Chapter 4 METAL CASTING PROCESSES The automation of

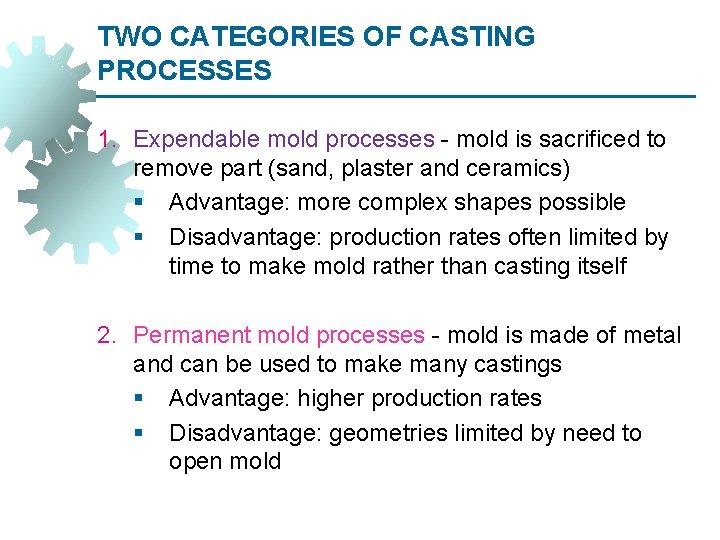
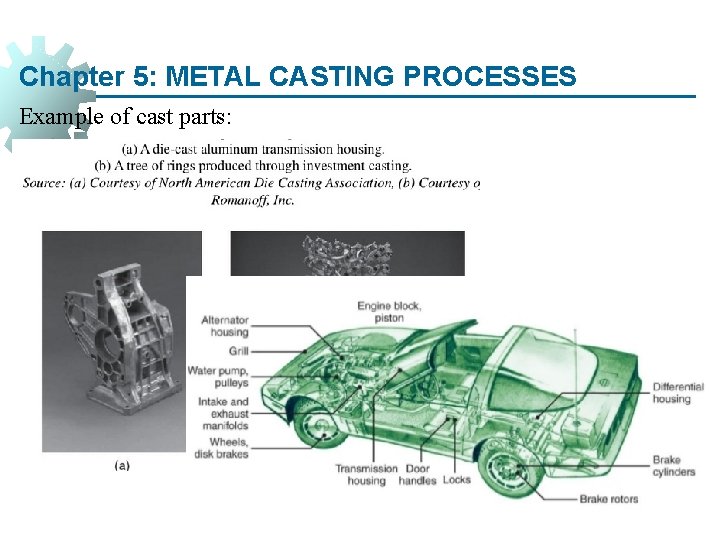
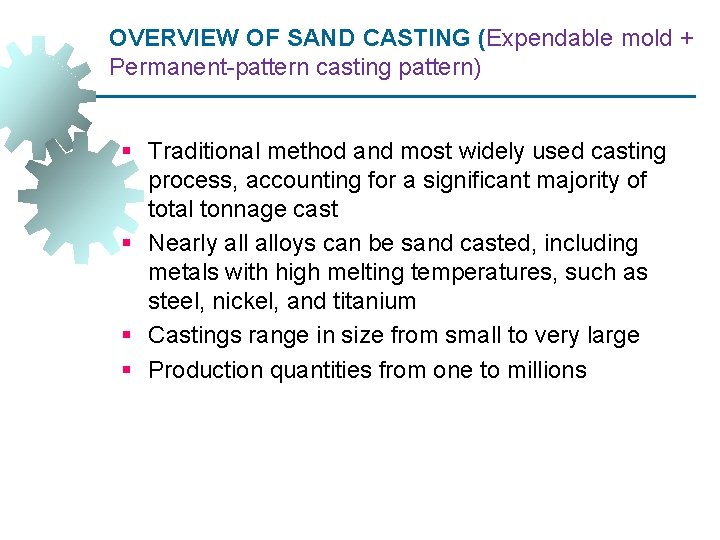
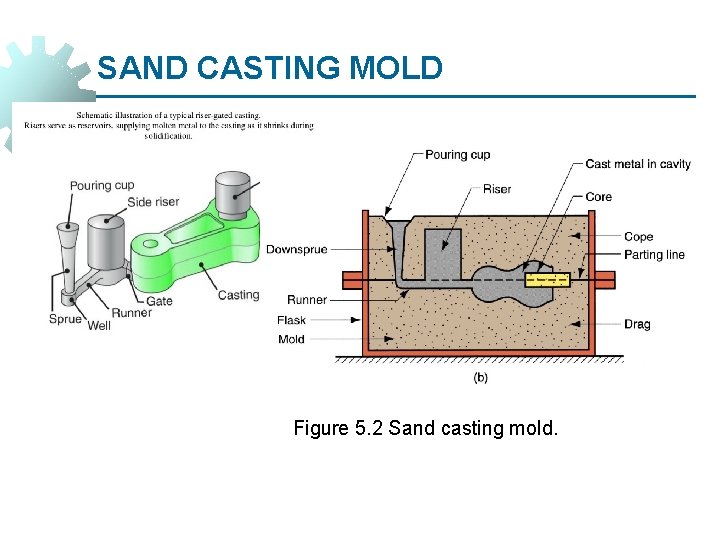
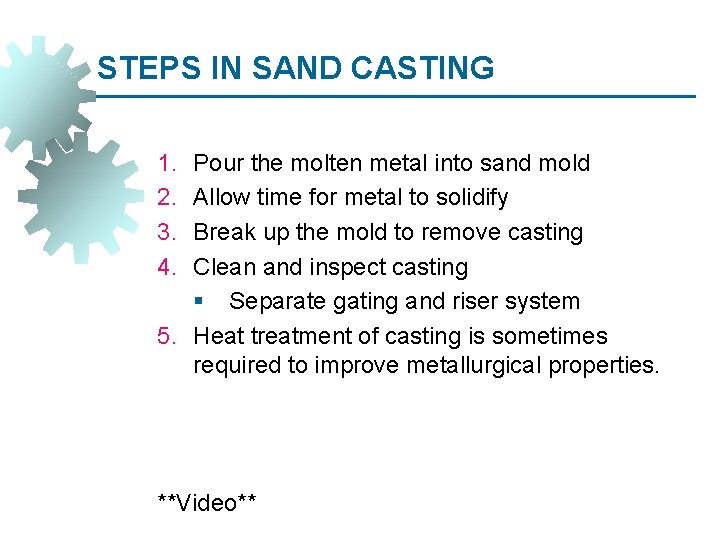
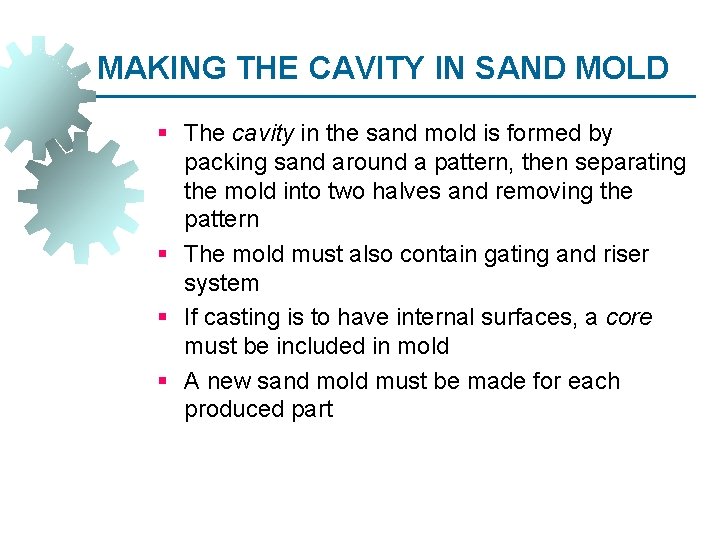
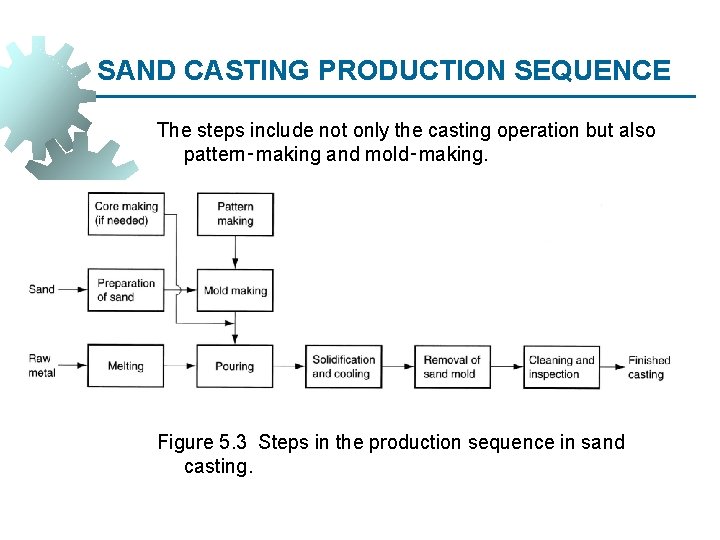
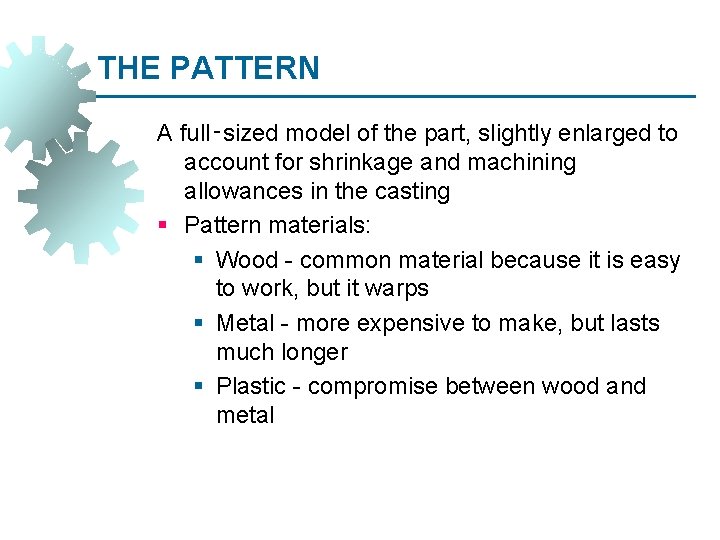
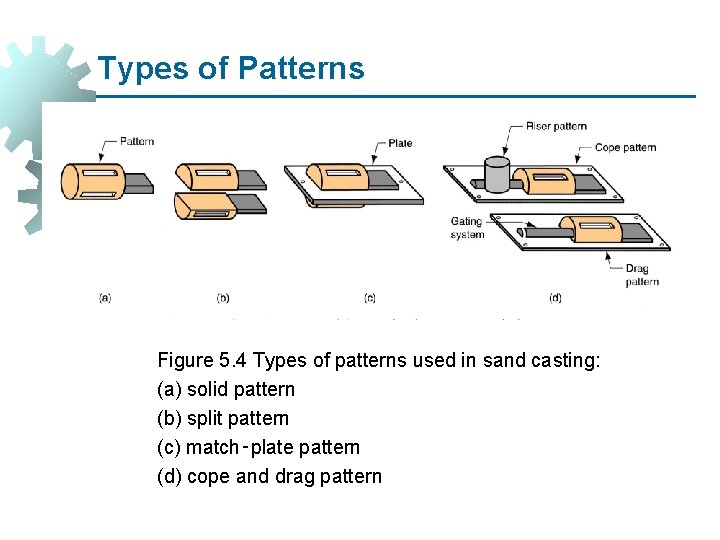
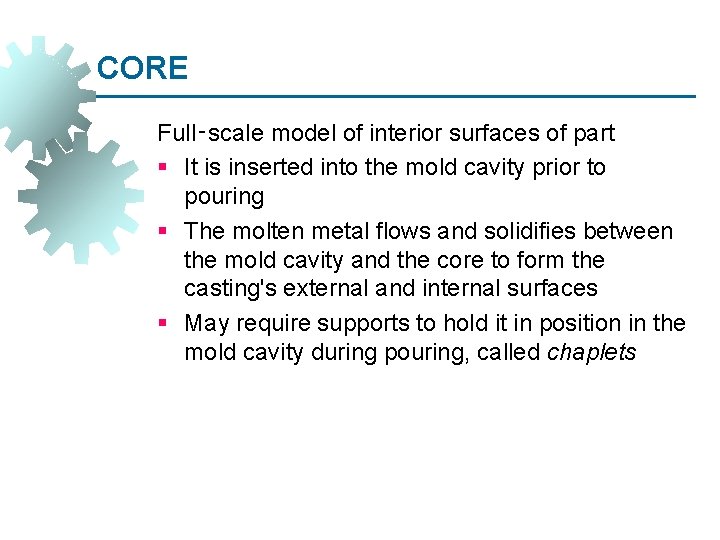
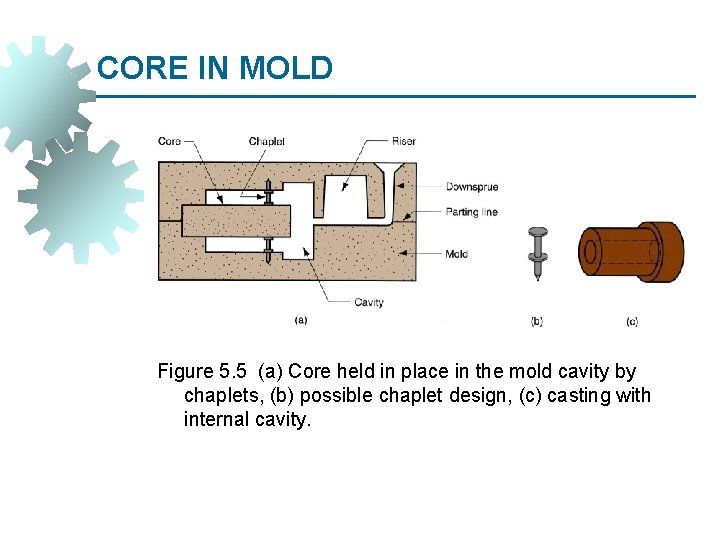
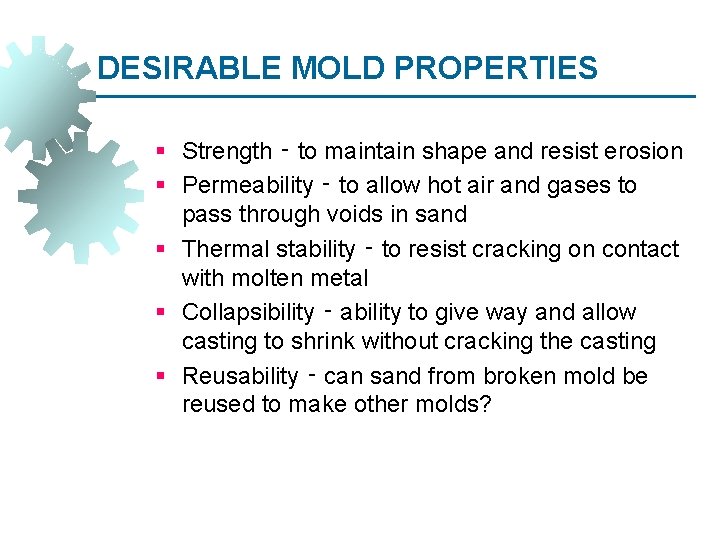
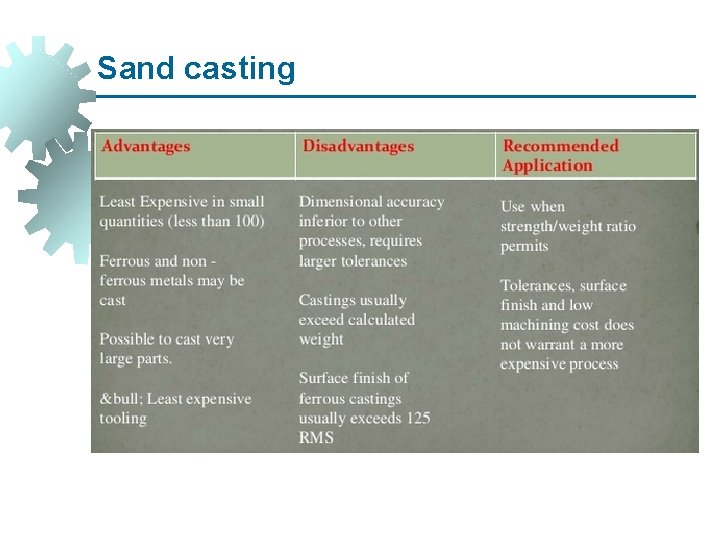
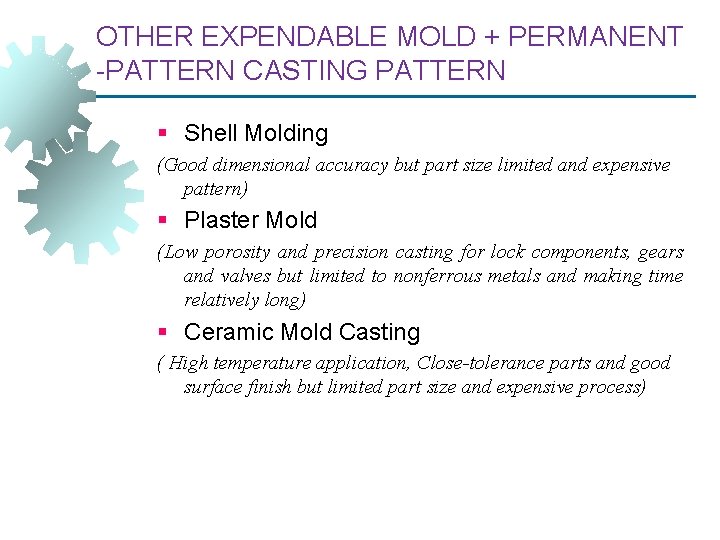
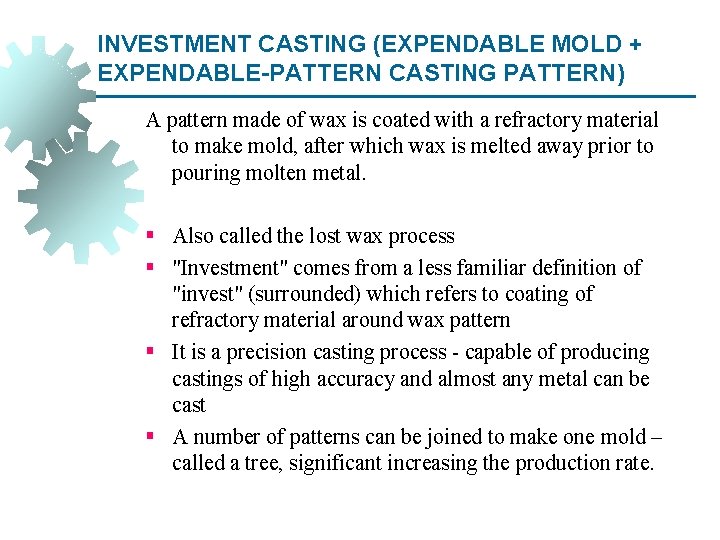
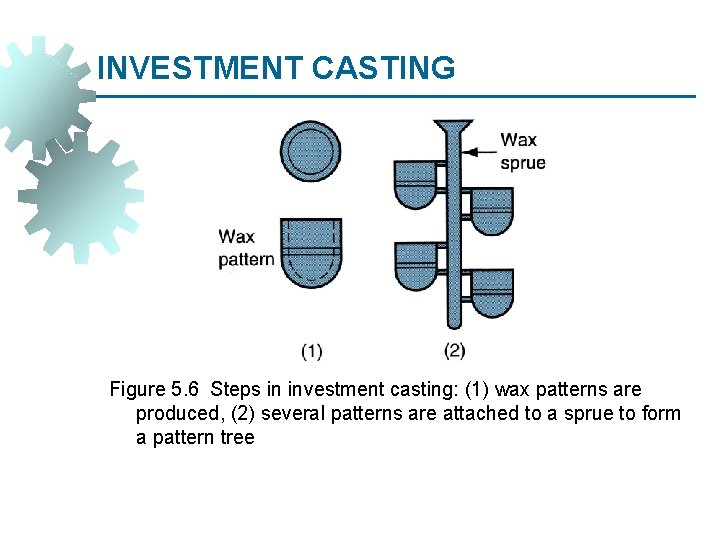
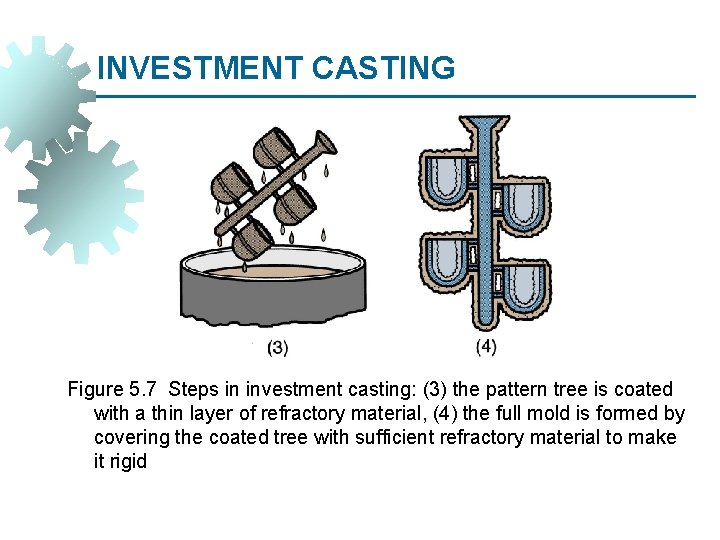
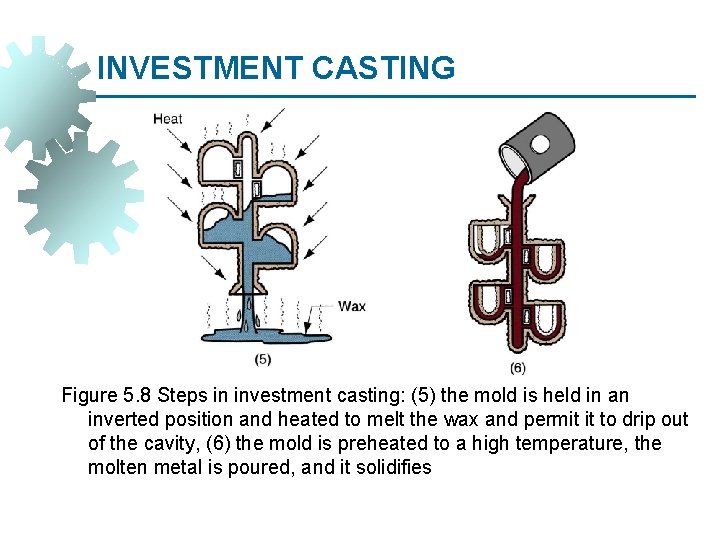
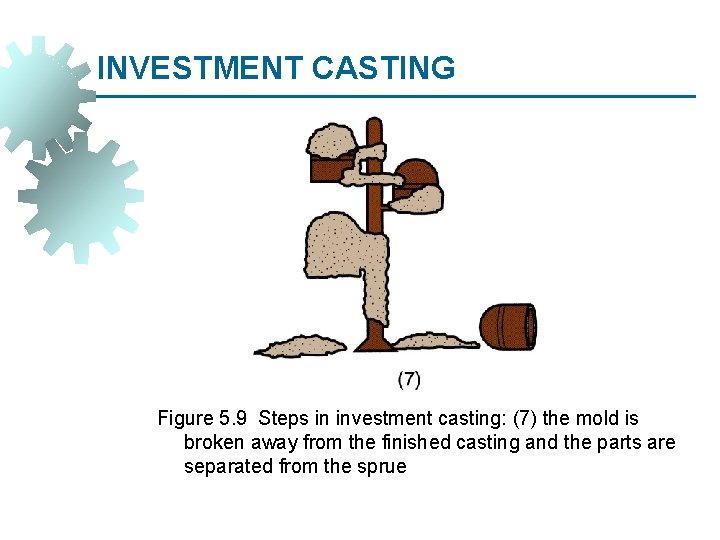
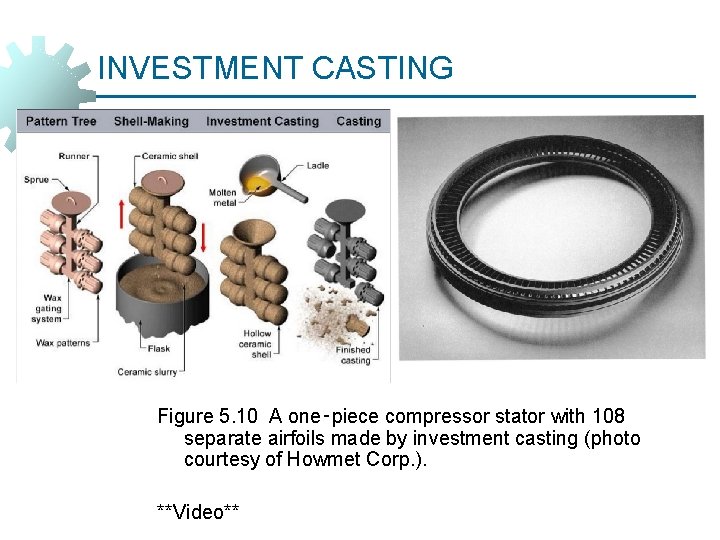
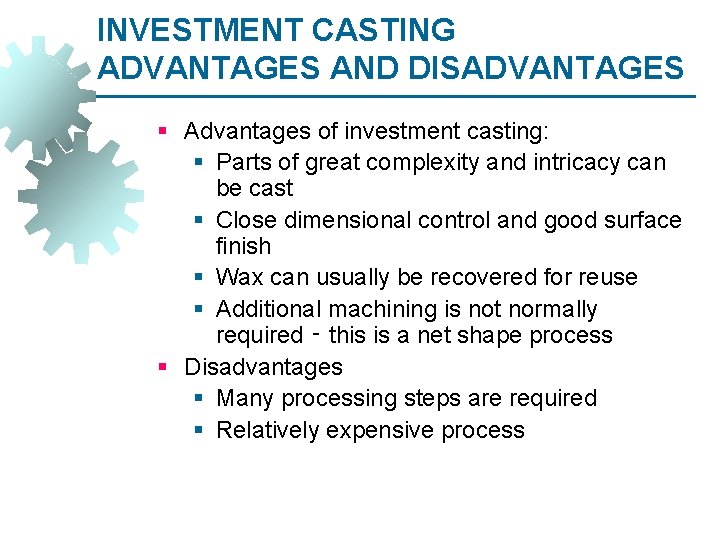
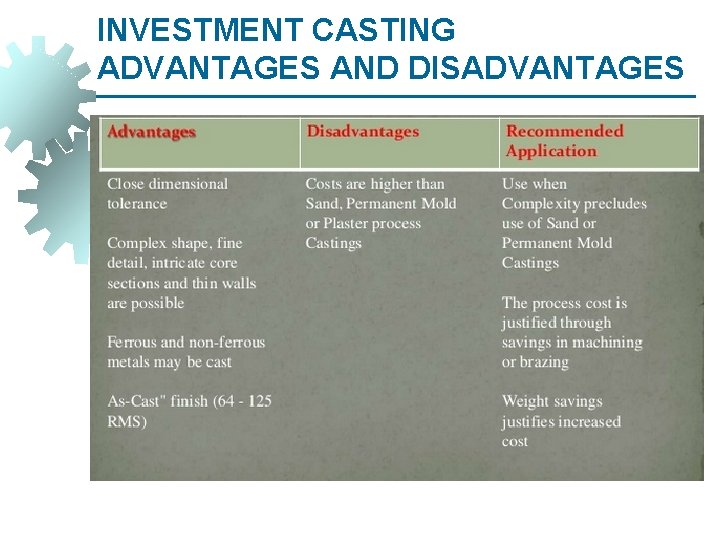
