1 ENGI 8926 Mechanical Design Project II Downhole
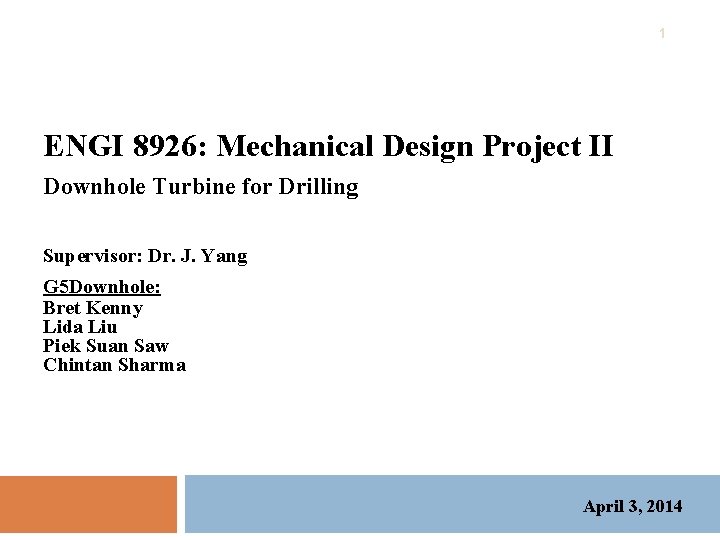
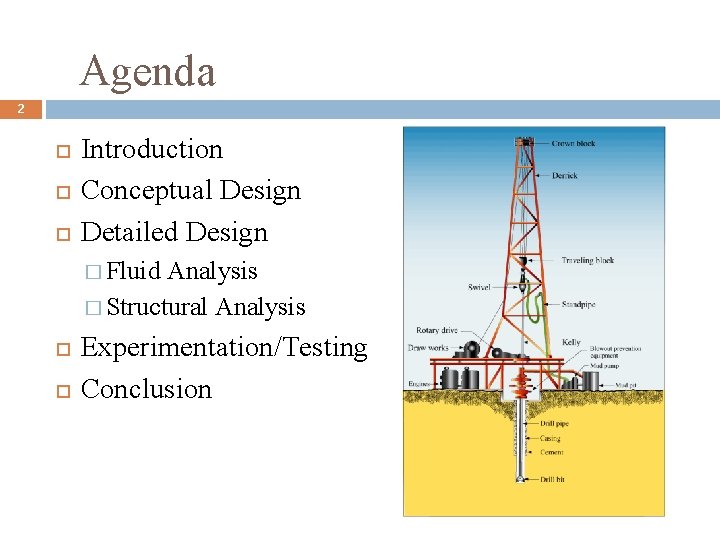
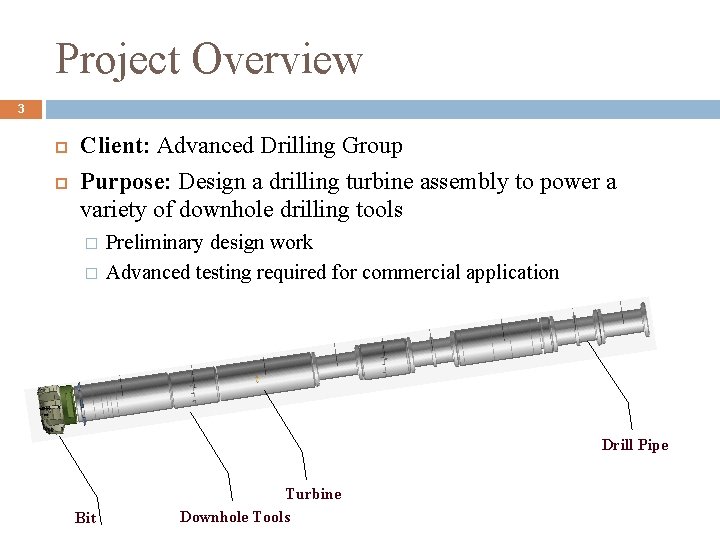
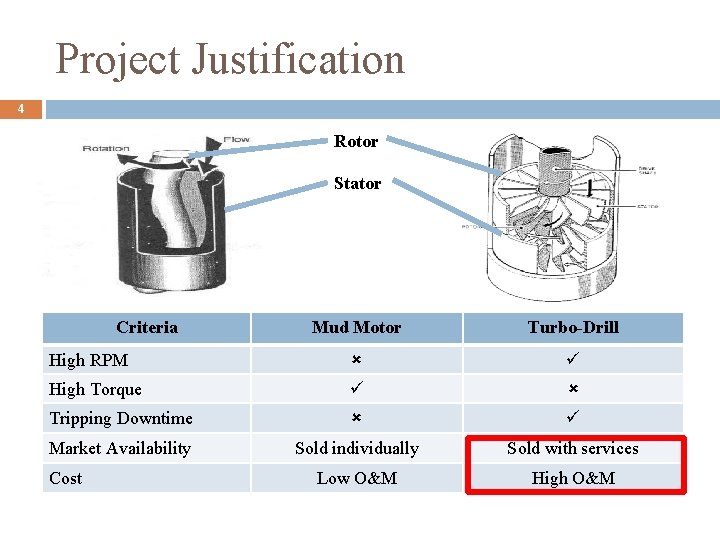
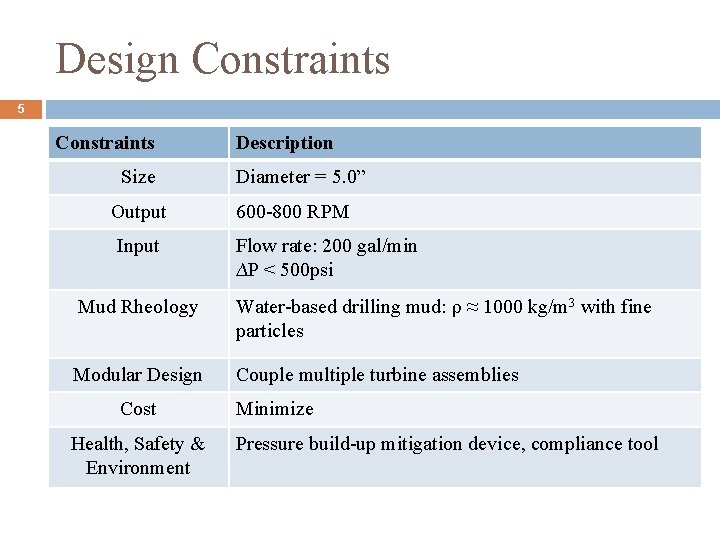
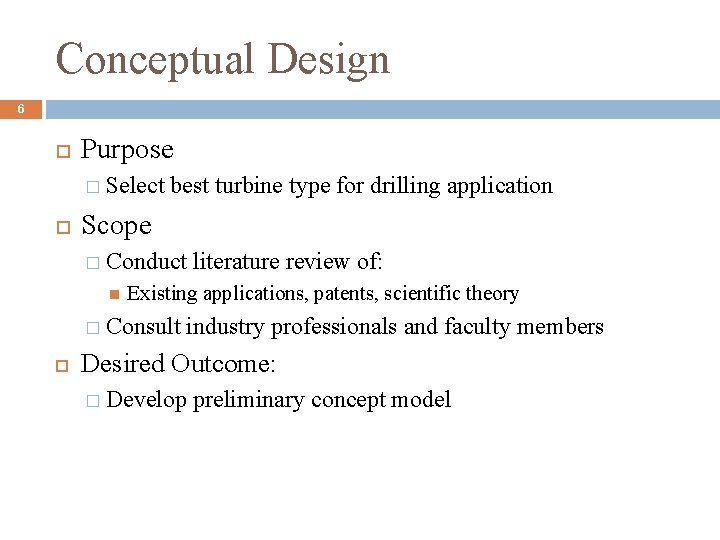
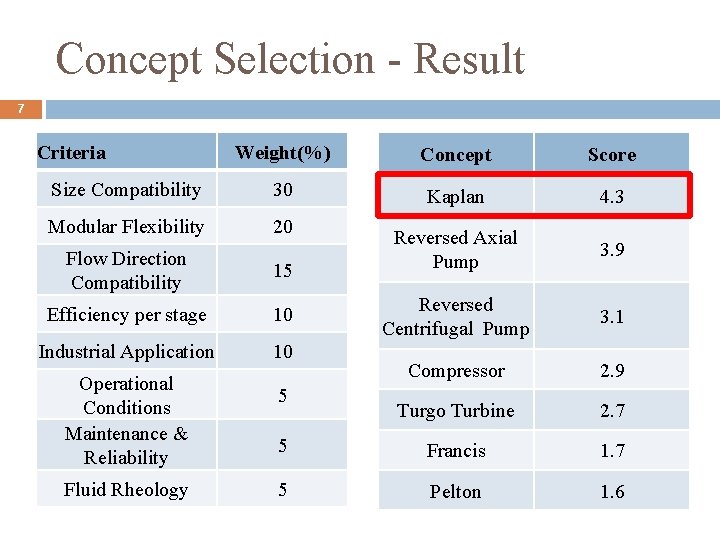
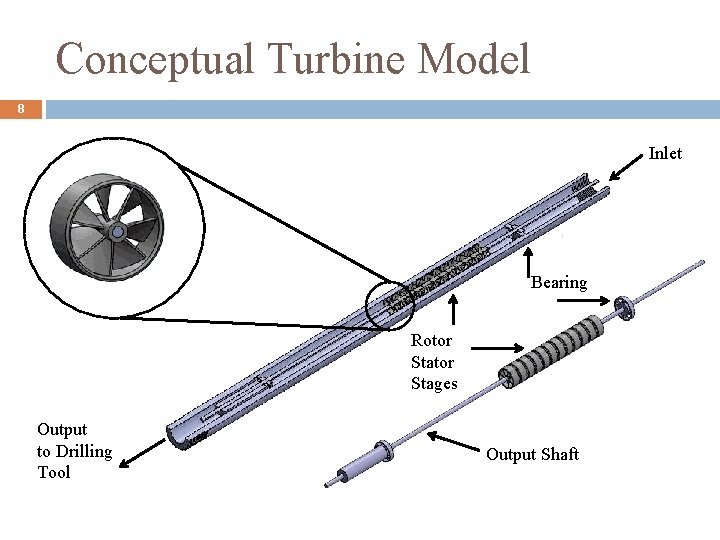
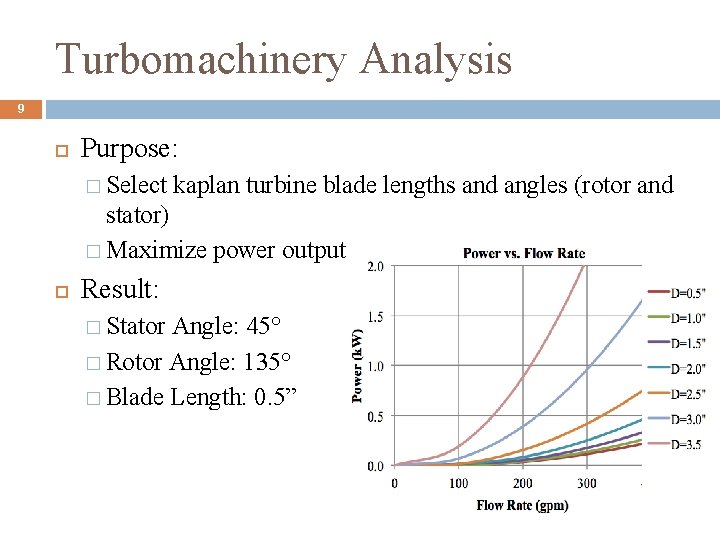
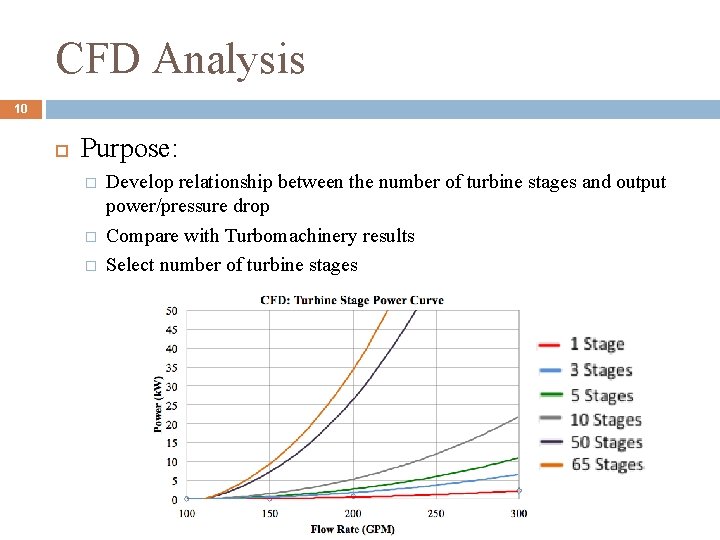
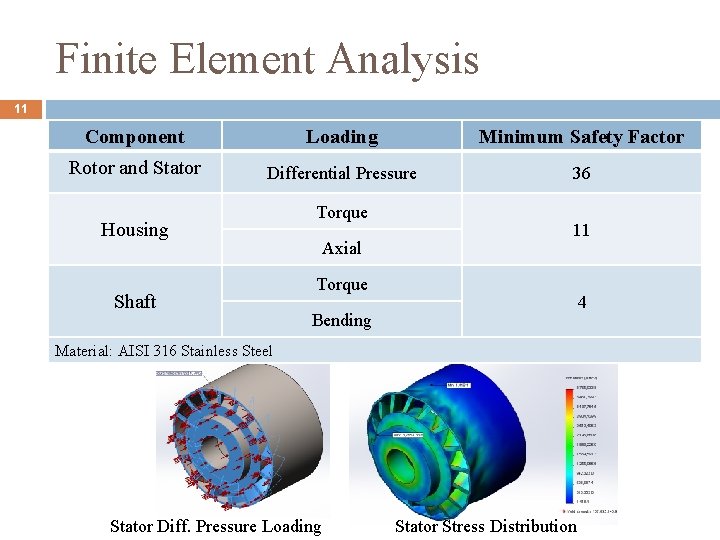
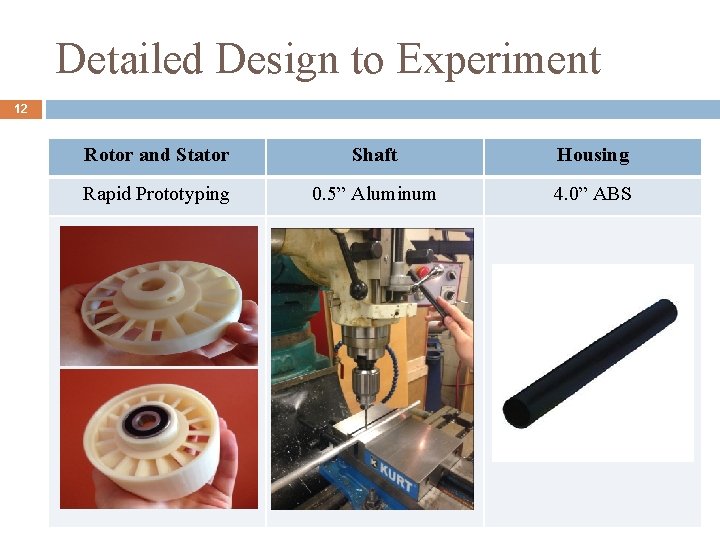
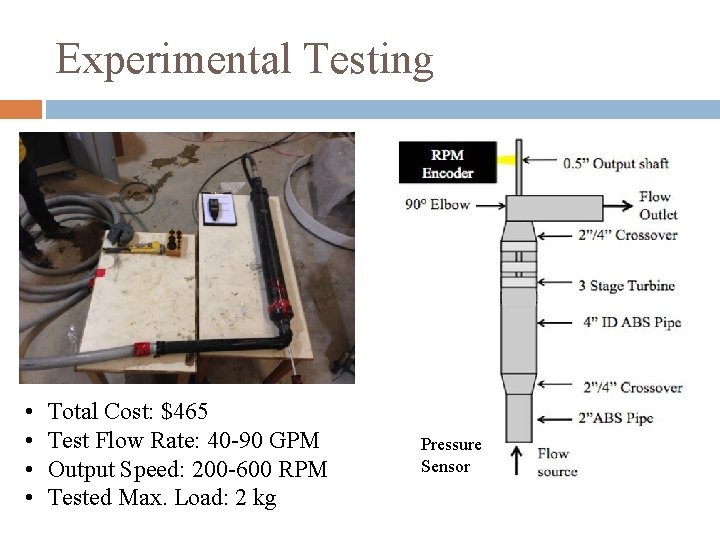
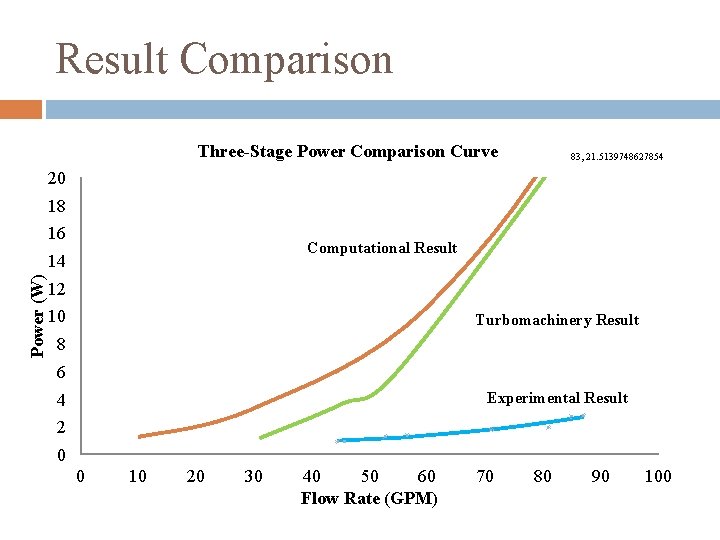
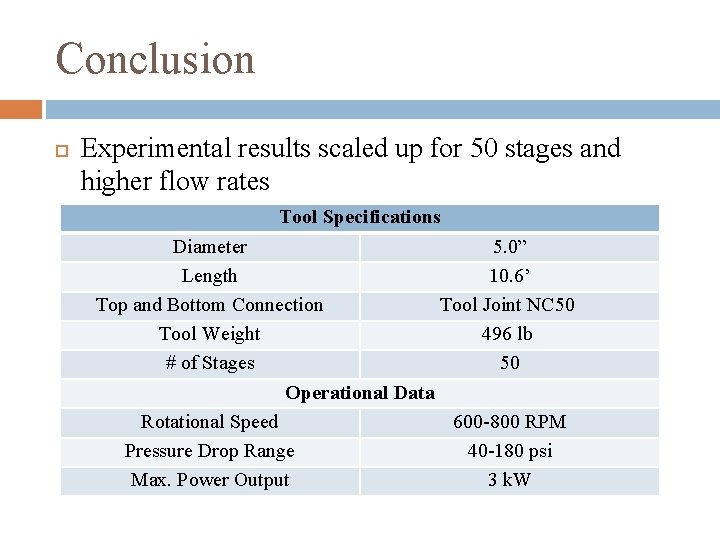
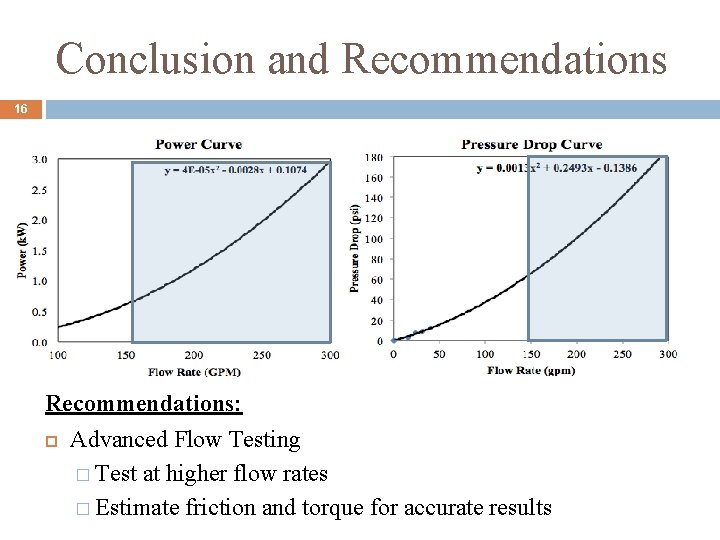
