BETON KALTE KONTROL BETON RETMNDE KULLANILAN MALZEMELER ZERNDE
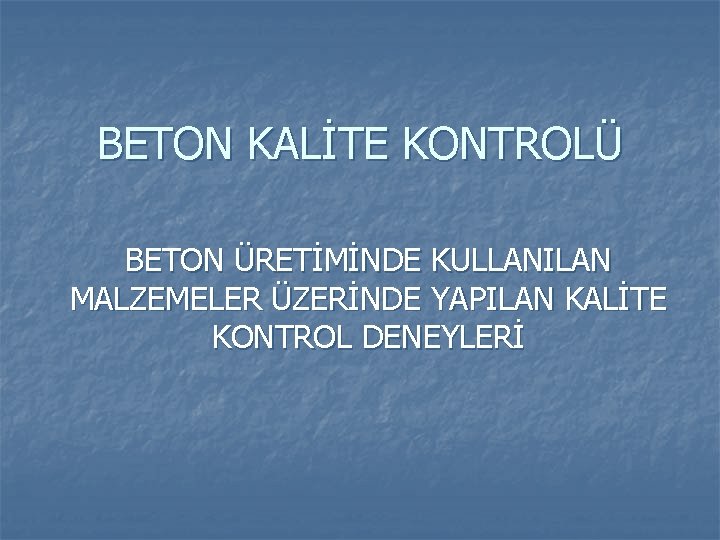
BETON KALİTE KONTROLÜ BETON ÜRETİMİNDE KULLANILAN MALZEMELER ÜZERİNDE YAPILAN KALİTE KONTROL DENEYLERİ
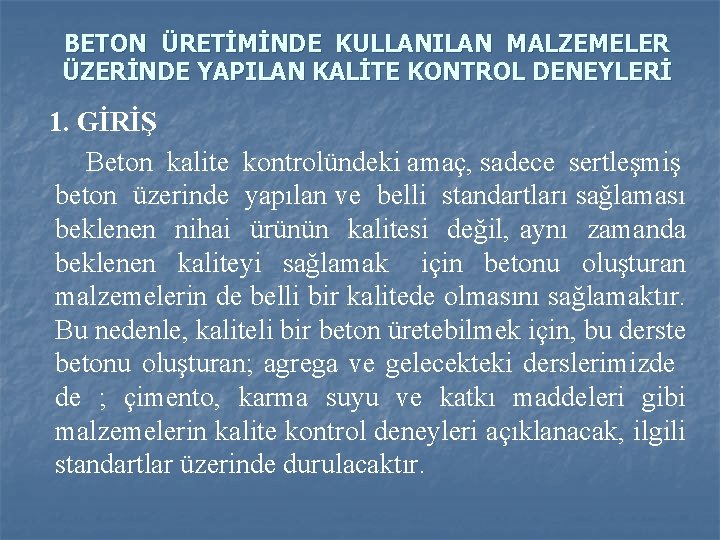
BETON ÜRETİMİNDE KULLANILAN MALZEMELER ÜZERİNDE YAPILAN KALİTE KONTROL DENEYLERİ 1. GİRİŞ Beton kalite kontrolündeki amaç, sadece sertleşmiş beton üzerinde yapılan ve belli standartları sağlaması beklenen nihai ürünün kalitesi değil, aynı zamanda beklenen kaliteyi sağlamak için betonu oluşturan malzemelerin de belli bir kalitede olmasını sağlamaktır. Bu nedenle, kaliteli bir beton üretebilmek için, bu derste betonu oluşturan; agrega ve gelecekteki derslerimizde de ; çimento, karma suyu ve katkı maddeleri gibi malzemelerin kalite kontrol deneyleri açıklanacak, ilgili standartlar üzerinde durulacaktır.
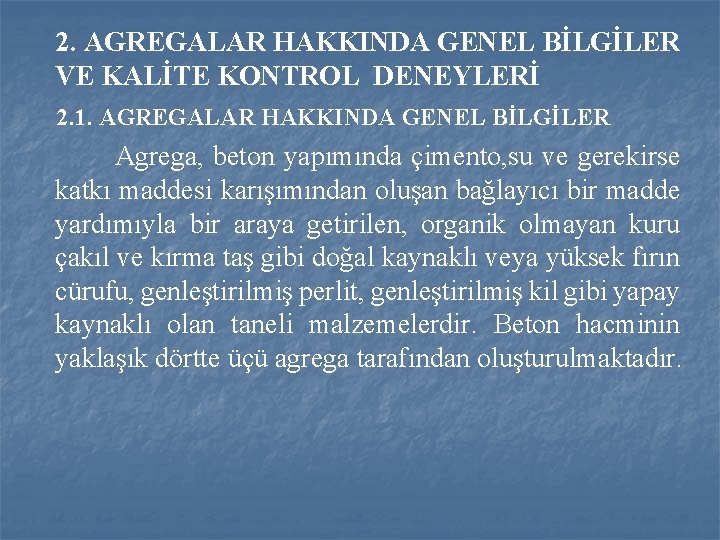
2. AGREGALAR HAKKINDA GENEL BİLGİLER VE KALİTE KONTROL DENEYLERİ 2. 1. AGREGALAR HAKKINDA GENEL BİLGİLER Agrega, beton yapımında çimento, su ve gerekirse katkı maddesi karışımından oluşan bağlayıcı bir madde yardımıyla bir araya getirilen, organik olmayan kuru çakıl ve kırma taş gibi doğal kaynaklı veya yüksek fırın cürufu, genleştirilmiş perlit, genleştirilmiş kil gibi yapay kaynaklı olan taneli malzemelerdir. Beton hacminin yaklaşık dörtte üçü agrega tarafından oluşturulmaktadır.
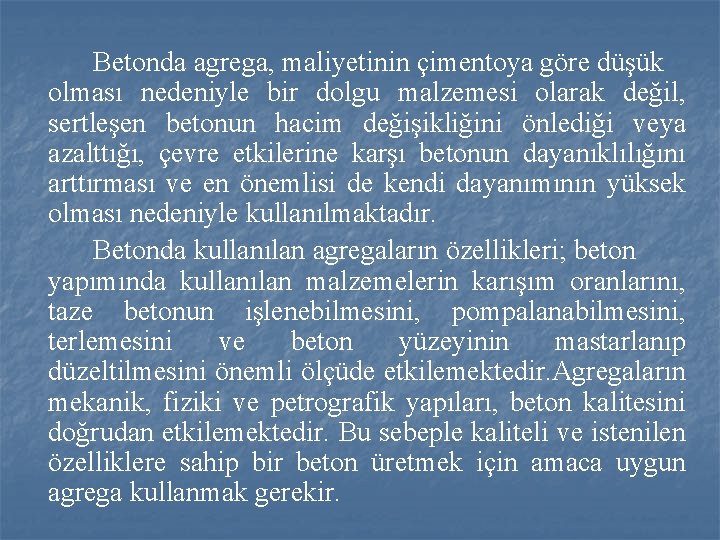
Betonda agrega, maliyetinin çimentoya göre düşük olması nedeniyle bir dolgu malzemesi olarak değil, sertleşen betonun hacim değişikliğini önlediği veya azalttığı, çevre etkilerine karşı betonun dayanıklılığını arttırması ve en önemlisi de kendi dayanımının yüksek olması nedeniyle kullanılmaktadır. Betonda kullanılan agregaların özellikleri; beton yapımında kullanılan malzemelerin karışım oranlarını, taze betonun işlenebilmesini, pompalanabilmesini, terlemesini ve beton yüzeyinin mastarlanıp düzeltilmesini önemli ölçüde etkilemektedir. Agregaların mekanik, fiziki ve petrografik yapıları, beton kalitesini doğrudan etkilemektedir. Bu sebeple kaliteli ve istenilen özelliklere sahip bir beton üretmek için amaca uygun agrega kullanmak gerekir.
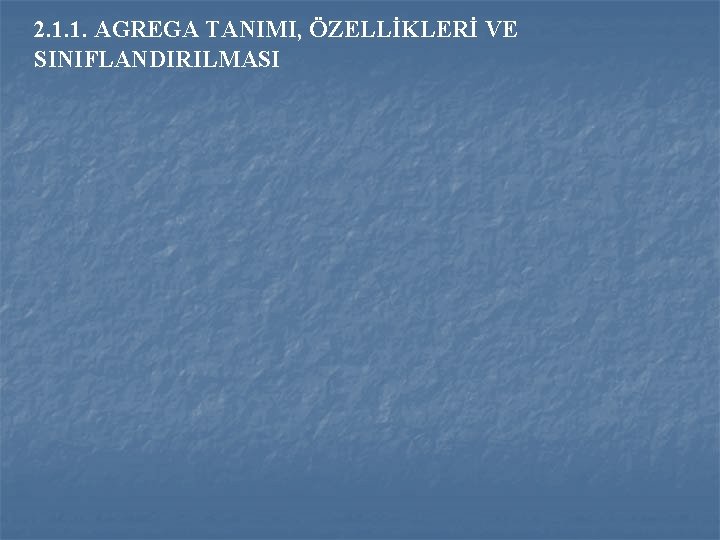
2. 1. 1. AGREGA TANIMI, ÖZELLİKLERİ VE SINIFLANDIRILMASI
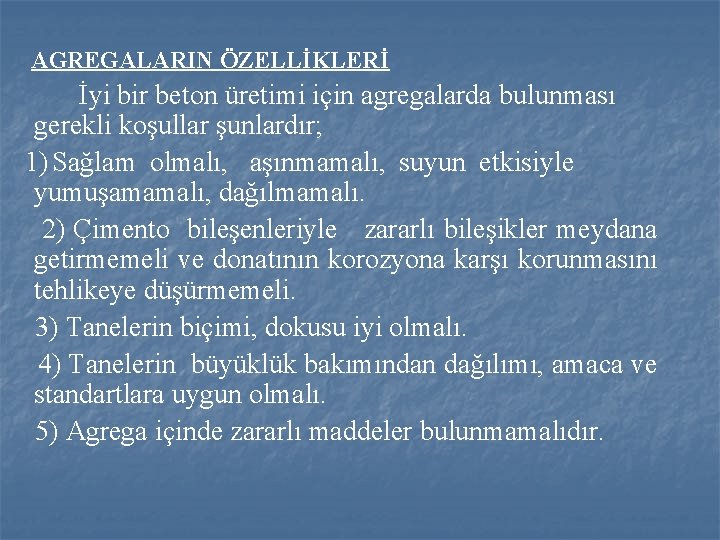
AGREGALARIN ÖZELLİKLERİ İyi bir beton üretimi için agregalarda bulunması gerekli koşullar şunlardır; 1) Sağlam olmalı, aşınmamalı, suyun etkisiyle yumuşamamalı, dağılmamalı. 2) Çimento bileşenleriyle zararlı bileşikler meydana getirmemeli ve donatının korozyona karşı korunmasını tehlikeye düşürmemeli. 3) Tanelerin biçimi, dokusu iyi olmalı. 4) Tanelerin büyüklük bakımından dağılımı, amaca ve standartlara uygun olmalı. 5) Agrega içinde zararlı maddeler bulunmamalıdır.
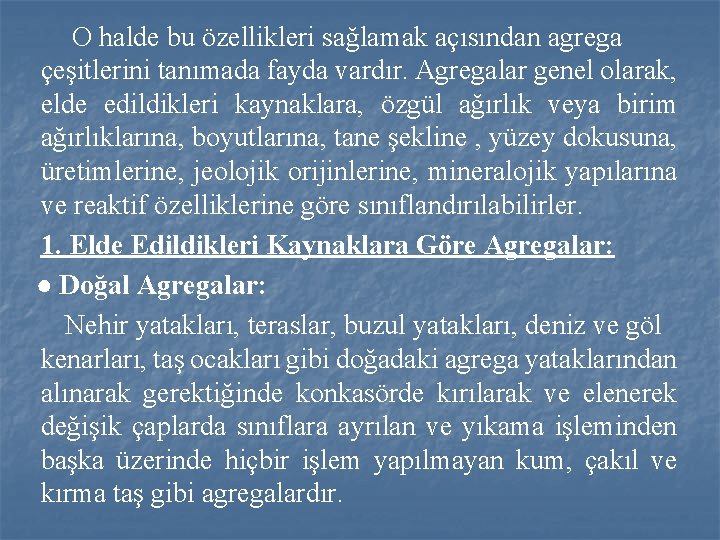
O halde bu özellikleri sağlamak açısından agrega çeşitlerini tanımada fayda vardır. Agregalar genel olarak, elde edildikleri kaynaklara, özgül ağırlık veya birim ağırlıklarına, boyutlarına, tane şekline , yüzey dokusuna, üretimlerine, jeolojik orijinlerine, mineralojik yapılarına ve reaktif özelliklerine göre sınıflandırılabilirler. 1. Elde Edildikleri Kaynaklara Göre Agregalar: ● Doğal Agregalar: Nehir yatakları, teraslar, buzul yatakları, deniz ve göl kenarları, taş ocakları gibi doğadaki agrega yataklarından alınarak gerektiğinde konkasörde kırılarak ve elenerek değişik çaplarda sınıflara ayrılan ve yıkama işleminden başka üzerinde hiçbir işlem yapılmayan kum, çakıl ve kırma taş gibi agregalardır.
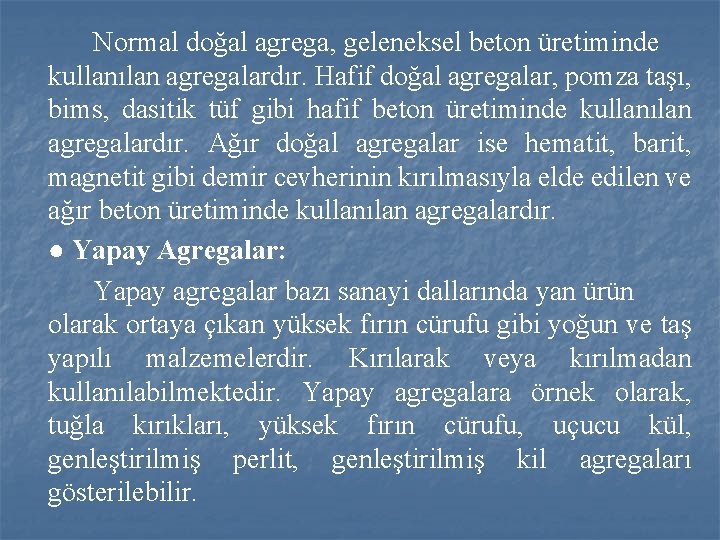
Normal doğal agrega, geleneksel beton üretiminde kullanılan agregalardır. Hafif doğal agregalar, pomza taşı, bims, dasitik tüf gibi hafif beton üretiminde kullanılan agregalardır. Ağır doğal agregalar ise hematit, barit, magnetit gibi demir cevherinin kırılmasıyla elde edilen ve ağır beton üretiminde kullanılan agregalardır. ● Yapay Agregalar: Yapay agregalar bazı sanayi dallarında yan ürün olarak ortaya çıkan yüksek fırın cürufu gibi yoğun ve taş yapılı malzemelerdir. Kırılarak veya kırılmadan kullanılabilmektedir. Yapay agregalara örnek olarak, tuğla kırıkları, yüksek fırın cürufu, uçucu kül, genleştirilmiş perlit, genleştirilmiş kil agregaları gösterilebilir.
