CASTING PDT 253 CASTING v Casting is a
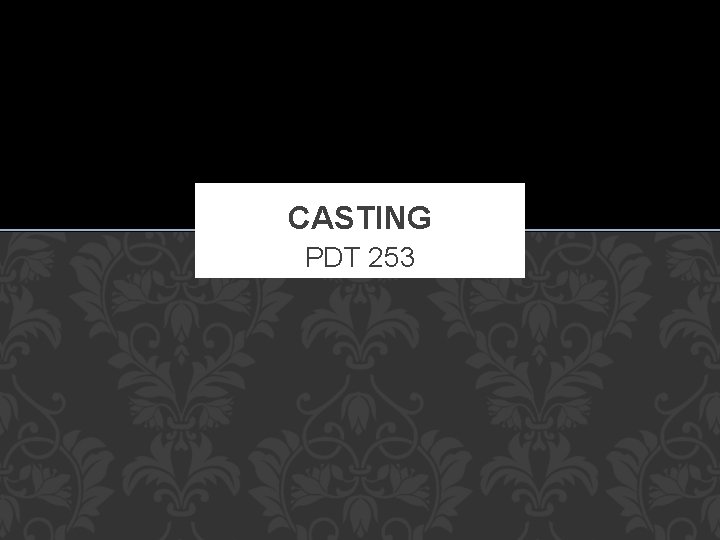
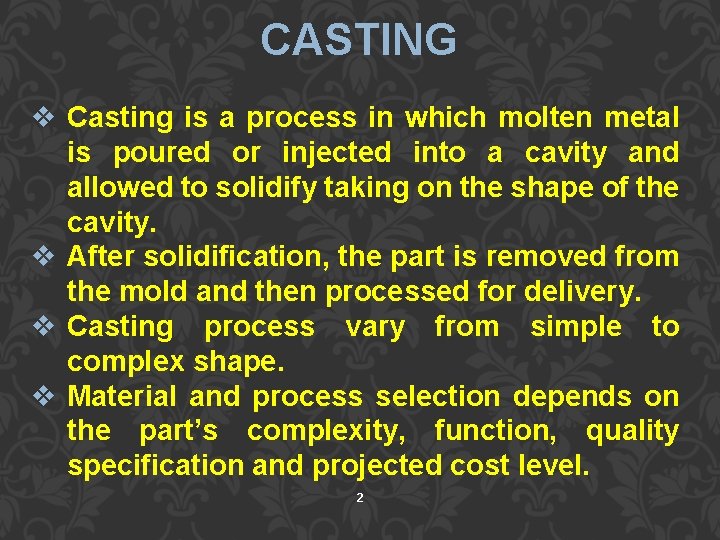
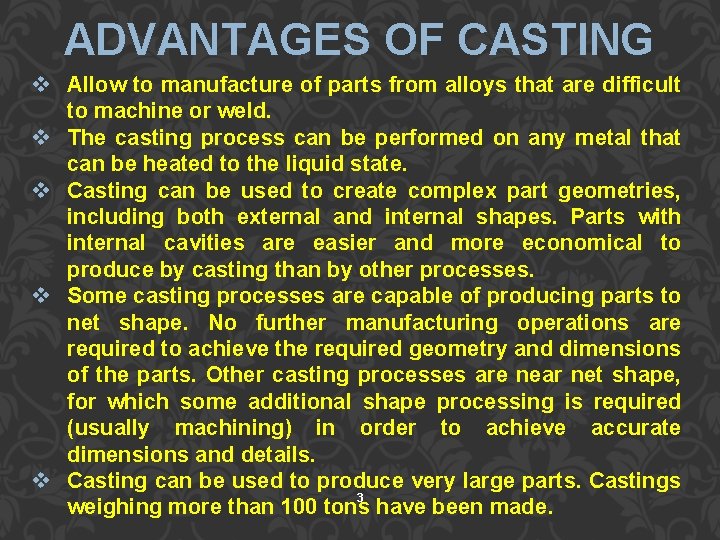
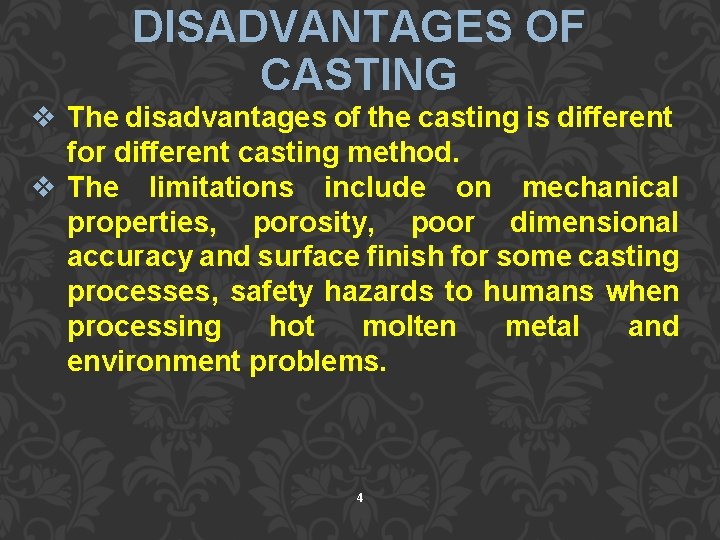
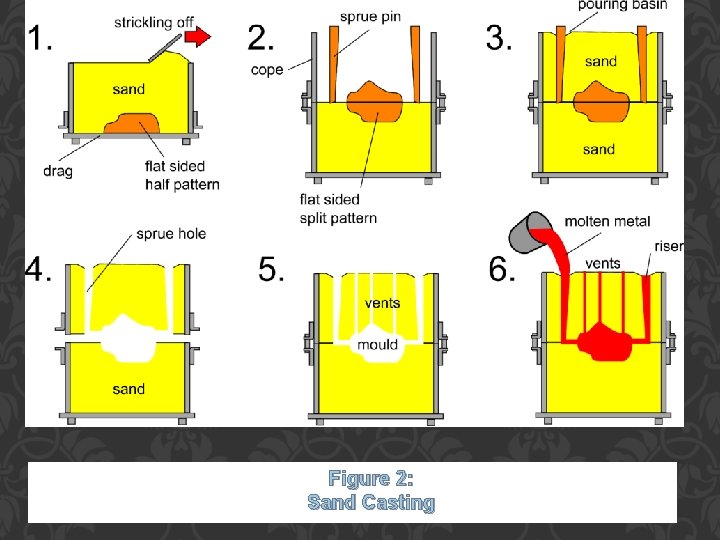
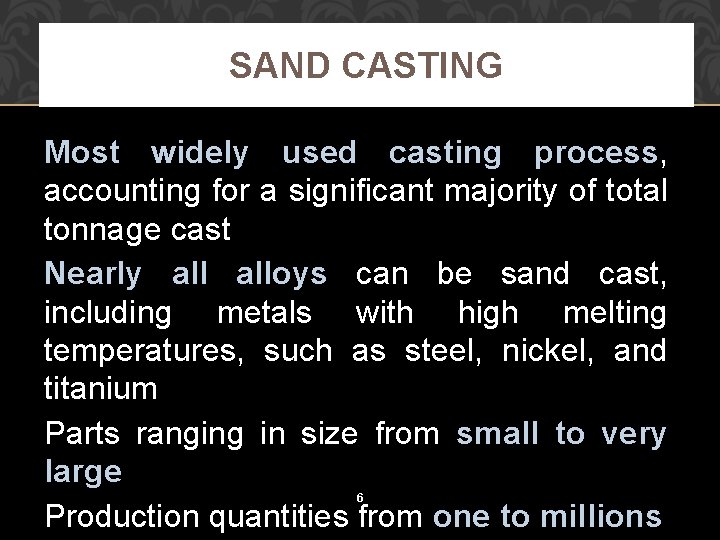
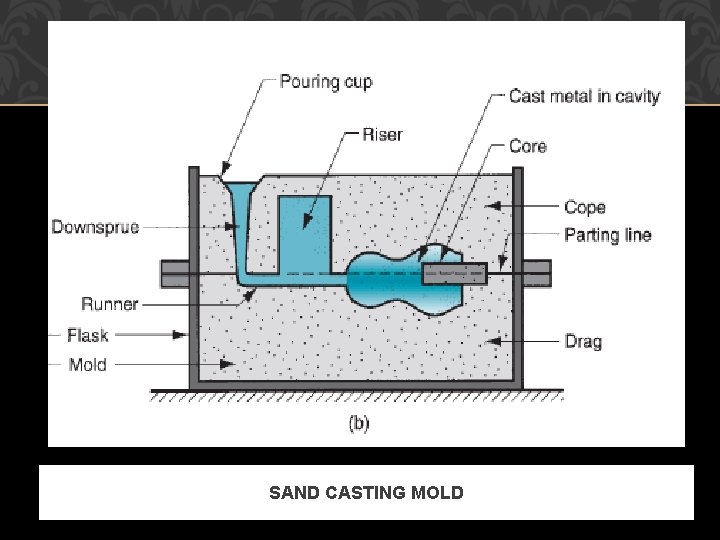
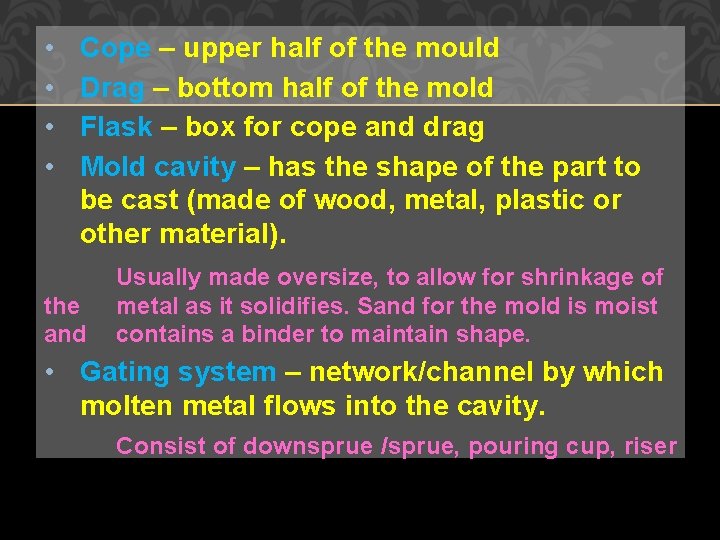

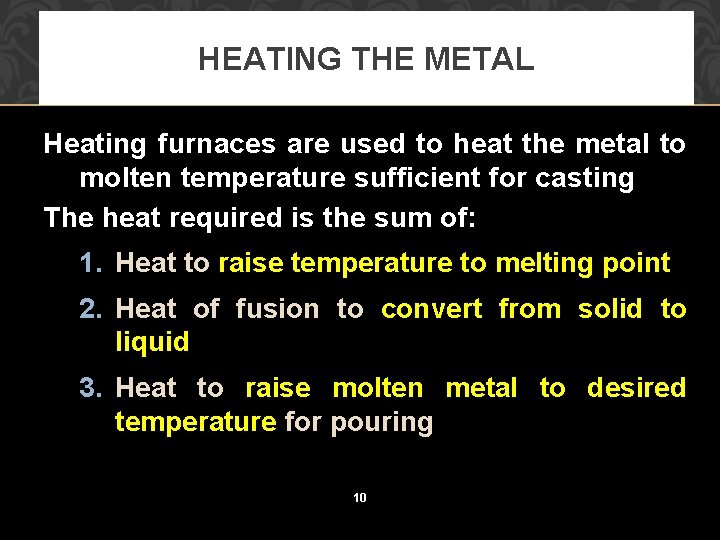