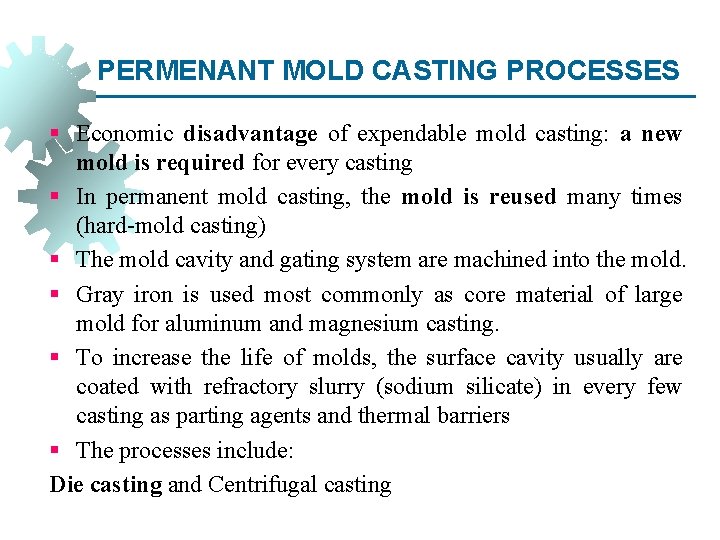
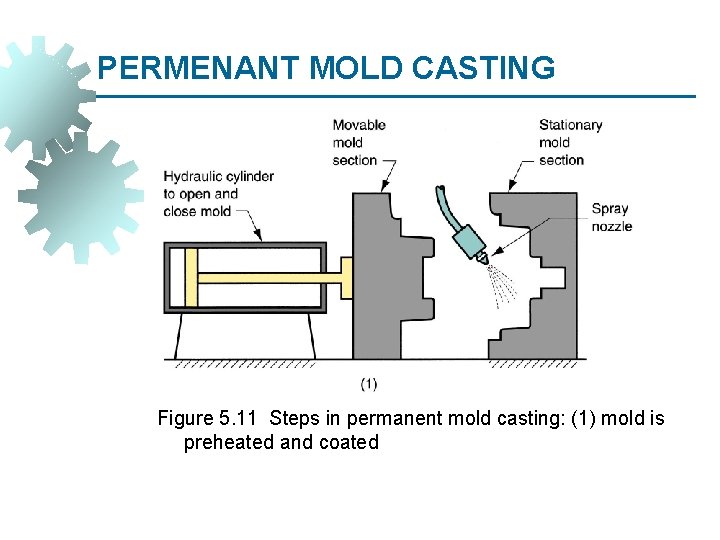
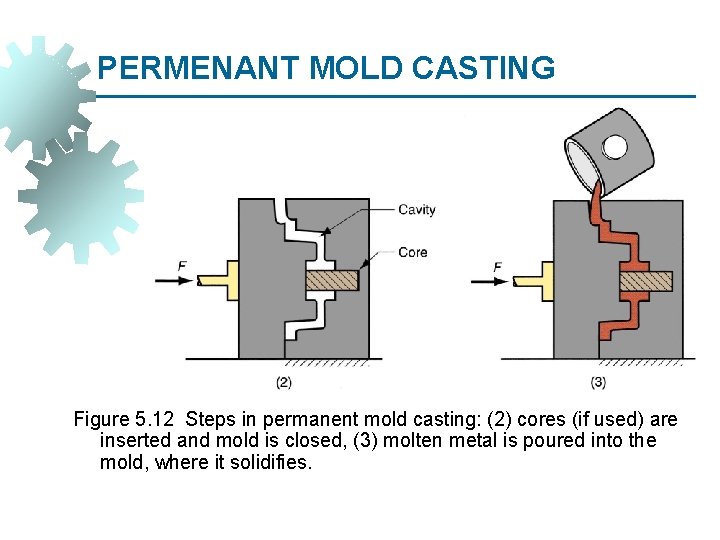
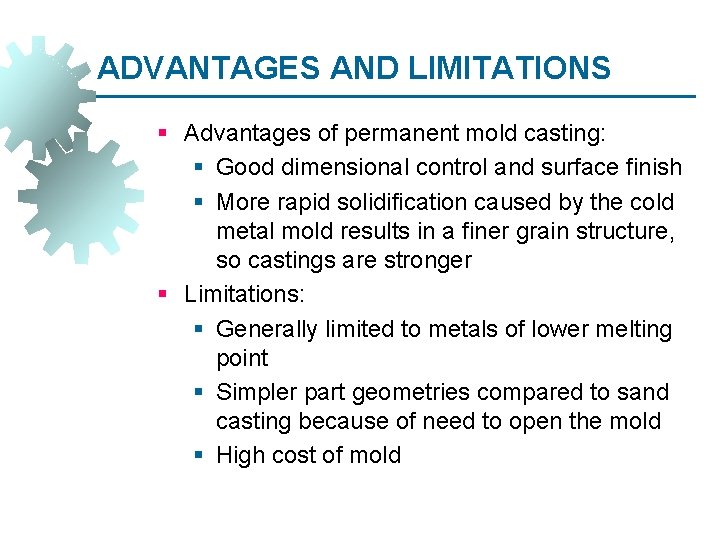
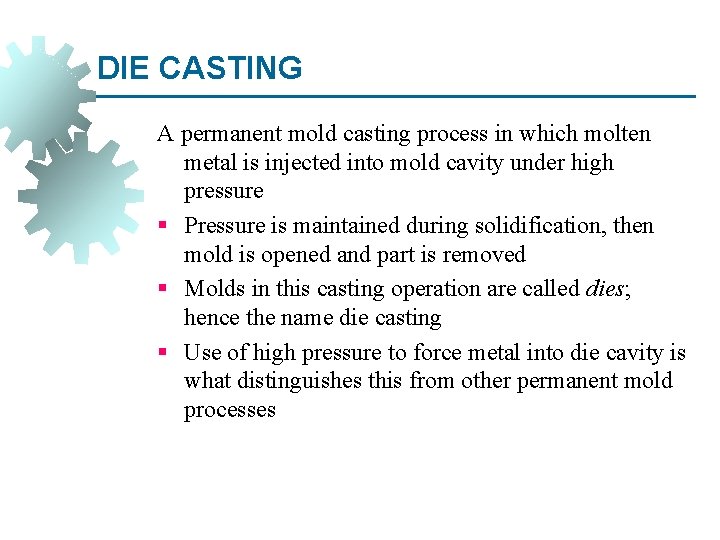
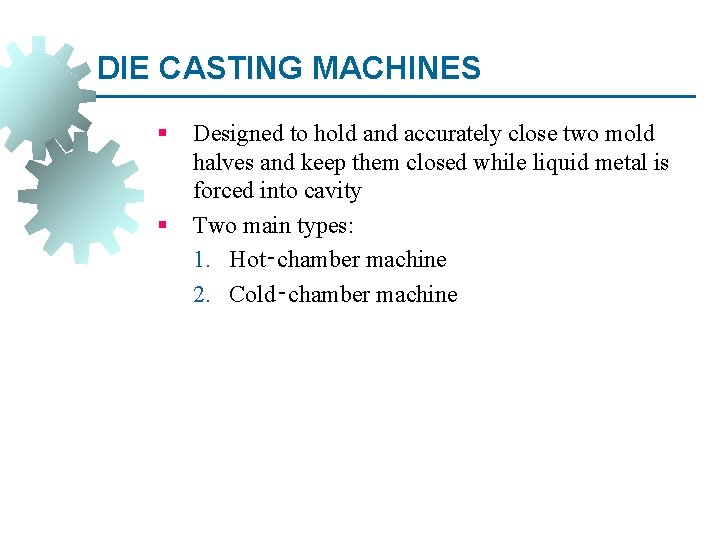
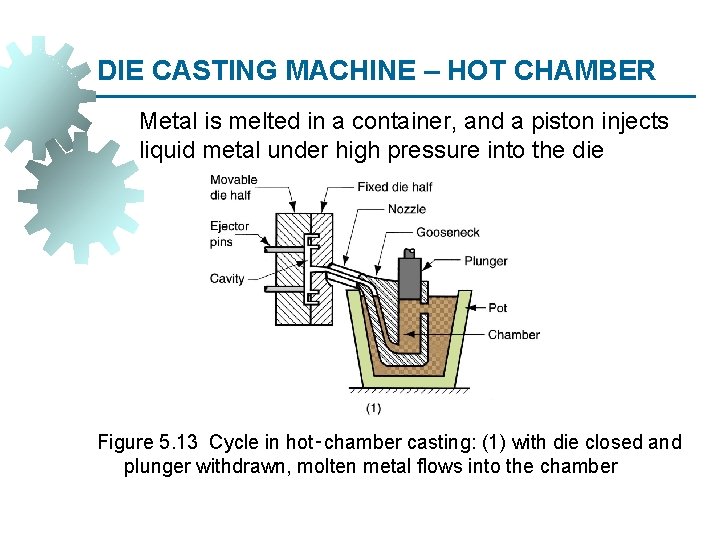
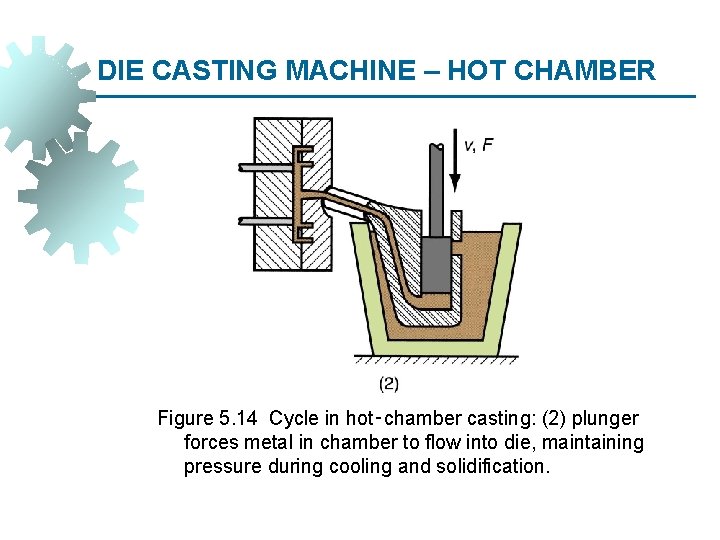
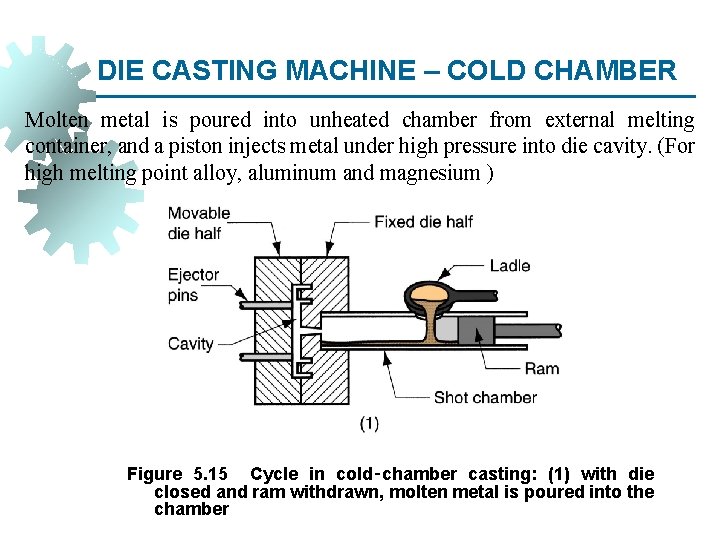
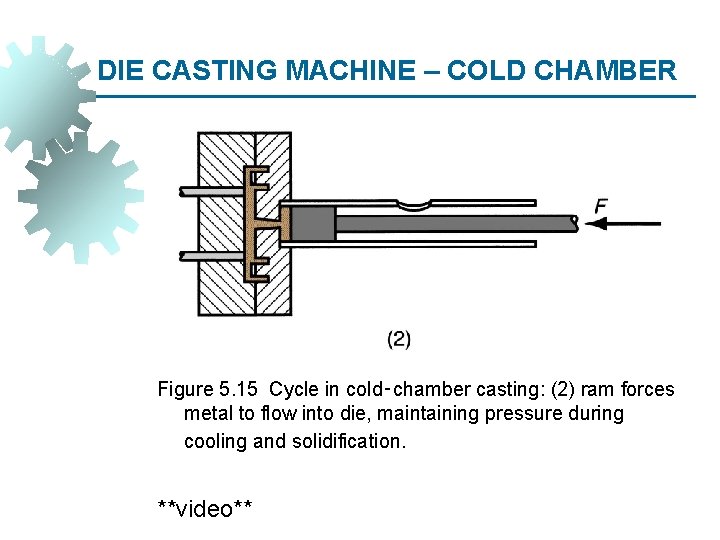
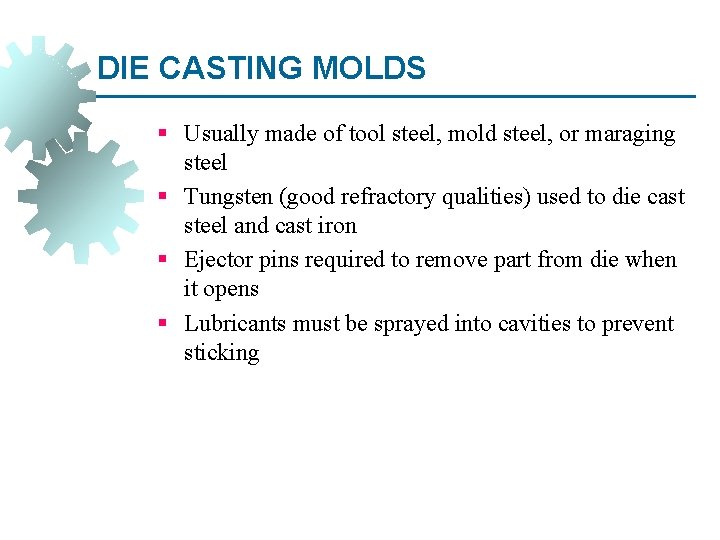
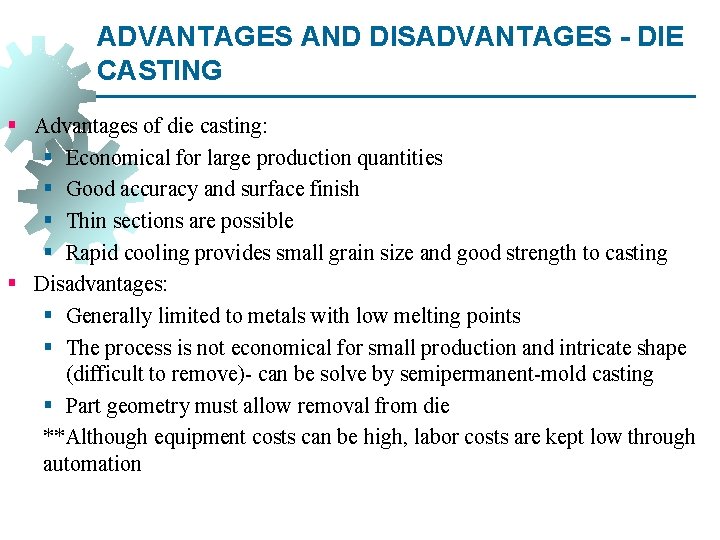
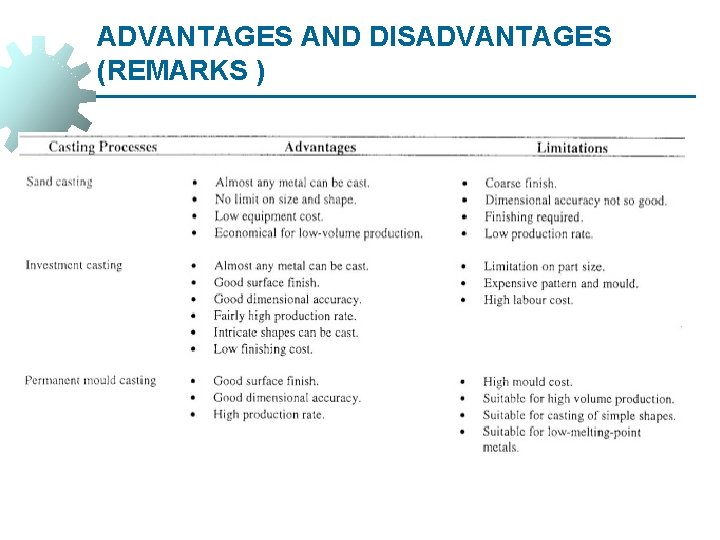
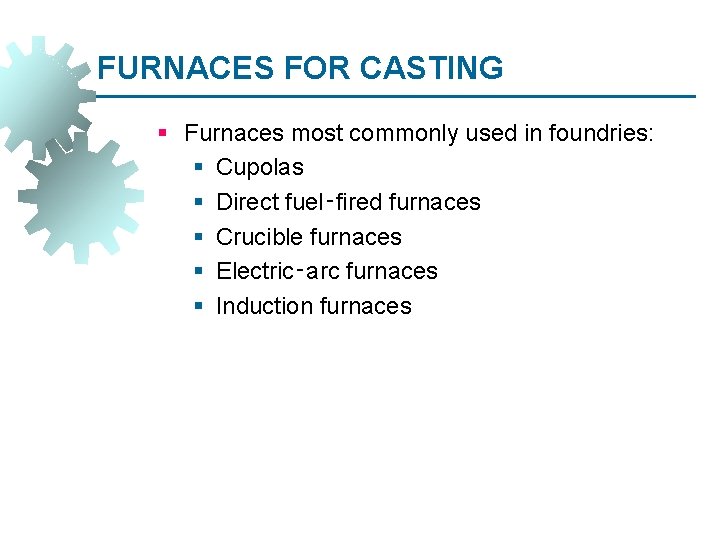
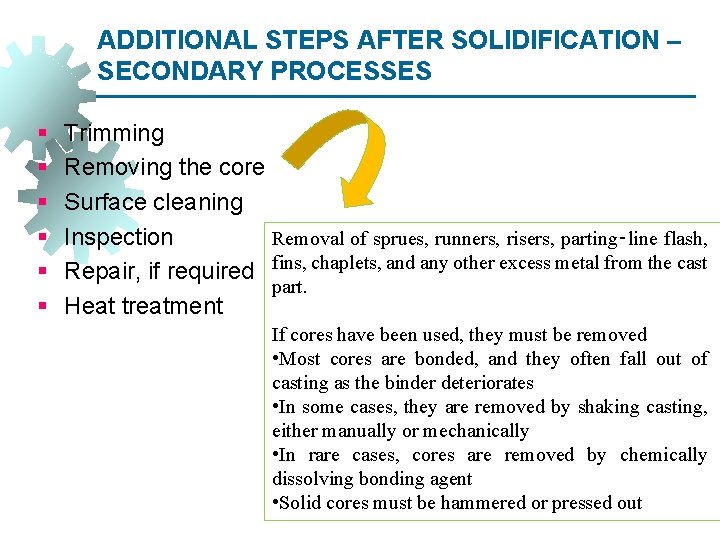
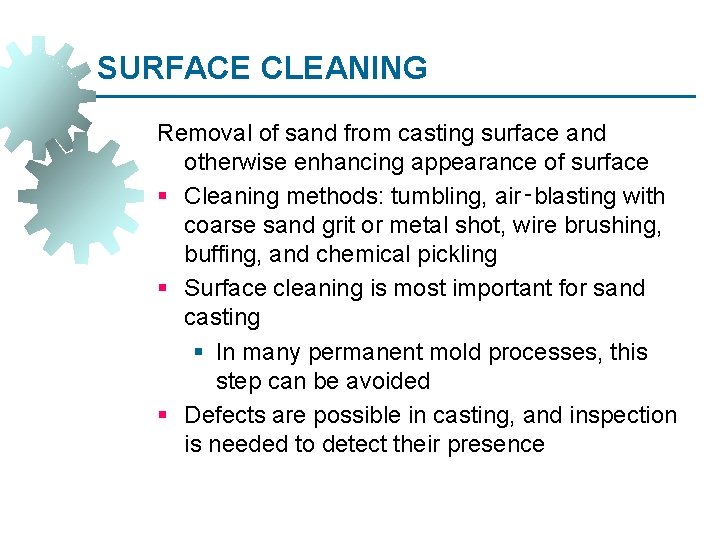
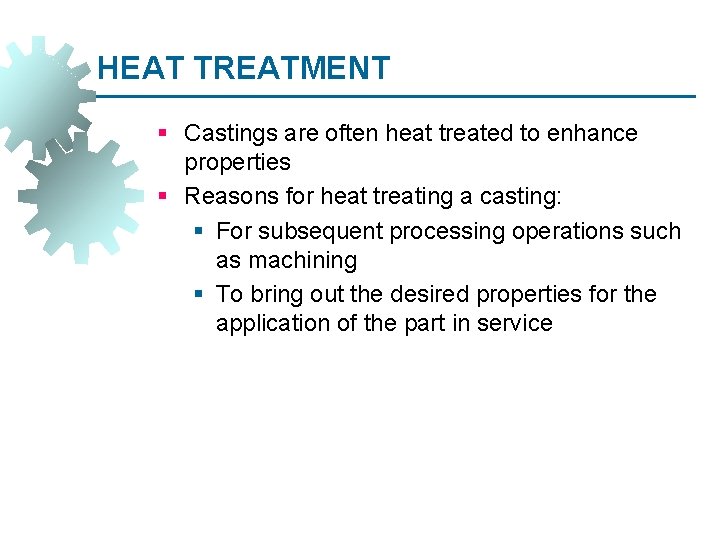
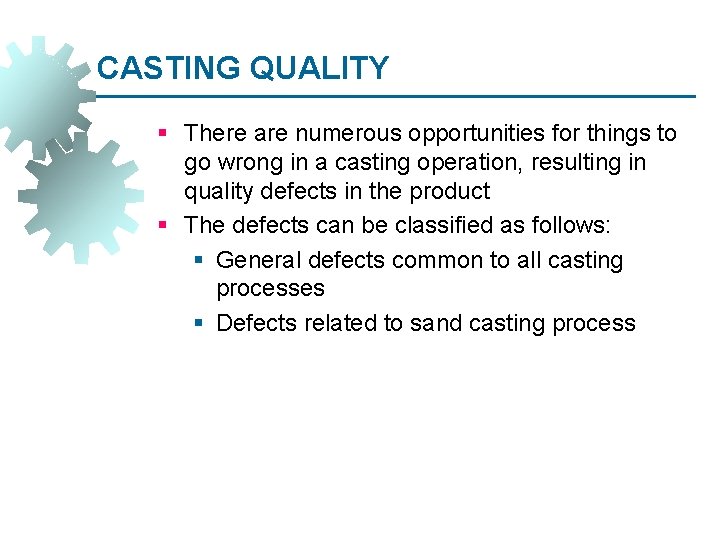
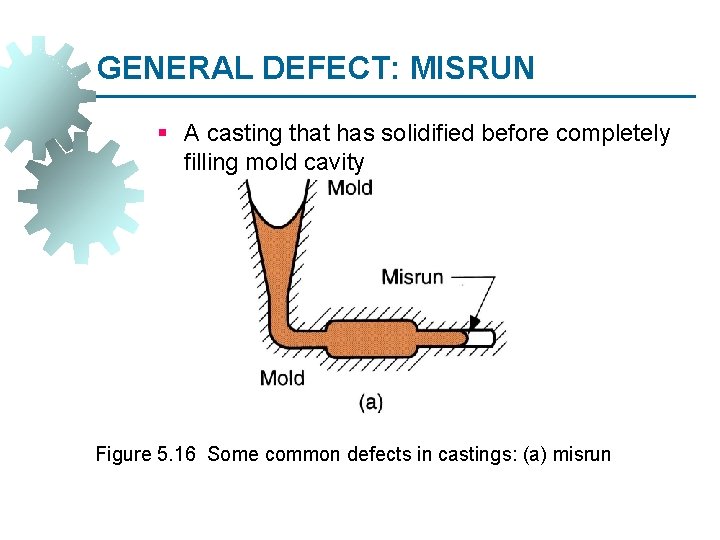
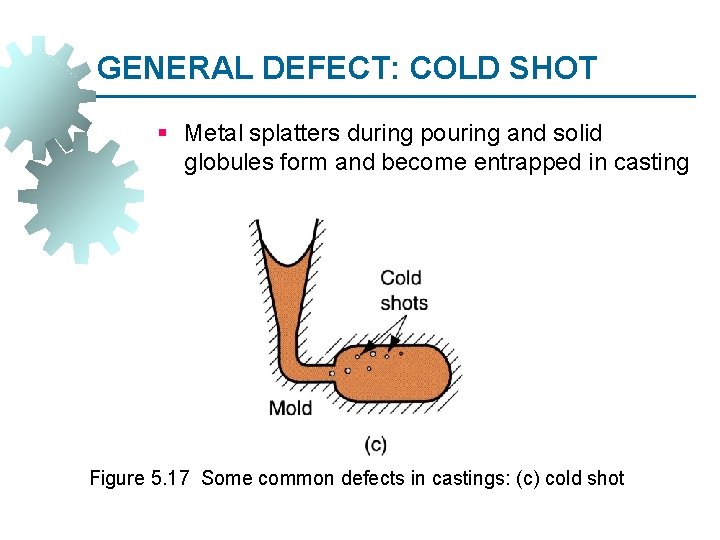
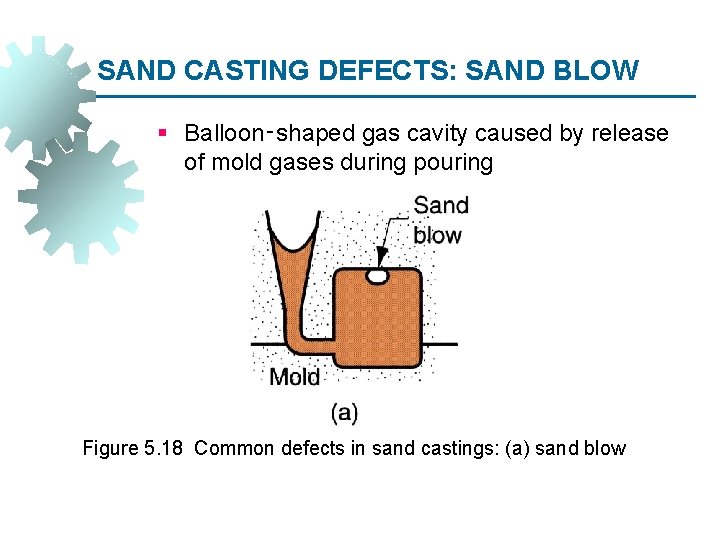
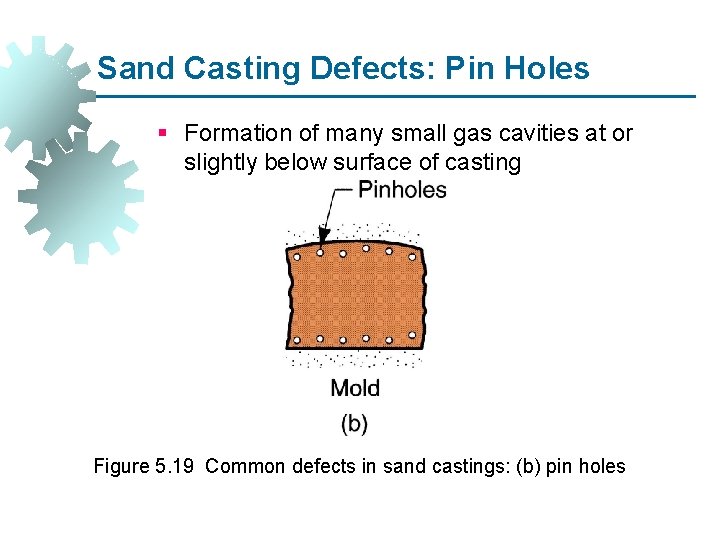
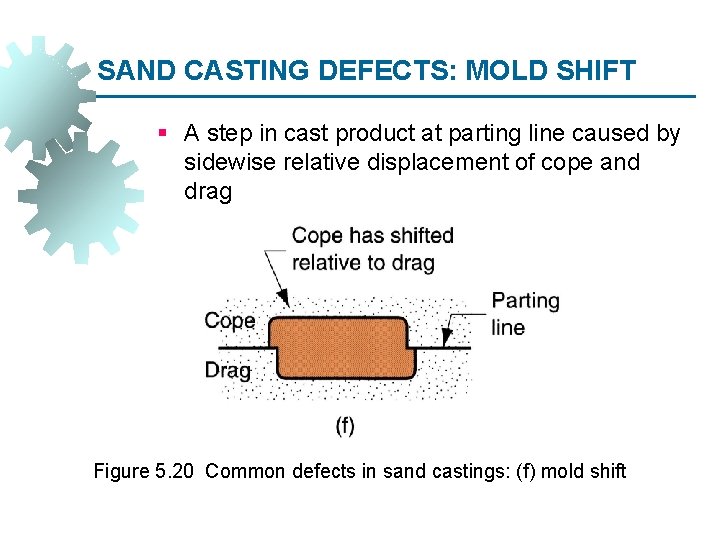
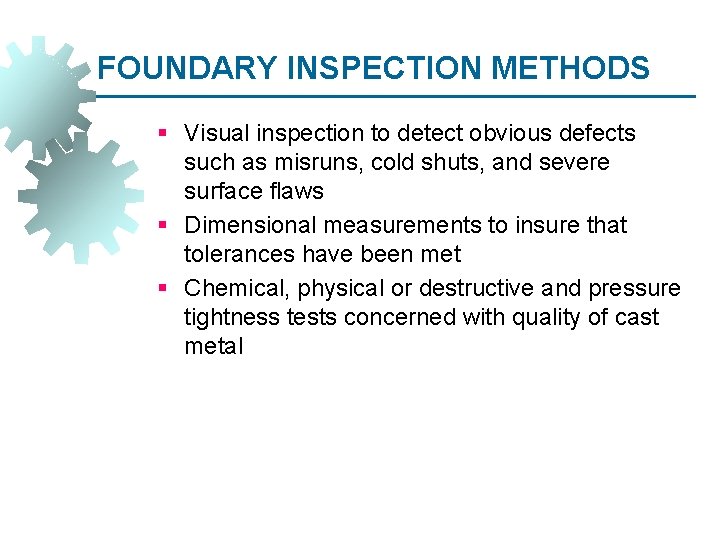
