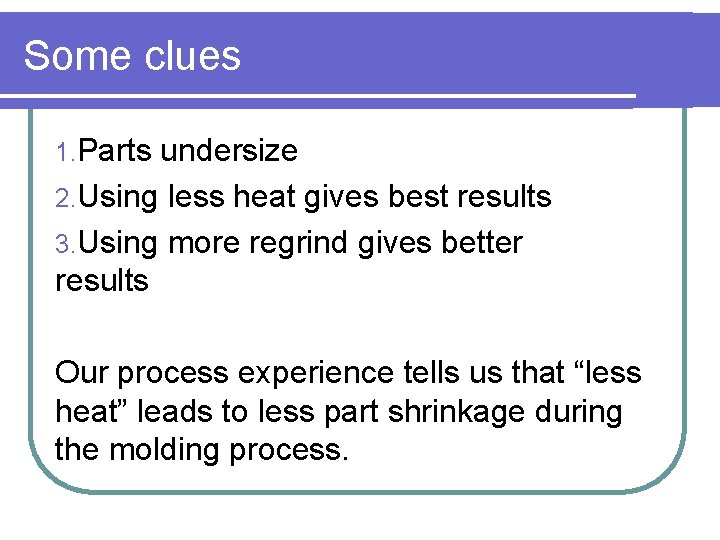
Some clues 1. Parts undersize 2. Using less heat gives best results 3. Using more regrind gives better results Our process experience tells us that “less heat” leads to less part shrinkage during the molding process.
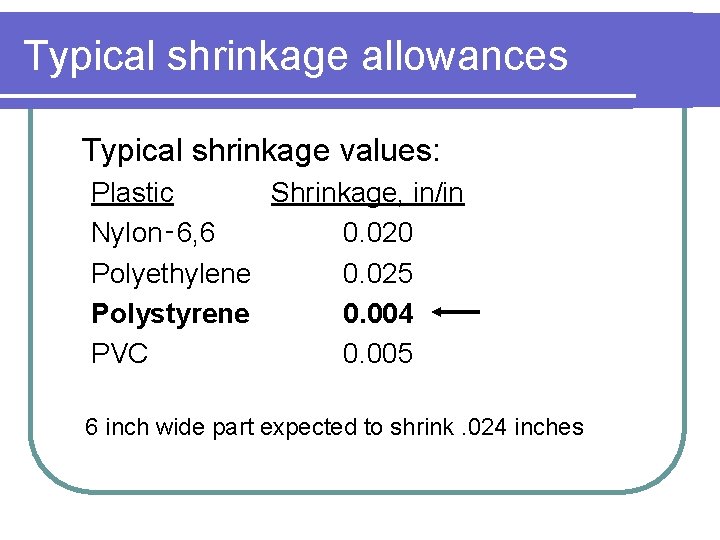
Typical shrinkage allowances Typical shrinkage values: Plastic Shrinkage, in/in Nylon‑ 6, 6 0. 020 Polyethylene 0. 025 Polystyrene 0. 004 PVC 0. 005 6 inch wide part expected to shrink. 024 inches
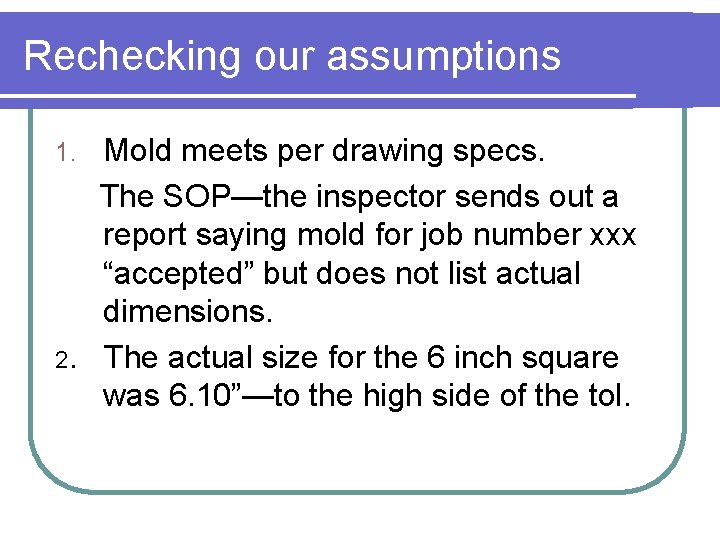
Rechecking our assumptions Mold meets per drawing specs. The SOP—the inspector sends out a report saying mold for job number xxx “accepted” but does not list actual dimensions. 2. The actual size for the 6 inch square was 6. 10”—to the high side of the tol. 1.
