Accurate Signoff with Advanced Variation Methodology Moonsu Kim
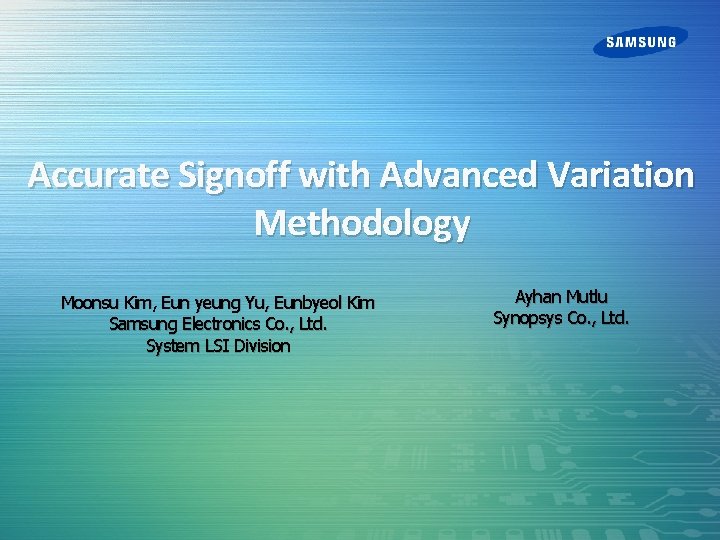
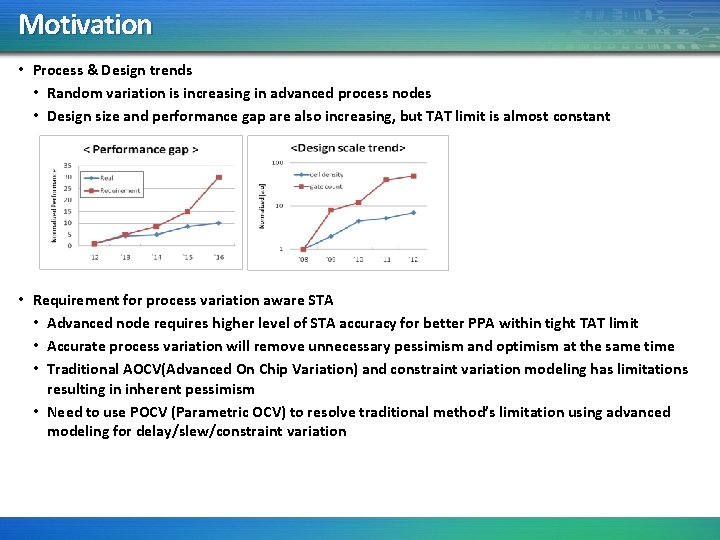
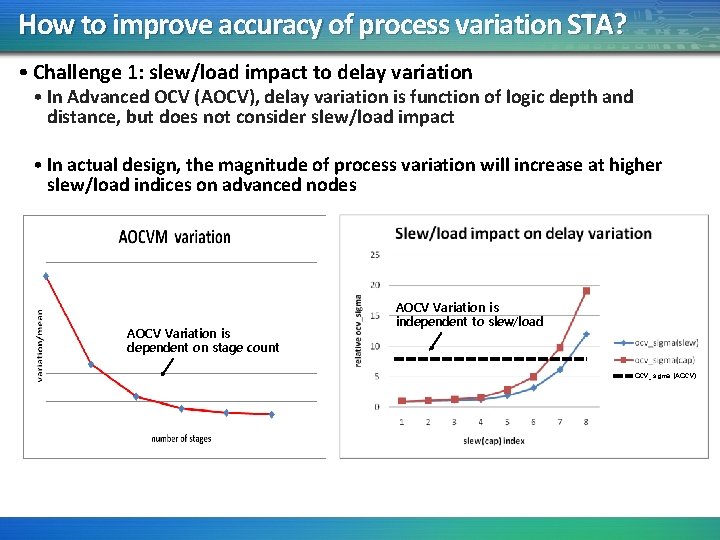
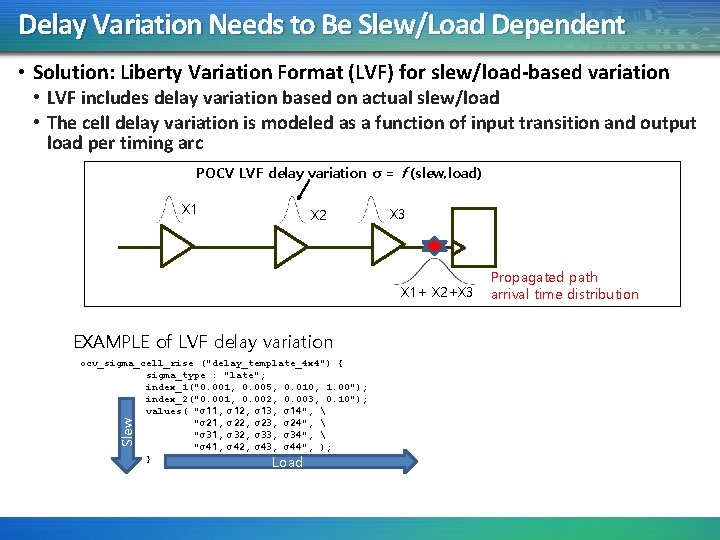
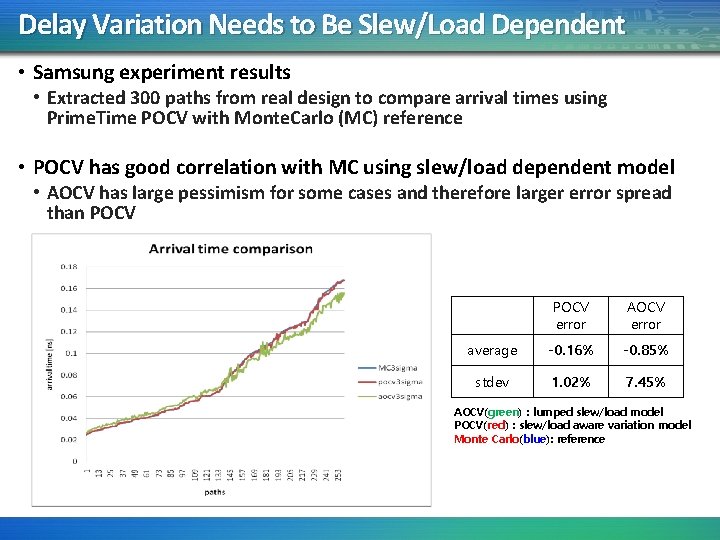
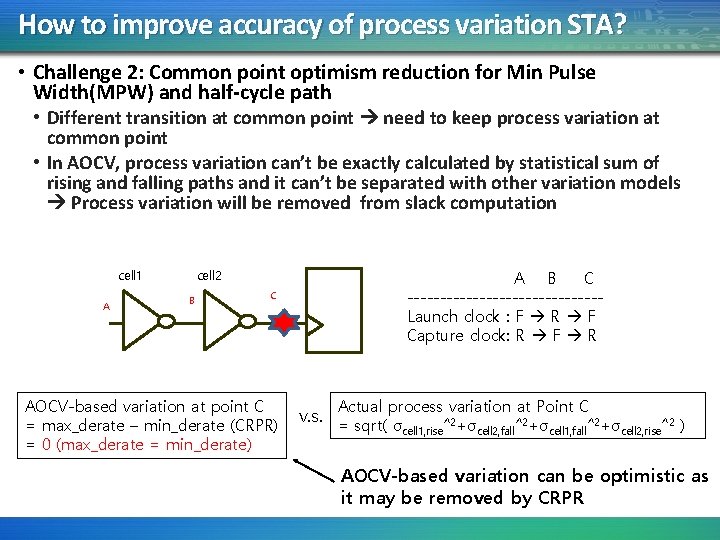
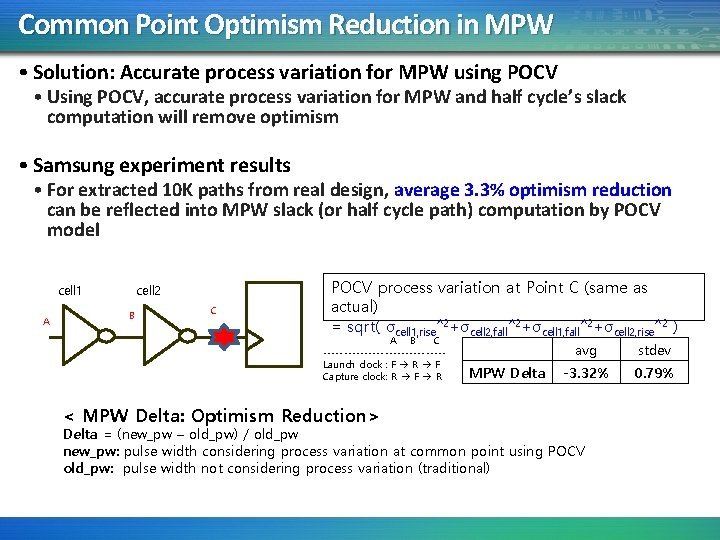
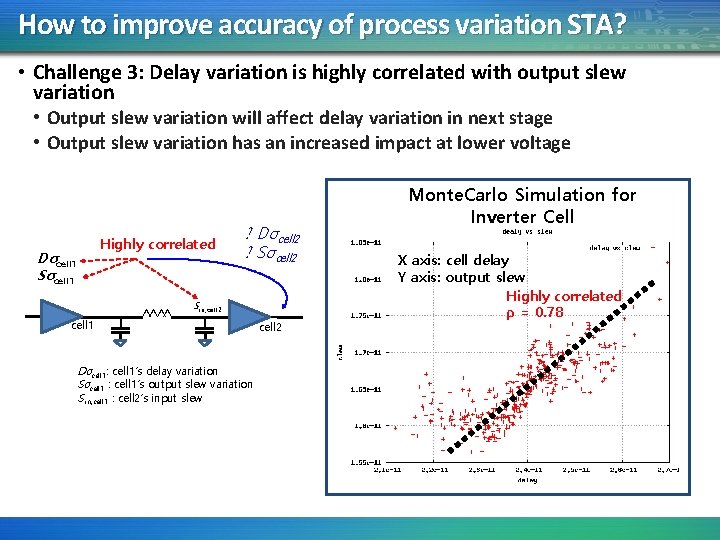
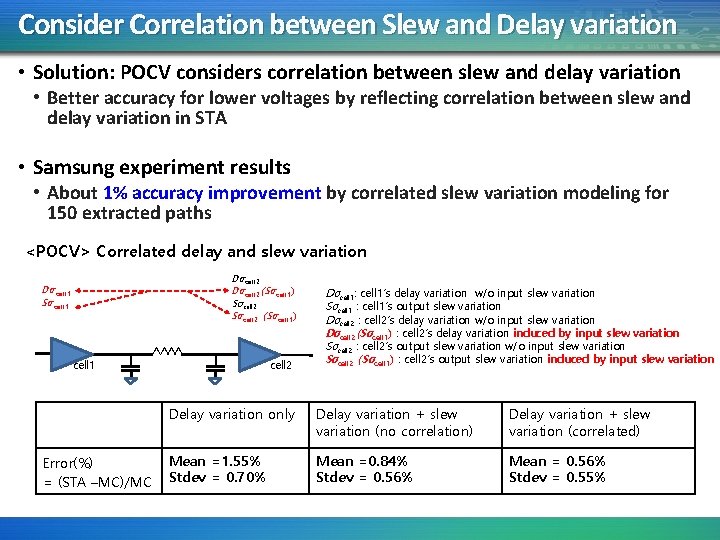
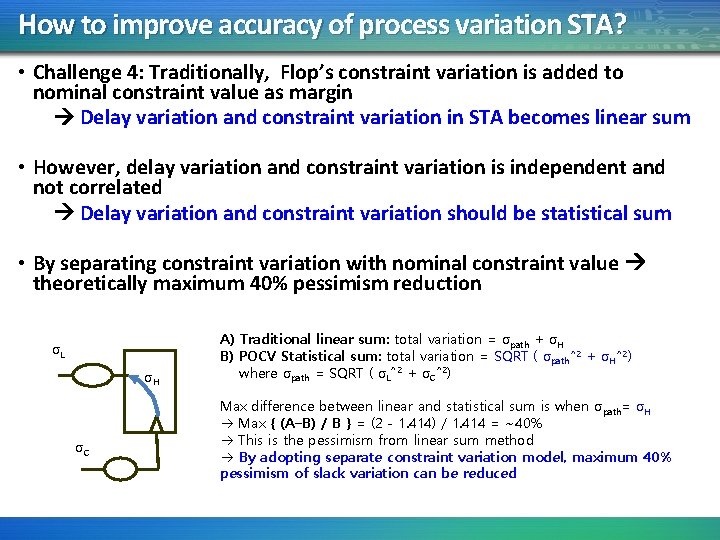
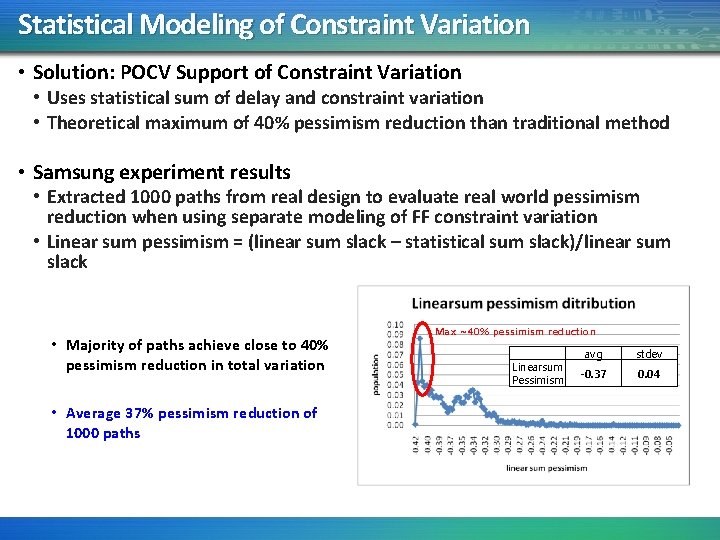
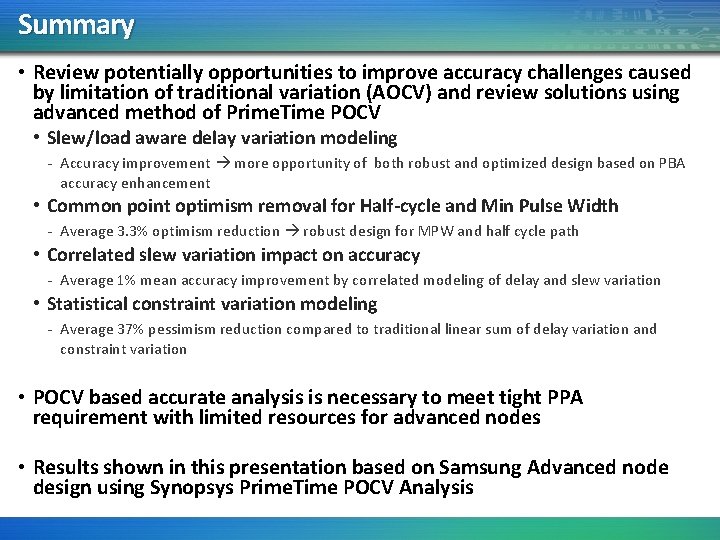
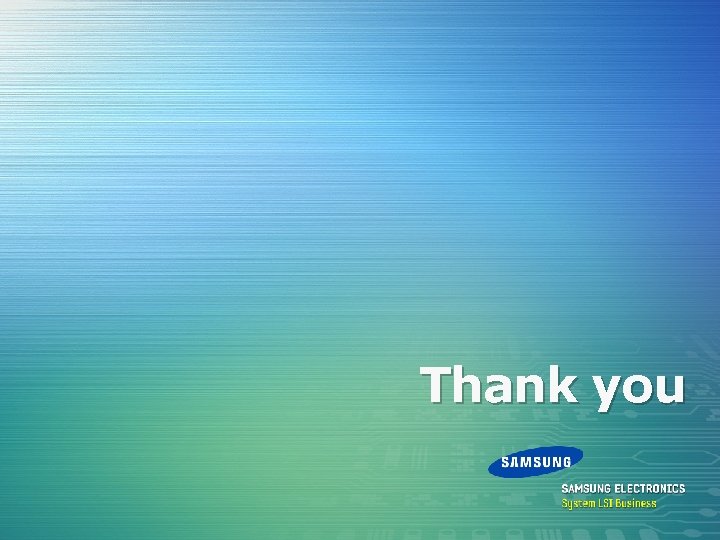
- Slides: 13
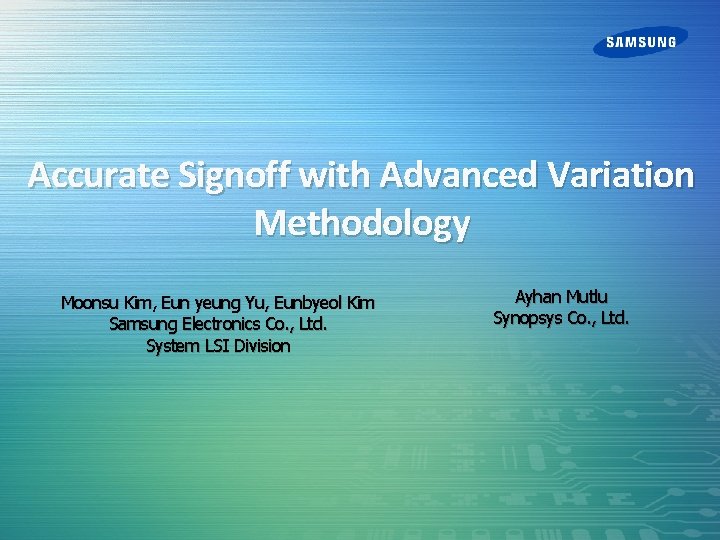
Accurate Signoff with Advanced Variation Methodology Moonsu Kim, Eun yeung Yu, Eunbyeol Kim Samsung Electronics Co. , Ltd. System LSI Division Ayhan Mutlu Synopsys Co. , Ltd.
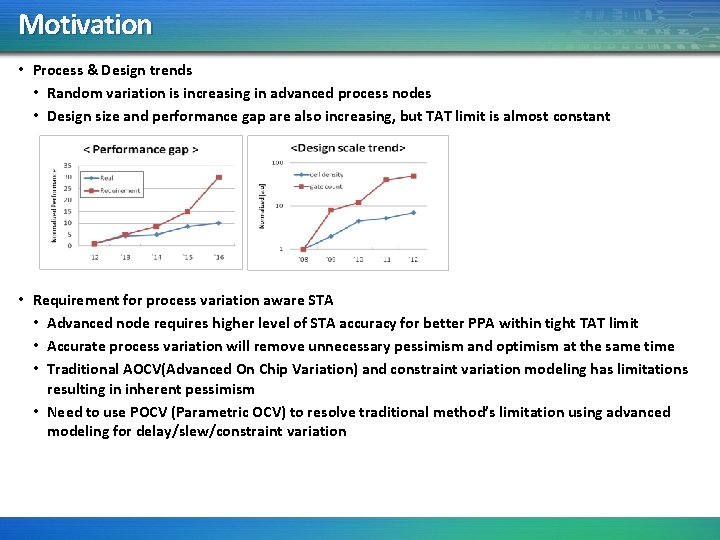
Motivation • Process & Design trends • Random variation is increasing in advanced process nodes • Design size and performance gap are also increasing, but TAT limit is almost constant • Requirement for process variation aware STA • Advanced node requires higher level of STA accuracy for better PPA within tight TAT limit • Accurate