DC Motor Interfacing and PWM 1 DC Motor
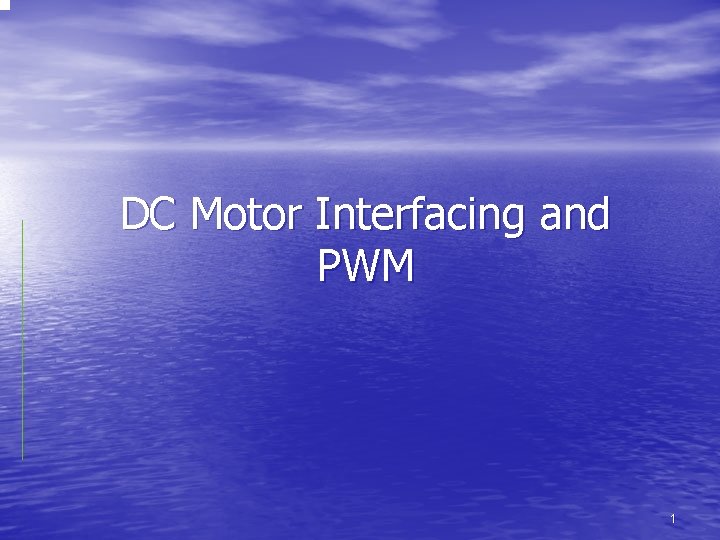
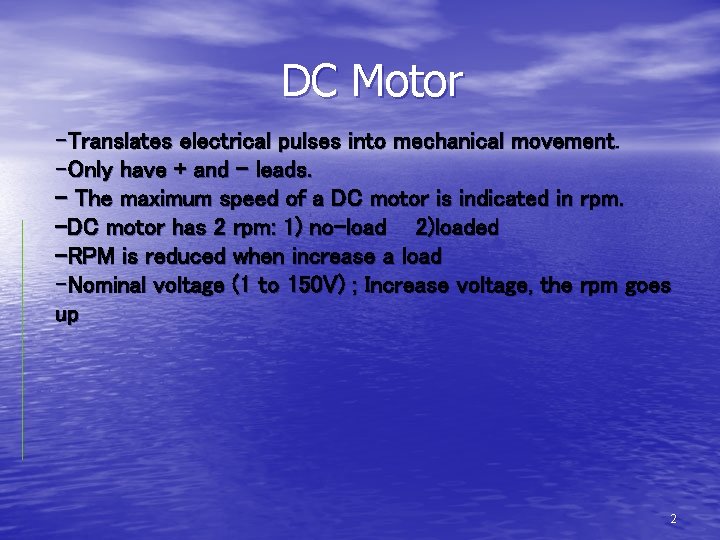
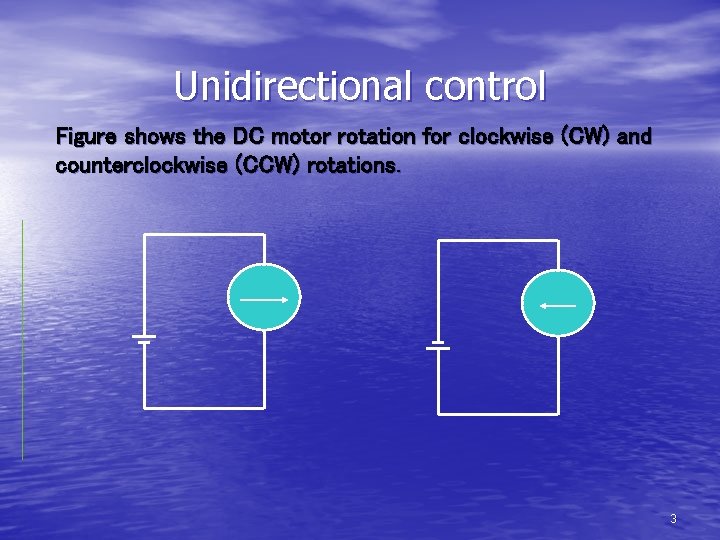
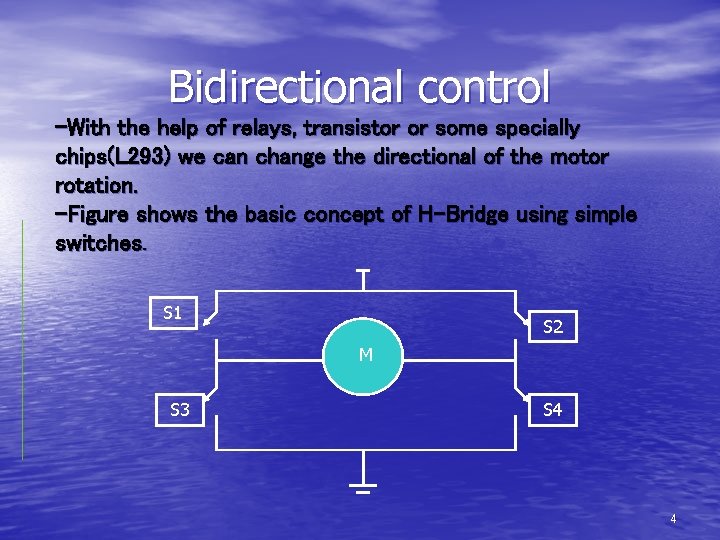
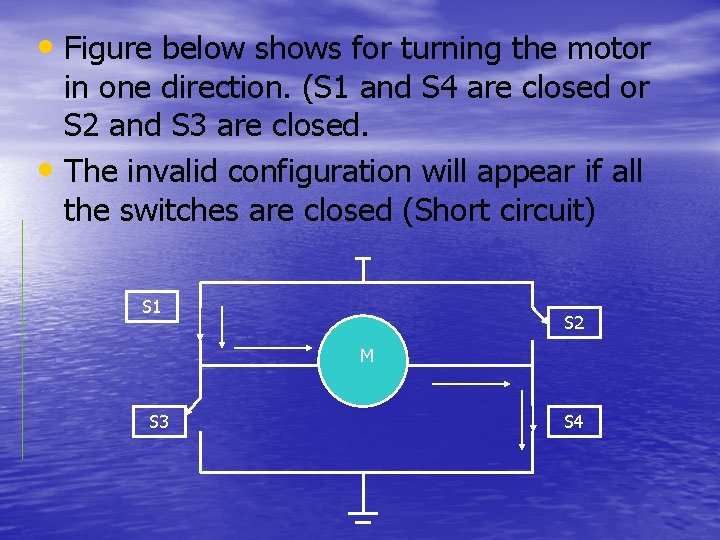
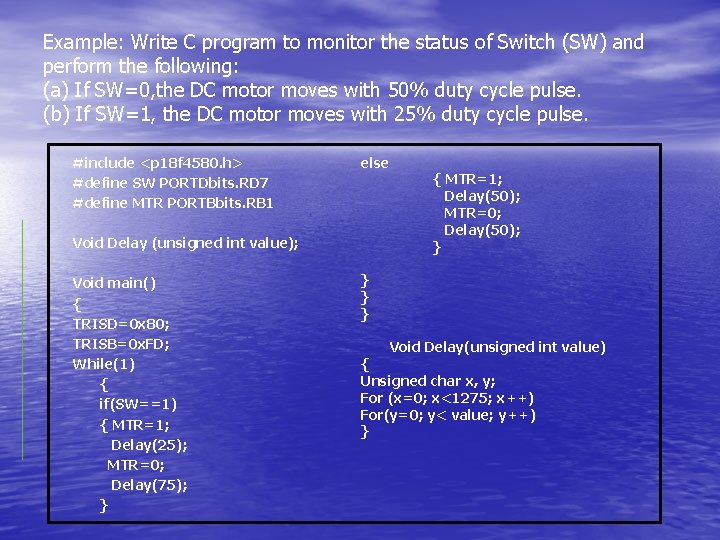
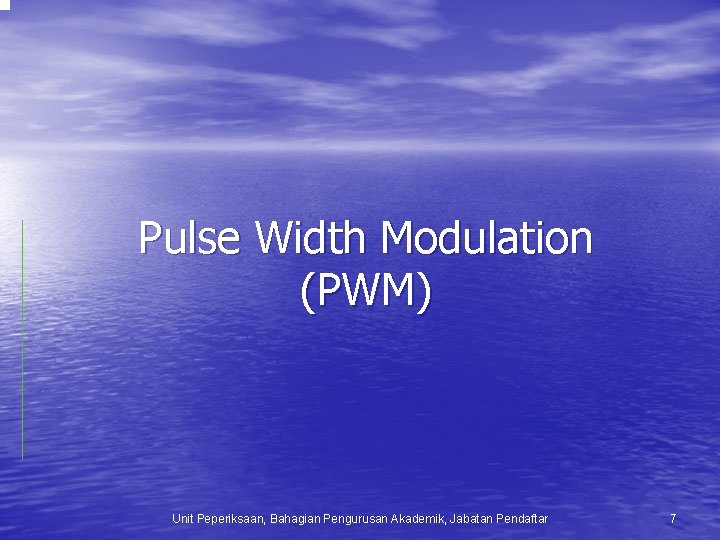
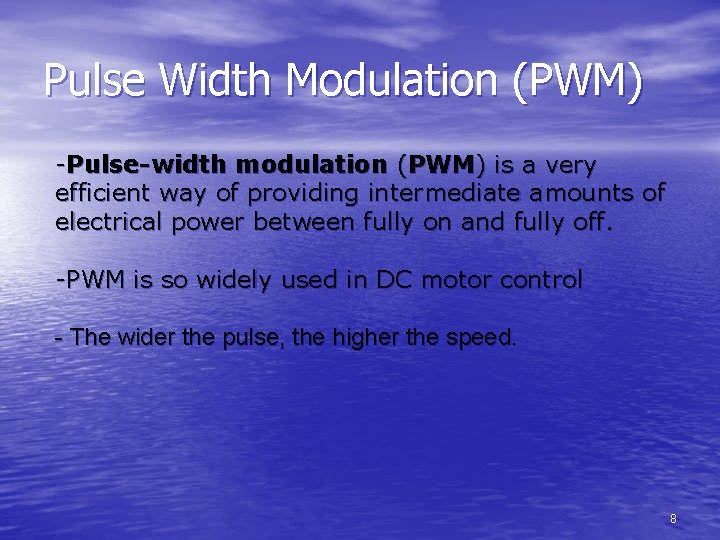
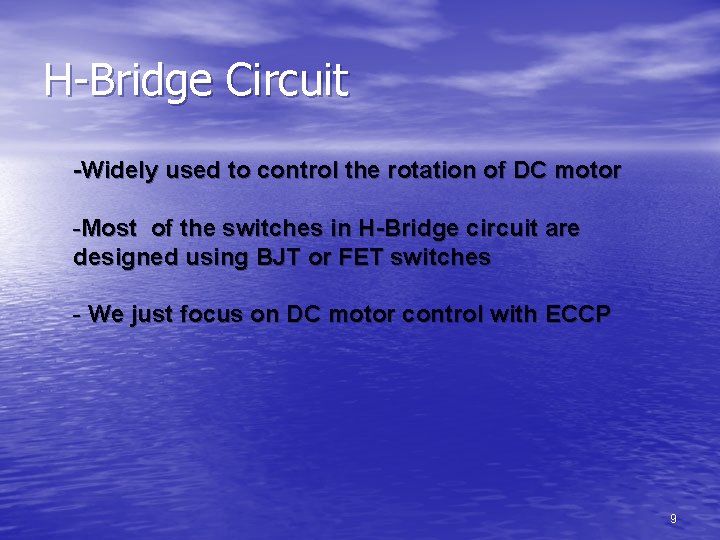
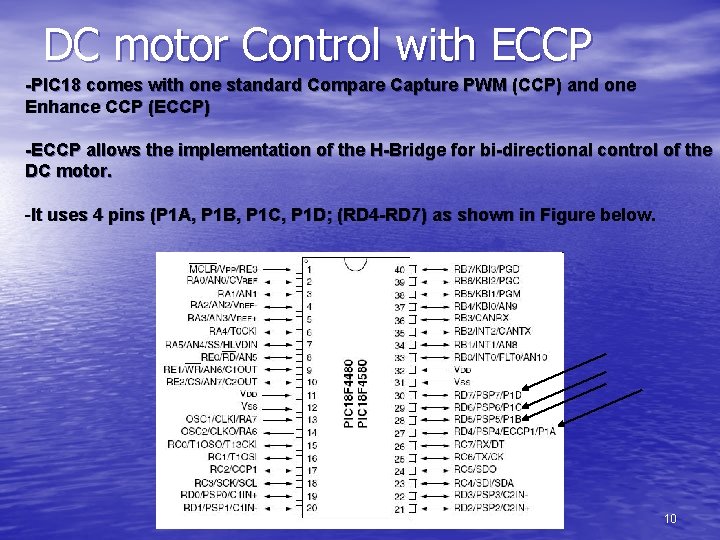
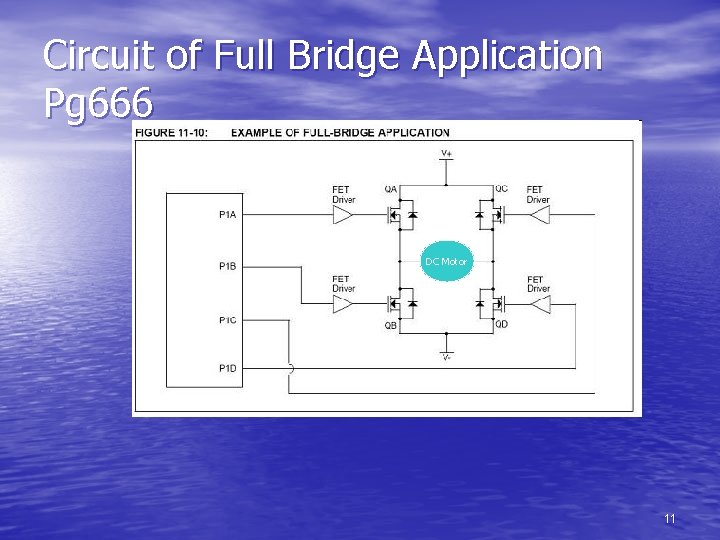
