Contact Lens Polymers Drawing by Leonardo Da Vinci
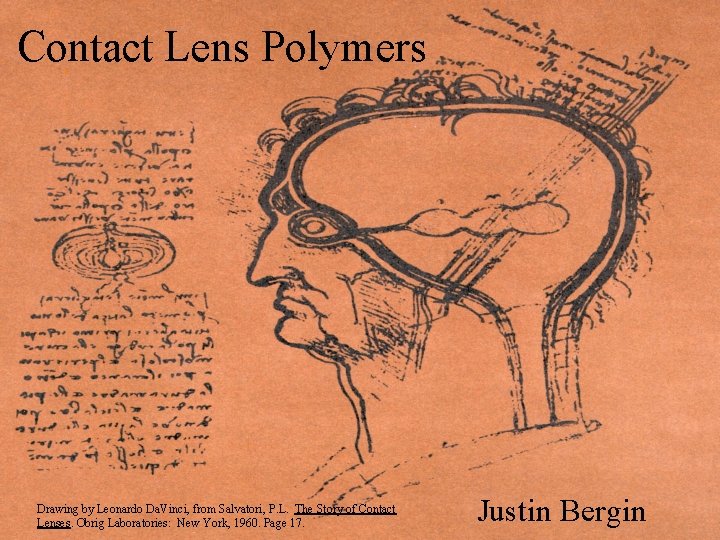
Contact Lens Polymers Drawing by Leonardo Da. Vinci, from Salvatori, P. L. The Story of Contact Lenses. Obrig Laboratories: New York, 1960. Page 17. Justin Bergin
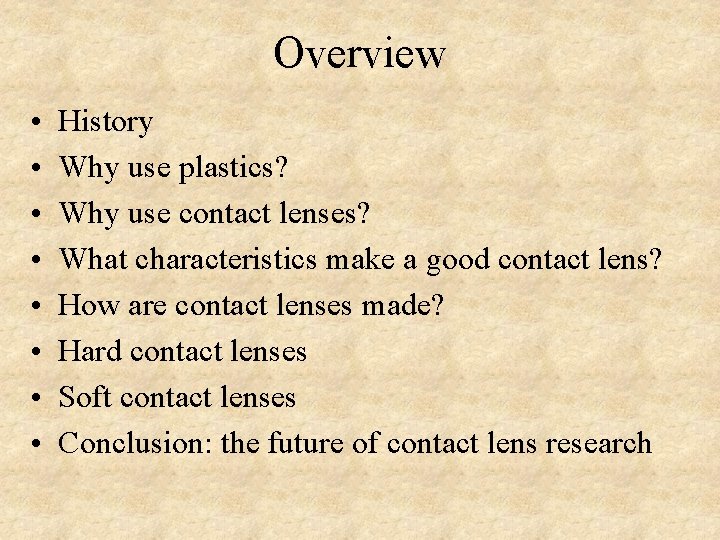
Overview • • History Why use plastics? Why use contact lenses? What characteristics make a good contact lens? How are contact lenses made? Hard contact lenses Soft contact lenses Conclusion: the future of contact lens research
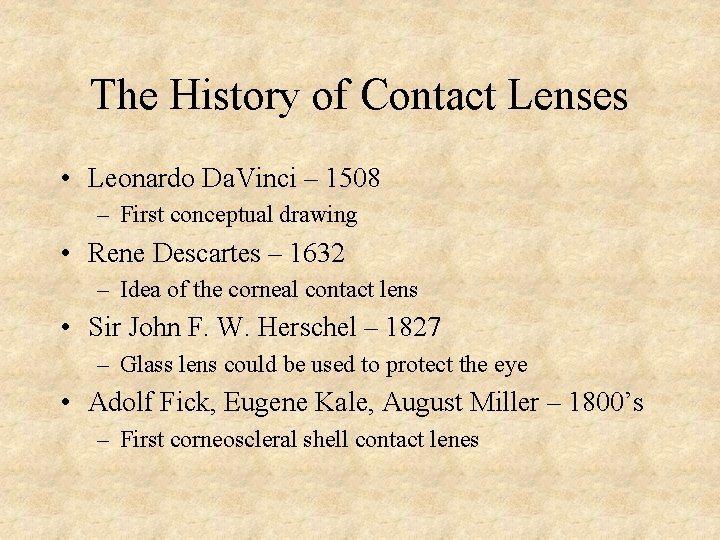
The History of Contact Lenses • Leonardo Da. Vinci – 1508 – First conceptual drawing • Rene Descartes – 1632 – Idea of the corneal contact lens • Sir John F. W. Herschel – 1827 – Glass lens could be used to protect the eye • Adolf Fick, Eugene Kale, August Miller – 1800’s – First corneoscleral shell contact lenes
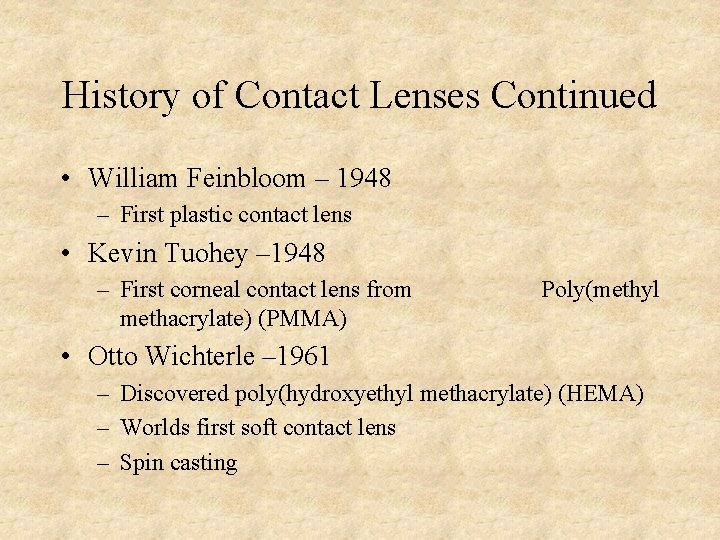
History of Contact Lenses Continued • William Feinbloom – 1948 – First plastic contact lens • Kevin Tuohey – 1948 – First corneal contact lens from Poly(methyl methacrylate) (PMMA) • Otto Wichterle – 1961 – Discovered poly(hydroxyethyl methacrylate) (HEMA) – Worlds first soft contact lens – Spin casting
