CONFIDENTIAL Value Stream Mapping Training Material November 1999
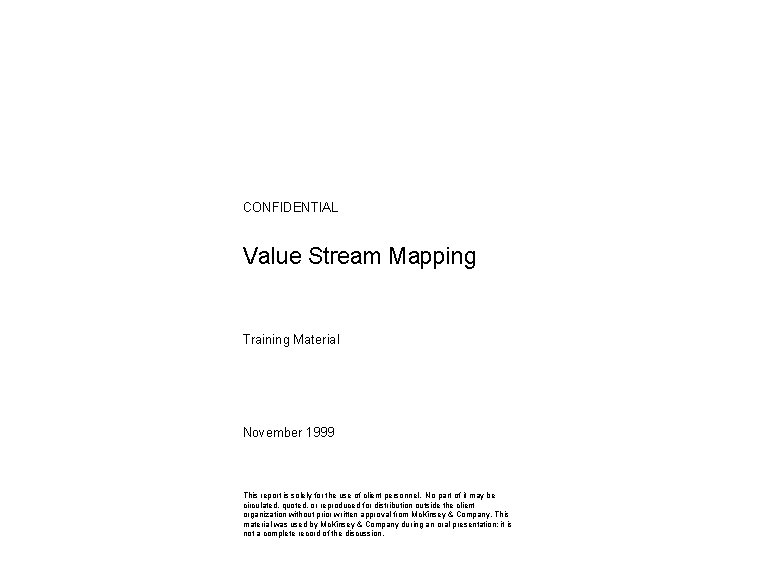
CONFIDENTIAL Value Stream Mapping Training Material November 1999 This report is solely for the use of client personnel. No part of it may be circulated, quoted, or reproduced for distribution outside the client organization without prior written approval from Mc. Kinsey & Company. This material was used by Mc. Kinsey & Company during an oral presentation; it is not a complete record of the discussion.
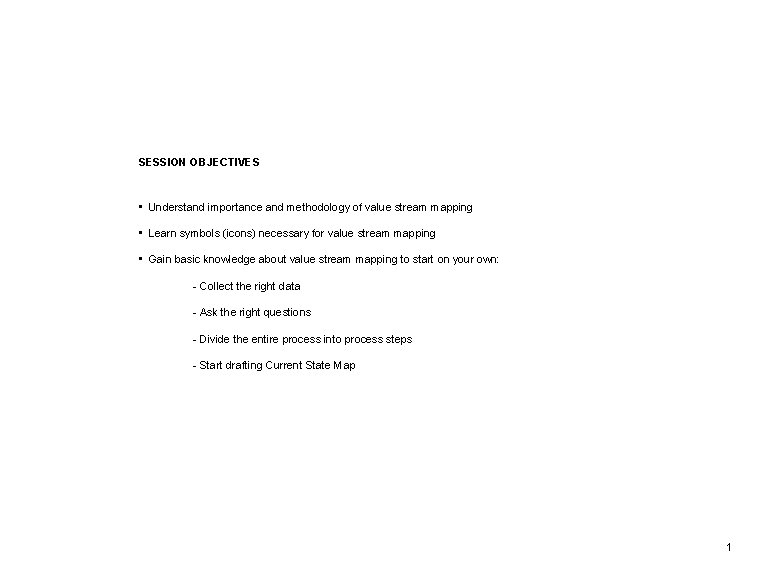
SESSION OBJECTIVES • Understand importance and methodology of value stream mapping • Learn symbols (icons) necessary for value stream mapping • Gain basic knowledge about value stream mapping to start on your own: - Collect the right data - Ask the right questions - Divide the entire process into process steps - Start drafting Current State Map 1
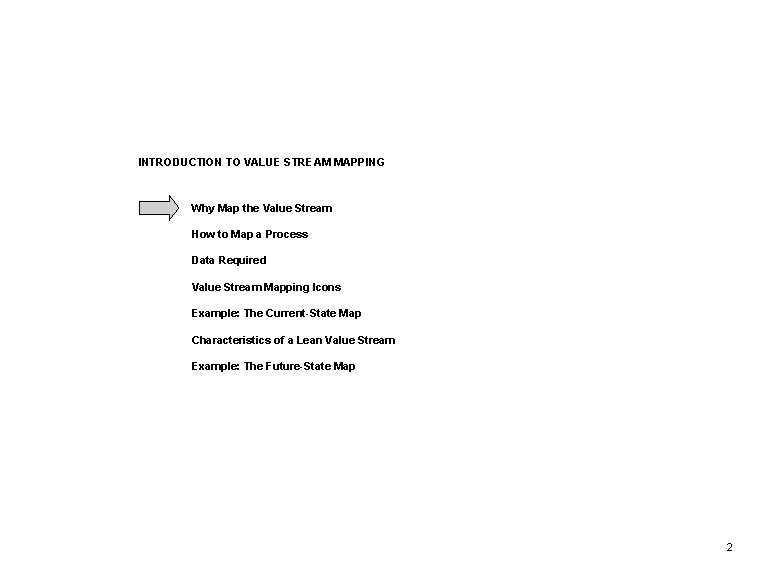
INTRODUCTION TO VALUE STREAM MAPPING Why Map the Value Stream How to Map a Process Data Required Value Stream Mapping Icons Example: The Current-State Map Characteristics of a Lean Value Stream Example: The Future-State Map 2
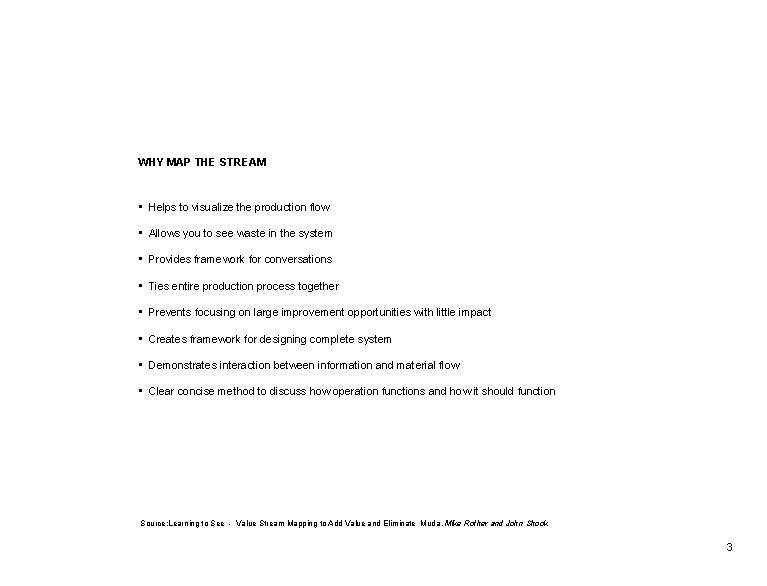
WHY MAP THE STREAM • Helps to visualize the production flow • Allows you to see waste in the system • Provides framework for conversations • Ties entire production process together • Prevents focusing on large improvement opportunities with little impact • Creates framework for designing complete system • Demonstrates interaction between information and material flow • Clear concise method to discuss how operation functions and how it should function Source: Learning to See - Value Stream Mapping to Add Value and Eliminate Muda, Mike Rother and John Shook 3
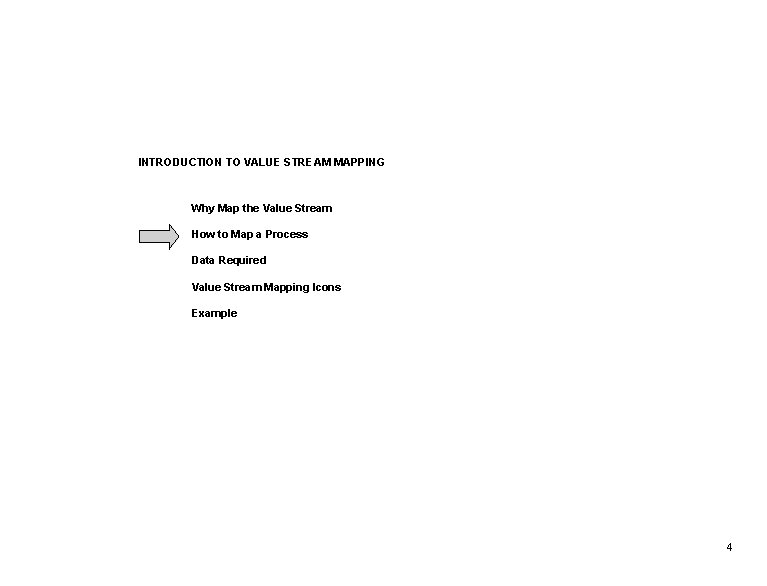
INTRODUCTION TO VALUE STREAM MAPPING Why Map the Value Stream How to Map a Process Data Required Value Stream Mapping Icons Example 4
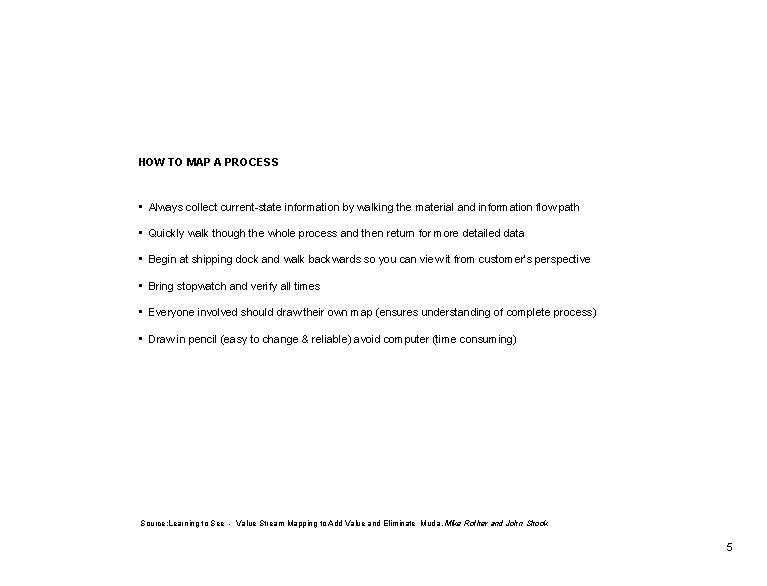
HOW TO MAP A PROCESS • Always collect current-state information by walking the material and information flow path • Quickly walk though the whole process and then return for more detailed data • Begin at shipping dock and walk backwards so you can view it from customer’s perspective • Bring stopwatch and verify all times • Everyone involved should draw their own map (ensures understanding of complete process) • Draw in pencil (easy to change & reliable) avoid computer (time consuming) Source: Learning to See - Value Stream Mapping to Add Value and Eliminate Muda, Mike Rother and John Shook 5
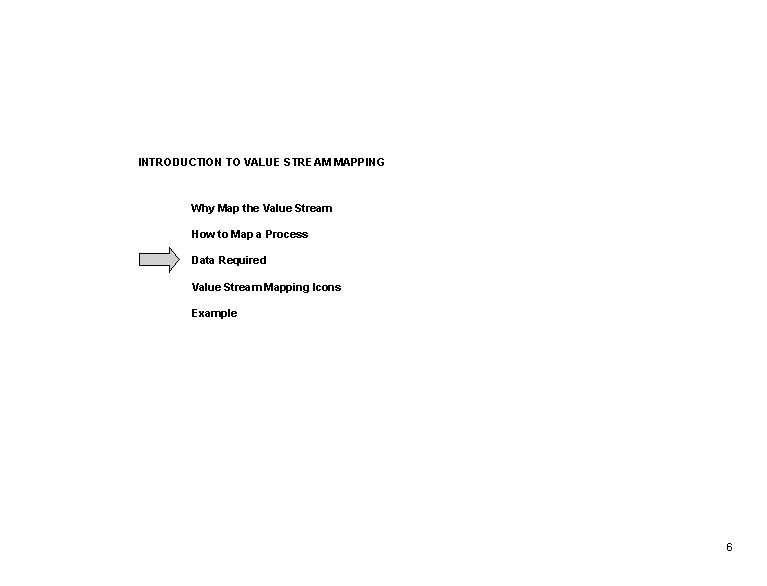
INTRODUCTION TO VALUE STREAM MAPPING Why Map the Value Stream How to Map a Process Data Required Value Stream Mapping Icons Example 6
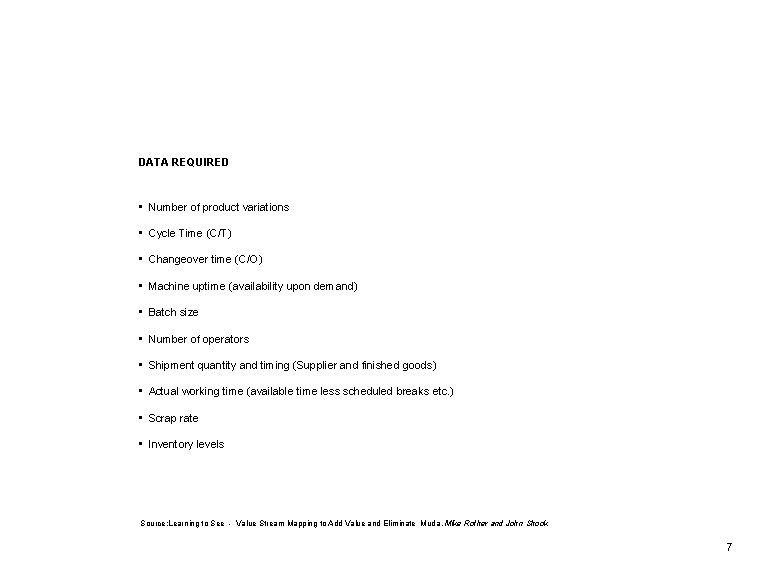
DATA REQUIRED • Number of product variations • Cycle Time (C/T) • Changeover time (C/O) • Machine uptime (availability upon demand) • Batch size • Number of operators • Shipment quantity and timing (Supplier and finished goods) • Actual working time (available time less scheduled breaks etc. ) • Scrap rate • Inventory levels Source: Learning to See - Value Stream Mapping to Add Value and Eliminate Muda, Mike Rother and John Shook 7