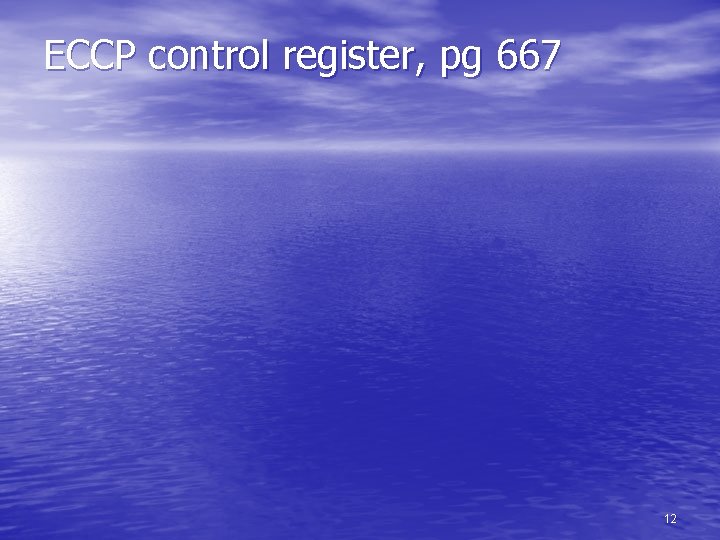
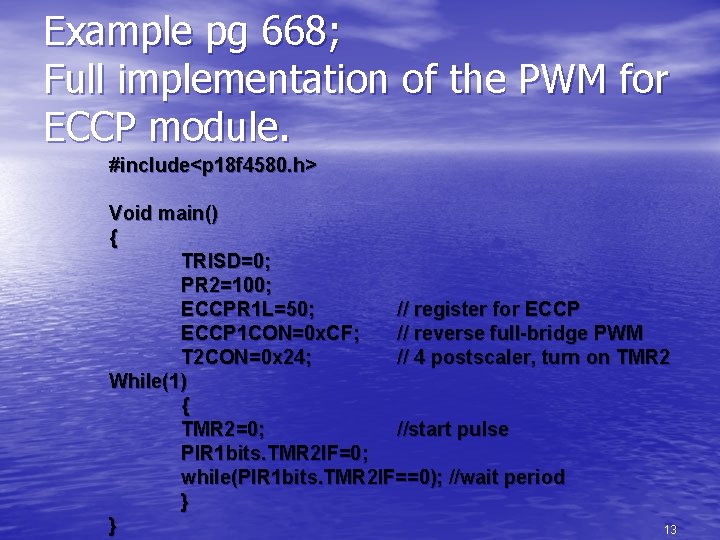
- Slides: 13
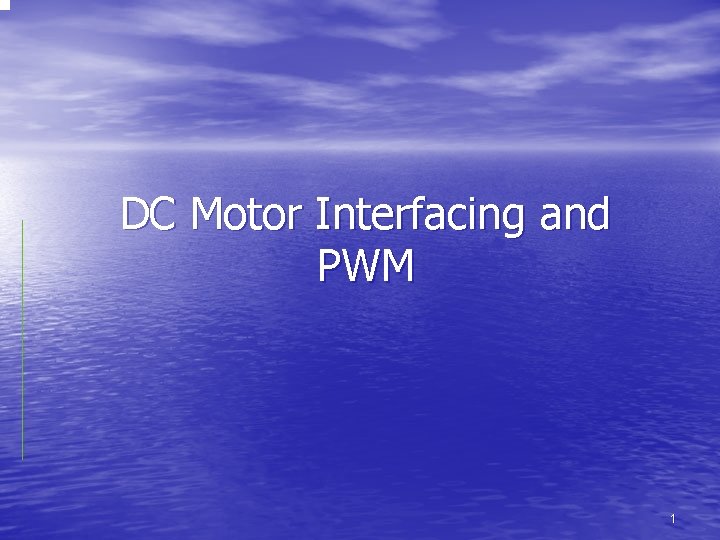
DC Motor Interfacing and PWM 1
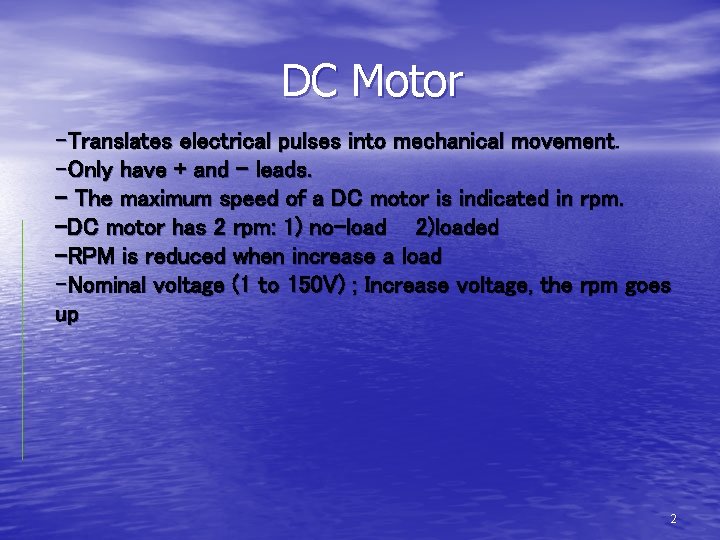
DC Motor -Translates electrical pulses into mechanical movement. -Only have + and – leads. - The maximum speed of a DC motor is indicated in rpm. -DC motor has 2 rpm: 1) no-load 2)loaded -RPM is reduced when increase a load -Nominal voltage (1 to 150 V) ; Increase voltage, the rpm goes up 2