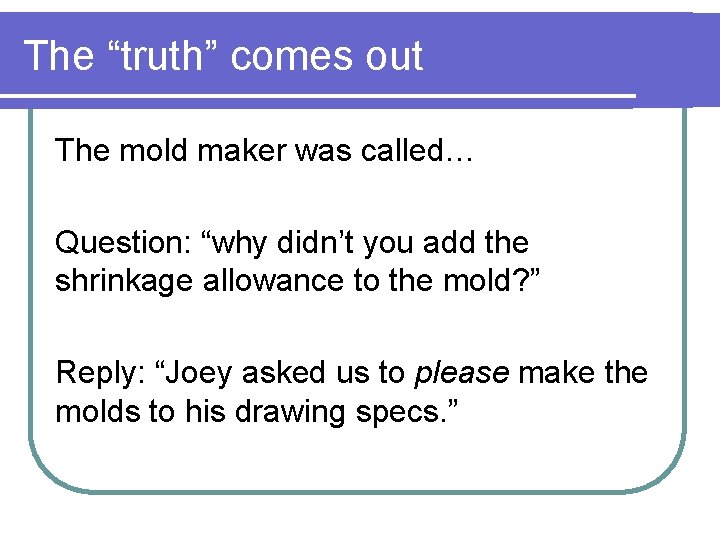
The “truth” comes out The mold maker was called… Question: “why didn’t you add the shrinkage allowance to the mold? ” Reply: “Joey asked us to please make the molds to his drawing specs. ”
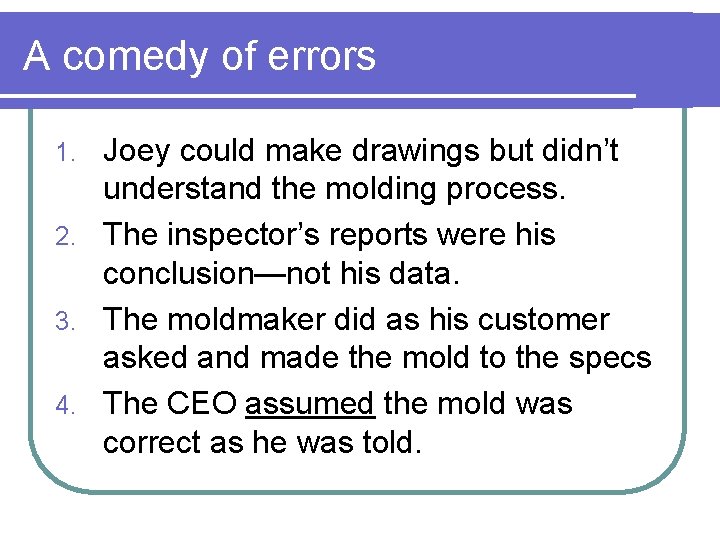
A comedy of errors Joey could make drawings but didn’t understand the molding process. 2. The inspector’s reports were his conclusion—not his data. 3. The moldmaker did as his customer asked and made the mold to the specs 4. The CEO assumed the mold was correct as he was told. 1.
