Chapter 9 Question 2 Anisha Patel The management
![Chapter 9 Question 2 [Anisha Patel] The management of Hartman Company is trying to Chapter 9 Question 2 [Anisha Patel] The management of Hartman Company is trying to](https://slidetodoc.com/presentation_image/3f3716091b7a8fc8f9eb8cb599517955/image-1.jpg)
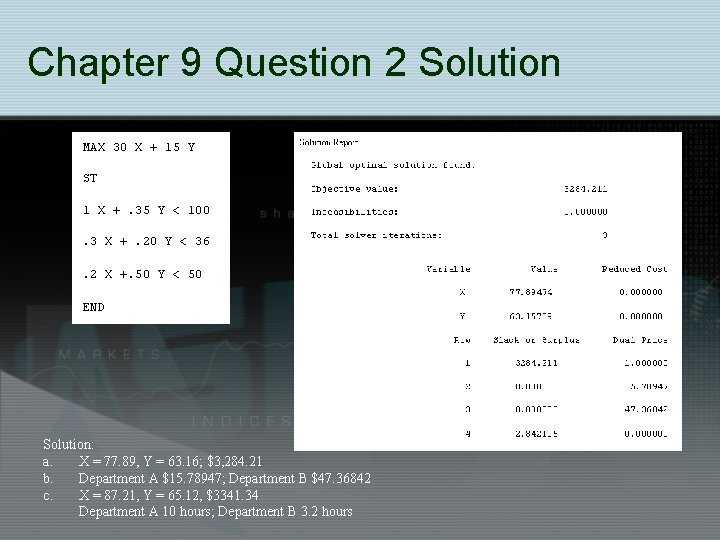
![Chapter 9 Question 17 [Anisha Patel] 2. Frandec Corporation manufactures, assembles, and rebuilds material Chapter 9 Question 17 [Anisha Patel] 2. Frandec Corporation manufactures, assembles, and rebuilds material](https://slidetodoc.com/presentation_image/3f3716091b7a8fc8f9eb8cb599517955/image-3.jpg)
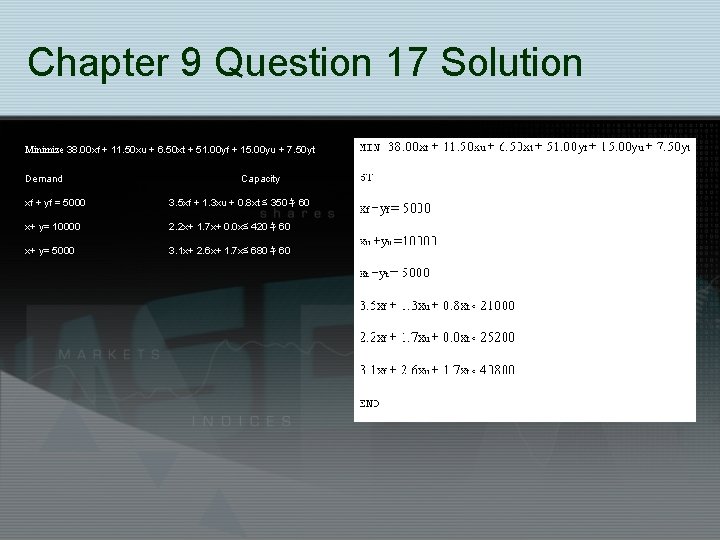
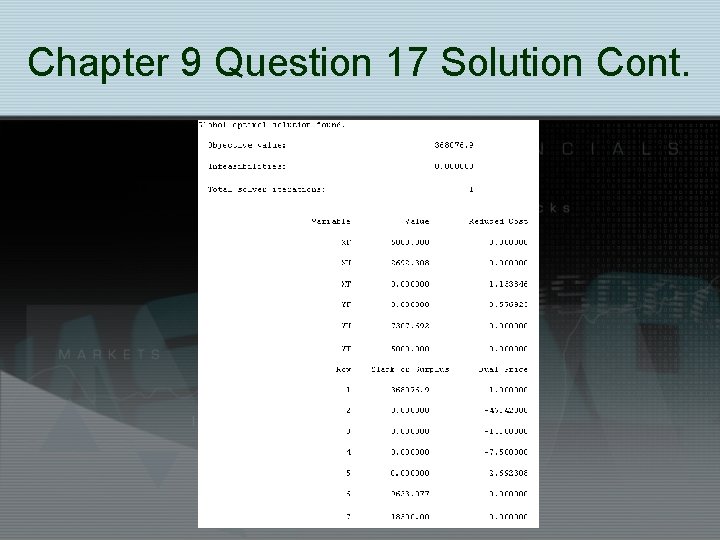
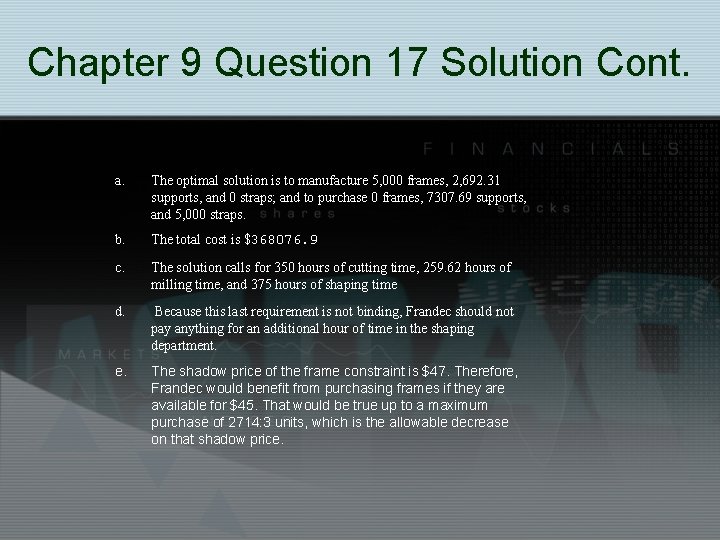
- Slides: 6
![Chapter 9 Question 2 Anisha Patel The management of Hartman Company is trying to Chapter 9 Question 2 [Anisha Patel] The management of Hartman Company is trying to](https://slidetodoc.com/presentation_image/3f3716091b7a8fc8f9eb8cb599517955/image-1.jpg)
Chapter 9 Question 2 [Anisha Patel] The management of Hartman Company is trying to determine the amount of each of two products to produce over the coming planning period. The following information concerns labor availability, labor utility, and product profitability. Product (hours/unit) Department 1 2 Labour-Hours Available A 1. 00 0. 35 100 B 0. 30 0. 20 36 C 0. 20 0. 50 50 Profit contribution/unit $30. 00 $15. 00 a. b. c. Develop a linear programming model of the Hartman Company problem. Solve the model to determine the optimal production quantities of products 1 and 2. In computing the profit contribution per unit, management doesn’t deduct labor costs because they are considered fixed for the upcoming planning period. However, suppose that overtime can be scheduled in some of the departments. Which departments would you recommend scheduling for overtime? How much would you be willing to pay per hour of overtime in ach department? Suppose that 10, 6, and 8 hours if overtime may be scheduled in departments A, B, and C, respectively. The cost per hour of overtime is $18 in department A, $22. 50 in department B, and $12 in department C. Formulate a linear programming model that can be used to determine the optimal production quantities if overtime is made available. What are the optimal production quantities, and what is the revised total contribution to profit? How much overtime do you recommend using in each department? What is the increase in the total contribution to profit if overtime is used?