process variation will remove unnecessary pessimism and optimism at the same time • Traditional AOCV(Advanced On Chip Variation) and constraint variation modeling has limitations resulting in inherent pessimism • Need to use POCV (Parametric OCV) to resolve traditional method’s limitation using advanced modeling for delay/slew/constraint variation
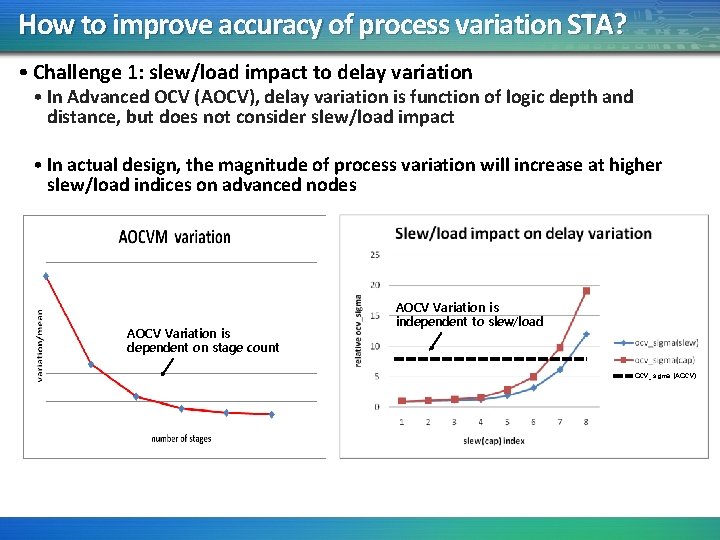
How to improve accuracy of process variation STA? • Challenge 1: slew/load impact to delay variation • In Advanced OCV (AOCV), delay variation is function of logic depth and distance, but does not consider slew/load impact • In actual design, the magnitude of process variation will increase at higher slew/load indices on advanced nodes AOCV Variation is dependent on stage count AOCV Variation is independent to slew/load OCV_sigma (AOCV)
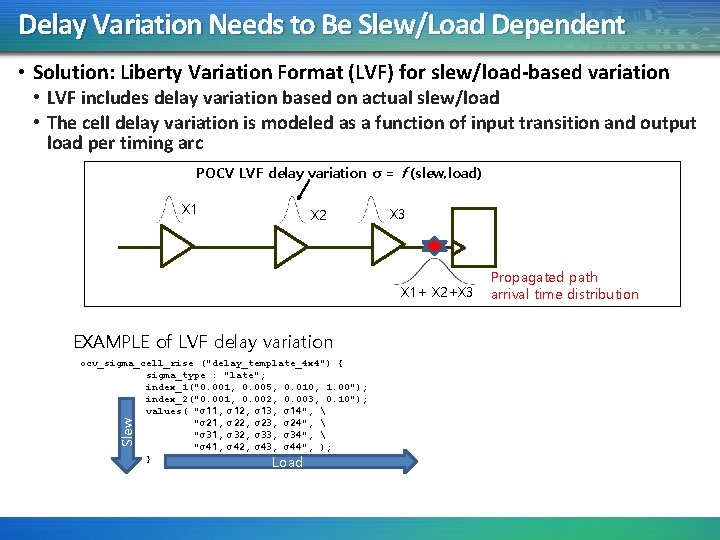
Delay Variation Needs to Be Slew/Load Dependent • Solution: Liberty Variation Format (LVF) for slew/load-based variation • LVF includes delay variation based on actual slew/load • The cell delay variation is modeled as a function of input transition and output load per timing arc POCV LVF delay variation σ = f (slew, load) X 1 X 2 X 3 X 1+ X 2+X 3 EXAMPLE of LVF delay variation Slew ocv_sigma_cell_rise ("delay_template_4 x 4") { sigma_type : "late"; index_1("0. 