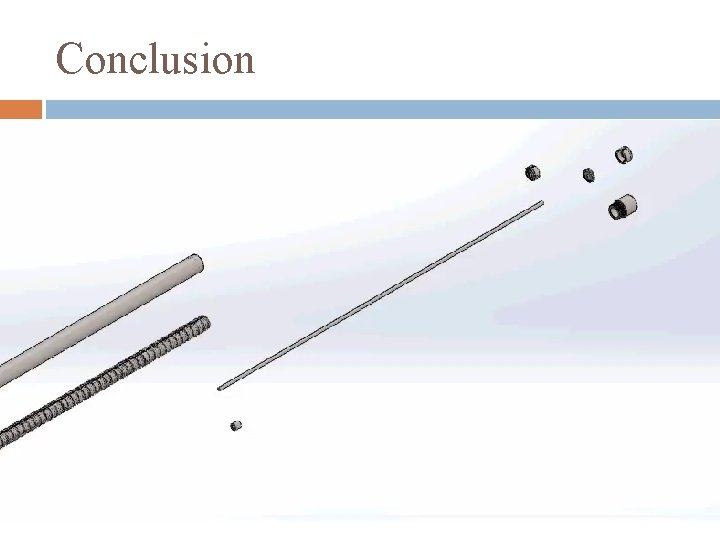
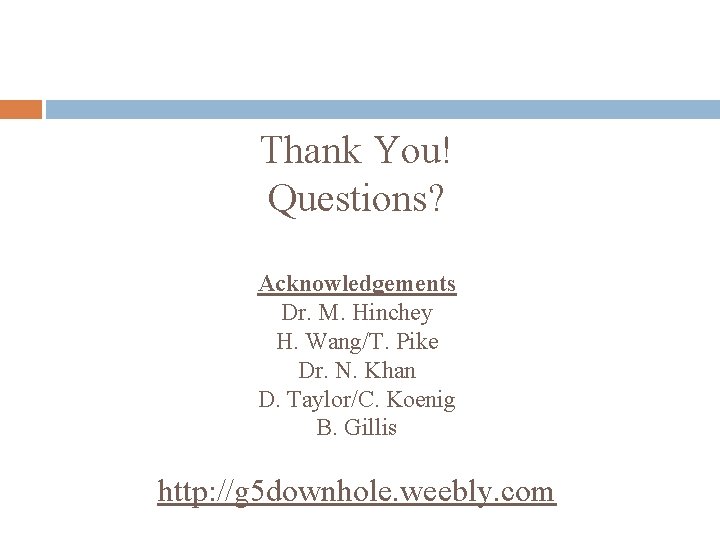
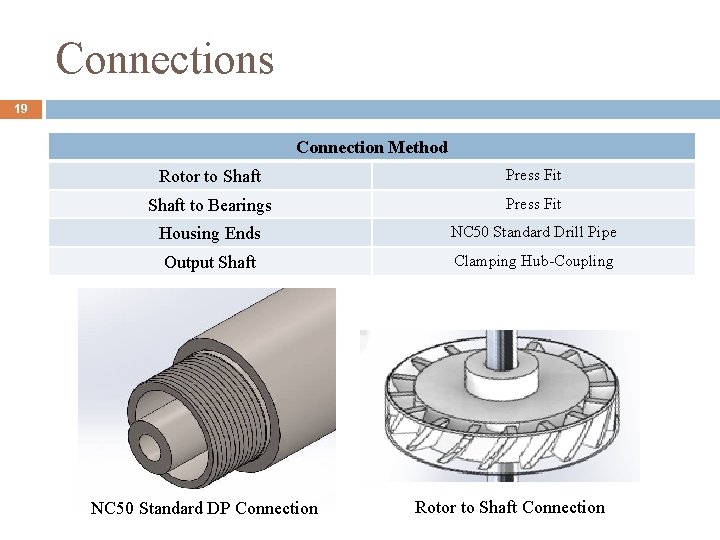
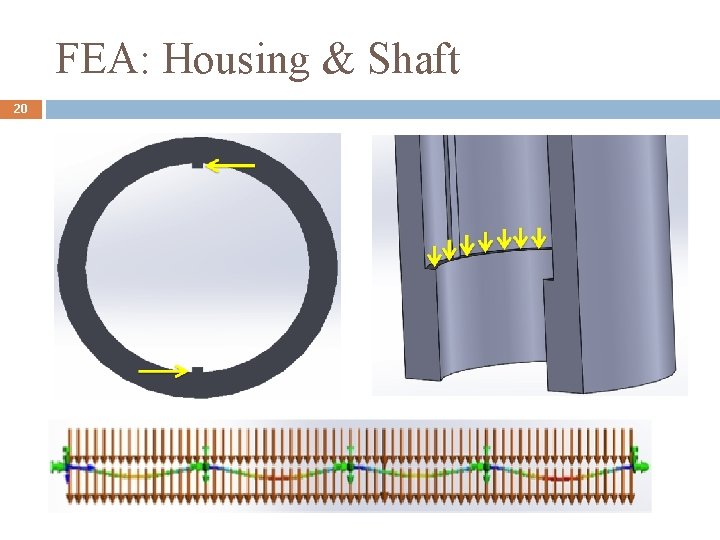
- Slides: 20
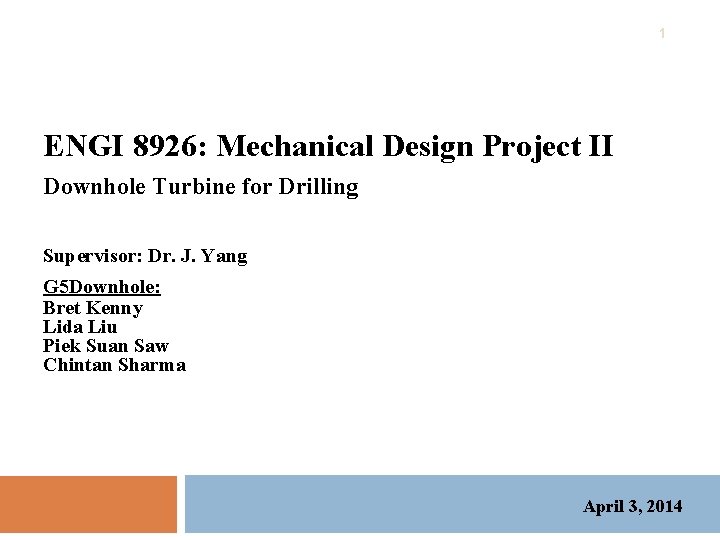
1 ENGI 8926: Mechanical Design Project II Downhole Turbine for Drilling Supervisor: Dr. J. Yang G 5 Downhole: Bret Kenny Lida Liu Piek Suan Saw Chintan Sharma April 3, 2014
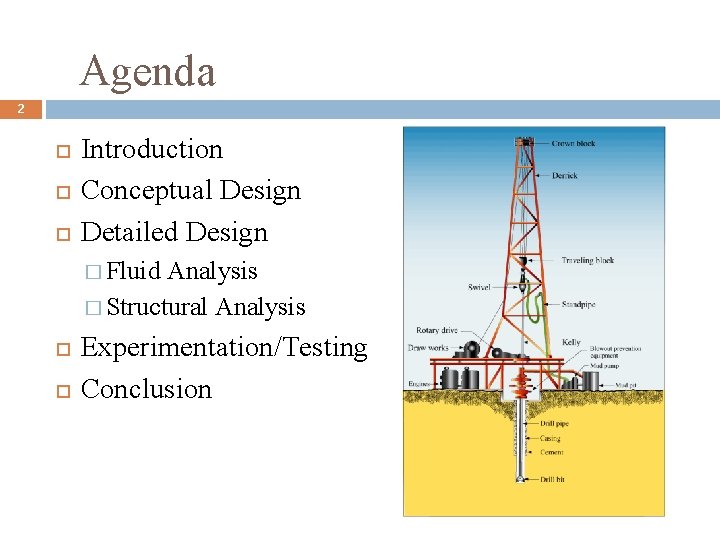
Agenda 2 Introduction Conceptual Design Detailed Design � Fluid Analysis � Structural Analysis Experimentation/Testing Conclusion
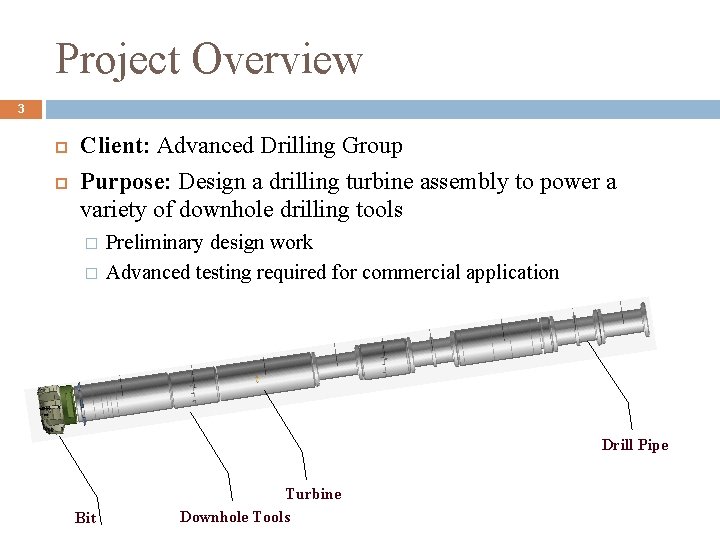