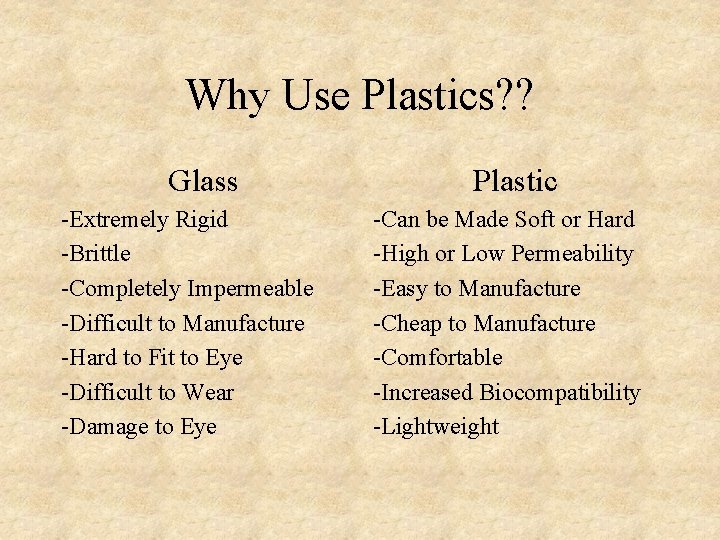
Why Use Plastics? ? Glass -Extremely Rigid -Brittle -Completely Impermeable -Difficult to Manufacture -Hard to Fit to Eye -Difficult to Wear -Damage to Eye Plastic -Can be Made Soft or Hard -High or Low Permeability -Easy to Manufacture -Cheap to Manufacture -Comfortable -Increased Biocompatibility -Lightweight
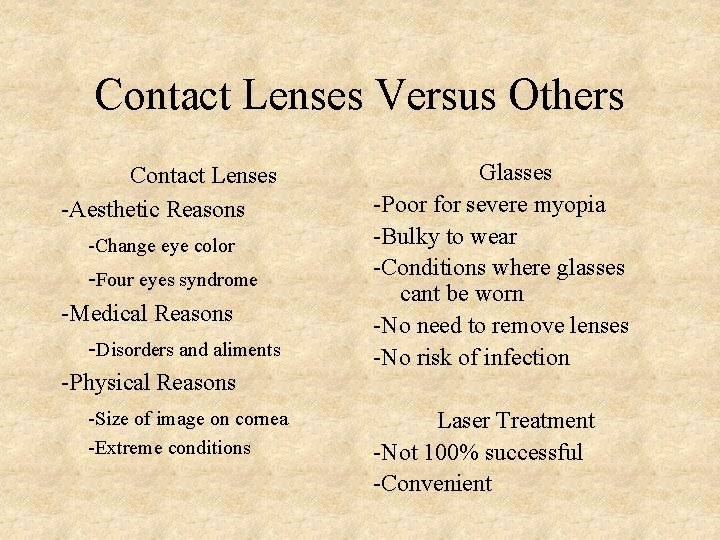
Contact Lenses Versus Others Contact Lenses -Aesthetic Reasons -Change eye color -Four eyes syndrome -Medical Reasons -Disorders and aliments -Physical Reasons -Size of image on cornea -Extreme conditions Glasses -Poor for severe myopia -Bulky to wear -Conditions where glasses cant be worn -No need to remove lenses -No risk of infection Laser Treatment -Not 100% successful -Convenient
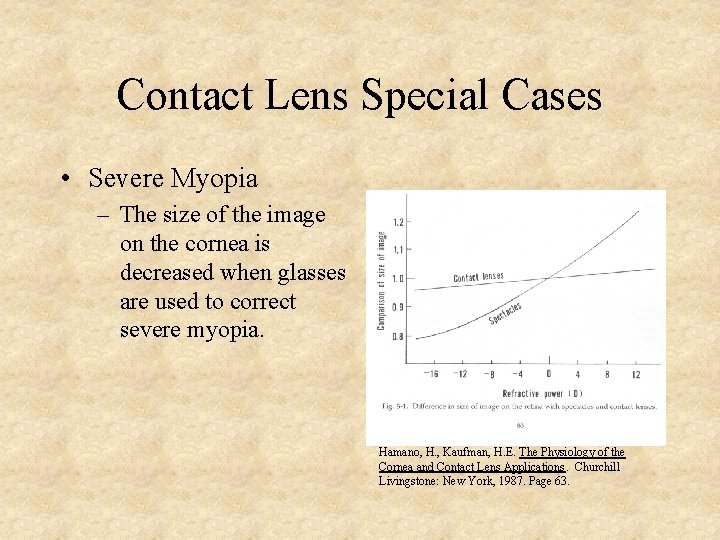
Contact Lens Special Cases • Severe Myopia – The size of the image on the cornea is decreased when glasses are used to correct severe myopia. Hamano, H. , Kaufman, H. E. The Physiology of the Cornea and Contact Lens Applications. Churchill Livingstone: New York, 1987. Page 63.