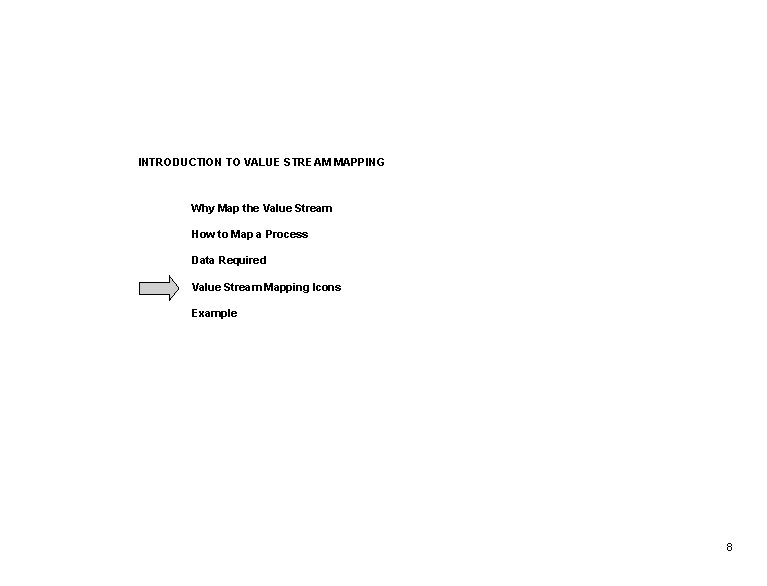
INTRODUCTION TO VALUE STREAM MAPPING Why Map the Value Stream How to Map a Process Data Required Value Stream Mapping Icons Example 8
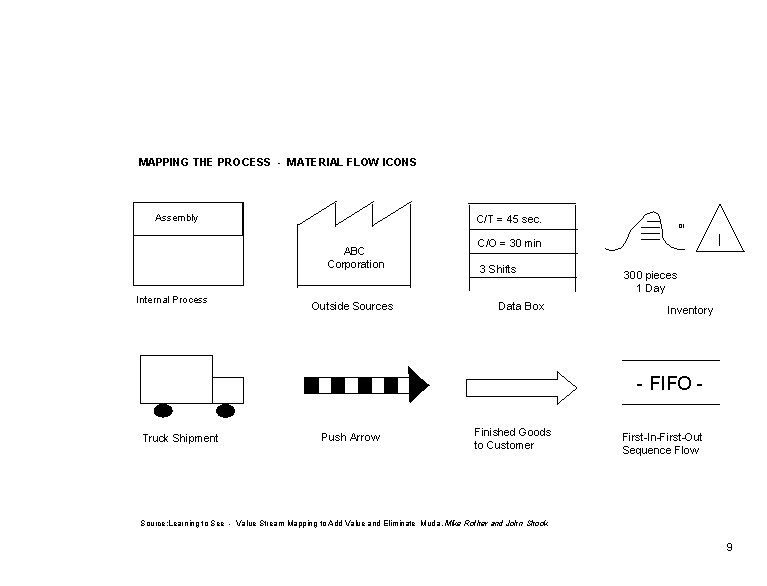
MAPPING THE PROCESS - MATERIAL FLOW ICONS Assembly C/T = 45 sec. ABC Corporation Internal Process Outside Sources or I C/O = 30 min 3 Shifts Data Box 300 pieces 1 Day Inventory - FIFO Truck Shipment Push Arrow Finished Goods to Customer First-In-First-Out Sequence Flow Source: Learning to See - Value Stream Mapping to Add Value and Eliminate Muda, Mike Rother and John Shook 9
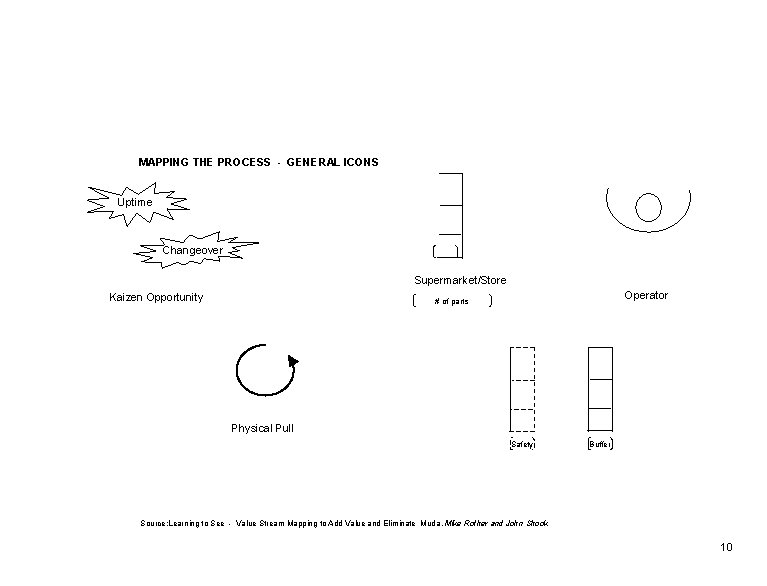
MAPPING THE PROCESS - GENERAL ICONS Uptime Changeover Supermarket/Store Kaizen Opportunity Operator # of parts Physical Pull Safety Buffer Source: Learning to See - Value Stream Mapping to Add Value and Eliminate Muda, Mike Rother and John Shook 10
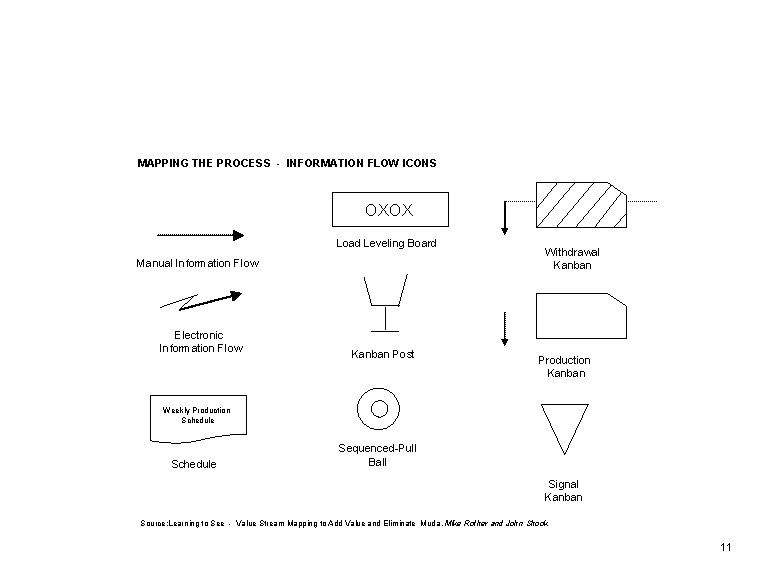
MAPPING THE PROCESS - INFORMATION FLOW ICONS OXOX Load Leveling Board Manual Information Flow Electronic Information Flow Kanban Post Withdrawal Kanban Production Kanban Weekly Production Schedule Sequenced-Pull Ball Signal Kanban Source: Learning to See - Value Stream Mapping to Add Value and Eliminate Muda, Mike Rother and John Shook 11
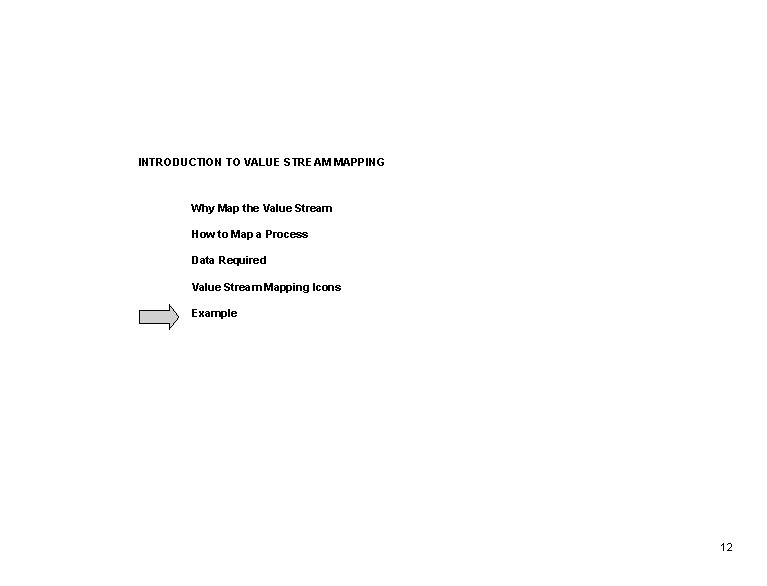
INTRODUCTION TO VALUE STREAM MAPPING Why Map the Value Stream How to Map a Process Data Required Value Stream Mapping Icons Example 12
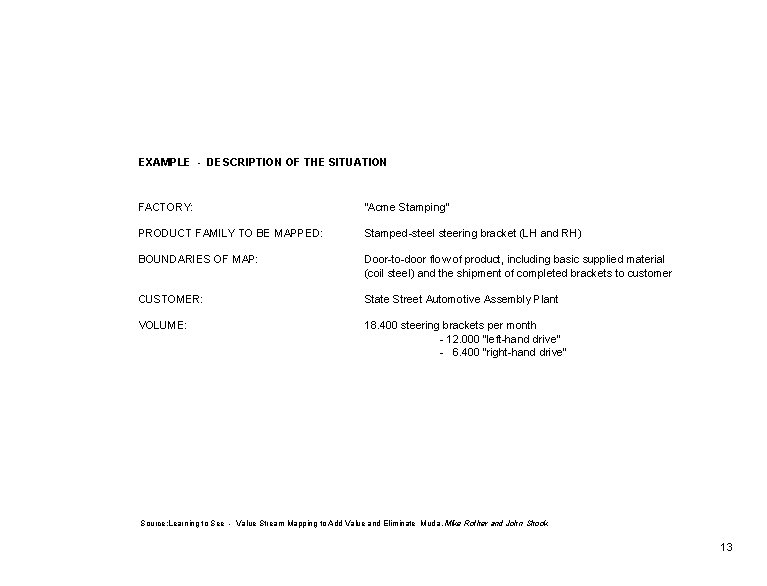
EXAMPLE - DESCRIPTION OF THE SITUATION FACTORY: “Acme Stamping” PRODUCT FAMILY TO BE MAPPED: Stamped-steel steering bracket (LH and RH) BOUNDARIES OF MAP: Door-to-door flow of product, including basic supplied material (coil steel) and the shipment of completed brackets to customer CUSTOMER: State Street Automotive Assembly Plant VOLUME: 18. 400 steering brackets per month - 12. 000 “left-hand drive” - 6. 400 “right-hand drive” Source: Learning to See - Value Stream Mapping to Add Value and Eliminate Muda, Mike Rother and John Shook 13
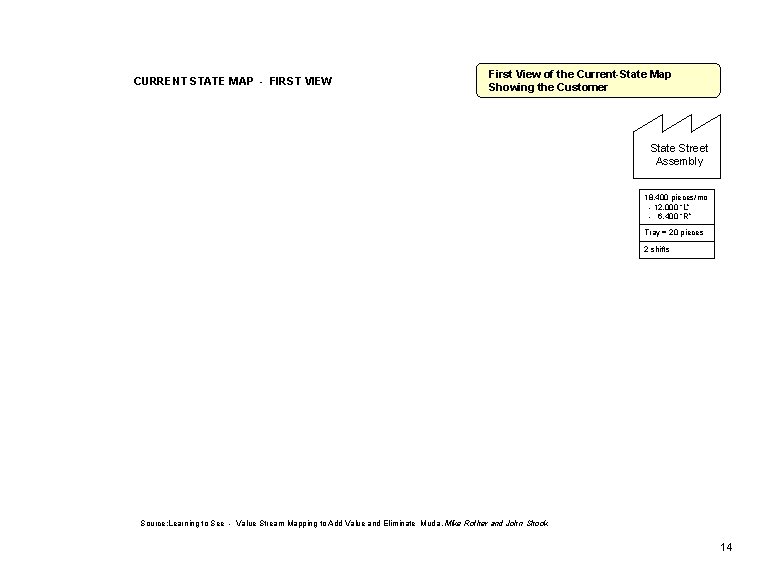
CURRENT STATE MAP - FIRST VIEW First View of the Current-State Map Showing the Customer State Street Assembly 18, 400 pieces/mo - 12, 000 “L” - 6, 400 “R” Tray = 20 pieces 2 shifts Source: Learning to See - Value Stream Mapping to Add Value and Eliminate Muda, Mike Rother and John Shook 14
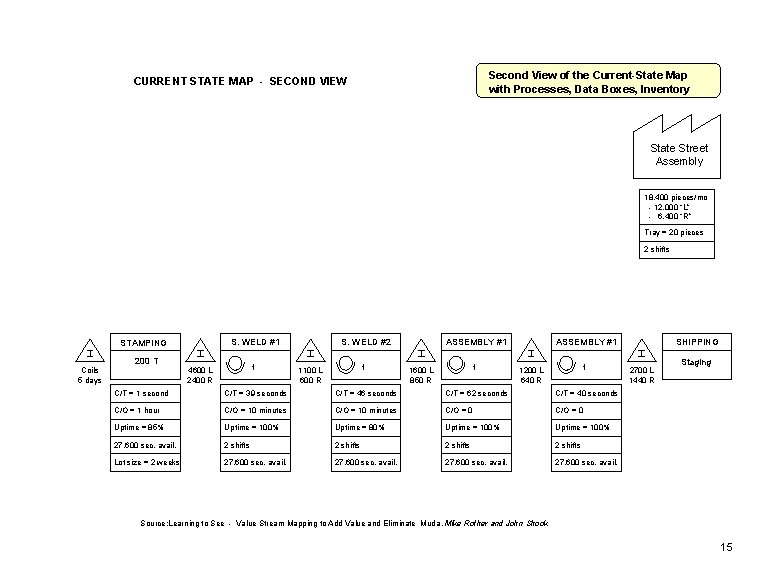
Second View of the Current-State Map with Processes, Data Boxes, Inventory CURRENT STATE MAP - SECOND VIEW State Street Assembly 18, 400 pieces/mo - 12, 000 “L” - 6, 400 “R” Tray = 20 pieces 2 shifts S. WELD #1 STAMPING Coils 5 days 200 T 1 4600 L 2400 R S. WELD #2 1 1100 L 600 R ASSEMBLY #1 1 1600 L 850 R ASSEMBLY #1 1 1200 L 640 R C/T = 1 second C/T = 39 seconds C/T = 46 seconds C/T = 62 seconds C/T = 40 seconds C/O = 1 hour C/O = 10 minutes C/O = 0 Uptime = 85% Uptime = 100% Uptime = 80% Uptime = 100% 27, 600 sec. avail. 2 shifts Lot size = 2 weeks 27, 600 sec. avail. SHIPPING 2700 L 1440 R Staging Source: Learning to See - Value Stream Mapping to Add Value and Eliminate Muda, Mike Rother and John Shook 15
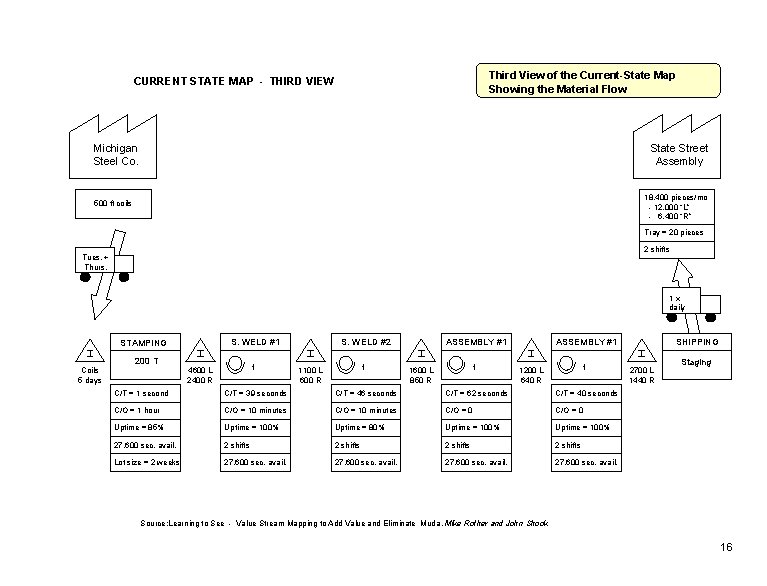