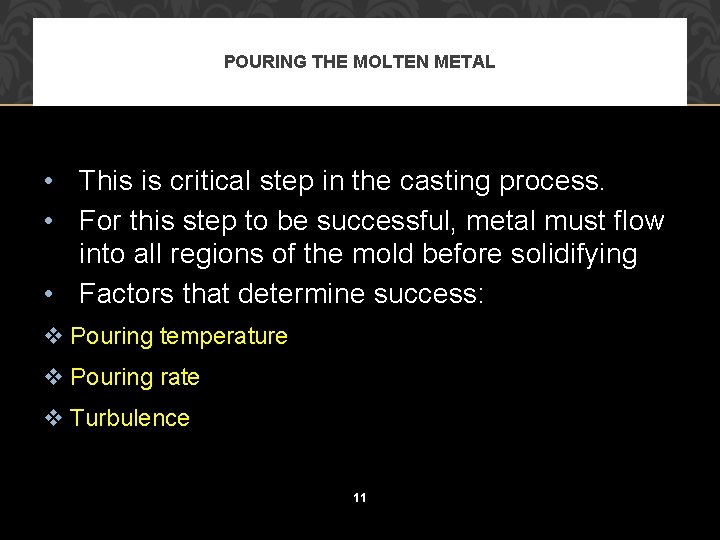
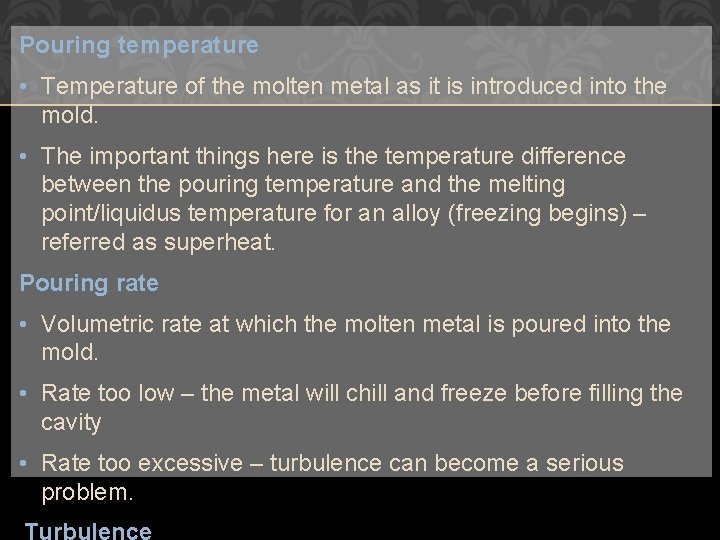
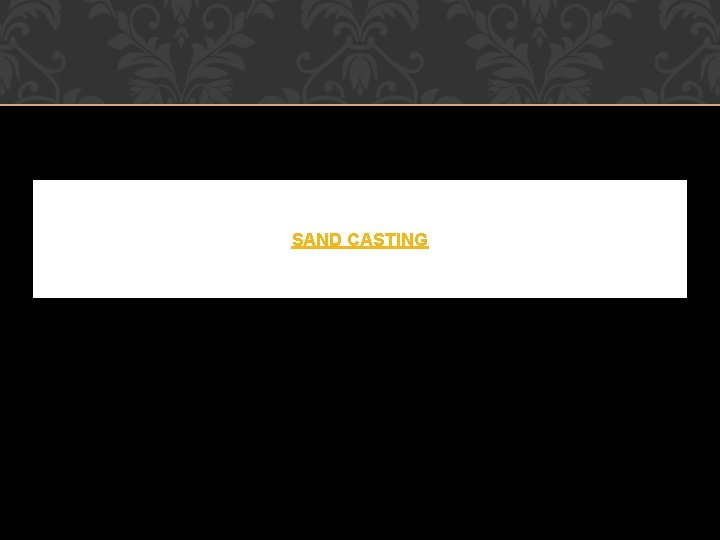
- Slides: 13
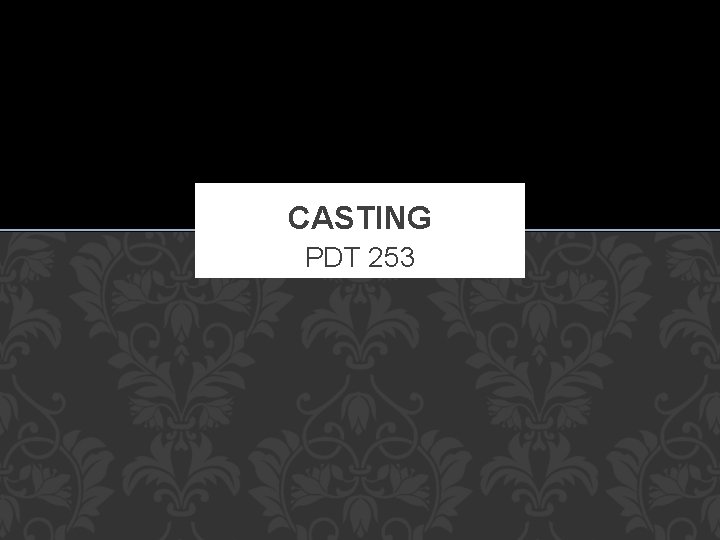
CASTING PDT 253
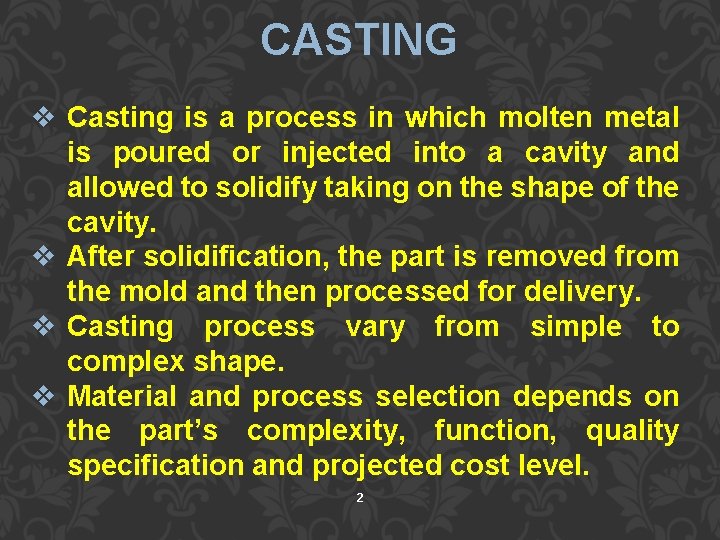
CASTING v Casting is a process in which molten metal is poured or injected into a cavity and allowed to solidify taking on the shape of the