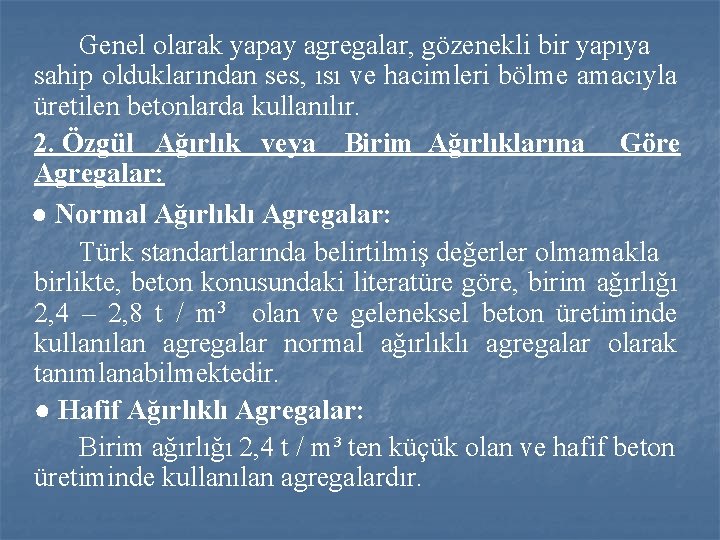
Genel olarak yapay agregalar, gözenekli bir yapıya sahip olduklarından ses, ısı ve hacimleri bölme amacıyla üretilen betonlarda kullanılır. 2. Özgül Ağırlık veya Birim Ağırlıklarına Göre Agregalar: ● Normal Ağırlıklı Agregalar: Türk standartlarında belirtilmiş değerler olmamakla birlikte, beton konusundaki literatüre göre, birim ağırlığı 2, 4 – 2, 8 t / m 3 olan ve geleneksel beton üretiminde kullanılan agregalar normal ağırlıklı agregalar olarak tanımlanabilmektedir. ● Hafif Ağırlıklı Agregalar: Birim ağırlığı 2, 4 t / m³ ten küçük olan ve hafif beton üretiminde kullanılan agregalardır.
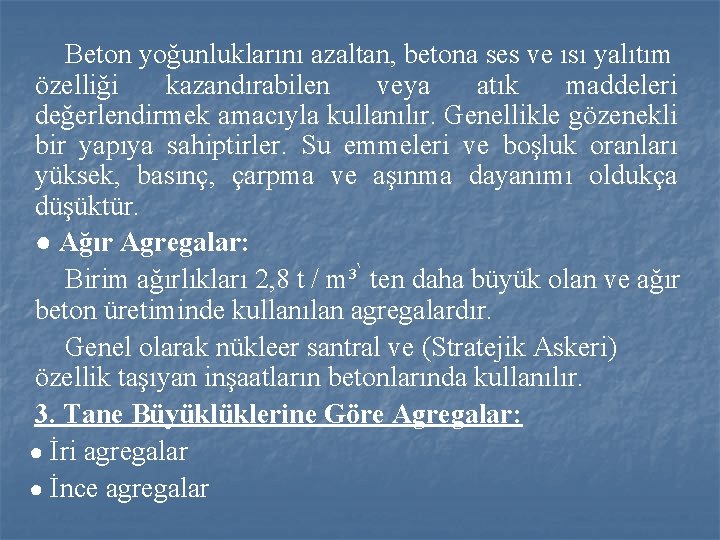
Beton yoğunluklarını azaltan, betona ses ve ısı yalıtım özelliği kazandırabilen veya atık maddeleri değerlendirmek amacıyla kullanılır. Genellikle gözenekli bir yapıya sahiptirler. Su emmeleri ve boşluk oranları yüksek, basınç, çarpma ve aşınma dayanımı oldukça düşüktür. ● Ağır Agregalar: Birim ağırlıkları 2, 8 t / m³ ten daha büyük olan ve ağır beton üretiminde kullanılan agregalardır. Genel olarak nükleer santral ve (Stratejik Askeri) özellik taşıyan inşaatların betonlarında kullanılır. 3. Tane Büyüklüklerine Göre Agregalar: ● İri agregalar ● İnce agregalar
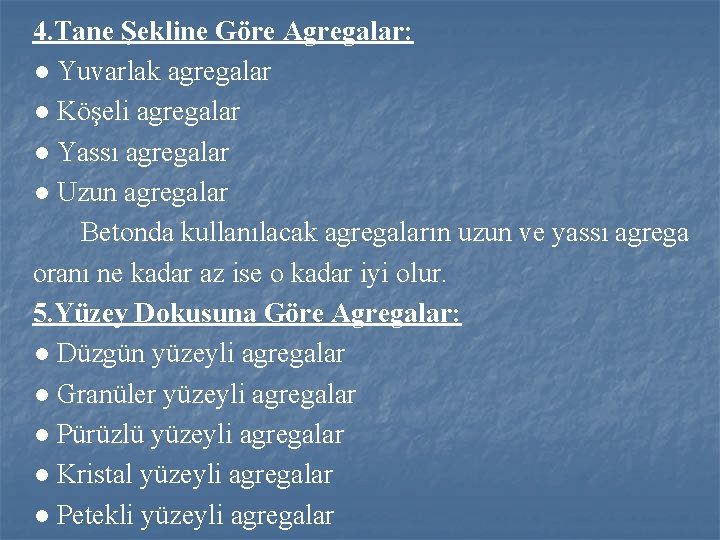
4. Tane Şekline Göre Agregalar: ● Yuvarlak agregalar ● Köşeli agregalar ● Yassı agregalar ● Uzun agregalar Betonda kullanılacak agregaların uzun ve yassı agrega oranı ne kadar az ise o kadar iyi olur. 5. Yüzey Dokusuna Göre Agregalar: ● Düzgün yüzeyli agregalar ● Granüler yüzeyli agregalar ● Pürüzlü yüzeyli agregalar ● Kristal yüzeyli agregalar ● Petekli yüzeyli agregalar
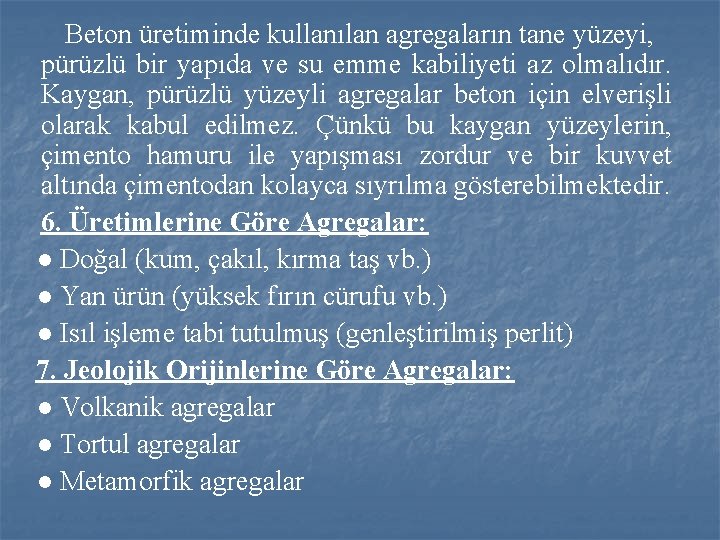
Beton üretiminde kullanılan agregaların tane yüzeyi, pürüzlü bir yapıda ve su emme kabiliyeti az olmalıdır. Kaygan, pürüzlü yüzeyli agregalar beton için elverişli olarak kabul edilmez. Çünkü bu kaygan yüzeylerin, çimento hamuru ile yapışması zordur ve bir kuvvet altında çimentodan kolayca sıyrılma gösterebilmektedir. 6. Üretimlerine Göre Agregalar: ● Doğal (kum, çakıl, kırma taş vb. ) ● Yan ürün (yüksek fırın cürufu vb. ) ● Isıl işleme tabi tutulmuş (genleştirilmiş perlit) 7. Jeolojik Orijinlerine Göre Agregalar: ● Volkanik agregalar ● Tortul agregalar ● Metamorfik agregalar
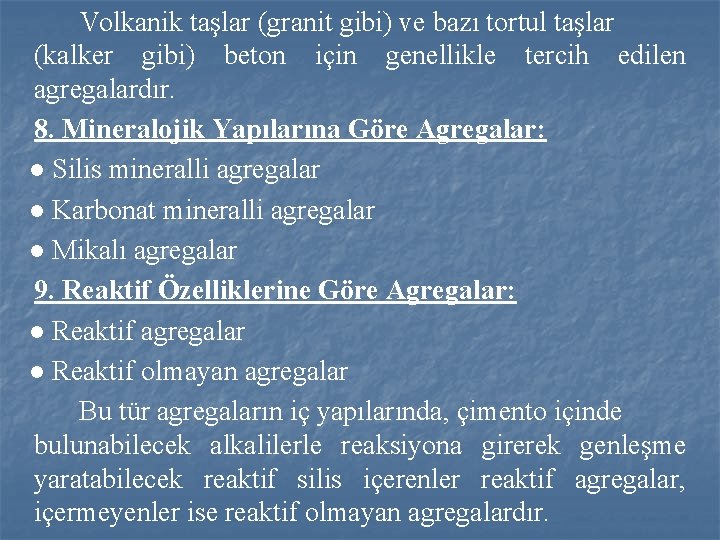
Volkanik taşlar (granit gibi) ve bazı tortul taşlar (kalker gibi) beton için genellikle tercih edilen agregalardır. 8. Mineralojik Yapılarına Göre Agregalar: ● Silis mineralli agregalar ● Karbonat mineralli agregalar ● Mikalı agregalar 9. Reaktif Özelliklerine Göre Agregalar: ● Reaktif agregalar ● Reaktif olmayan agregalar Bu tür agregaların iç yapılarında, çimento içinde bulunabilecek alkalilerle reaksiyona girerek genleşme yaratabilecek reaktif silis içerenler reaktif agregalar, içermeyenler ise reaktif olmayan agregalardır.
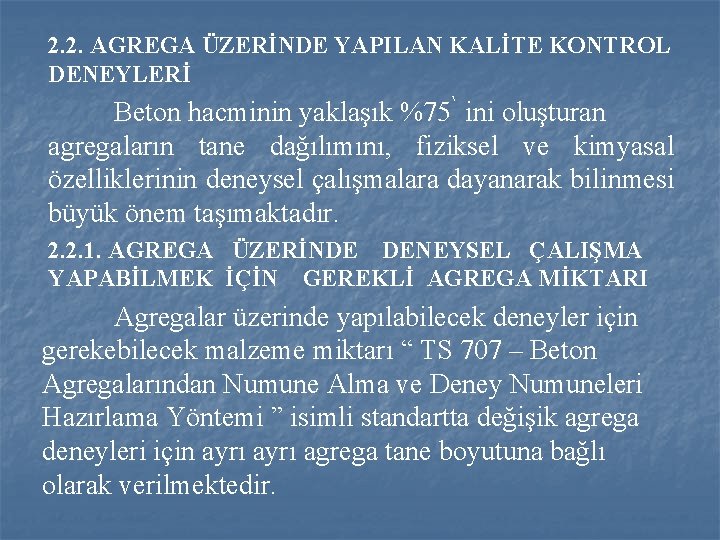
2. 2. AGREGA ÜZERİNDE YAPILAN KALİTE KONTROL DENEYLERİ Beton hacminin yaklaşık %75 ini oluşturan agregaların tane dağılımını, fiziksel ve kimyasal özelliklerinin deneysel çalışmalara dayanarak bilinmesi büyük önem taşımaktadır. 2. 2. 1. AGREGA ÜZERİNDE DENEYSEL ÇALIŞMA YAPABİLMEK İÇİN GEREKLİ AGREGA MİKTARI Agregalar üzerinde yapılabilecek deneyler için gerekebilecek malzeme miktarı “ TS 707 – Beton Agregalarından Numune Alma ve Deney Numuneleri Hazırlama Yöntemi ” isimli standartta değişik agrega deneyleri için ayrı agrega tane boyutuna bağlı olarak verilmektedir.
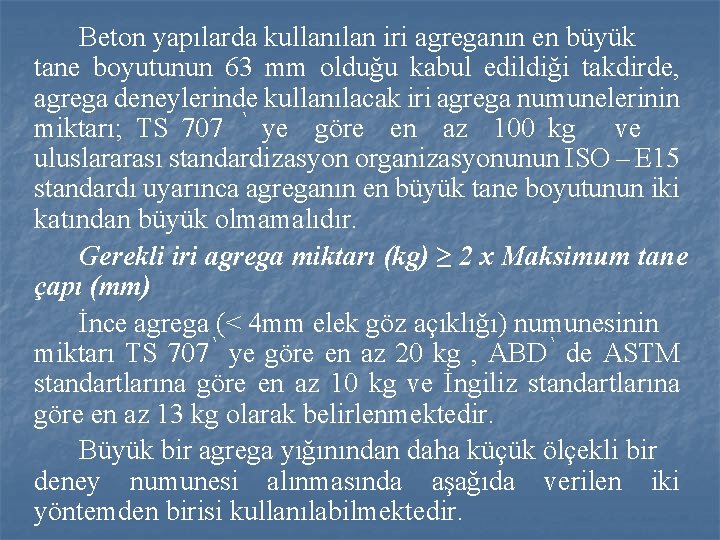
Beton yapılarda kullanılan iri agreganın en büyük tane boyutunun 63 mm olduğu kabul edildiği takdirde, agrega deneylerinde kullanılacak iri agrega numunelerinin miktarı; TS 707 ye göre en az 100 kg ve uluslararası standardizasyon organizasyonunun ISO – E 15 standardı uyarınca agreganın en büyük tane boyutunun iki katından büyük olmamalıdır. Gerekli iri agrega miktarı (kg) ≥ 2 x Maksimum tane çapı (mm) İnce agrega (< 4 mm elek göz açıklığı) numunesinin miktarı TS 707 ye göre en az 20 kg , ABD de ASTM standartlarına göre en az 10 kg ve İngiliz standartlarına göre en az 13 kg olarak belirlenmektedir. Büyük bir agrega yığınından daha küçük ölçekli bir deney numunesi alınmasında aşağıda verilen iki yöntemden birisi kullanılabilmektedir.