Third View of the Current-State Map Showing the Material Flow CURRENT STATE MAP - THIRD VIEW Michigan Steel Co. State Street Assembly 18, 400 pieces/mo - 12, 000 “L” - 6, 400 “R” 500 ft coils Tray = 20 pieces 2 shifts Tues. + Thurs. 1 x daily S. WELD #1 STAMPING Coils 5 days 200 T 1 4600 L 2400 R S. WELD #2 1 1100 L 600 R ASSEMBLY #1 1 1600 L 850 R ASSEMBLY #1 1 1200 L 640 R C/T = 1 second C/T = 39 seconds C/T = 46 seconds C/T = 62 seconds C/T = 40 seconds C/O = 1 hour C/O = 10 minutes C/O = 0 Uptime = 85% Uptime = 100% Uptime = 80% Uptime = 100% 27, 600 sec. avail. 2 shifts Lot size = 2 weeks 27, 600 sec. avail. SHIPPING 2700 L 1440 R Staging Source: Learning to See - Value Stream Mapping to Add Value and Eliminate Muda, Mike Rother and John Shook 16
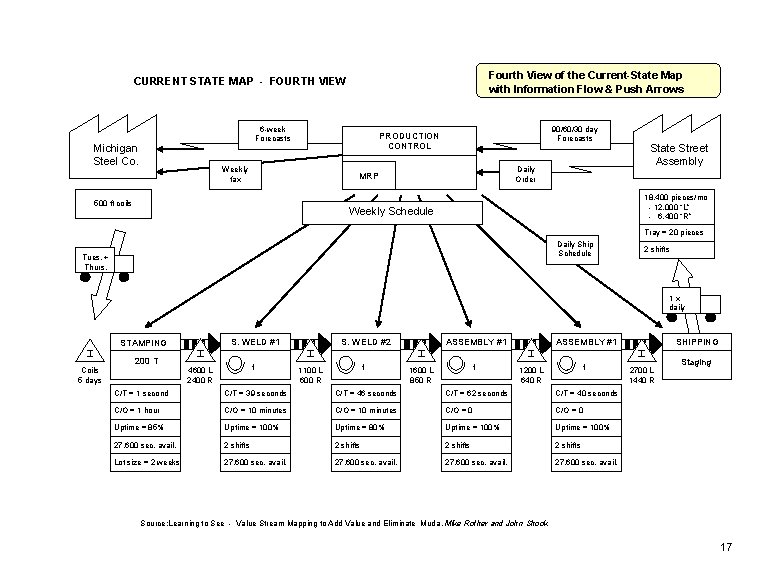
Fourth View of the Current-State Map with Information Flow & Push Arrows CURRENT STATE MAP - FOURTH VIEW 6 -week Forecasts Michigan Steel Co. 90/60/30 day Forecasts PRODUCTION CONTROL Weekly fax Daily Order MRP 500 ft coils State Street Assembly 18, 400 pieces/mo - 12, 000 “L” - 6, 400 “R” Weekly Schedule Tray = 20 pieces Daily Ship Schedule Tues. + Thurs. 2 shifts 1 x daily S. WELD #1 STAMPING Coils 5 days 200 T 1 4600 L 2400 R S. WELD #2 1 1100 L 600 R ASSEMBLY #1 1 1600 L 850 R ASSEMBLY #1 1 1200 L 640 R C/T = 1 second C/T = 39 seconds C/T = 46 seconds C/T = 62 seconds C/T = 40 seconds C/O = 1 hour C/O = 10 minutes C/O = 0 Uptime = 85% Uptime = 100% Uptime = 80% Uptime = 100% 27, 600 sec. avail. 2 shifts Lot size = 2 weeks 27, 600 sec. avail. SHIPPING 2700 L 1440 R Staging Source: Learning to See - Value Stream Mapping to Add Value and Eliminate Muda, Mike Rother and John Shook 17
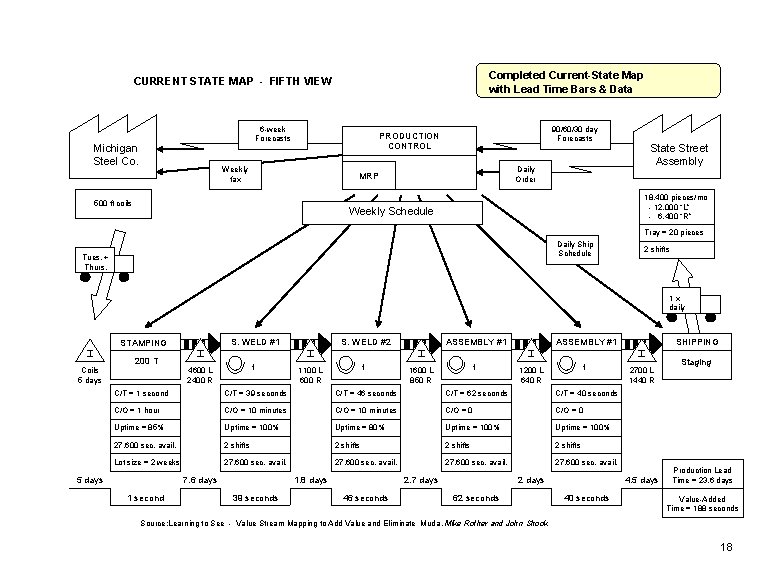
Completed Current-State Map with Lead Time Bars & Data CURRENT STATE MAP - FIFTH VIEW 6 -week Forecasts Michigan Steel Co. 90/60/30 day Forecasts PRODUCTION CONTROL Weekly fax Daily Order MRP 500 ft coils State Street Assembly 18, 400 pieces/mo - 12, 000 “L” - 6, 400 “R” Weekly Schedule Tray = 20 pieces Daily Ship Schedule Tues. + Thurs. 2 shifts 1 x daily S. WELD #1 STAMPING Coils 5 days 200 T 1 4600 L 2400 R S. WELD #2 1 1100 L 600 R ASSEMBLY #1 1 1600 L 850 R ASSEMBLY #1 1 1200 L 640 R C/T = 1 second C/T = 39 seconds C/T = 46 seconds C/T = 62 seconds C/T = 40 seconds C/O = 1 hour C/O = 10 minutes C/O = 0 Uptime = 85% Uptime = 100% Uptime = 80% Uptime = 100% 27, 600 sec. avail. 2 shifts Lot size = 2 weeks 27, 600 sec. avail. 5 days 7. 6 days 1 second 1. 8 days 39 seconds 2. 7 days 46 seconds 2 days 62 seconds SHIPPING 2700 L 1440 R 4. 5 days 40 seconds Staging Production Lead Time = 23. 6 days Value-Added Time = 188 seconds Source: Learning to See - Value Stream Mapping to Add Value and Eliminate Muda, Mike Rother and John Shook 18
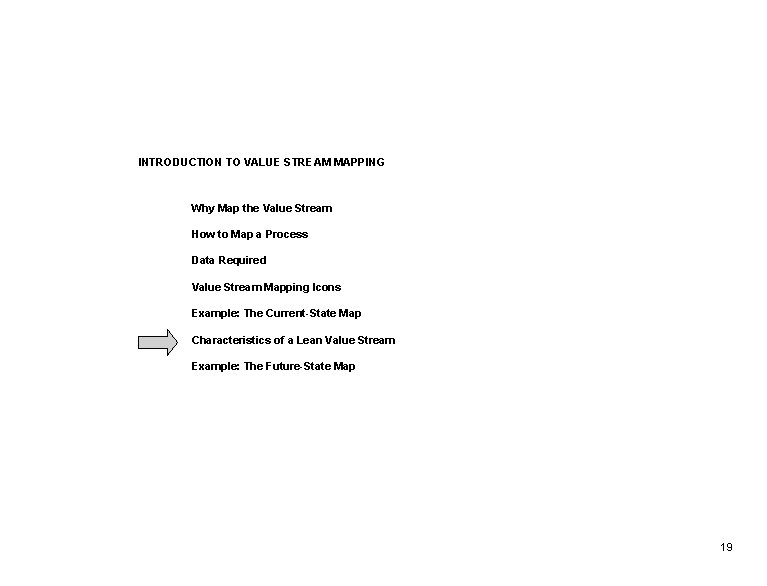
INTRODUCTION TO VALUE STREAM MAPPING Why Map the Value Stream How to Map a Process Data Required Value Stream Mapping Icons Example: The Current-State Map Characteristics of a Lean Value Stream Example: The Future-State Map 19
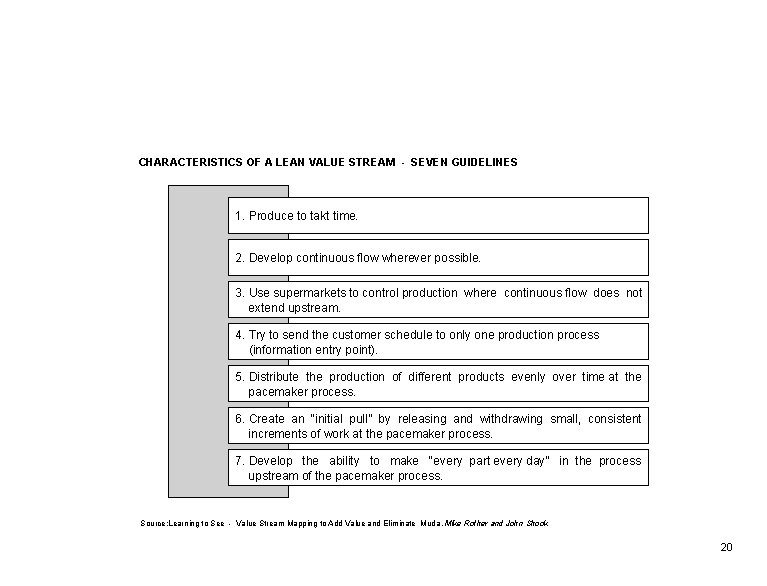