001, 0. 005, 0. 010, 1. 00"); index_2("0. 001, 0. 002, 0. 003, 0. 10"); values( "σ11, σ12, σ13, σ14", "σ21, σ22, σ23, σ24", "σ31, σ32, σ33, σ34", "σ41, σ42, σ43, σ44", ); } Load Propagated path arrival time distribution
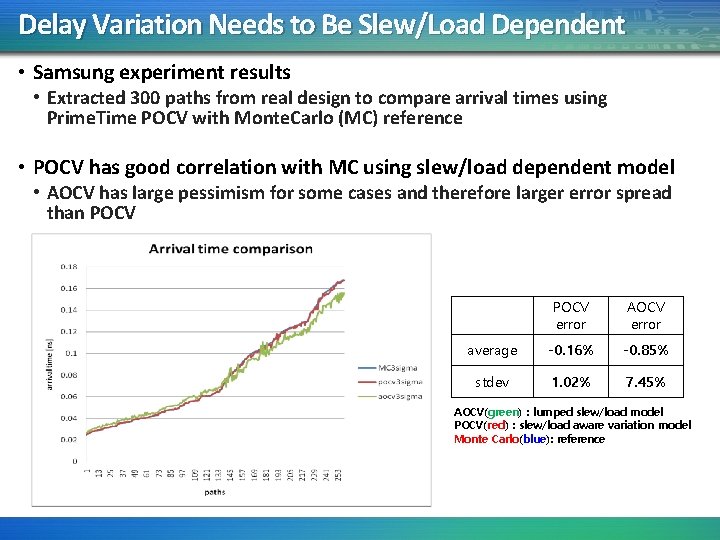
Delay Variation Needs to Be Slew/Load Dependent • Samsung experiment results • Extracted 300 paths from real design to compare arrival times using Prime. Time POCV with Monte. Carlo (MC) reference • POCV has good correlation with MC using slew/load dependent model • AOCV has large pessimism for some cases and therefore larger error spread than POCV error AOCV error average -0. 16% -0. 85% stdev 1. 02% 7. 45% AOCV(green) : lumped slew/load model POCV(red) : slew/load aware variation model Monte Carlo(blue): reference
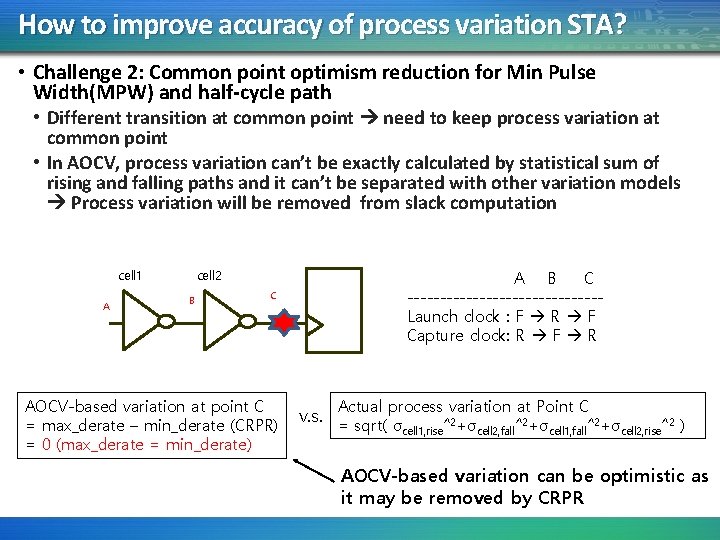
How to improve accuracy of process variation STA? • Challenge 2: Common point optimism reduction for Min Pulse Width(MPW) and half-cycle path • Different transition at common point need to keep process variation at common