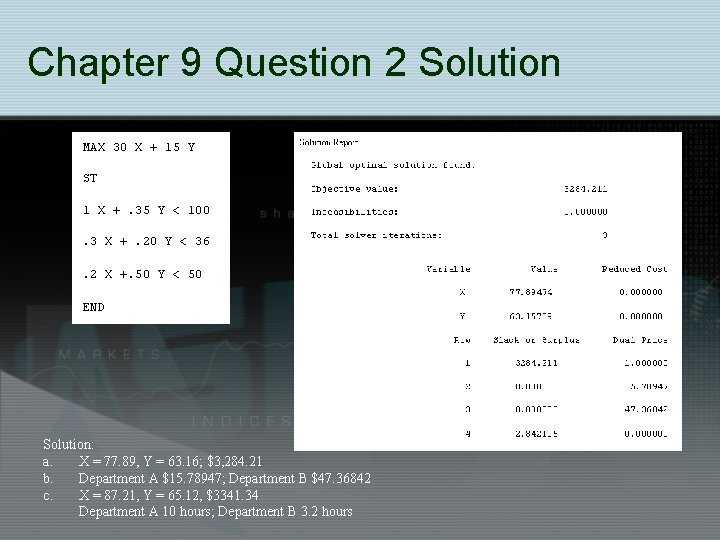
Chapter 9 Question 2 Solution: a. X = 77. 89, Y = 63. 16; $3, 284. 21 b. Department A $15. 78947; Department B $47. 36842 c. X = 87. 21, Y = 65. 12, $3341. 34 Department A 10 hours; Department B 3. 2 hours
![Chapter 9 Question 17 Anisha Patel 2 Frandec Corporation manufactures assembles and rebuilds material Chapter 9 Question 17 [Anisha Patel] 2. Frandec Corporation manufactures, assembles, and rebuilds material](https://slidetodoc.com/presentation_image/3f3716091b7a8fc8f9eb8cb599517955/image-3.jpg)
Chapter 9 Question 17 [Anisha Patel] 2. Frandec Corporation manufactures, assembles, and rebuilds material handling equipment used in warehouses and distribution centers. One product, called a Liftmaster, is assembled from four components: a frame, a motor, two supports, and a metal strap. Frandec’s production schedule calls for 5, 000 Liftmasters to be made next month. Frandec purchases the motors from an outside supplier, but the frames, supports, and straps may either be manufactured by the company or purchased from an outside supplier. Manufacturing and purchase costs per unit are shown. Component Frame Support Strap Manufacturing Cost $38. 00 $11. 50 $6. 50 Purchase Cost $51. 00 $15. 00 $7. 50 Three departments are involved in the production of these components. The time (in minutes per unit) required to process each component in each department and the available capacity (in hours) for the three departments are as follows: Component Frame Support Strap Capacity (hours) Department Cutting 3. 5 1. 3 0. 8 350 Milling 2. 2 1. 7 0. 0 420 Shaping 3. 1 2. 6 1. 7 680 a. Formulate and solve a linear programming model for this make-or-buy application. How many of each component should be manufactured and how many should be purchased? b. What is the total cost of the manufacturing and purchasing plan? c. How many hours of production time are used in each department? d. How much should Frandec be willing to pay for an additional hour of time in the shaping department? e. Another manufacturer has o� ered to sell frames to Frandec for $45. 00 per unit. Could Frandec improve its position by pursuing this opportunity? Why or why not?