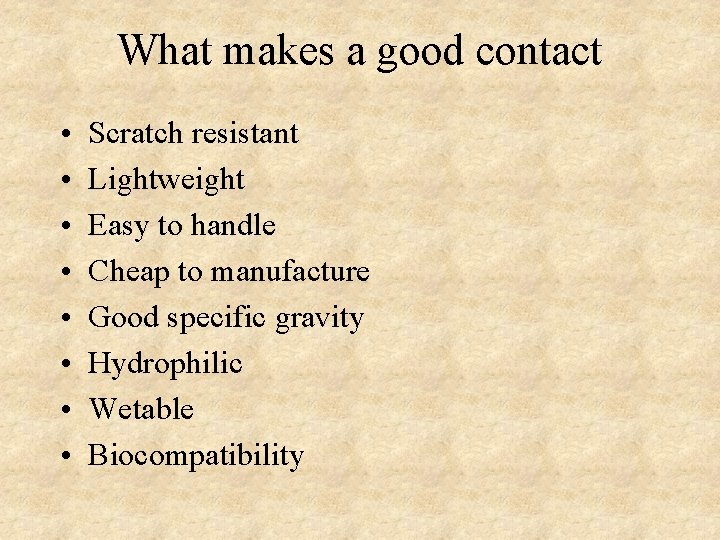
What makes a good contact • • Scratch resistant Lightweight Easy to handle Cheap to manufacture Good specific gravity Hydrophilic Wetable Biocompatibility
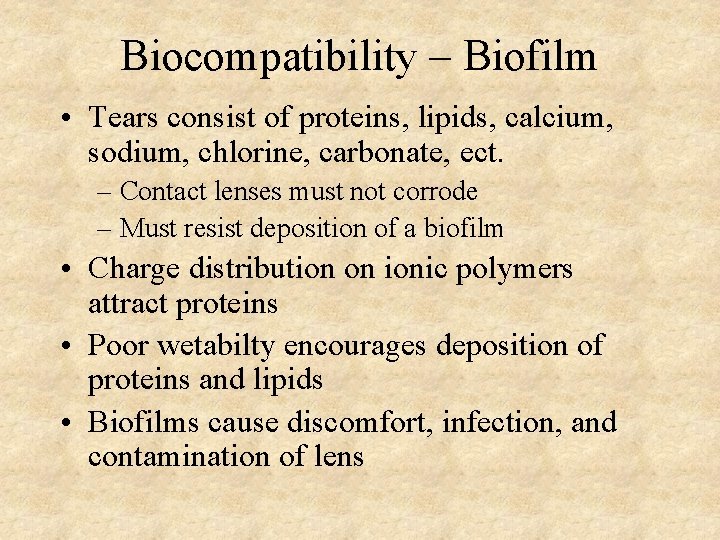
Biocompatibility – Biofilm • Tears consist of proteins, lipids, calcium, sodium, chlorine, carbonate, ect. – Contact lenses must not corrode – Must resist deposition of a biofilm • Charge distribution on ionic polymers attract proteins • Poor wetabilty encourages deposition of proteins and lipids • Biofilms cause discomfort, infection, and contamination of lens
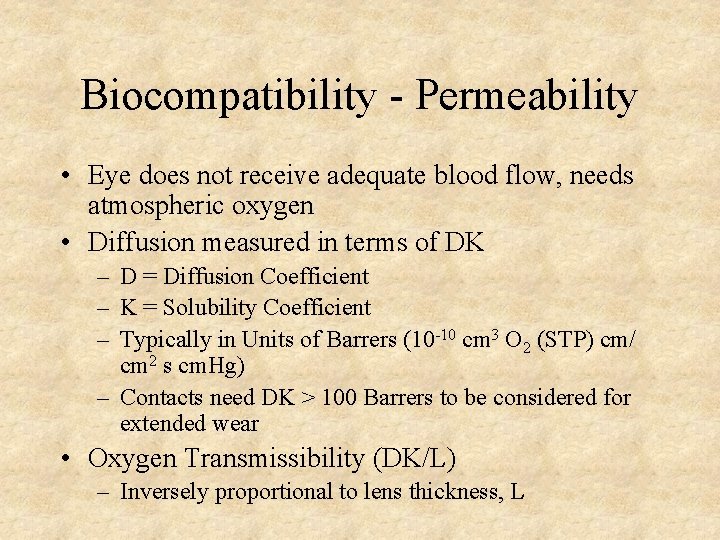
Biocompatibility - Permeability • Eye does not receive adequate blood flow, needs atmospheric oxygen • Diffusion measured in terms of DK – D = Diffusion Coefficient – K = Solubility Coefficient – Typically in Units of Barrers (10 -10 cm 3 O 2 (STP) cm/ cm 2 s cm. Hg) – Contacts need DK > 100 Barrers to be considered for extended wear • Oxygen Transmissibility (DK/L) – Inversely proportional to lens thickness, L
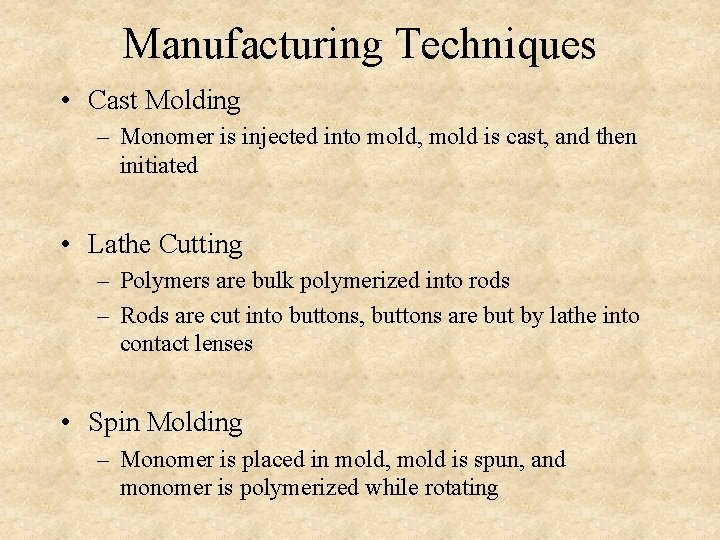