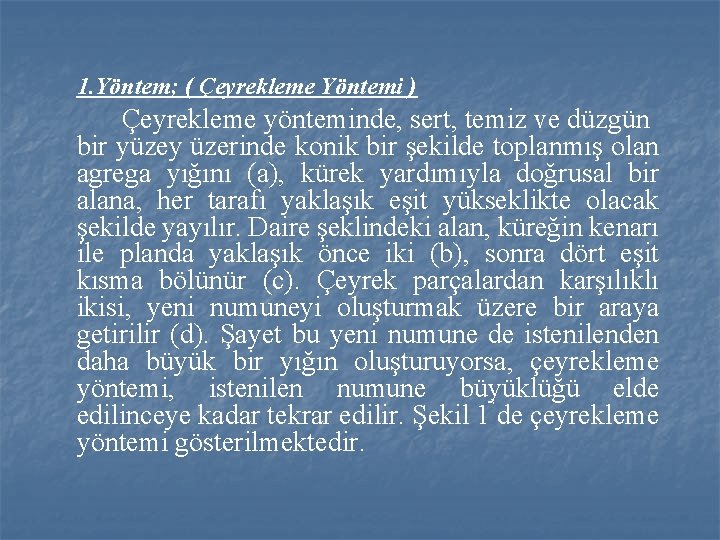
1. Yöntem; ( Çeyrekleme Yöntemi ) Çeyrekleme yönteminde, sert, temiz ve düzgün bir yüzey üzerinde konik bir şekilde toplanmış olan agrega yığını (a), kürek yardımıyla doğrusal bir alana, her tarafı yaklaşık eşit yükseklikte olacak şekilde yayılır. Daire şeklindeki alan, küreğin kenarı ile planda yaklaşık önce iki (b), sonra dört eşit kısma bölünür (c). Çeyrek parçalardan karşılıklı ikisi, yeni numuneyi oluşturmak üzere bir araya getirilir (d). Şayet bu yeni numune de istenilenden daha büyük bir yığın oluşturuyorsa, çeyrekleme yöntemi, istenilen numune büyüklüğü elde edilinceye kadar tekrar edilir. Şekil 1 de çeyrekleme yöntemi gösterilmektedir.
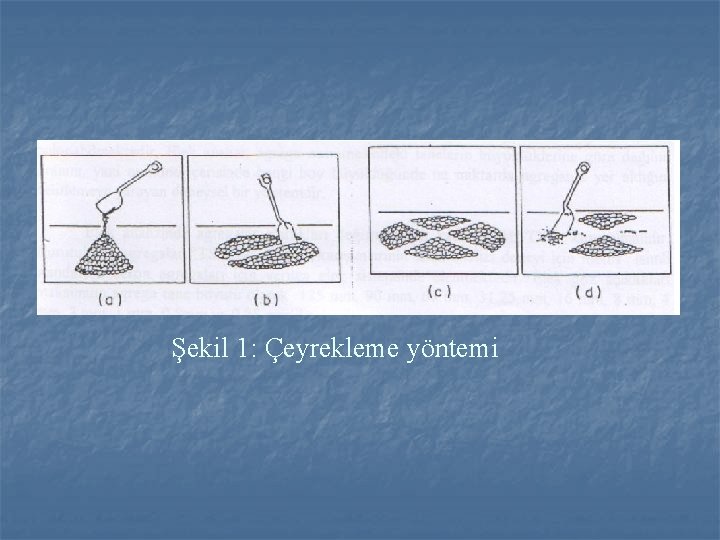
Şekil 1: Çeyrekleme yöntemi
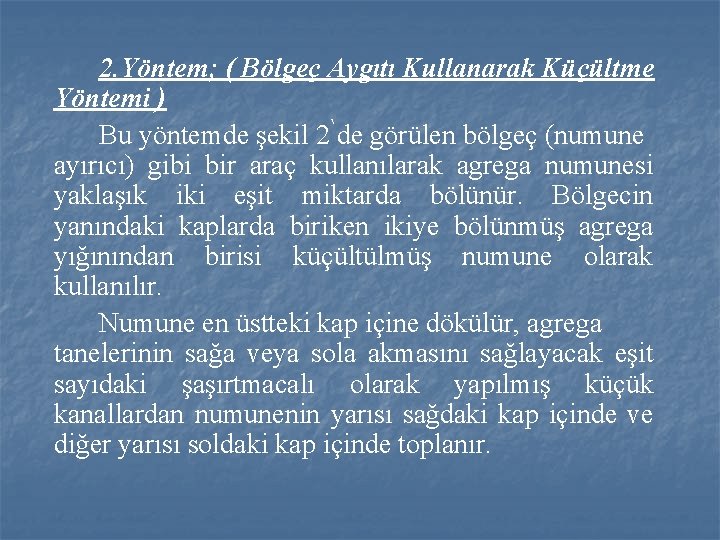
2. Yöntem; ( Bölgeç Aygıtı Kullanarak Küçültme Yöntemi ) Bu yöntemde şekil 2 de görülen bölgeç (numune ayırıcı) gibi bir araç kullanılarak agrega numunesi yaklaşık iki eşit miktarda bölünür. Bölgecin yanındaki kaplarda biriken ikiye bölünmüş agrega yığınından birisi küçültülmüş numune olarak kullanılır. Numune en üstteki kap içine dökülür, agrega tanelerinin sağa veya sola akmasını sağlayacak eşit sayıdaki şaşırtmacalı olarak yapılmış küçük kanallardan numunenin yarısı sağdaki kap içinde ve diğer yarısı soldaki kap içinde toplanır.
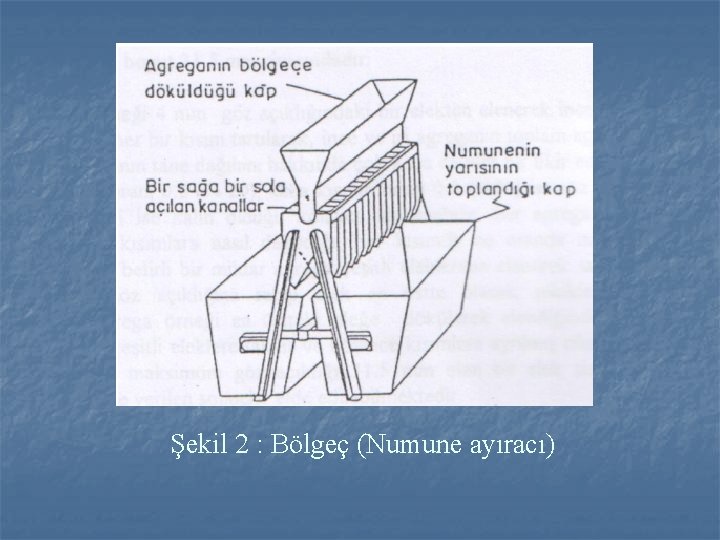
Şekil 2 : Bölgeç (Numune ayıracı)
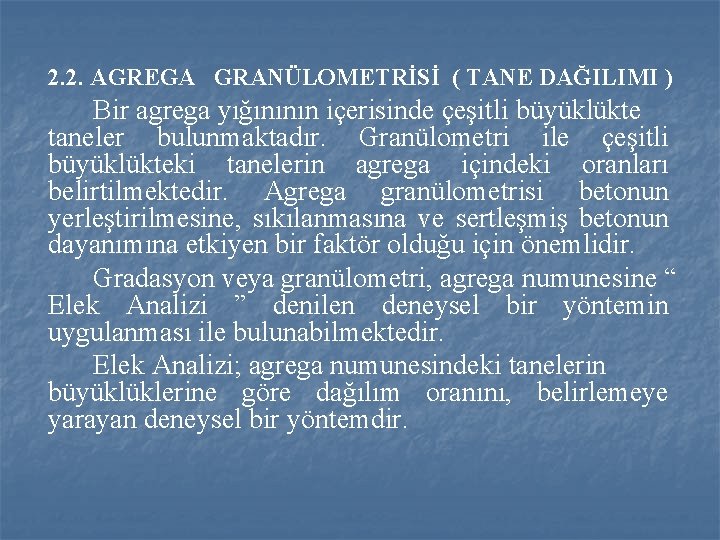
2. 2. AGREGA GRANÜLOMETRİSİ ( TANE DAĞILIMI ) Bir agrega yığınının içerisinde çeşitli büyüklükte taneler bulunmaktadır. Granülometri ile çeşitli büyüklükteki tanelerin agrega içindeki oranları belirtilmektedir. Agrega granülometrisi betonun yerleştirilmesine, sıkılanmasına ve sertleşmiş betonun dayanımına etkiyen bir faktör olduğu için önemlidir. Gradasyon veya granülometri, agrega numunesine “ Elek Analizi ” denilen deneysel bir yöntemin uygulanması ile bulunabilmektedir. Elek Analizi; agrega numunesindeki tanelerin büyüklüklerine göre dağılım oranını, belirlemeye yarayan deneysel bir yöntemdir.
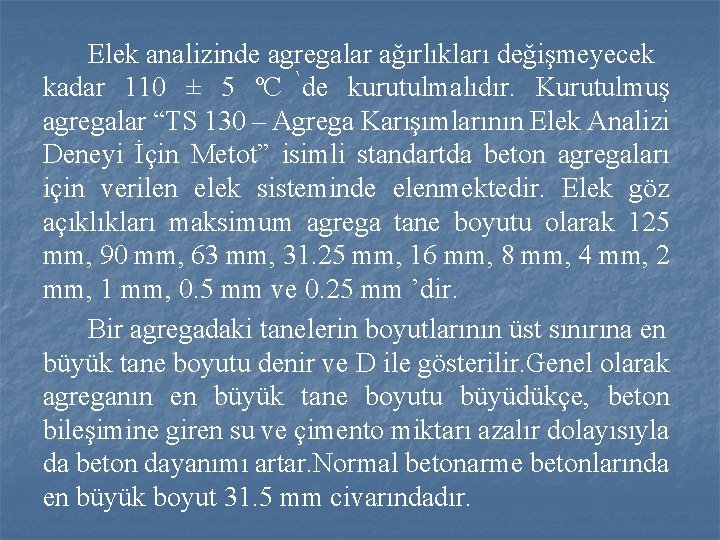
Elek analizinde agregalar ağırlıkları değişmeyecek kadar 110 ± 5 ºC de kurutulmalıdır. Kurutulmuş agregalar “TS 130 – Agrega Karışımlarının Elek Analizi Deneyi İçin Metot” isimli standartda beton agregaları için verilen elek sisteminde elenmektedir. Elek göz açıklıkları maksimum agrega tane boyutu olarak 125 mm, 90 mm, 63 mm, 31. 25 mm, 16 mm, 8 mm, 4 mm, 2 mm, 1 mm, 0. 5 mm ve 0. 25 mm ’dir. Bir agregadaki tanelerin boyutlarının üst sınırına en büyük tane boyutu denir ve D ile gösterilir. Genel olarak agreganın en büyük tane boyutu büyüdükçe, beton bileşimine giren su ve çimento miktarı azalır dolayısıyla da beton dayanımı artar. Normal betonarme betonlarında en büyük boyut 31. 5 mm civarındadır.
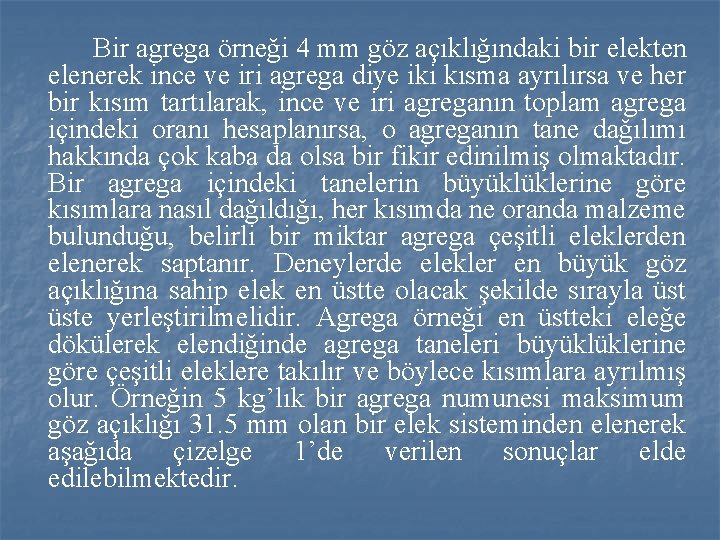
Bir agrega örneği 4 mm göz açıklığındaki bir elekten elenerek ince ve iri agrega diye iki kısma ayrılırsa ve her bir kısım tartılarak, ince ve iri agreganın toplam agrega içindeki oranı hesaplanırsa, o agreganın tane dağılımı hakkında çok kaba da olsa bir fikir edinilmiş olmaktadır. Bir agrega içindeki tanelerin büyüklüklerine göre kısımlara nasıl dağıldığı, her kısımda ne oranda malzeme bulunduğu, belirli bir miktar agrega çeşitli eleklerden elenerek saptanır. Deneylerde elekler en büyük göz açıklığına sahip elek en üstte olacak şekilde sırayla üste yerleştirilmelidir. Agrega örneği en üstteki eleğe dökülerek elendiğinde agrega taneleri büyüklüklerine göre çeşitli eleklere takılır ve böylece kısımlara ayrılmış olur. Örneğin 5 kg’lık bir agrega numunesi maksimum göz açıklığı 31. 5 mm olan bir elek sisteminden elenerek aşağıda çizelge 1’de verilen sonuçlar elde edilebilmektedir.