CHARACTERISTICS OF A LEAN VALUE STREAM - SEVEN GUIDELINES 1. Produce to takt time. 2. Develop continuous flow wherever possible. 3. Use supermarkets to control production where continuous flow does not extend upstream. 4. Try to send the customer schedule to only one production process (information entry point). 5. Distribute the production of different products evenly over time at the pacemaker process. 6. Create an “initial pull” by releasing and withdrawing small, consistent increments of work at the pacemaker process. 7. Develop the ability to make “every part every day” in the process upstream of the pacemaker process. Source: Learning to See - Value Stream Mapping to Add Value and Eliminate Muda, Mike Rother and John Shook 20
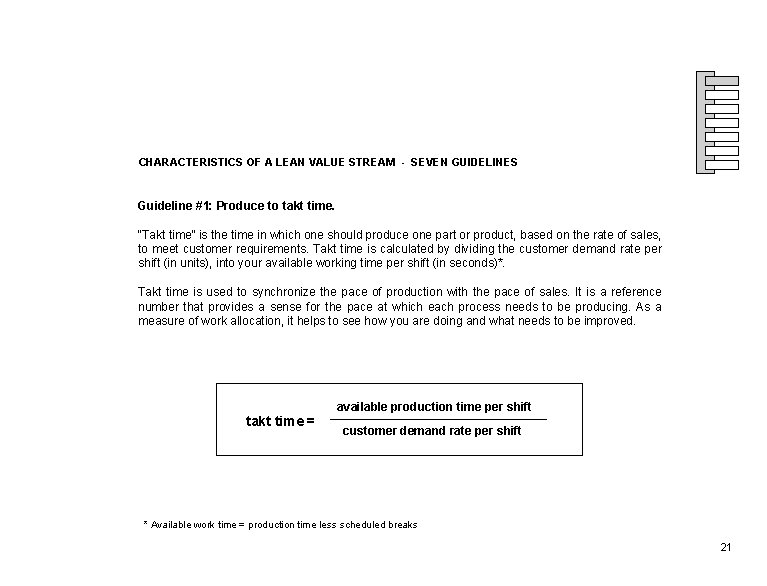
CHARACTERISTICS OF A LEAN VALUE STREAM - SEVEN GUIDELINES Guideline #1: Produce to takt time. “Takt time” is the time in which one should produce one part or product, based on the rate of sales, to meet customer requirements. Takt time is calculated by dividing the customer demand rate per shift (in units), into your available working time per shift (in seconds)*. Takt time is used to synchronize the pace of production with the pace of sales. It is a reference number that provides a sense for the pace at which each process needs to be producing. As a measure of work allocation, it helps to see how you are doing and what needs to be improved. takt time = available production time per shift customer demand rate per shift * Available work time = production time less scheduled breaks 21
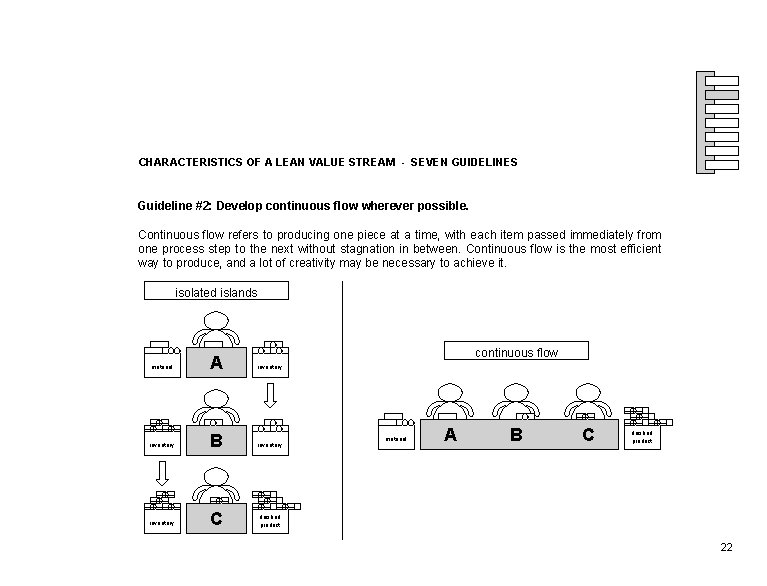
CHARACTERISTICS OF A LEAN VALUE STREAM - SEVEN GUIDELINES Guideline #2: Develop continuous flow wherever possible. Continuous flow refers to producing one piece at a time, with each item passed immediately from one process step to the next without stagnation in between. Continuous flow is the most efficient way to produce, and a lot of creativity may be necessary to achieve it. isolated islands continuous flow material A inventory B inventory C finished product material A B C finished product 22
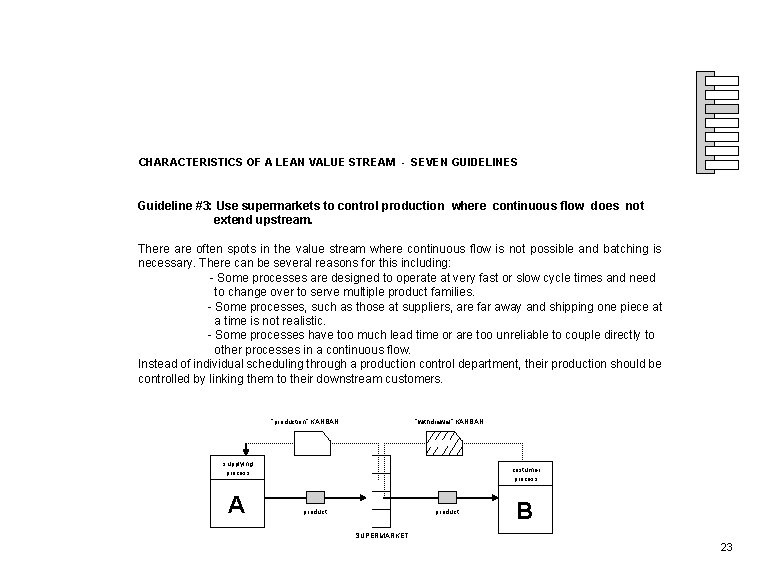
CHARACTERISTICS OF A LEAN VALUE STREAM - SEVEN GUIDELINES Guideline #3: Use supermarkets to control production where continuous flow does not extend upstream. There are often spots in the value stream where continuous flow is not possible and batching is necessary. There can be several reasons for this including: - Some processes are designed to operate at very fast or slow cycle times and need to change over to serve multiple product families. - Some processes, such as those at suppliers, are far away and shipping one piece at a time is not realistic. - Some processes have too much lead time or are too unreliable to couple directly to other processes in a continuous flow. Instead of individual scheduling through a production control department, their production should be controlled by linking them to their downstream customers. “production” KANBAN “withdrawal” KANBAN supplying process A costumer process product B SUPERMARKET 23
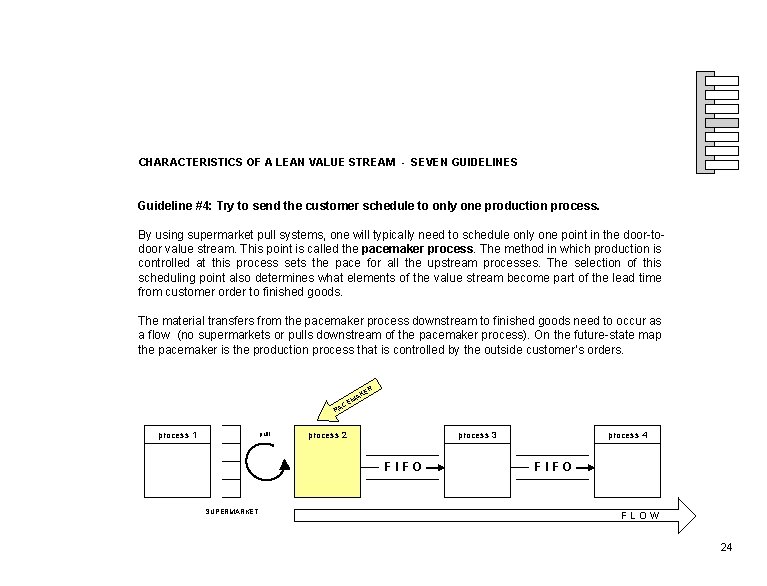