Manufacturing Techniques • Cast Molding – Monomer is injected into mold, mold is cast, and then initiated • Lathe Cutting – Polymers are bulk polymerized into rods – Rods are cut into buttons, buttons are but by lathe into contact lenses • Spin Molding – Monomer is placed in mold, mold is spun, and monomer is polymerized while rotating
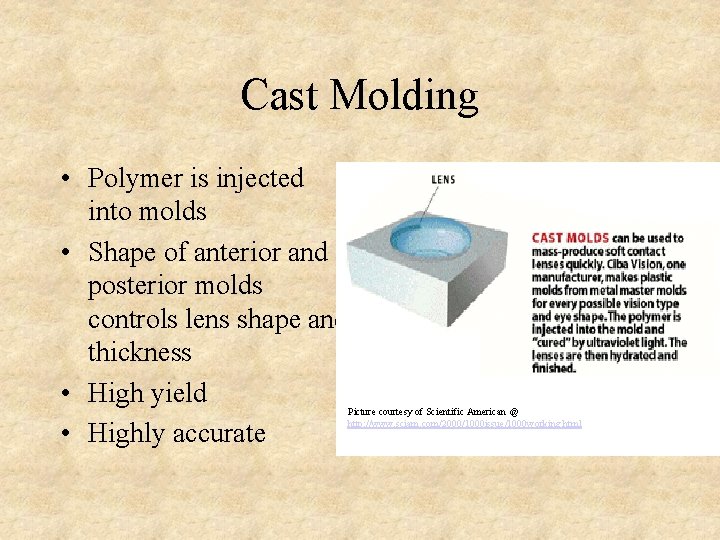
Cast Molding • Polymer is injected into molds • Shape of anterior and posterior molds controls lens shape and thickness • High yield • Highly accurate Picture courtesy of Scientific American @ http: //www. sciam. com/2000/1000 issue/1000 working. html
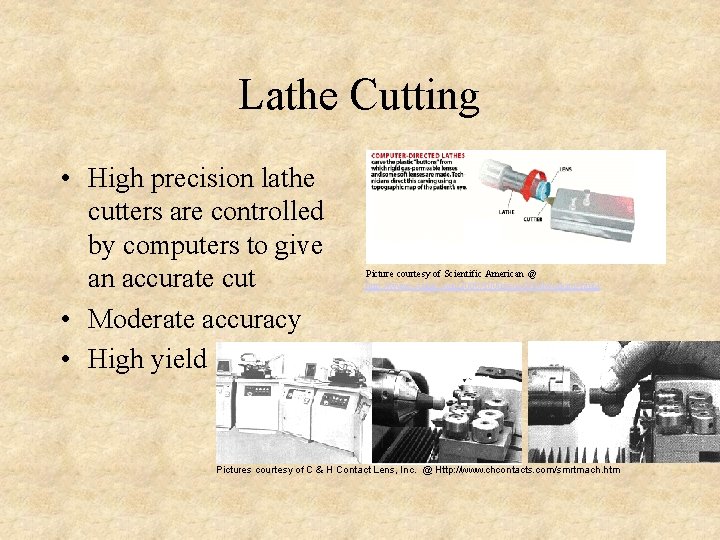
Lathe Cutting • High precision lathe cutters are controlled by computers to give an accurate cut • Moderate accuracy • High yield Picture courtesy of Scientific American @ http: //www. sciam. com/2000/1000 issue/1000 working. html Pictures courtesy of C & H Contact Lens, Inc. @ Http: //www. chcontacts. com/smrtmach. htm
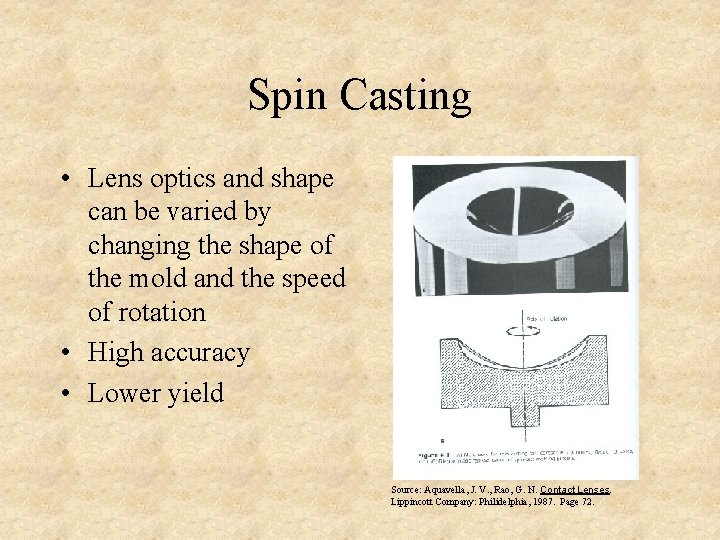
Spin Casting • Lens optics and shape can be varied by changing the shape of the mold and the speed of rotation • High accuracy • Lower yield Source: Aquavella, J. V. , Rao, G. N. Contact Lenses. Lippincott Company: Philidelphia, 1987. Page 72.