cavity. v After solidification, the part is removed from the mold and then processed for delivery. v Casting process vary from simple to complex shape. v Material and process selection depends on the part’s complexity, function, quality specification and projected cost level. 2
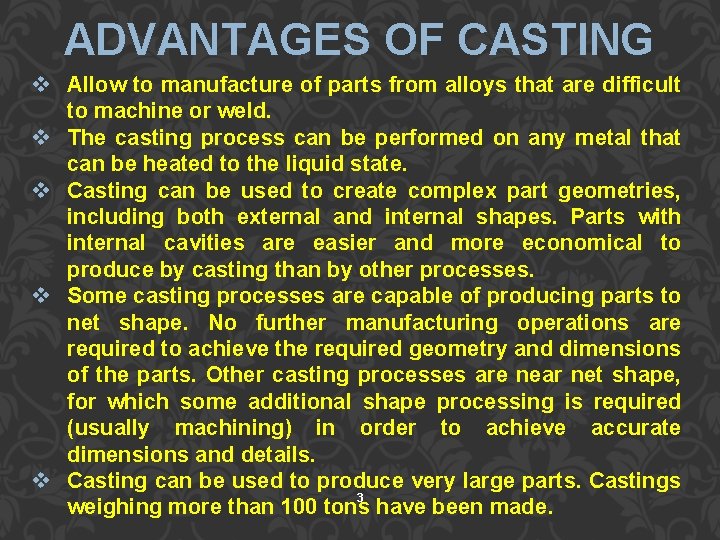
ADVANTAGES OF CASTING v Allow to manufacture of parts from alloys that are difficult to machine or weld. v The casting process can be performed on any metal that can be heated to the liquid state. v Casting can be used to create complex part geometries, including both external and internal shapes. Parts with internal cavities are easier and more economical to produce by casting than by other processes. v Some casting processes are capable of producing parts to net shape. No further manufacturing operations are required to achieve the required geometry and dimensions of the parts. Other casting processes are near net shape, for which some additional shape processing is required (usually machining) in order to achieve accurate dimensions and details. v Casting can be used to produce very large parts. Castings 3 weighing more than 100 tons have been made.