CHARACTERISTICS OF A LEAN VALUE STREAM - SEVEN GUIDELINES Guideline #4: Try to send the customer schedule to only one production process. By using supermarket pull systems, one will typically need to schedule only one point in the door-todoor value stream. This point is called the pacemaker process. The method in which production is controlled at this process sets the pace for all the upstream processes. The selection of this scheduling point also determines what elements of the value stream become part of the lead time from customer order to finished goods. The material transfers from the pacemaker process downstream to finished goods need to occur as a flow (no supermarkets or pulls downstream of the pacemaker process). On the future-state map the pacemaker is the production process that is controlled by the outside customer’s orders. ER AK M CE PA pull process 1 process 2 process 3 FIFO SUPERMARKET process 4 FIFO FLOW 24
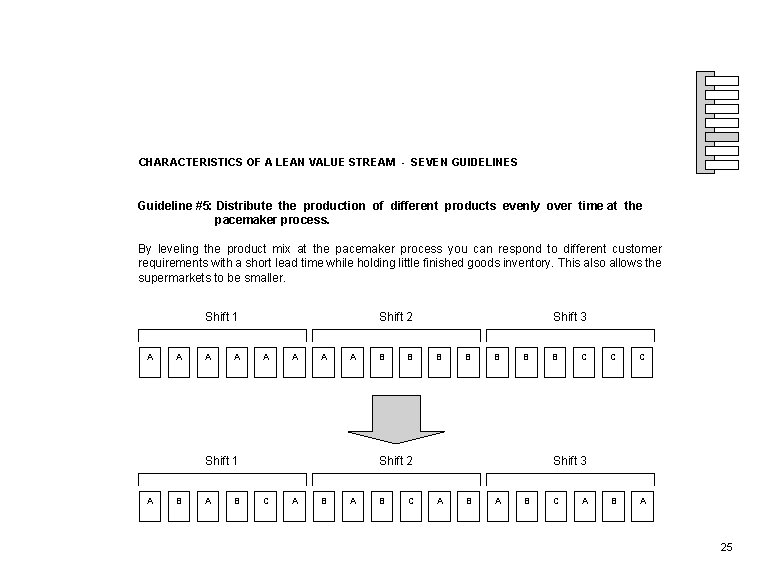
CHARACTERISTICS OF A LEAN VALUE STREAM - SEVEN GUIDELINES Guideline #5: Distribute the production of different products evenly over time at the pacemaker process. By leveling the product mix at the pacemaker process you can respond to different customer requirements with a short lead time while holding little finished goods inventory. This also allows the supermarkets to be smaller. Shift 1 A A Shift 2 A A Shift 1 A B B B Shift 3 B B Shift 2 C A B C B C C C B A Shift 3 A B C A 25
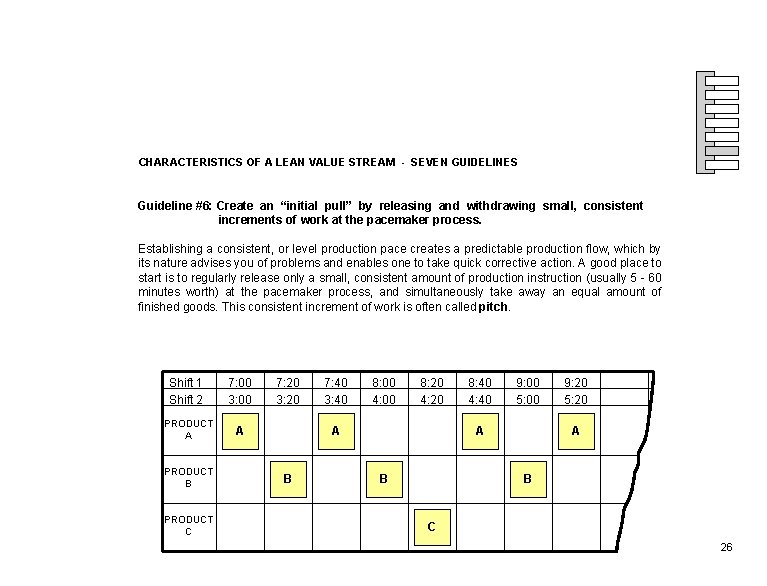
CHARACTERISTICS OF A LEAN VALUE STREAM - SEVEN GUIDELINES Guideline #6: Create an “initial pull” by releasing and withdrawing small, consistent increments of work at the pacemaker process. Establishing a consistent, or level production pace creates a predictable production flow, which by its nature advises you of problems and enables one to take quick corrective action. A good place to start is to regularly release only a small, consistent amount of production instruction (usually 5 - 60 minutes worth) at the pacemaker process, and simultaneously take away an equal amount of finished goods. This consistent increment of work is often called pitch. Shift 1 Shift 2 7: 00 3: 00 PRODUCT A A PRODUCT B PRODUCT C 7: 20 3: 20 7: 40 3: 40 8: 00 4: 00 8: 20 4: 20 A B 8: 40 4: 40 9: 00 5: 00 A B 9: 20 5: 20 A B C 26
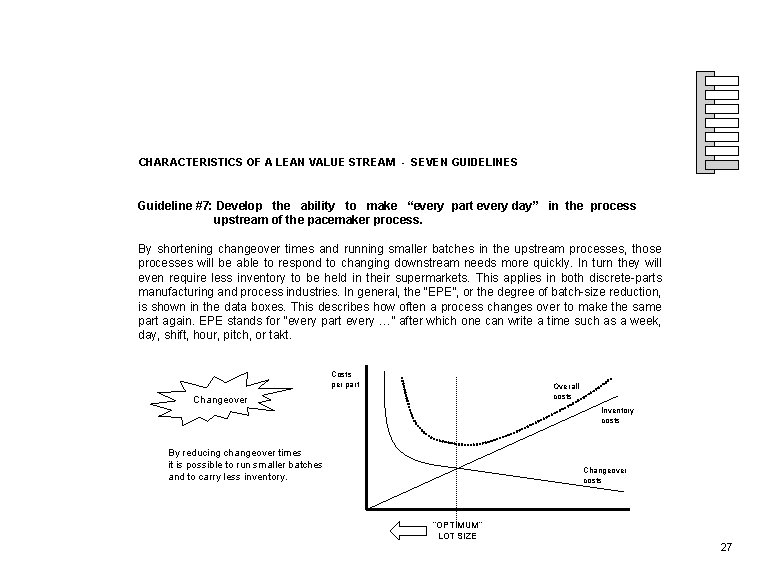
CHARACTERISTICS OF A LEAN VALUE STREAM - SEVEN GUIDELINES Guideline #7: Develop the ability to make “every part every day” in the process upstream of the pacemaker process. By shortening changeover times and running smaller batches in the upstream processes, those processes will be able to respond to changing downstream needs more quickly. In turn they will even require less inventory to be held in their supermarkets. This applies in both discrete-parts manufacturing and process industries. In general, the “EPE”, or the degree of batch-size reduction, is shown in the data boxes. This describes how often a process changes over to make the same part again. EPE stands for “every part every …” after which one can write a time such as a week, day, shift, hour, pitch, or takt. Costs per part Overall costs Changeover Inventory costs By reducing changeover times it is possible to run smaller batches and to carry less inventory. Changeover costs “OPTIMUM” LOT SIZE 27
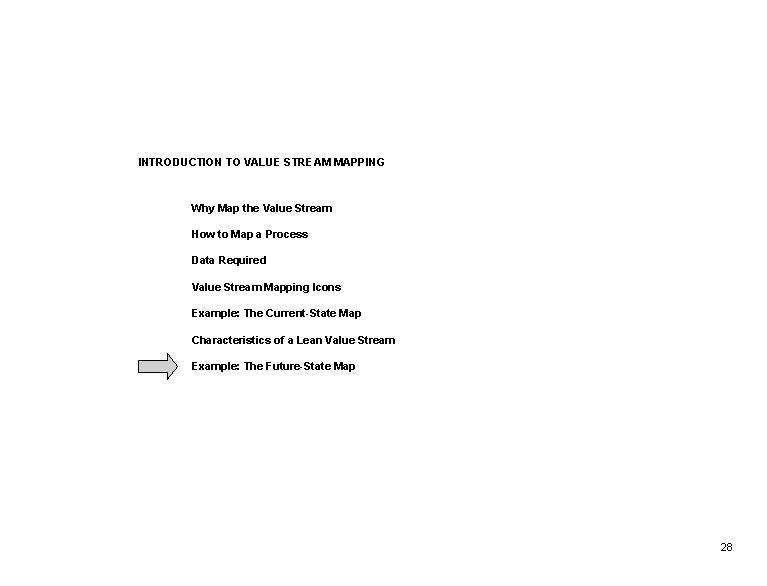
INTRODUCTION TO VALUE STREAM MAPPING Why Map the Value Stream How to Map a Process Data Required Value Stream Mapping Icons Example: The Current-State Map Characteristics of a Lean Value Stream Example: The Future-State Map 28
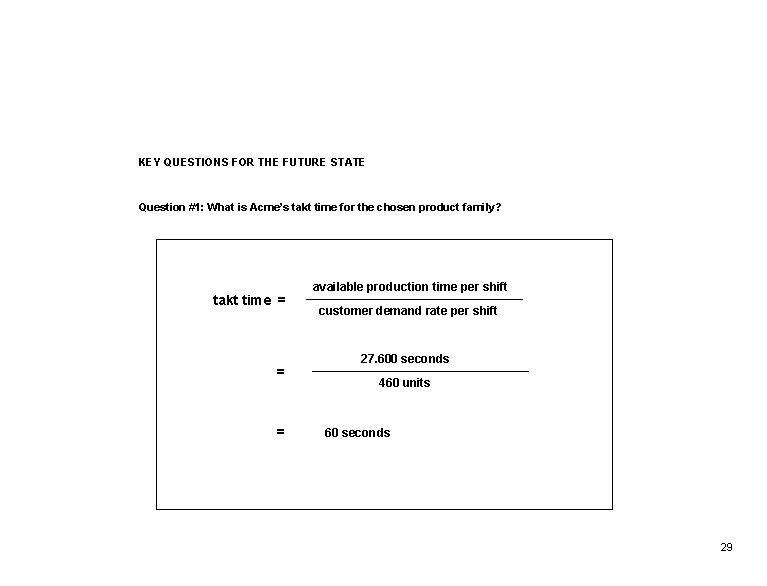