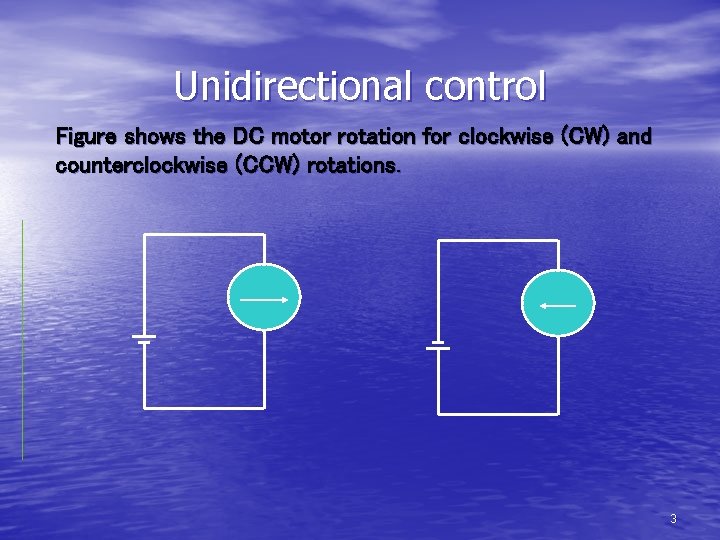
Unidirectional control Figure shows the DC motor rotation for clockwise (CW) and counterclockwise (CCW) rotations. 3
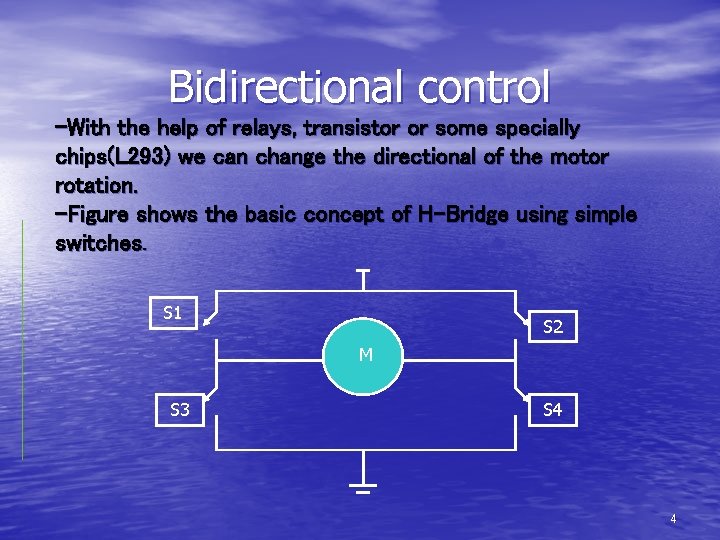
Bidirectional control -With the help of relays, transistor or some specially chips(L 293) we can change the directional of the motor rotation. -Figure shows the basic concept of H-Bridge using simple switches. S 1 S 2 M S 3 S 4 4
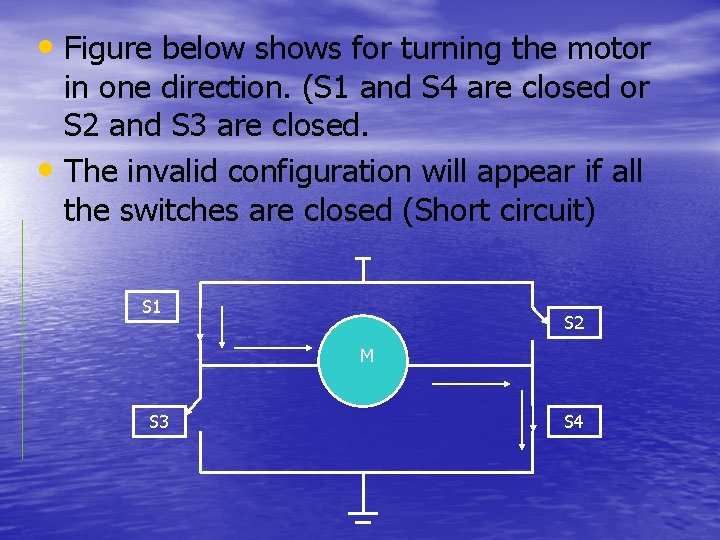