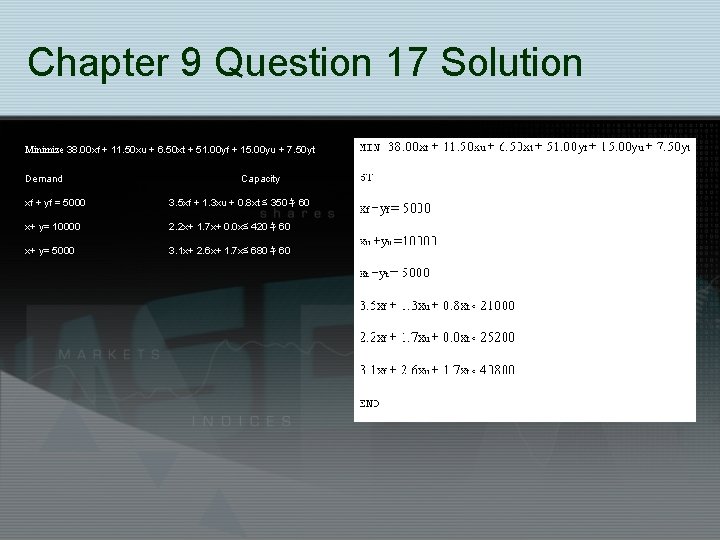
Chapter 9 Question 17 Solution Minimize 38. 00 xf + 11. 50 xu + 6. 50 xt + 51. 00 yf + 15. 00 yu + 7. 50 yt Demand Capacity xf + yf = 5000 3. 5 xf + 1. 3 xu + 0. 8 xt ≤ 350 キ 60 x+ y= 10000 2. 2 x+ 1. 7 x+ 0. 0 x≤ 420 キ 60 x+ y= 5000 3. 1 x+ 2. 6 x+ 1. 7 x≤ 680 キ 60
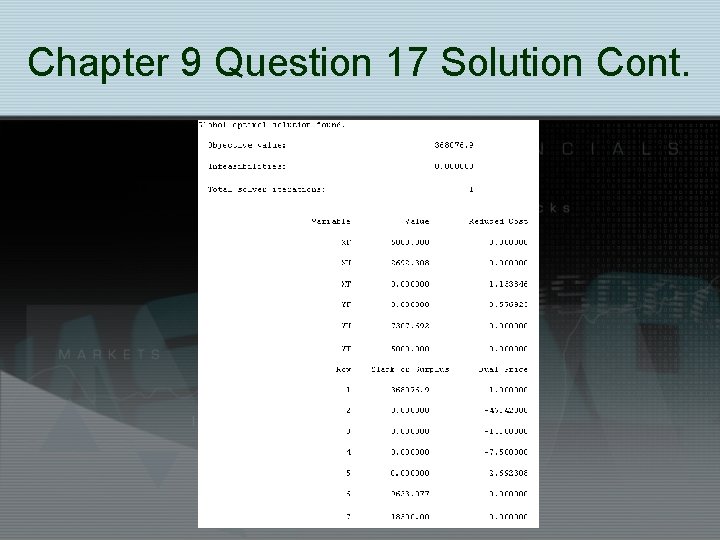
Chapter 9 Question 17 Solution Cont.
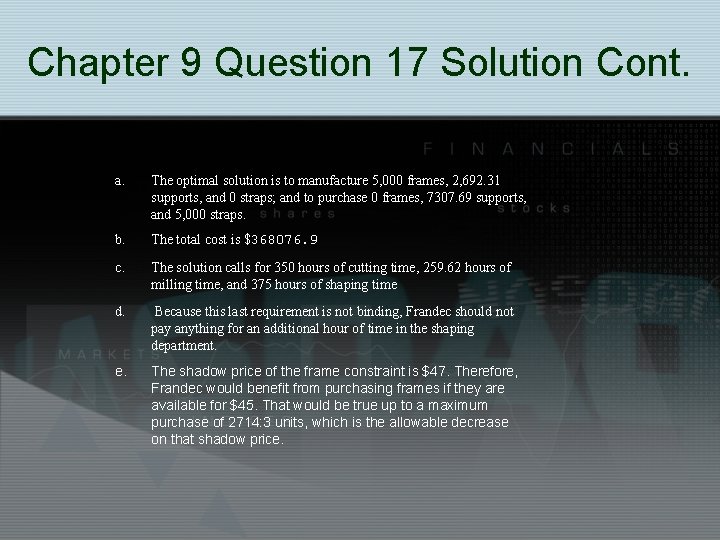
Chapter 9 Question 17 Solution Cont. a. The optimal solution is to manufacture 5, 000 frames, 2, 692. 31 supports, and 0 straps; and to purchase 0 frames, 7307. 69 supports, and 5, 000 straps. b. The total cost is $368076. 9 c. The solution calls for 350 hours of cutting time, 259. 62 hours of milling time, and 375 hours of shaping time d. Because this last requirement is not binding, Frandec should not pay anything for an additional hour of time in the shaping department. e. The shadow price of the frame constraint is $47. Therefore, Frandec would benefit from purchasing frames if they are available for $45. That would be true up to a maximum purchase of 2714: 3 units, which is the allowable decrease on that shadow price.