KEY QUESTIONS FOR THE FUTURE STATE Question #1: What is Acme’s takt time for the chosen product family? takt time = = = available production time per shift customer demand rate per shift 27. 600 seconds 460 units 60 seconds 29
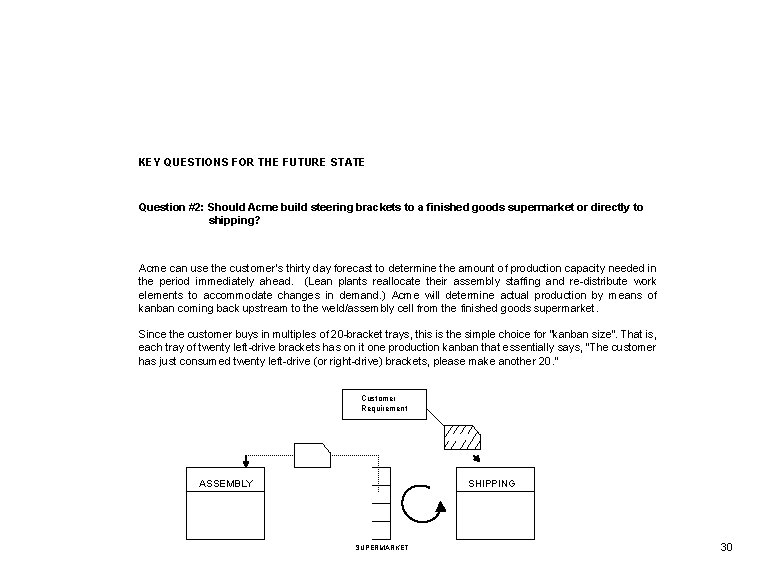
KEY QUESTIONS FOR THE FUTURE STATE Question #2: Should Acme build steering brackets to a finished goods supermarket or directly to shipping? Acme can use the customer’s thirty day forecast to determine the amount of production capacity needed in the period immediately ahead. (Lean plants reallocate their assembly staffing and re-distribute work elements to accommodate changes in demand. ) Acme will determine actual production by means of kanban coming back upstream to the weld/assembly cell from the finished goods supermarket. Since the customer buys in multiples of 20 -bracket trays, this is the simple choice for “kanban size”. That is, each tray of twenty left-drive brackets has on it one production kanban that essentially says, “The customer has just consumed twenty left-drive (or right-drive) brackets, please make another 20. ” Customer Requirement ASSEMBLY SHIPPING SUPERMARKET 30
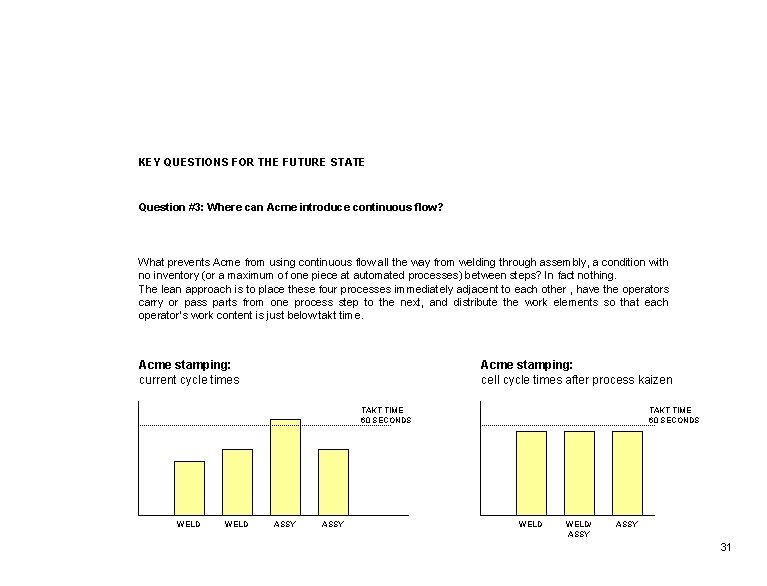
KEY QUESTIONS FOR THE FUTURE STATE Question #3: Where can Acme introduce continuous flow? What prevents Acme from using continuous flow all the way from welding through assembly, a condition with no inventory (or a maximum of one piece at automated processes) between steps? In fact nothing. The lean approach is to place these four processes immediately adjacent to each other , have the operators carry or pass parts from one process step to the next, and distribute the work elements so that each operator’s work content is just below takt time. Acme stamping: current cycle times Acme stamping: cell cycle times after process kaizen TAKT TIME 60 SECONDS WELD ASSY TAKT TIME 60 SECONDS WELD/ ASSY 31
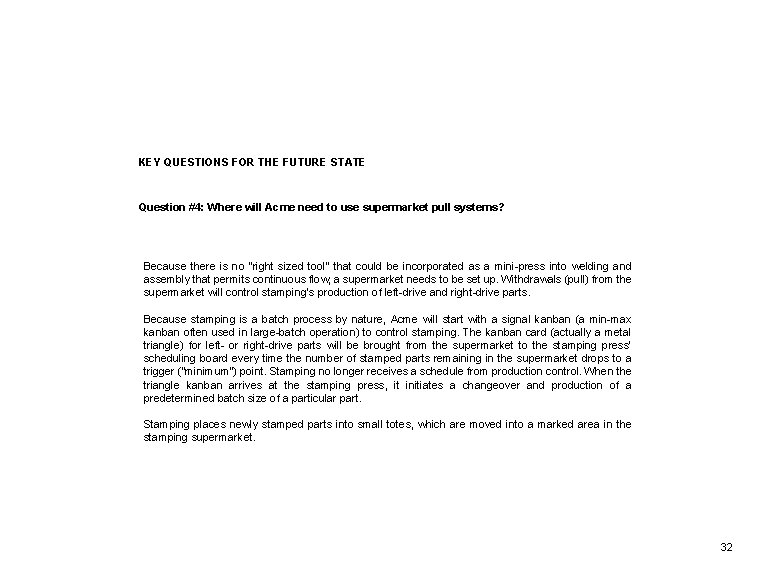
KEY QUESTIONS FOR THE FUTURE STATE Question #4: Where will Acme need to use supermarket pull systems? Because there is no “right sized tool” that could be incorporated as a mini-press into welding and assembly that permits continuous flow, a supermarket needs to be set up. Withdrawals (pull) from the supermarket will control stamping’s production of left-drive and right-drive parts. Because stamping is a batch process by nature, Acme will start with a signal kanban (a min-max kanban often used in large-batch operation) to control stamping. The kanban card (actually a metal triangle) for left- or right-drive parts will be brought from the supermarket to the stamping press’ scheduling board every time the number of stamped parts remaining in the supermarket drops to a trigger (“minimum”) point. Stamping no longer receives a schedule from production control. When the triangle kanban arrives at the stamping press, it initiates a changeover and production of a predetermined batch size of a particular part. Stamping places newly stamped parts into small totes, which are moved into a marked area in the stamping supermarket. 32
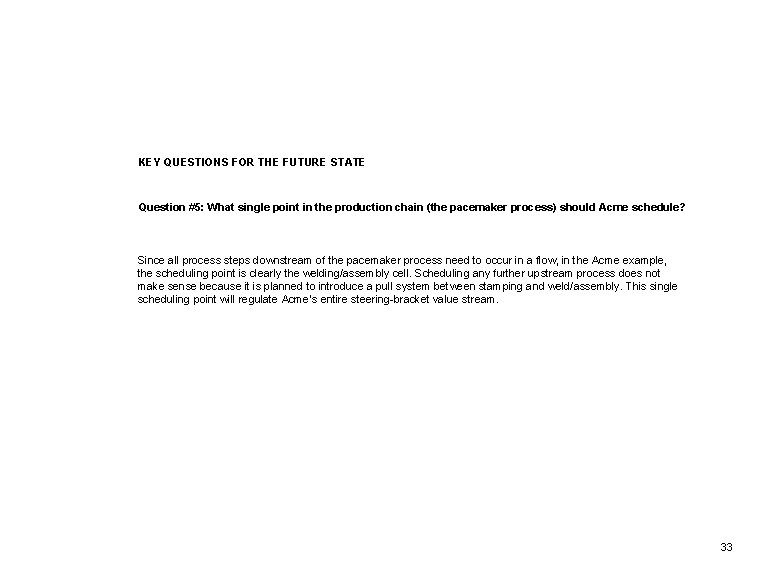