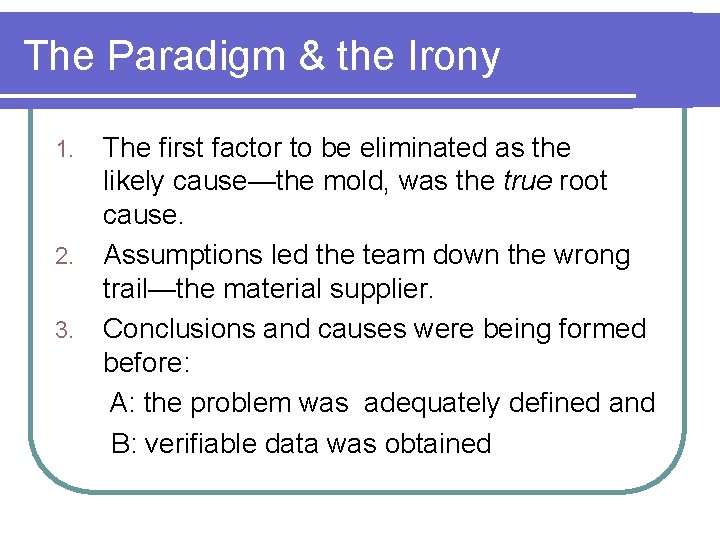
The Paradigm & the Irony The first factor to be eliminated as the likely cause—the mold, was the true root cause. 2. Assumptions led the team down the wrong trail—the material supplier. 3. Conclusions and causes were being formed before: A: the problem was adequately defined and B: verifiable data was obtained 1.
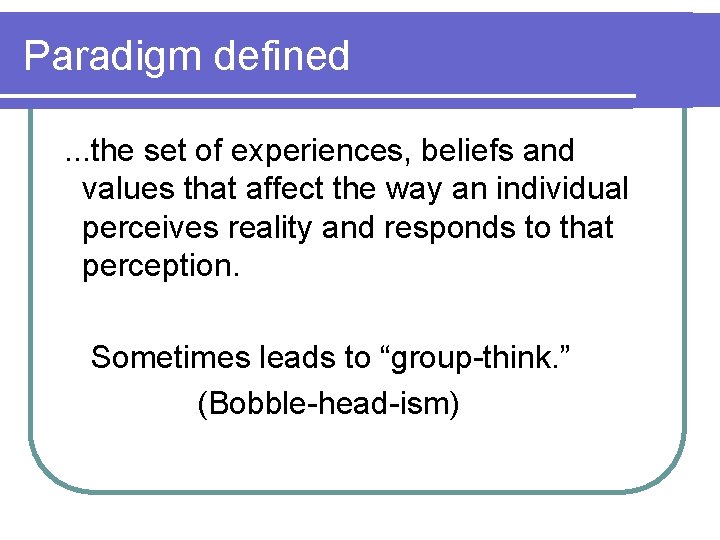
Paradigm defined . . . the set of experiences, beliefs and values that affect the way an individual perceives reality and responds to that perception. Sometimes leads to “group-think. ” (Bobble-head-ism)
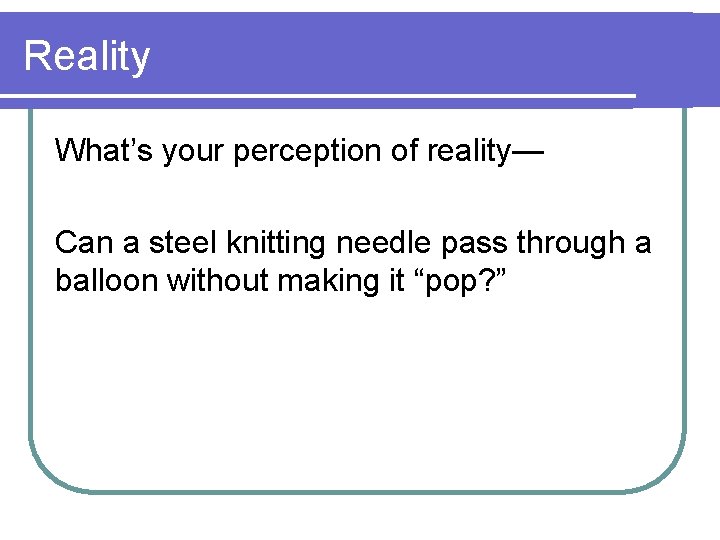
Reality What’s your perception of reality— Can a steel knitting needle pass through a balloon without making it “pop? ”
- Slides: 35