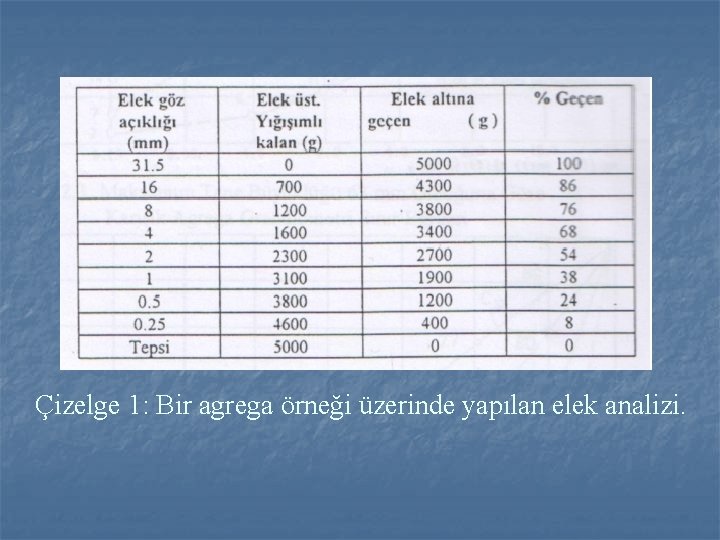
Çizelge 1: Bir agrega örneği üzerinde yapılan elek analizi.
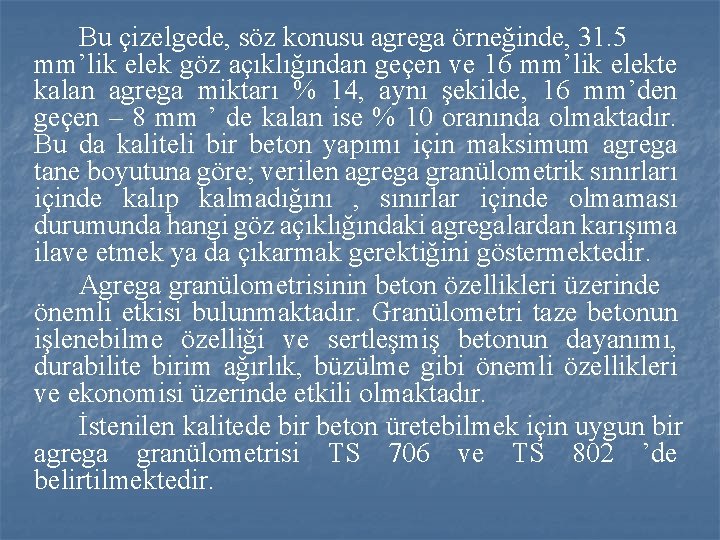
Bu çizelgede, söz konusu agrega örneğinde, 31. 5 mm’lik elek göz açıklığından geçen ve 16 mm’lik elekte kalan agrega miktarı % 14, aynı şekilde, 16 mm’den geçen – 8 mm ’ de kalan ise % 10 oranında olmaktadır. Bu da kaliteli bir beton yapımı için maksimum agrega tane boyutuna göre; verilen agrega granülometrik sınırları içinde kalıp kalmadığını , sınırlar içinde olmaması durumunda hangi göz açıklığındaki agregalardan karışıma ilave etmek ya da çıkarmak gerektiğini göstermektedir. Agrega granülometrisinin beton özellikleri üzerinde önemli etkisi bulunmaktadır. Granülometri taze betonun işlenebilme özelliği ve sertleşmiş betonun dayanımı, durabilite birim ağırlık, büzülme gibi önemli özellikleri ve ekonomisi üzerinde etkili olmaktadır. İstenilen kalitede bir beton üretebilmek için uygun bir agrega granülometrisi TS 706 ve TS 802 ’de belirtilmektedir.
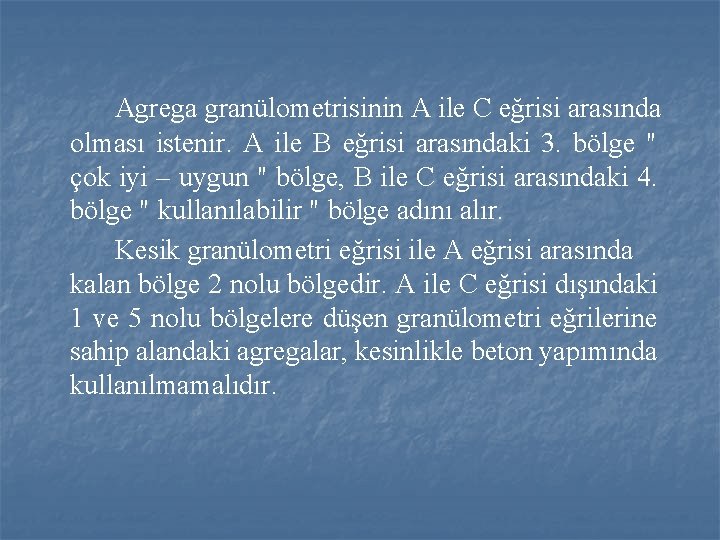
Agrega granülometrisinin A ile C eğrisi arasında olması istenir. A ile B eğrisi arasındaki 3. bölge " çok iyi – uygun " bölge, B ile C eğrisi arasındaki 4. bölge " kullanılabilir " bölge adını alır. Kesik granülometri eğrisi ile A eğrisi arasında kalan bölge 2 nolu bölgedir. A ile C eğrisi dışındaki 1 ve 5 nolu bölgelere düşen granülometri eğrilerine sahip alandaki agregalar, kesinlikle beton yapımında kullanılmamalıdır.
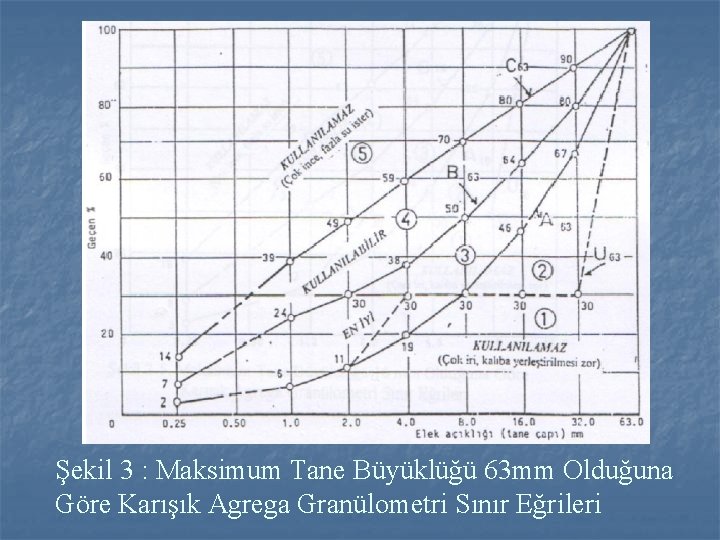
Şekil 3 : Maksimum Tane Büyüklüğü 63 mm Olduğuna Göre Karışık Agrega Granülometri Sınır Eğrileri
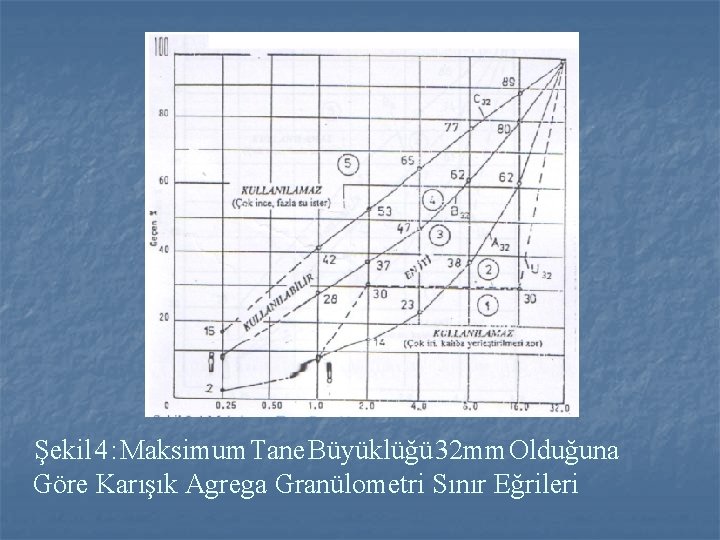
Şekil 4 : Maksimum Tane Büyüklüğü 32 mm Olduğuna Göre Karışık Agrega Granülometri Sınır Eğrileri
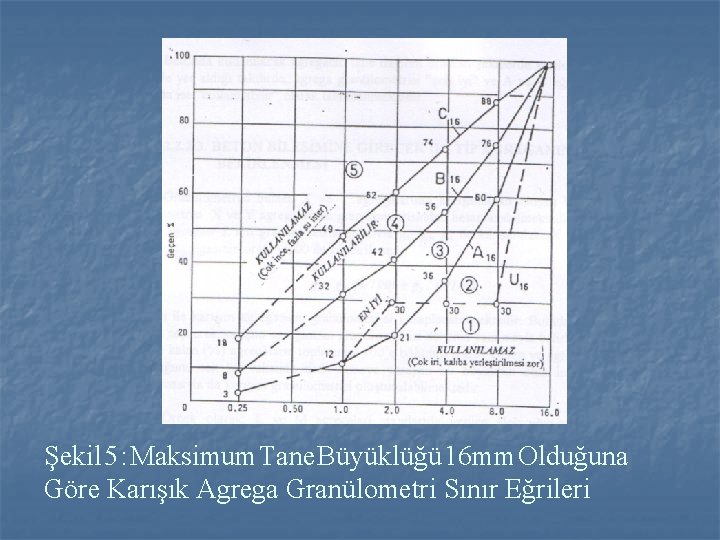
Şekil 5 : Maksimum Tane Büyüklüğü 16 mm Olduğuna Göre Karışık Agrega Granülometri Sınır Eğrileri
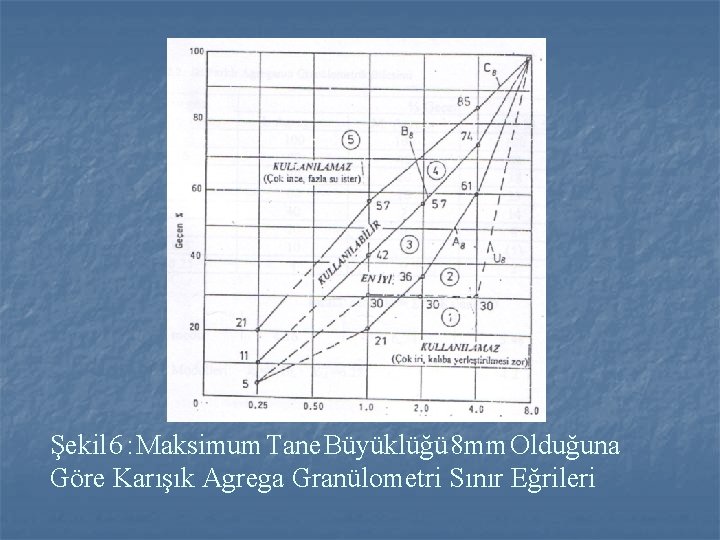
Şekil 6 : Maksimum Tane Büyüklüğü 8 mm Olduğuna Göre Karışık Agrega Granülometri Sınır Eğrileri
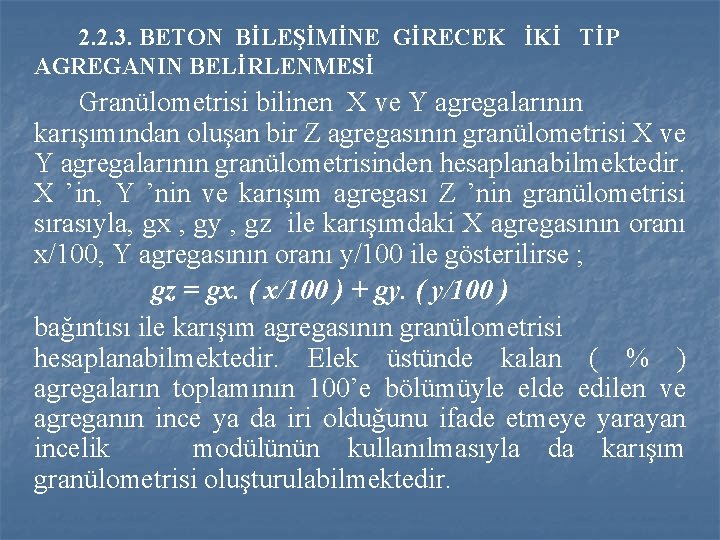
2. 2. 3. BETON BİLEŞİMİNE GİRECEK İKİ TİP AGREGANIN BELİRLENMESİ Granülometrisi bilinen X ve Y agregalarının karışımından oluşan bir Z agregasının granülometrisi X ve Y agregalarının granülometrisinden hesaplanabilmektedir. X ’in, Y ’nin ve karışım agregası Z ’nin granülometrisi sırasıyla, gx , gy , gz ile karışımdaki X agregasının oranı x/100, Y agregasının oranı y/100 ile gösterilirse ; gz = gx. ( x/100 ) + gy. ( y/100 ) bağıntısı ile karışım agregasının granülometrisi hesaplanabilmektedir. Elek üstünde kalan ( % ) agregaların toplamının 100’e bölümüyle elde edilen ve agreganın ince ya da iri olduğunu ifade etmeye yarayan incelik modülünün kullanılmasıyla da karışım granülometrisi oluşturulabilmektedir.