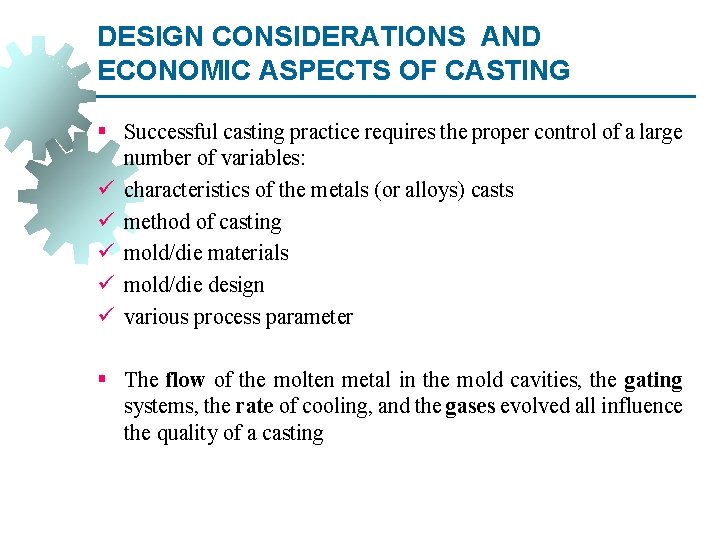
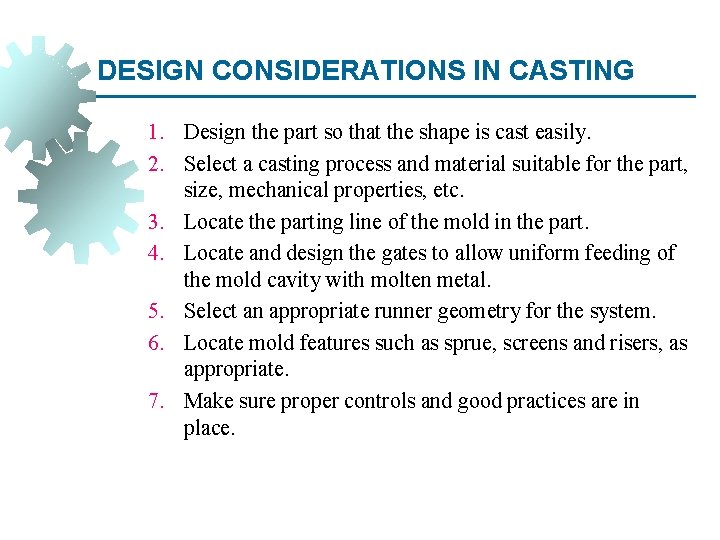
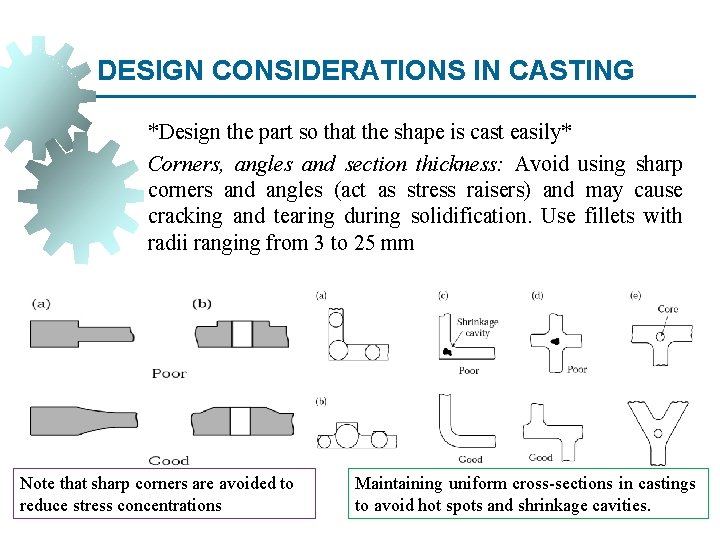
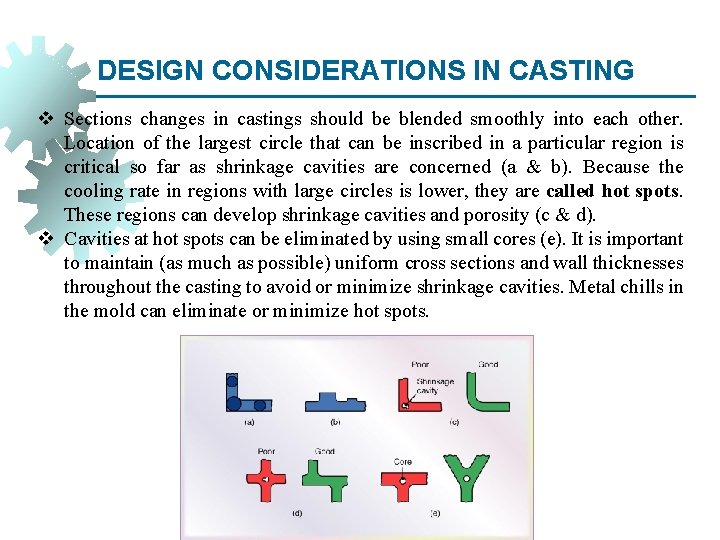
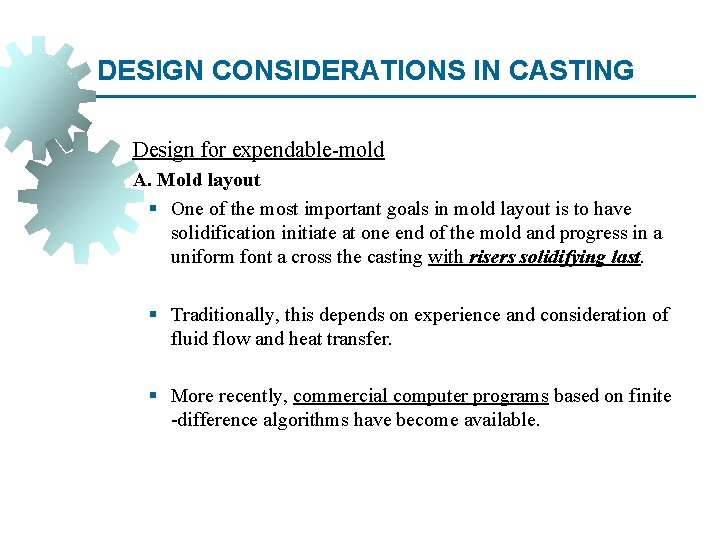
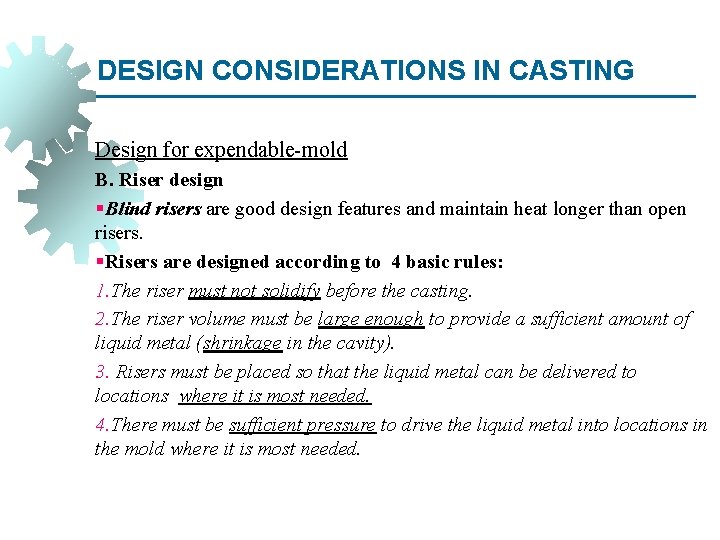
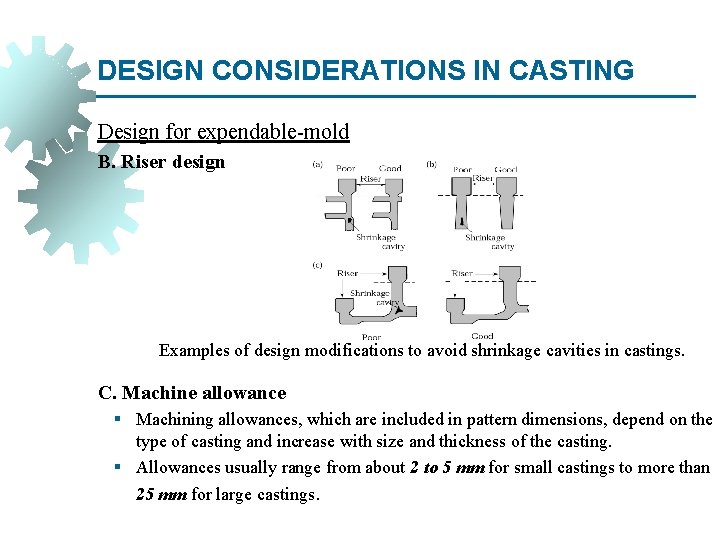
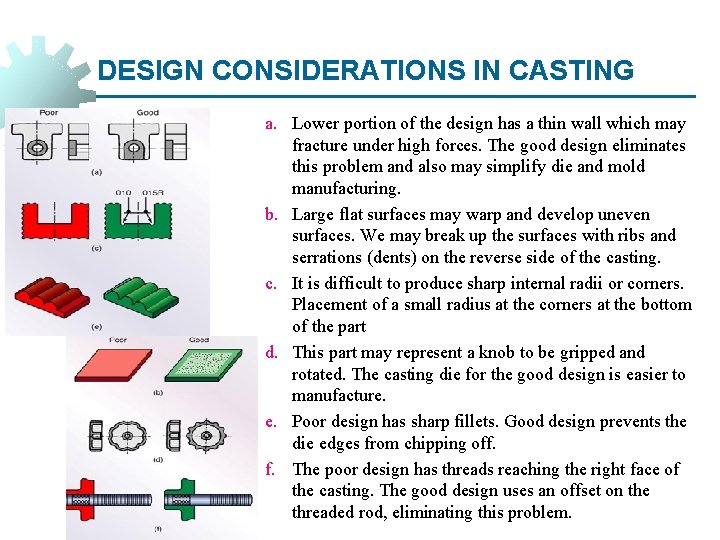
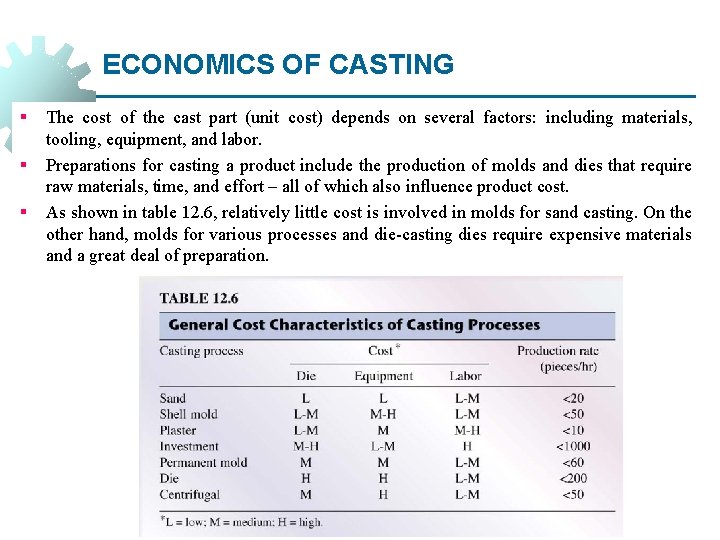
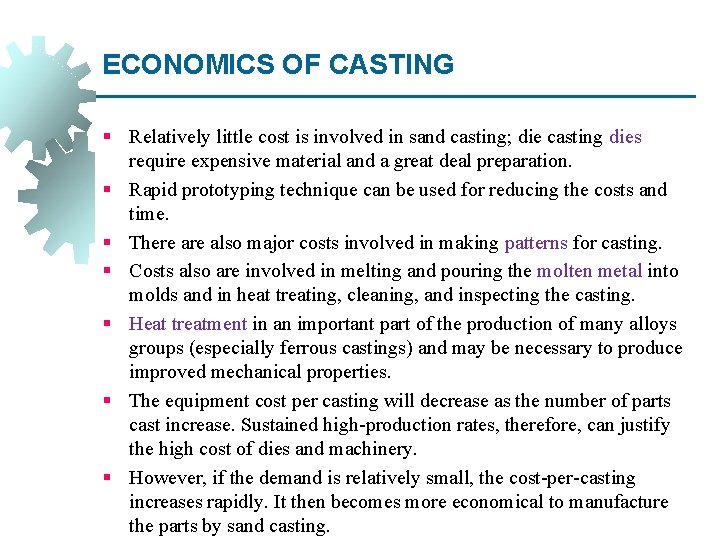
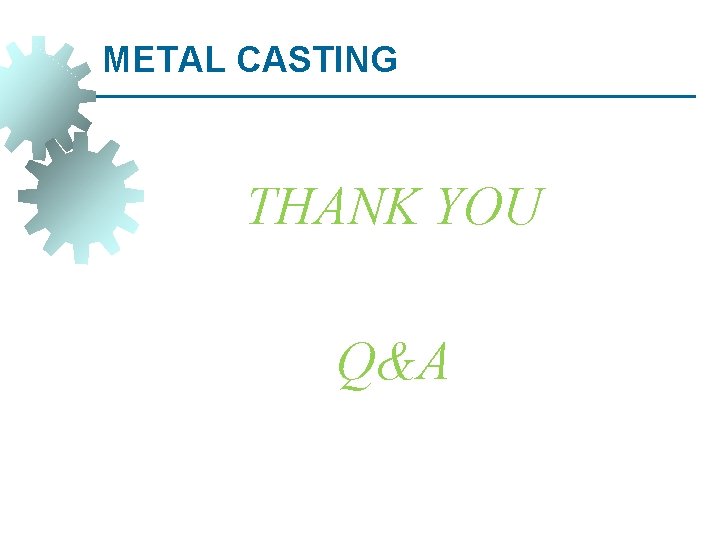
- Slides: 58

Chapter 4: METAL CASTING PROCESSES -The automation of casting process and increasing demand of high quality casting, which has led to significant change in the use of equipment and labor in casting industry. -Thus, it can be divided onto two major categories according to types of mold used; Pattern is reused Consumes
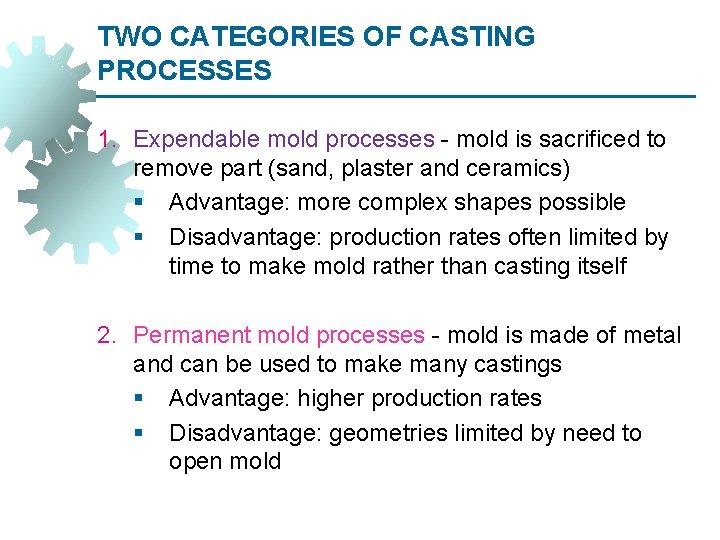