Project Overview 3 Client: Advanced Drilling Group Purpose: Design a drilling turbine assembly to power a variety of downhole drilling tools � � Preliminary design work Advanced testing required for commercial application Drill Pipe Bit Turbine Downhole Tools
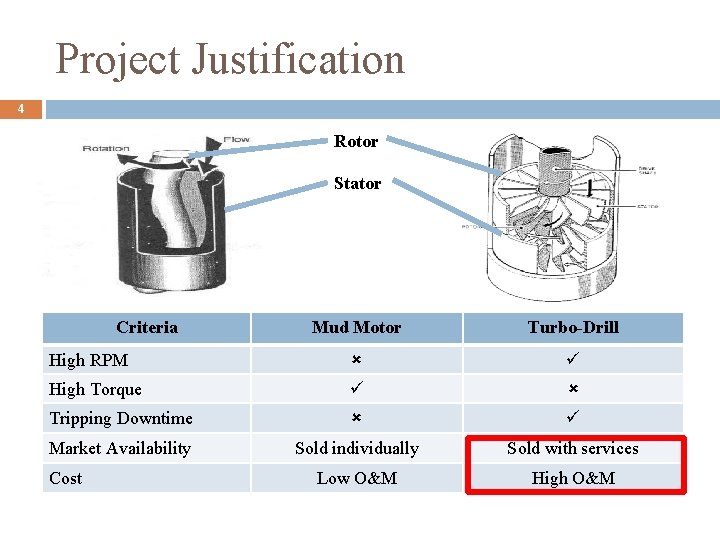
Project Justification 4 Rotor Stator Criteria Mud Motor Turbo-Drill High RPM High Torque Tripping Downtime Market Availability Sold individually Sold with services Low O&M High O&M Cost
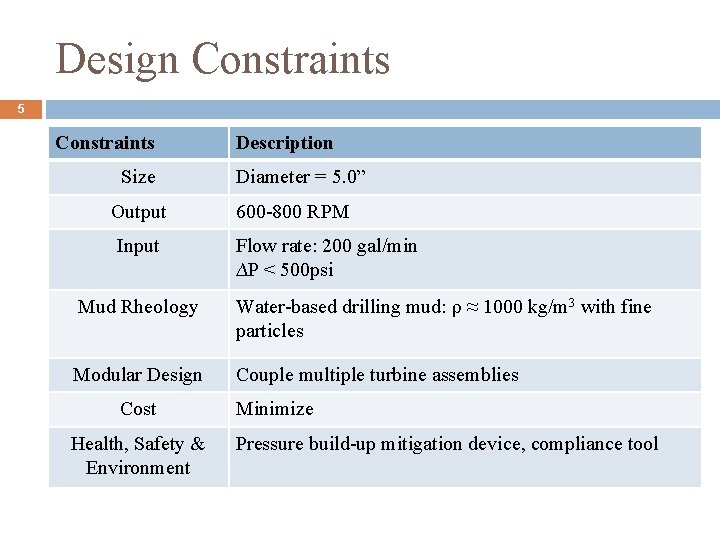
Design Constraints 5 Constraints Size Output Input Description Diameter = 5. 0” 600 -800 RPM Flow rate: 200 gal/min ∆P < 500 psi Mud Rheology Water-based drilling mud: ρ ≈ 1000 kg/m 3 with fine particles Modular Design Couple