point • In AOCV, process variation can’t be exactly calculated by statistical sum of rising and falling paths and it can’t be separated with other variation models Process variation will be removed from slack computation cell 1 A cell 2 B C AOCV-based variation at point C = max_derate – min_derate (CRPR) = 0 (max_derate = min_derate) A B C ---------------Launch clock : F R F Capture clock: R F R Actual process variation at Point C v. s. = sqrt( σ ^2 ^2 ) cell 1, rise +σcell 2, fall +σcell 1, fall +σcell 2, rise AOCV-based variation can be optimistic as it may be removed by CRPR
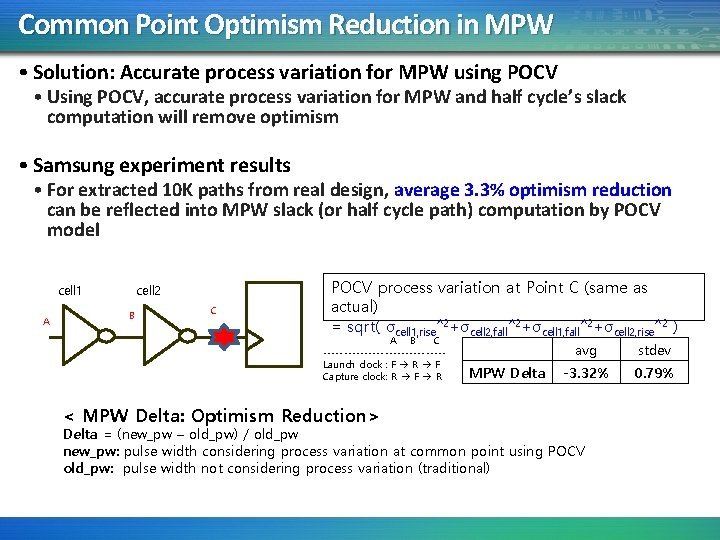
Common Point Optimism Reduction in MPW • Solution: Accurate process variation for MPW using POCV • Using POCV, accurate process variation for MPW and half cycle’s slack computation will remove optimism • Samsung experiment results • For extracted 10 K paths from real design, average 3. 3% optimism reduction can be reflected into MPW slack (or half cycle path) computation by POCV model cell 1 A cell 2 B C POCV process variation at Point C (same as actual) = sqrt( σcell 1, rise^2+σcell 2, fall^2+σcell 1, fall^2+σcell 2, rise^2 ) A B C ---------------Launch clock : F R F Capture clock: R F R < MPW Delta: Optimism Reduction> MPW Delta avg stdev -3. 