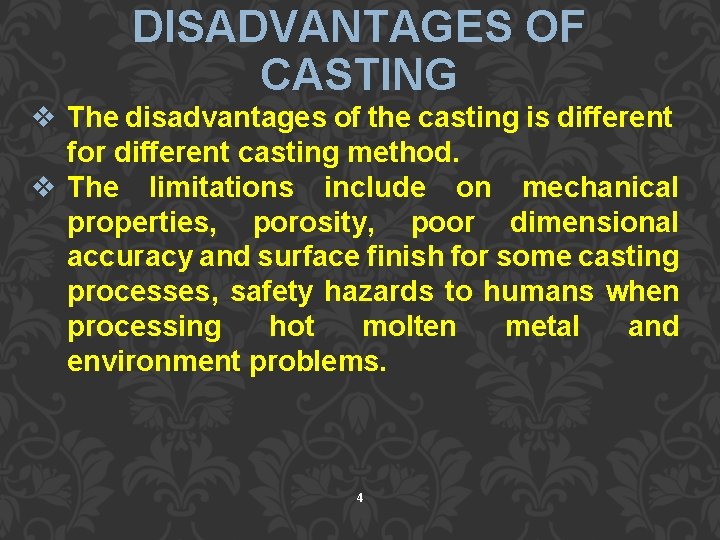
DISADVANTAGES OF CASTING v The disadvantages of the casting is different for different casting method. v The limitations include on mechanical properties, porosity, poor dimensional accuracy and surface finish for some casting processes, safety hazards to humans when processing hot molten metal and environment problems. 4
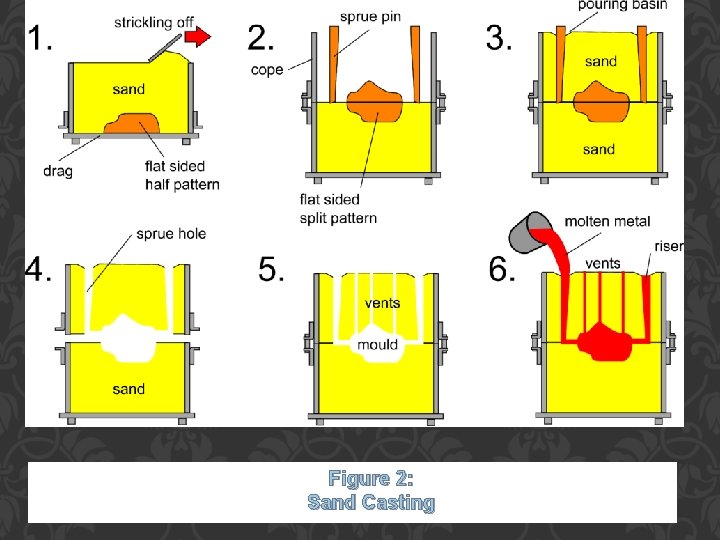
Figure 2: Sand Casting
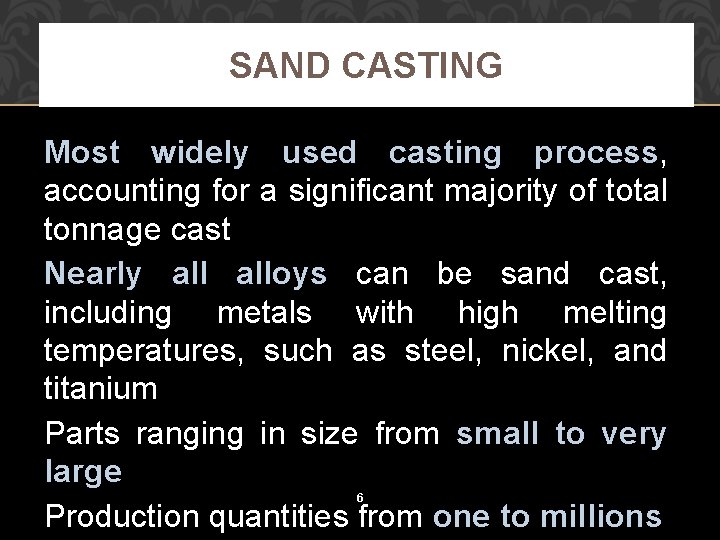
SAND CASTING Most widely used casting process, accounting for a significant majority of total tonnage cast Nearly alloys can be sand cast, including metals with high melting temperatures, such as steel, nickel, and titanium Parts ranging in size from small to very large Production quantities from one to millions 6
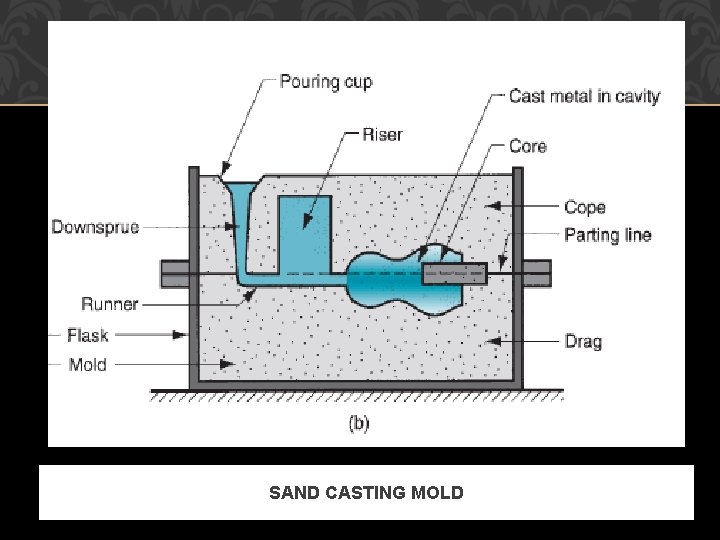
SAND CASTING MOLD
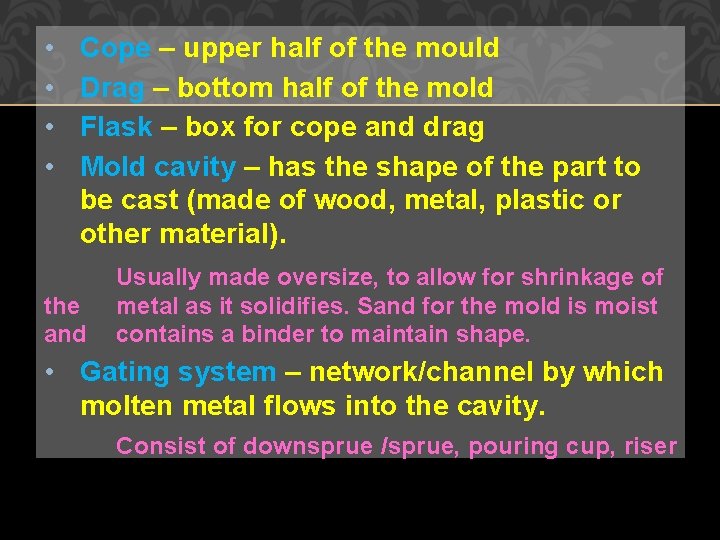