TWO CATEGORIES OF CASTING PROCESSES 1. Expendable mold processes - mold is sacrificed to remove part (sand, plaster and ceramics) § Advantage: more complex shapes possible § Disadvantage: production rates often limited by time to make mold rather than casting itself 2. Permanent mold processes - mold is made of metal and can be used to make many castings § Advantage: higher production rates § Disadvantage: geometries limited by need to open mold
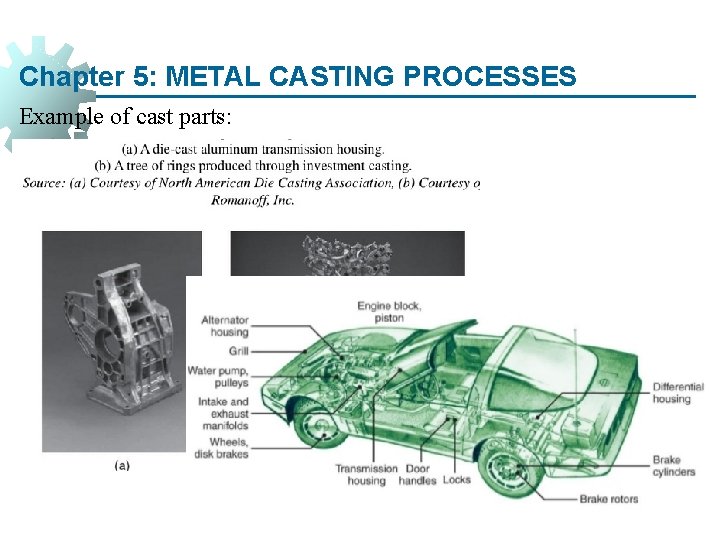
Chapter 5: METAL CASTING PROCESSES Example of cast parts:
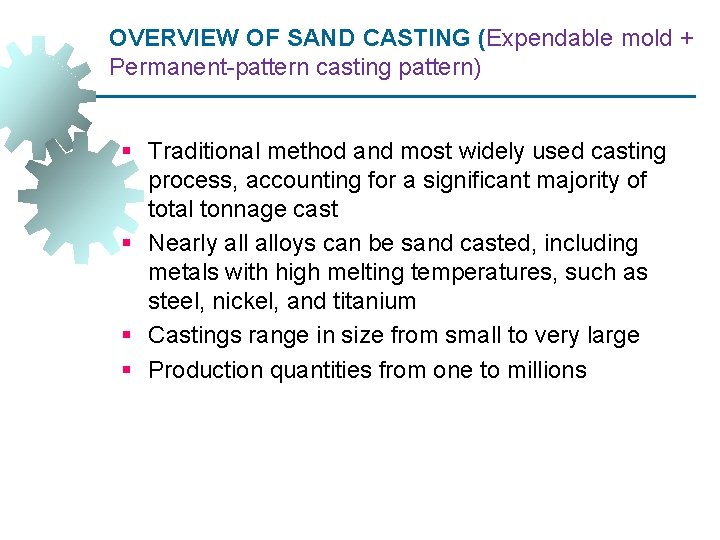
OVERVIEW OF SAND CASTING (Expendable mold + Permanent-pattern casting pattern) § Traditional method and most widely used casting process, accounting for a significant majority of total tonnage cast § Nearly alloys can be sand casted, including metals with high melting temperatures, such as steel, nickel, and titanium § Castings range in size from small to very large § Production quantities from one to millions
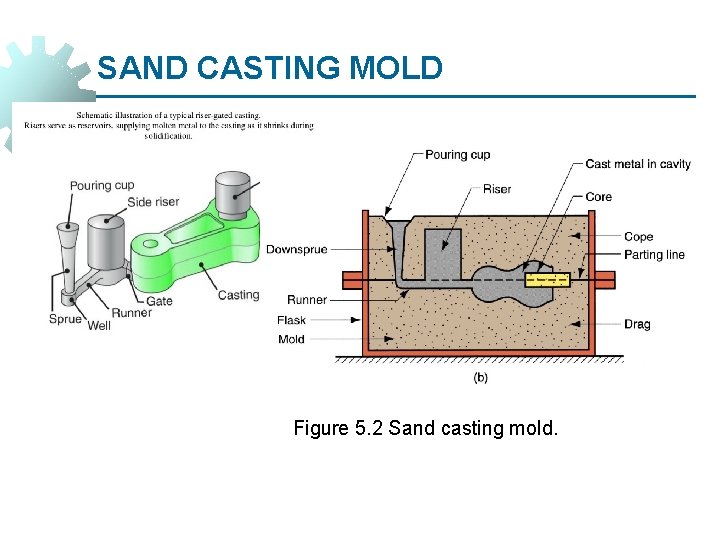
SAND CASTING MOLD Figure 5. 2 Sand casting mold.