32% 0. 79% Delta = (new_pw – old_pw) / old_pw new_pw: pulse width considering process variation at common point using POCV old_pw: pulse width not considering process variation (traditional)
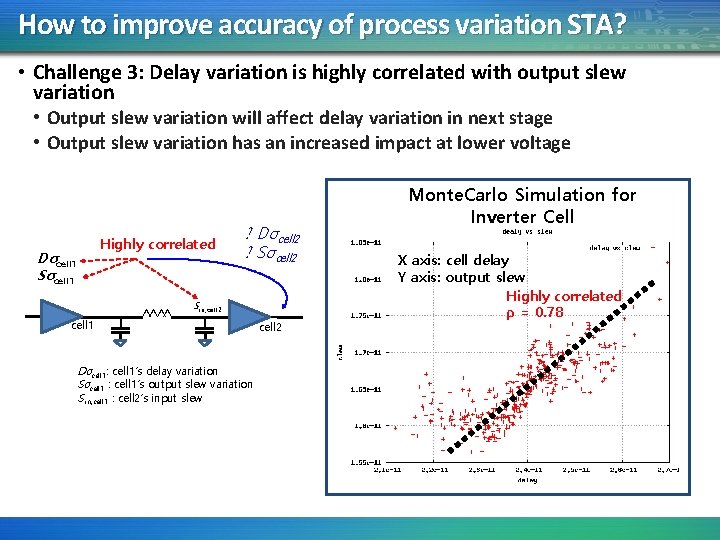
How to improve accuracy of process variation STA? • Challenge 3: Delay variation is highly correlated with output slew variation • Output slew variation will affect delay variation in next stage • Output slew variation has an increased impact at lower voltage Highly correlated Dσcell 1 Sσcell 1 ^^^^ ? Dσcell 2 ? Sσcell 2 Sin, cell 2 Dσcell 1: cell 1’s delay variation Sσcell 1 : cell 1’s output slew variation S in, cell 1 : cell 2’s input slew cell 2 Monte. Carlo Simulation for Inverter Cell X axis: cell delay Y axis: output slew Highly correlated ρ = 0. 78
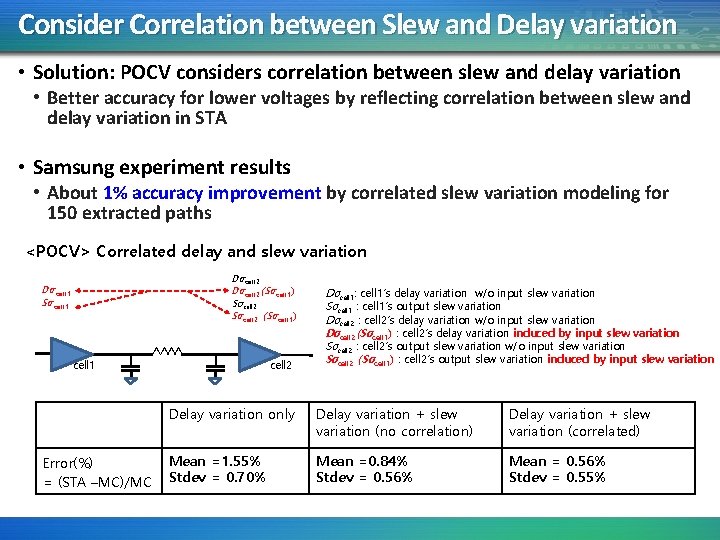
Consider Correlation between Slew and Delay variation • Solution: POCV considers correlation between slew and delay variation • Better accuracy for lower voltages by reflecting correlation between slew and delay variation in STA • Samsung experiment results • About 1% accuracy