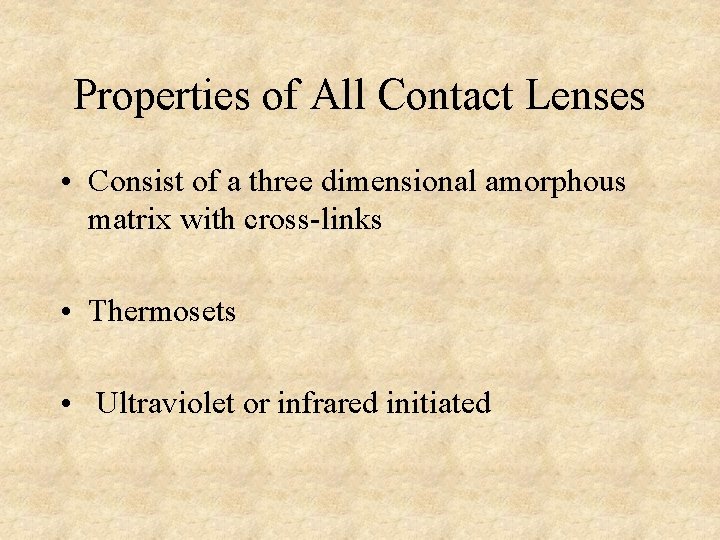
Properties of All Contact Lenses • Consist of a three dimensional amorphous matrix with cross-links • Thermosets • Ultraviolet or infrared initiated
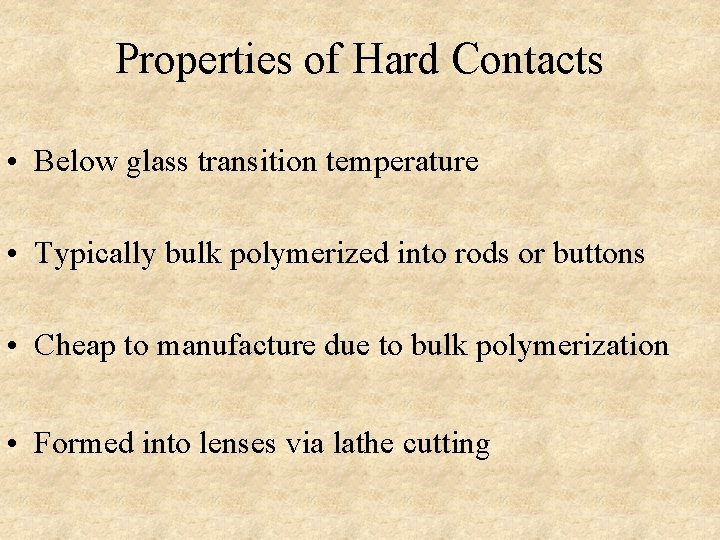
Properties of Hard Contacts • Below glass transition temperature • Typically bulk polymerized into rods or buttons • Cheap to manufacture due to bulk polymerization • Formed into lenses via lathe cutting
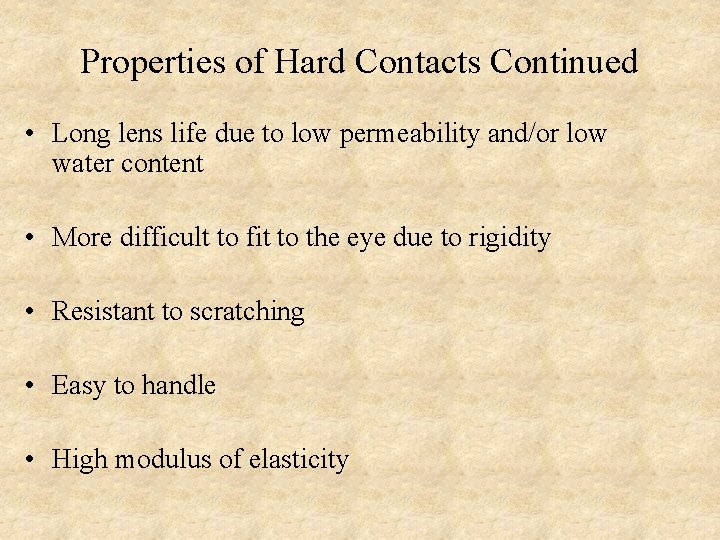
Properties of Hard Contacts Continued • Long lens life due to low permeability and/or low water content • More difficult to fit to the eye due to rigidity • Resistant to scratching • Easy to handle • High modulus of elasticity
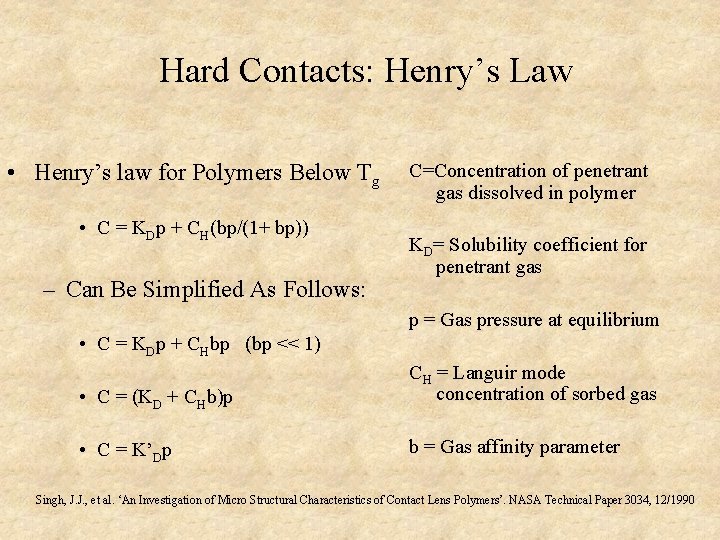
Hard Contacts: Henry’s Law • Henry’s law for Polymers Below Tg • C = KDp + CH(bp/(1+ bp)) – Can Be Simplified As Follows: C=Concentration of penetrant gas dissolved in polymer KD= Solubility coefficient for penetrant gas p = Gas pressure at equilibrium • C = KDp + CHbp (bp << 1) • C = (KD + CHb)p CH = Languir mode concentration of sorbed gas • C = K’Dp b = Gas affinity parameter Singh, J. J. , et al. ‘An Investigation of Micro Structural Characteristics of Contact Lens Polymers’. NASA Technical Paper 3034, 12/1990
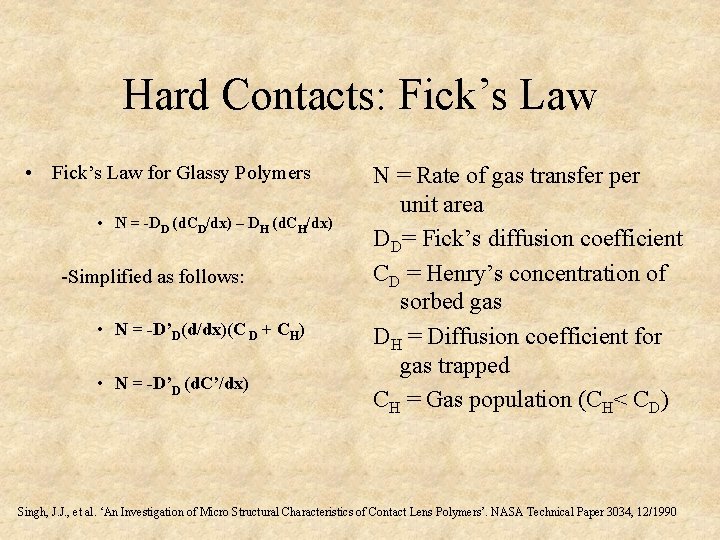