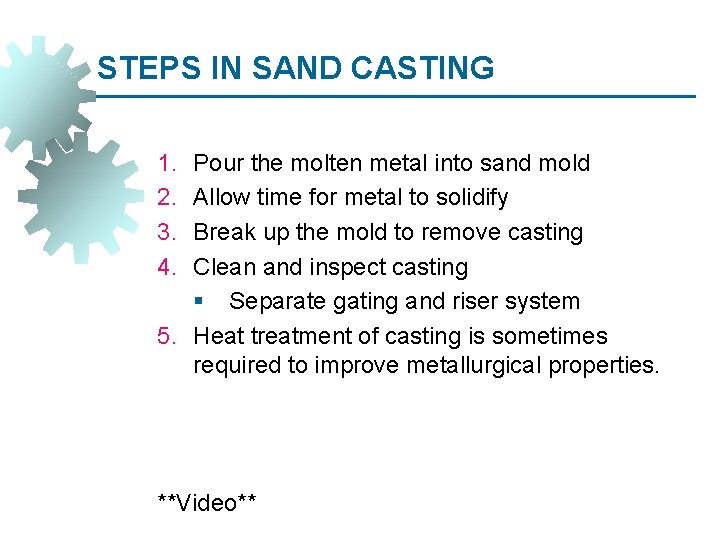
STEPS IN SAND CASTING 1. 2. 3. 4. Pour the molten metal into sand mold Allow time for metal to solidify Break up the mold to remove casting Clean and inspect casting § Separate gating and riser system 5. Heat treatment of casting is sometimes required to improve metallurgical properties. **Video**
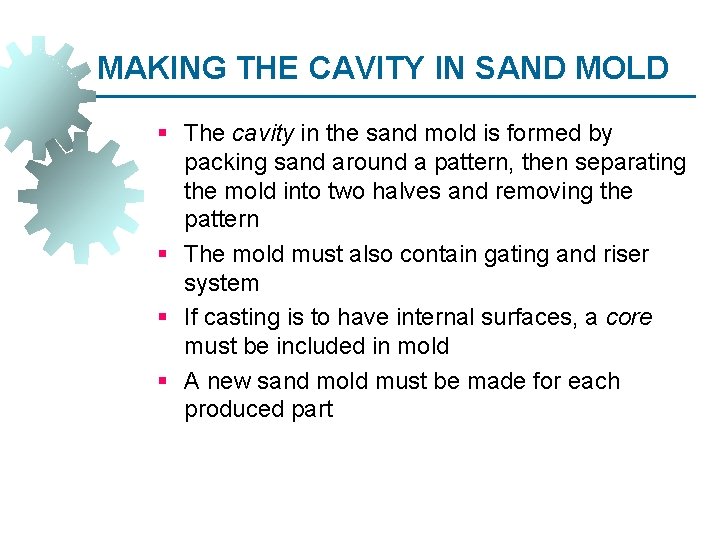
MAKING THE CAVITY IN SAND MOLD § The cavity in the sand mold is formed by packing sand around a pattern, then separating the mold into two halves and removing the pattern § The mold must also contain gating and riser system § If casting is to have internal surfaces, a core must be included in mold § A new sand mold must be made for each produced part
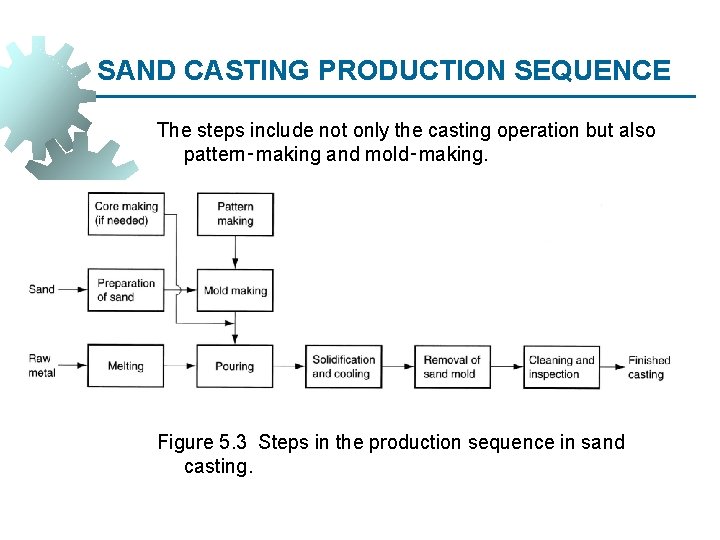
SAND CASTING PRODUCTION SEQUENCE The steps include not only the casting operation but also pattern‑making and mold‑making. Figure 5. 3 Steps in the production sequence in sand casting.
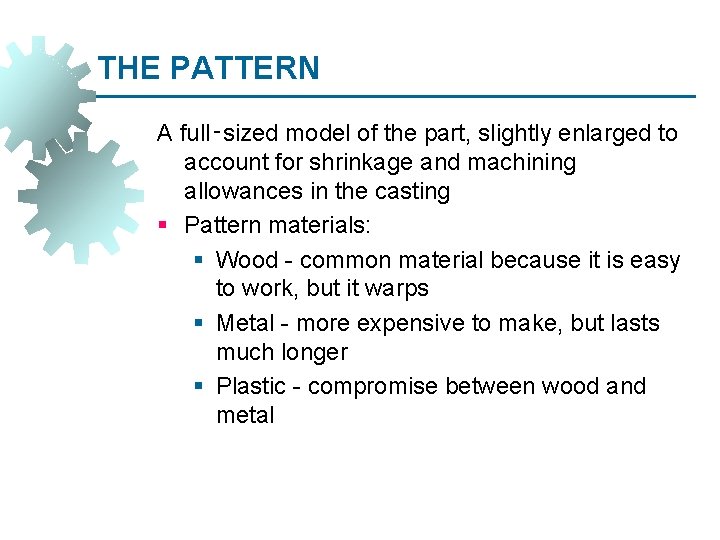
THE PATTERN A full‑sized model of the part, slightly enlarged to account for shrinkage and machining allowances in the casting § Pattern materials: § Wood - common material because it is easy to work, but it warps § Metal - more expensive to make, but lasts much longer § Plastic - compromise between wood and metal
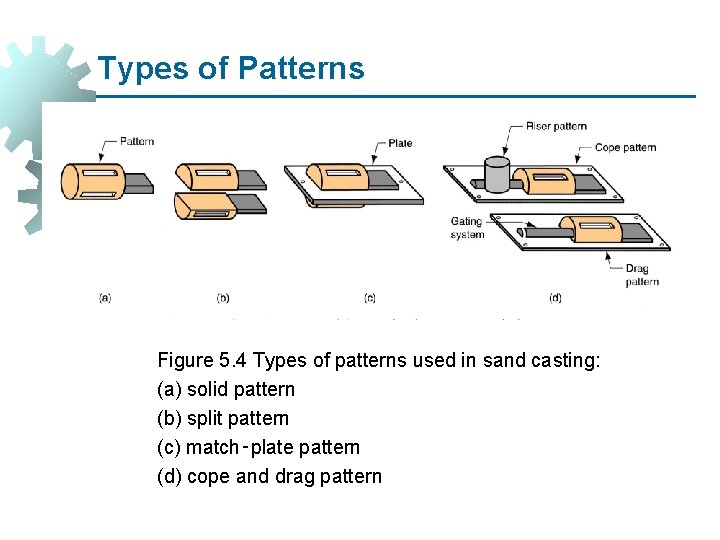
Types of Patterns Figure 5. 4 Types of patterns used in sand casting: (a) solid pattern (b) split pattern (c) match‑plate pattern (d) cope and drag pattern
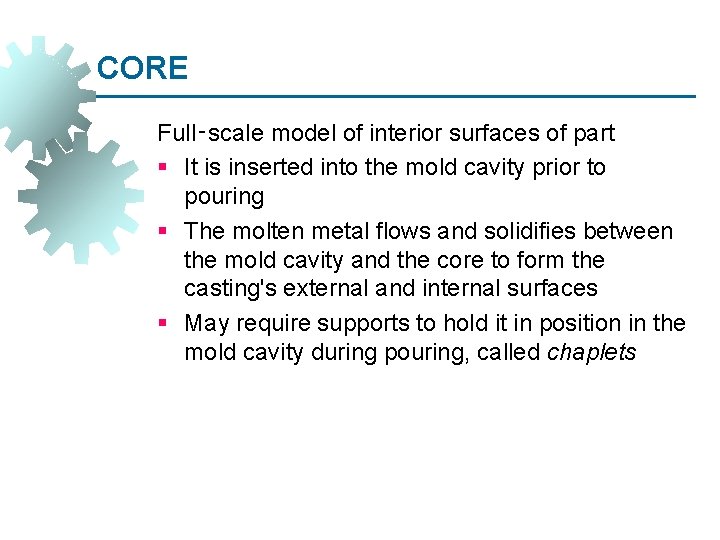
CORE Full‑scale model of interior surfaces of part § It is inserted into the mold cavity prior to pouring § The molten metal flows and solidifies between the mold cavity and the core to form the casting's external and internal surfaces § May require supports to hold it in position in the mold cavity during pouring, called chaplets
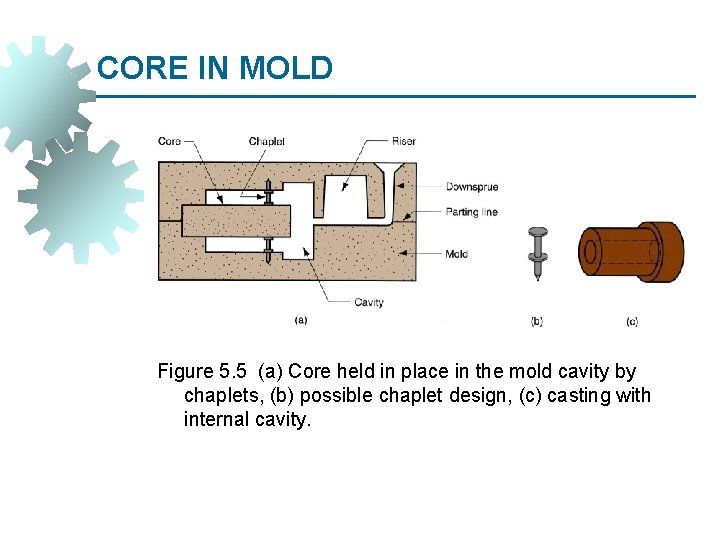
CORE IN MOLD Figure 5. 5 (a) Core held in place in the mold cavity by chaplets, (b) possible chaplet design, (c) casting with internal cavity.
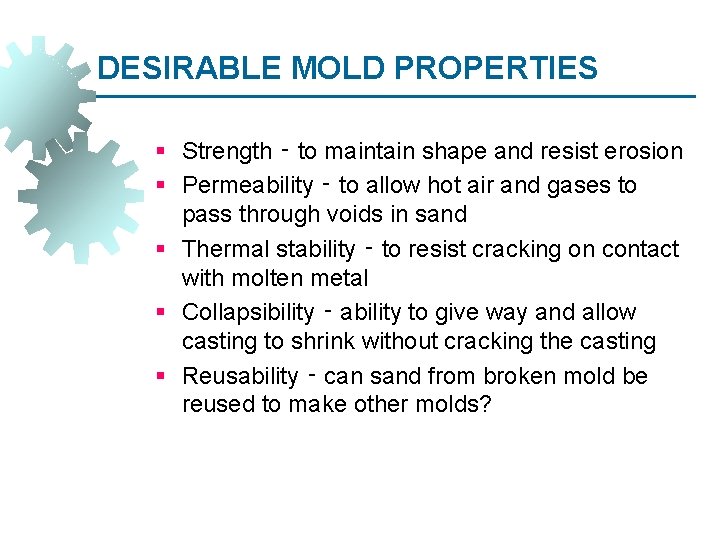
DESIRABLE MOLD PROPERTIES § Strength ‑ to maintain shape and resist erosion § Permeability ‑ to allow hot air and gases to pass through voids in sand § Thermal stability ‑ to resist cracking on contact with molten metal § Collapsibility ‑ ability to give way and allow casting to shrink without cracking the casting § Reusability ‑ can sand from broken mold be reused to make other molds?
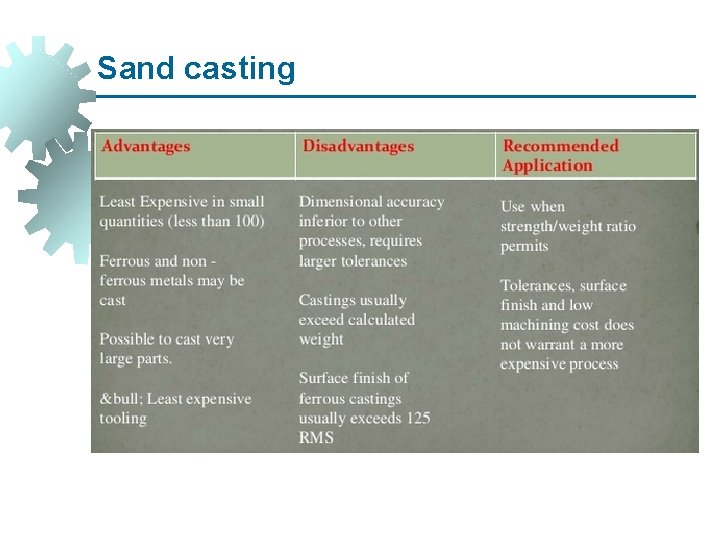
Sand casting
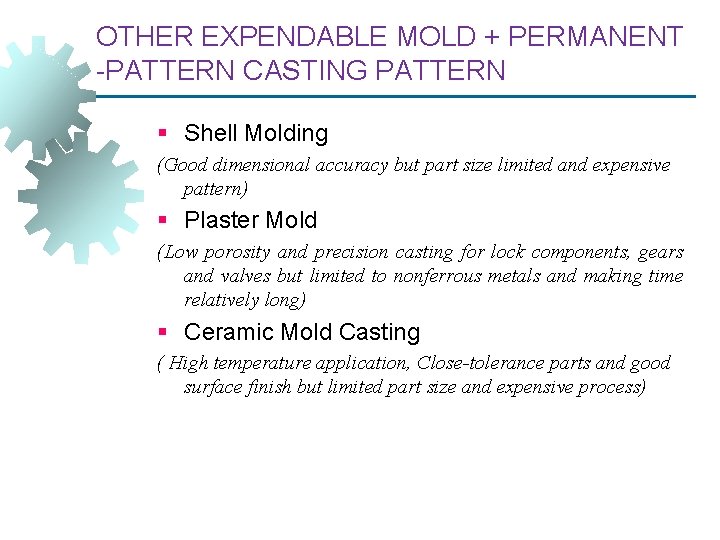
OTHER EXPENDABLE MOLD + PERMANENT -PATTERN CASTING PATTERN § Shell Molding (Good dimensional accuracy but part size limited and expensive pattern) § Plaster Mold (Low porosity and precision casting for lock components, gears and valves but limited to nonferrous metals and making time relatively long) § Ceramic Mold Casting ( High temperature application, Close-tolerance parts and good surface finish but limited part size and expensive process)
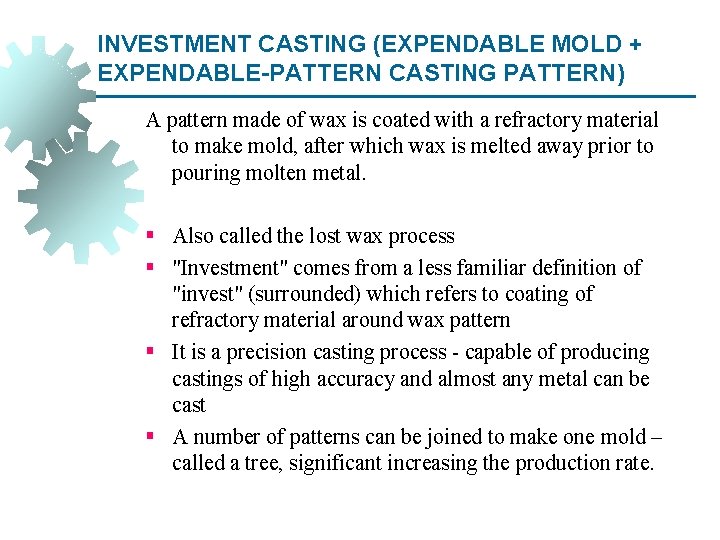
INVESTMENT CASTING (EXPENDABLE MOLD + EXPENDABLE-PATTERN CASTING PATTERN) A pattern made of wax is coated with a refractory material to make mold, after which wax is melted away prior to pouring molten metal. § Also called the lost wax process § "Investment" comes from a less familiar definition of "invest" (surrounded) which refers to coating of refractory material around wax pattern § It is a precision casting process - capable of producing castings of high accuracy and almost any metal can be cast § A number of patterns can be joined to make one mold – called a tree, significant increasing the production rate.