• Figure below shows for turning the motor in one direction. (S 1 and S 4 are closed or S 2 and S 3 are closed. • The invalid configuration will appear if all the switches are closed (Short circuit) S 1 S 2 M S 3 S 4
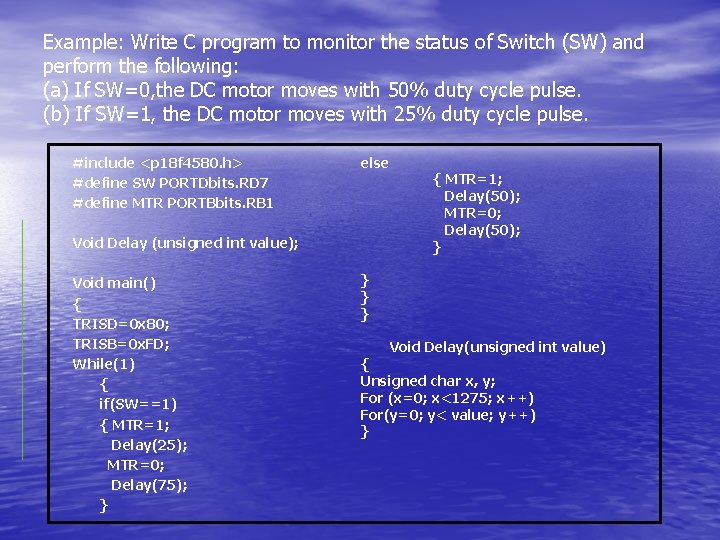
Example: Write C program to monitor the status of Switch (SW) and perform the following: (a) If SW=0, the DC motor moves with 50% duty cycle pulse. (b) If SW=1, the DC motor moves with 25% duty cycle pulse. #include <p 18 f 4580. h> #define SW PORTDbits. RD 7 #define MTR PORTBbits. RB 1 else Void Delay (unsigned int value); Void main() { TRISD=0 x 80; TRISB=0 x. FD; While(1) { if(SW==1) { MTR=1; Delay(25); MTR=0; Delay(75); } { MTR=1; Delay(50); MTR=0; Delay(50); } } Void Delay(unsigned int value) { Unsigned char x, y; For (x=0; x<1275; x++) For(y=0; y< value; y++) }
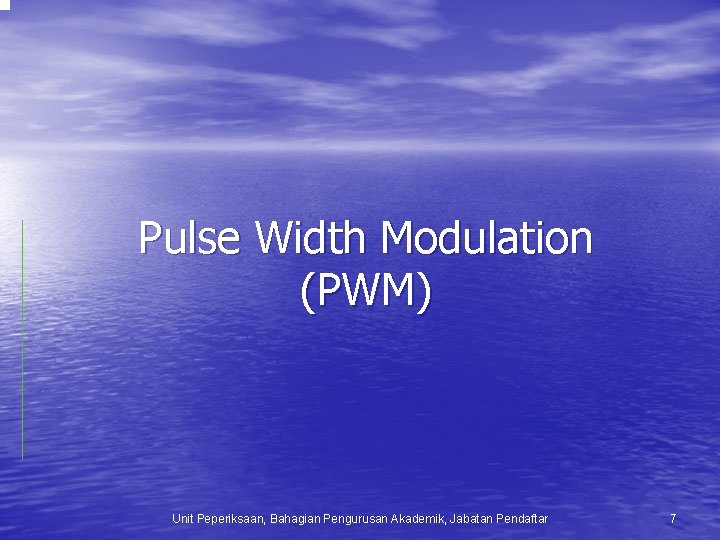
Pulse Width Modulation (PWM) Unit Peperiksaan, Bahagian Pengurusan Akademik, Jabatan Pendaftar 7