• • Cope – upper half of the mould Drag – bottom half of the mold Flask – box for cope and drag Mold cavity – has the shape of the part to be cast (made of wood, metal, plastic or other material). the and Usually made oversize, to allow for shrinkage of metal as it solidifies. Sand for the mold is moist contains a binder to maintain shape. • Gating system – network/channel by which molten metal flows into the cavity. Consist of downsprue /sprue, pouring cup, riser

• Downsprue/sprue – runner that leads molten metal into the main cavity • Pouring cups – open channel leading to the sprue, to minimize splash and turbulence as the metal flows. • Riser – reservoir in the mold, serve as a source of liquid metal to compensate for shrinkage during solidification. • Small vents holes are drilled into the mold or machined into the parting line to permit removal of air and gases. Natural porosity of the sand also permits the air and gases to
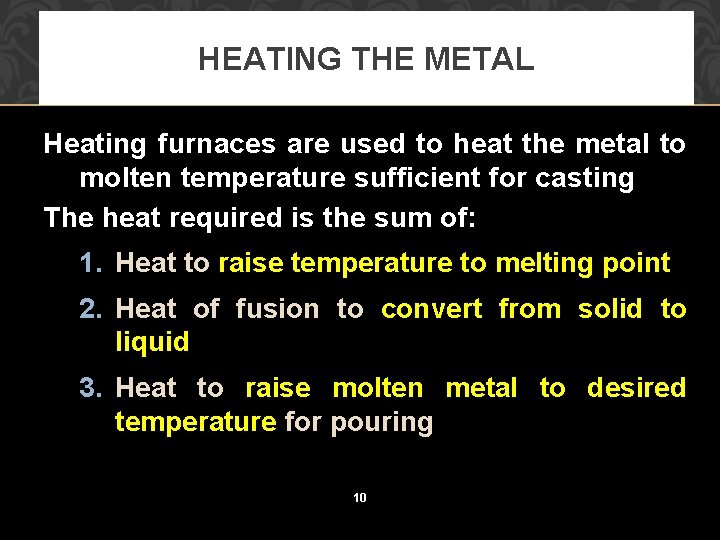
HEATING THE METAL Heating furnaces are used to heat the metal to molten temperature sufficient for casting The heat required is the sum of: 1. Heat to raise temperature to melting point 2. Heat of fusion to convert from solid to liquid 3. Heat to raise molten metal to desired temperature for pouring 10