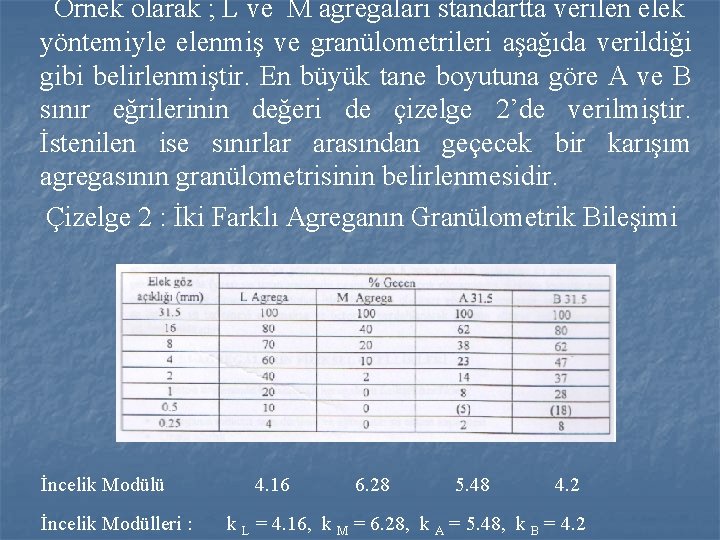
Örnek olarak ; L ve M agregaları standartta verilen elek yöntemiyle elenmiş ve granülometrileri aşağıda verildiği gibi belirlenmiştir. En büyük tane boyutuna göre A ve B sınır eğrilerinin değeri de çizelge 2’de verilmiştir. İstenilen ise sınırlar arasından geçecek bir karışım agregasının granülometrisinin belirlenmesidir. Çizelge 2 : İki Farklı Agreganın Granülometrik Bileşimi İncelik Modülü İncelik Modülleri : 4. 16 6. 28 5. 48 4. 2 k L = 4. 16, k M = 6. 28, k A = 5. 48, k B = 4. 2
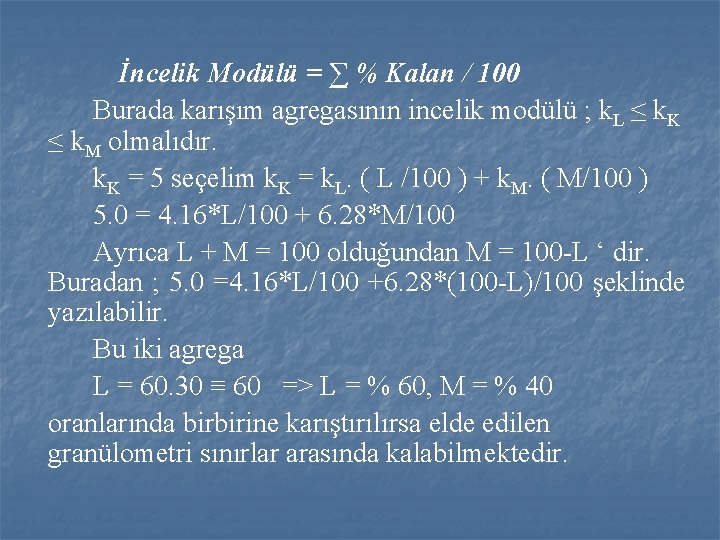
İncelik Modülü = ∑ % Kalan / 100 Burada karışım agregasının incelik modülü ; k. L ≤ k. K ≤ k. M olmalıdır. k. K = 5 seçelim k. K = k. L. ( L /100 ) + k. M. ( M/100 ) 5. 0 = 4. 16*L/100 + 6. 28*M/100 Ayrıca L + M = 100 olduğundan M = 100 -L ‘ dir. Buradan ; 5. 0 =4. 16*L/100 +6. 28*(100 -L)/100 şeklinde yazılabilir. Bu iki agrega L = 60. 30 ≡ 60 => L = % 60, M = % 40 oranlarında birbirine karıştırılırsa elde edilen granülometri sınırlar arasında kalabilmektedir.
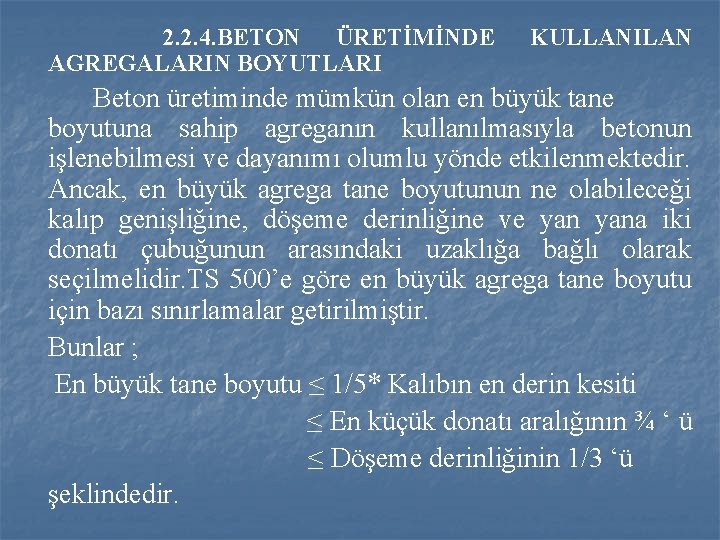
2. 2. 4. BETON ÜRETİMİNDE AGREGALARIN BOYUTLARI KULLANILAN Beton üretiminde mümkün olan en büyük tane boyutuna sahip agreganın kullanılmasıyla betonun işlenebilmesi ve dayanımı olumlu yönde etkilenmektedir. Ancak, en büyük agrega tane boyutunun ne olabileceği kalıp genişliğine, döşeme derinliğine ve yana iki donatı çubuğunun arasındaki uzaklığa bağlı olarak seçilmelidir. TS 500’e göre en büyük agrega tane boyutu için bazı sınırlamalar getirilmiştir. Bunlar ; En büyük tane boyutu ≤ 1/5* Kalıbın en derin kesiti ≤ En küçük donatı aralığının ¾ ‘ ü ≤ Döşeme derinliğinin 1/3 ‘ü şeklindedir.
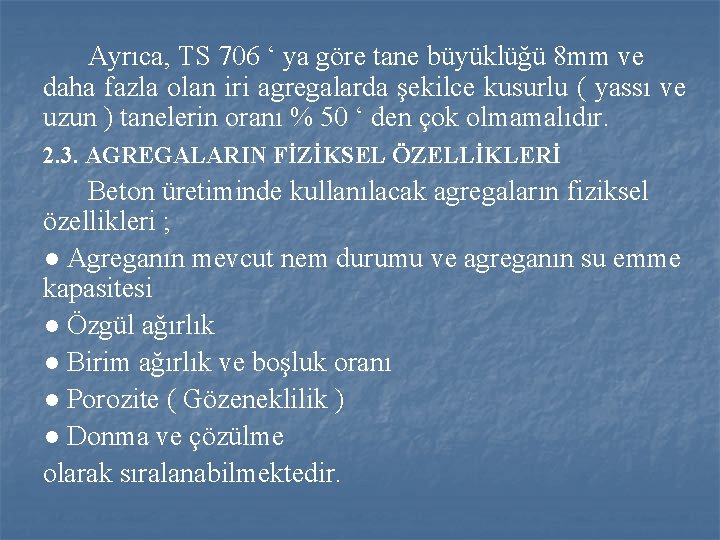
Ayrıca, TS 706 ‘ ya göre tane büyüklüğü 8 mm ve daha fazla olan iri agregalarda şekilce kusurlu ( yassı ve uzun ) tanelerin oranı % 50 ‘ den çok olmamalıdır. 2. 3. AGREGALARIN FİZİKSEL ÖZELLİKLERİ Beton üretiminde kullanılacak agregaların fiziksel özellikleri ; ● Agreganın mevcut nem durumu ve agreganın su emme kapasitesi ● Özgül ağırlık ● Birim ağırlık ve boşluk oranı ● Porozite ( Gözeneklilik ) ● Donma ve çözülme olarak sıralanabilmektedir.
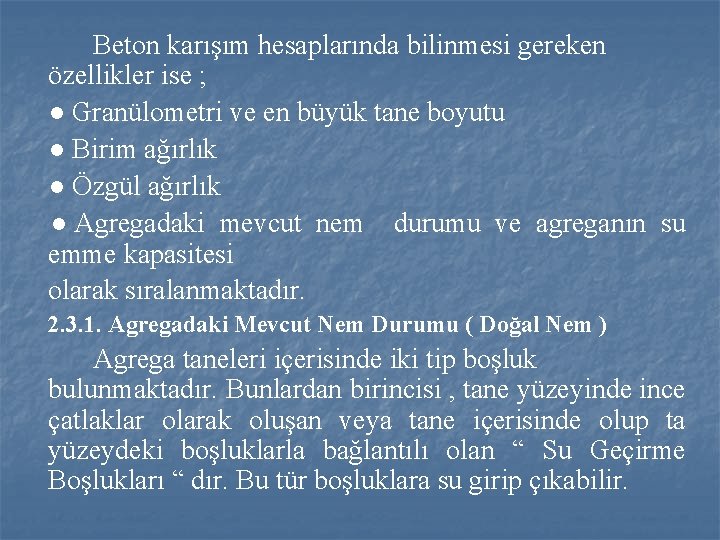
Beton karışım hesaplarında bilinmesi gereken özellikler ise ; ● Granülometri ve en büyük tane boyutu ● Birim ağırlık ● Özgül ağırlık ● Agregadaki mevcut nem durumu ve agreganın su emme kapasitesi olarak sıralanmaktadır. 2. 3. 1. Agregadaki Mevcut Nem Durumu ( Doğal Nem ) Agrega taneleri içerisinde iki tip boşluk bulunmaktadır. Bunlardan birincisi , tane yüzeyinde ince çatlaklar olarak oluşan veya tane içerisinde olup ta yüzeydeki boşluklarla bağlantılı olan “ Su Geçirme Boşlukları “ dır. Bu tür boşluklara su girip çıkabilir.
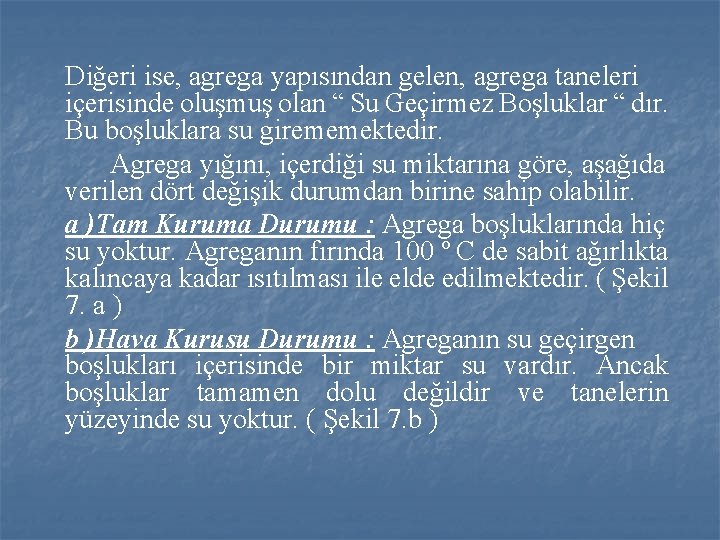
Diğeri ise, agrega yapısından gelen, agrega taneleri içerisinde oluşmuş olan “ Su Geçirmez Boşluklar “ dır. Bu boşluklara su girememektedir. Agrega yığını, içerdiği su miktarına göre, aşağıda verilen dört değişik durumdan birine sahip olabilir. a )Tam Kuruma Durumu : Agrega boşluklarında hiç su yoktur. Agreganın fırında 100 º C de sabit ağırlıkta kalıncaya kadar ısıtılması ile elde edilmektedir. ( Şekil 7. a ) b )Hava Kurusu Durumu : Agreganın su geçirgen boşlukları içerisinde bir miktar su vardır. Ancak boşluklar tamamen dolu değildir ve tanelerin yüzeyinde su yoktur. ( Şekil 7. b )
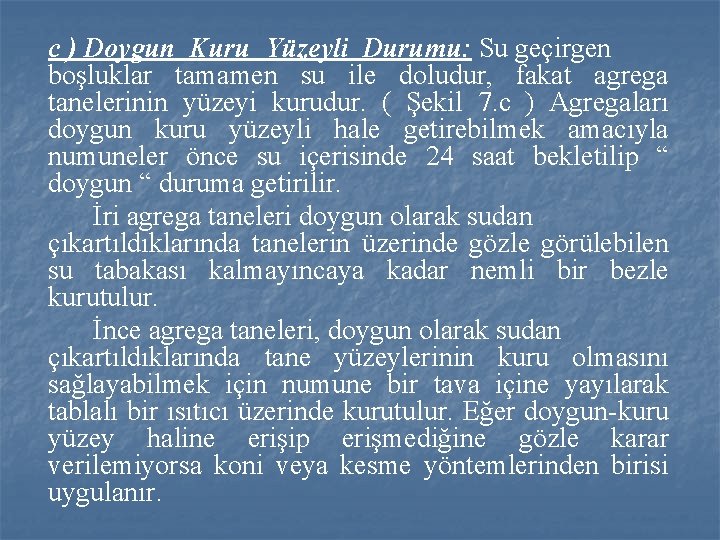
c ) Doygun Kuru Yüzeyli Durumu: Su geçirgen boşluklar tamamen su ile doludur, fakat agrega tanelerinin yüzeyi kurudur. ( Şekil 7. c ) Agregaları doygun kuru yüzeyli hale getirebilmek amacıyla numuneler önce su içerisinde 24 saat bekletilip “ doygun “ duruma getirilir. İri agrega taneleri doygun olarak sudan çıkartıldıklarında tanelerin üzerinde gözle görülebilen su tabakası kalmayıncaya kadar nemli bir bezle kurutulur. İnce agrega taneleri, doygun olarak sudan çıkartıldıklarında tane yüzeylerinin kuru olmasını sağlayabilmek için numune bir tava içine yayılarak tablalı bir ısıtıcı üzerinde kurutulur. Eğer doygun-kuru yüzey haline erişip erişmediğine gözle karar verilemiyorsa koni veya kesme yöntemlerinden birisi uygulanır.