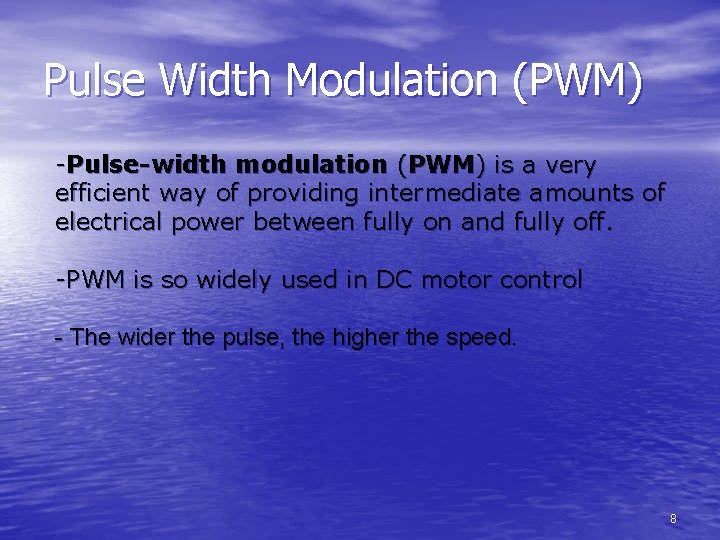
Pulse Width Modulation (PWM) -Pulse-width modulation (PWM) is a very efficient way of providing intermediate amounts of electrical power between fully on and fully off. -PWM is so widely used in DC motor control - The wider the pulse, the higher the speed. 8
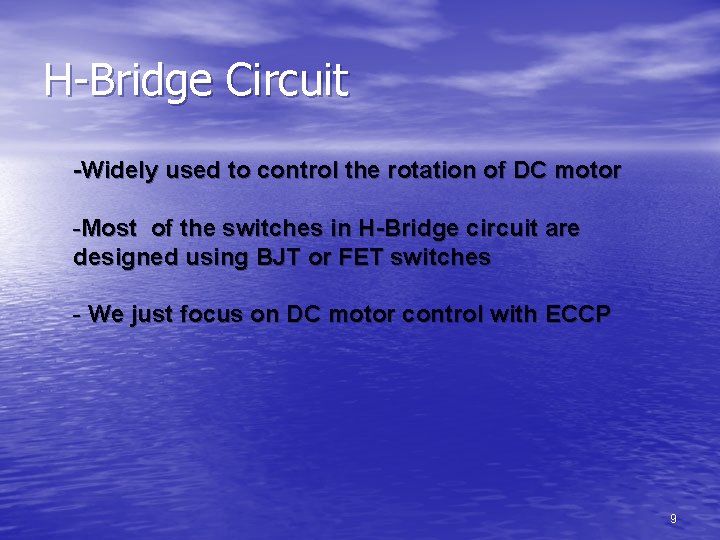
H-Bridge Circuit -Widely used to control the rotation of DC motor -Most of the switches in H-Bridge circuit are designed using BJT or FET switches - We just focus on DC motor control with ECCP 9