multiple turbine assemblies Cost Health, Safety & Environment Minimize Pressure build-up mitigation device, compliance tool
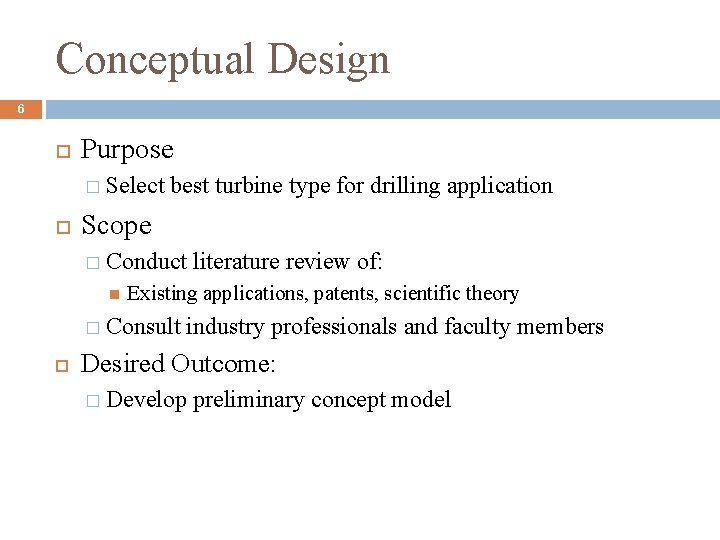
Conceptual Design 6 Purpose � Select best turbine type for drilling application Scope � Conduct literature review of: Existing applications, patents, scientific theory � Consult industry professionals and faculty members Desired Outcome: � Develop preliminary concept model
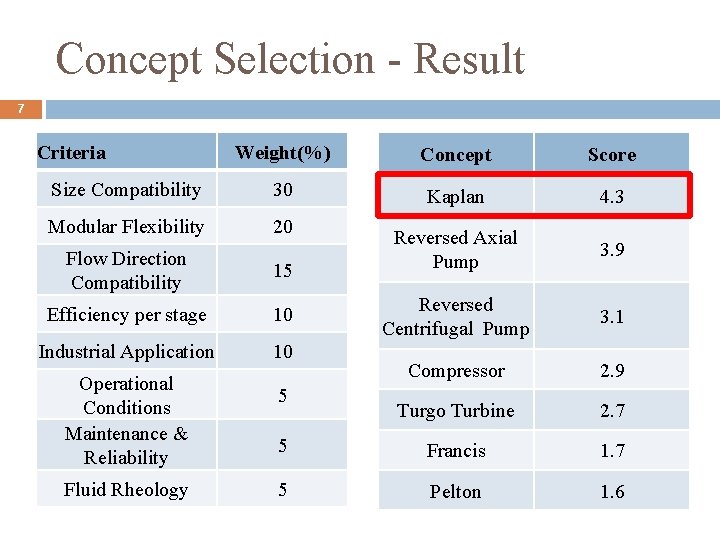
Concept Selection - Result 7 Criteria Weight(%) Concept Score Size Compatibility 30 Kaplan 4. 3 Modular Flexibility 20 Reversed Axial Pump 3. 9 Reversed Centrifugal Pump 3. 1 Compressor 2. 9 Turgo Turbine 2. 