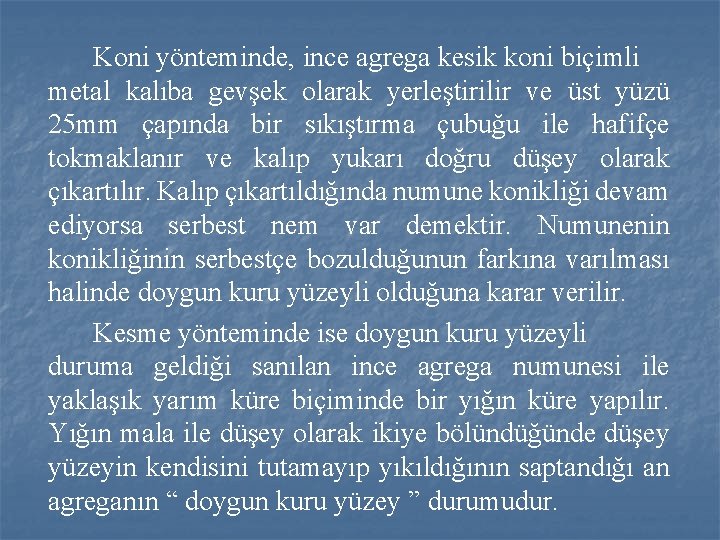
Koni yönteminde, ince agrega kesik koni biçimli metal kalıba gevşek olarak yerleştirilir ve üst yüzü 25 mm çapında bir sıkıştırma çubuğu ile hafifçe tokmaklanır ve kalıp yukarı doğru düşey olarak çıkartılır. Kalıp çıkartıldığında numune konikliği devam ediyorsa serbest nem var demektir. Numunenin konikliğinin serbestçe bozulduğunun farkına varılması halinde doygun kuru yüzeyli olduğuna karar verilir. Kesme yönteminde ise doygun kuru yüzeyli duruma geldiği sanılan ince agrega numunesi ile yaklaşık yarım küre biçiminde bir yığın küre yapılır. Yığın mala ile düşey olarak ikiye bölündüğünde düşey yüzeyin kendisini tutamayıp yıkıldığının saptandığı an agreganın “ doygun kuru yüzey ” durumudur.
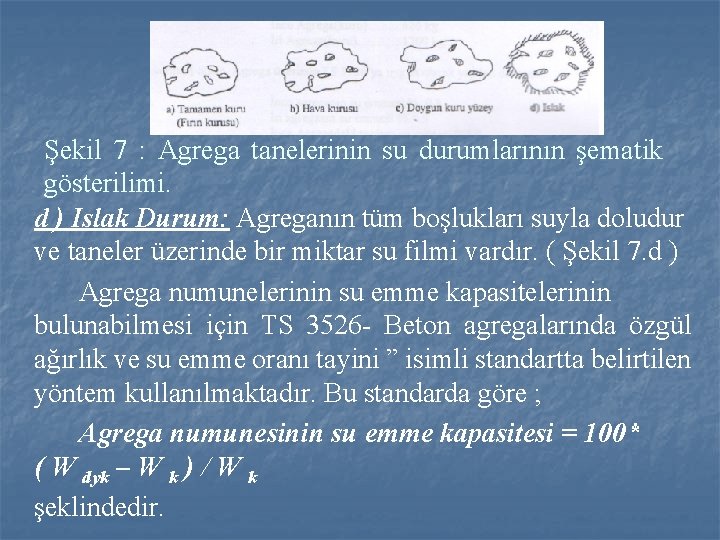
Şekil 7 : Agrega tanelerinin su durumlarının şematik gösterilimi. d ) Islak Durum: Agreganın tüm boşlukları suyla doludur ve taneler üzerinde bir miktar su filmi vardır. ( Şekil 7. d ) Agrega numunelerinin su emme kapasitelerinin bulunabilmesi için TS 3526 - Beton agregalarında özgül ağırlık ve su emme oranı tayini ” isimli standartta belirtilen yöntem kullanılmaktadır. Bu standarda göre ; Agrega numunesinin su emme kapasitesi = 100* ( W dyk – W k ) / W k şeklindedir.
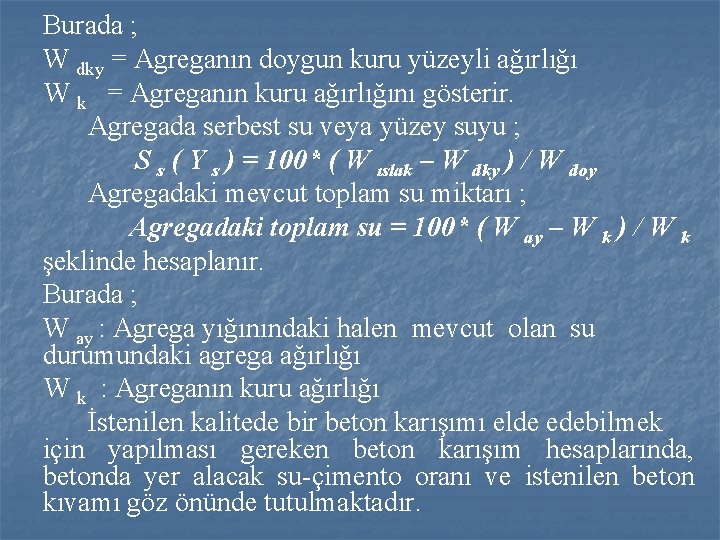
Burada ; W dky = Agreganın doygun kuru yüzeyli ağırlığı W k = Agreganın kuru ağırlığını gösterir. Agregada serbest su veya yüzey suyu ; S s ( Y s ) = 100* ( W ıslak – W dky ) / W doy Agregadaki mevcut toplam su miktarı ; Agregadaki toplam su = 100* ( W ay – W k ) / W k şeklinde hesaplanır. Burada ; W ay : Agrega yığınındaki halen mevcut olan su durumundaki agrega ağırlığı W k : Agreganın kuru ağırlığı İstenilen kalitede bir beton karışımı elde edebilmek için yapılması gereken beton karışım hesaplarında, betonda yer alacak su-çimento oranı ve istenilen beton kıvamı göz önünde tutulmaktadır.
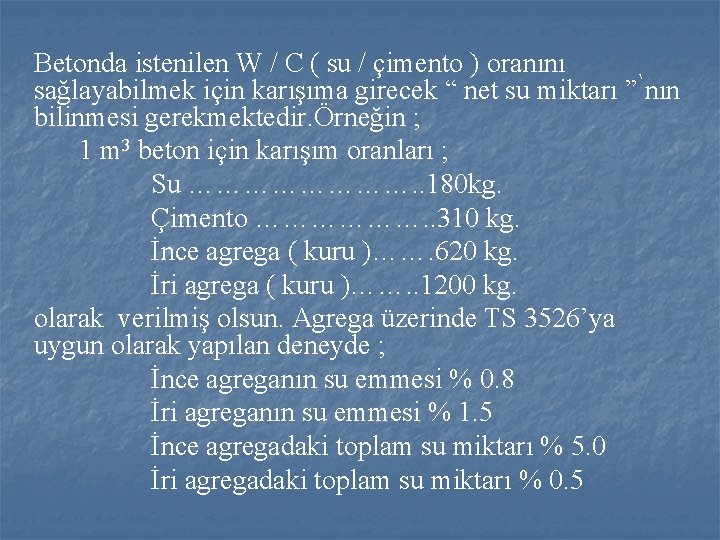
Betonda istenilen W / C ( su / çimento ) oranını sağlayabilmek için karışıma girecek “ net su miktarı ” nın bilinmesi gerekmektedir. Örneğin ; 1 m 3 beton için karışım oranları ; Su …………. . 180 kg. Çimento ………………. . 310 kg. İnce agrega ( kuru )……. 620 kg. İri agrega ( kuru )……. . 1200 kg. olarak verilmiş olsun. Agrega üzerinde TS 3526’ya uygun olarak yapılan deneyde ; İnce agreganın su emmesi % 0. 8 İri agreganın su emmesi % 1. 5 İnce agregadaki toplam su miktarı % 5. 0 İri agregadaki toplam su miktarı % 0. 5
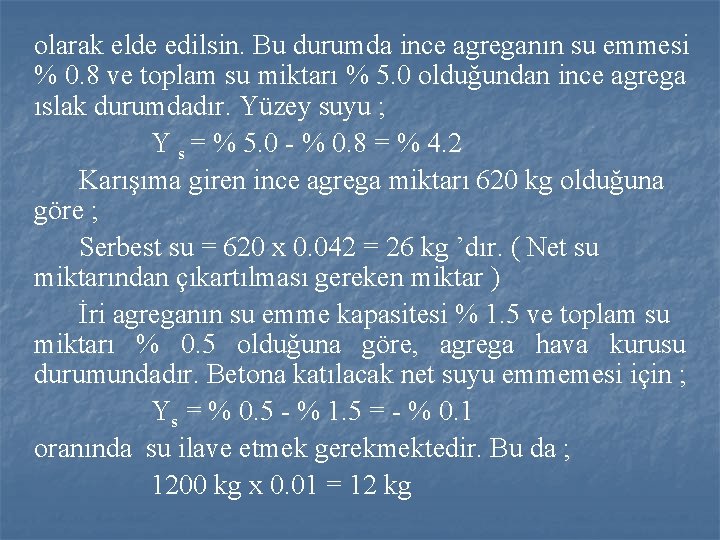
olarak elde edilsin. Bu durumda ince agreganın su emmesi % 0. 8 ve toplam su miktarı % 5. 0 olduğundan ince agrega ıslak durumdadır. Yüzey suyu ; Y s = % 5. 0 - % 0. 8 = % 4. 2 Karışıma giren ince agrega miktarı 620 kg olduğuna göre ; Serbest su = 620 x 0. 042 = 26 kg ’dır. ( Net su miktarından çıkartılması gereken miktar ) İri agreganın su emme kapasitesi % 1. 5 ve toplam su miktarı % 0. 5 olduğuna göre, agrega hava kurusu durumundadır. Betona katılacak net suyu emmemesi için ; Ys = % 0. 5 - % 1. 5 = - % 0. 1 oranında su ilave etmek gerekmektedir. Bu da ; 1200 kg x 0. 01 = 12 kg
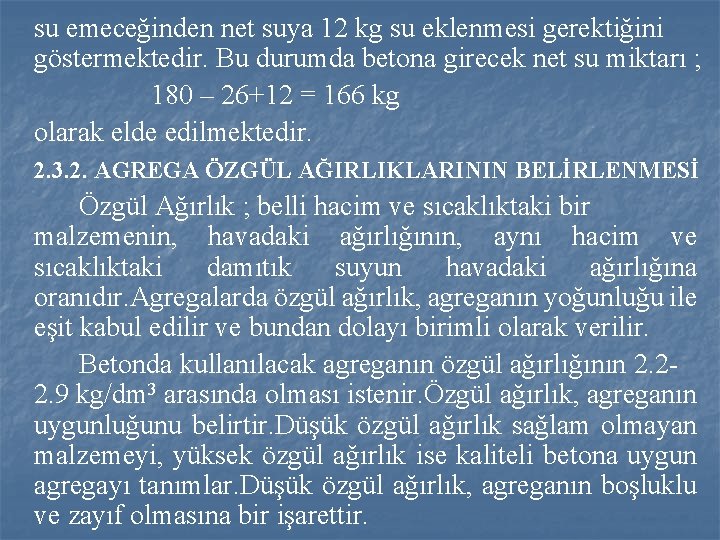
su emeceğinden net suya 12 kg su eklenmesi gerektiğini göstermektedir. Bu durumda betona girecek net su miktarı ; 180 – 26+12 = 166 kg olarak elde edilmektedir. 2. 3. 2. AGREGA ÖZGÜL AĞIRLIKLARININ BELİRLENMESİ Özgül Ağırlık ; belli hacim ve sıcaklıktaki bir malzemenin, havadaki ağırlığının, aynı hacim ve sıcaklıktaki damıtık suyun havadaki ağırlığına oranıdır. Agregalarda özgül ağırlık, agreganın yoğunluğu ile eşit kabul edilir ve bundan dolayı birimli olarak verilir. Betonda kullanılacak agreganın özgül ağırlığının 2. 22. 9 kg/dm 3 arasında olması istenir. Özgül ağırlık, agreganın uygunluğunu belirtir. Düşük özgül ağırlık sağlam olmayan malzemeyi, yüksek özgül ağırlık ise kaliteli betona uygun agregayı tanımlar. Düşük özgül ağırlık, agreganın boşluklu ve zayıf olmasına bir işarettir.
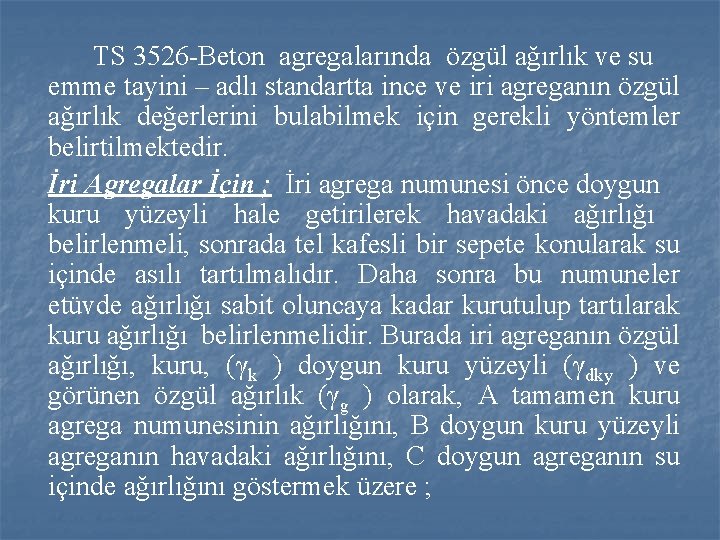
TS 3526 -Beton agregalarında özgül ağırlık ve su emme tayini – adlı standartta ince ve iri agreganın özgül ağırlık değerlerini bulabilmek için gerekli yöntemler belirtilmektedir. İri Agregalar İçin ; İri agrega numunesi önce doygun kuru yüzeyli hale getirilerek havadaki ağırlığı belirlenmeli, sonrada tel kafesli bir sepete konularak su içinde asılı tartılmalıdır. Daha sonra bu numuneler etüvde ağırlığı sabit oluncaya kadar kurutulup tartılarak kuru ağırlığı belirlenmelidir. Burada iri agreganın özgül ağırlığı, kuru, (γk ) doygun kuru yüzeyli (γdky ) ve görünen özgül ağırlık (γg ) olarak, A tamamen kuru agrega numunesinin ağırlığını, B doygun kuru yüzeyli agreganın havadaki ağırlığını, C doygun agreganın su içinde ağırlığını göstermek üzere ;
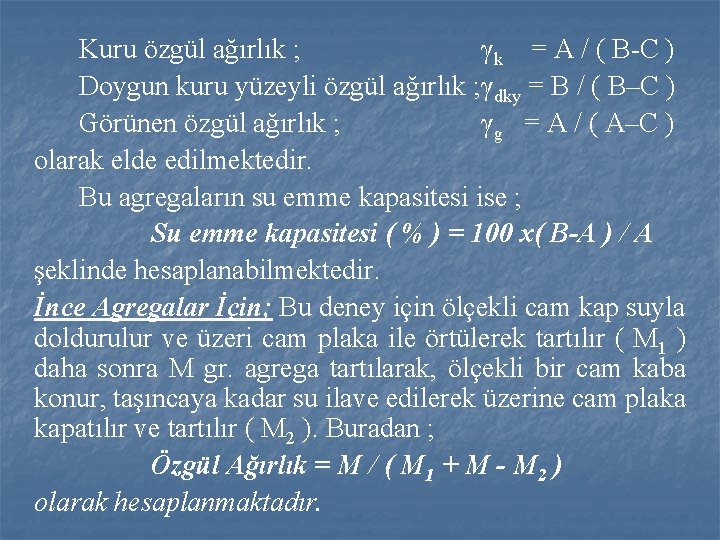
Kuru özgül ağırlık ; γk = A / ( B-C ) Doygun kuru yüzeyli özgül ağırlık ; γdky = B / ( B–C ) Görünen özgül ağırlık ; γg = A / ( A–C ) olarak elde edilmektedir. Bu agregaların su emme kapasitesi ise ; Su emme kapasitesi ( % ) = 100 x( B-A ) / A şeklinde hesaplanabilmektedir. İnce Agregalar İçin; Bu deney için ölçekli cam kap suyla doldurulur ve üzeri cam plaka ile örtülerek tartılır ( M 1 ) daha sonra M gr. agrega tartılarak, ölçekli bir cam kaba konur, taşıncaya kadar su ilave edilerek üzerine cam plaka kapatılır ve tartılır ( M 2 ). Buradan ; Özgül Ağırlık = M / ( M 1 + M - M 2 ) olarak hesaplanmaktadır.