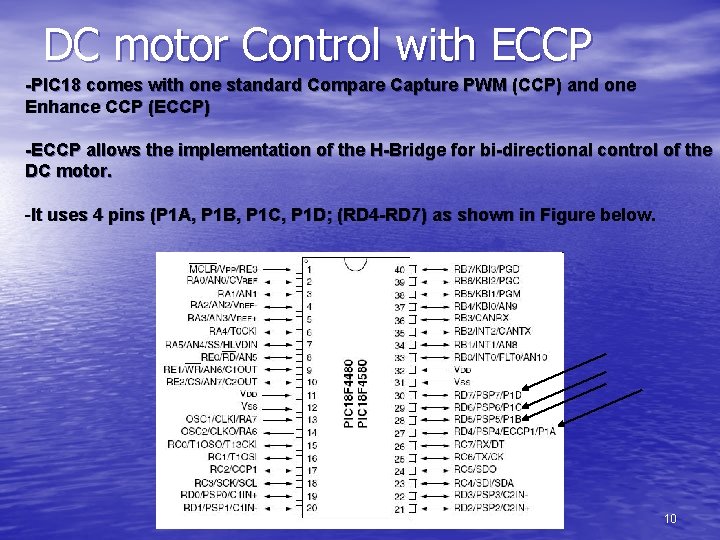
DC motor Control with ECCP -PIC 18 comes with one standard Compare Capture PWM (CCP) and one Enhance CCP (ECCP) -ECCP allows the implementation of the H-Bridge for bi-directional control of the DC motor. -It uses 4 pins (P 1 A, P 1 B, P 1 C, P 1 D; (RD 4 -RD 7) as shown in Figure below. 10
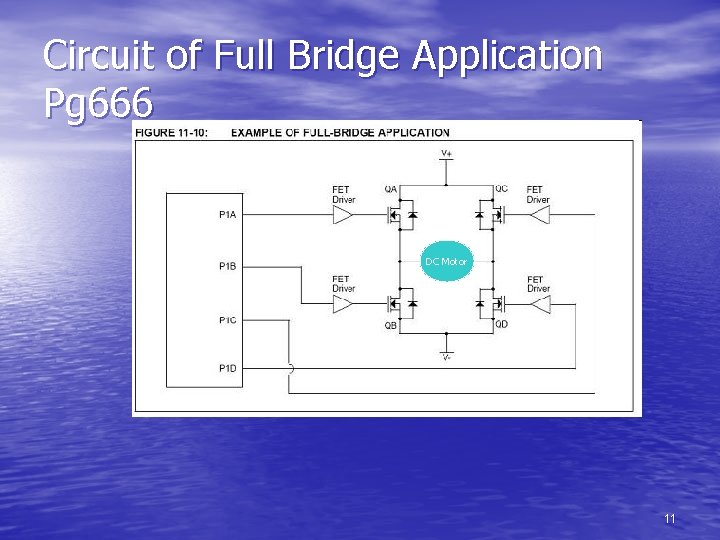
Circuit of Full Bridge Application Pg 666 DC Motor 11