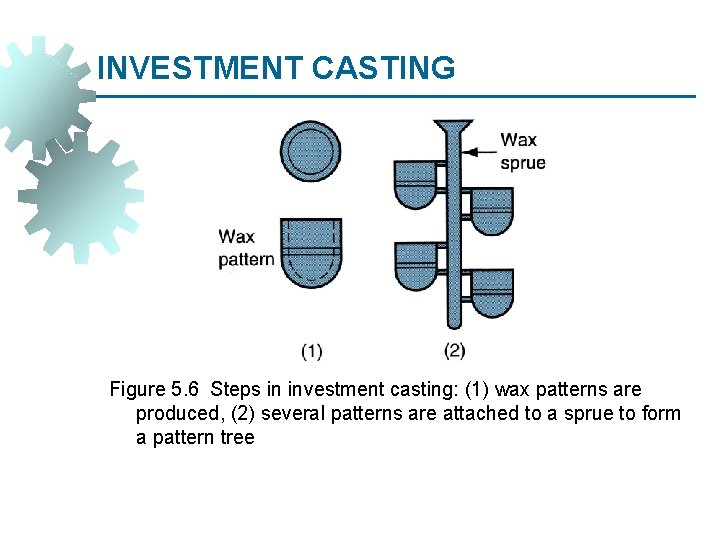
INVESTMENT CASTING Figure 5. 6 Steps in investment casting: (1) wax patterns are produced, (2) several patterns are attached to a sprue to form a pattern tree
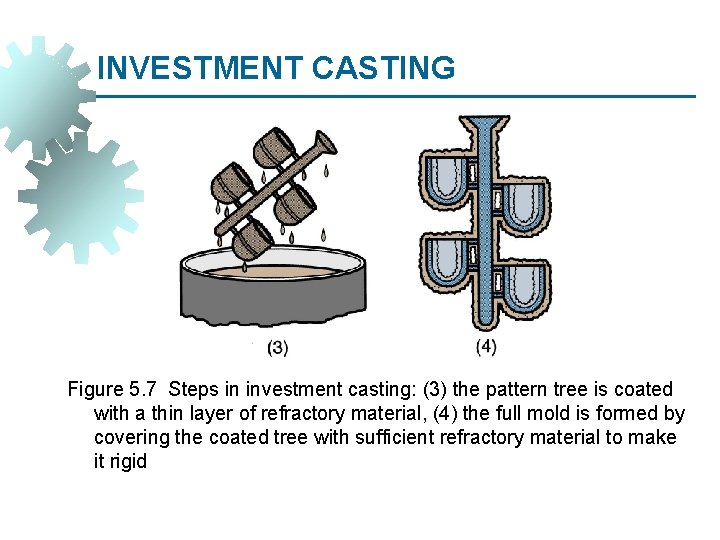
INVESTMENT CASTING Figure 5. 7 Steps in investment casting: (3) the pattern tree is coated with a thin layer of refractory material, (4) the full mold is formed by covering the coated tree with sufficient refractory material to make it rigid
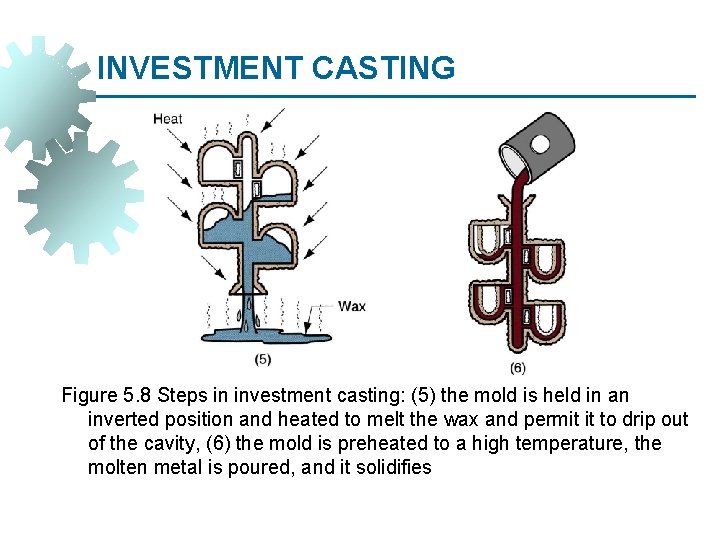
INVESTMENT CASTING Figure 5. 8 Steps in investment casting: (5) the mold is held in an inverted position and heated to melt the wax and permit it to drip out of the cavity, (6) the mold is preheated to a high temperature, the molten metal is poured, and it solidifies
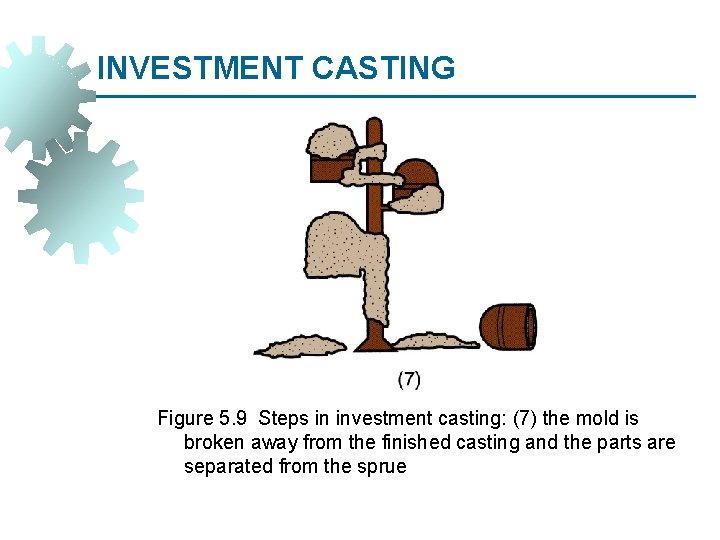
INVESTMENT CASTING Figure 5. 9 Steps in investment casting: (7) the mold is broken away from the finished casting and the parts are separated from the sprue
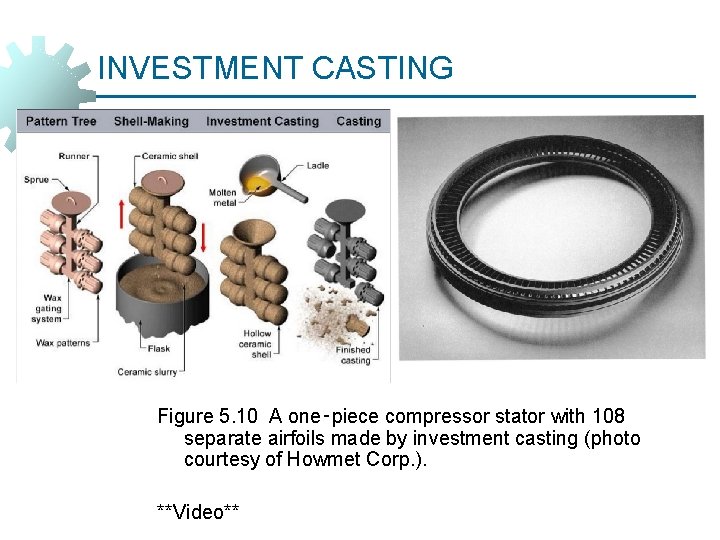
INVESTMENT CASTING Figure 5. 10 A one‑piece compressor stator with 108 separate airfoils made by investment casting (photo courtesy of Howmet Corp. ). **Video**
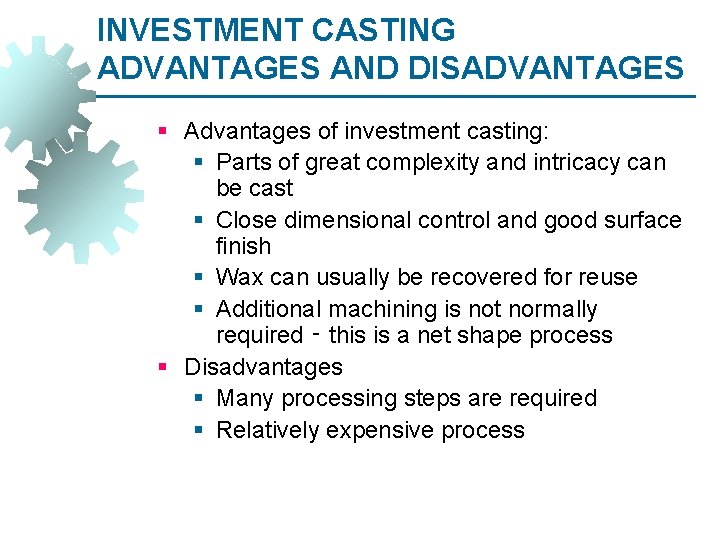
INVESTMENT CASTING ADVANTAGES AND DISADVANTAGES § Advantages of investment casting: § Parts of great complexity and intricacy can be cast § Close dimensional control and good surface finish § Wax can usually be recovered for reuse § Additional machining is not normally required ‑ this is a net shape process § Disadvantages § Many processing steps are required § Relatively expensive process
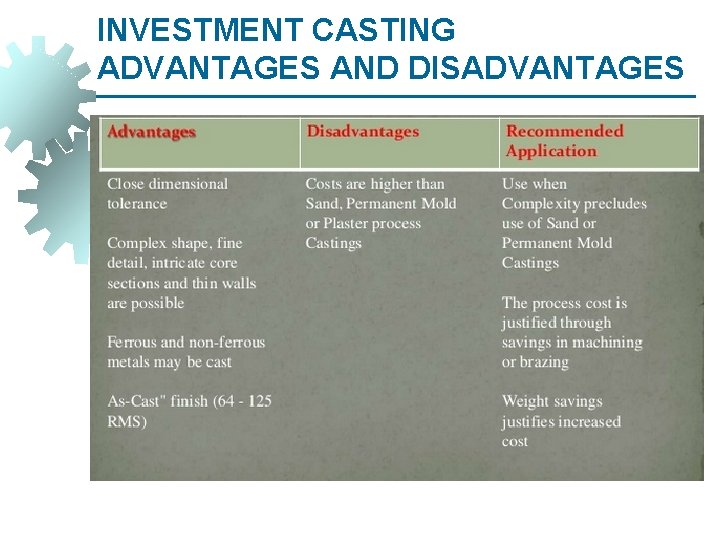
INVESTMENT CASTING ADVANTAGES AND DISADVANTAGES
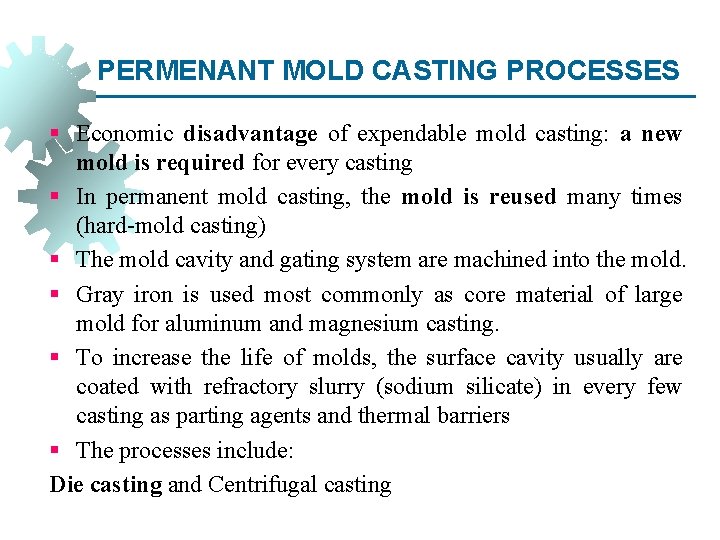
PERMENANT MOLD CASTING PROCESSES § Economic disadvantage of expendable mold casting: a new mold is required for every casting § In permanent mold casting, the mold is reused many times (hard-mold casting) § The mold cavity and gating system are machined into the mold. § Gray iron is used most commonly as core material of large mold for aluminum and magnesium casting. § To increase the life of molds, the surface cavity usually are coated with refractory slurry (sodium silicate) in every few casting as parting agents and thermal barriers § The processes include: Die casting and Centrifugal casting
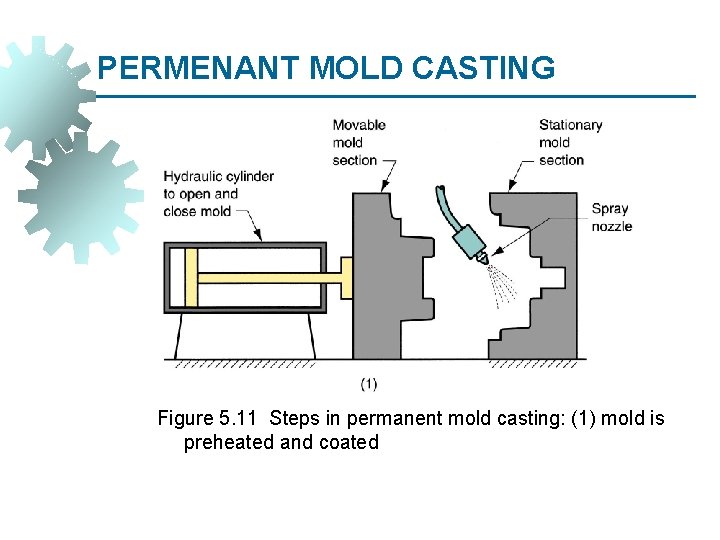
PERMENANT MOLD CASTING Figure 5. 11 Steps in permanent mold casting: (1) mold is preheated and coated
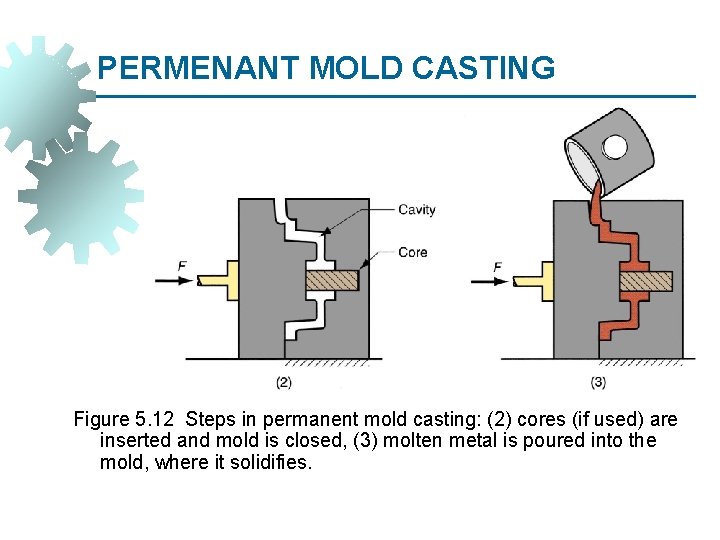
PERMENANT MOLD CASTING Figure 5. 12 Steps in permanent mold casting: (2) cores (if used) are inserted and mold is closed, (3) molten metal is poured into the mold, where it solidifies.
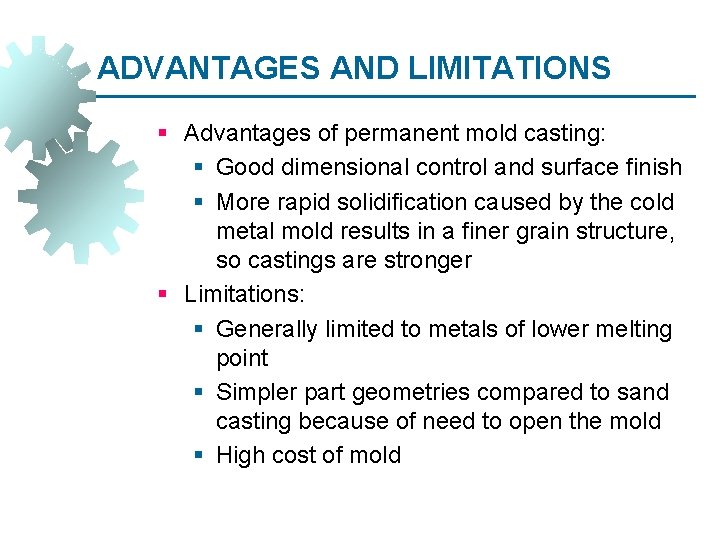
ADVANTAGES AND LIMITATIONS § Advantages of permanent mold casting: § Good dimensional control and surface finish § More rapid solidification caused by the cold metal mold results in a finer grain structure, so castings are stronger § Limitations: § Generally limited to metals of lower melting point § Simpler part geometries compared to sand casting because of need to open the mold § High cost of mold
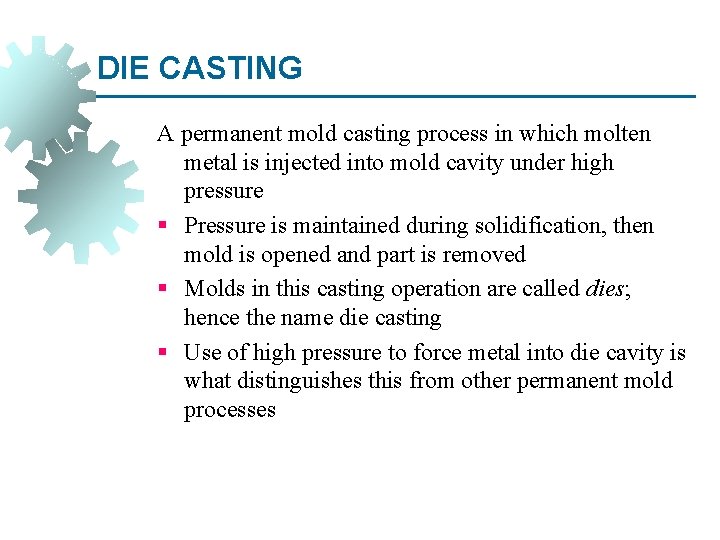
DIE CASTING A permanent mold casting process in which molten metal is injected into mold cavity under high pressure § Pressure is maintained during solidification, then mold is opened and part is removed § Molds in this casting operation are called dies; hence the name die casting § Use of high pressure to force metal into die cavity is what distinguishes this from other permanent mold processes
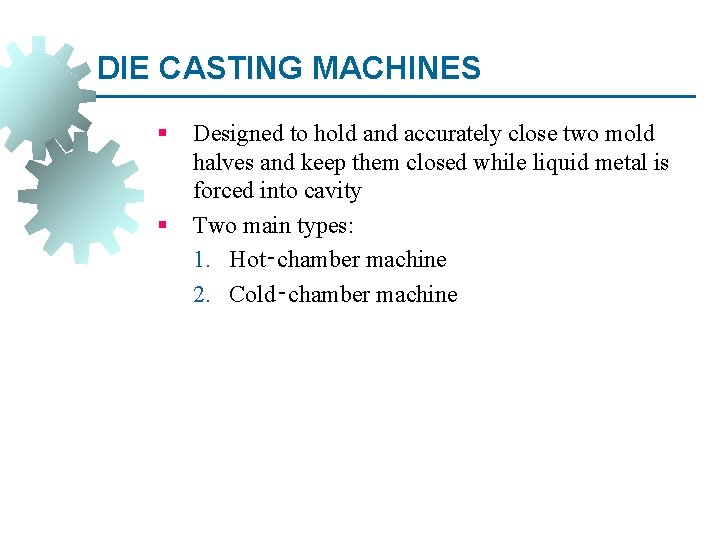
DIE CASTING MACHINES § § Designed to hold and accurately close two mold halves and keep them closed while liquid metal is forced into cavity Two main types: 1. Hot‑chamber machine 2. Cold‑chamber machine
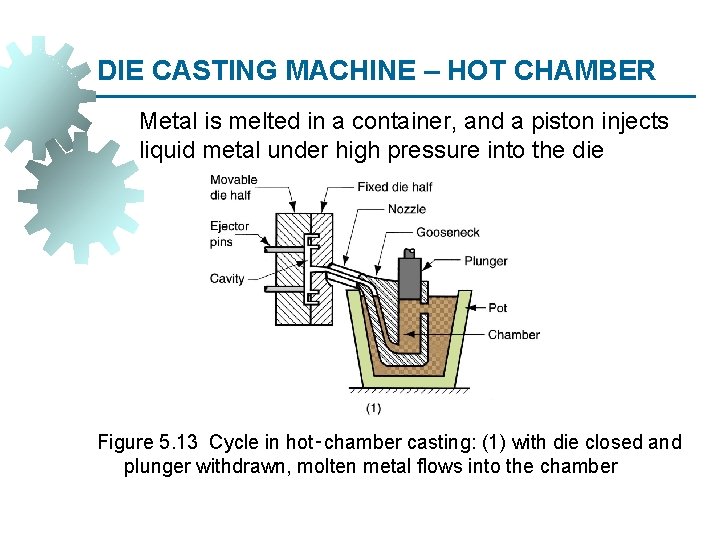
DIE CASTING MACHINE – HOT CHAMBER Metal is melted in a container, and a piston injects liquid metal under high pressure into the die Figure 5. 13 Cycle in hot‑chamber casting: (1) with die closed and plunger withdrawn, molten metal flows into the chamber
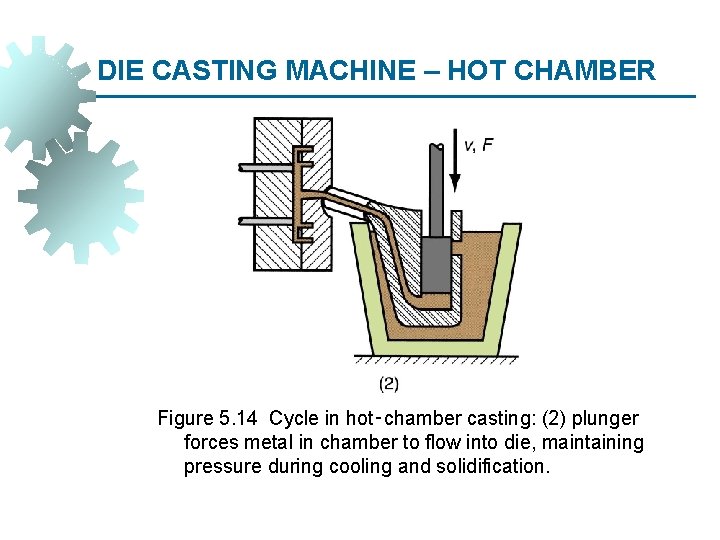
DIE CASTING MACHINE – HOT CHAMBER Figure 5. 14 Cycle in hot‑chamber casting: (2) plunger forces metal in chamber to flow into die, maintaining pressure during cooling and solidification.