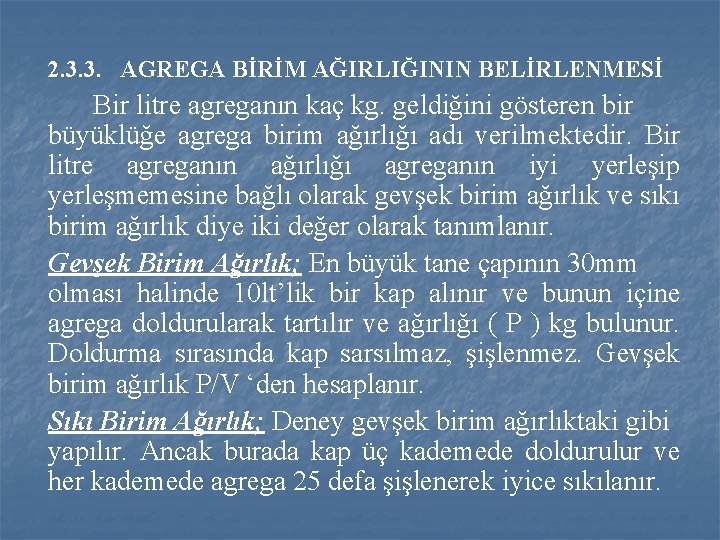
2. 3. 3. AGREGA BİRİM AĞIRLIĞININ BELİRLENMESİ Bir litre agreganın kaç kg. geldiğini gösteren bir büyüklüğe agrega birim ağırlığı adı verilmektedir. Bir litre agreganın ağırlığı agreganın iyi yerleşip yerleşmemesine bağlı olarak gevşek birim ağırlık ve sıkı birim ağırlık diye iki değer olarak tanımlanır. Gevşek Birim Ağırlık; En büyük tane çapının 30 mm olması halinde 10 lt’lik bir kap alınır ve bunun içine agrega doldurularak tartılır ve ağırlığı ( P ) kg bulunur. Doldurma sırasında kap sarsılmaz, şişlenmez. Gevşek birim ağırlık P/V ‘den hesaplanır. Sıkı Birim Ağırlık; Deney gevşek birim ağırlıktaki gibi yapılır. Ancak burada kap üç kademede doldurulur ve her kademede agrega 25 defa şişlenerek iyice sıkılanır.

Birim ağırlığı yüksek bir betonun dayanımı, dayanıklılığı ve taşıma gücü fazladır. Beton agregaların birim ağırlığı 1. 300 -1. 850 kg/dm 3 arasında değişir. 2. 3. 4. ÇAMURLU MADDE MİKTARININ SAPTANMASI Agrega içinde fazla miktarda çamurlu madde bulunması halinde, agrega çimentoyla iyice birleşemez. Çamur miktarını saptamak için 6. 5 cm çapında ve ölçekli bir kap içine ( 1 kg ) agrega ve su konulur. Kap çalkalanıp içindeki taneler çökelmeye bırakılarak bir iki saat beklenir. Bu süre sonunda agreganın üstünde toplanan çamur tabakasının kalınlığı toplam agrega tabakasının kalınlığının % 5 ’ ini geçmemelidir.
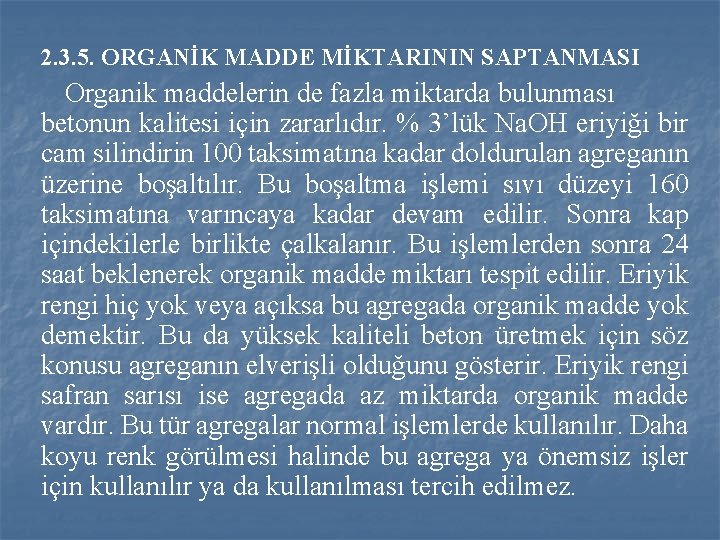
2. 3. 5. ORGANİK MADDE MİKTARININ SAPTANMASI Organik maddelerin de fazla miktarda bulunması betonun kalitesi için zararlıdır. % 3’lük Na. OH eriyiği bir cam silindirin 100 taksimatına kadar doldurulan agreganın üzerine boşaltılır. Bu boşaltma işlemi sıvı düzeyi 160 taksimatına varıncaya kadar devam edilir. Sonra kap içindekilerle birlikte çalkalanır. Bu işlemlerden sonra 24 saat beklenerek organik madde miktarı tespit edilir. Eriyik rengi hiç yok veya açıksa bu agregada organik madde yok demektir. Bu da yüksek kaliteli beton üretmek için söz konusu agreganın elverişli olduğunu gösterir. Eriyik rengi safran sarısı ise agregada az miktarda organik madde vardır. Bu tür agregalar normal işlemlerde kullanılır. Daha koyu renk görülmesi halinde bu agrega ya önemsiz işler için kullanılır ya da kullanılması tercih edilmez.
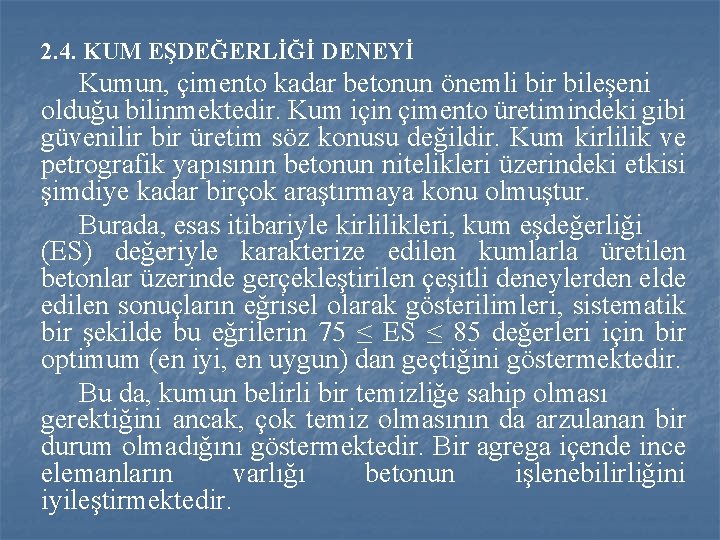
2. 4. KUM EŞDEĞERLİĞİ DENEYİ Kumun, çimento kadar betonun önemli bir bileşeni olduğu bilinmektedir. Kum için çimento üretimindeki gibi güvenilir bir üretim söz konusu değildir. Kum kirlilik ve petrografik yapısının betonun nitelikleri üzerindeki etkisi şimdiye kadar birçok araştırmaya konu olmuştur. Burada, esas itibariyle kirlilikleri, kum eşdeğerliği (ES) değeriyle karakterize edilen kumlarla üretilen betonlar üzerinde gerçekleştirilen çeşitli deneylerden elde edilen sonuçların eğrisel olarak gösterilimleri, sistematik bir şekilde bu eğrilerin 75 ≤ ES ≤ 85 değerleri için bir optimum (en iyi, en uygun) dan geçtiğini göstermektedir. Bu da, kumun belirli bir temizliğe sahip olması gerektiğini ancak, çok temiz olmasının da arzulanan bir durum olmadığını göstermektedir. Bir agrega içende ince elemanların varlığı betonun işlenebilirliğini iyileştirmektedir.
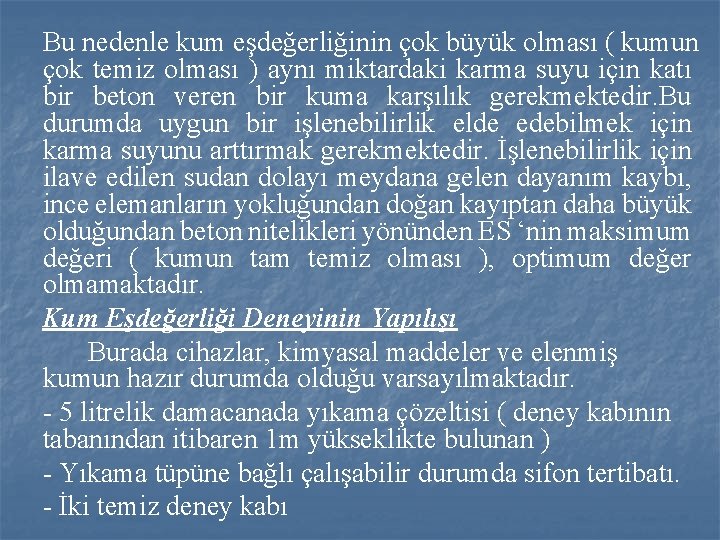
Bu nedenle kum eşdeğerliğinin çok büyük olması ( kumun çok temiz olması ) aynı miktardaki karma suyu için katı bir beton veren bir kuma karşılık gerekmektedir. Bu durumda uygun bir işlenebilirlik elde edebilmek için karma suyunu arttırmak gerekmektedir. İşlenebilirlik için ilave edilen sudan dolayı meydana gelen dayanım kaybı, ince elemanların yokluğundan doğan kayıptan daha büyük olduğundan beton nitelikleri yönünden ES ‘nin maksimum değeri ( kumun tam temiz olması ), optimum değer olmamaktadır. Kum Eşdeğerliği Deneyinin Yapılışı Burada cihazlar, kimyasal maddeler ve elenmiş kumun hazır durumda olduğu varsayılmaktadır. - 5 litrelik damacanada yıkama çözeltisi ( deney kabının tabanından itibaren 1 m yükseklikte bulunan ) - Yıkama tüpüne bağlı çalışabilir durumda sifon tertibatı. - İki temiz deney kabı
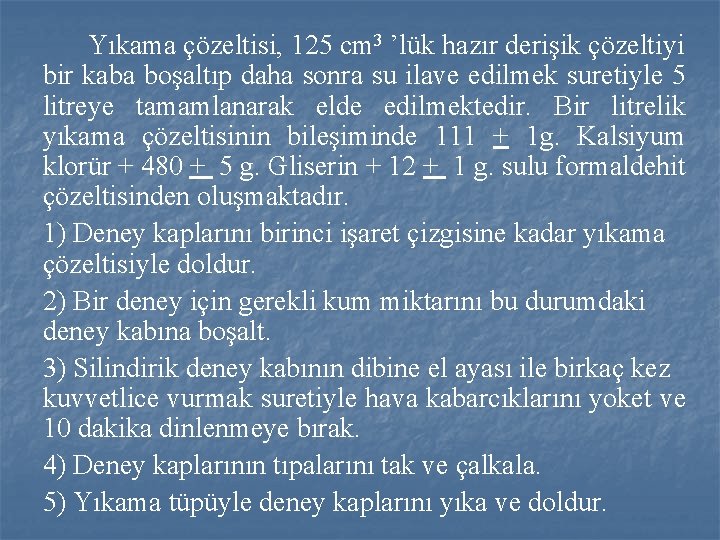
Yıkama çözeltisi, 125 cm 3 ’lük hazır derişik çözeltiyi bir kaba boşaltıp daha sonra su ilave edilmek suretiyle 5 litreye tamamlanarak elde edilmektedir. Bir litrelik yıkama çözeltisinin bileşiminde 111 + 1 g. Kalsiyum klorür + 480 + 5 g. Gliserin + 12 + 1 g. sulu formaldehit çözeltisinden oluşmaktadır. 1) Deney kaplarını birinci işaret çizgisine kadar yıkama çözeltisiyle doldur. 2) Bir deney için gerekli kum miktarını bu durumdaki deney kabına boşalt. 3) Silindirik deney kabının dibine el ayası ile birkaç kez kuvvetlice vurmak suretiyle hava kabarcıklarını yoket ve 10 dakika dinlenmeye bırak. 4) Deney kaplarının tıpalarını tak ve çalkala. 5) Yıkama tüpüyle deney kaplarını yıka ve doldur.
