Computer Simulation of elastomeric PolymerbyDesign to Protect the
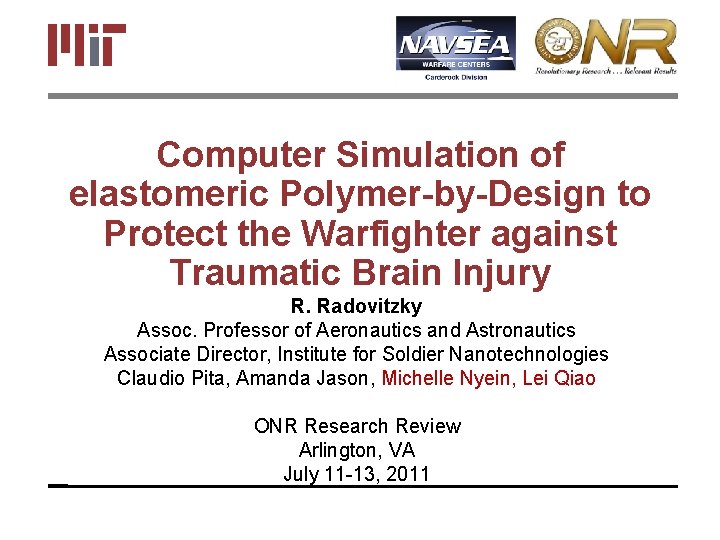
Computer Simulation of elastomeric Polymer-by-Design to Protect the Warfighter against Traumatic Brain Injury R. Radovitzky Assoc. Professor of Aeronautics and Astronautics Associate Director, Institute for Soldier Nanotechnologies Claudio Pita, Amanda Jason, Michelle Nyein, Lei Qiao ONR Research Review Arlington, VA July 11 -13, 2011

Computer Simulation of Elastomeric Polymer-by-Design to Protect the Warfighter against Traumatic Brain Injury S&T OBJECTIVES Support polymer-by-design approach to TBI mitigation via advanced simulation Computationally explore improvements in blast mitigation characteristics of head protection systems APPROACH Biofidelic models of human head incorporating existing and modified protection equipment (ACH) Polymer-by-design constitutive model integration in MIT HPC codes (with UCSD & NWU) Model Validation (Carderock blast tests) Performance evaluation of blast TBI mitigation concepts exploiting polymer-bydesign Results/ Impact/ Readiness Significant progress validating coupled models against Carderock blast tests Completed integration of UCSD PU model into MIT HPC code. Preliminary exploration of mitigation performance sensitivity to polymer properties

A multidisciplinary approach to better understand protect against blast-induced Traumatic Brain Injury R. Radovitzky Assoc. Professor of Aeronautics and Astronautics Associate Director, MIT Institute for Soldier Nanotechnologies Briefing to SASC September 27, 2010

(Towards) High-fidelity simulation of blast effects on humans R. Radovitzky Department of Aeronautics and Astronautics Massachusetts Institute of Technology Cambridge, MA Collaborators: L. Noels, S. Socrate (MIT) Presented at: DSRC Blast Injury Mitigation Workshop Arlington, VA April 14 th, 2005


Objectives of MIT effort • Assist Polymer-by-design approach by transitioning modeling tools developed under JIEDDO Program for Blast-Induced TBI – Simulate coupled full-physics of blast event impacting human head – Assess mitigation performance of existing protection (ACH, ECH) and emerging concepts from this program – Propose optimization approaches • Further validate models • Explore blast mitigation strategies

Approach • Integrate Polymer-by-design multiscale models developed by other member teams into MIT coupled fluid-structure interaction code • Develop computational model of head dummy in collaboration with Carderock • Conduct large-scale simulations informed with polymer models of real blast tests conducted at Carderock • Compare simulations with experiments • Conduct fully coupled three-dimensional end-to-end simulations of integrated PPE and biofidelic head model subject to blast conditions to assess performance of existing and new protection concept • Provide feedback to constitutive model developers • Propose optimizations of structural (geometric) and mechanical properties of polymers-by-design

Integration of UCSD PU model Strong collaboration with A. Amirkhizi, S. Nemat. Nasser

Summary of equations Shear Bulk Dissipation and Temperature

Uniaxial strain wave propagation: Vp=100 m/s

Simplified model • Volumetric response: – Clifton EOS: – Linear viscous term • Deviatoric response – Constant shear modulus – Linear viscous term

Uniaxial strain wave propagation: Vp=100 m/s, simplified model

Comparison UCSD and simplified PU model

Validation against Carderock blast tests Strong collaboration with Phil Dudt, Roshdy Barsoum

Model validation against Carderock Dummy Blast Tests (Barsoum, Dudt) Polyethylene Skull with pressure gages and accelerometers Bare head Sylgard Gel Brain Flexible “Neck” Head + ACH Silicon Polymer “Flesh” Head + ACH + Polymer

Close and internal Pressure sensor locations

Experimental findings • Side blast: 1/8 lb explosive, 3. 5 ft standoff For side blast, the ACH noticeably reduces intracranial stresses