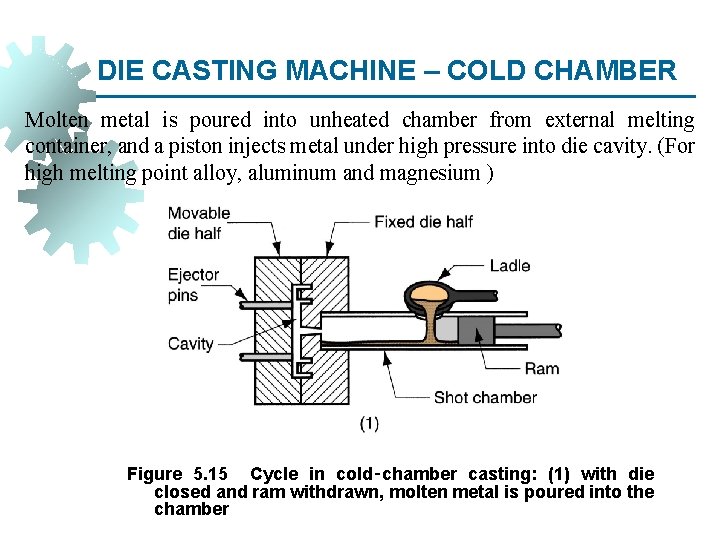
DIE CASTING MACHINE – COLD CHAMBER Molten metal is poured into unheated chamber from external melting container, and a piston injects metal under high pressure into die cavity. (For high melting point alloy, aluminum and magnesium ) Figure 5. 15 Cycle in cold‑chamber casting: (1) with die closed and ram withdrawn, molten metal is poured into the chamber
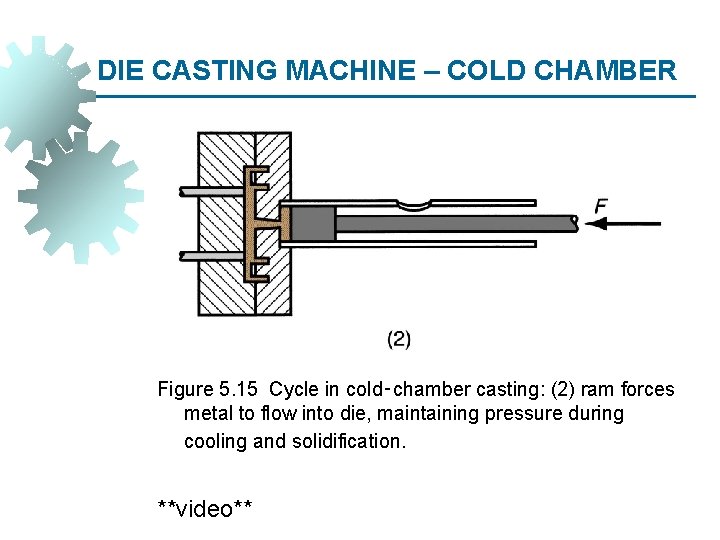
DIE CASTING MACHINE – COLD CHAMBER Figure 5. 15 Cycle in cold‑chamber casting: (2) ram forces metal to flow into die, maintaining pressure during cooling and solidification. **video**
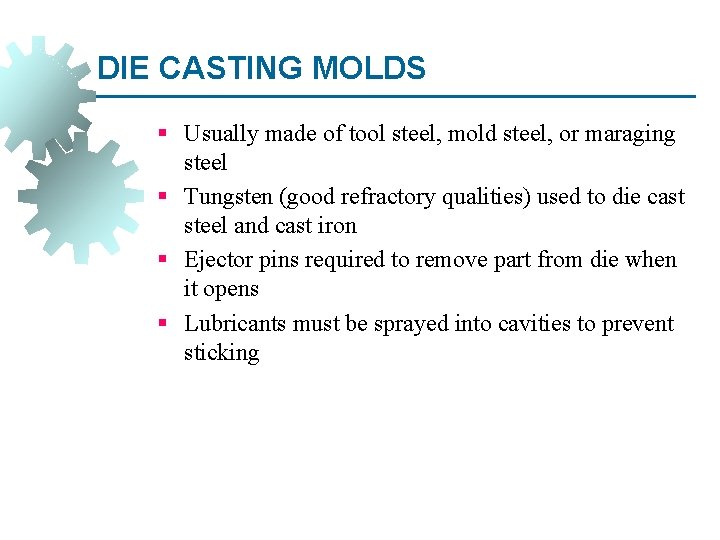
DIE CASTING MOLDS § Usually made of tool steel, mold steel, or maraging steel § Tungsten (good refractory qualities) used to die cast steel and cast iron § Ejector pins required to remove part from die when it opens § Lubricants must be sprayed into cavities to prevent sticking
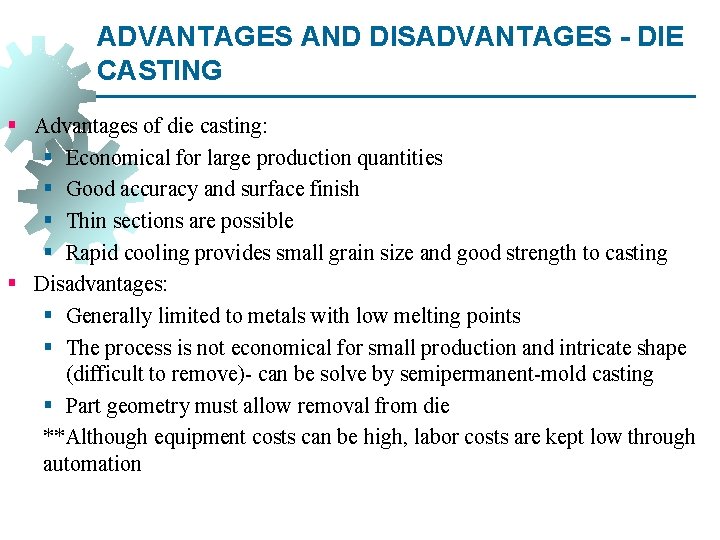
ADVANTAGES AND DISADVANTAGES - DIE CASTING § Advantages of die casting: § Economical for large production quantities § Good accuracy and surface finish § Thin sections are possible § Rapid cooling provides small grain size and good strength to casting § Disadvantages: § Generally limited to metals with low melting points § The process is not economical for small production and intricate shape (difficult to remove)- can be solve by semipermanent-mold casting § Part geometry must allow removal from die **Although equipment costs can be high, labor costs are kept low through automation
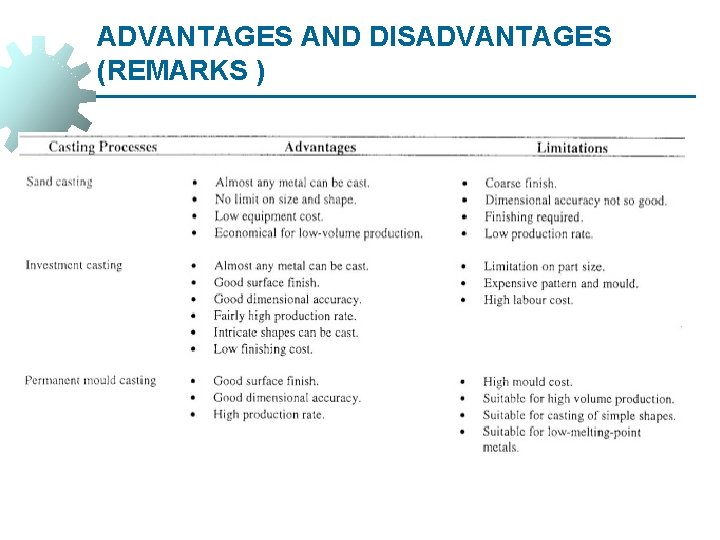
ADVANTAGES AND DISADVANTAGES (REMARKS )
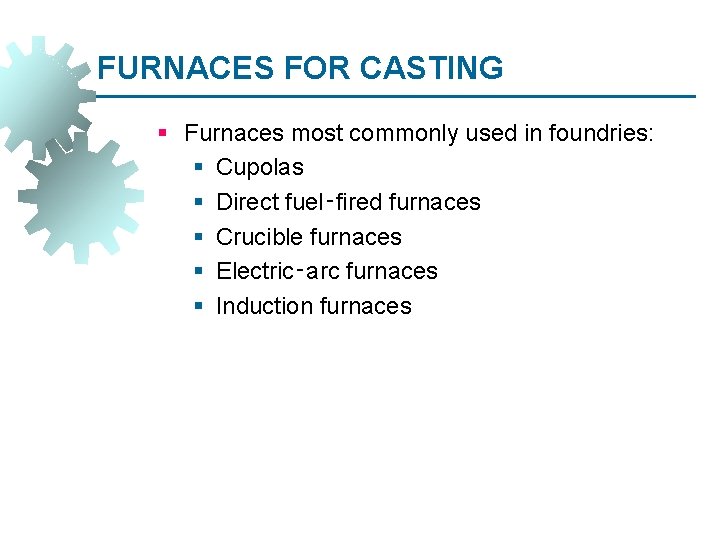
FURNACES FOR CASTING § Furnaces most commonly used in foundries: § Cupolas § Direct fuel‑fired furnaces § Crucible furnaces § Electric‑arc furnaces § Induction furnaces
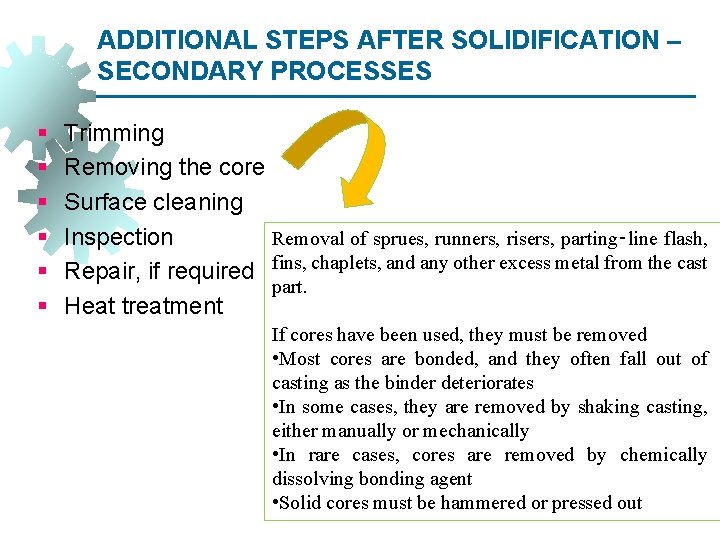
ADDITIONAL STEPS AFTER SOLIDIFICATION – SECONDARY PROCESSES § § § Trimming Removing the core Surface cleaning Inspection Removal of sprues, runners, risers, parting‑line flash, Repair, if required fins, chaplets, and any other excess metal from the cast part. Heat treatment If cores have been used, they must be removed • Most cores are bonded, and they often fall out of casting as the binder deteriorates • In some cases, they are removed by shaking casting, either manually or mechanically • In rare cases, cores are removed by chemically dissolving bonding agent • Solid cores must be hammered or pressed out
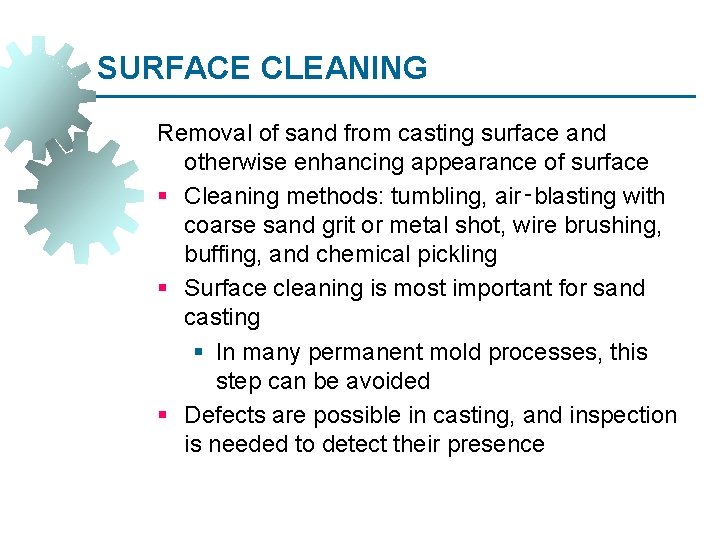
SURFACE CLEANING Removal of sand from casting surface and otherwise enhancing appearance of surface § Cleaning methods: tumbling, air‑blasting with coarse sand grit or metal shot, wire brushing, buffing, and chemical pickling § Surface cleaning is most important for sand casting § In many permanent mold processes, this step can be avoided § Defects are possible in casting, and inspection is needed to detect their presence
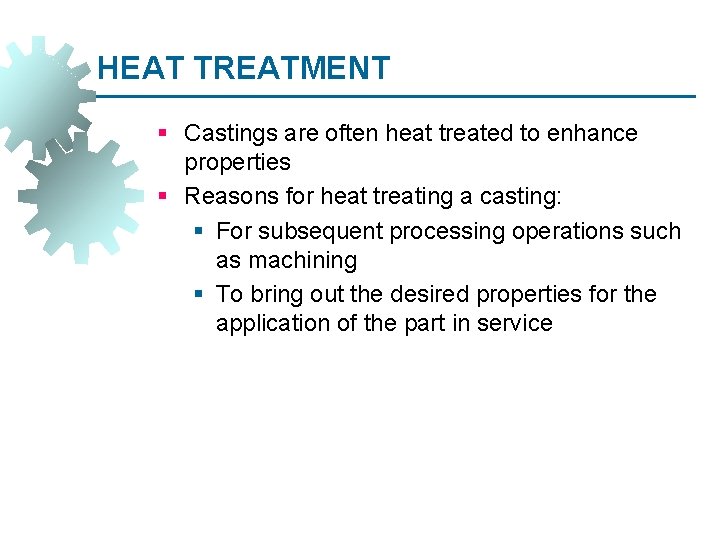
HEAT TREATMENT § Castings are often heat treated to enhance properties § Reasons for heat treating a casting: § For subsequent processing operations such as machining § To bring out the desired properties for the application of the part in service
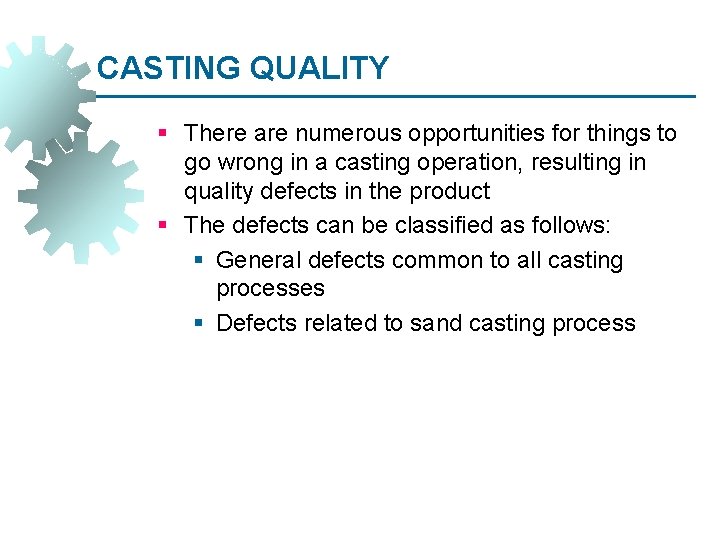
CASTING QUALITY § There are numerous opportunities for things to go wrong in a casting operation, resulting in quality defects in the product § The defects can be classified as follows: § General defects common to all casting processes § Defects related to sand casting process
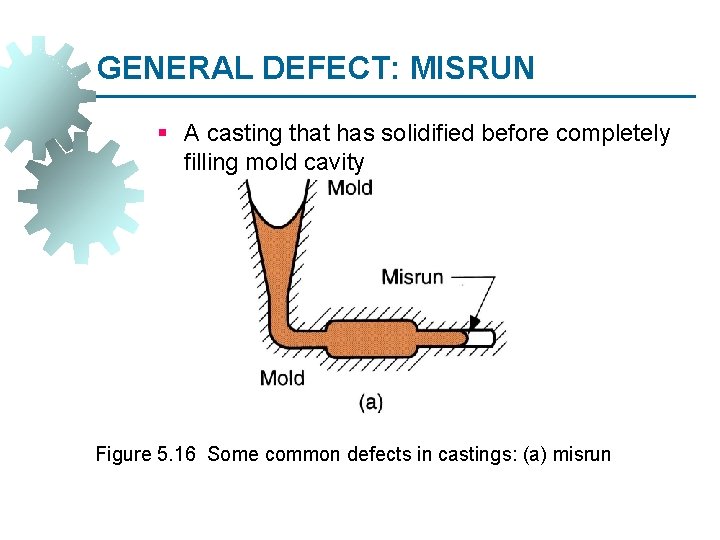
GENERAL DEFECT: MISRUN § A casting that has solidified before completely filling mold cavity Figure 5. 16 Some common defects in castings: (a) misrun
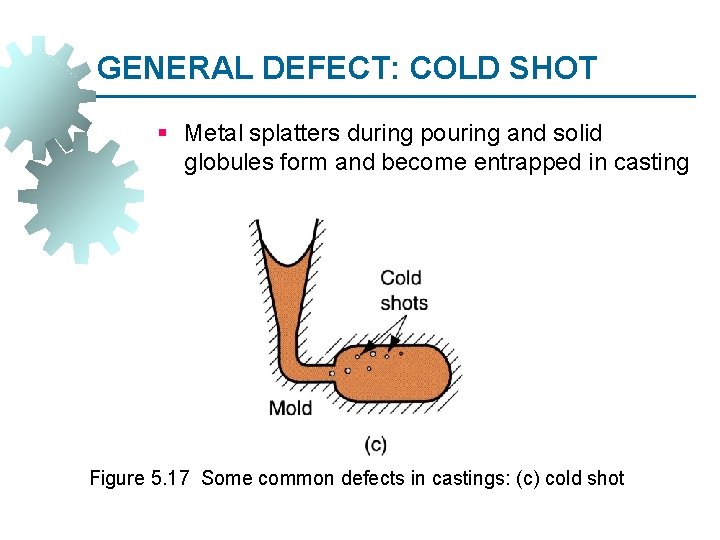
GENERAL DEFECT: COLD SHOT § Metal splatters during pouring and solid globules form and become entrapped in casting Figure 5. 17 Some common defects in castings: (c) cold shot
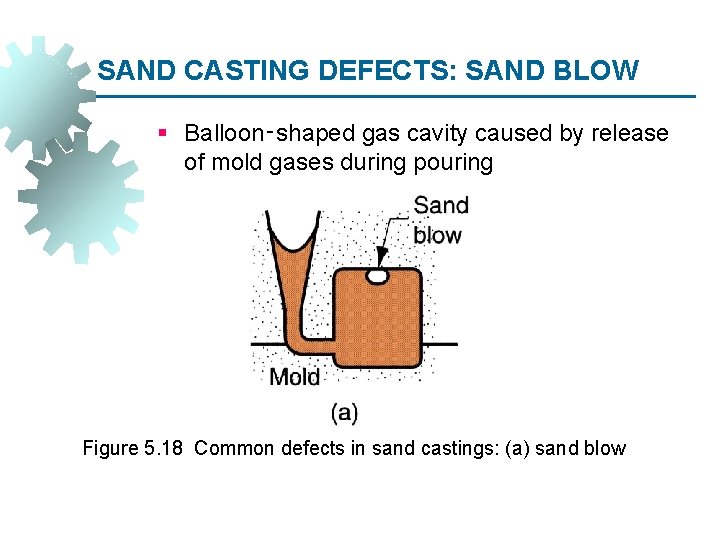
SAND CASTING DEFECTS: SAND BLOW § Balloon‑shaped gas cavity caused by release of mold gases during pouring Figure 5. 18 Common defects in sand castings: (a) sand blow
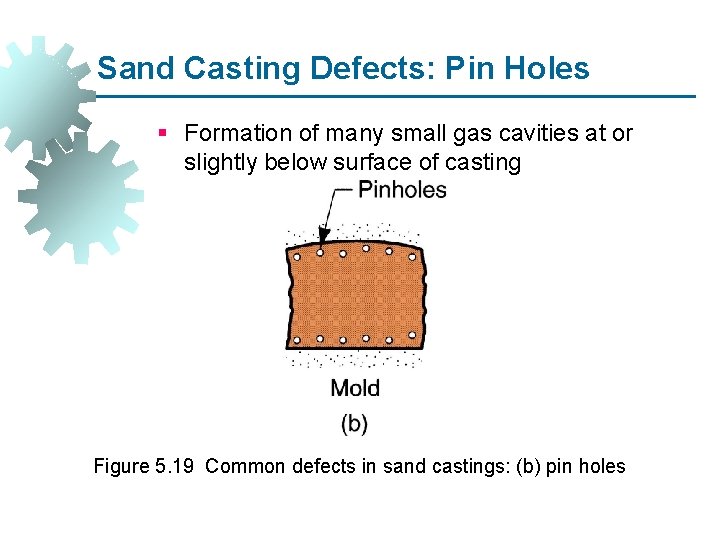
Sand Casting Defects: Pin Holes § Formation of many small gas cavities at or slightly below surface of casting Figure 5. 19 Common defects in sand castings: (b) pin holes
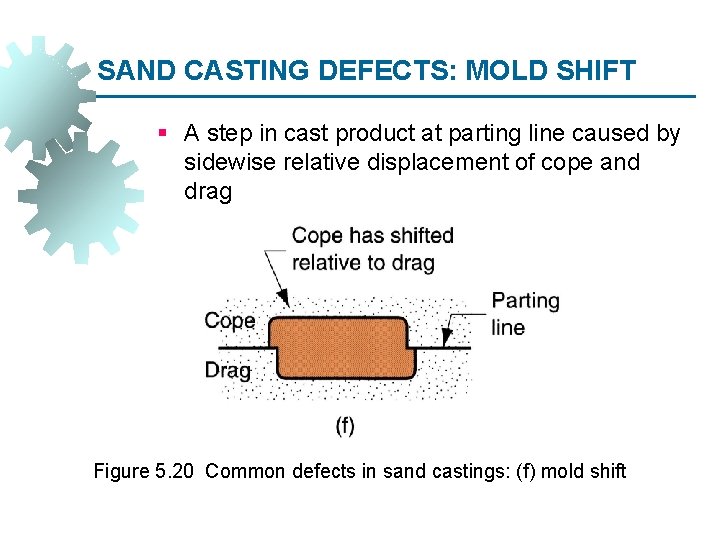
SAND CASTING DEFECTS: MOLD SHIFT § A step in cast product at parting line caused by sidewise relative displacement of cope and drag Figure 5. 20 Common defects in sand castings: (f) mold shift
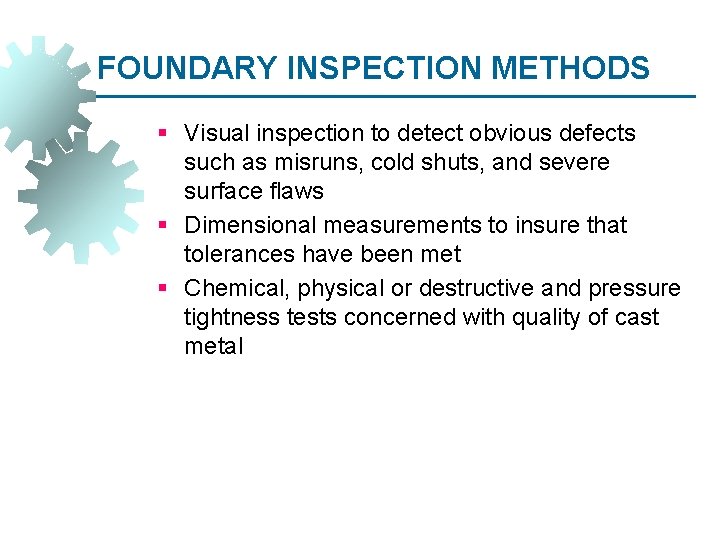
FOUNDARY INSPECTION METHODS § Visual inspection to detect obvious defects such as misruns, cold shuts, and severe surface flaws § Dimensional measurements to insure that tolerances have been met § Chemical, physical or destructive and pressure tightness tests concerned with quality of cast metal
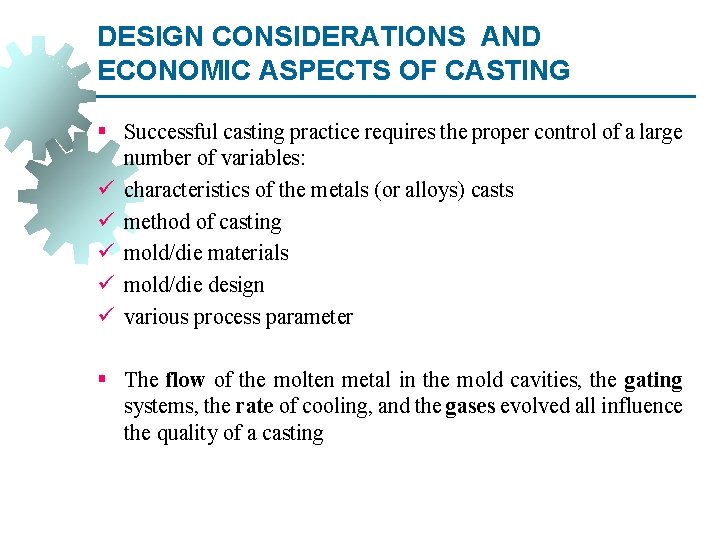
DESIGN CONSIDERATIONS AND ECONOMIC ASPECTS OF CASTING § Successful casting practice requires the proper control of a large number of variables: ü characteristics of the metals (or alloys) casts ü method of casting ü mold/die materials ü mold/die design ü various process parameter § The flow of the molten metal in the mold cavities, the gating systems, the rate of cooling, and the gases evolved all influence the quality of a casting
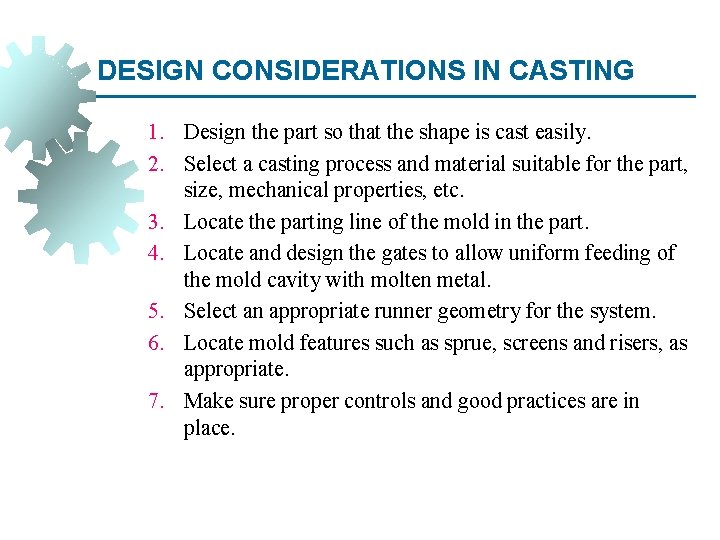
DESIGN CONSIDERATIONS IN CASTING 1. Design the part so that the shape is cast easily. 2. Select a casting process and material suitable for the part, size, mechanical properties, etc. 3. Locate the parting line of the mold in the part. 4. Locate and design the gates to allow uniform feeding of the mold cavity with molten metal. 5. Select an appropriate runner geometry for the system. 6. Locate mold features such as sprue, screens and risers, as appropriate. 7. Make sure proper controls and good practices are in place.