7 5 Francis 1. 7 5 Pelton 1. 6 Flow Direction Compatibility 15 Efficiency per stage 10 Industrial Application 10 Operational Conditions Maintenance & Reliability Fluid Rheology 5
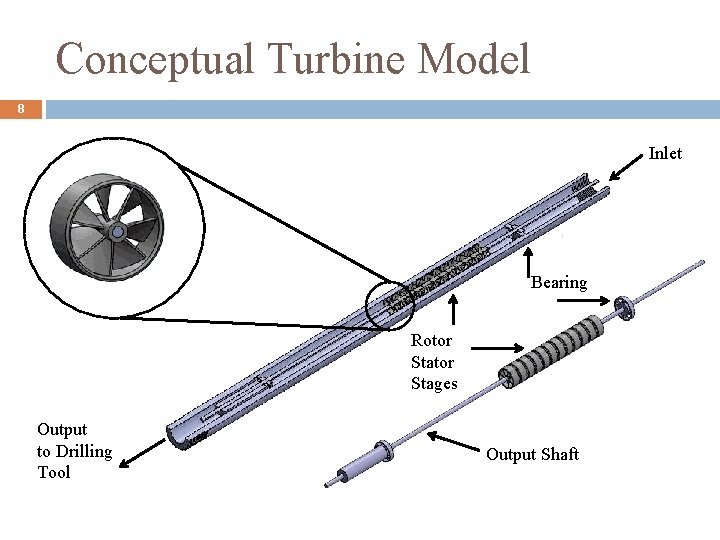
Conceptual Turbine Model 8 Inlet Bearing Rotor Stages Output to Drilling Tool Output Shaft
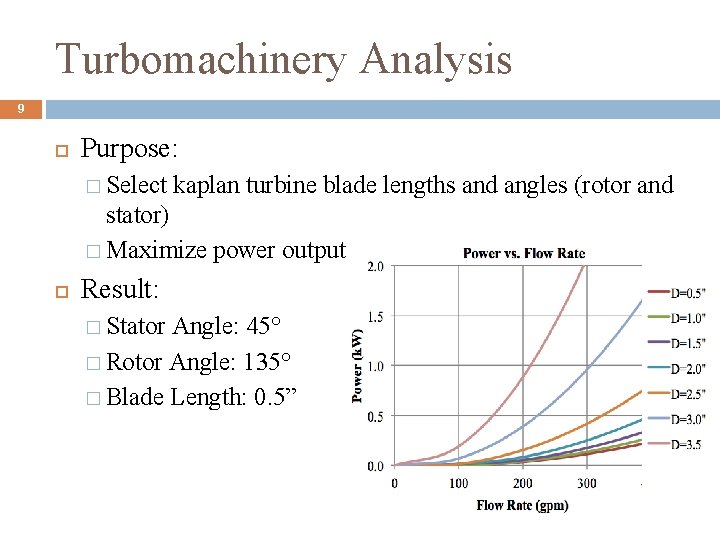
Turbomachinery Analysis 9 Purpose: � Select kaplan turbine blade lengths and angles (rotor and stator) � Maximize power output Result: � Stator Angle: 45° � Rotor Angle: 135° � Blade Length: 0. 5”
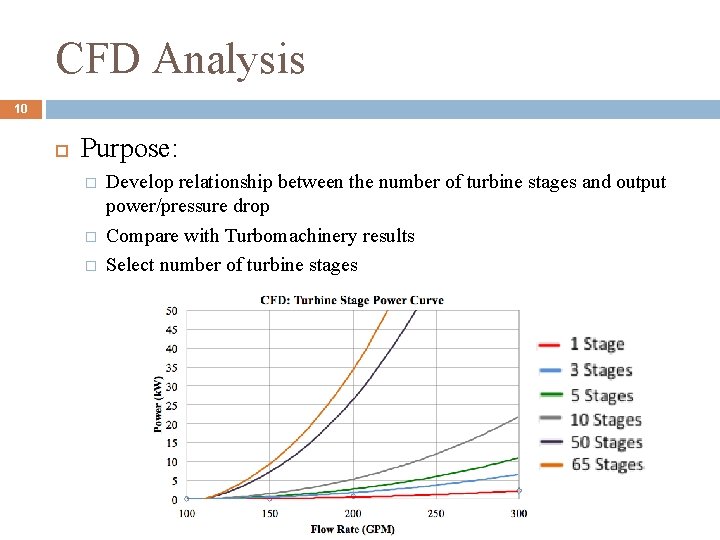
CFD Analysis 10 Purpose: � � � Develop relationship between the number of turbine stages and output power/pressure drop Compare with Turbomachinery results Select number of turbine stages