improvement by correlated slew variation modeling for 150 extracted paths <POCV> Correlated delay and slew variation Dσcell 2(Sσcell 1) Sσcell 2 (Sσcell 1) Dσcell 1 Sσcell 1 ^^^^ Error(%) = (STA –MC)/MC cell 2 Dσcell 1: cell 1’s delay variation w/o input slew variation Sσcell 1 : cell 1’s output slew variation Dσcell 2 : cell 2’s delay variation w/o input slew variation Dσcell 2(Sσcell 1) : cell 2’s delay variation induced by input slew variation Sσcell 2 : cell 2’s output slew variation w/o input slew variation Sσcell 2 (Sσcell 1) : cell 2’s output slew variation induced by input slew variation Delay variation only Delay variation + slew variation (no correlation) Delay variation + slew variation (correlated) Mean =1. 55% Stdev = 0. 70% Mean =0. 84% Stdev = 0. 56% Mean = 0. 56% Stdev = 0. 55%
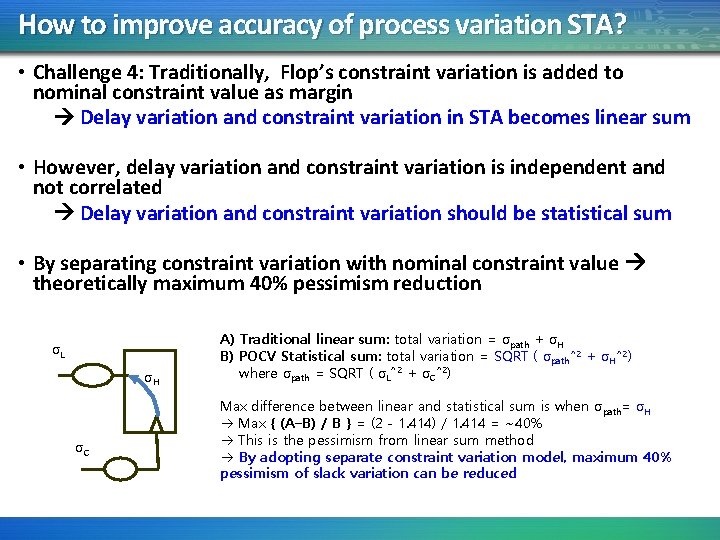
How to improve accuracy of process variation STA? • Challenge 4: Traditionally, Flop’s constraint variation is added to nominal constraint value as margin Delay variation and constraint variation in STA becomes linear sum • However, delay variation and constraint variation is independent and not correlated Delay variation and constraint variation