Hard Contacts: Fick’s Law • Fick’s Law for Glassy Polymers • N = -DD (d. CD/dx) – DH (d. CH/dx) -Simplified as follows: • N = -D’D(d/dx)(C D + CH) • N = -D’D (d. C’/dx) N = Rate of gas transfer per unit area DD= Fick’s diffusion coefficient CD = Henry’s concentration of sorbed gas DH = Diffusion coefficient for gas trapped CH = Gas population (CH< CD) Singh, J. J. , et al. ‘An Investigation of Micro Structural Characteristics of Contact Lens Polymers’. NASA Technical Paper 3034, 12/1990
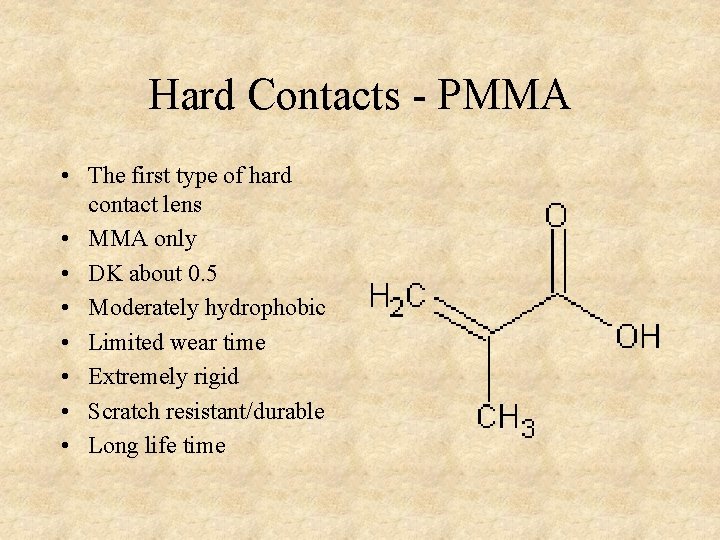
Hard Contacts - PMMA • The first type of hard contact lens • MMA only • DK about 0. 5 • Moderately hydrophobic • Limited wear time • Extremely rigid • Scratch resistant/durable • Long life time
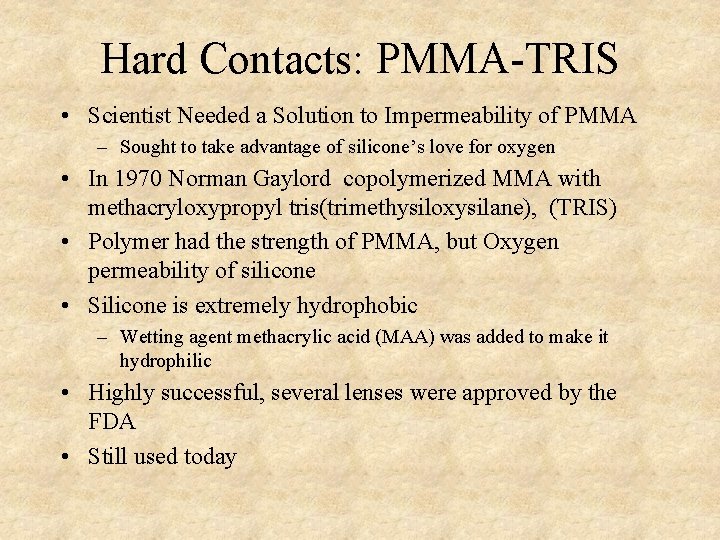
Hard Contacts: PMMA-TRIS • Scientist Needed a Solution to Impermeability of PMMA – Sought to take advantage of silicone’s love for oxygen • In 1970 Norman Gaylord copolymerized MMA with methacryloxypropyl tris(trimethysiloxysilane), (TRIS) • Polymer had the strength of PMMA, but Oxygen permeability of silicone • Silicone is extremely hydrophobic – Wetting agent methacrylic acid (MAA) was added to make it hydrophilic • Highly successful, several lenses were approved by the FDA • Still used today
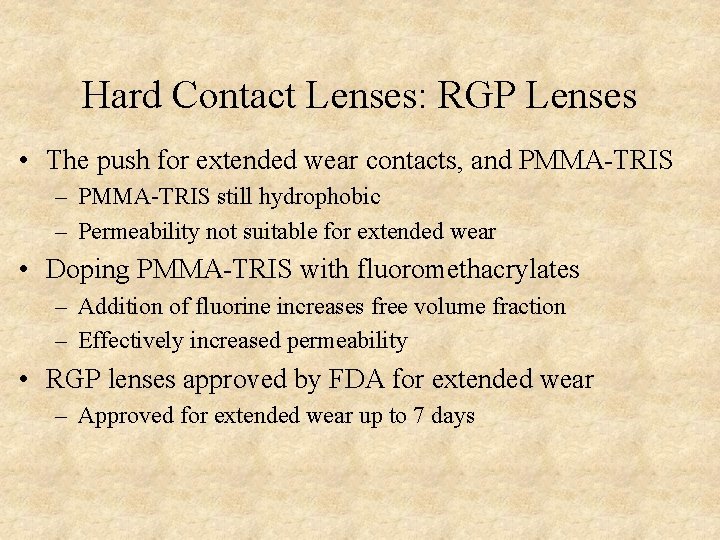