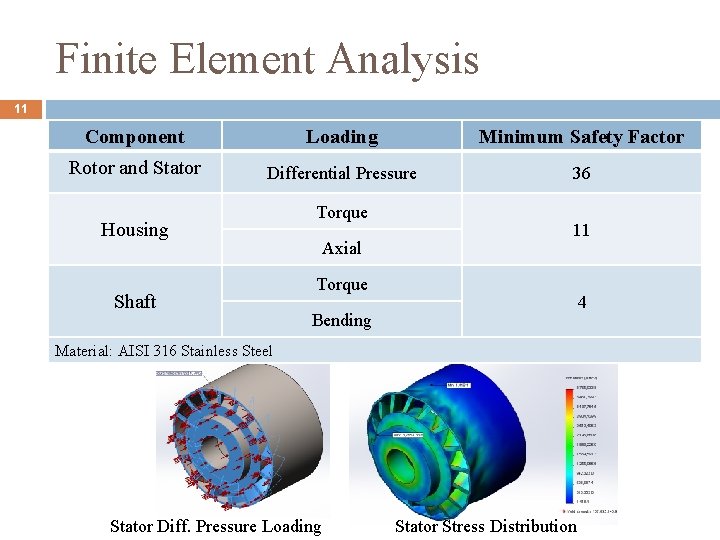
Finite Element Analysis 11 Component Loading Minimum Safety Factor Rotor and Stator Differential Pressure 36 Housing Shaft Torque Axial 11 Torque 4 Bending Material: AISI 316 Stainless Steel Stator Diff. Pressure Loading Stator Stress Distribution
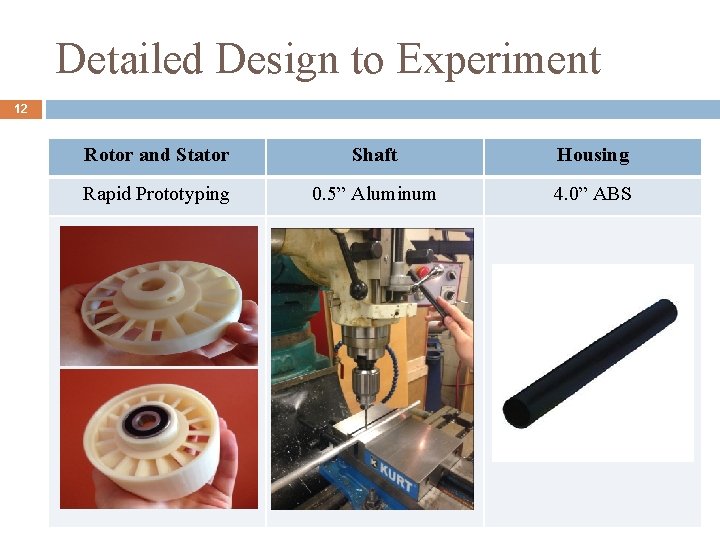
Detailed Design to Experiment 12 Rotor and Stator Shaft Housing Rapid Prototyping 0. 5” Aluminum 4. 0” ABS
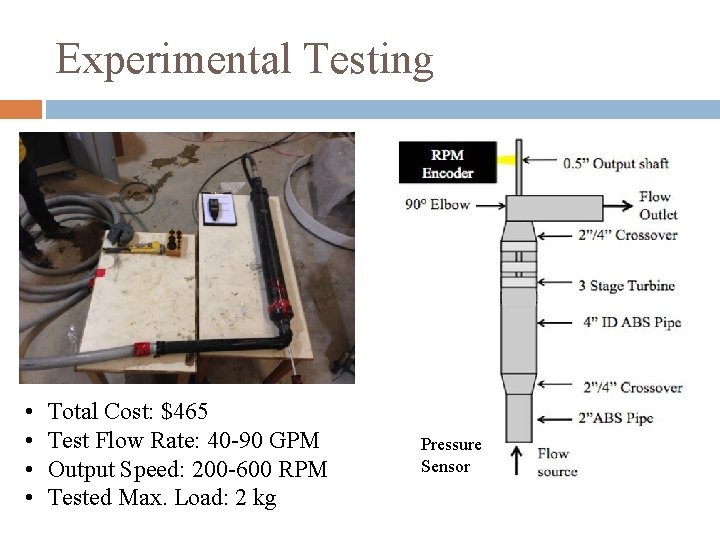
Experimental Testing • • Total Cost: $465 Test Flow Rate: 40 -90 GPM Output Speed: 200 -600 RPM Tested Max. Load: 2 kg Pressure Sensor