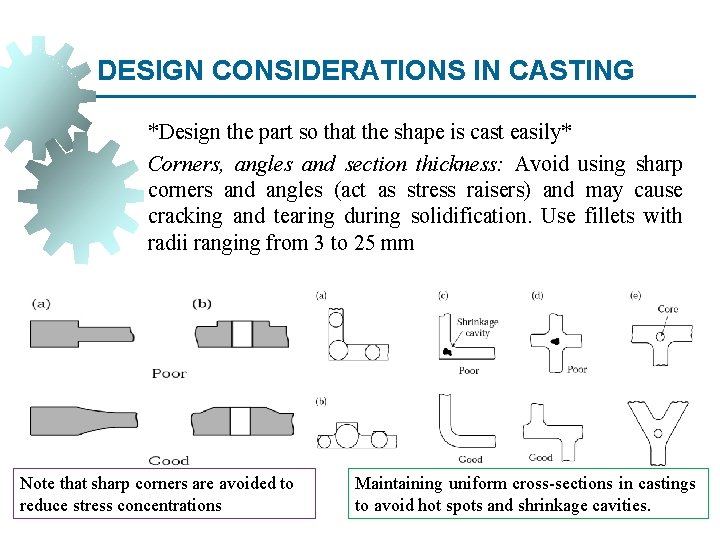
DESIGN CONSIDERATIONS IN CASTING *Design the part so that the shape is cast easily* Corners, angles and section thickness: Avoid using sharp corners and angles (act as stress raisers) and may cause cracking and tearing during solidification. Use fillets with radii ranging from 3 to 25 mm Note that sharp corners are avoided to reduce stress concentrations Maintaining uniform cross-sections in castings to avoid hot spots and shrinkage cavities.
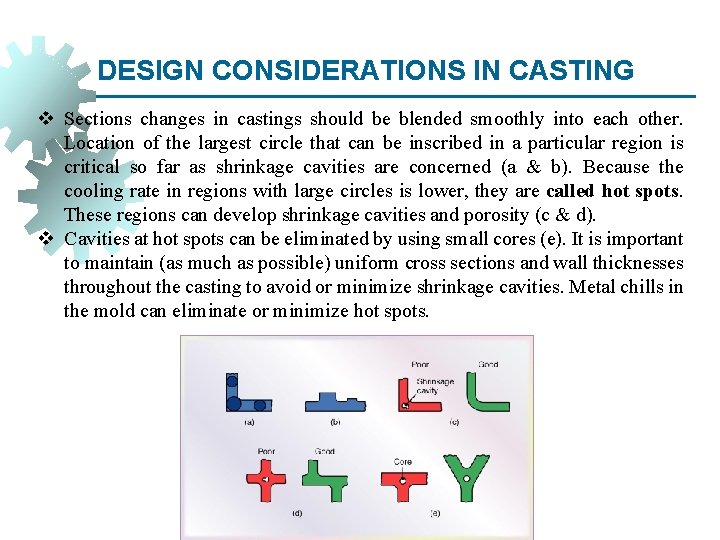
DESIGN CONSIDERATIONS IN CASTING v Sections changes in castings should be blended smoothly into each other. Location of the largest circle that can be inscribed in a particular region is critical so far as shrinkage cavities are concerned (a & b). Because the cooling rate in regions with large circles is lower, they are called hot spots. These regions can develop shrinkage cavities and porosity (c & d). v Cavities at hot spots can be eliminated by using small cores (e). It is important to maintain (as much as possible) uniform cross sections and wall thicknesses throughout the casting to avoid or minimize shrinkage cavities. Metal chills in the mold can eliminate or minimize hot spots.
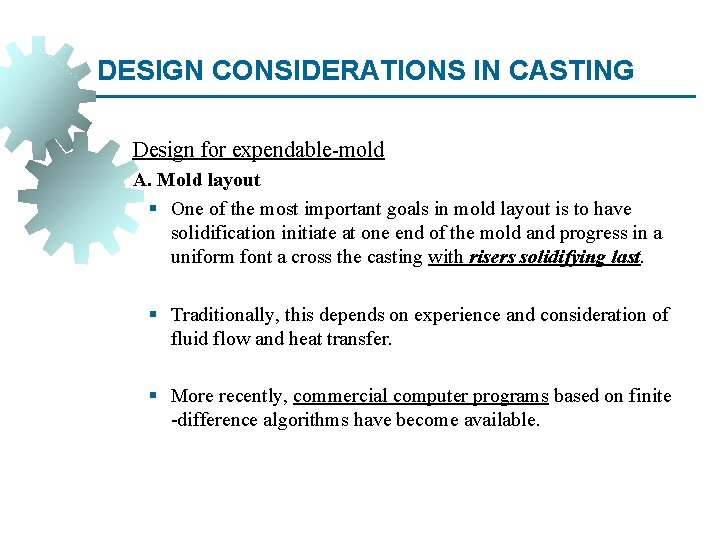
DESIGN CONSIDERATIONS IN CASTING Design for expendable-mold A. Mold layout § One of the most important goals in mold layout is to have solidification initiate at one end of the mold and progress in a uniform font a cross the casting with risers solidifying last. § Traditionally, this depends on experience and consideration of fluid flow and heat transfer. § More recently, commercial computer programs based on finite -difference algorithms have become available.
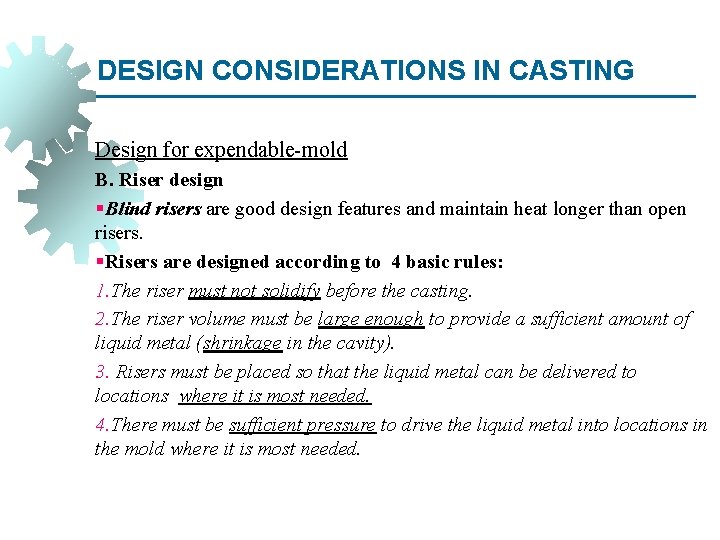
DESIGN CONSIDERATIONS IN CASTING Design for expendable-mold B. Riser design §Blind risers are good design features and maintain heat longer than open risers. §Risers are designed according to 4 basic rules: 1. The riser must not solidify before the casting. 2. The riser volume must be large enough to provide a sufficient amount of liquid metal (shrinkage in the cavity). 3. Risers must be placed so that the liquid metal can be delivered to locations where it is most needed. 4. There must be sufficient pressure to drive the liquid metal into locations in the mold where it is most needed.
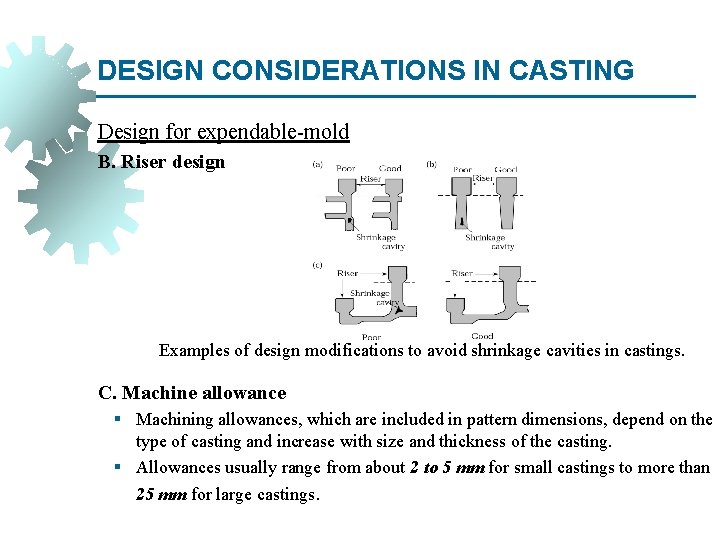
DESIGN CONSIDERATIONS IN CASTING Design for expendable-mold B. Riser design Examples of design modifications to avoid shrinkage cavities in castings. C. Machine allowance § Machining allowances, which are included in pattern dimensions, depend on the type of casting and increase with size and thickness of the casting. § Allowances usually range from about 2 to 5 mm for small castings to more than 25 mm for large castings.
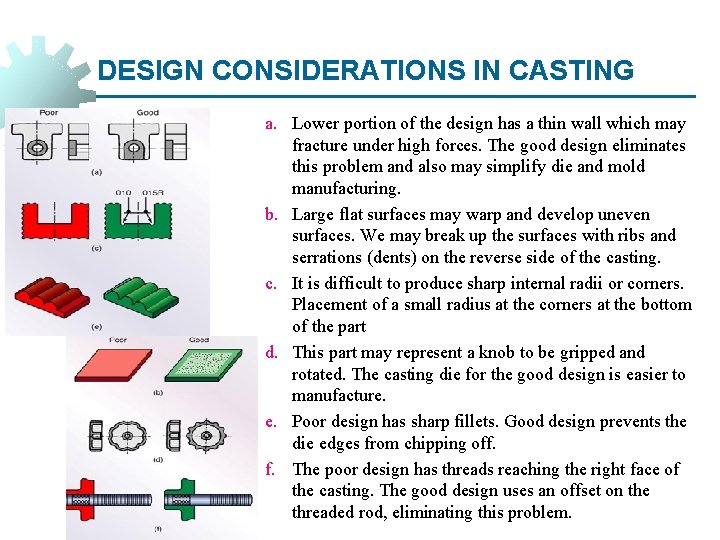
DESIGN CONSIDERATIONS IN CASTING a. Lower portion of the design has a thin wall which may fracture under high forces. The good design eliminates this problem and also may simplify die and mold manufacturing. b. Large flat surfaces may warp and develop uneven surfaces. We may break up the surfaces with ribs and serrations (dents) on the reverse side of the casting. c. It is difficult to produce sharp internal radii or corners. Placement of a small radius at the corners at the bottom of the part d. This part may represent a knob to be gripped and rotated. The casting die for the good design is easier to manufacture. e. Poor design has sharp fillets. Good design prevents the die edges from chipping off. f. The poor design has threads reaching the right face of the casting. The good design uses an offset on the threaded rod, eliminating this problem.
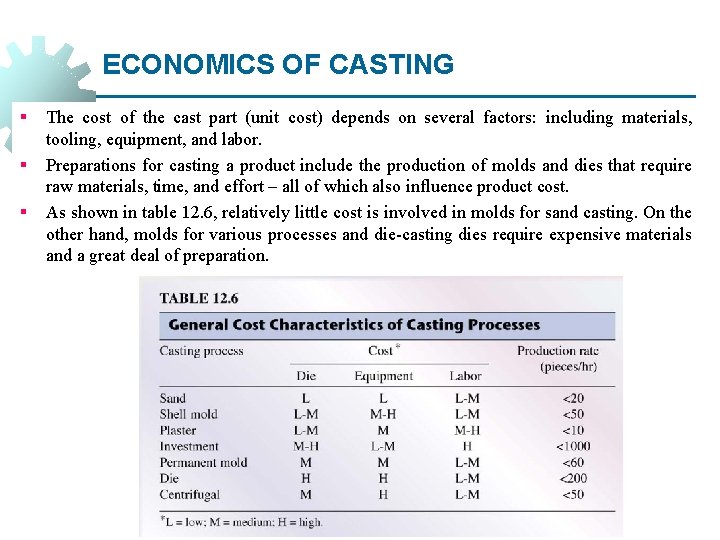
ECONOMICS OF CASTING § § § The cost of the cast part (unit cost) depends on several factors: including materials, tooling, equipment, and labor. Preparations for casting a product include the production of molds and dies that require raw materials, time, and effort – all of which also influence product cost. As shown in table 12. 6, relatively little cost is involved in molds for sand casting. On the other hand, molds for various processes and die-casting dies require expensive materials and a great deal of preparation.
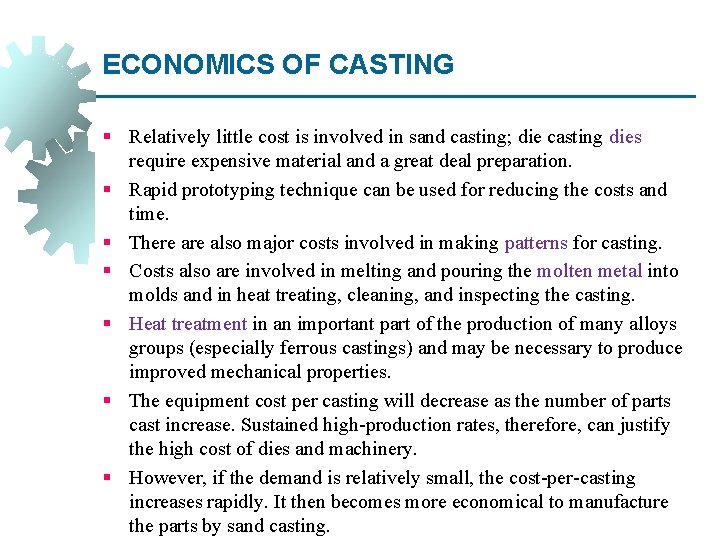
ECONOMICS OF CASTING § Relatively little cost is involved in sand casting; die casting dies require expensive material and a great deal preparation. § Rapid prototyping technique can be used for reducing the costs and time. § There also major costs involved in making patterns for casting. § Costs also are involved in melting and pouring the molten metal into molds and in heat treating, cleaning, and inspecting the casting. § Heat treatment in an important part of the production of many alloys groups (especially ferrous castings) and may be necessary to produce improved mechanical properties. § The equipment cost per casting will decrease as the number of parts cast increase. Sustained high-production rates, therefore, can justify the high cost of dies and machinery. § However, if the demand is relatively small, the cost-per-casting increases rapidly. It then becomes more economical to manufacture the parts by sand casting.
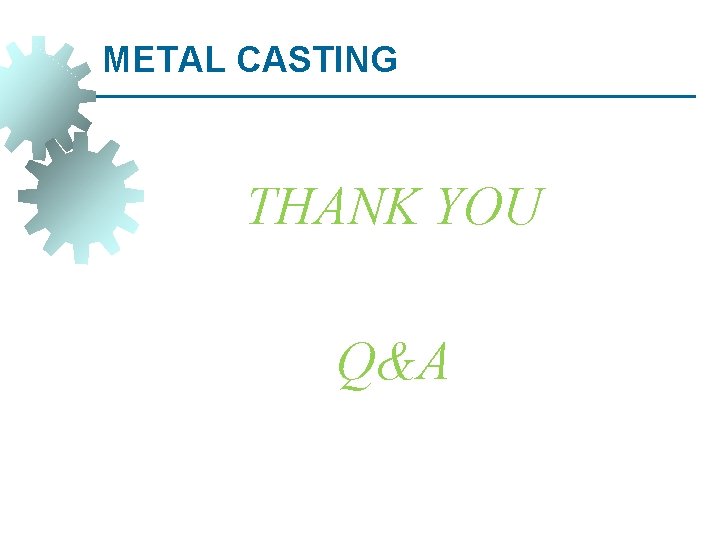
METAL CASTING THANK YOU Q&A