Hard Contact Lenses: RGP Lenses • The push for extended wear contacts, and PMMA-TRIS – PMMA-TRIS still hydrophobic – Permeability not suitable for extended wear • Doping PMMA-TRIS with fluoromethacrylates – Addition of fluorine increases free volume fraction – Effectively increased permeability • RGP lenses approved by FDA for extended wear – Approved for extended wear up to 7 days
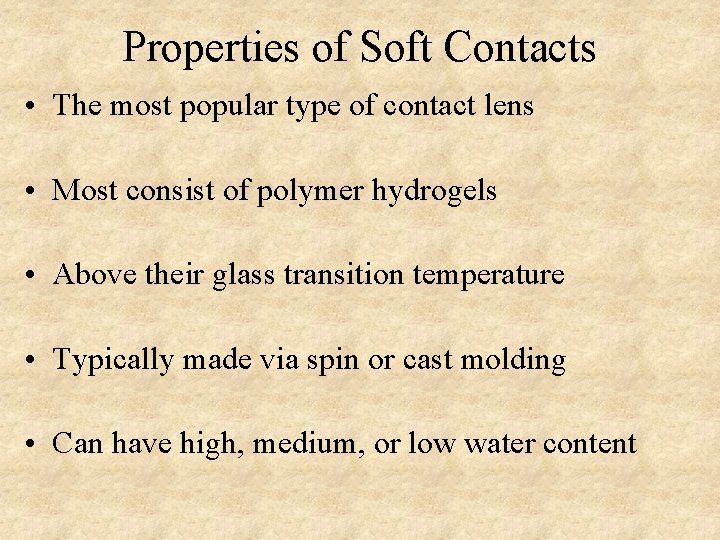
Properties of Soft Contacts • The most popular type of contact lens • Most consist of polymer hydrogels • Above their glass transition temperature • Typically made via spin or cast molding • Can have high, medium, or low water content
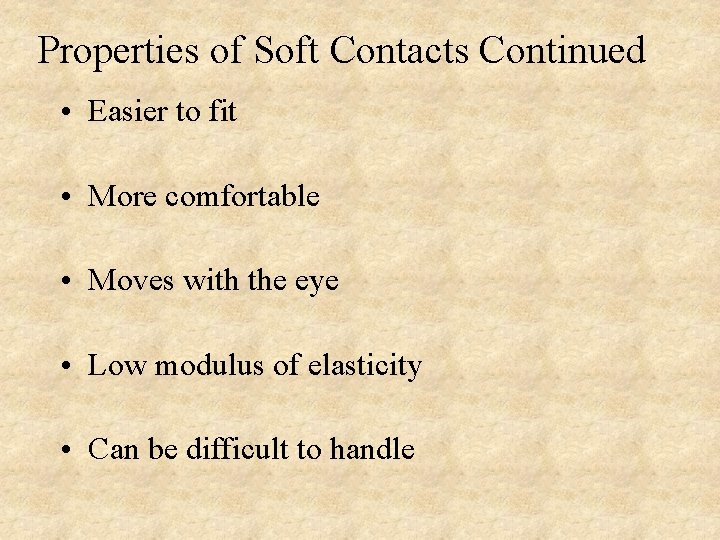
Properties of Soft Contacts Continued • Easier to fit • More comfortable • Moves with the eye • Low modulus of elasticity • Can be difficult to handle
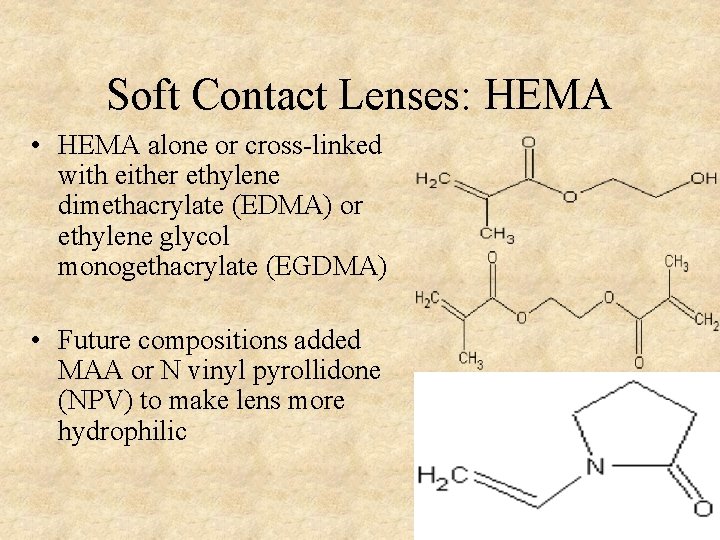
Soft Contact Lenses: HEMA • HEMA alone or cross-linked with either ethylene dimethacrylate (EDMA) or ethylene glycol monogethacrylate (EGDMA) • Future compositions added MAA or N vinyl pyrollidone (NPV) to make lens more hydrophilic
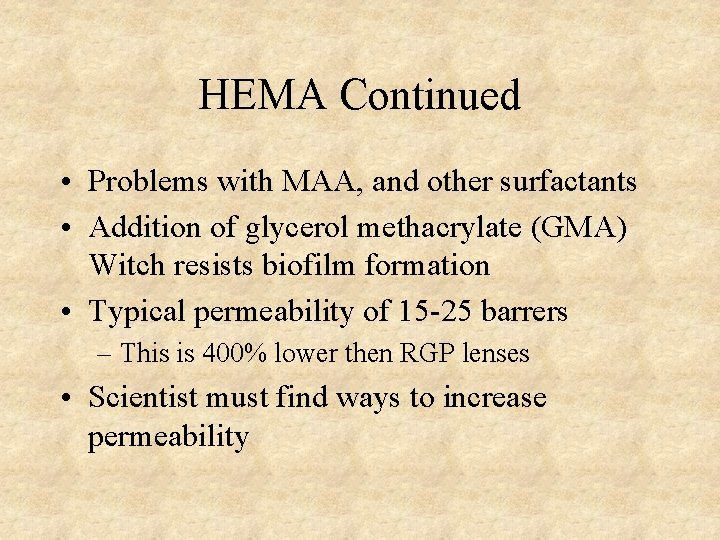