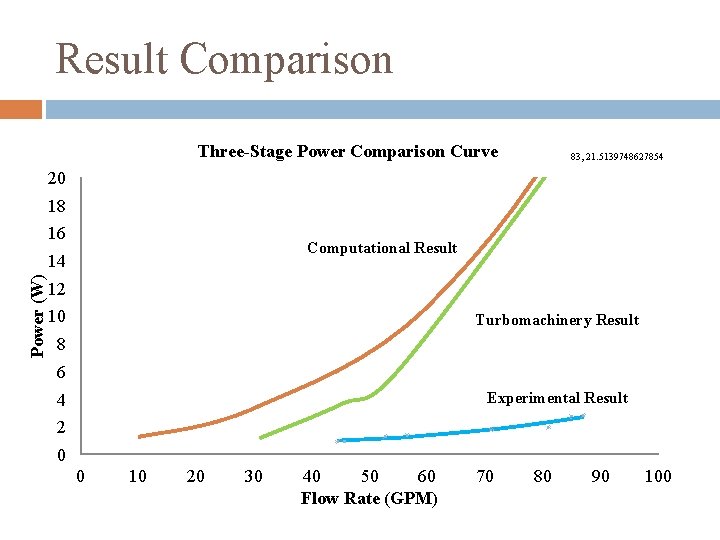
Result Comparison Three-Stage Power Comparison Curve 83, 21. 5139748627854 20 18 16 Computational Result Power (W) 14 12 10 Turbomachinery Result 8 6 Experimental Result 4 2 0 0 10 20 30 40 50 60 Flow Rate (GPM) 70 80 90 100
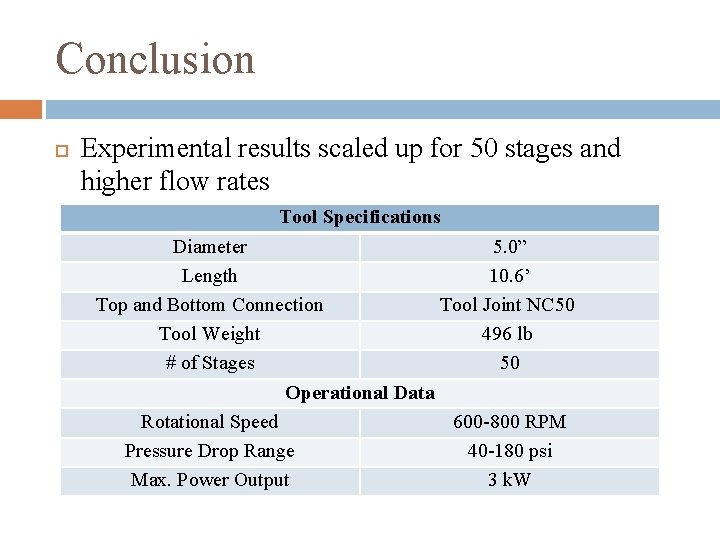
Conclusion Experimental results scaled up for 50 stages and higher flow rates Tool Specifications Diameter 5. 0” Length 10. 6’ Top and Bottom Connection Tool Joint NC 50 Tool Weight 496 lb # of Stages 50 Operational Data Rotational Speed 600 -800 RPM Pressure Drop Range 40 -180 psi Max. Power Output 3 k. W
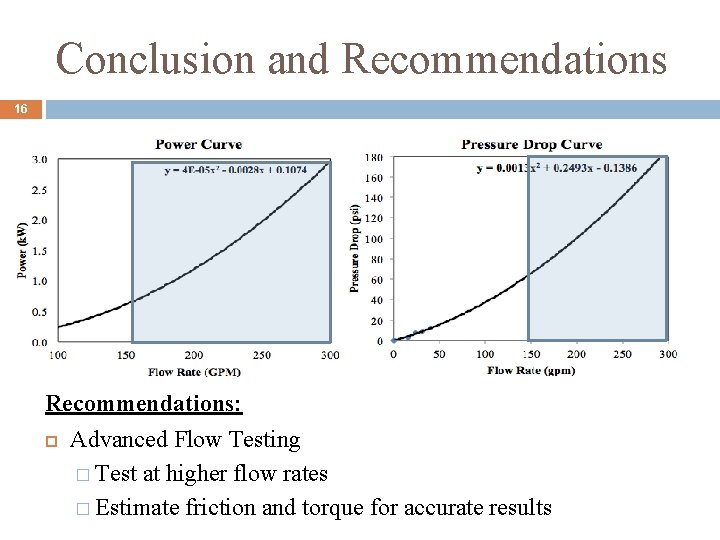