KEY QUESTIONS FOR THE FUTURE STATE Question #5: What single point in the production chain (the pacemaker process) should Acme schedule? Since all process steps downstream of the pacemaker process need to occur in a flow, in the Acme example, the scheduling point is clearly the welding/assembly cell. Scheduling any further upstream process does not make sense because it is planned to introduce a pull system between stamping and weld/assembly. This single scheduling point will regulate Acme’s entire steering-bracket value stream. 33
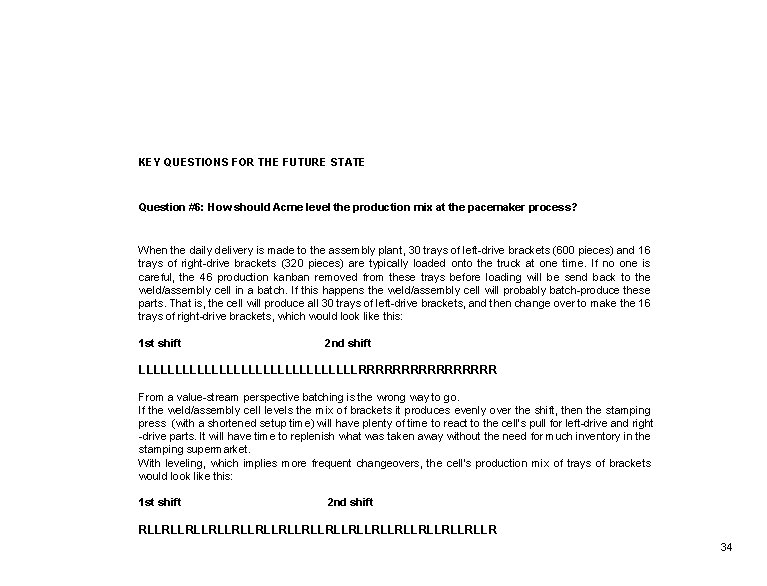
KEY QUESTIONS FOR THE FUTURE STATE Question #6: How should Acme level the production mix at the pacemaker process? When the daily delivery is made to the assembly plant, 30 trays of left-drive brackets (600 pieces) and 16 trays of right-drive brackets (320 pieces) are typically loaded onto the truck at one time. If no one is careful, the 46 production kanban removed from these trays before loading will be send back to the weld/assembly cell in a batch. If this happens the weld/assembly cell will probably batch-produce these parts. That is, the cell will produce all 30 trays of left-drive brackets, and then change over to make the 16 trays of right-drive brackets, which would look like this: 1 st shift 2 nd shift LLLLLLLLLLLLLLLRRRRRRRR From a value-stream perspective batching is the wrong way to go. If the weld/assembly cell levels the mix of brackets it produces evenly over the shift, then the stamping press (with a shortened setup time) will have plenty of time to react to the cell’s pull for left-drive and right -drive parts. It will have time to replenish what was taken away without the need for much inventory in the stamping supermarket. With leveling, which implies more frequent changeovers, the cell’s production mix of trays of brackets would look like this: 1 st shift 2 nd shift RLLRLLRLLRLLRLLRLLRLLRLLR 34
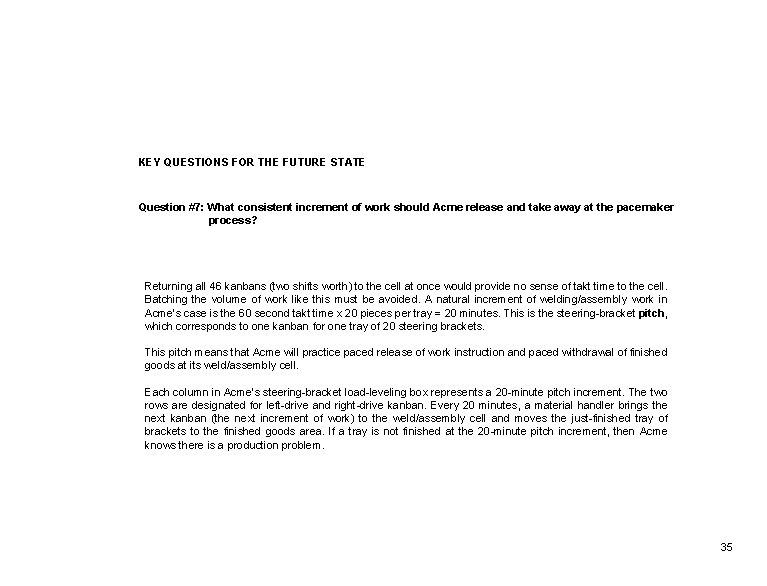
KEY QUESTIONS FOR THE FUTURE STATE Question #7: What consistent increment of work should Acme release and take away at the pacemaker process? Returning all 46 kanbans (two shifts worth) to the cell at once would provide no sense of takt time to the cell. Batching the volume of work like this must be avoided. A natural increment of welding/assembly work in Acme’s case is the 60 second takt time x 20 pieces per tray = 20 minutes. This is the steering-bracket pitch, which corresponds to one kanban for one tray of 20 steering brackets. This pitch means that Acme will practice paced release of work instruction and paced withdrawal of finished goods at its weld/assembly cell. Each column in Acme’s steering-bracket load-leveling box represents a 20 -minute pitch increment. The two rows are designated for left-drive and right-drive kanban. Every 20 minutes, a material handler brings the next kanban (the next increment of work) to the weld/assembly cell and moves the just-finished tray of brackets to the finished goods area. If a tray is not finished at the 20 -minute pitch increment, then Acme knows there is a production problem. 35
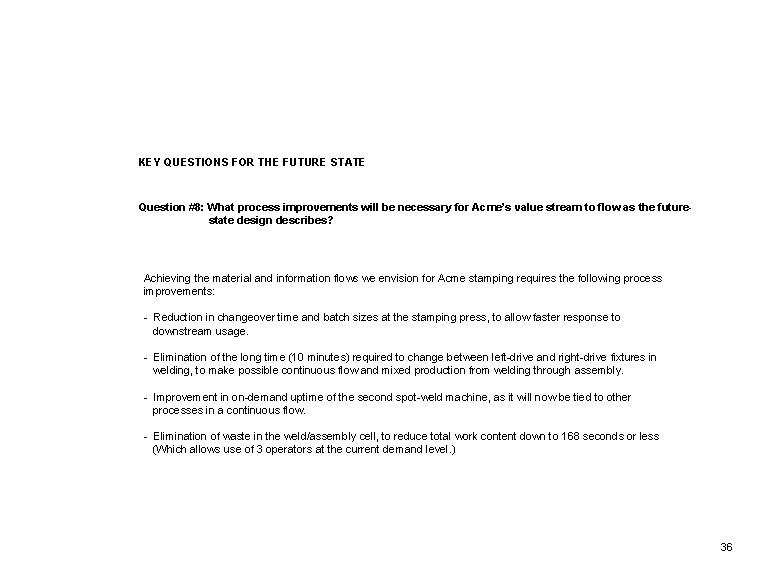