HEMA Continued • Problems with MAA, and other surfactants • Addition of glycerol methacrylate (GMA) Witch resists biofilm formation • Typical permeability of 15 -25 barrers – This is 400% lower then RGP lenses • Scientist must find ways to increase permeability
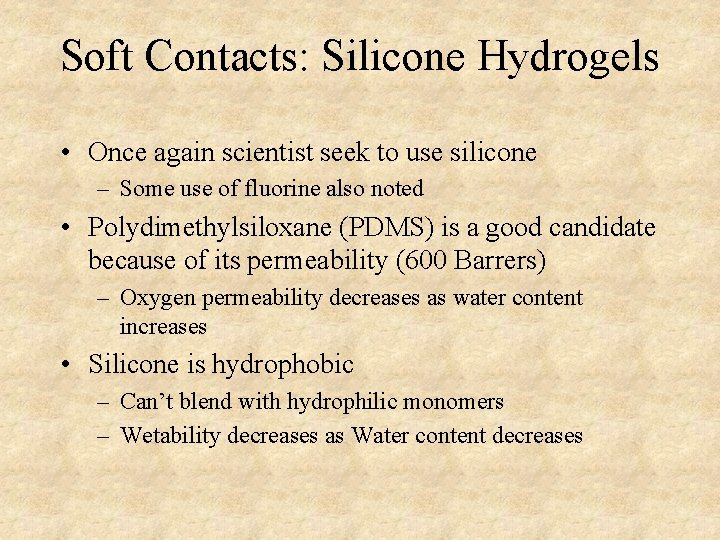
Soft Contacts: Silicone Hydrogels • Once again scientist seek to use silicone – Some use of fluorine also noted • Polydimethylsiloxane (PDMS) is a good candidate because of its permeability (600 Barrers) – Oxygen permeability decreases as water content increases • Silicone is hydrophobic – Can’t blend with hydrophilic monomers – Wetability decreases as Water content decreases
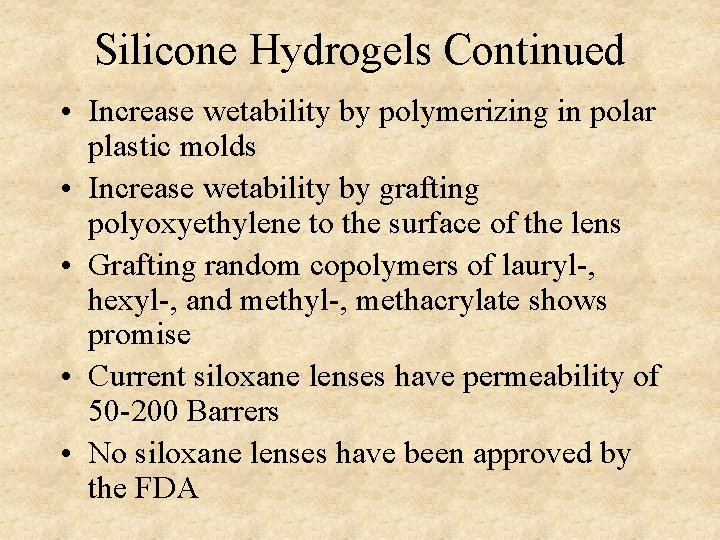
Silicone Hydrogels Continued • Increase wetability by polymerizing in polar plastic molds • Increase wetability by grafting polyoxyethylene to the surface of the lens • Grafting random copolymers of lauryl-, hexyl-, and methyl-, methacrylate shows promise • Current siloxane lenses have permeability of 50 -200 Barrers • No siloxane lenses have been approved by the FDA
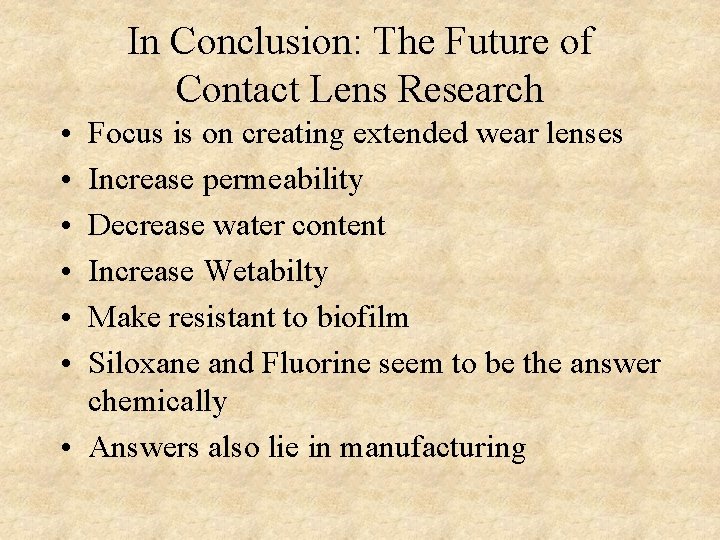
In Conclusion: The Future of Contact Lens Research • • • Focus is on creating extended wear lenses Increase permeability Decrease water content Increase Wetabilty Make resistant to biofilm Siloxane and Fluorine seem to be the answer chemically • Answers also lie in manufacturing
- Slides: 29