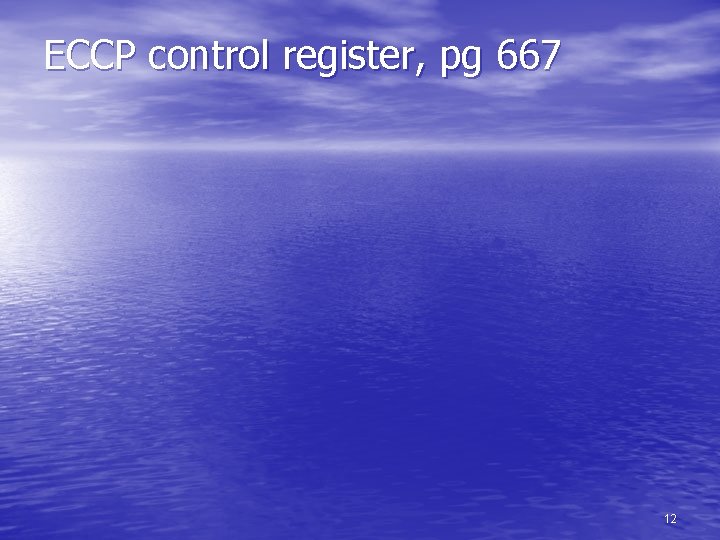
ECCP control register, pg 667 12
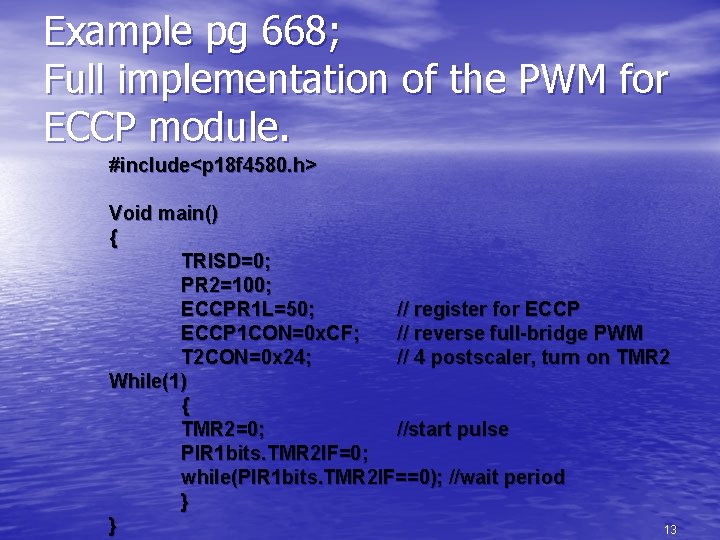
Example pg 668; Full implementation of the PWM for ECCP module. #include<p 18 f 4580. h> Void main() { TRISD=0; PR 2=100; ECCPR 1 L=50; // register for ECCP 1 CON=0 x. CF; // reverse full-bridge PWM T 2 CON=0 x 24; // 4 postscaler, turn on TMR 2 While(1) { TMR 2=0; //start pulse PIR 1 bits. TMR 2 IF=0; while(PIR 1 bits. TMR 2 IF==0); //wait period } } 13