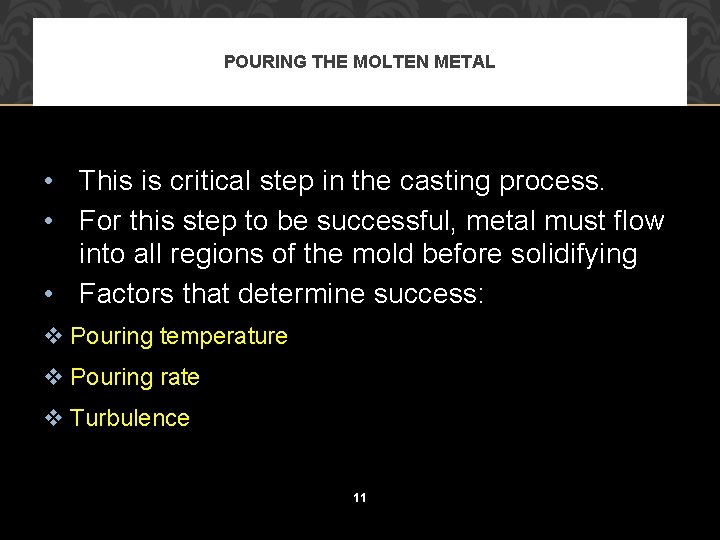
POURING THE MOLTEN METAL • This is critical step in the casting process. • For this step to be successful, metal must flow into all regions of the mold before solidifying • Factors that determine success: v Pouring temperature v Pouring rate v Turbulence 11
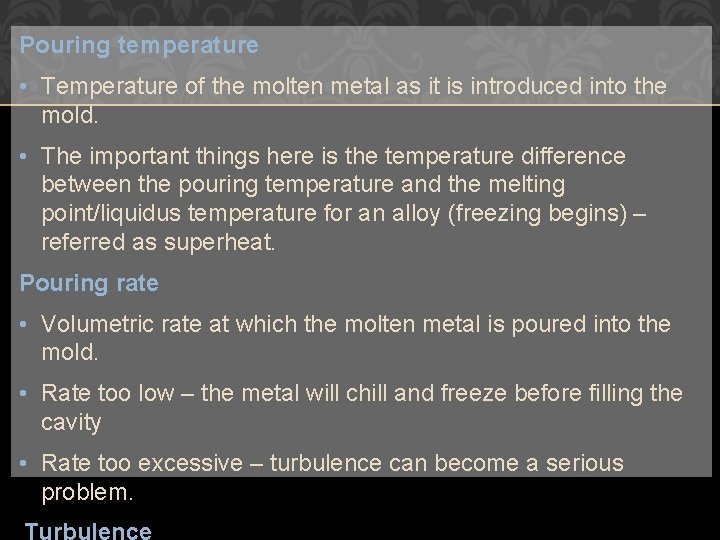
Pouring temperature • Temperature of the molten metal as it is introduced into the mold. • The important things here is the temperature difference between the pouring temperature and the melting point/liquidus temperature for an alloy (freezing begins) – referred as superheat. Pouring rate • Volumetric rate at which the molten metal is poured into the mold. • Rate too low – the metal will chill and freeze before filling the cavity • Rate too excessive – turbulence can become a serious problem.
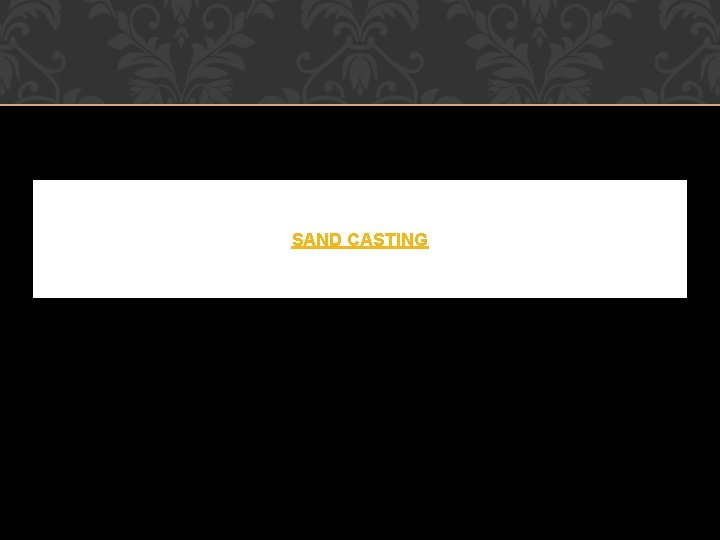
SAND CASTING