should be statistical sum • By separating constraint variation with nominal constraint value theoretically maximum 40% pessimism reduction σL σH σC A) Traditional linear sum: total variation = σpath + σH B) POCV Statistical sum: total variation = SQRT ( σpath^2 + σH^2) where σpath = SQRT ( σL^2 + σC^2) Max difference between linear and statistical sum is when σpath= σH Max { (A–B) / B } = (2 - 1. 414) / 1. 414 = ~40% This is the pessimism from linear sum method By adopting separate constraint variation model, maximum 40% pessimism of slack variation can be reduced
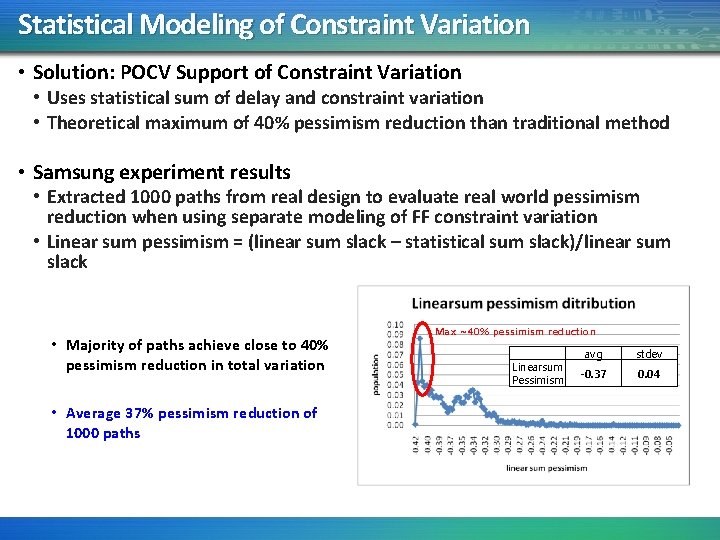
Statistical Modeling of Constraint Variation • Solution: POCV Support of Constraint Variation • Uses statistical sum of delay and constraint variation • Theoretical maximum of 40% pessimism reduction than traditional method • Samsung experiment results • Extracted 1000 paths from real design to evaluate real world pessimism reduction when using separate modeling of FF constraint variation • Linear sum pessimism = (linear sum slack – statistical sum slack)/linear sum slack • Majority of paths achieve close to 40% pessimism reduction in total variation • Average 37% pessimism reduction of 1000 paths Max ~40% pessimism reduction Linearsum Pessimism avg stdev -0. 37 0. 04