Conclusion and Recommendations 16 Recommendations: Advanced Flow Testing � Test at higher flow rates � Estimate friction and torque for accurate results
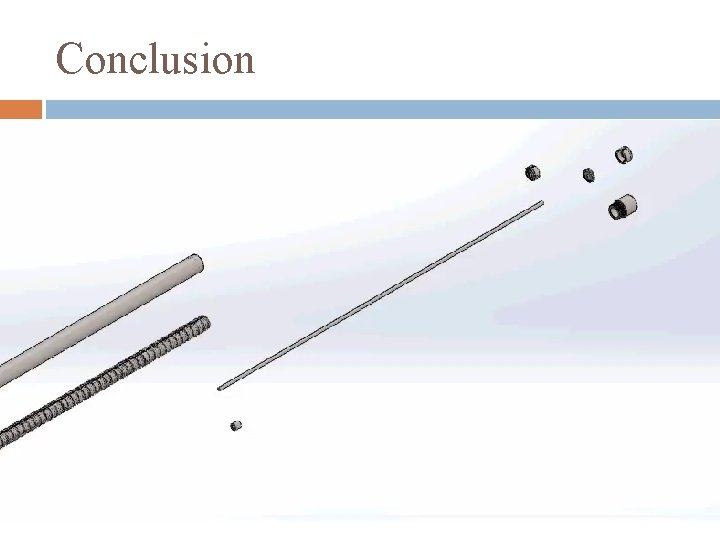
Conclusion
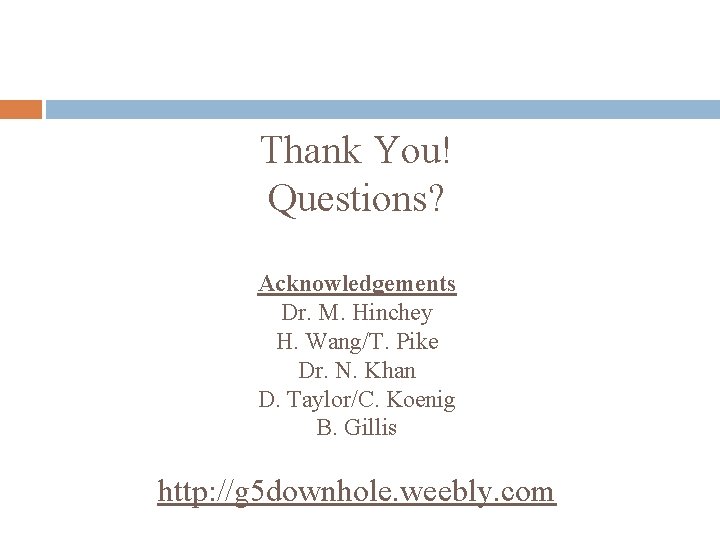
Thank You! Questions? Acknowledgements Dr. M. Hinchey H. Wang/T. Pike Dr. N. Khan D. Taylor/C. Koenig B. Gillis http: //g 5 downhole. weebly. com
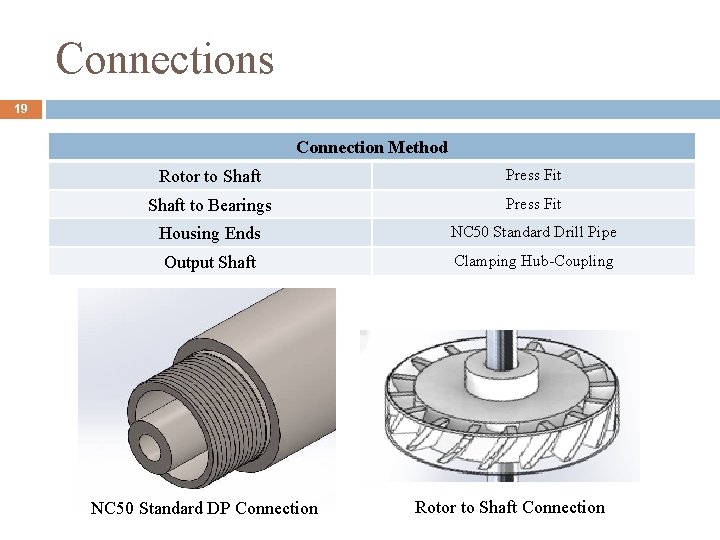
Connections 19 Connection Method Rotor to Shaft Press Fit Shaft to Bearings Press Fit Housing Ends NC 50 Standard Drill Pipe Output Shaft Clamping Hub-Coupling NC 50 Standard DP Connection Rotor to Shaft Connection
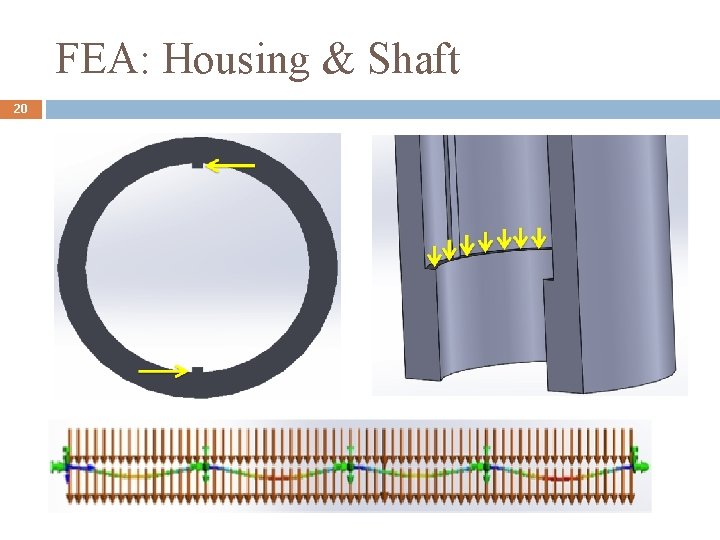
FEA: Housing & Shaft 20