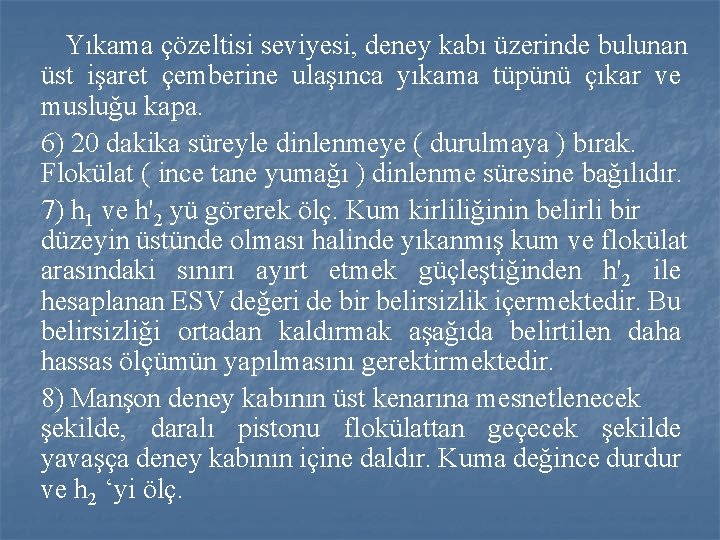
Yıkama çözeltisi seviyesi, deney kabı üzerinde bulunan üst işaret çemberine ulaşınca yıkama tüpünü çıkar ve musluğu kapa. 6) 20 dakika süreyle dinlenmeye ( durulmaya ) bırak. Flokülat ( ince tane yumağı ) dinlenme süresine bağılıdır. 7) h 1 ve h'2 yü görerek ölç. Kum kirliliğinin belirli bir düzeyin üstünde olması halinde yıkanmış kum ve flokülat arasındaki sınırı ayırt etmek güçleştiğinden h'2 ile hesaplanan ESV değeri de bir belirsizlik içermektedir. Bu belirsizliği ortadan kaldırmak aşağıda belirtilen daha hassas ölçümün yapılmasını gerektirmektedir. 8) Manşon deney kabının üst kenarına mesnetlenecek şekilde, daralı pistonu flokülattan geçecek şekilde yavaşça deney kabının içine daldır. Kuma değince durdur ve h 2 ‘yi ölç.
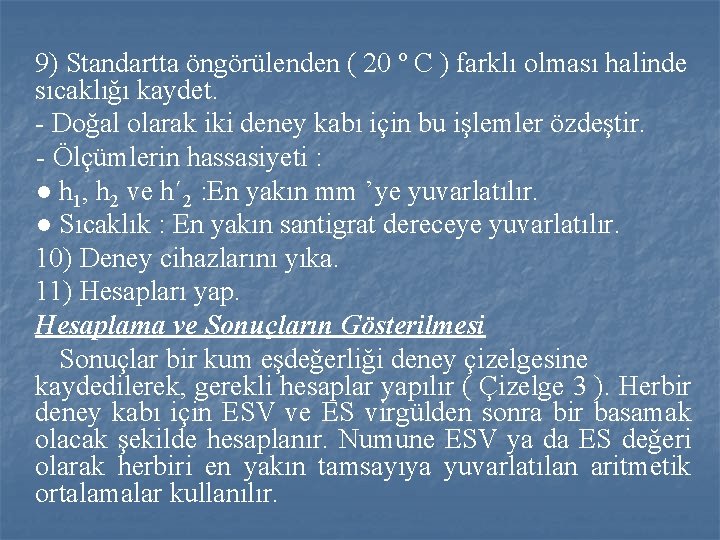
9) Standartta öngörülenden ( 20 º C ) farklı olması halinde sıcaklığı kaydet. - Doğal olarak iki deney kabı için bu işlemler özdeştir. - Ölçümlerin hassasiyeti : ● h 1, h 2 ve h´ 2 : En yakın mm ’ye yuvarlatılır. ● Sıcaklık : En yakın santigrat dereceye yuvarlatılır. 10) Deney cihazlarını yıka. 11) Hesapları yap. Hesaplama ve Sonuçların Gösterilmesi Sonuçlar bir kum eşdeğerliği deney çizelgesine kaydedilerek, gerekli hesaplar yapılır ( Çizelge 3 ). Herbir deney kabı için ESV ve ES virgülden sonra bir basamak olacak şekilde hesaplanır. Numune ESV ya da ES değeri olarak herbiri en yakın tamsayıya yuvarlatılan aritmetik ortalamalar kullanılır.
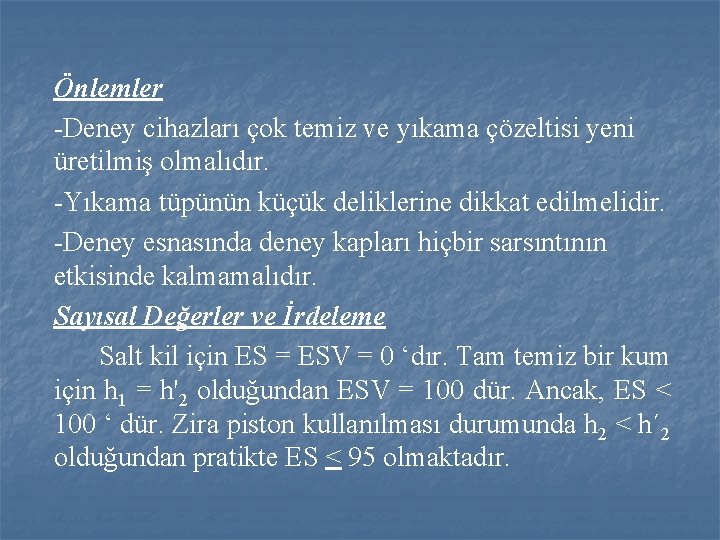
Önlemler -Deney cihazları çok temiz ve yıkama çözeltisi yeni üretilmiş olmalıdır. -Yıkama tüpünün küçük deliklerine dikkat edilmelidir. -Deney esnasında deney kapları hiçbir sarsıntının etkisinde kalmamalıdır. Sayısal Değerler ve İrdeleme Salt kil için ES = ESV = 0 ‘dır. Tam temiz bir kum için h 1 = h'2 olduğundan ESV = 100 dür. Ancak, ES < 100 ‘ dür. Zira piston kullanılması durumunda h 2 < h´ 2 olduğundan pratikte ES < 95 olmaktadır.
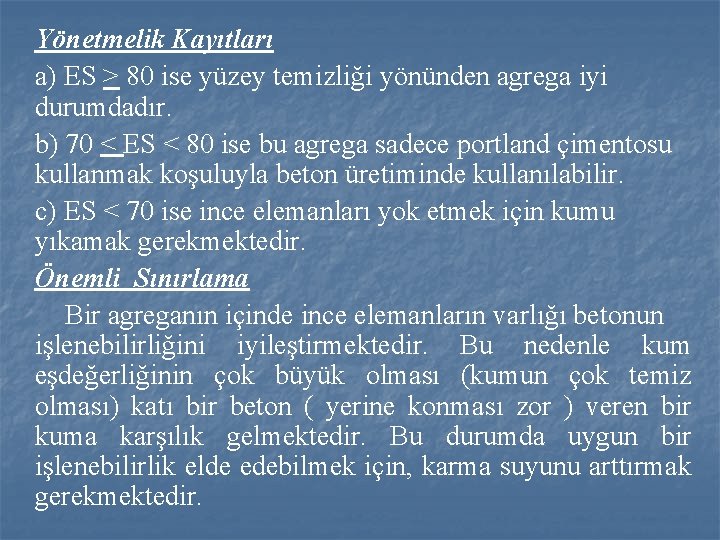
Yönetmelik Kayıtları a) ES > 80 ise yüzey temizliği yönünden agrega iyi durumdadır. b) 70 < ES < 80 ise bu agrega sadece portland çimentosu kullanmak koşuluyla beton üretiminde kullanılabilir. c) ES < 70 ise ince elemanları yok etmek için kumu yıkamak gerekmektedir. Önemli Sınırlama Bir agreganın içinde ince elemanların varlığı betonun işlenebilirliğini iyileştirmektedir. Bu nedenle kum eşdeğerliğinin çok büyük olması (kumun çok temiz olması) katı bir beton ( yerine konması zor ) veren bir kuma karşılık gelmektedir. Bu durumda uygun bir işlenebilirlik elde edebilmek için, karma suyunu arttırmak gerekmektedir.
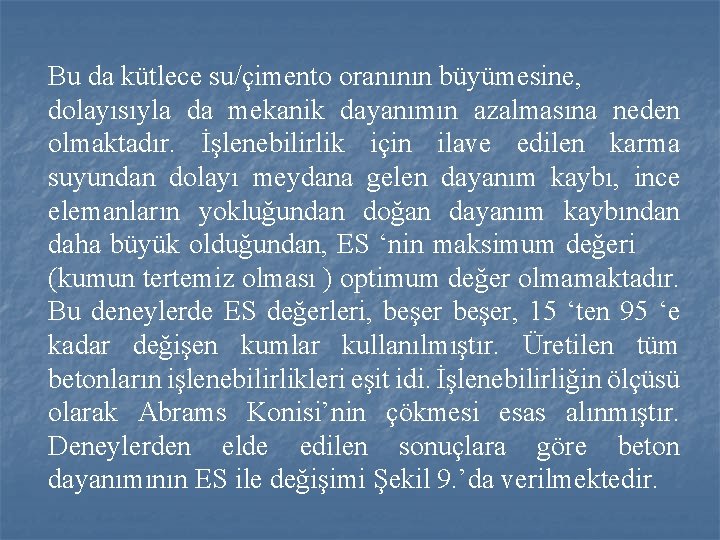
Bu da kütlece su/çimento oranının büyümesine, dolayısıyla da mekanik dayanımın azalmasına neden olmaktadır. İşlenebilirlik için ilave edilen karma suyundan dolayı meydana gelen dayanım kaybı, ince elemanların yokluğundan doğan dayanım kaybından daha büyük olduğundan, ES ‘nin maksimum değeri (kumun tertemiz olması ) optimum değer olmamaktadır. Bu deneylerde ES değerleri, beşer, 15 ‘ten 95 ‘e kadar değişen kumlar kullanılmıştır. Üretilen tüm betonların işlenebilirlikleri eşit idi. İşlenebilirliğin ölçüsü olarak Abrams Konisi’nin çökmesi esas alınmıştır. Deneylerden elde edilen sonuçlara göre beton dayanımının ES ile değişimi Şekil 9. ’da verilmektedir.
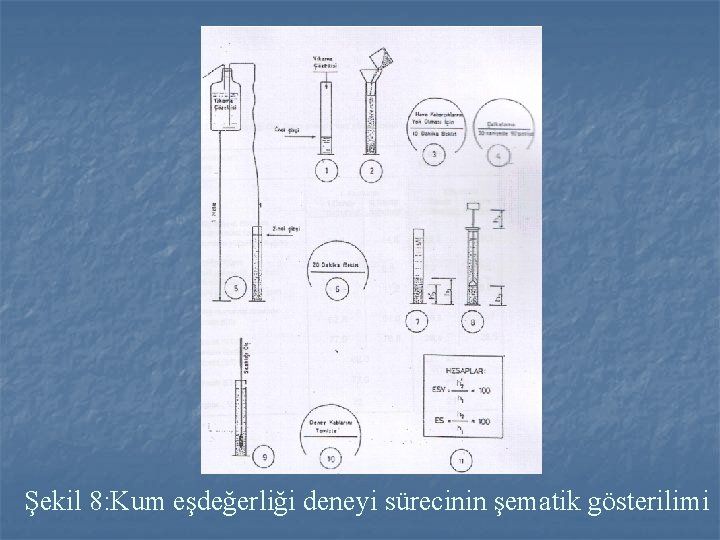
Şekil 8: Kum eşdeğerliği deneyi sürecinin şematik gösterilimi
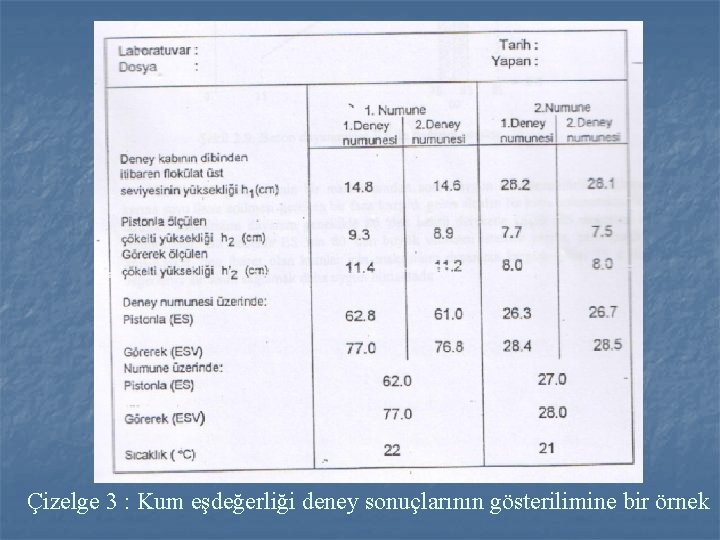
Çizelge 3 : Kum eşdeğerliği deney sonuçlarının gösterilimine bir örnek
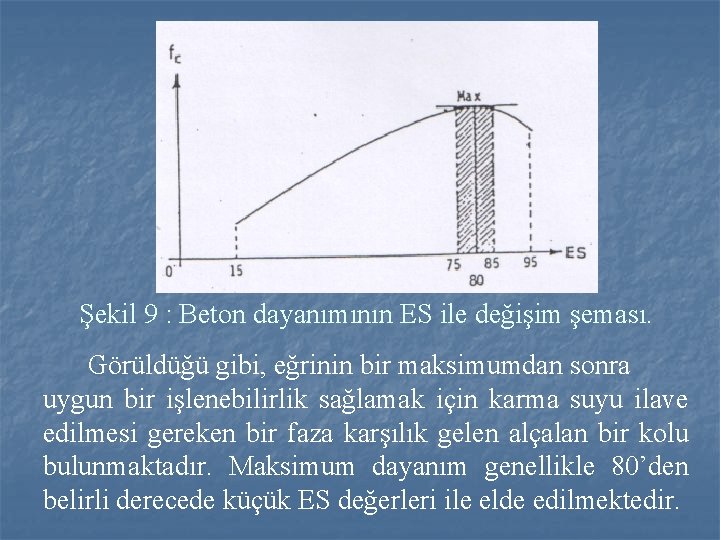
Şekil 9 : Beton dayanımının ES ile değişim şeması. Görüldüğü gibi, eğrinin bir maksimumdan sonra uygun bir işlenebilirlik sağlamak için karma suyu ilave edilmesi gereken bir faza karşılık gelen alçalan bir kolu bulunmaktadır. Maksimum dayanım genellikle 80’den belirli derecede küçük ES değerleri ile elde edilmektedir.
- Slides: 59