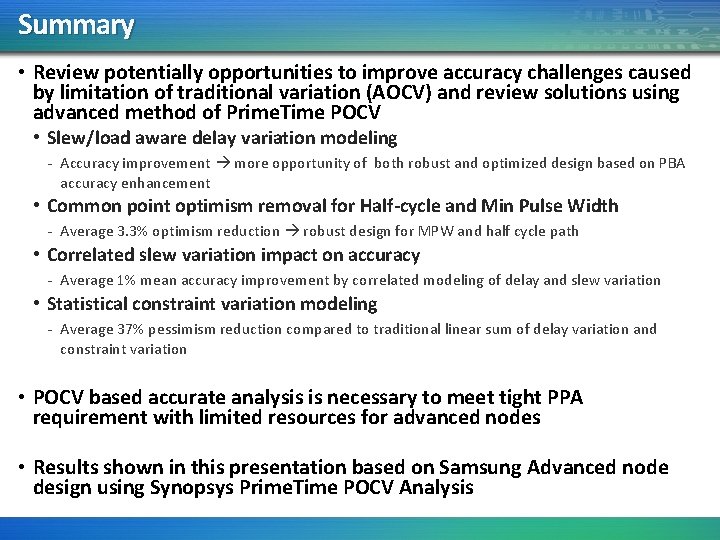
Summary • Review potentially opportunities to improve accuracy challenges caused by limitation of traditional variation (AOCV) and review solutions using advanced method of Prime. Time POCV • Slew/load aware delay variation modeling - Accuracy improvement more opportunity of both robust and optimized design based on PBA accuracy enhancement • Common point optimism removal for Half-cycle and Min Pulse Width - Average 3. 3% optimism reduction robust design for MPW and half cycle path • Correlated slew variation impact on accuracy - Average 1% mean accuracy improvement by correlated modeling of delay and slew variation • Statistical constraint variation modeling - Average 37% pessimism reduction compared to traditional linear sum of delay variation and constraint variation • POCV based accurate analysis is necessary to meet tight PPA requirement with limited resources for advanced nodes • Results shown in this presentation based on Samsung Advanced node design using Synopsys Prime. Time POCV Analysis
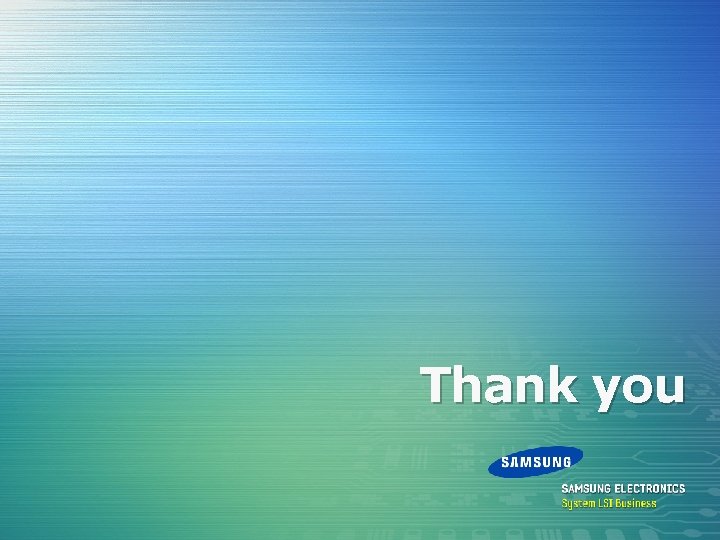
Thank you