KEY QUESTIONS FOR THE FUTURE STATE Question #8: What process improvements will be necessary for Acme’s value stream to flow as the futurestate design describes? Achieving the material and information flows we envision for Acme stamping requires the following process improvements: - Reduction in changeover time and batch sizes at the stamping press, to allow faster response to downstream usage. - Elimination of the long time (10 minutes) required to change between left-drive and right-drive fixtures in welding, to make possible continuous flow and mixed production from welding through assembly. - Improvement in on-demand uptime of the second spot-weld machine, as it will now be tied to other processes in a continuous flow. - Elimination of waste in the weld/assembly cell, to reduce total work content down to 168 seconds or less (Which allows use of 3 operators at the current demand level. ) 36
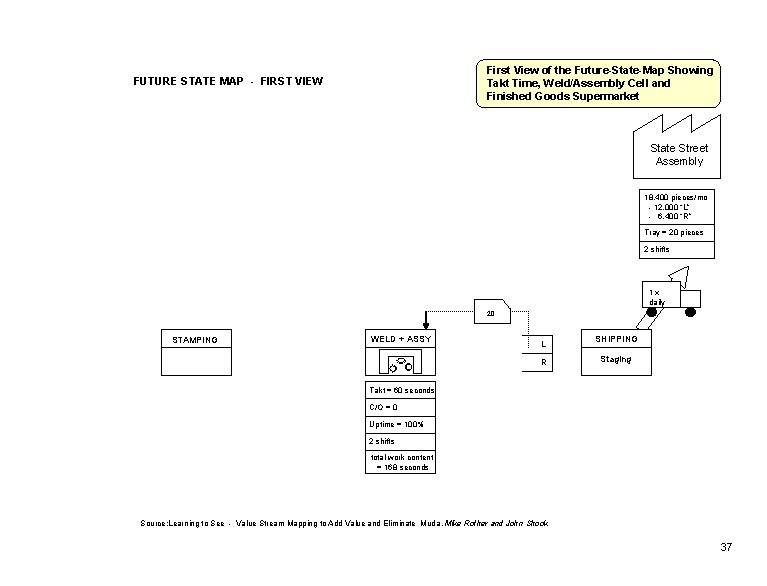
First View of the Future-State-Map Showing Takt Time, Weld/Assembly Cell and Finished Goods Supermarket FUTURE STATE MAP - FIRST VIEW State Street Assembly 18, 400 pieces/mo - 12, 000 “L” - 6, 400 “R” Tray = 20 pieces 2 shifts 1 x daily 20 STAMPING WELD + ASSY L R SHIPPING Staging Takt = 60 seconds C/O = 0 Uptime = 100% 2 shifts total work content = 168 seconds Source: Learning to See - Value Stream Mapping to Add Value and Eliminate Muda, Mike Rother and John Shook 37
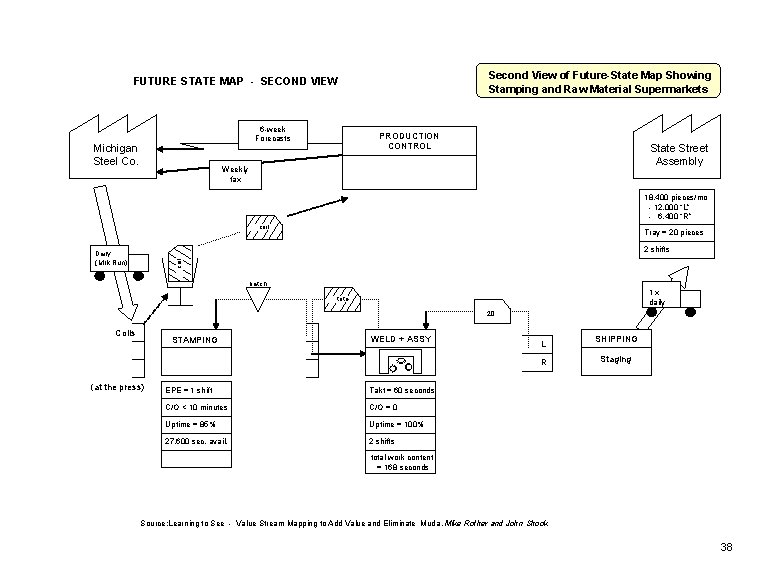
Second View of Future-State Map Showing Stamping and Raw Material Supermarkets FUTURE STATE MAP - SECOND VIEW 6 -week Forecasts Michigan Steel Co. PRODUCTION CONTROL State Street Assembly Weekly fax 18, 400 pieces/mo - 12, 000 “L” - 6, 400 “R” coil Tray = 20 pieces 2 shifts coil Daily (Milk Run) batch 1 x daily tote 20 Coils STAMPING WELD + ASSY L R (at the press) EPE = 1 shift Takt = 60 seconds C/O < 10 minutes C/O = 0 Uptime = 85% Uptime = 100% 27, 600 sec. avail. 2 shifts SHIPPING Staging total work content = 168 seconds Source: Learning to See - Value Stream Mapping to Add Value and Eliminate Muda, Mike Rother and John Shook 38
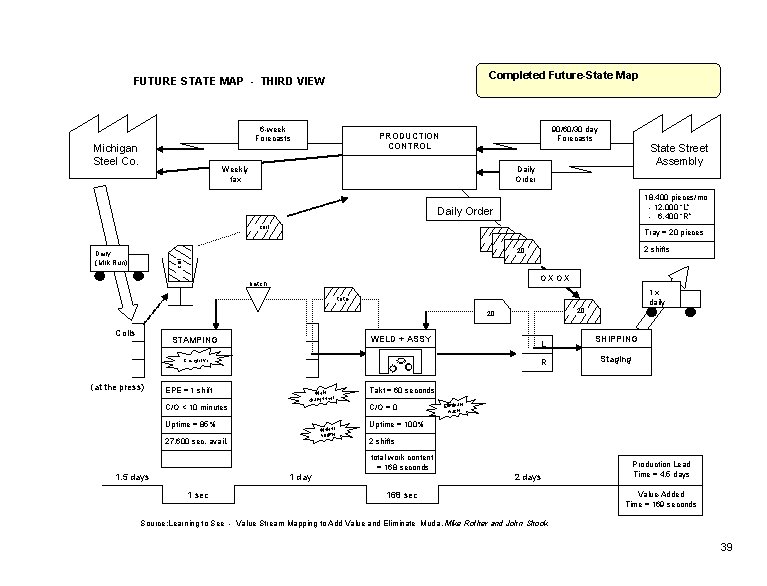
Completed Future-State Map FUTURE STATE MAP - THIRD VIEW 6 -week Forecasts Michigan Steel Co. 90/60/30 day Forecasts PRODUCTION CONTROL Weekly fax State Street Assembly Daily Order 18, 400 pieces/mo - 12, 000 “L” - 6, 400 “R” Daily Order coil Tray = 20 pieces 2 shifts 20 coil Daily (Milk Run) OXOX batch 1 x daily tote 20 20 Coils WELD + ASSY STAMPING L Changeover (at the press) EPE = 1 shift C/O < 10 minutes R Weld er changeov Uptime = 85% Welder uptime 27, 600 sec. avail. C/O = 0 Eliminate waste Uptime = 100% 2 shifts 1 day 1 sec Staging Takt = 60 seconds total work content = 168 seconds 1. 5 days SHIPPING 2 days 168 sec Production Lead Time = 4. 5 days Value-Added Time = 169 seconds Source: Learning to See - Value Stream Mapping to Add Value and Eliminate Muda, Mike Rother and John Shook 39
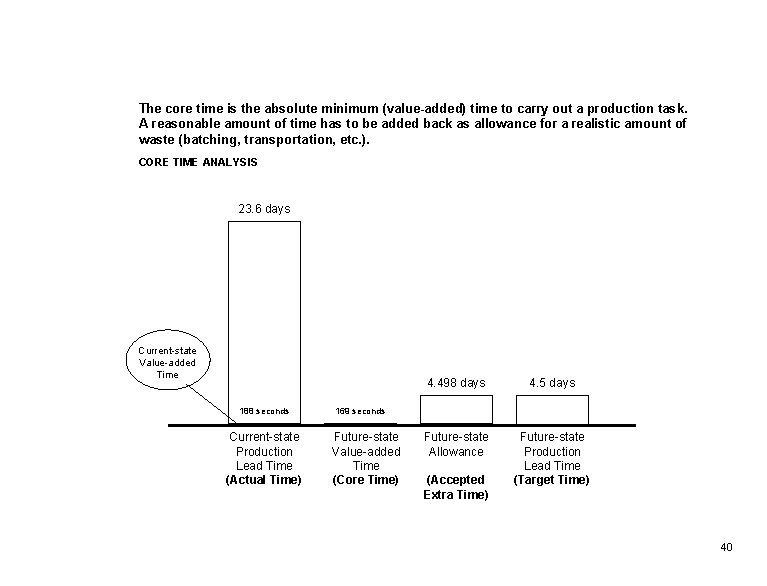
The core time is the absolute minimum (value-added) time to carry out a production task. A reasonable amount of time has to be added back as allowance for a realistic amount of waste (batching, transportation, etc. ). CORE TIME ANALYSIS 23. 6 days Current-state Value-added Time 188 seconds Current-state Production Lead Time (Actual Time) 4. 498 days 4. 5 days Future-state Allowance Future-state Production Lead Time (Target Time) 169 seconds Future-state Value-added Time (Core Time) (Accepted Extra Time) 40
- Slides: 41