MIT/DVBIC Full Head Model with ACH

Model Modifications for validation tests: • 3 differentiated materials: § Gel replacing CSF, eyes, venous cavities, ventricles, GM, WM, glia, and sinus cavities § Skin + fat + muscle § Skull • ACH: Kevlar shell + standard padding geometry • Outer layer of Polyurea • Coarsest model: 900 K elements

Constitutive Models for Tissue surrogates, helmet, foam pads • Volumetric Response: • Mie-Gruneisen/Hugoniot equation of state (Skull) • Tait equation of state for remaining soft materials– (cranium cavity gel, outer silicon layer) • Deviatoric Response: • Neohookean model extended to compressible range

Material Properties Structure (kg/m^3) K(Pa) G(Pa) B 0 Gel 890 2. 19 e 9 3. 5 e 4 - 3. 5 e 5 3. 063 e 8 6. 15 Skin/Fat/Mu scle 1100 3. 47 e 7 5. 88 e 6 4. 866 e 6 6. 15 Structure (kg/m 3) K(Pa) G(Pa) C 0 S Skull 1412 6. 5 e 9 2. 66 e 8 0. 22 1. 85 e 3 0. 94 Structure (kg/m 3) E(Pa) Helmet 1440 1. 24 e 9 0. 22 Padding 61. 3 8. 44 e 6 0. 2 Polyurea 1200 66. 69 e 6 0. 485 Replaced with Improved models

Simulation setup

Simulations of Carderock tests Unprotected Head • Approximate geometry: MIT/DVBIC FHM different from Carderock dummies • Approximaterial properties for tissue simulants: Sylgard gel (brain tissue), polyethylene (skull bone) • PU approximate properties/model Head with ACH + PU layer

Comparison: Free-field pressure histories for different stand-offs

Detailed comparison of simulation and experiment (3. 5 ft stand-off test)

Effect of PU layer Strong collaboration with Phil Dudt, Roshdy Barsoum

Comparison of Simulation and Experiment (3. 5 ft standoff) 27

Comparison ACH vs ACH+PU layer

Effect of external PU layer vs. unprotected head and head+ACH

Effect of PU layer, dissipation:

Head Model + Protective Devices 31

ECH vs. ACH helmets comparison • Data from Team Wendy – Pad and shell properties – Pad Geometry (CAD) • ACH geometry for both helmets – ECH thicker shell • 3. 16 gr of TNT at 0. 12 m standoff • front blast

ECH vs. ACH helmets comparison

Simulations with human head and ACH, faceshield, and goggles • 3. 16 g TNT at 0. 12 m, producing an incident overpressure of 10 atm 34

Simulations with human head and ACH, faceshield, and goggles 35

Head Model + Protective Devices Mtek Design, LLC 36

Visible Human Project (VHP) Model • Segmented axial anatomical images from the Visible Human Project male • 10 differentiated structures: gray matter, white matter, CSF, bone, cerebellum, brainstem, ventricles, eyes, sinus, skin/fat/muscle • Partially segmented torso to create extended mesh • Includes heart and lungs as distinct materials 37

Towards a full human model • Investigate alternative load transmission pathways: e. g. Cernak’s “vasculature surge” hypothesis • Provide platform for analysis of polytrauma • Model built from Visual Human Project dataset • Simplified model accounts for major vessels and homogenized tissue • Preliminary analysis indicates surge unlikely

Thank you

Computational framework: • Lagrangian solid formulation ideal for: – – – Large deformations Tracking of material interfaces Materials with history: plasticity, fracture Unstructured mesh, finite element approach Mesh healing and optimization (Heal. Mesh): eliminate mesh distortion • Eulerian fluid formulation: – Well-established shock capturing and advection schemes • Structured grid, finite volume approach • Automatic Mesh Refinement: capture pressure/density gradients/boundary geometry • FSI coupled approach: Virtual Test Facility : – Based on ghost-fluid method/level sets – Coupling enforced at every fluid time step RR et al, 1998, 2001, Cirak/RR, 2005 Deiterding et al, 2006

Do. D Taxonomy of Blast Injuries Secondary Tertiary Primary Tertiary Quaternary Quintic Primary: shock overpressure. Causes internal injury, unique to blast. Secondary: fragments, debris. Causes Blunt or penetrating trauma. Tertiary: acceleration due to wind. Causes blunt injury similar to car accidents Quaternary: explosion products (toxic gases, fire, EM fields). Causes inhalation injury, burns, blindness, … Quintic: contaminants (bacteria, radiation), Causes post-event clinical consequences Do. D Annual Report to Congress, Prevention, Mitigation and Treatment of Blast Injuries, 2008

Improved blast models • • Avoid the need to model the detonation process while accurately describe blast waves. Arbitrary blast strength, accounts for ambient conditions Initial condition to CFD calculation Generalized Ohkosimskii method – Point source model for planar, cylindrical and spherical symmetries – Convert the resulting onedimensional conservation laws into characteristic form – Discretize the characteristic equations using finite difference method T. Bui, RR, 2009 Peak incident overpressure vs. scaled distance Against other models and experiments Peak incident underpressure Against experiments only

Biofidelic models: • Hierarchical set of models of increasing biofidelity: – Engineering vs medical relevance • FHM Example: 11 differentiated tissues and anatomical structures + ACH shell and pads(NSRDEC, PEO Soldier), Millions of dofs,
- Slides: 43